This introductory paper is the research content of the paper ["Predicting Die Cracking in Die-Cast Products Using a Surrogate Model Based on Geometrical Features"] published by [Computer-Aided Design & Applications]
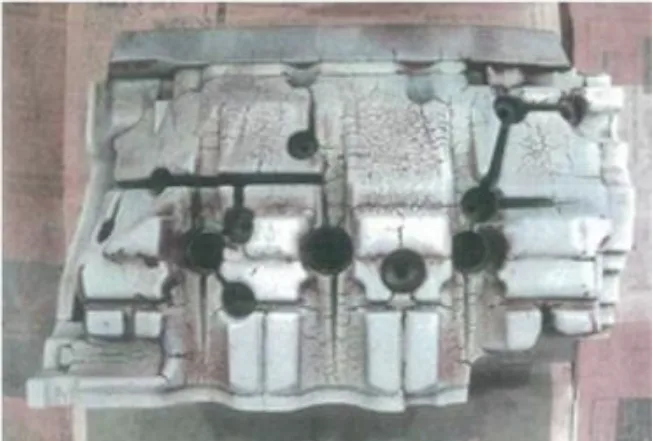
1. Overview:
- Title: Predicting Die Cracking in Die-Cast Products Using a Surrogate Model Based on Geometrical Features
- Author: Tomoya Yamazaki, Koh Hirokawa, Akira Murakami, Misato Baba, and Chisako Muramatsu
- Publication Year: 2025
- Publishing Journal/Academic Society: Computer-Aided Design & Applications, 22(2), 2025, 217-228
- Keywords: Die casting, Surrogate model, VAE, Neural network, Computer-aided design, die cracking, geometrical features, automotive industry, machine learning, defect prediction, 3D shape data
2. Abstracts or Introduction
This paper explores the development and application of a surrogate model for predicting die cracks in die-cast products, focusing on the geometrical features of the product design. Die casting is highlighted for its efficiency in mass-producing complex shapes, especially in the automotive industry for vehicle weight and part count reduction. The paper addresses the challenges of ensuring product quality and minimizing development lead time, which are exacerbated by difficulties in predicting defects in complex shapes at the product design stage. Traditional simulation technologies are noted as limited by long preparation and execution times, leading to a shift towards big data and machine learning for efficient defect prediction. This study introduces a novel surrogate model employing Variational Autoencoders (VAEs) and neural networks to predict die crack occurrence. The model, analyzing engine block parts and transaxle cases from Toyota Motor Corporation, demonstrates promising results in predicting die cracks with high accuracy, suggesting a new direction for improving die-casting processes by leveraging product shape data for early defect detection.
3. Research Background:
Background of the Research Topic:
Die casting is widely utilized in industrial production, particularly in the automotive industry, for mass-producing complex shapes at high speed, contributing to vehicle weight reduction and part count reduction. Shortening product development lead time is crucial for competitiveness. The automotive industry's product development process typically follows a flow from "Product design" to "Die design," "Productivity simulation," "Process design," "Functional evaluation," and finally "Mass production." This process is iterative, but as it progresses, specifications become more complex, increasing rework. Early, accurate defect prediction is essential to minimize rework and shorten lead times. "Pre-prediction," a preliminary estimation of potential defects in early design stages, is critical, differing from detailed predictions in later phases. Accurate pre-predictions for complex shapes are challenging, and inaccuracies can lead to rework.
Status of Existing Research:
Simulation technology is a standard technique in industrial product development for predicting functionality and rectifying issues before manufacturing. Casting simulation traditionally focused on fluid analysis but now incorporates ambient air compression calculations. Research is ongoing to reduce computation time using quantum computers. However, even with advancements in simulation accuracy and speed, preparing die model information for simulation is time-consuming, taking several days even with revisions, thus only partially solving the problem of long preliminary examination time.
Necessity of the Research:
Given the limitations of simulation technology, an alternative approach using big data from past defect occurrences and simulation results for pattern recognition is being pursued. Surrogate modeling, employing machine learning to predict using known data instead of detailed simulations, is gaining traction for reducing computation costs and pre-required information. While surrogate models show promise, many reported cases simplify problems to two dimensions, and their applicability to complex 3D shapes and defect prediction in casting based on geometric information is not well-established. Demonstrating the feasibility of surrogate models for defect prediction in die casting based on product geometry would significantly impact industrial product development.
4. Research Purpose and Research Questions:
Research Purpose:
This research aims to develop and validate a surrogate model for predicting die cracking in die-cast products, utilizing geometrical features of the product design. The goal is to enhance early defect detection and improve the efficiency of the die-casting process by leveraging product shape data.
Key Research:
- Development of a novel surrogate model employing Variational Autoencoders (VAEs) and neural networks for die crack prediction.
- Evaluation of the model's accuracy in predicting die cracks in engine block parts and transaxle cases from Toyota Motor Corporation, using geometrical features.
- Investigation of the effectiveness of using product shape data for early defect detection in die casting.
- Analysis of the model's performance using F1 score and comparison with previous surrogate models for die soldering.
5. Research Methodology
Research Design:
The research employs a quantitative approach, developing and evaluating a surrogate model for die crack prediction. The model is built using VAEs and neural networks, trained on a dataset of engine block parts and transaxle cases. The model's predictive performance is assessed by comparing its predictions with CAE analysis results.
Data Collection Method:
The data consists of 3D CAD models of 113 engine block parts and 130 trans axle cases produced by Toyota Motor Corporation. Simulation results of maximum compressive strain, calculated using the Adventure cluster by SCSK Corporation, are used as the target variable for die crack prediction. The CAD models are converted into voxel-based models for feature extraction.
Analysis Method:
- Surrogate Model Construction: A VAE is trained to extract feature vectors from cubic shapes cut from the surface of voxelized 3D models. A neural network is then trained to predict simulation results (maximum compressive strain) from these feature vectors.
- Model Evaluation: The F1 score is used as the evaluation metric. Predicted and CAE analysis results are compared by defining regions with values above a threshold as defect regions. The F1 score is calculated based on the overlap between predicted and actual defect regions. Bootstrap method is used to compare the performance with a previous surrogate model for die soldering.
Research Subjects and Scope:
The research focuses on predicting die cracking in engine block parts and transaxle cases produced by Toyota Motor Corporation using die casting. The geometrical features of these parts are the primary input for the surrogate model. The scope is limited to die cracking caused by thermal stress, specifically low-cycle fatigue.
6. Main Research Results:
Key Research Results:
- A surrogate model for predicting die cracking in die-cast products was successfully developed using VAEs and neural networks, based on geometrical features.
- The model demonstrated promising results in predicting die cracks in engine block parts and transaxle cases from Toyota Motor Corporation.
- For engine block parts, the model achieved an F1 score of approximately 0.62, with 594 True Positives (TP), 208 False Negatives (FN), and 530 False Positives (FP).
- For transaxle case models, the F1 score was approximately 0.58, with 174 TPs, 73 FNs, and 178 FPs.
- The performance of the die crack prediction model is comparable to that of a previously developed surrogate model for die soldering.
Analysis of presented data:
- Figure 6: Shows the training curves for the VAE and neural networks, indicating appropriate training progression for both engine block and transaxle case models.
- Figure 7: Illustrates the transition of F1 score as the decision threshold varies, showing that a relatively high F1 score is achievable for both models.
- Figure 8: Presents the bootstrap distribution of F1 score difference, suggesting that the die crack prediction model achieves a similar level of predictive accuracy as the die soldering model.
- Figure 9: Shows the trend of F1 score with increasing number of models, indicating that accuracy improvement saturates with larger datasets, suggesting the need for architectural changes rather than just more data.
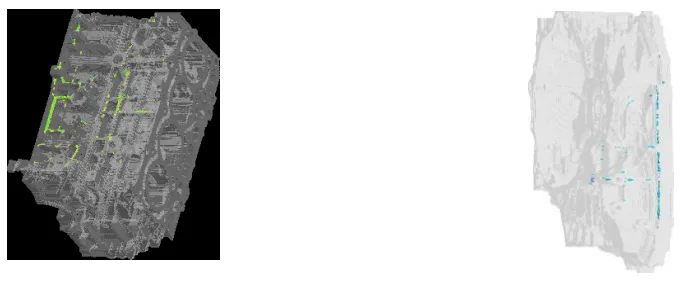
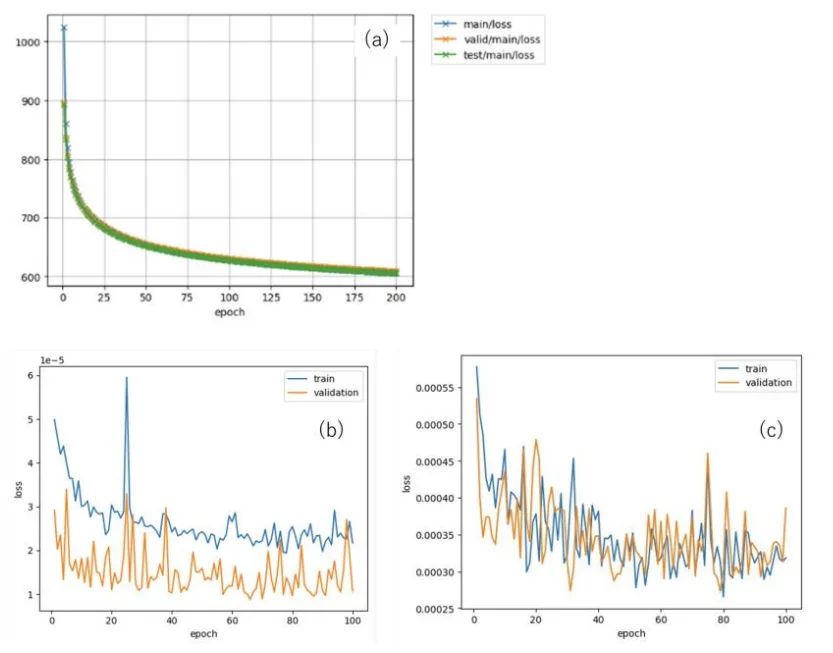
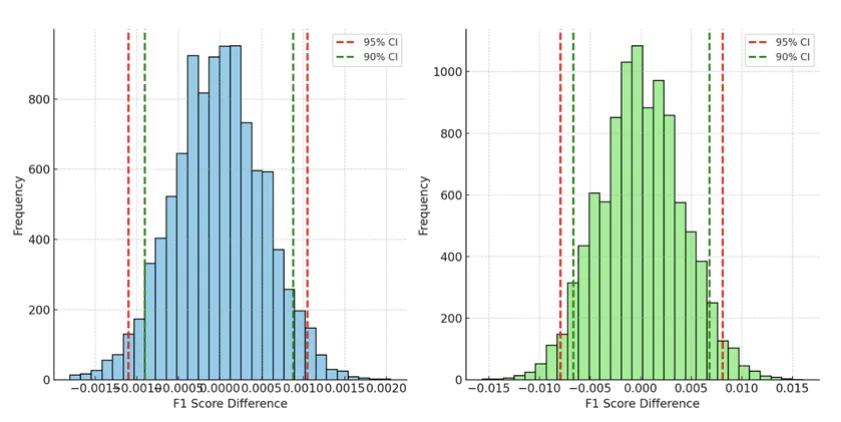
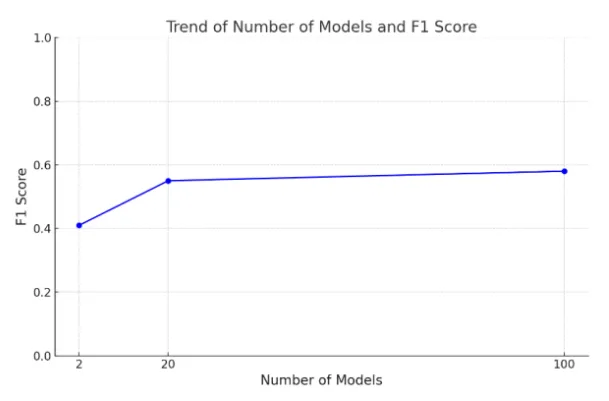
Figure Name List:
- Figure 1: Image of Die in the actual die-casting process, which has cracks (red lines) on the surface.
- Figure 2: Image of product shape (a)Engine block, (b)Trans axel case.
- Figure 3: Image of constructing the surrogate model.
- Figure 4: Image of evaluation method.
- Figure 5: Architecture of VAE and neural network.
- Figure 6: Train curve of a) VAE, b) Neural network for the engine block, and (c)Trans axel case.
- Figure 7: Transition of F1 score of a) Engine block's surrogate model and b) Trans axel case's surrogate model.
- Figure 8: Bootstrap distribution of F1 score difference between (a) Engine model and referenced model, and (b)Trans axel case model and referenced model.
- Figure 9: Trends of the Number of Engine block models and F1 score
- Figure 10: Example of (a) rule-based prediction and (b) actual die model.
- Figure 11: Die architecture of the pertinent part
7. Conclusion:
Summary of Key Findings:
This study successfully constructed a surrogate model using VAE and NN to predict die cracking in die-cast dies based on product shape, achieving a certain level of accuracy. The model leverages geometrical features and demonstrates comparable performance to a prior model for die soldering prediction. However, the model exhibits limitations in accurately predicting cracks in areas with complex internal features like cooling circuits, leading to false positives. Accuracy improvements from increased data volume appear to saturate, suggesting the need for more sophisticated model architectures or incorporating additional factors beyond surface shape.
Academic Significance of the Study:
This research contributes to the field by demonstrating the feasibility of using surrogate models based on geometrical features for predicting die cracking, a critical defect in die casting. It introduces a novel approach using VAEs and neural networks for this purpose and provides a benchmark for predictive accuracy using shape data. The study highlights the potential and limitations of shape-based defect prediction in die casting, paving the way for further research in this area.
Practical Implications:
The developed surrogate model offers a faster and more efficient method for early defect prediction in die casting compared to traditional simulation techniques. By leveraging product shape data, it can assist engineers in identifying potential die cracking risks during the early design stages, enabling proactive design modifications to enhance product quality and reduce development lead time and costs.
Limitations of the Study and Areas for Future Research:
The model's accuracy is limited by its reliance solely on surface shape data, neglecting internal die features like cooling circuits which significantly influence thermal stress and cracking. The occurrence of false positives, particularly in areas with hidden design elements, indicates this limitation. Future research should focus on incorporating more multifaceted factors, such as cooling circuit arrangements and temperature distribution within the die, into the model to improve prediction accuracy and reduce false positives. Exploring fundamental changes in the learning architecture and optimizing model learning data are also suggested for further accuracy enhancement.
8. References:
- [1] Czerwinski, F.: Current Trends in Automotive Lightweighting Strategies and Materials, Materials, 14(6631), 2024. http://doi.org/10.3390/ma14216631
- [2] Pahl, G.; Beitz, W.; Feldhusen, J.; Grote, K.-H.: Engineering Design: A Systematic Approach (3rd ed., Wallace, K.; Blessing, L., Trans. & Eds.), Springer, 2007.
- [3] Morgan, J. M.; Liker, J. K.: The Toyota Product Development System, Productivity Press, New York, NY, 2006.
- [4] Khalilpourazary, S.; Dadvand, A.; Azdast, T.; Sadeghi, M. H.: Design and manufacturing of a straight bevel gear in hot precision forging process using finite volume method and CAD/CAE technology, International Journal of Advanced Manufacturing Technology, 56, 87-95. http://doi.org/10.1007/s00170-011-3159-z
- [5] Kwon, H.-J.; Kwon, H.-K.: Computer-aided engineering (CAE) simulation for the design optimization of gate system on high pressure die casting (HPDC) process, Robotics and Computer-Integrated Manufacturing, 55(Part B), 2019, 147-153. http://doi.org/10.1016/j.rcim.2018.01.003
- [6] Liu, J.; Ma, Y.; Fu, J.; Duke, K.: A novel CACD/CAD/CAE integrated design framework for fiber-reinforced plastic parts, Advances in Engineering Software, 87, 2015, 13-29. http://doi.org/10.1016/j.advengsoft.2015.04.013
- [7] Matsushita, S.; Aoki, T.: Gas-liquid two-phase flows simulation based on a weakly compressible scheme with interface-adapted AMR method, 2021.
- [8] Gaitan, F.: Finding Solutions of the Navier-Stokes Equations through Quantum Computing—Recent Progress, a Generalization, and Next Steps Forward, 2021.
- [9] Fei, T.; Jiangfeng, C.; Qinglin, Q.; Meng, Z.; He, Z.; Fangyuan, S.: Digital twin-driven product design, manufacturing and service with big data, International Journal of Advanced Manufacturing Technology, 94, 2018, 3563-3576.
- [10] Hemmasian, A. P.; Ogoke, F.; Akbari, P.; Malen, J.; Beuth, J.; Barati Farimani, A.: Surrogate Modeling of Melt Pool Temperature Field using Deep Learning, Additive Manufacturing Letters, 5, 2023
- [11] Paulete-Periáñez, C.; Andrés-Pérez, E.; Lozano, C.: Surrogate modelling for aerodynamic coefficients prediction in aeronautical configurations, Proceedings of the 8th European Conference for Aeronautics and Space Sciences (EUCASS), http://doi.org/10.13009/EUCASS2019-870.
- [12] Yamazaki, T.; Hirokawa, K.; Murakami, A.; Baba, M.; Muramatsu, C.: Predicting Soldering Failure in Die-Cast Products Using a Surrogate Model Based on Geometrical Features, CAD Journal, 21(4), 2024, 581-590. http://www.cad-journal.net/files/vol_21/CAD_21(4)_2024_581-590.pdf
- [13] Brock, A.; Lim, T.; Ritchie, J. M.; Weston, N.: Generative and Discriminative Voxel Modeling with Convolutional Neural Networks, arXiv preprint arXiv:1608.04236.
- [14] Klobčar, D.; Tušek, J.; Taljat, B.: Thermal fatigue of materials for die-casting tooling, Materials Science and Engineering: A, 472(1-2), 2008, 198-207. http://doi.org/10.1016/j.msea.2007.03.025
- [15] ADVENTURE PROJECT Seminar Materials: Material and Geometric Nonlinear Algorithms (ADV_Solid), Presented on May 15, 2001, University of Tokyo. Retrieved from: https://adventure.sys.t.u-tokyo.ac.jp/jp/pub/seminar20010515/adv_seminar_solver_algo/index.htm
- [16] Roger, L.: An Introduction to the Boostrap, 2021.
- [17] Namiki, K.; Kawano, M.; Schade, T.: High Thermal Conductivity Steel and its Application to Die Casting Tools, NADCA Die Casting Congress & Exposition, Transaction No. T12-071, 2012.
- [18] Morris Jr, J. W.; Guo, Z.; Krenn, C. R.; Kim, Y.-H.: The Limits of Strength and Toughness in Steel, ISIJ International, 41(6), 2001, 599-611.
9. Copyright:
- This material is "Tomoya Yamazaki"'s paper: Based on "Predicting Die Cracking in Die-Cast Products Using a Surrogate Model Based on Geometrical Features".
- Paper Source: https://doi.org/10.14733/cadaps.2025.217-228
This material was created to introduce the above paper, and unauthorized use for commercial purposes is prohibited.
Copyright © 2025 CASTMAN. All rights reserved.