This introductory paper is the research content of the paper ["Use of Duplex PVD Coatings to Increase the Life of Moulds and Cores for die Casting of Aluminium Alloys in the Automotive Industry"] published by [Acta Mechanica Slovaca].
1. Overview:
- Title: Use of Duplex PVD Coatings to Increase the Life of Moulds and Cores for die Casting of Aluminium Alloys in the Automotive Industry
- Author: Janette Brezinová, Ján Viňáš, Miroslav Džupon, Dagmar Jakubeczyová, Jakub Brezina, Henrich Sailer, Ján Hašuľ, Michal Považan
- Publication Year: 2022
- Publishing Journal/Academic Society: Acta Mechanica Slovaca
- Keywords: PVD coatings, laser surface remelting, die casting of aluminium, tribology
![Table 1: Chemical composition of Uddeholm Dievar [15]](https://castman.co.kr/wp-content/uploads/image-1323-png.webp)
![Table 2: Mechanical properties of Uddeholm Dievar [15]](https://castman.co.kr/wp-content/uploads/image-1324-png.webp)
2. Abstracts or Introduction
This paper elucidates research outcomes aimed at enhancing the longevity of moulds and cores employed in high-pressure aluminium die casting, specifically for automotive industry components. The methodology involved applying local impulse heating to the surface of Uddeholm Dievar mould steel, utilizing three distinct heating rates. Post-surface treatment, structural analysis was conducted, followed by the application of a PVD nACRo³ coating via Larc technology. Coating quality assessment was performed using Scratch and Mercedes tests. Surface microgeometry, subsequent to laser treatment and nACRo³ coating application, was evaluated according to ISO 25 178. The coated surface was then subjected to immersion in an Al–Si-based alloy melt at 680 ± 20°C for durations of 120 and 300 minutes. Experimental findings substantiated a significant augmentation in the resistance of the mould surface.
The introduction underscores the paramount importance of aluminium and plastic castings in the automotive sector, predominantly manufactured using metal moulds for die casting and injection moulding. Die casting moulds, typically composed of chrome or tool steel and heat-treated to a hardness range of 29-48 HRC, are critical components whose lifespan significantly impacts mass production productivity. Mould damage, varying with application, commonly manifests as thermal fatigue cracking, often observed as networks of fine cracks or distinct cracks on the tool surface. Thermal fatigue crack formation leads to surface material loss in small fragments. Other damage mechanisms include tensile cracks from structural notches, local alloy adhesion (soldering), and steel erosion. While plastic injection moulds operate at lower temperatures, they endure more demanding pressure cycles, predisposing them to mechanical fatigue and overload failures [1]. Mould parts and cores for aluminium alloy casting necessitate suitable physical and mechanical properties at elevated temperatures, defined by thermal and mechanical stress and interface interactions with the aluminium melt. High rates of turbulent mould cavity filling with aluminium melt, coupled with hydrodynamic pressures and elevated surface temperatures, curtail mould and core life. These phenomena induce surface degradation through erosion, abrasion, corrosion, and thermal fatigue, acting concurrently.
3. Research Background:
Background of the Research Topic:
Aluminium and plastic castings are pivotal in the automotive industry, primarily produced via die casting and injection moulding using metal moulds. Die casting moulds, typically made of chrome or tool steel and heat-treated to 29-48 HRC, face substantial challenges impacting their lifespan and production efficiency. Mould life is a critical factor in die casting productivity, strongly influenced by various types of mould damage depending on the casting or mould application. Thermal fatigue cracking is a prevalent failure mode, manifesting as networks of fine cracks or individual cracks on the tool surface, leading to material loss. Additional damage causes include tensile cracks from structural irregularities, soldering (local adhesion of casting alloy), and steel erosion. These degradation mechanisms are exacerbated by high hydrodynamic pressures and temperatures during aluminium melt injection, leading to erosion, abrasion, corrosion, and thermal fatigue [2].
Status of Existing Research:
Current industrial practices emphasize surface protection and treatment of tools and machine parts. However, advancements in final surface finishing methods are lagging. Research and development in final surface treatment methods are primarily concentrated in academic and specialized laboratories [6]. Progressive surface finishing technologies are being developed to achieve enhanced properties and enable new applications. Surface pretreatment is crucial for ensuring proper coating deposition and achieving desired service life and durability [7]. Wear in pressure die casting tools and moulds is mainly attributed to thermal fatigue, abrasive, erosive, and corrosive actions of molten metal on mould functional surfaces, resulting in surface morphology changes and melt sticking [8].
Necessity of the Research:
A potential solution to mitigate mould surface degradation involves surface treatment of parts in contact with molten aluminium. Due to harsh casting conditions (thermal and chemical actions), mould surfaces are prone to damage, making mould life a critical concern. Laser hardening of thermally treated tools, followed by PVD coating deposition, is a promising approach to enhance resistance. This method leverages laser pretreatment to achieve better surface adhesive properties before coating [9]. The automotive industry in the Slovak Republic, a significant part of European car production, is strategically focused on lighter, more economical, and greener vehicles. Replacing steel parts with light metal alloys, particularly aluminium castings produced via cost-effective die-casting technology [10], is a key strategy. Optimizing die casting technology, including alloy properties, mould design, and operational parameters, is crucial for production efficiency and casting quality. Mould design and technological life are decisive factors, limited by casting quality requirements and technological parameter tolerances [11].
4. Research Purpose and Research Questions:
Research Purpose:
The primary research purpose is to increase the service life of moulds and cores used in high-pressure die casting of aluminium alloys for the automotive industry. This is achieved through the application of duplex PVD coatings in conjunction with laser surface remelting techniques.
Key Research:
The key research focuses on evaluating the effectiveness of duplex PVD coatings, specifically AIXN³ and nACRo³, on laser-treated Uddeholm Dievar steel surfaces. The study investigates the enhancement of mould surface resistance to degradation mechanisms prevalent in aluminium die casting, such as thermal fatigue, erosion, and abrasion. The research also aims to characterize the adhesion and microgeometry of the applied coatings and their performance under simulated die casting conditions.
5. Research Methodology
Research Design:
The research employs an experimental design involving surface treatment of Uddeholm Dievar steel samples using local intensive laser heating, followed by the deposition of duplex PVD coatings (AIXN³ and nACRo³) using Larc technology. Control samples without laser treatment were also prepared. The treated and coated samples were then subjected to various evaluation methods to assess coating quality and surface properties. These methods include Scratch tests, Mercedes tests, surface microgeometry analysis according to ISO 25 178, and immersion in molten Al-Si alloy to simulate die casting conditions.
Data Collection Method:
Data was collected through several experimental techniques:
- Scratch test and Mercedes test: To evaluate the adhesive-cohesive behavior of the coatings. The Mercedes test, using a Rockwell indenter at 1500 N load, was evaluated according to DIN EN ISO 18265 and categorized using adhesion numbers HF1 to HF6 [19].
- Surface microgeometry analysis: Evaluated according to ISO 25 178 standards to quantify surface roughness and topography parameters after laser treatment and coating.
- Immersion test: Samples were immersed in Al-Si alloy melt at 680 ± 20°C for 120 and 300 minutes to assess coating resistance to molten metal attack.
- Microscopy (Light and SEM): Used for visual inspection of surface defects, coating cross-sections, and indentation morphology.
- EDX microanalysis: To determine local chemical composition.
- Microhardness testing: To evaluate hardness profiles across the coating and substrate.
- Capillary test: To identify surface and subsurface defects on worn mould inserts.
Analysis Method:
- Qualitative analysis: Visual inspection and microscopic examination of surface defects, crack propagation, and coating integrity. Evaluation of Mercedes test imprints based on HF scale.
- Quantitative analysis: Measurement of scratch test critical loads, surface roughness parameters (Sa, Sq, Ssk, Sku, Sp, Sv, Sz) from ISO 25 178 analysis, and microhardness values. Statistical analysis of surface parameter data to compare different treatment conditions.
- Comparative analysis: Comparison of results between AIXN³ and nACRo³ coatings, and between laser-treated and non-laser-treated samples to determine the effectiveness of the combined surface treatment approach.
Research Subjects and Scope:
The research subjects were samples made of Uddeholm Dievar steel, a chromium-molybdenum tool steel commonly used for die casting moulds and cores. The scope of the study is limited to investigating duplex PVD coatings (AIXN³ and nACRo³) applied to these steel samples, with a focus on their performance in aluminium die casting applications within the automotive industry. The study specifically examines the effect of laser surface remelting as a pretreatment to enhance coating adhesion and performance.
6. Main Research Results:
Key Research Results:
- Increased Mould Surface Resistance: Experimental work confirmed that the resistance of the mould surface significantly increased after laser surface remelting and application of duplex PVD coatings (AIXN³ and nACRo³).
- Good Coating Adhesion: Both AIXN³ and nACRo³ coatings exhibited satisfactory adhesion, as confirmed by scratch tests and Mercedes tests. The adhesion was categorized as HF 1-2 in Mercedes tests, indicating good to satisfactory adhesion with minimal cracking around indentations.
- Surface Microgeometry: Surface microgeometry parameters evaluated according to ISO 25 178 showed that laser surface pretreatment and grinding did not significantly affect the surface parameters of the duplex PVD coatings compared to ground surfaces.
- Hardness Improvement: Microhardness measurements showed an increase of 18.6 - 25% HV0.025 in the coated area on the laser-treated substrate compared to the substrate material.
- Resistance to Molten Aluminium: After immersion in molten Al-Si alloy at 680 ± 20°C, the coatings remained compact and intact, forming a barrier between the base material and the melt, demonstrating resistance to high-temperature corrosion.
- Laser Hardening Parameters: Laser surface hardening achieved heating depths of 160 μm, 90 µm, 80 µm, and 75 µm at scan speeds of 20 mm/s, 30 mm/s, 40 mm/s, and 60 mm/s, respectively, using a 400 W laser with a 3 mm beam diameter.
Analysis of presented data:
- Hardness Profile (Figure 10): Figure 10 illustrates the hardness profile HV0.025 from the surface towards the substrate for both nACRo³ and AIXN³ coatings. It shows higher hardness values at the surface for both coatings, decreasing towards the substrate and approaching the substrate hardness (W300). Indents 0.025 HVm for the nACRo-coated sample are shown at the interface of the laser zone and the W300 substrate.
- Surface Parameters (Table 4): Table 4 presents the surface parameters of PVD coatings according to ISO 25 178. It compares Sq, Ssk, Sku, Sp, Sv, Sz, and Sa values for PVD coating duplex nACRo³, PVD coating duplex AIXN³, PVD coating duplex nACRo³ on a laser-treated surface, and PVD coating duplex AIXN³ on a laser-treated surface. The data indicates that laser pretreatment did not significantly alter the surface microgeometry parameters.
- Mercedes Test (Figure 12 & 13): Figure 12 and Figure 13 show the morphology of indentation impressions from the Mercedes test for AIXN³ and nACRo³ coatings, respectively. The images reveal only isolated radial cracks, confirming good coating quality and adhesion, corresponding to HF 1-2 adhesion degree.
Figure Name List:
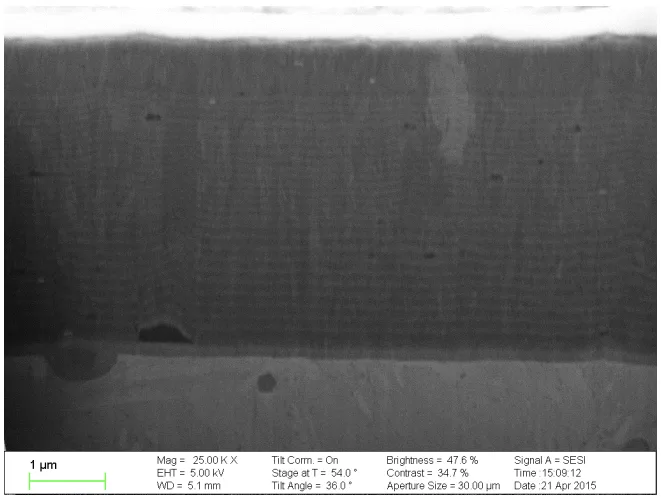
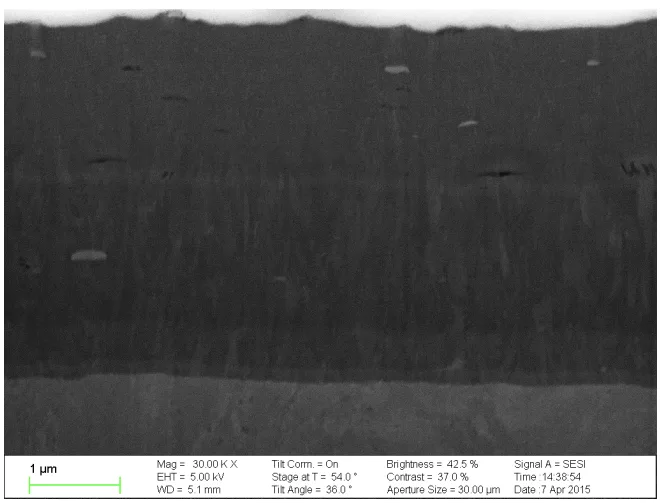
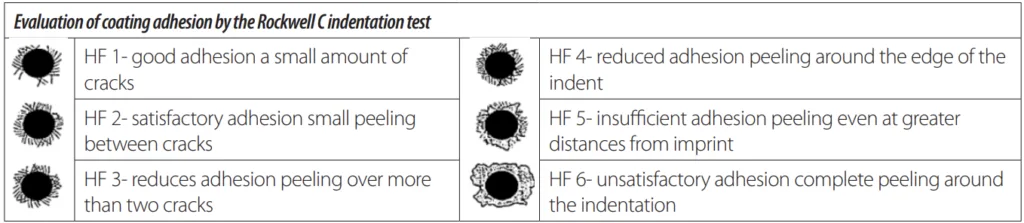
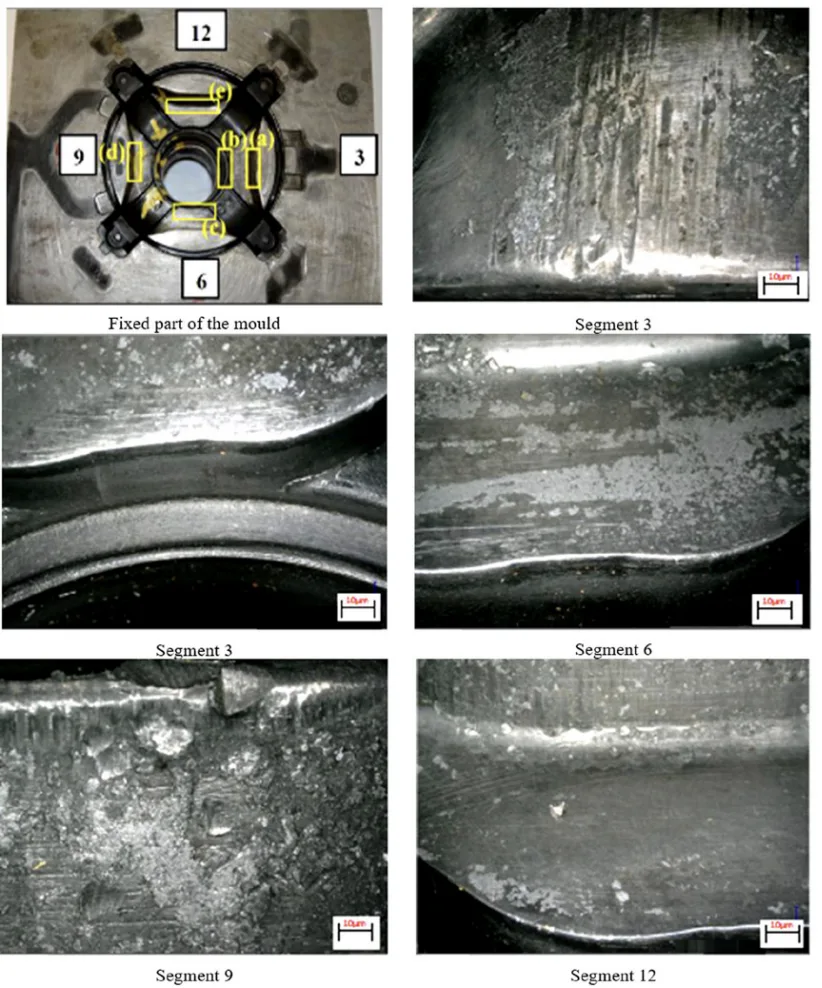
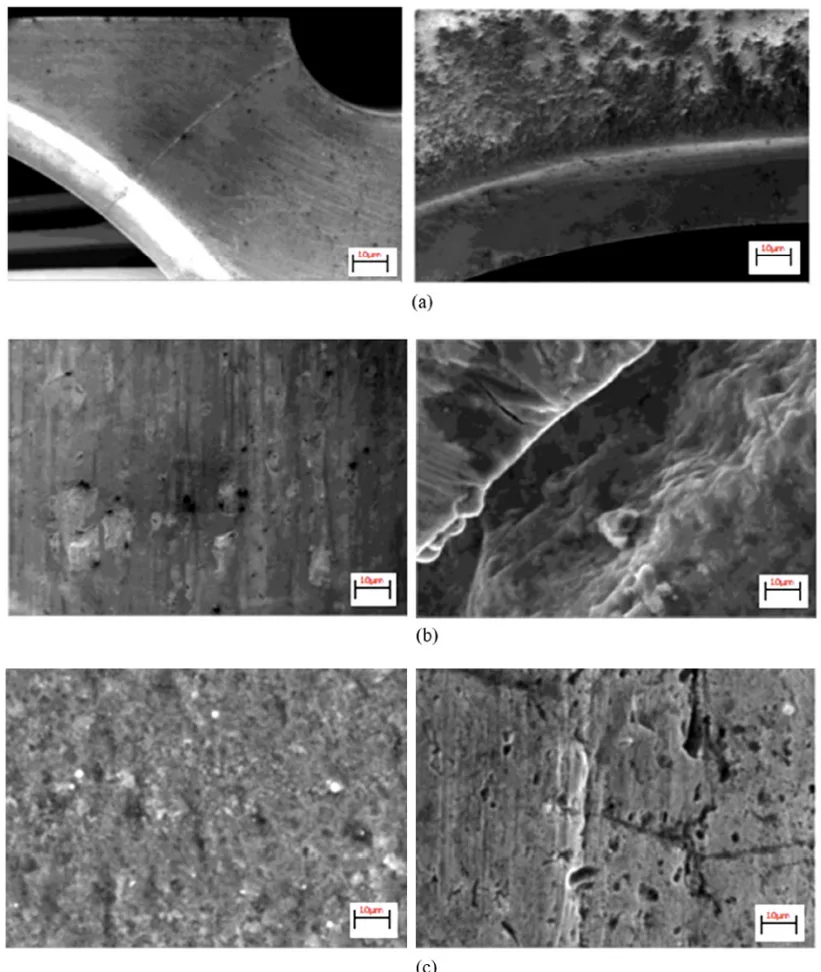
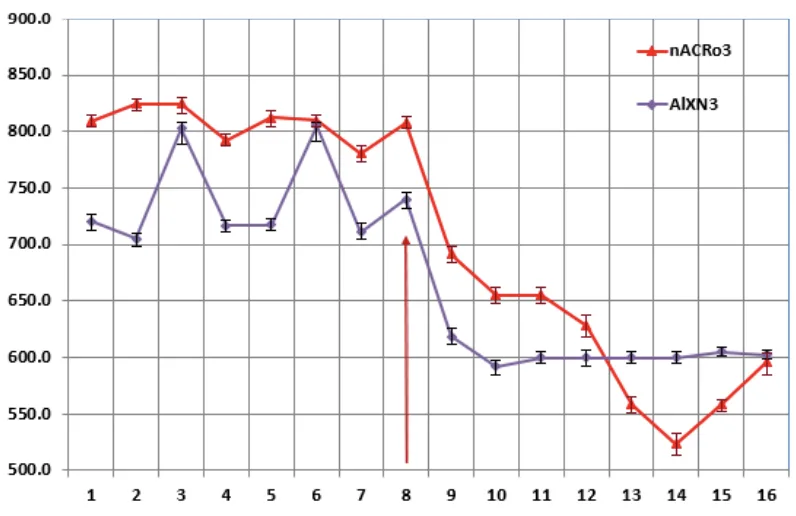
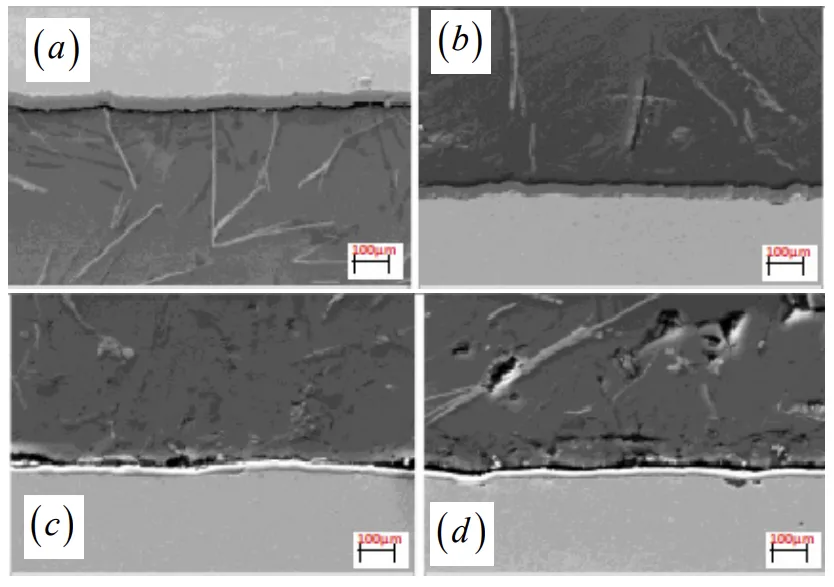
- Figure 1: Cross section of AIXN³ coating made on a FIB (Focused Ion Beam) device
- Figure 2: Cross section of nACRo³ coating performed on a FIB device
- Figure 3: Worn solid half of the mould part - mould insert
- Figure 4: Shaped part of the mould after capillary testing
- Figure 5: Appearance of cracks at the bottom of the mould
- Figure 6: Detail of the worn form; a) Crack around the ejector and the core cavity b) Separating means on the surface of the moulded part c) Contact of the movable core and the moulded part
- Figure 7: Laser surface hardening
- Figure 8: Surface of PVD coatings of control samples and samples after laser treatment and deposition of coatings
- Figure 9: Indents for the nACRo coated sample
- Figure 10: Hardness test HV0.025 from the surface towards the substrate
- Figure 11: Scratch test systems o PVD coatings - laser heat treated substrate; a) PVD coating duplex AIXN³; b) PVD coating duplex nACRo³; c) PVD coating duplex AIXN³ on a laser terated surface; d) PVD coating duplex nACRo3 on a laser terated surface
- Figure 12: Morphology of indentation impression in AIXN3 coating (X = Cr)
- Figure 13: Morphology of indentation indentation into the coating nACR03, LM
- Figure 14: PVD coatings duplex on laser treated and ground surfaces after exposure in Al mel; a) Duplex AIXN³/120 minutes/680+/-20°C/Al-Si; b) Duplex AIXN³/300 minutes/680 +/-20°C/Al-Si; c) Duplex nACRo³/120 minutes/680+/-20°C/Al-Si; d) Duplex nACRo³/300 minutes/680+/-20°C/Al-Si
7. Conclusion:
Summary of Key Findings:
The research successfully demonstrated an innovative surface treatment method for die casting moulds and cores, combining local laser surface remelting and duplex PVD coatings (AIXN³ and nACRo³). This approach significantly increased the resistance of the mould surface to degradation in aluminium die casting environments. The applied PVD coatings exhibited high quality and strong adhesion, effectively acting as a barrier against molten aluminium and high-temperature corrosion. Surface microgeometry was not significantly altered by the laser pretreatment and grinding.
Academic Significance of the Study:
This study contributes to the fundamental understanding of degradation mechanisms in die casting moulds and provides a validated methodology for enhancing mould life through advanced surface engineering techniques. The research highlights the synergistic effect of laser surface remelting and duplex PVD coatings in improving the performance of tool steels in harsh die casting conditions.
Practical Implications:
The findings have significant practical implications for the automotive and die casting industries. The developed surface treatment method offers a viable solution to extend the service life of die casting moulds and cores, leading to reduced tooling costs, increased production efficiency, and improved casting quality. This is particularly relevant for the production of lightweight aluminium components in the automotive sector, contributing to the development of more economical and greener vehicles.
Limitations of the Study and Areas for Future Research:
The study focused on laboratory-scale experiments and simulated die casting conditions. Future research should focus on:
- Industrial-scale validation: Testing the developed surface treatment method in industrial die casting operations to assess its performance and scalability in real-world production environments.
- Long-term performance evaluation: Conducting long-term durability tests to evaluate the lifespan extension of treated moulds and cores under continuous die casting cycles.
- Optimization of laser and coating parameters: Further optimizing laser surface remelting and PVD coating parameters to maximize coating performance and efficiency.
- Economic analysis: Performing a comprehensive economic analysis to quantify the cost-effectiveness of the proposed surface treatment method compared to conventional mould maintenance and replacement strategies.
- Investigation of other coating materials: Exploring other advanced PVD coating materials and compositions to further enhance mould surface properties and resistance to specific degradation mechanisms.
8. References:
- [1] Changrong Chen et al.: Energy based approach to thermal fatigue life of tool steels for die casting dies. In: International Journal of Fatigue Volume 92, Part 1, November 2016, Pages 166-178.
- [2] J. Lin et al.: Design methodology for optimized die coatings: The case for aluminium pressure die-casting In: Surface and Coatings Technology 201 (2006) pp. 2930-2941.
- [3] K. Domkin, J.H. Hattel, J. Thorborg, Modeling of high temperature- and diffusion-controlled die soldering in aluminium high pressure die casting, J. Mater. Process. Technol. 209 (8) (2009) 4051-4061.
- [4] Sundqvist M., Hogmark S.: Effects of liquid aluminium on hot-work tool steel Tribol. Int. 26 (1993) in International Journal of Fatigue p. 129.
- [5] H. Zhu, J. Guo, J. Jia, Experimental study and theoretical analysis on die soldering in aluminium die casting, J. Mater. Process. Technol. 123 (2) (2002) 229-235.
- [6] Z.W. Chen, M.Z. Jahedi, Die erosion and its effect on soldering formation in high pressure die casting of aluminium alloys, Mater. Des. 20 (6) (1999) 303-309.
- [7] K. Venkatesan, R. Shivpuri, Experimental and numerical investigation of the effect of process parameters on the erosive wear of die casting dies, J. Mater. Eng. Perform. 4 (2) (1995) 166-174. R. Markežič et al. Engineering Failure Analysis 95 (2019) 171-180179.
- [8] A Mohammed, M.B. Marshall, R. Lewis, Development of a method for assessing erosive wear damage on dies used in aluminium casting, Wear 332-333 (2015)1215-1224.
- [9] LF. Hou, Y.H. Wei, Y.G. Li, B.S. Liu, H.Y. Du, C.L. Guo, Erosion process analysis of die-casting inserts for magnesium alloy components, Eng. Fail. Anal. 33 (2013)457-564.
- [10] D.W.C. Baker, K.H. Jolliffe, D. Pearson, The resistance of materials to impact erosion damage, Philos. Trans. R. Soc. A Math. Phys. Eng. Sci. 260 (1110) (1966) 193-203.
- [11] A. Persson, S. Hogmark, J. Bergström, Temperature profiles and conditions for thermal fatigue cracking in brass die casting dies, J. Mater. Process. Technol. 152(2) (2004) 228-236.
- [12] C. Rosbrook, Analysis of Thermal Fatigue and Heat Checking in Die-Casting Dies: A Finite Element Approach, PhD thesis Ohio State University, 1992.
- [13] F. Medjedoub, G. Dour, S. Le Roux, P. Lamesle, M. Salem, P. Hairy, F. Rézaï-Aria, Experimental conditions and environment effects on thermal fatigue damage accumulation and life of die-casting steel X38CrMoV5 (AISI H11), Int. J. Microstruct. Mater. Propert. 3 (2-3) (2008).
- [14] P. Hansson, "Modern prehardened tool steels in die-casting applications," Materials and Manufacturing Processes, vol. 24, no. 7-8, pp. 824-827, 2009.
- [15] Uddeholm, "Dievar," 2014, (18.10.2021) internet: http://www.uddeholm.com
- [16] D. Klobčar, J. Tušek, B. Taljat, Thermal fatigue of materials for die-casting tooling, Mater. Sci. Eng. A 472 (1) (2008) 198-207.
- [17] D. Schwam, J. F. Wallace, and S. Birceanu, "Die Materials for Critical Applications and Increased Production Rates," Case Western Reserve University, 2002.
- [18] Methodical measurement and evaluation of adhesive cohesive behavior of thin film - substrate systems, 2005, (19.10.2021) internet: https://www.opi.zcu.cz/adheze.html
- [19] J. Tkáčová, E. Zdravecká, E. Evin, M. Tomáš, D. Jakubéczyová: Koroze a ochrana materiálu 63(4) 159-166 (2019).
- [20] D. Klobčar, et al.: Thermo fatigue cracking of die casting dies. In: Engineering Faliure Analysis Volume 20, March 2012, pp. 43-53.
- [21] D. Jakubéczyová, M. Džupon: Effect of the roughness on the adhesive properties of nanocomposite PVD coatings. In Vrstvy a povlaky 2016: 15. ročník konferencie. Rožnov pod Radhoštěm, 17.-18.10.2016. - Plzeň: Západočeská univerzita, 2016, p. . 49-55.(Layers and coatings 2016)
9. Copyright:
- This material is "Janette Brezinová et al."'s paper: Based on "Use of Duplex PVD Coatings to Increase the Life of Moulds and Cores for die Casting of Aluminium Alloys in the Automotive Industry".
- Paper Source: https://doi.org/10.21496/ams.2022.003
This material was created to introduce the above paper, and unauthorized use for commercial purposes is prohibited.
Copyright © 2025 CASTMAN. All rights reserved.