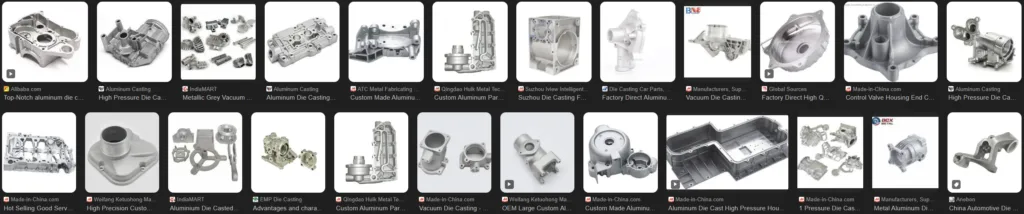
1. Introduction to High-Pressure Die Casting:
High-pressure die casting (HPDC) is a metal casting process characterized by injecting molten metal into a metal mold (die) under high pressure. Aluminum, valued for its lightweight yet strong nature and excellent corrosion resistance, is a prevalent material in HPDC, leading to its widespread use in diverse industries like automotive, electronics, and construction. The process is especially suitable for high-volume production demanding both speed and precision.
2. The Aluminum HPDC Process:
The HPDC process typically involves these stages:
- Melting: Aluminum alloy ingots are melted in furnaces (electric or gas-fired). Precise temperature and time control is crucial to maintain the desired alloy composition and quality. Refining processes, such as fluxing and filtration, are essential to remove impurities from the molten metal.
- Injection: Molten aluminum is injected into the die under high pressure (typically 700-1500 bar). This high pressure ensures rapid mold filling and accurate reproduction of even intricate designs. Injection speed and pressure significantly affect product quality, demanding precise control.
- Die: The die, usually crafted from high-strength steel or specialized alloys, precisely mirrors the final product's shape. Die design and fabrication are critical for product quality and production efficiency, requiring specialized expertise. Die durability and thermal management are paramount. Efficient cooling channel design is vital for extending die life and boosting production speed.
- Cooling: Molten aluminum solidifies within the die. Cooling rate directly impacts mechanical properties and surface finish, necessitating a well-designed cooling system. This might involve water, air, or specialized coolants.
- Ejection: The solidified casting is removed from the die. Die design and the ejection system are crucial to prevent damage and maintain efficiency. The placement and operation of ejector pins are critical.
- Post-processing: Castings undergo secondary operations to become finished products. These include trimming, drilling, tapping, and surface treatments (painting, anodizing, electroplating, etc.).
3. Aluminum Alloy Selection:
Numerous aluminum alloys are suitable for HPDC, each exhibiting unique properties. Alloy selection depends on the required mechanical properties, corrosion resistance, machinability, and cost-effectiveness. Common alloys include 380, 383, and 390. Alloy composition and heat treatment can fine-tune product characteristics.
4. Die Design and Manufacturing:
The die is paramount in HPDC. Die design considers product geometry, dimensions, surface finish, and mechanical properties. Durability, productivity, and maintainability are also vital factors. CAD/CAM systems are used for design, and CNC machining for fabrication. Die material selection balances wear resistance, heat resistance, and corrosion resistance.
5. Process Control and Quality Assurance:
HPDC is sensitive to numerous variables, demanding precise control and quality assurance. Parameters like temperature, pressure, injection speed, and cooling rate are monitored and controlled to maintain consistent product quality. Dimensional accuracy, surface finish, and mechanical properties are measured and inspected. Statistical Process Control (SPC) techniques ensure process stability and minimize defects.
6. Advantages and Disadvantages of HPDC:
Advantages:
- High productivity: Enables high-speed mass production.
- Excellent dimensional accuracy: Produces intricate parts with precision.
- Superior surface finish: Achieves smooth and lustrous surfaces.
- High mechanical strength: Offers a range of mechanical properties through alloy selection.
- Lightweight: Leverages aluminum's inherent lightness.
- Recyclability: Aluminum is a recyclable and environmentally friendly material.
Disadvantages:
- High initial investment: Requires expensive dies and equipment.
- Die life: Die lifespan is limited by the number of castings produced.
- Residual stresses: High injection pressure can induce residual stresses in the casting.
- Surface defects: Porosity, cracks, or other defects may occur.
- Safety concerns: Handling high-pressure molten metal necessitates stringent safety measures.
7. Applications:
HPDC finds applications across numerous industries:
- Automotive: Engine components, transmission parts, body parts, etc.
- Electronics: Cell phone casings, laptop housings, appliance components, etc.
- Construction: Window frames, door handles, building materials, etc.
- Machinery: Machine components, pumps, valves, etc.
8. Future Outlook:
HPDC technology continues to advance. Future developments will focus on meeting the increasing demands for higher productivity and quality. This includes advancements in high-strength die materials, more sophisticated process control, and automation. Sustainable processes are also a key research area, encompassing energy-efficient melting techniques, waste reduction strategies, and enhanced recycling methods.
9. Conclusion:
Aluminum HPDC is an efficient manufacturing process offering high productivity and excellent product quality. However, the high initial investment, die lifespan limitations, and potential for residual stresses must be carefully considered. Continuous technological advancements will likely lead to even more efficient and environmentally friendly processes in the future. Optimal results are achieved through careful alloy selection, die design, process control, and quality assurance, all requiring the expertise of skilled professionals. This summary provides a general overview; consult specialized literature for detailed information.