This article introduces the paper ['Thermofluid topology optimization for cooling channel design'] presented at the ['arXiv.org']
1. Overview:
- Title: Thermofluid topology optimization for cooling channel design
- Author: Farshad Navah, Marc-Étienne Lamarche-Gagnon, Florin Ilinca
- Publication Year: 2023
- Publishing Journal/Academic Society: arXiv.org
- Keywords: topology optimization, cooling channel, additive manufacturing, adjoint method, verification and validation.
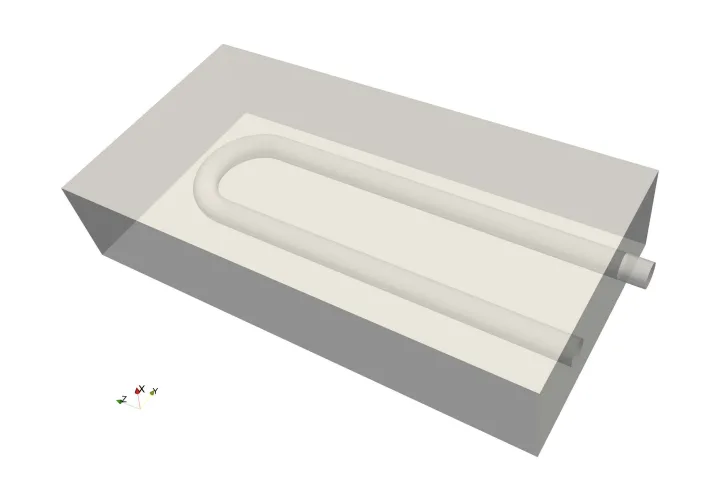
2. Research Background:
Background of the Research Topic:
Cooling channels are critical components in technological systems involving heat extraction, notably in die casting molds. The integration of cooling channels in molds significantly impacts cycle time, part shape deviations, and residual stresses. Conformal cooling channels, enabled by additive manufacturing, are gaining prominence over traditional straight-drilled channels due to enhanced heat removal efficiency. However, designing these conformal channels is complex and time-consuming, necessitating automated algorithmic approaches like gradient-based topology optimization to achieve balanced designs.
Status of Existing Research:
Topology optimization, initially focused on structural stiffness and weight minimization, has expanded into fluid mechanics and heat transfer applications. In Conjugate Heat Transfer (CHT) problems, the objective is to optimize the fluid-solid contact surface, such as fluid channels, to minimize temperature-dependent functions. While topology optimization shows promise for conformal cooling channel design, limited research has been dedicated to this area. Existing studies often simplify CHT problems, focusing on 2D analyses or using approximations like Newton's law of cooling or Darcy's law, and rarely compare outcomes with full-blown 3D CHT topology optimization approaches.
Necessity of the Research:
Despite the increasing use of three-dimensional CHT approaches for cooling channel design, prior research has not adequately addressed the design of conformal cooling channels, particularly for applications like die casting molds with heated surfaces. Existing studies mainly focus on maximizing heat extraction in uniformly heated domains or designing fin-type heat sinks and two-fluid heat exchangers, lacking direct application to complex geometries and conformal cooling needs in die casting. Furthermore, solver verification in topology optimization literature is often overlooked, highlighting a gap in ensuring the reliability of computational results.
3. Research Purpose and Research Questions:
Research Purpose:
This research aims to propose a three-dimensional CHT topology optimization approach specifically for designing conformal cooling channels in applications with heated surfaces, such as die casting molds. The approach is based on density modeling with fluid and solid states, utilizing a porosity-based solution of the Navier-Stokes and energy equations for laminar flow.
Key Research:
The key research questions addressed in this paper include:
- Development and verification of a porosity-based CHT solver for topology optimization.
- Calibration of the Darcy friction coefficient within the porosity-based model.
- Investigation of the effects of various optimization parameters on the resulting cooling channel designs.
- Validation of the optimized designs against a body-fitted CHT solver.
- Solver verification, particularly regarding the porosity-based CHT solver and adjoint sensitivities.
Research Hypotheses:
The research implicitly hypothesizes that:
- A density-based topology optimization approach using a porosity model can effectively design conformal cooling channels for die casting molds.
- Systematic verification and validation, including comparison with body-fitted solvers and manufactured solutions, are crucial for ensuring the reliability of topology optimization results in CHT problems.
- Careful calibration of parameters like the Darcy coefficient is essential for accurate porosity-based CHT simulations.
4. Research Methodology
Research Design:
The research employs a computational approach based on density-based topology optimization for CHT. This involves formulating an optimization problem to minimize a cost function related to temperature, subject to constraints on design variables and physical laws governed by the Navier-Stokes and energy equations. The design variable is the solid fraction, parametrized using a smoothed-Heaviside filter.
Data Collection Method:
Data is generated through numerical simulations using DFEM, a proprietary multiphysics solver developed by the National Research Council Canada (NRC). The simulations solve the steady-state conservation equations of mass, momentum, and energy in a medium with variable porosity and conductivity.
Analysis Method:
The analysis involves:
- Sensitivity Analysis: Utilizing the discrete adjoint approach to evaluate sensitivities of the objective function with respect to the design variables.
- Solver Verification: Numerically validating the porosity-based CHT solver against a body-fitted CHT solver using manufactured solutions and solution verification for a U-shaped cooling channel problem.
- Parameter Studies: Investigating the effects of optimization parameters such as filter radius, maximum fluid volume, and pressure loss penalization on the optimized designs.
- Calibration: Calibrating the Darcy friction coefficient by comparing porous solver solutions to body-fitted solver solutions.
Research Subjects and Scope:
The research focuses on a simplified die casting mold geometry with a U-shaped cooling channel. Optimizations are performed for Reynolds numbers of 100 and 1,000, representing laminar flow conditions. The design domain and boundary conditions are defined to simulate heat extraction from a heated surface representing a die casting mold insert.
5. Main Research Results:
Key Research Results:
- Solver Verification: The porosity-based CHT solver was verified against a body-fitted CHT solver, demonstrating good numerical agreement, particularly after calibrating the Darcy friction coefficient. A manufactured solution was introduced for porosity-based CHT solver verification. Adjoint sensitivities were verified using finite differencing.
- Darcy Coefficient Calibration: A Darcy coefficient value of "Ca = 1 × 10^10 kg/m³/s" was identified as optimal for the U-shaped channel case, minimizing spurious flow in solid regions and accurately predicting pressure drops compared to body-fitted solutions.
- Optimization Parameter Effects: Variations in filter radius, fluid volume fraction, and pressure loss penalization significantly influenced the topology of the optimized cooling channels, affecting channel complexity, ramification, and diameter.
- Objective Function Impact: Different objective functions (domain-averaged temperature vs. surface-averaged temperature) resulted in distinct design paradigms. Minimizing surface-averaged temperature led to channels concentrated near the heated cavity, while minimizing domain-averaged temperature resulted in channels spanning the domain.
- Reynolds Number Influence: Increasing the Reynolds number to 1,000 enhanced cooling capacity, leading to channels closer to the heated cavity compared to Re = 100 cases.
Data Interpretation:
The numerical validation and calibration steps are crucial for ensuring the reliability of the porosity-based CHT solver. The parameter studies highlight the sensitivity of topology optimization to hyper-parameter choices, emphasizing the need for careful selection to achieve desired design characteristics. The comparison of different objective functions demonstrates the ability to tailor cooling channel designs based on specific performance goals, whether minimizing cavity surface temperature or overall mold temperature.
Figure Name List:
- Figure 1: Geometrical configuration of the U-shaped cooling channel case.
- Figure 2: Conformal discretization of the U-shaped configuration on the cutting plane x = 0 for refinement levels 2 and 4.
- Figure 3: Conformal vs non-conformal discretizations of the U-shaped configuration on the cutting plane x = 0.
- Figure 4: Linear interpolation of the solid fraction field of the U-shaped configuration on the cutting plane x = 0 and mesh m3-n.
- Figure 5: Implicit versus explicit solid-fluid interface representations.
- Figure 6: Convergence of the pressure and velocity magnitude profiles of the body-fitted CHT solver with mesh refinement along the transverse (y) direction, for x = 0 and for two streamwise (z) locations.
- Figure 7: Convergence of the temperature profiles of the body-fitted CHT solver with mesh refinement along the transverse (y) direction, for x = 0 and for two streamwise (z) locations.
- Figure 8: Calibration of Ca; Solutions of the porous CHT solver on conformal mesh m3-c vs solution of the body-fitted CHT solver on conformal mesh m4-c, along the transverse (y) direction, for x = 0 and for two streamwise (z) locations.
- Figure 9: Effect of Ca; Solutions of the porous CHT solver on non-conformal mesh ml-n vs solution of the body-fitted CHT solver on conformal mesh m4-c, along the transverse (y) direction, for x = 0 and for two streamwise (z) locations.
- Figure 10: Effect of Ca; Solutions of the porous CHT solver on non-conformal mesh m2-n vs solution of the body-fitted CHT solver on conformal mesh m4-c, along the transverse (y) direction, for x = 0 and for two streamwise (z) locations.
- Figure 11: Effect of Ca; Solutions of the porous CHT solver on non-conformal mesh m3-n vs solution of the body-fitted CHT solver on conformal mesh m4-c, along the transverse (y) direction, for x = 0 and for two streamwise (z) locations.
- Figure 12: Effect of conformal versus non-conformal discretization on the flow speed solutions of the porous solver and the effective channel section area.
- Figure 13: Convergence of the temperature profiles of the porous CHT solver on non-conformal meshes with mesh refinement, as compared to a body-fitted solution on m4-c, for x = 0 and for two streamwise (z) positions.
- Figure 14: Domain and cut plane of the mesh for the optimization cases.
- Figure 15: Baseline design.
- Figure 16: Evolution of the cost function C, cavity average surface temperature Tr and volume constraint G1, versus optimization steps, for Case A.
- Figure 17: Optimized channel designs at selected steps for Case A, as represented by the 10^-3 m/s isocontour of the flow speed and colored by the pressure; Velocity vectors outside of the channels.
- Figure 18: Case A; Optimized designs at different β values; Solid fraction on the outer domain walls, clip on y ≤ 0.5 and isocontour of y = 0.999.
- Figure 19: Case A; Optimized designs at different β values; Isocontours of flow speed at 10^-3 m/s, colored by the temperature.
- Figure 20: Optimization Cases A-I: on the small cavity and with Re = 100; Solid fraction on the outer domain walls, clip on y ≤ 0.5 and isocontour of y = 0.999.
- Figure 21: Optimization Cases A-I: on the small cavity and with Re = 100; Temperature on the outer domain walls and isocontour of flow speed at 10^-3 m/s, colored by the temperature.
- Figure 22: Optimization Cases A-I: on the small cavity and with Re = 100; Temperature on the outer domain walls and isocontour of flow speed at 10^-3 m/s, colored by the temperature.
- Figure 23: Isocontours of flow speed at 10^-3 m/s and velocity vectors outside of the channels, colored by the velocity magnitude.
- Figure 24: Optimization Cases J-L: on the small cavity and with Re = 1,000; Solid fraction on the outer domain walls, clip on y ≤ 0.5 and isocontour of y = 0.999.
- Figure 25: Optimization Cases J-L: on the small cavity and with Re = 1,000; Temperature on the outer domain walls and isocontour of flow speed at 10^-3 m/s, colored by the temperature.
- Figure 26: Optimization Cases J-L: on the small cavity and with Re = 1,000; Temperature on the outer domain walls and isocontour of flow speed at 10^-3 m/s, colored by the temperature.
- Figure 27: Body-fitted mesh generated using the final design for Case A. The refined regions correspond to the position of the interface.
- Figure 28: Top and cut (along the y-z symmetry plane) views comparing the body-fitted (left) and porosity (right) temperature distributions for Case A. Both solutions were obtained using the body-fitted mesh (cf. Fig 27.)
- Figure B.29: Histogram of matching significant digits between the cost function computation via the adjoint solver versus the sensitivity analysis.
- Figure B.30: Lagrangian function gradient as computed by the adjoint method and its absolute and relative differences with regards to the cost function computed by sensitivity analysis.
- Figure C.31: Evolution of the errors of u and T in L2 norm and with mesh refinement, as a function of h, the element size.
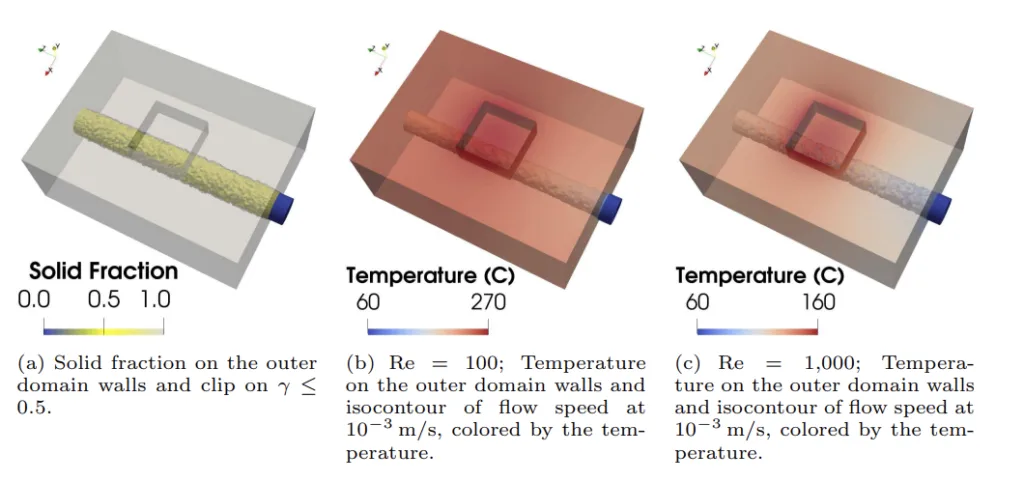
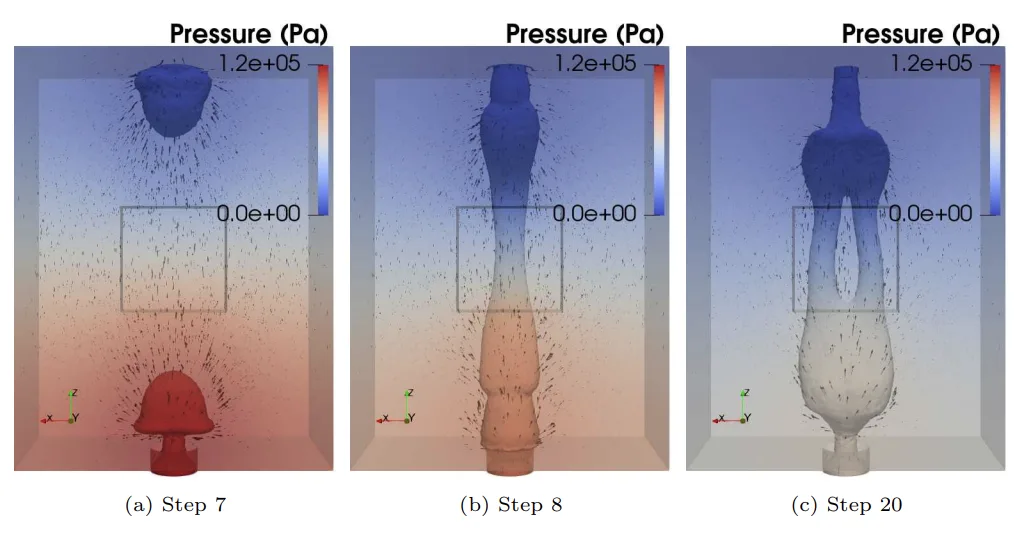
m/s isocontour of the flow speed and colored by the pressure; Velocity vectors outside of the
channels.
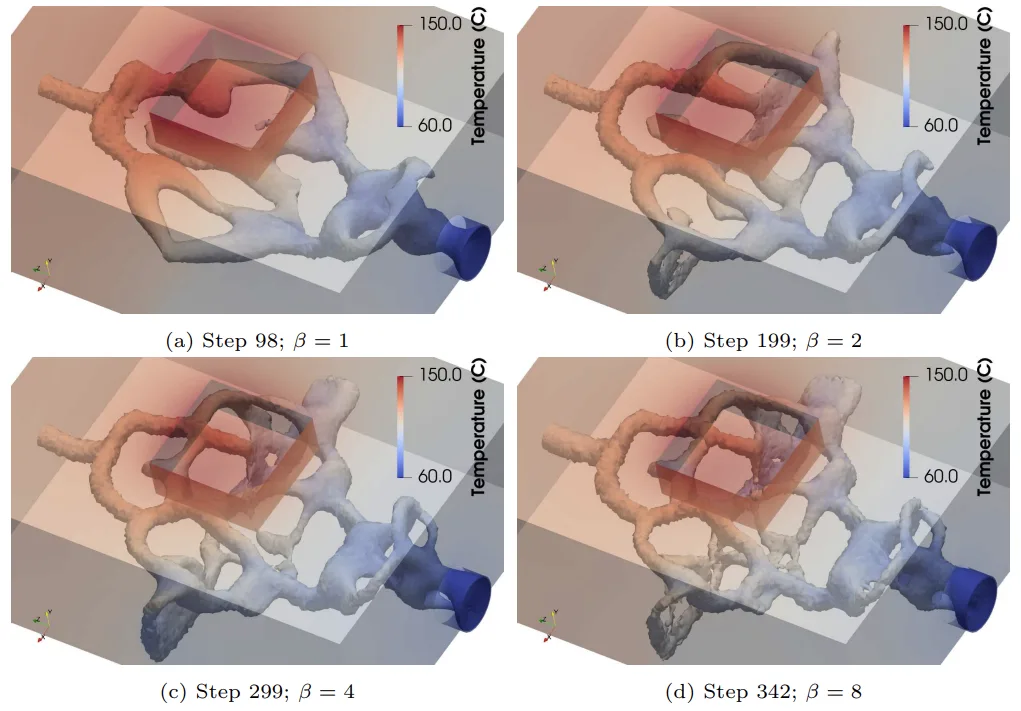
10−3 m/s, colored by the temperature.
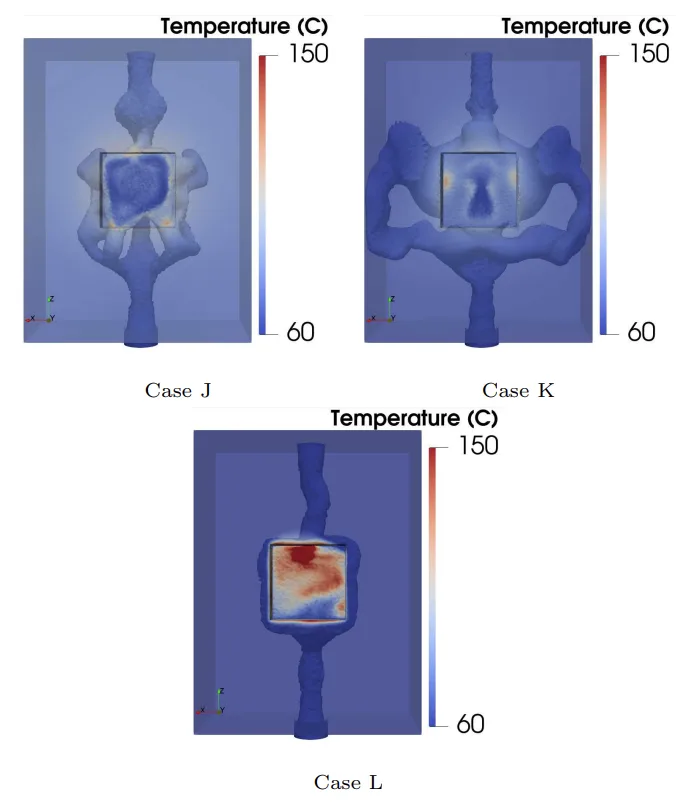
the outer domain walls and isocontour of flow speed at 10−3 m/s, colored by the temperature.
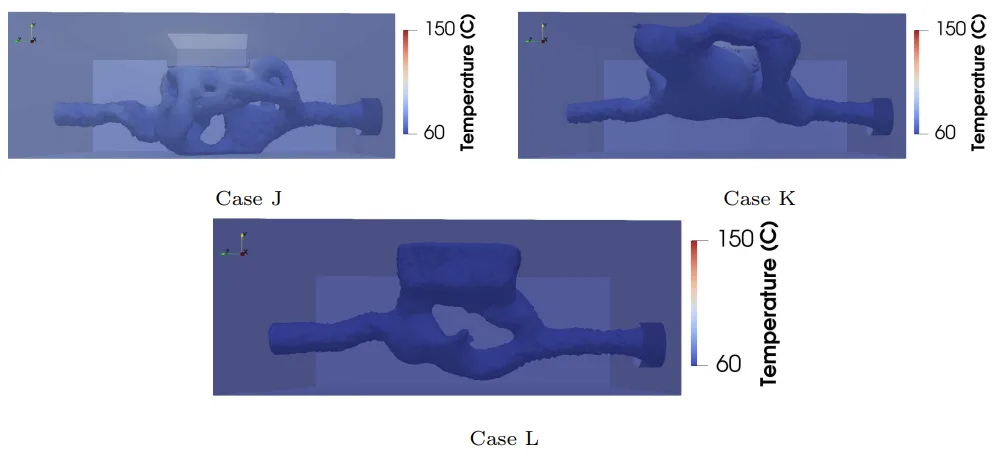
the outer domain walls and isocontour of flow speed at 10−3 m/s, colored by the temperature.
6. Conclusion:
Summary of Main Results:
This research successfully developed and validated a 3D CHT topology optimization framework for conformal cooling channel design in die casting molds. The framework utilizes a porosity-based approach, solving Navier-Stokes and energy equations with a discrete adjoint method for sensitivity analysis. Numerical verification against body-fitted solvers and manufactured solutions, along with Darcy coefficient calibration, ensures the reliability of the computational results. Parameter studies revealed the influence of optimization settings on design topology, and different objective functions enabled tailoring designs for specific cooling performance targets.
Academic Significance of the Research:
This work contributes to the field of topology optimization by providing a verified and validated methodology for 3D CHT problems, specifically addressing the design of conformal cooling channels. It emphasizes the importance of solver verification in topology optimization and provides a detailed analysis of parameter effects, offering valuable insights for researchers and practitioners in the field. The introduction of a manufactured solution for porosity-based CHT solver verification is a notable methodological contribution.
Practical Implications:
The proposed framework offers a powerful tool for automated design of additively manufactured cooling channels in die casting molds. By optimizing channel topology, it enables improved heat management, potentially leading to reduced cycle times, decreased part warpage, and enhanced part quality in die casting processes. The ability to tailor designs through objective function selection and parameter tuning provides flexibility for addressing specific industrial needs.
Limitations of the Research
While the paper does not explicitly state limitations, it is important to note that the research focuses on laminar flow conditions and simplified die casting mold geometries. The application to turbulent flow regimes and more complex industrial scenarios would require further investigation and potentially model enhancements.
7. Future Follow-up Research:
- Directions for Follow-up Research
Future research directions identified by the authors include: - Incorporating additive manufacturing constraints into the optimization process, such as preventing overhanging features.
- Integrating structural optimization into a multi-objective framework to consider structural integrity and longevity alongside thermal performance.
- Developing mesh adaptation strategies to improve computational efficiency for complex 3D problems.
- Exploring full- or reduced-order modeling techniques to account for turbulent flow effects.
- Areas Requiring Further Exploration
Further exploration should focus on applying the developed framework to more complex, industrially relevant die casting mold designs and validating the optimized designs through experimental studies. Investigating the performance of the framework under turbulent flow conditions and exploring the use of more advanced turbulence models would also be beneficial. Additionally, research into efficient mesh adaptation techniques and parallel computing strategies is needed to address the computational cost associated with 3D topology optimization for large-scale industrial problems.
8. References:
- [1] S. Feng, A. M. Kamat, Y. Pei, Design and fabrication of conformal cooling channels in molds: Review and progress updates, International Journal of Heat and Mass Transfer 171 (2021) 121082. doi:10.1016/j.ijheatmasstransfer.2021.121082.
- [2] B. B. Kanbur, S. Suping, F. Duan, Design and optimization of conformal cooling channels for injection molding: A review, The International Journal of Advanced Manufacturing Technology 106 (7) (2020) 3253-3271. doi:10.1007/s00170-019-04697-9.
- [3] K. Eiamsa-ard, K. Wannissorn, Conformal bubbler cooling for molds by metal deposition process, Computer-Aided Design 69 (2015) 126-133. doi:10.1016/j.cad.2015.04.004.
- [4] M. Bendsøe, Optimal shape design as a material distribution problem, Structural Optimization 1 (4) (1989) 193–202.
- [5] O. Sigmund, K. Maute, Topology optimization approaches: A comparative review, Structural and Multidisciplinary Optimization 48 (6) (2013) 1031–1055. doi:10.1007/s00158-013-0978-6.
- [6] J. Alexandersen, C. S. Andreasen, A Review of Topology Optimisation for Fluid-Based Problems, Fluids 5 (1) (2020) 29. doi:10.3390/fluids5010029.
- [7] F. Navah, M.-É. Lamarche-Gagnon, F. Ilinca, M. Audet, M. Molavi-Zarandi, V. Raymond, Development of a Topology Optimization Framework for Cooling Channel Design in Die Casting Molds, in: Proceedings of the ASME 2021, International Mechanical Engineering Congress and Exposition, IMECE2021-73363, November 1-5, 2021, Virtual, Online.
- [8] M.-É. Lamarche-Gagnon, F. Navah, F. Ilinca, M. Molavi-Zarandi, V. Raymond, A Comparative Study Between a Sharp and a Diffuse Topology Optimization Method for Thermal Problems, in: Proceedings of the ASME 2021, International Mechanical Engineering Congress and Exposition, IMECE2021-72861, November 1-5, 2021, Virtual, Online.
- [9] E. M. Dede, Multiphysics Topology Optimization of Heat Transfer and Fluid Flow Systems, Proceedings of the COMSOL Conference 2009 Boston (2009) 7.
- [10] T. Matsumori, T. Kondoh, A. Kawamoto, T. Nomura, Topology optimization for fluid-thermal interaction problems under constant input power, Structural and Multidisciplinary Optimization 47 (4) (2013) 571-581. doi:10.1007/s00158-013-0887-8.
- [11] P. Coffin, K. Maute, Level set topology optimization of cooling and heating devices using a simplified convection model, Structural and Multidisciplinary Optimization 53 (5) (2016) 985-1003. doi:10.1007/s00158-015-1343-8.
- [12] J. Liu, R. Li, K. Wang, Net-based topology optimization approach for cooling channels, International Journal of Thermal Sciences 156 (2020) 106494. doi:10.1016/j.ijthermalsci.2020.106494.
- [13] Z. Li, X. Wang, J. Gu, S. Ruan, C. Shen, Y. Lyu, Y. Zhao, Topology Optimization for the Design of Conformal Cooling System in Thin-wall Injection Molding Based on BEM, The International Journal of Advanced Manufacturing Technology 94 (1) (2018) 1041-1059. doi:10.1007/s00170-017-0901-1.
- [14] X. Zhao, M. Zhou, O. Sigmund, C. S. Andreasen, A “poor man's approach” to topology optimization of cooling channels based on a Darcy flow model, International Journal of Heat and Mass Transfer 116 (2018) 1108-1123. doi:10.1016/j.ijheatmasstransfer.2017.09.090.
- [15] S. Kambampati, H. A. Kim, Level set topology optimization of cooling channels using the Darcy flow model, Structural and Multidisciplinary Optimization 61 (4) (2020) 1345–1361. doi:10.1007/s00158-019-02482-6.
- [16] K. Yaji, T. Yamada, S. Kubo, K. Izui, S. Nishiwaki, A topology optimization method for a coupled thermal-fluid problem using level set boundary expressions, International Journal of Heat and Mass Transfer 81 (2015) 878-888. doi:10.1016/j.ijheatmasstransfer.2014.11.005.
- [17] M. Yu, S. Ruan, J. Gu, M. Ren, Z. Li, X. Wang, C. Shen, Three-dimensional topology optimization of thermal-fluid-structural problems for cooling system design, Structural and Multidisciplinary Optimization 62 (6) (2020) 3347-3366. doi:10.1007/s00158-020-02731-z.
- [18] S. B. Dilgen, C. B. Dilgen, D. R. Fuhrman, O. Sigmund, B. S. Lazarov, Density based topology optimization of turbulent flow heat transfer systems, Structural and Multidisciplinary Optimization 57 (5) (2018) 1905-1918. doi:10.1007/s00158-018-1967-6.
- [19] S. Sun, P. Liebersbach, X. Qian, 3D topology optimization of heat sinks for liquid cooling, Applied Thermal Engineering 178 (2020) 115540. doi:10.1016/j.applthermaleng.2020.115540.
- [20] N. Gilmore, V. Timchenko, C. Menictas, Manifold microchannel heat sink topology optimisation, International Journal of Heat and Mass Transfer 170 (2021) 121025. doi:10.1016/j.ijheatmasstransfer.2021.121025.
- [21] L. C. Høghøj, D. R. Nørhave, J. Alexandersen, O. Sigmund, C. S. Andreasen, Topology optimization of two fluid heat exchangers, International Journal of Heat and Mass Transfer 163 (2020) 120543. doi:10.1016/j.ijheatmasstransfer.2020.120543.
- [22] F. Feppon, G. Allaire, C. Dapogny, P. Jolivet, Body-fitted topology optimization of 2D and 3D fluid-to-fluid heat exchangers, Computer Methods in Applied Mechanics and Engineering 376 (2021) 113638. doi:10.1016/j.cma.2020.113638.
- [23] H. Kobayashi, K. Yaji, S. Yamasaki, K. Fujita, Topology design of two-fluid heat exchange, Structural and Multidisciplinary Optimization 63 (2) (2021) 821-834. doi:10.1007/s00158-020-02736-8.
- [24] M. Audet, libDFEM: théorie et concepts, Tech. rep., Conseil national de recherches du Canada. Institut des matériaux industriels (2003).
- [25] M. Zhou, B. S. Lazarov, F. Wang, O. Sigmund, Minimum length scale in topology optimization by geometric constraints, Computer Methods in Applied Mechanics and Engineering 293 (2015) 266-282. doi:10.1016/j.cma.2015.05.003.
- [26] T. Tezduyar, S. Mittal, S. Ray, R. Shih, Incompressible flow computations with stabilized bilinear and linear equal-order-interpolation velocity-pressure elements, Computer Methods in Applied Mechanics and Engineering 95 (2) (1992) 221-242. doi:10.1016/0045-7825(92)90141-6.
- [27] J. Alexandersen, N. Aage, C. S. Andreasen, O. Sigmund, Topology optimisation for natural convection problems, International Journal for Numerical Methods in Fluids 76 (10) (2014) 699-721. doi:10.1002/fld.3954.
- [28] S. G. Johnson, The NLopt nonlinear-optimization package (2021).
- [29] K. Svanberg, A Class of Globally Convergent Optimization Methods Based on Conservative Convex Separable Approximations, SIAM Journal on Optimization 12 (2) (2002) 555-573. doi:10.1137/S1052623499362822.
- [30] A. Díaz, O. Sigmund, Checkerboard patterns in layout optimization, Structural optimization 10 (1) (1995) 40-45. doi:10.1007/BF01743693.
- [31] O. Sigmund, J. Petersson, Numerical instabilities in topology optimization: A survey on procedures dealing with checkerboards, mesh-dependencies and local minima, Structural optimization 16 (1) (1998) 68–75. doi:10.1007/BF01214002.
- [32] J. K. Guest, J. H. Prévost, T. Belytschko, Achieving minimum length scale in topology optimization using nodal design variables and projection functions, International Journal for Numerical Methods in Engineering 61 (2) (2004) 238-254. doi:10.1002/nme.1064.
- [33] O. Sigmund, Morphology-based black and white filters for topology optimization, Structural and Multidisciplinary Optimization 33 (4-5) (2007) 401-424. doi:10.1007/s00158-006-0087-x.
- [34] F. Wang, B. S. Lazarov, O. Sigmund, On projection methods, convergence and robust formulations in topology optimization, Structural and Multidisciplinary Optimization 43 (6) (2011) 767-784. doi:10.1007/s00158-010-0602-y.
- [35] C. Geuzaine, J.-F. Remacle, Gmsh: A 3-D finite element mesh generator with built-in pre- and post-processing facilities, International Journal for Numerical Methods in Engineering 79 (11) (2009) 1309-1331. doi:10.1002/nme.2579.
- [36] B. S. Lazarov, O. Sigmund, Filters in topology optimization based on Helmholtz-type differential equations, International Journal for Numerical Methods in Engineering 86 (6) (2011) 765–781. doi:10.1002/nme.3072.
- [37] C. Dapogny, C. Dobrzynski, P. Frey, Three-dimensional adaptive domain remeshing, implicit domain meshing, and applications to free and moving boundary problems, Journal of Computational Physics 262 (2014) 358-378. doi:10.1016/j.jcp.2014.01.005.
- [38] M. B. Giles, N. A. Pierce, An Introduction to the Adjoint Approach to Design, Flow, Turbulence and Combustion 65 (3) (2000) 393-415. doi:10.1023/A:1011430410075.
- [39] F. Navah, S. Nadarajah, A comprehensive high-order solver verification methodology for free fluid flows, Aerospace Science and Technology 80 (2018) 101-126. doi:10.1016/j.ast.2018.07.006.
9. Copyright:
- This material is "Farshad Navah, Marc-Étienne Lamarche-Gagnon, Florin Ilinca"'s paper: Based on "Thermofluid topology optimization for cooling channel design".
- Paper Source: https://arxiv.org/abs/2302.04745v2
This material was summarized based on the above paper, and unauthorized use for commercial purposes is prohibited.
Copyright © 2025 CASTMAN. All rights reserved.