Unlocking the Secrets of Dissimilar Metal Joining: Advanced Imaging Techniques Reveal How to Create Stronger, More Reliable Copper-Steel Bonds.
This technical brief is based on the academic paper "A combined full-field imaging and metallography approach to assess the local properties of friction stir welded (FSW) copper-stainless steel joints" by S. Ramachandran, J.M. Dulieu-Barton, P.A.S. Reed, and A.K. Lakshminarayanan. It is summarized and analyzed for HPDC professionals by the experts at CASTMAN.
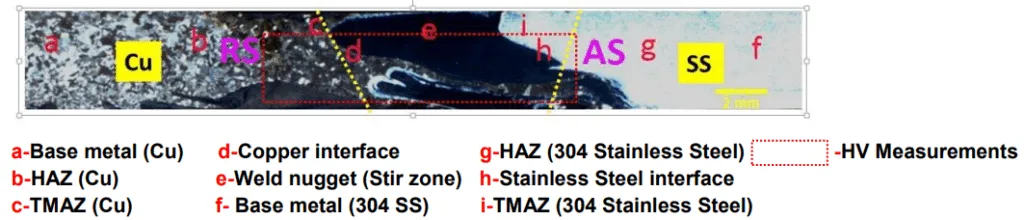
Keywords
- Primary Keyword: Dissimilar Metal Joining
- Secondary Keywords: Friction Stir Welding (FSW), Copper-Stainless Steel Joints, Microhardness Mapping, Digital Image Correlation (DIC), Weld Microstructure, Heat Affected Zone (HAZ), Thermoelastic Stress Analysis (TSA)
Executive Summary
- The Challenge: Joining materials with vastly different properties, like copper (Cu) and stainless steel (SS), is notoriously difficult using traditional fusion welding, often leading to defects and reduced mechanical performance.
- The Method: Researchers employed Friction Stir Welding (FSW), a solid-state process, to join 2 mm thick sheets of Cu and 304 SS. They then used a suite of advanced imaging and analysis techniques—including microhardness mapping, Digital Image Correlation (DIC), and Thermoelastic Stress Analysis (TSA)—to meticulously characterize the resulting joint.
- The Key Breakthrough: The study successfully identified and mapped the distinct microstructural zones across the weld—the Heat Affected Zone (HAZ), Thermomechanically Affected Zone (TMAZ), and the weld nugget. It revealed large hardness fluctuations within the nugget, directly corresponding to the mixture of Cu and SS particles.
- The Bottom Line: This research demonstrates a powerful, multi-faceted approach for understanding and validating the local properties of complex, dissimilar material joints. The FSW process, combined with detailed full-field analysis, offers a pathway to creating robust bonds without the defects of melting.
The Challenge: Why This Research Matters for HPDC Professionals
For decades, engineers have struggled with the challenge of joining dissimilar materials. As the paper’s introduction highlights, materials like copper and stainless steel have wide differences in melting point (Cu-1085°C vs. SS-1400-1500°C) and thermal conductivity (Cu is ~20x more conductive). In traditional fusion welding, this means one material melts long before the other, leading to defects like intermetallic phases, porosity, and cracking [Ref. 1].
While HPDC is not a joining process in the same vein, the core challenge is analogous. In advanced HPDC applications, such as casting aluminum around a steel or copper insert, managing the thermal gradients and understanding the material properties at the interface is critical to prevent defects and ensure component integrity. The problems of differential thermal behavior described in this paper are directly relevant to the challenges faced in overmolding and creating bimetallic HPDC components.
The Approach: Unpacking the Methodology
To overcome the limitations of fusion welding, the researchers utilized Friction Stir Welding (FSW). The paper describes FSW as a "solid-state" welding process that joins materials without melting them. A non-consumable rotating tool generates friction and severe plastic deformation, effectively forging the two materials together at a temperature below their melting points [Ref. 2].
To analyze the resulting joint, the team employed a combined, full-field approach:
- Metallography: Techniques including optical microscopy, SEM, and EBSD were used to visualize the microstructural features of the different weld zones.
- Microhardness Mapping: A 2D contour map of Vickers hardness was created across the entire joint to quantify local strength variations.
- Advanced Mechanical Analysis: Digital Image Correlation (DIC) and Thermoelastic Stress Analysis (TSA) were used to evaluate mechanical properties and stress distribution, providing a full-field view of the joint's performance under load.
The Breakthrough: Key Findings & Data
The study produced a detailed characterization of the Cu-SS FSW joint, revealing a complex but well-defined structure.
- Distinct Weld Zones: As shown in the macrostructure in Figure 1, the process created several distinct zones: the base metals (Cu and SS), the Heat Affected Zones (HAZ) on both sides, the Thermomechanically Affected Zones (TMAZ), and a central weld nugget or "Stir Zone" (SZ).
- Heterogeneous Hardness: The 2D microhardness map (Figure 2) provides a powerful visualization of the mechanical property changes. The hardness transitions smoothly from the soft copper base metal (HV 85-95) to the very hard stainless steel base metal (HV 250-280). Critically, the weld nugget shows large fluctuations, confirming it is a mechanical mixture of harder SS particles within a softer Cu matrix.
- Microstructural Transformation: The optical micrographs in Figure 3 clearly show the changes in grain structure. The weld nugget (Fig. 3c) consists of fine, recrystallized grains, a direct result of the severe plastic deformation from the FSW tool. In contrast, the HAZs (Fig. 3d, 3e) exhibit grain growth compared to the original base metals (Fig. 3a, 3b).
Practical Implications for Your HPDC Operations
While this paper focuses on FSW, its methodology and findings offer valuable lessons for advanced HPDC. The challenges of managing material interfaces and ensuring mechanical integrity are universal.
- For Process Engineers: The study's detailed mapping of HAZs demonstrates the profound impact of localized thermal input on material microstructure and properties. This is directly analogous to how die temperature and cooling rates in HPDC affect the grain structure and mechanical properties of a casting, especially near an insert. The techniques used here could be adapted to better understand and optimize thermal management in HPDC.
- For Quality Control: The use of full-field techniques like microhardness mapping and DIC, as shown in Figure 2, provides a far more comprehensive picture of joint quality than traditional point-based testing. For critical HPDC components with inserts, adopting similar mapping techniques could provide unprecedented insight into the integrity of the bond interface and identify potential weak spots.
- For Die Design & Bimetallic Components: This study on joining Cu and SS provides a blueprint for characterizing any dissimilar metal interface. For HPDC applications involving cast-in inserts, understanding the "stir zone" or interface is paramount. The paper's approach to analyzing this mixed-material zone offers a robust methodology for validating the design and performance of bimetallic HPDC parts.
Paper Details
A combined full-field imaging and metallography approach to assess the local properties of friction stir welded (FSW) copper-stainless steel joints
1. Overview:
- Title: A combined full-field imaging and metallography approach to assess the local properties of friction stir welded (FSW) copper-stainless steel joints
- Author: S. Ramachandran, J.M. Dulieu-Barton, P.A.S. Reed, A.K.Lakshminarayanan
- Year of publication: Not specified, but references are from 2003-2009.
- Journal/academic society of publication: Not specified.
- Keywords: FSW, Cu, SS, DIC, TSA, Metallography, Microhardness, local properties
2. Abstract:
The Friction Stir Welding (FSW) process was used to join 2 mm thick sheets of copper (Cu) and 304 stainless steel (SS). Various metallography techniques (EBSD, SEM, optical microscopy) were employed to establish the local material morphology. These techniques identified varying microstructural features in the weld zone, including the Heat Affected Zone (HAZ), the Thermomechanically Affected Zone (TMAZ), and the weld nugget. Microhardness variations were mapped to analyze hardness distributions. Digital Image Correlation (DIC) and Thermoelastic Stress Analysis (TSA) were used to evaluate mechanical properties and stress redistribution at the weld.
3. Introduction:
Joining dissimilar materials like copper and stainless steel is challenging due to wide differences in physical properties such as melting point and thermal conductivity. Traditional fusion welding often leads to defects like intermetallic phases, porosity, and cracking. FSW is a solid-state process that avoids melting, thus eliminating many drawbacks of fusion welding. It joins materials through the forging action of a rotating tool, which induces severe plastic deformation. The lower heat input of FSW makes it suitable for joining dissimilar materials.
4. Summary of the study:
Background of the research topic:
The significant difference in physical properties between copper and stainless steel makes them difficult to weld using conventional fusion methods. Copper's high thermal conductivity rapidly dissipates heat, while the large melting point difference complicates the process. These challenges often result in defective joints with reduced mechanical properties.
Status of previous research:
Previous research indicates that fusion welding processes suffer from drawbacks like the formation of intermetallic phases and various forms of cracking [Ref. 1]. FSW has been identified as a promising alternative because its solid-state nature and lower heat input can overcome these issues [Ref. 2].
Purpose of the study:
The purpose was to use a combination of full-field imaging (DIC, TSA) and metallography techniques to comprehensively assess the local morphological and mechanical properties of a friction stir welded joint between copper and 304 stainless steel.
Core study:
The core of the study involved creating a FSW joint between Cu and SS and then subjecting it to extensive analysis. This included identifying and characterizing the different zones (HAZ, TMAZ, weld nugget) through optical microscopy, mapping the hardness distribution across the joint with a 2D contour plot, and using DIC and TSA to evaluate the mechanical response and stress distribution.
5. Research Methodology
Research Design:
2 mm thick sheets of copper and 304 stainless steel were joined using the Friction Stir Welding (FSW) process. The resulting joint was sectioned transversely for analysis.
Data Collection and Analysis Methods:
- Metallography: EBSD, SEM, and optical microscopy were used to examine the microstructure.
- Microhardness Testing: Vickers microhardness tests (HV) were performed across the joint to create a 2D contour map. The map consisted of 420 indents (5 rows x 84 columns).
- Mechanical Analysis: Digital Image Correlation (DIC) and Thermoelastic Stress Analysis (TSA) were employed to evaluate mechanical properties and stress redistribution.
Research Topics and Scope:
The research focused on the characterization of the local properties of the FSW Cu-SS joint. The scope included identifying microstructural zones, mapping hardness variations, and evaluating mechanical behavior using advanced imaging techniques.
6. Key Results:
Key Results:
The FSW process successfully joined copper and 304 stainless steel. The resulting weld nugget was found to be a mixture of Cu and SS, generated by the stirring action of the tool. This mixture led to large fluctuations in hardness within the nugget, corresponding to the different hardness values of Cu (HV 85-95) and SS (HV 250-280). The HAZs in both materials showed significant variations in grain size compared to the base metals.
Figure Name List:
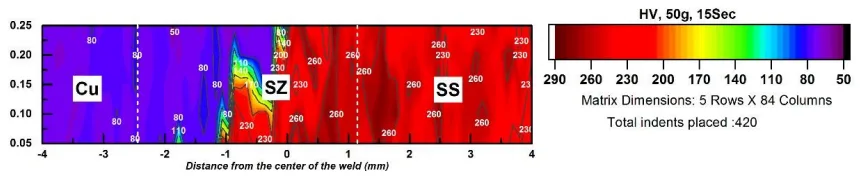
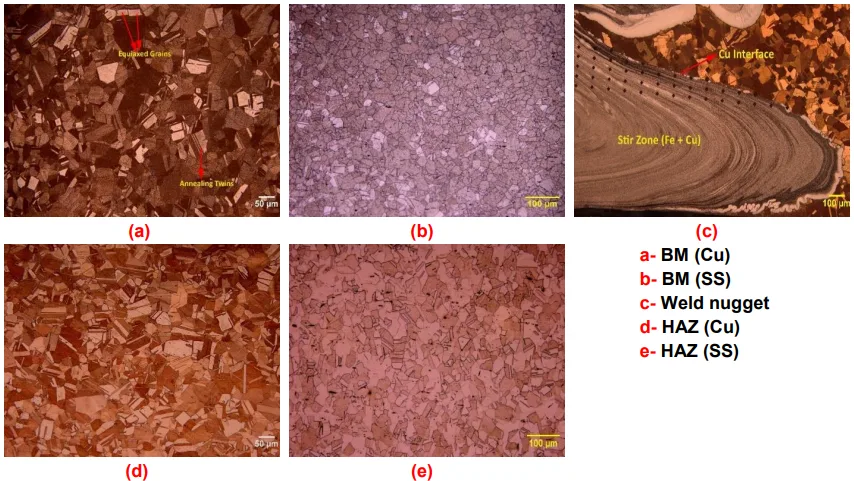
- Fig. 1 Macrostructure along a transverse section of the friction stir welded Cu-SS joint
- Fig. 2 Microhardness 2D-contour map of Cu-SS FSW joint over the region shown in Fig. 1
- Fig. 3 Microstructures at different zones of the friction stir welded Cu-SS Joint
7. Conclusion:
The paper does not contain a formal conclusion section, but the abstract and experimental work sections conclude that FSW can join Cu and SS, creating distinct microstructural zones. The weld nugget is a heterogeneous mixture of the two materials, which is reflected in significant local hardness variations. The study successfully demonstrates that a combined approach of metallography and full-field imaging can effectively characterize the complex local properties of such joints. The authors state that future work will involve high-resolution DIC and TSA on tensile specimens to further evaluate local properties.
8. References:
- http://nhml.com/weld-discrepancies/
- Bhadeshia, H.K.D.H. & Debroy, T., 2009. Critical assessment: friction stir welding of steels. Science and Technology of Welding and Joining, 14(3), pp. 193-196.
- Lockwood, W.D. & Reynolds, A.P., 2003. Simulation of the global response of a friction stir weld using local constitutive behaviour. Materials Science and Engineering A, 339(1-2), pp.35-42.
Conclusion & Next Steps
This research provides a valuable roadmap for characterizing complex, dissimilar-material joints. By moving beyond simple pass/fail tests and embracing a full-field, multi-technique approach, engineers can gain a much deeper understanding of how processing affects local material properties and, ultimately, final component performance.
At CASTMAN, we are dedicated to applying the latest industry research to solve our customers' most challenging die casting problems. If the issues of joining dissimilar materials or characterizing complex interfaces resonate with your operational goals, contact our engineering team to discuss how we can help you implement advanced analytical principles in your components.
Expert Q&A: Your Top Questions Answered
Q1: What makes Friction Stir Welding better than traditional fusion welding for joining copper and steel?
A1: According to the paper's Introduction
, FSW is a "solid-state" process that avoids melting the materials. This eliminates many defects common in fusion welding, such as intermetallic phases, porosity, and solidification cracking, which arise from the large differences in melting point and thermal conductivity between copper and steel.
Q2: What does the "weld nugget" consist of?
A2: The paper states in the Experimental work
section that the weld nugget is a "mixture of Cu and SS generated as a result of the stirring action of the FSW tool." This is confirmed by the large hardness fluctuations seen in Figure 2.
Q3: Is this FSW process applicable to materials other than copper and stainless steel?
A3: This study, as described in the Abstract
and Experimental work
sections, specifically focuses on joining 2 mm thick sheets of copper (Cu) and 304 stainless steel (SS). The applicability to other material combinations would require separate investigation.
Q4: What specific measurement technique revealed the hardness variations across the weld?
A4: The researchers used Vickers microhardness testing to create a detailed 2D contour map of the joint. As noted in Figure 2, they placed a total of 420 indents in a dense matrix to capture the local hardness variations with high resolution.
Q5: According to the paper, what is the planned next step for this research?
A5: The authors state in the Future work
section that the next step is to "conduct high resolution DIC on specimens of Cu-SS FSW joints loaded in uniaxial tension" and to use TSA "to evaluate the stress distribution in the weld."
Q6: What is the direct, practical takeaway from this paper for a facility that uses cast-in inserts?
A6: The core takeaway, based on the paper "A combined full-field imaging and metallography approach...", is that the interface between two dissimilar materials is not a simple line but a complex, heterogeneous zone. The paper provides a powerful methodology (combining microscopy, hardness mapping, and DIC/TSA) for characterizing this zone, which is directly relevant for validating the quality and predicting the performance of HPDC parts with cast-in inserts.
Copyright
- This material is an analysis of the paper "A combined full-field imaging and metallography approach to assess the local properties of friction stir welded (FSW) copper-stainless steel joints" by S. Ramachandran et al.
- Source of the paper: The provided document does not list a formal publication venue or DOI.
- This material is for informational purposes only. Unauthorized commercial use is prohibited.
- Copyright © 2025 CASTMAN. All rights reserved.