This article introduces the paper ['Eco-sustainable lightweight automotive part manufacturing: GHGs-free die casting of brake leverage prototype made of AZ91D-1.5CaO magnesium alloy'] published by ['La Metallurgia Italiana'].
1. Overview:
- Title: Eco-sustainable lightweight automotive part manufacturing: GHGs-free die casting of brake leverage prototype made of AZ91D-1.5CaO magnesium alloy
- Author: F. D'Errico, D. Casari
- Publication Year: Marzo 2022
- Publishing Journal/Academic Society: La Metallurgia Italiana, International Journal of the Italian Association for Metallurgy
- Keywords: MAGNESIUM, CALCIUM OXIDE, SUSTAINABLE METALLURGY;
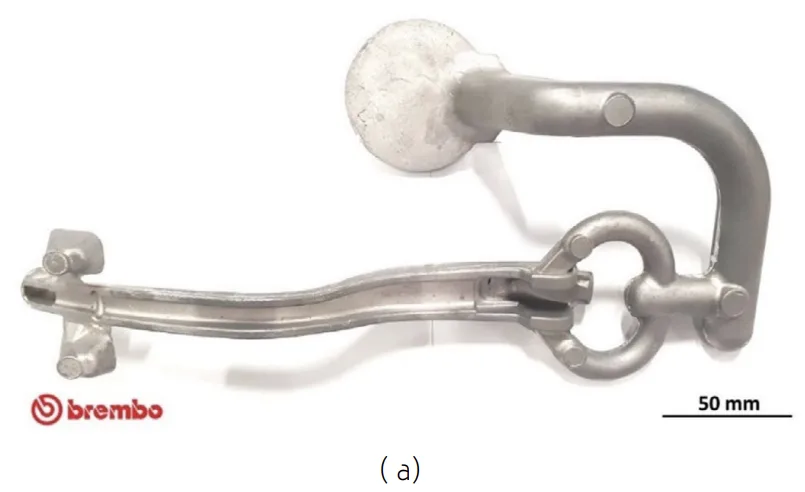
2. Abstracts or Introduction
Employing non-flammable AZ91D-1.5CaO Eco-Magnesium® (Eco-Mg) alloy in the European project CRAL provides the lowest carbon footprint for the magnesium cast process. Non-flammable magnesium AZ91D alloyed with Ca (in the form of CaO) was successfully processed by experimenting specific casting process window to melt the non-flammable magnesium alloy in a stationary furnace with no SF6 cover gas and then poured in the air into a vertical short-injection displacement press machinery specifically developed in EU CRAL project.
Brake leverage made of AZ91-1.5CaO Eco-Mg series alloy was successfully manufactured at Brembo Spa premise, as a real example of Mg cast component alternative to the current component made of forged aluminium alloy. As discussed in the experimental part, a preliminary computer-aided simulation test campaign reduced uncertainty in cast trials. The CRAL EU project with the realization of Mg-SF6 free cast part for brake systems has promoted the drastic reduction of Global Warming Potential (GWP) of the Mg cast process route. The Eco-Mg series is a feasible and affordable casting solution for introducing non-flammable Mg alloys in the automobile sector; today struggled for researching cost-driven lightweight components due to forthcoming CO2 emissions restrictions.
3. Research Background:
Background of the Research Topic:
The development of magnesium alloys, initially driven by the aerospace industry, has historically aimed to meet the transport industry's demand for weight reduction. Magnesium alloys offer superior castability and reduced chemical compatibility with steel, crucial for mold construction. This enables the production of intricate part geometries, comparable to plastics, while extending the lifespan of steel molds. Despite these advantages, the high flammability of magnesium in air remains a significant safety concern. Upon ignition, magnesium undergoes exothermic self-combustion, forming magnesium oxide and releasing substantial heat, with combustion flame temperatures rapidly reaching between 2,000° K and 4,000°K. This necessitates specific measures for safe magnesium processing.
Status of Existing Research:
Magnesium alloys necessitate specialized melting facilities and skilled personnel, increasing casting production costs. Safe control in the molten state requires eliminating oxygen contact with the metal bath to prevent combustion. Inert atmospheres are created using techniques like vacuum melting or inert gas-equipped melting plants. Common inert atmospheres include SF6 and CO2 mixtures, or alternatives based on freon gas R-134a and SO2. SF6 and freon gas R-134a are potent greenhouse gases with high global warming potential (GWP). SO2, while environmentally preferable to SF6 and R-134a, is highly toxic and requires stringent safety protocols. Although SO2 is a greener alternative to SF6, its corrosiveness to steel equipment and reaction with water to form H2SO3 pose health risks. SF6, while non-toxic and non-corrosive, was prohibited in European Union magnesium die-casting recycling from January 1, 2018, due to its greenhouse effect [1].
Necessity of the Research:
The automotive industry's shift towards lighter materials for combustion engine vehicles is crucial for emission reduction. Weight saving is a key strategy for automakers to meet the demands of an environmentally conscious market and comply with stringent EU emission targets for new vehicles. These targets, coupled with penalties for exceeding emission limits, incentivize the adoption of zero- and low-emission vehicles. However, focusing solely on tailpipe emissions is insufficient for a comprehensive green manufacturing approach. As depicted in Fig.1, substituting heavy ferrous alloys (1) with lightweight metals (2, 3) can reduce emissions over the product lifespan. However, magnesium alloy production from primary Pidgeon processes (3) can have a high initial carbon footprint.
4. Research Purpose and Research Questions:
Research Purpose:
This research aims to address the challenge of reducing the total Greenhouse Gas (GHG) emissions associated with the magnesium cast part lifecycle. The study focuses on eliminating protective gases during the die-casting process of magnesium components, specifically targeting brake system parts within the CRAL EU project. The ultimate goal is to validate the Eco-Mg series as a viable and cost-effective casting solution for non-flammable magnesium alloys in the automotive sector, aligning with the industry's drive for cost-effective lightweight components amidst increasing CO2 emission restrictions.
Key Research:
The key research objectives are:
- To experiment with a specific casting process window for melting non-flammable AZ91D alloyed with Calcium (in the form of CaO) in a stationary furnace without SF6 cover gas.
- To process this alloy by pouring it in air using a vertical short-injection displacement press machinery developed within the EU CRAL project.
- To manufacture a brake leverage prototype from AZ91-1.5CaO Eco-Mg series alloy at Brembo Spa, serving as a practical example of a magnesium cast component as an alternative to forged aluminum.
- To conduct preliminary computer-aided simulation tests to minimize uncertainties in casting trials.
Research Hypotheses:
While not explicitly stated as hypotheses, the research is based on the premise that:
- Utilizing AZ91D-1.5CaO Eco-Mg alloy enables magnesium die casting without SF6 protective gas.
- Optimized casting parameters and a vertical injection die-casting press facilitate successful air-poured magnesium casting.
- This approach significantly reduces the Global Warming Potential (GWP) of the magnesium casting process route.
5. Research Methodology
Research Design:
The research employed an experimental design focused on the die-casting of a brake leverage prototype using AZ91D-1.5CaO Eco-Mg alloy. The study was conducted using a vertical injection die-casting press machinery.
Data Collection Method:
Data was collected through the practical manufacturing of a brake leverage prototype at Brembo Spa facilities. This involved monitoring and adjusting casting parameters to achieve successful production in an air environment without protective gases. Microstructural analysis using SEM imaging was performed on the as-cast billet. Machine characteristics and casting parameters were documented.
Analysis Method:
The analysis was primarily qualitative, focusing on the successful demonstration of GHG-free die-casting. The study assessed the feasibility of casting the AZ91D-1.5CaO alloy in air, the effectiveness of the vertical injection press, and the resulting prototype quality. Data analysis included examination of the as-cast microstructure (Fig.3) and evaluation of the machine parameters (Tab.1). The weight reduction achieved compared to aluminum was quantitatively assessed.
Research Subjects and Scope:
The research focused on:
- Material: AZ91D Eco-Mg series alloy modified with 1.5% CaO.
- Component: Automotive brake leverage prototype.
- Manufacturing Process: High-pressure die-casting using a vertical injection press.
- Location: Advanced Materials Research and Development laboratories in Brembo facility, Stezzano, Italy.
6. Main Research Results:
Key Research Results:
The experimental procedure successfully demonstrated the die-casting of a brake leverage prototype from AZ91D-1.5CaO Eco-Mg alloy without the use of SF6 or other protective gases. Key findings include:
- Successful air-poured die-casting of AZ91D-1.5CaO Eco-Mg alloy was achieved using a vertical injection die-casting press.
- A 32% weight reduction was attained in the magnesium prototype compared to the current aluminum component.
- The casting process was conducted safely in ambient air, attributed to the compact cycle time of the vertical injection press.
- The AZ91D-1.5CaO alloy, overheated to 700°C in a stationary furnace, maintained a pouring temperature above 630°C into the pre-heated injection chamber (220-250°C).
- A nitrogen cap on the furnace effectively reduced oxygen content, eliminating the need for protective fluxes.
- Molten magnesium alloy was safely maintained for up to one hour under overheating conditions without ignition issues.
Analysis of presented data:
- Figure 1 (Fig.1) illustrates three scenarios comparing the environmental impact of heavy (1) versus light metals (2, 3) over the product lifespan, highlighting the potential of lightweight solutions and the carbon footprint challenges of primary magnesium production.
- Figure 2 (Fig.2) provides the Pilling-Bedworth Ratio (PBR) explanation of high-temperature oxidation behavior, correlating oxide film porosity with stress type (tensile or compressive) and oxide layer cracking.
- Figure 3 (Fig.3) presents a SEM image of the as-cast AZ91D-1.5CaO billet microstructure, showing typical features of high aluminum content casting magnesium alloys with α-Mg and discontinuous β-Mg17Al12 compound at grain boundaries.
- Figure 4 (Fig.4) displays the die-cast brake leverage prototype: (a) with in-gate channels and sprue, and (b) after removing the sprue and in-gates, ready for mechanical testing.
- Table 1 (Tab.1) summarizes the main machine characteristics of the vertical injection die-casting press, including injection plunger velocity, plunger stroke, locking force, projected shot area, specific pressure, and injection force.
Figure Name List:
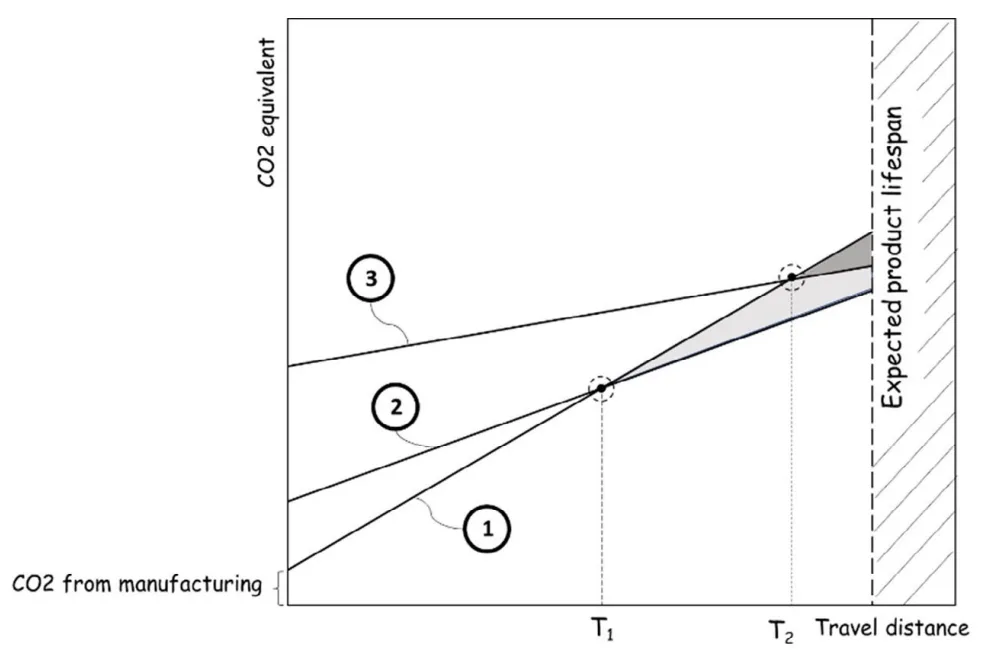
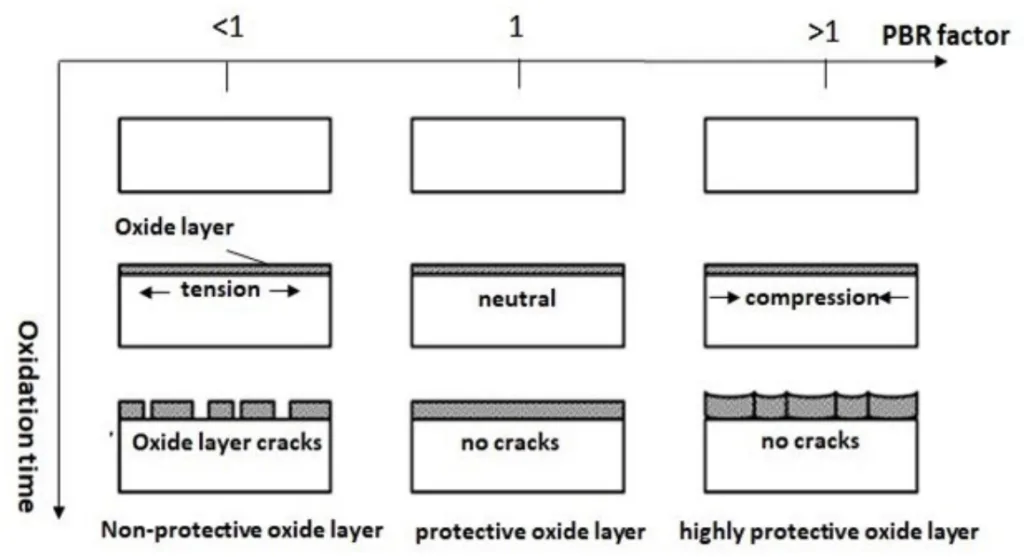
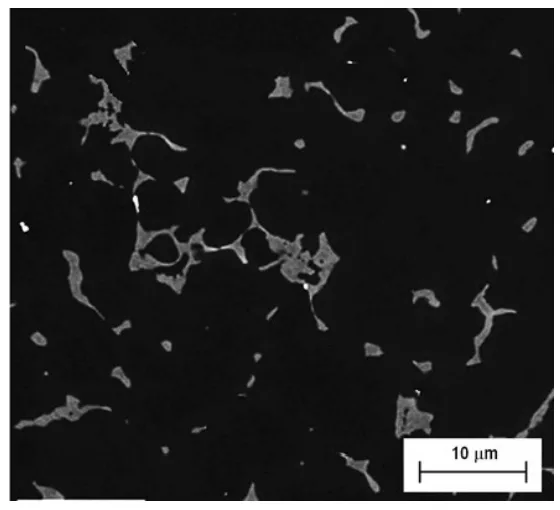
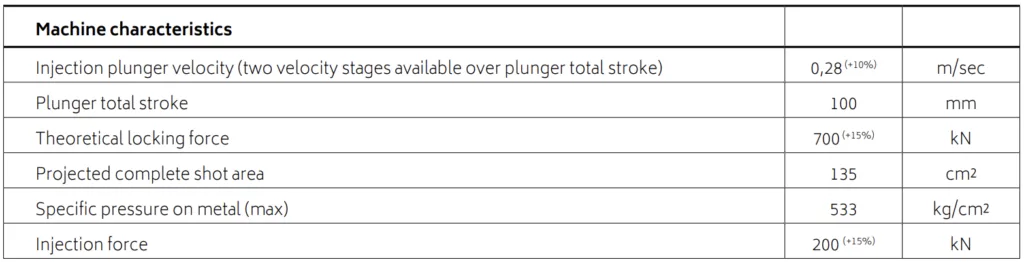
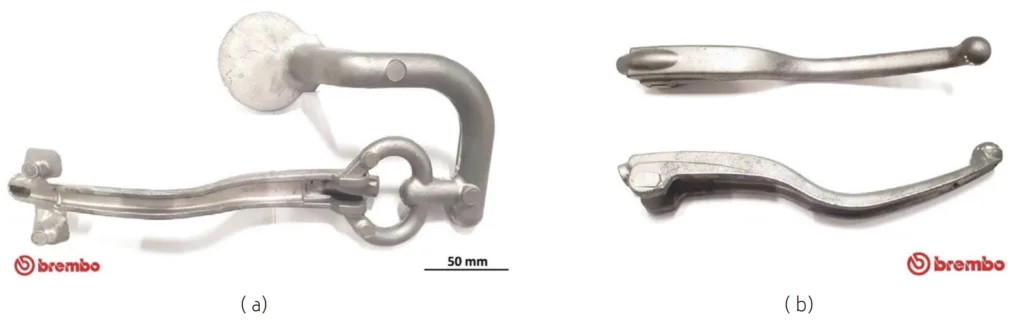
- Fig.1 - Three qualitative scenarios for addressing at-a-whole the environmental impact over the product lifespan of using light metals (2) and (3) to substitute the heavy solution (1).
- Fig.2 - The PBR explanation of the high temperature oxidation behavior of different metals and their oxides in correlation with porous or non-porous oxide film developed by air oxidation.
- Fig.3 - SEM image of as-cast billet received.
- Fig.4 - a) The die-cast brake leverage with in-gate channels and sprue; b) die-cast brake leverage after re-moving sprue and in-gate channels.
7. Conclusion:
Summary of Key Findings:
The research successfully demonstrated a vertical high-pressure die-casting process for manufacturing a magnesium brake leverage prototype using AZ91D-CaO alloy without environmentally harmful protective gases. This GHG-free process achieved a 32% weight reduction compared to aluminum. The process was safely conducted in air due to the vertical press's compact cycle time. The study indicates the feasibility of affordable cover gas-free die-casting and the potential of processing commercial Eco-Mg alloys in air using compact, low-cost presses suitable for both Mg and Al alloys.
Academic Significance of the Study:
This study contributes to the academic field by demonstrating the viability of eliminating environmentally impactful protective gases in magnesium die-casting. It provides valuable insights into sustainable manufacturing practices for lightweight metal components, specifically through the application of AZ91D-CaO alloy and vertical die-casting technology.
Practical Implications:
The practical implications of this research are significant for the automotive industry, offering an eco-sustainable approach to manufacturing lightweight automotive parts. The GHG-free die-casting process reduces reliance on SF6 and other harmful gases, providing a cost-effective and environmentally responsible solution for magnesium component production. This facilitates the broader adoption of non-flammable magnesium alloys in automobiles, contributing to reduced vehicle weight and improved fuel efficiency.
Limitations of the Study and Areas for Future Research:
This study represents a preliminary test campaign. Further research is recommended to optimize and scale up the demonstrated process for industrial application. Ongoing mechanical testing and validation of the brake leverage prototype are necessary. Future research should explore process optimization, long-term performance evaluation, and broader application of this GHG-free die-casting method to other magnesium components and alloy systems.
8. References:
[1] EU Regulation (EU) No 517/2014.
[2] S. Ramakrishnan et all., "Global warming impact of the magnesium produced in China using the Pidgeon process," Resources, Conservation and Recycling, Volume 42, 1: 49–64, 2004.
[3] D'Errico, F., Ranza, L. "Guidelines for the market competitiveness of sustainable lightweight design by magnesium solution: a new Life Cycle Assessment integrated approach”, Paper presented at the 72nd Annual World Magnesium Conference, Vancouver, Canada, 17-19 May 2015.
[4] H.E. Friedrich, et all., "Solutions for Next Generation Automotive Lightweight Concepts Based on Material Selection and Functional Integration", Magnesium Technology 2018, The Minerals, Metals & Materials Society, 343-348, 2018.
[5] N. B. Pilling, R. E. Bedworth, "The oxidation of metals at high temperatures", J. Inst. Met, 29: 529-591, 1923.
[6] E. F. Emley, "Principles of magnesium technology" Pergamon Press, Oxford, New York, 1966.
[7] G. C. Wood, "High-temperature oxidation of alloys", Oxidation of Metals, 2:11-57, 1970.
[8] F. Czerwinski, "Oxidation Characteristics of Magnesium Alloys", JOM, 64 (12):1477-1483, 2012.
[9] Y. M. Kim, et all., "Key factor influencing the ignition resistance of magnesium alloys at elevated temperatures", Scripta Materialia, 65(11):958-961, 2011.
[10] M. Sakamoto, et all., "Suppression of ignition and burning of molten Mg alloys by Ca bearing stable oxide", Journal of Materials Science Letters, 16 (12):1048-1050, 1997.
[11] S.H. Ha et all., "Effect of CaO on oxidation resistance and microstructure of pure Mg", Materials Transactions, 49(5) 1081-1083, 2008
[12] S.K. KIM and J. H. SEO, "Magnesium-based alloy for high temperature and manufacturing method thereof", US Patent 8,808,423, 2014.
[13] J.K. Lee, S.K. Kim, "Effect of CaO Addition on the Ignition Resistance of. Mg-Al Alloys", Materials Transactions, Vol. 52, 1483-1488, 2011.
9. Copyright:
- This material is "F. D'Errico, D. Casari"'s paper: Based on "Eco-sustainable lightweight automotive part manufacturing: GHGs-free die casting of brake leverage prototype made of AZ91D-1.5CaO magnesium alloy".
- Paper Source: [DOI URL] (DOI URL was not provided in the text, please add if available, otherwise use journal link if possible)
This material was summarized based on the above paper, and unauthorized use for commercial purposes is prohibited.
Copyright © 2025 CASTMAN. All rights reserved.