This introductory paper is the research content of the paper "Numerical and experimental analysis of a high pressure die casting Aluminum suspension cross beam for light commercial vehicles" published by La Metallurgia Italiana.
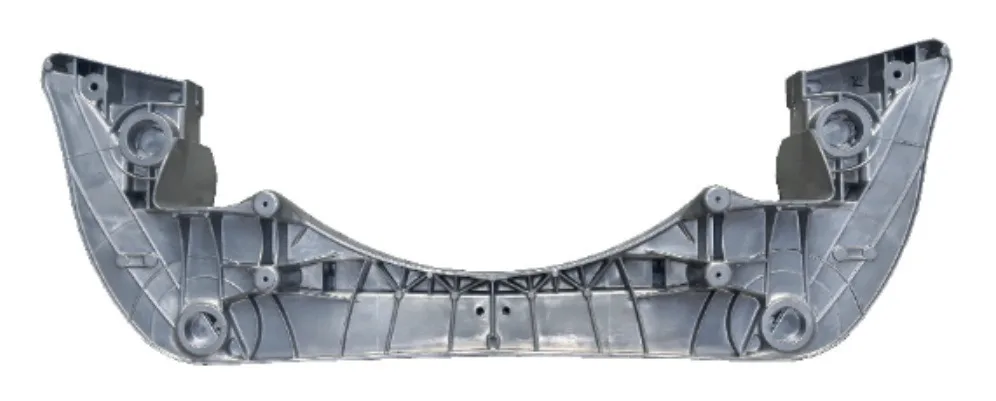
1. Overview:
- Title: Numerical and experimental analysis of a high pressure die casting Aluminum suspension cross beam for light commercial vehicles
- Author: S. Cecchel, D. Ferrario
- Publication Year: 2016
- Published Journal/Society: La Metallurgia Italiana
- Keywords: ALUMINUM - HIGH PRESSURE DIE CASTING - SUSPENSION - CROSS BEAM - COMMERCIAL VEHICLE - LIGHTWEIGHT - AUTOMOTIVE
2. Abstract
The purpose of the present paper is to enhance and deepen the lightweight optimization in automotive, in particular for commercial vehicles and buses. In detail, aim of this research is to develop a technically reliable and cost effective safety component for Light Commercial Vehicles (LCVs) in aluminum alloy. Different solutions of Aluminium Cross beams for an independent front suspension for LCVs have been analyzed, with a weight saving target in comparison with the traditional welded sheet metal structure of almost 40/50%. Moreover, further environmental advantages have to be considered; for instance improved corrosion resistance, no painting or cataphoresis required, benefits on recyclability and residual value at the end of life. The goal of this project has been achieved through: technical and economical study of some different lightweighting solution and selection of the best case; improvement of the solution selected with the help of structural FEA and casting process simulations, a Life Cycle Assessment from cradle to grave (not here described), prototypes realization and preliminary experimental correlation.
3. Research Background:
Background of the research topic:
Vehicle weight decrease is a remarkable method to moderate the automotive carbon footprint, by reducing fuel consumptions and environmental emissions. Furthermore, the lightweighting improves power to weight ratio and passenger safety and allows an increase of the payload [1].
Status of previous research:
In the last years the lightweighting design in automotive has exponentially increased. Although, the use of “steel” and “iron” is still pre-dominant for commercial vehicles and buses especially for safety relevant components [2]. Suspension cross beam for commercial vehicles is usually made with metal sheet parts or steel tubes welded together and protected to avoid corrosion. The main technological trends are looking to alternative materials such as Advanced High Strength Steel, light alloys or composites.
Need for research:
Even if light alloys and composites would offer the best weight benefit, the use of these technologies in LCVs is limited both for the necessity of high-er stress at break and stiffness, both for cost limits. In particular, at the current known state of the art none suspension cross beam in aluminum has never developed in this range of vehicles.
4. Research purpose and research question:
Research purpose:
To overcome this state of the art by developing a technically reliable and cost effective safety relevant suspension component for Light Commercial Vehicles (LCVs) in aluminum alloy. To evaluate the element that gives the higher lightweighting benefit a preliminary benchmark on a complete suspension assembly has been performed, outlining the object of the study in a suspension cross beam element.
Core research:
With the purpose to overcome these limits, during the present work the shape and the production technology of the studied component have been completely devised by optimizing the me-chanical properties and by reducing the material used.
5. Research methodology
Different suspension cross beam lightweighting solutions have been developed (Fig. 1). In detail, materials, processes, technologies and business case have been analyzed for each solution and preliminary finite element analyses (structural MSC/MarcMentat and process ESI PROCAST) have been conducted. An elastokinematic multi-body model of the suspension system has been defined and performed in MSC/AdamsCar in order to determine the forces of the main load set conditions. These loads have been used as inputs for the structural FEA performed in MSC Marc/Mentat and the results compared with the outputs of the ESI/PROCAST process FEA. The dies have been manufactured and some prototypes have been casted (Fig. 3). The finite element analyses conducted during the design have been useful for the manufacturing of the dies (i.e. local cooling, squeeze, chill-vents, gate injection, etc. ) and for the definition of the initial process parameters. Castings have been analyzed through a proper X-ray machine and with a 3D scanner device in order to identify the macro-defect (porosity and deformation).
6. Key research results:
Key research results and presented data analysis:
The comparison of the different analyses' results has led to the conclusion that the solution with the most lightweight and economic potential was high pressure die casting aluminum. The feasibility of this solution has been achieved by the use of proper materials and by a new concept of design that allowed to overcome the structural limits. The alloy selected for the production has been AlSi9MgMn (Tab. 1), that guarantees as-cast elevated mechanical properties (Tab.1). A completely hollow structure obtained through the addition of sliders for the total length of the component (Fig. 2). Sliders are a technology widely used to avoid undercuts but are not applied for the manufacturing of hollow structural components, especially in the field of LCVs. This solution leads to a component stiffness improvement - in the direction of the main vertical load - of about 40% in comparison with the steel baseline.
This component's manufacturing requests a high tonnage (at least 3000 t) vacuum machine.
Sequence of steps brought to an increased lightweighting (from the initial 35% to 47%) of the suspension cross beam.
The X-ray results confirmed the presence of some porosities in the thickest sections, already evaluated during FEM simulations (Fig. 4).
Porosities have been minimized and a correct hard points' alignment has been reached.


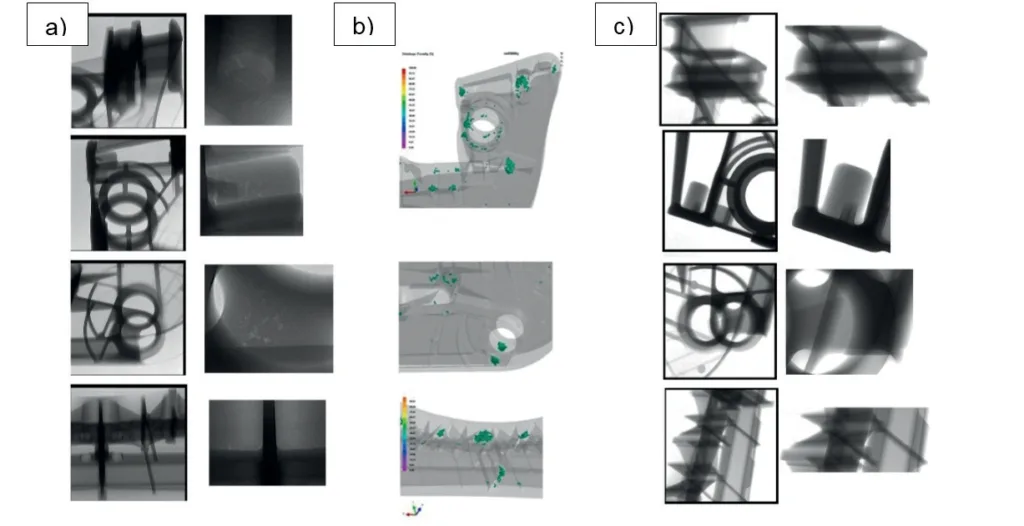
List of figure names:
- Fig. 1 - Cross beams: -1) HPDC aluminum, 2) LPDC and extruded aluminum, 3) LPDC and CFRP, 4) Extruded aluminum
- Tab. 1 - Chemical composition AlSi9MgMn (left) [5], Mechanical properties AlSi9MgMn (right)[5]
- Fig. 2 - a) Sliders layout b) Cross beam hollowed longitudinal section c) remarkable hollow sections
- Fig. 3 - Dies and prototypes
- Fig. 4 - Porosity identify by a) X-ray on components from the first experimental activity, b) FEM simulations, c) X-ray on components from the final experimental activity (optimization of process parameters)
7. Conclusion:
Summary of key findings:
The paper enhances the lightweight optimization for commercial vehicles developing a technically reliable and cost effective safety component for Light Commercial Vehicles (LCVs) in aluminum alloy. The best solution is in a high pressure die casting aluminum component. The shape and the technology production of the studied component have been completely devised by optimizing the mechanical properties and by reducing the material used. The design have been enhanced thanks to further iterations of structural and process finite element analyses. A proper component resistance has been achieved by the selection of a primary AlSi9MgMn alloy and by the substitution of the traditional high pressure die casting plane or “U” shape with a completely hollow structure obtained through the addition of sliders for the total length of the component.
Summary of research results. Academic significance of the research, practical implications of the research
The manufacturing of the prototypes has been performed on a high tonnage (at least 3000 t) vacuum machine as a result of the remarkable dimensions of casting (about 1260x450 mm) and sliders (approximately equal to the piece), and the die (about double of the piece).
Porosities have been minimized and a correct hard points' alignment has been reached thanks to some die modification and a careful iterative selection of the proper process parameters.
8. References:
- [1] J. HIRSCH, Materials forum volume 28, (2004), p 15.
- [2] S.DAS, JOM, 8, (2000), p.41-44.
- [3] L. KALLIEN, T. WEIDLER, M. BECKER, International found-ry research, 4, (2014), p. 20-27.
- [4] R.MOSCHINI, R.MOLINA, XXXI Congresso tecnico di fon-deria ASSOFOND, (2012).
- [5] RHEINFELDEN, Leghe d'alluminio da pressocolata.
9. Copyright:
- This material is a paper by "S. Cecchel, D. Ferrario": Based on "Numerical and experimental analysis of a high pressure die casting Aluminum suspension cross beam for light commercial vehicles".
- Source of paper: La Metallurgia Italiana - n. 6 2016
This material was created to introduce the above paper, and unauthorized use for commercial purposes is prohibited. Copyright © 2025 CASTMAN. All rights reserved.