This introductory paper is the research content of the paper "Aluminum Alloys for Structural Die Casting" published by DIE CASTING ENGINEER.

1. Overview:
- Title: Aluminum Alloys for Structural Die Casting
- Author: Martin Hartlieb
- Publication Year: 2013
- Published Journal/Society: DIE CASTING ENGINEER (May 2013)
- Keywords: Structural die casting, Aluminum alloys, Silafont-36, Aural, Mercalloy, Magsimal-59, die soldering, Fe needles, mechanical properties, elongation.
2. Abstract
The number of projects and applications for structural die casting using special alloys and sophisticated process technologies is increasing exponentially. These structural die castings are often large, thin-walled (Figure 1), heat-treatable, welded, or joined, requiring high impact, fatigue strength, and corrosion resistance. Traditional die casting alloys, with high iron (Fe) content to prevent die soldering, struggle to achieve the necessary mechanical properties. Low-Fe alloys, utilizing Mn and Sr, have been developed to address this.
3. Research Background:
Background of the research topic:
Structural die castings are increasingly used in automotive and other industries, requiring high mechanical properties, especially elongation, and often need to be heat treatable, weldable, and corrosion-resistant.
Status of previous research:
Traditional die casting alloys rely on high Fe to prevent die soldering, but this compromises mechanical properties. Rheinfelden developed Silafont™-36 (AA 365) with low Fe (0.15% max) and replaced it with Mn (0.5-0.8%). Alcoa, Alusuisse/Alcan, and Pechiney developed similar alloys. Mercury Marine used Sr in their Mercalloy™ series to reduce Mn content.
Need for research:
There is a need to understand the properties and applications of specialized low-Fe alloys for structural die casting, and how elements like Mn and Sr mitigate the negative effects of Fe, improving ductility and feeding behavior.
4. Research purpose and research question:
Research purpose:
To summarize the state of knowledge regarding aluminum alloys used in structural die casting, focusing on alloy composition, properties, and industry perceptions.
Core research:
- What are the key characteristics of structural die castings and the alloys used to produce them?
- What is the industry's understanding and perception of these alloys?
5. Research methodology
- Research Design: Mixed-methods approach.
- Data Collection:
- Literature review of existing alloys and their properties.
- NADCA online survey (over 150 participants).
- Personal interviews with industry experts (a few dozen).
- Analysis Method: Descriptive statistics of survey responses, qualitative analysis of interview data.
- Research Scope: Primarily focused on North American die casters and OEMs, with some input from European experts.
6. Key research results:
Key research results and presented data analysis:
- Two main alloy families: Al-Si-Mg (e.g., Silafont™-36, Aural™, Mercalloy™) and Al-Mg(-Si) (e.g., Magsimal™-59).
- Al-Si-Mg alloys are more popular, especially in North America.
- Mn and Sr are used to replace Fe for die soldering resistance, reducing the negative impact of Fe needles (Figure 2).
- Industry awareness of these alloys and their properties is varied.
- About 2/3 aware of special alloys for structural applications.
- 43% had requests for structural die castings.
- Varying levels of understanding regarding the roles of Fe, Mn, and Sr.
- Mercalloy™ is the best-known alloy, followed by Silafont™-36.
- Alloy preference varies, with Silafont™-36 often being the first choice.
- Availability and cost are important considerations.
- Mechanical properties (especially from representative castings) are the most desired data from alloy suppliers.
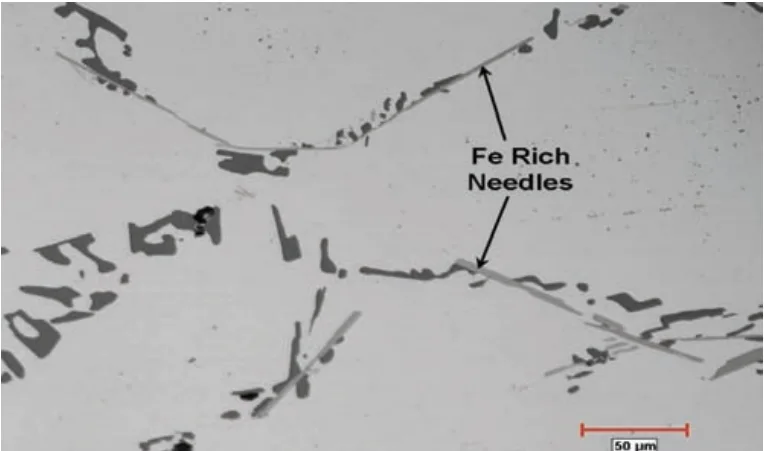
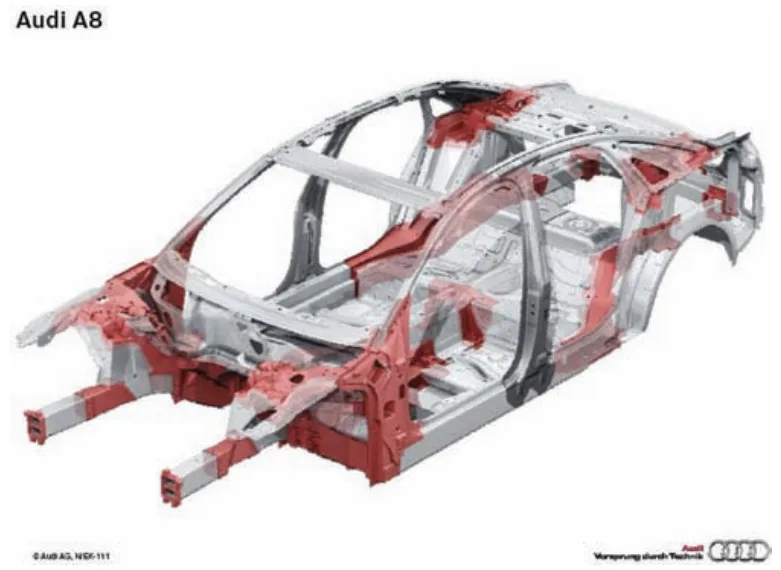
List of figure names:
- Figure 1 – BMW X5 Shock tower cast by Albany Chicago in Aural-2 alloy.
- Figure 2 – AlFeSi needle-like phase.
- Figure 3 - Al Space Frame showing structural die castings in red.
7. Conclusion:
Summary of key findings:
Structural die casting is a growing market, driven by the automotive industry's need for lightweight, high-strength components. Specialized low-Fe aluminum alloys, utilizing Mn and Sr, are crucial for achieving the required properties. While industry knowledge is growing, there are still gaps in understanding and awareness of specific alloy characteristics and preferences.
- Academic significance of the research: The research provides a comprehensive overview of the current state of structural die casting alloys, highlighting the importance of alloy composition and industry perceptions.
- Practical implications of the research: The findings can inform die casters and OEMs about alloy selection, process optimization, and the need for further education and research in this area.
8. References:
- The paper does not contain a dedicated reference list. However, it mentions several alloy developers and their products:
- Rheinfelden (Silafont™-36, Castasil™-37, Magsimal™-59)
- Alcoa (C601/611, Aural™-2/3/5)
- Mercury Marine (Mercalloy™ 367, 368, 362)
- Pechiney (Calypso™ 43 and 54SM)
- Ryobi (W3 alloy, ADC3SF)
9. Copyright:
- This material is a paper by "Martin Hartlieb": Based on "Aluminum Alloys for Structural Die Casting".
- Source of paper: www.diecasting.org/dce (The original URL is provided, but a specific DOI is not given in the document.)
This material was created to introduce the above paper, and unauthorized use for commercial purposes is prohibited. Copyright © 2025 CASTMAN. All rights reserved.