This article introduces the paper "The Influence of Pressure During Solidification of High Pressure Die Cast Aluminum Telecommunications Components".
Core Objective:
To investigate the effects of key process parameters (intensification pressure, delay time, and casting velocity) on the porosity of high-pressure die-cast aluminum telecommunication components. The primary goal was to establish optimal process parameters to minimize porosity and improve product quality, facilitating a cost-effective transition from high-speed machining to high-pressure die casting for these components.
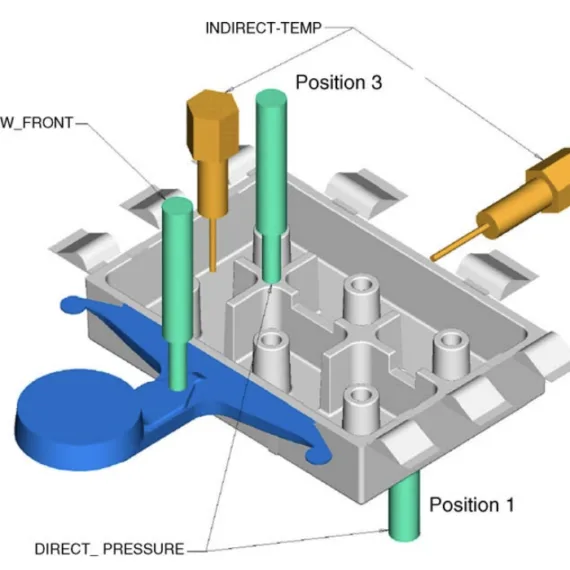
Methodology:
The researchers employed an experimental approach using in-cavity pressure sensors to monitor the pressure within the die cavity during the high-pressure die casting process. This allowed for a direct correlation between process parameters and the resulting porosity in the final castings. The experiments involved manipulating three key parameters:
- Intensification Pressure: The pressure applied after the die cavity is filled. This pressure helps consolidate the molten metal and reduce porosity. Several pressure levels were tested.
- Delay Time: The time interval between the completion of cavity filling and the application of intensification pressure.
- Casting Velocity: The speed at which the molten metal is injected into the die cavity. Higher velocities can lead to increased turbulence and potentially higher porosity.
Two different aluminum alloys (DA 401 and CA 313) were used in the experiments. A Buhler 53 D Evolution 530-ton cold chamber high-pressure die casting machine equipped with a Buhler Shot Control system was utilized. The porosity levels in the resulting castings were quantitatively measured and analyzed.
Key Results:
- Intensification Pressure: Increasing the intensification pressure generally led to a reduction in porosity, indicating that higher pressure effectively consolidates the molten metal and reduces the formation of pores. The effect was more pronounced in alloy DA 401 than in CA 313, suggesting a potential influence of alloy composition on the response to pressure.
- Delay Time: The delay time before applying the intensification pressure had a minimal impact on porosity levels within the tested range. While a slight increasing trend in porosity was observed with increasing delay times in one alloy, this was not statistically significant.
- Casting Velocity: Higher casting velocities resulted in increased porosity. This is attributed to increased turbulence during filling, leading to greater air entrapment and a higher likelihood of pore formation. The influence of velocity was less significant at higher intensification pressures.
- Set vs. Measured Values: A significant discrepancy was observed between the set pressure values (as programmed into the machine) and the actual measured pressures inside the die cavity. This difference increased with higher set pressures, highlighting the importance of in-cavity pressure monitoring for precise process control. Similar discrepancies, though less pronounced, were observed between set and measured casting velocities.
Researcher Information:
- Affiliation: ªCRC for Cast Metals Manufacturing (CAST), The University of Queensland, Australia; ᵇEcole des Mines d'Albi-Carmaux, France; ᶜFerra Engineering Pty Ltd., Australia; ᵈCRC for Cast Metals Manufacturing (CAST), CSIRO Manufacturing and Infrastructure Technology, Australia
- Authors: Matthew S. Dargusch, G. Dour, N. Schauer, C.M. Dinnis, G. Savage
- Research Areas: High-pressure die casting, process optimization, materials science, manufacturing engineering
Background and Objectives:
High-pressure die casting (HPDC) offers significant advantages for high-volume production of aluminum components. However, maintaining tight dimensional tolerances, low and consistent porosity, and high surface finish quality presents a challenge, especially for demanding applications like telecommunications components. Traditionally, high-speed machining was favored for these components due to its ability to meet stringent quality standards. However, this method is less cost-effective for mass production. This research aimed to address these limitations by exploring HPDC as a viable alternative, focusing on optimizing the process parameters to achieve superior quality and efficiency compared to machining.
Main Objectives and Research Content:
The main objective was to establish optimal process parameters for HPDC of aluminum telecommunications components, minimizing porosity and ensuring consistent product quality. This involved:
- In-Cavity Pressure Measurement: Implementing in-cavity pressure sensors provided crucial real-time data, enabling a direct assessment of the influence of process parameters on the solidification process within the die cavity.
- Parameter Optimization: Systematic variation of key parameters (intensification pressure, delay time, and casting velocity) allowed for the determination of their individual and combined effects on porosity.
- Alloy Comparison: Using two different aluminum alloys provided insights into the influence of material properties on the process.
- Data Analysis and Optimization: Statistical analysis of the collected data identified the optimal process parameter settings for minimizing porosity while maintaining high product quality.
Key Figures: (Descriptions of the key figures would be included here, detailing what each figure shows and its significance to the research. Referencing figures 3 through 15 from the original OCR would be included here.)
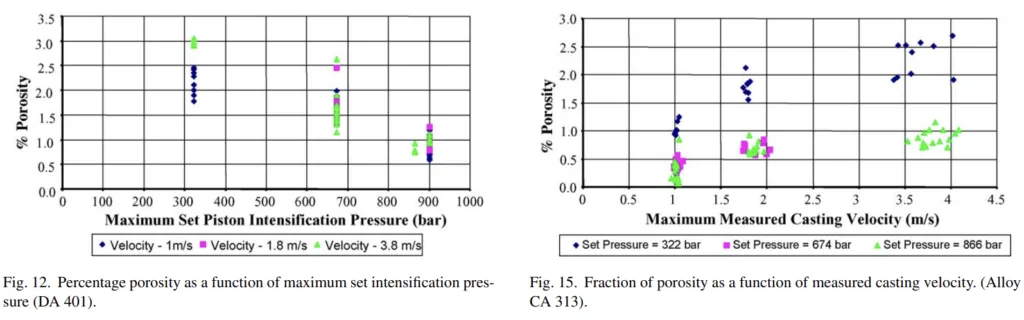
Results and Achievements:
- Quantitative Results: The study yielded quantitative data on the relationship between process parameters (intensification pressure, delay time, casting velocity) and porosity levels for two different aluminum alloys. The data allowed for the precise quantification of the effect of each parameter on the resulting porosity.
- Qualitative Results: The use of in-cavity pressure sensors provided a deeper understanding of the solidification process and its dynamics within the die cavity. The findings highlighted the limitations of relying solely on set parameters (as programmed into the machine) and emphasized the critical importance of direct measurement for process optimization.
- Technical Achievements: The research demonstrated the effectiveness of using in-cavity pressure measurement for optimizing HPDC processes. The established correlations between process parameters and porosity levels provide valuable guidance for producing high-quality aluminum castings, facilitating the cost-effective transition from traditional machining methods to HPDC. This approach reduces reliance on trial-and-error methods, improving efficiency and reducing costs.
Copyright and References:
This summary is based on the research paper "The influence of pressure during solidification of high pressure die cast aluminium telecommunications components" by Matthew S. Dargusch et al.
Source: DOI: 10.1016/j.jmatprotec.2006.05.001
Copyright © 2006 Elsevier B.V. All rights reserved. This summary is for informational purposes only and should not be used for commercial purposes without permission from the copyright holder.