The content of this introduction paper is based on the article "Review of technologies for identification of die casting parts" originating from researchers affiliated with Laserax Inc., Université Laval, and Viami International.
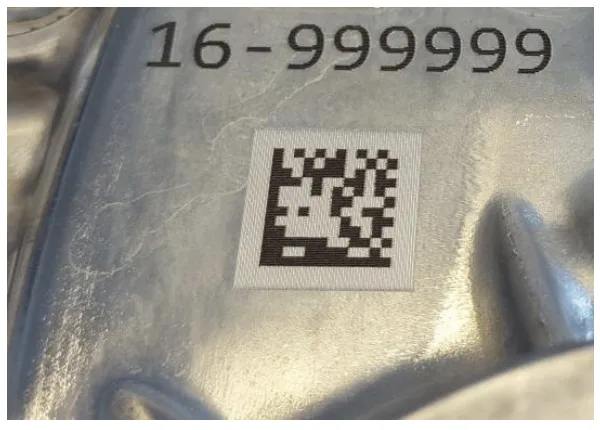
1. Overview:
- Title: Review of technologies for identification of die casting parts
- Author: A. Fraser, J. Maltais¹, M. Hartlieb³, C. Frayssinous², R. Vallée² and X. P. Godmaire¹ (Affiliations: ¹Laserax Inc, ²Université Laval, ³Viami International)
- Year of publication: Not explicitly specified in the provided document.
- Journal/academic society of publication: Not explicitly specified; affiliations include Laserax Inc., Université Laval, Viami International.
- Keywords: Keywords not provided in the paper.
2. Abstract:
Part traceability is increasingly required not only for safety critical applications, but for a growing number of applications within various industries. Die castings are no exception to this and with the structural/high integrity market as the fastest growing segment, it is no wonder that traceability and marking of die castings are becoming a hot topic. High integrity parts typically have an identification requirement for 100% of the parts produced. This does not only allow immediate access to alloy and process data in case of an incident with the part, it also helps to improve part quality and management. Different technologies are available on the market and provide inherent pros and cons. The die casting industry presents several aspects that are very important to consider when choosing the right marking technology. Complex components with uneven surfaces, often at high temperature when being marked, short cycle time and post marking processes like shot blast treatment are among the most important ones. Part marking - while a vital step in the production process of the castings – should never be the bottle neck in the process, nor should it be a contributor to scrap rate. This paper aims to analyze the different marking methods available and to point out the most suitable one for inline marking of die casting parts. Some marking results are presented with the emphasis on the influence of the temperature, the cycle time and the shot blast post-treatment. The results show that a laser based technology is well suited to address all the requirements of the die casting industry.
3. Introduction:
Traceability and therefore individualized marking of castings is becoming an increasing requirement both during the development process (where it helps to quickly identify flaws in the process and which process parameters need to be modified) as well as for series production of high integrity parts [1]. The obvious challenges in an industrial die casting environment are (a) fast cycle time (and part marking should certainly not be the bottleneck in this very capital intensive process), (b) marking on surfaces that are not perfectly flat, (c) parts that are typically still at elevated temperature when marked, and not perfectly clean but covered with remains of lubricants or dirt, and (d) the marking's ability to also withstand additional processing like heat treatment, shot blasting, washing, etching, conversion coating, etc.. Finally, the marking should remain safely on the part for its entire operational lifetime.
Traditionally part marking required clamping the parts in a precise position in order to obtain perfectly repetitive marking. When cycle time is key and process complexity and investment need to be minimized, then we would ideally like to have a marking system that will work perfectly even at a distance and with a certain tolerance (e.g. at 1 foot from the marker with a tolerance of an inch or two either way, so the part does not have to be clamped in any point but simply held by the extraction robot in front of the marker). This paper will present a review of the technologies available to identify die casting parts. It will present pros and cons of different technologies and for which utilization they are adapted. Result will then be presented including the effect of the temperature on the marking speed and the effect of post treatment such as shot blast.
4. Summary of the study:
Background of the research topic:
The increasing demand for part traceability in various industries, particularly for safety-critical and high-integrity die castings, necessitates reliable and efficient identification methods. Traceability aids in quality management, process optimization, and provides crucial data access in case of part incidents.
Status of previous research:
Several technologies exist for part identification, each with limitations in the context of die casting:
- Labels and Nameplates: Prone to falling off during processing or use, costly consumables and labor, unsuitable for high temperatures and uneven surfaces.
- Pin Stamping / Dot Peen: Creates deep, permanent marks but is relatively slow, requires close contact and precise positioning, may not provide contrast, and the surface deformation can exceed quality specifications for high-integrity parts.
- Inkjet Printing: Offers colored marks but lacks durability against subsequent processes like machining, shot blasting, or washing/etching.
- Direct Mold Marking: Suitable for static information (alloy, facility, cavity) but not for individual part data or 2D barcodes linked to specific process parameters.
Purpose of the study:
This study aims to analyze available marking technologies for die casting parts, identify the most suitable method for inline marking considering industry-specific challenges (cycle time, temperature, surface condition, post-treatments), and specifically investigate the performance of laser marking, focusing on its resistance to shot blast post-treatment.
Core study:
The core of the study focuses on laser marking technology due to its potential advantages (speed, robustness, non-contact, high-temperature capability, precision on uneven surfaces). A key challenge identified is the susceptibility of standard laser black marking (which sits slightly above the surface) to removal by shot blasting. The study proposes and investigates a strategy to enhance shot blast resistance by pre-etching a crater with the laser before applying the black mark within this depression (Figure 6). Experiments were conducted using a 100W fiber laser on aluminum die casting surfaces, varying pre-etching parameters (passes, speed, line spacing) and code sizes. The marked samples were subjected to shot blasting using two different steel ball sizes (S170 and S460). The effects were evaluated using surface profilometry (Dektak 150) and visual inspection.
5. Research Methodology
Research Design:
The research employed a two-part design:
- A comparative review of existing part identification technologies (Labels, Pin Stamping, Inkjet Printing, Direct Mold Marking, Laser Marking) assessing their suitability for the die casting industry based on criteria like durability, speed, cost, and compatibility with process conditions.
- An experimental investigation focusing on laser marking, specifically examining the effect of shot blast post-treatment on mark durability and exploring a pre-etching strategy to improve resistance.
Data Collection and Analysis Methods:
- Laser Marking: A 1.06 µm fiber laser (100W average power, 100 ns pulse duration, 100 kHz frequency) was used to mark Data Matrix codes on aluminum samples. Parameters varied included the number of pre-etch passes (3 to 15), pre-etch speed (3000-7000 mm/s), line spacing (0.025-0.125 mm), and code size (4x4 mm, 6x6 mm). Black marking parameters were kept constant (400 mm/s speed, 0.125 mm line spacing).
- Shot Blast Treatment: Marked samples were subjected to shot blasting using S170 (0.355 mm diameter) and S460 (1 mm diameter) steel balls. Treatment duration was varied.
- Surface Analysis: A Dektak 150 surface profiler was used to measure surface profiles before and after shot blast treatment to quantify material removal and surface modification. 3D surface mapping was also performed.
- Visual Inspection: Photographs were taken to document the appearance of the markings before and after treatment. Mark readability was assessed visually.
Research Topics and Scope:
The research covered:
- Review and comparison of different part identification technologies for die castings.
- Evaluation of laser marking as a suitable technology for die casting environments.
- Investigation of the effect of shot blast post-treatment on laser markings.
- Development and testing of a pre-etching strategy to enhance the shot blast resistance of laser markings.
- Analysis of the influence of laser parameters (pre-etch depth) and shot blast parameters (ball size, duration) on mark survivability and readability.
- Assessment of marking on aluminum die casting alloy.
6. Key Results:
Key Results:
- Laser marking appears promising for die casting due to speed, precision, and ability to mark hot, uneven surfaces, but standard black marking is vulnerable to shot blasting as it creates raised features.
- A pre-etching strategy, creating a depression before black marking, was investigated to protect the mark. Surface profiles confirmed that multiple laser passes could create depressions below the original aluminum level (Figure 7).
- Shot blasting significantly alters the surface profile, removing the peaks associated with black marking and potentially the surrounding etched edges (Figure 8).
- Shot blasting with larger S460 balls (higher kinetic energy) resulted in deep surface impacts (approx. 48 µm deep holes) and completely destroyed the laser markings (Figure 10, Figure 12).
- Shot blasting with smaller S170 balls (lower kinetic energy) resulted in shallower impacts (approx. 20 µm deep holes) and smoother surfaces. While the black contrast was completely erased, remnants of the code structure were sometimes visible, though generally unreadable by algorithms (Figure 9).
- The effectiveness of the pre-etching strategy depends critically on achieving sufficient depth relative to the shot blast impact and ball size. The tested parameters, even with multiple pre-etch passes, were insufficient to fully protect the marking against the tested shot blast conditions, especially the S460 balls.
- Mark survivability is influenced by random factors like the duration the part spends in the shot blast stream and the location of the mark relative to part features (e.g., marks near protrusions may be shielded).
- Optimization potential exists by using smaller code cell sizes (e.g., 0.25 mm wide) combined with deeper pre-etching (approx. 100 µm deep) to potentially allow standard S170 balls to pass over without destroying the blackening at the bottom of the etched cell.
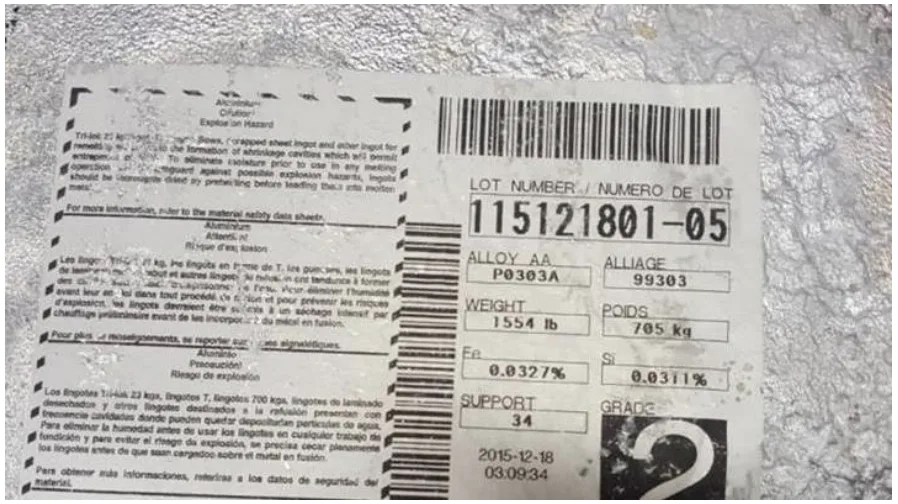
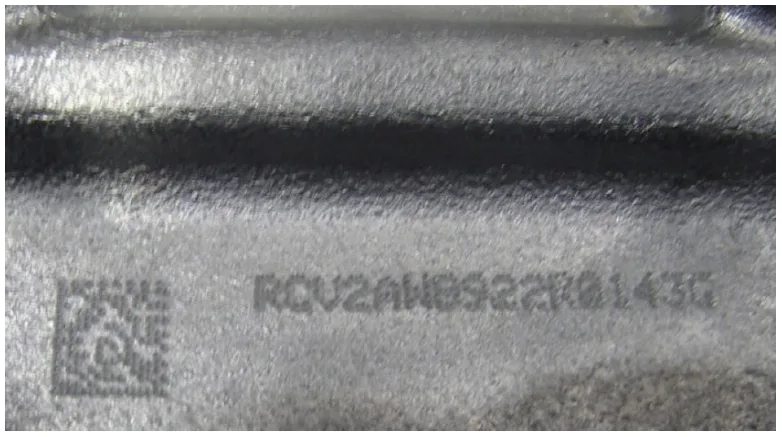
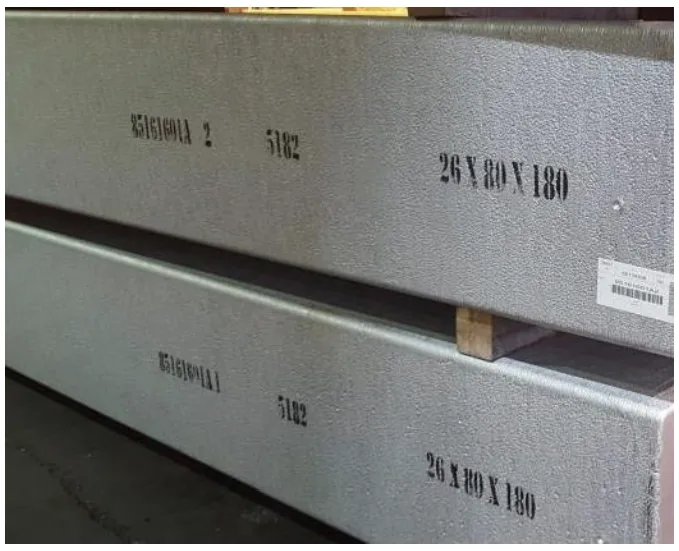
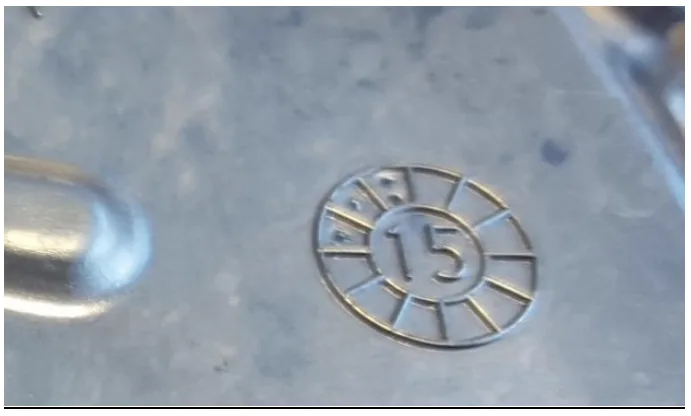
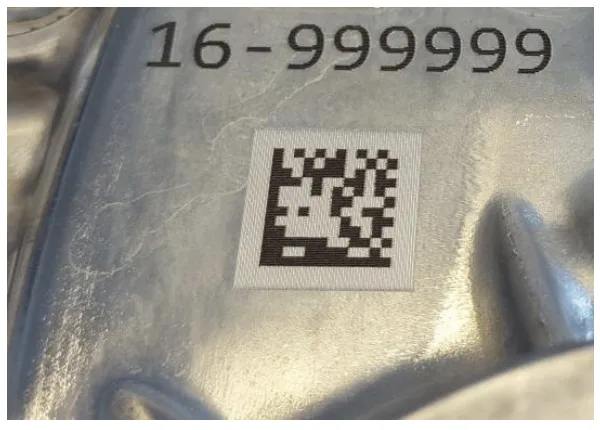
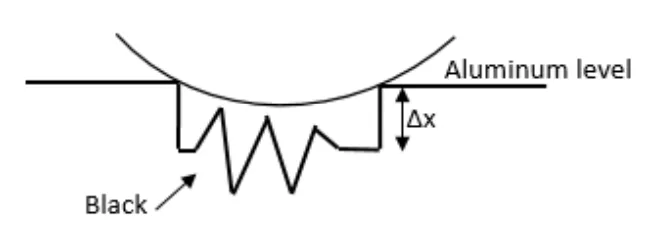
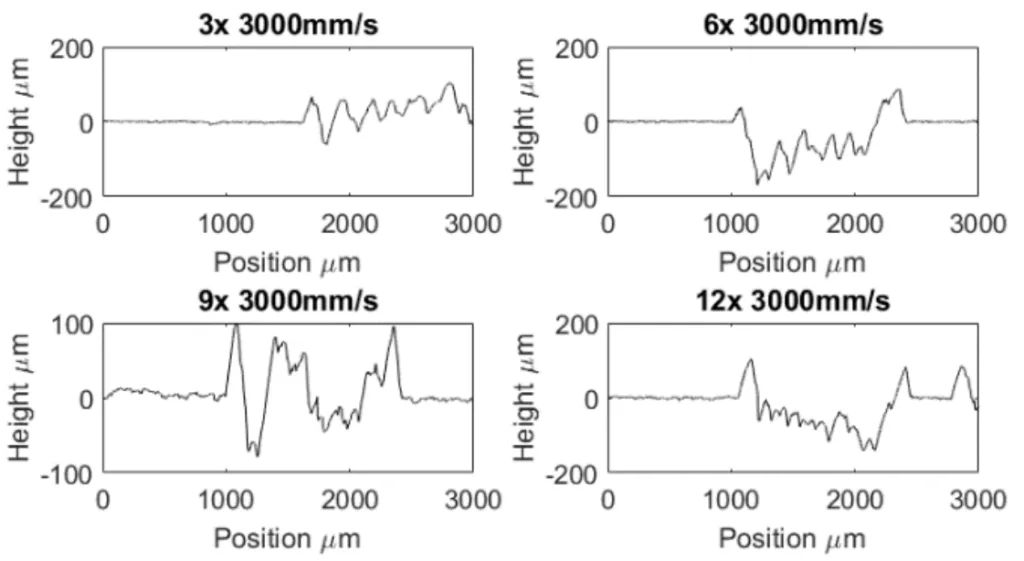
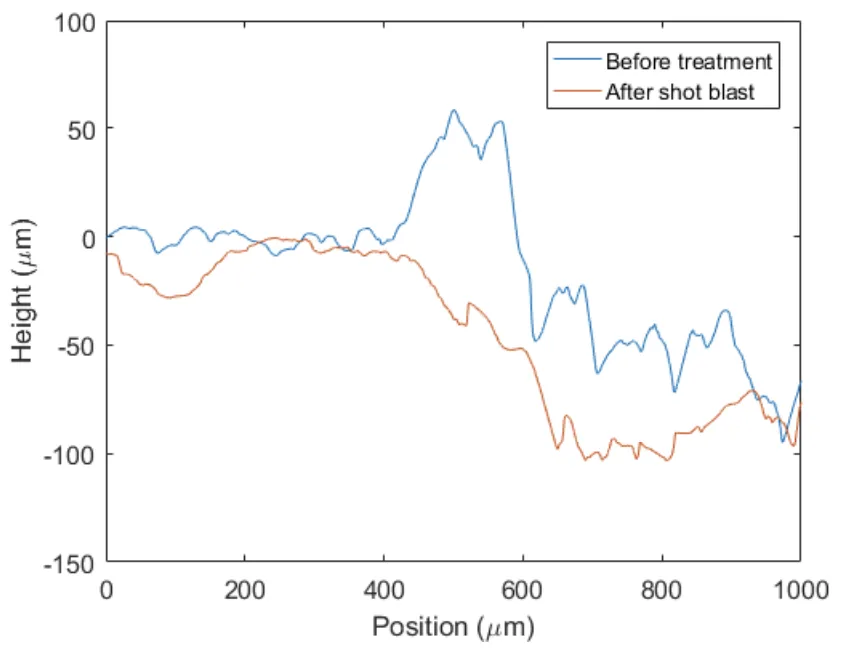
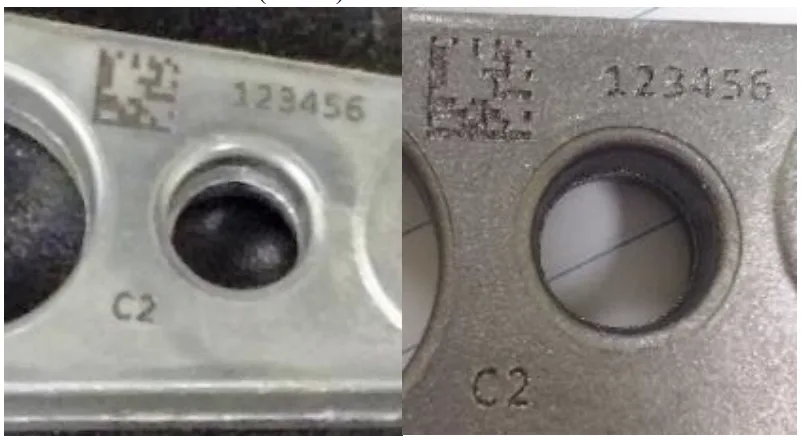
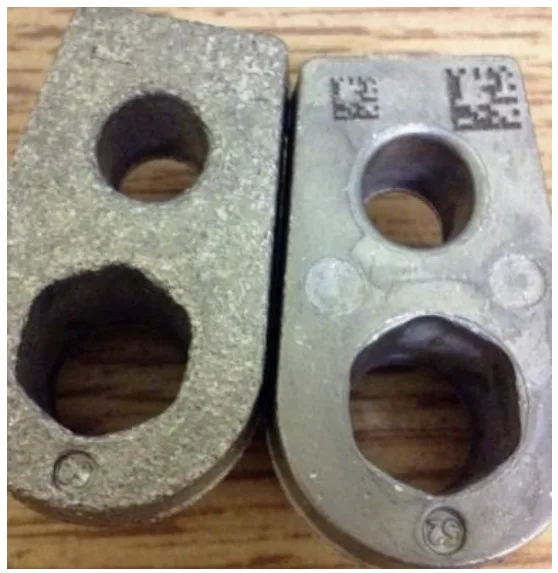
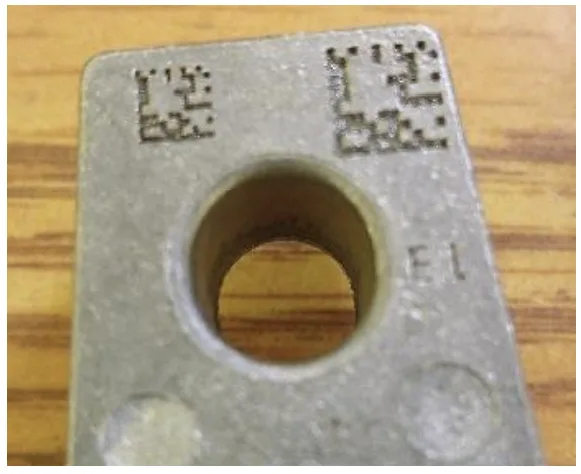
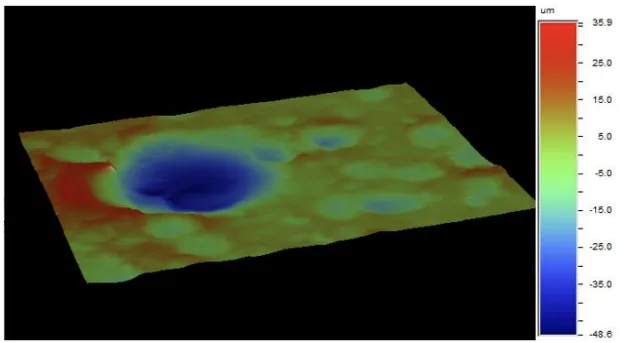
Figure Name List:
- Figure 1: Printed label (sticker)
- Figure 2: Pinstamp®/Dot peen marked die casting.
- Figure 3: Inkjet printing.
- Figure 4: Direct mold marking and punch
- Figure 5: Laser marked identifier on aluminum die casting alloy.
- Figure 6: Sketch of the idea behind the protected marking.
- Figure 7: Surface profile of samples before treatment where the laser was passed multiple times before marking the black.
- Figure 8: Surface profile measured with Dektak 150 of a marking before and after treatment with S170 balls.
- Figure 9: Photo of a marking before treatment (left) and after shot blast with S170 balls (center).
- Figure 10: Photo of 2 samples after 20 seconds shot blast with S460 balls.
- Figure 11: Photo of sample after a treatment of 20 seconds with S460 balls and another 20 seconds with S170 balls.
- Figure 12: 3D profile of surface after being hit by S470 and S170 balls.
7. Conclusion:
Laser marking is the most suitable process to permanently mark die castings. It can achieve the desired cycle times, quality and repeatability. It can easily withstand almost all surface treatments typically applied on die castings. The main challenge remains shot blasting which was researched in depth. All the shot blasting parameters previously presented play a role in the resistance of the code. With adequate shot blasting conditions, it should be possible, in our opinion, to preserve a readable code after shot blast treatment on a die casting part. This also includes having a relatively small time of the process. It is also important to have balls that are not too big because we have seen that they are destroying the aluminum surface. The balls must be big enough to not reach the bottom of the cases in order to keep the black surface intact. The dimension of the code is also a determining parameter. We think that the smaller cases increase the chance of obtaining a readable code after the treatment. The laser process should be optimized in order to achieve a cell size of around 0.25 mm wide and approximately 100 µm deep. We think this would allow using the standard S170 balls and keeping the blackening at the bottom intact. Further tests will be done to demonstrate this and will be presented at the NADCA conference.
Thanks to its versatility, laser technology can adapt to multiple requirements, including fostering resistance to treatments that are very common in die casting industries. Laser marking meets many industrial needs, namely robustness, speed, ability to mark on uneven surfaces as well as at high temperature.
8. References:
- [1] S. Desrosiers et Al., Alloy and heat treatment development for weldable structure parts, 2014 Die Casting ongress conference proceedings
- [2] J. Maltais and al., Surface analysis study of laser marking of aluminum, submitted to ICSOBA 2016 conference proceedings
- [3] Alex Fraser and al., Important considerations for laser marking an identifier on aluminum, Light metals 2016 (Proceedings of TMS 2016), p. 261-264
- [4] J. Benes, The lowdown on laser marking, americanmachinist.com, March 25th 2008
9. Copyright:
- This material is a summary of a paper by "A. Fraser, J. Maltais, M. Hartlieb, C. Frayssinous, R. Vallée and X. P. Godmaire". Based on "Review of technologies for identification of die casting parts".
- Source of the paper: DOI not provided in the paper.
This material is summarized based on the above paper, and unauthorized use for commercial purposes is prohibited.
Copyright © 2025 CASTMAN. All rights reserved.