The content of this introduction paper is based on the article "An Analytical Model of Induction Motors for Rotor Slot Parametric Design Performance Evaluation" published by "(IJACSA) International Journal of Advanced Computer Science and Applications".
![Fig. 1. Power flow diagram of induction motor [15], [16], [17]](https://castman.co.kr/wp-content/uploads/image-1825-1024x559.webp)
1. Overview:
- Title: An Analytical Model of Induction Motors for Rotor Slot Parametric Design Performance Evaluation
- Author: Ahamed Ibrahim Sithy Juhaniya, Ahmad Asrul Ibrahim, Muhammad Ammirrul Atiqi Mohd Zainuri, Mohd Asyraf Zulkifley
- Year of publication: 2022
- Journal/academic society of publication: (IJACSA) International Journal of Advanced Computer Science and Applications
- Keywords: Analytical model; efficiency; induction motor; rotor slot parameters
2. Abstract:
Induction motors are commonly used in most electricity generation due to their low investment cost. However, the performance of the induction motors for different applications highly depends on rotor design and machine geometry. For example, changing rotor bar height and width varies the rotor resistance and reactance, thereby leading to variation of the motor efficiency. A parametric study on rotor slot geometry parameters such as opening height, rotor slot depth, and rotor slot width, is carried out to investigate the effect of the parameters on the efficiency of a squirrel cage induction motor. The study is based on analytical model that considers a general-purpose squirrel cage induction motor with the specification of 5.5 kW, 60 Hz, and 460 V. The analytical model is developed and simulated within the MATLAB software environment. The effects of each parameter variation toward efficiency of the induction motor are investigated individually as well as all together using a 4D scatter plot. Results show that the efficiency can be improved up to 0.1% after designing a suitable setting of rotor slot parameters from the initial settings.
3. Introduction:
Electrical machines are essential for electromechanical energy conversion, widely used as motors or generators. Among motor types, induction motors are favored in residential and industrial applications due to their low cost, low maintenance, and self-starting capabilities. However, induction motors are known for their relatively low efficiency. Improving efficiency is crucial, and modeling with optimal parameter settings is a key approach. Rotor slot geometry parameters significantly influence motor performance because they determine the resistance and leakage reactance of the motor. Prior research has explored rotor slot redesign to enhance induction motor performance. However, previous investigations were mainly based on 2D analysis and Finite Element Method (FEM) techniques, which can be computationally burdensome and less flexible for parametric studies, especially in the initial design phase, and often lack direct focus on efficiency. This paper addresses these limitations by investigating the effect of rotor slot parameter changes on the efficiency of induction motors using an analytical model.
4. Summary of the study:
Background of the research topic:
Induction motors are widely utilized in electricity generation and various applications due to their low investment cost. Performance is highly dependent on rotor design and machine geometry. Rotor slot design is a critical factor affecting motor efficiency.
Status of previous research:
Previous studies have explored redesigning rotor slots to improve induction motor performance, including varying rotor bar shapes and materials. FEM techniques and 2D analysis have been employed to study the impact of rotor slot design on motor behavior, flux distribution, power losses, harmonic distortion, and starting characteristics. However, these methods often suffer from computational burden, limited flexibility for parametric studies, and insufficient focus on efficiency.
Purpose of the study:
This study aims to investigate the effect of varying rotor slot geometry parameters, specifically opening height (Hor), rotor slot depth (Hr), and rotor slot width (Btr), on the efficiency of squirrel cage induction motors. The research utilizes an analytical model to overcome the limitations of previous methods.
Core study:
The core of this study is the development and application of an analytical model within MATLAB to evaluate the efficiency of a 5.5 kW, 60 Hz, 460 V squirrel cage induction motor. The analytical model is used to conduct a parametric study, varying rotor slot parameters individually and collectively to assess their impact on motor efficiency. The study focuses on optimizing rotor slot geometry to enhance motor performance.
5. Research Methodology
Research Design:
This research employs an analytical modeling approach to investigate the impact of rotor slot geometry parameters on induction motor efficiency. The study is based on a parametric design evaluation using a developed analytical model.
Data Collection and Analysis Methods:
The analytical model of a squirrel cage induction motor is developed and simulated using MATLAB software. The model calculates motor efficiency based on varying rotor slot parameters. Data is generated through simulations by systematically changing rotor slot opening height (Hor), rotor slot depth (Hr), and rotor slot tooth width (Btr), both individually and in combination. The efficiency variations are then analyzed and visualized using graphs and 4D scatter plots to determine the optimal parameter settings.
Research Topics and Scope:
The research focuses on the parametric study of rotor slot geometry in squirrel cage induction motors. The scope includes:
- Development of an analytical model for efficiency calculation.
- Individual parametric analysis of rotor slot height (Hr), rotor slot opening height (Hor), and rotor slot tooth width (Btr).
- Amalgamated parametric analysis of Hr, Hor, and Btr using a 4D scatter plot.
- Evaluation of efficiency improvements based on parameter variations.
- The motor specifications are fixed at 5.5 kW, 60 Hz, and 460 V, with specific stator slot dimensions as defined in Table IV of the paper.
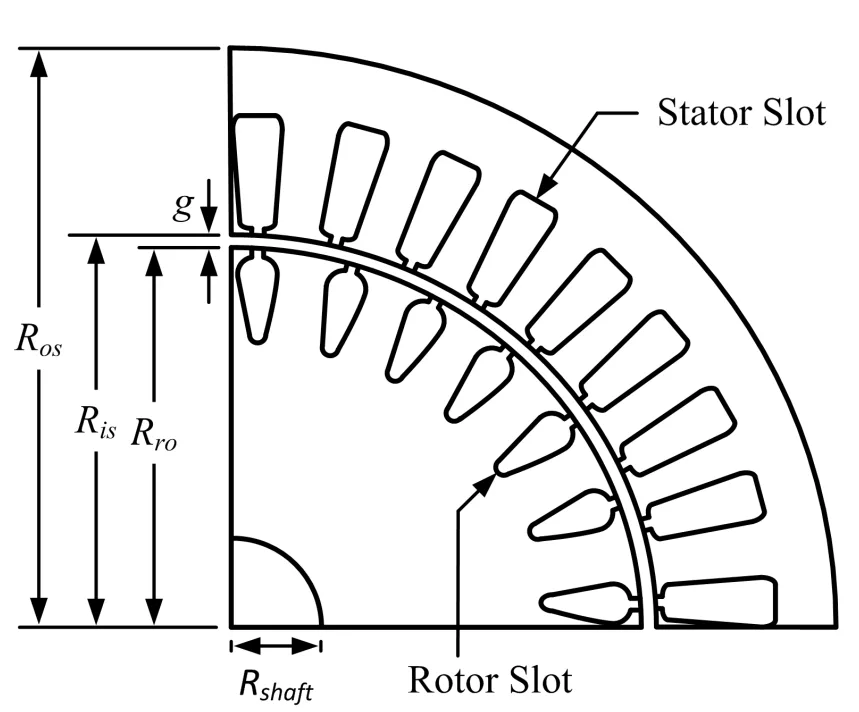
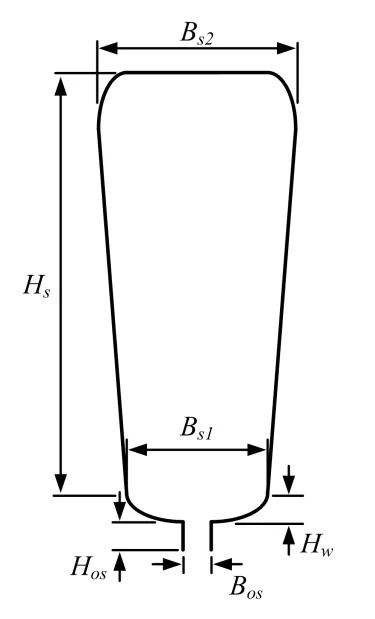
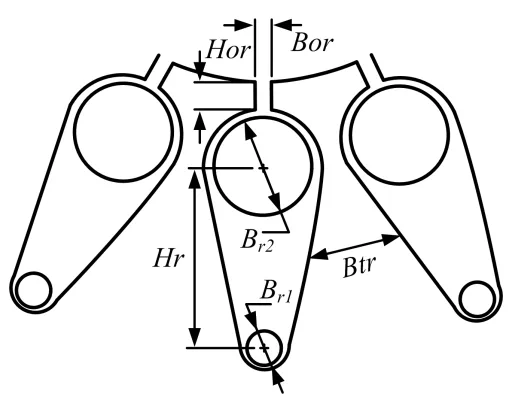
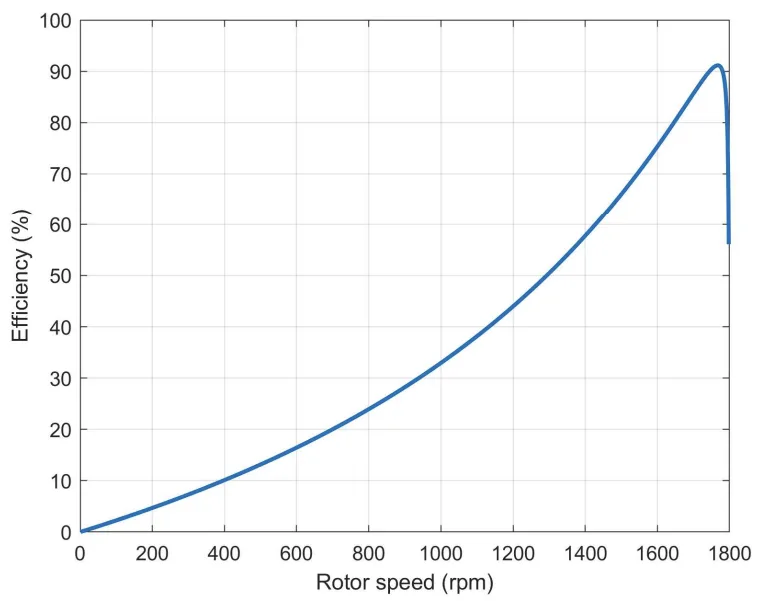
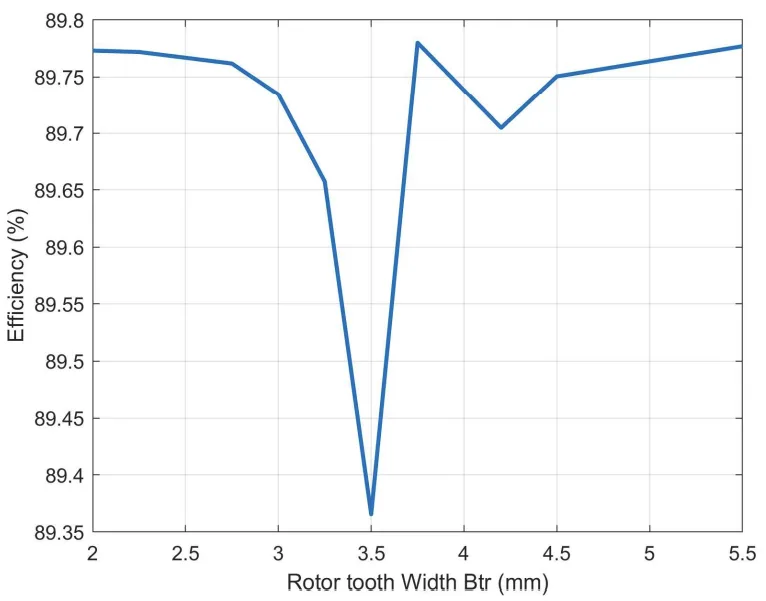
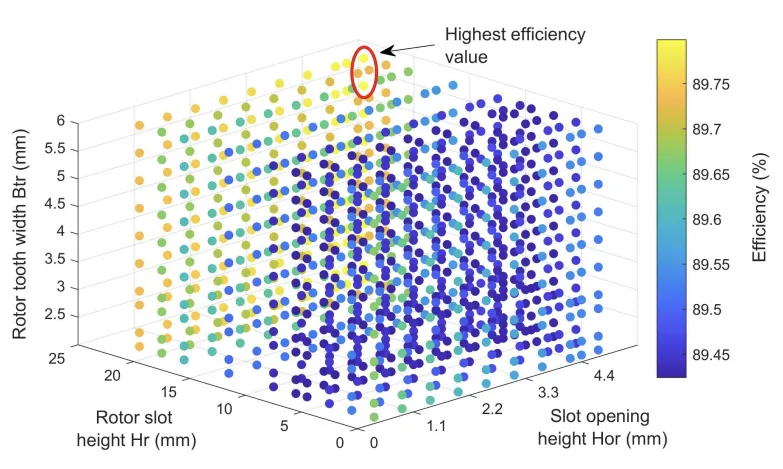
6. Key Results:
Key Results:
- Rotor Slot Height (Hr): Efficiency increases with Hr up to 22mm, achieving a maximum efficiency of 89.79%, a 0.09% improvement from the initial setting. Reducing Hr below 14mm initially decreases efficiency but rebounds due to reduced leakage reactance.
- Rotor Slot Opening Height (Hor): Efficiency slightly decreases initially and then increases to a maximum of 89.715% at Hor = 5mm, a 0.015% improvement. Hor has less impact on efficiency compared to Hr.
- Rotor Slot Tooth Width (Btr): Efficiency variation shows a different pattern, drastically dropping in the middle range of Btr. Maximum efficiency of 89.78% is achieved at Btr = 3.75mm, a 0.08% improvement.
- Combined Parameter Variation (Hr, Hor, Btr): Maximum efficiency reaches 89.8% when Hr, Hor, and Btr are set to 22mm, 5mm, and 5-5.5mm, respectively, representing a 0.1% improvement. Hr has the most significant influence on efficiency, followed by Btr.
Figure Name List:
- Fig. 6. Performance of the induction motor at initial settings
- Fig. 7. Individual variation of efficiency when changing Hr
- Fig. 8. Individual variation of efficiency when changing Hor
- Fig. 9. Individual variation of efficiency when changing Btr
- Fig. 10. 4D Scatter Plot of Efficiency when Changing All Parameters
7. Conclusion:
This paper presented an analytical approach to investigate the impact of rotor slot geometry parameters on the efficiency of squirrel cage induction motors. The study, using a MATLAB-based analytical model, examined the effects of individual and combined variations of rotor slot height (Hr), rotor slot opening height (Hor), and rotor slot tooth width (Btr). Individual parameter variations showed efficiency improvements of up to 0.09%, 0.015%, and 0.08% for Hr, Hor, and Btr, respectively. Amalgamated analysis demonstrated a maximum efficiency increase of 0.1%, reaching 89.8% with optimized parameter settings. The findings indicate that rotor slot geometry significantly influences induction motor efficiency and can be substantially improved through appropriate parameter selection. While this study focused on three parameters, future research could explore optimization approaches considering a broader range of parameters.
8. References:
- [1] A. Boglietti, A.M. Elrefaie, O. Drubel, A.M. Omekanda, N. Bianchi, E.B. Agamloh, M. Popescu, A.D. Gerlando and J.B. Bartolo. "Electrical machine topologies: Hottest topics in the electrical machine research community," IEEE Industrial Electronics Magazine, vol. 8, no. 2, pp. 18-30, 2014.
- [2] Q. Ding, Z. Yang, X. Sun, Q. Zhao and H. Zhu. "Analysis of rotor slot width influence on a bearingless induction motor," Computers and Electrical Engineering, vol. 81, pp. 1-16, 2019.
- [3] M. Sellami and S. Tounsi. "Control of axial flux DC motor with permanent magnet dedicated to electric traction," International Journal of Electrical Components and Energy Conversion, vol. 1, no. 1, pp. 44-48, 2015.
- [4] R.J. Swaraj and T. Archana. "Comparison of electric motors for electric vehicle applications," International Journal of Research in Engineering and Technology, vol. 6, no. 9, pp. 12-17, 2017.
- [5] W. Zhikun, C.T.Z.E. Wood, H. Shaojia, W. Hongtao and X. Tao. "Challenges faced by electric vehicle motors and their solutions," IEEE Access, vol. 9, pp. 5228-5249, 2020.
- [6] E. Makhetha, M. Muteba and D.V. Nicolae. "Effect of rotor bar shape and stator slot opening on the performance of three phase squirrel cage induction motors with broken rotor bars," Southern African Universities Power Engineering Conference/Robotics and Mechatronics/Pattern Recognition Association of South Africa, 2019, pp. 463-468.
- [7] K.A.I. Daut, K. Anayet, N. Gomesh, M. Asri and Y.M. Irwan. "Comparison of copper rotor bars with aluminium rotor bars using FEM software: A performance evaluation," International Conference on Computer and Electrical Engineering, 2009, pp. 453-456.
- [8] V.A. Galindo, X.M. Lopez-Fedez, J.A.D. Pinto and A.P. Coimbra. "Parametric study of rotor slot shape on a cage induction motor," International Symposium on Electromagnetic Fields in Electrical Engineering, 2002, pp. 190-195.
- [9] K.N. Gyftakis and J. Kappatou. "The impact of the rotor slot number on the behaviour of the induction motor," Advances in Power Electronics, pp. 837010, 2013.
- [10] J. Kappatou, K. Gyftakis and A. Safacas "FEM study of the rotor slot design influences on the induction machine characteristics," Advanced Computer Techniques in Applied Electromagnetics, vol. 30, pp. 247-252, 2007.
- [11] E. Maloma, M. Muteba and D. Nicolae. "Effect of rotor bar shape on the performance of three phase induction motors with broken rotor bars," International Conference on Optimization of Electrical and Electronic Equipment, 2017, pp. 364-369.
- [12] A. Leicht and K. Makowski. "Influence of shape and material of rotor bars on performance characteristics of single-phase self-excited induction generators," International Journal for Computation and Mathematics in Electrical and Electronic Engineering, vol. 38, no. 4, pp. 1235-1244, 2019.
- [13] I. Daut, K. Anayet and A. Fauzi. "Development of copper rotor of AC induction motor," Australian Journal of Basic and Applied Sciences, vol. 4, no. 12, pp. 5941-5946, 2010.
- [14] J. Singh, K. Singh and H. Kaur. "Designing of three phase squirrel cage induction motor for good efficiency," International Journal of Engineering and Innovative Technology, vol. 5, no. 7, pp. 40-45, 2016.
- [15] A.G. Yetgin, M. Turan, B. Cevher, A.İ. Çanakoğlu and A. Gün. "Squirrel cage induction motor design and the effect of specific magnetic and electrical loading coefficient," International Journal of Applied Mathematics Electronics and Computers, vol. 7, no. 1, pp. 1-8, 2019.
- [16] J.M. Apsley, S. Williamson, A.C. Smith and M. Barnes. "Induction motor performance as a function of phase number," IEE Proceedings: Electric Power Applications, vol. 153, no. 6, pp. 898-904, 2006.
- [17] M.A. Iqbal and V. Agarwal. "Investigation & analysis of three phase induction motor using finite element method for power quality improvement," International Journal of Electronic and Electrical Engineering, vol. 7, no. 9, pp. 901-908, 2014.
- [18] I. Boldea and S.A. Nasar. "The induction machines design handbook," Taylor and Francis Group, 2010.
- [19] D.J. Kim, J.H. Choi, Y.D. Chun, D.H. Koo and P.W. Han. "The study of the stray load loss and mechanical loss of three phase induction motor considering experimental results," Journal of Electrical Engineering and Technology, vol. 9, no. 1, pp. 121-126, 2014.
- [20] A. Boglietti, A. Cavagnino and M. Lazzari. "Geometrical approach to induction motor design," The 33rd Annual Conference of the IEEE Industrial Electronics Society, 2007, pp. 149-156.
9. Copyright:
- This material is a paper by "Ahamed Ibrahim Sithy Juhaniya, Ahmad Asrul Ibrahim, Muhammad Ammirrul Atiqi Mohd Zainuri, Mohd Asyraf Zulkifley". Based on "An Analytical Model of Induction Motors for Rotor Slot Parametric Design Performance Evaluation".
- Source of the paper: https://doi.org/10.5430/ijacsa.v13n12p883
This material is summarized based on the above paper, and unauthorized use for commercial purposes is prohibited.
Copyright © 2025 CASTMAN. All rights reserved.