This article introduces the paper "An Experimental and Computational Study on the Thermal Performance of Phase Change Material Heatsink Assemblies" presented at the ASME and Applied Thermal Engineering
1. Overview:
- Title: An Experimental and Computational Study on the Thermal Performance of Phase Change Material Heatsink Assemblies
- Author: Austin Jones
- Publication Year: May 2024 (Thesis), 2023 (ASME), 2024 (Applied Thermal Engineering)
- Publishing Journal/Academic Society: Thesis Submitted to Southern Illinois University Edwardsville, Proceedings of the ASME Heat Transfer Summer Conference, Applied Thermal Engineering
- Keywords: Phase Change Material, heatsink, thermal management
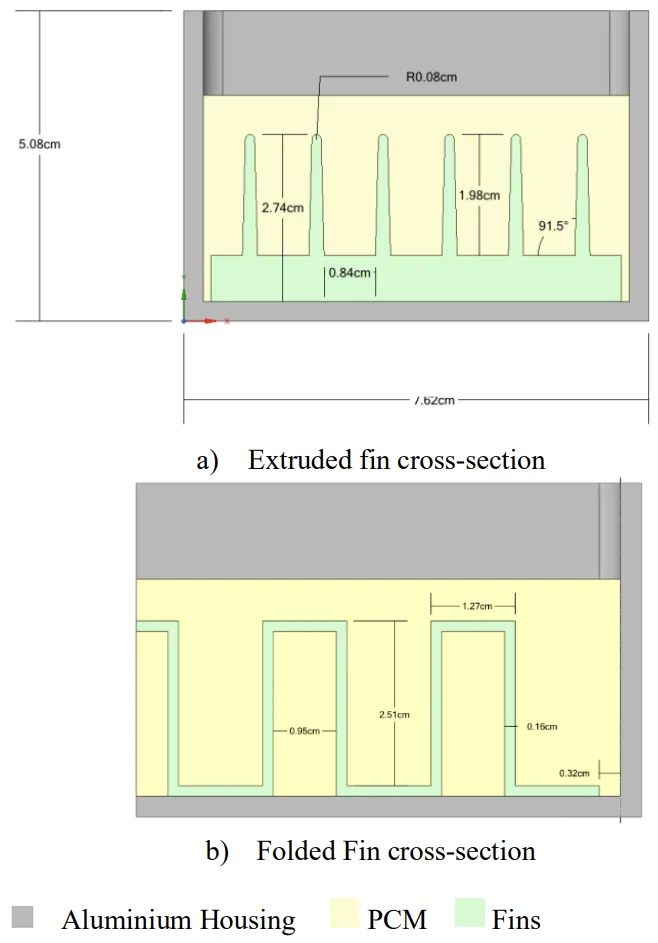
2. Research Background:
- Social/Academic Context of the Research Topic:
The demand for enhanced computing power within progressively smaller electronic device footprints has been steadily escalating. This trend leads to higher power density electronics that are prone to exceeding their operational temperature limits during standard duty cycles. Consequently, effective thermal management solutions are crucial for maintaining acceptable operating temperatures to ensure device reliability and safety. Phase Change Material (PCM) heatsinks are identified as a viable passive cooling solution, leveraging the high latent heat of fusion inherent in materials like paraffin wax to mitigate sensible heat increase during phase transition. - Limitations of Existing Research:
Traditional PCM heatsinks are constrained by the low thermal conductivity of most phase change materials. This limitation impedes the efficient transfer of heat away from electronic components, potentially leading to temperature overshoot despite the PCM undergoing melting. Existing approaches to enhance thermal conductivity, such as incorporating metallic nanoparticles or metal foams, often introduce trade-offs in cost, complexity, and latent heat storage capacity. - Necessity of the Research:
To overcome the limitations of PCM heatsinks, this research addresses the necessity to improve the thermal conductivity of PCM heatsink assemblies. The study focuses on innovative design modifications, specifically the integration of fin geometries and copper oxide nanoparticles, to optimize thermal performance without incurring excessive costs or compromising the inherent advantages of PCM-based cooling solutions.
3. Research Purpose and Research Questions:
- Research Purpose:
The primary research purpose is to experimentally and computationally investigate and optimize the thermal performance of PCM heatsink assemblies. This involves evaluating the effectiveness of modified fin geometries and the incorporation of copper oxide nanoparticles in enhancing heat dissipation and managing temperature in electronic devices. The study aims to provide valuable insights for optimizing PCM heatsink design to meet the cooling demands of future electronic power systems. - Key Research Questions:
This study seeks to answer the following key research questions:- How do modified fin geometries, specifically novel folded fin designs, affect the thermal effectiveness of PCM heatsinks compared to commercially available extruded fins?
- What is the impact of varying fin parameters such as fin orientation, fin thickness, and gap between fins on the overall thermal performance of PCM heatsink assemblies?
- How does the addition of copper oxide nanoparticles, both with and without fin integration, influence the thermal conductivity and heat storage capabilities of PCM heatsinks?
- What are the trade-offs between thermal conductivity enhancement and latent heat storage when designing finned PCM heatsinks?
- How can the geometry of PCM heatsinks be optimized in terms of device temperature and total operation time under varying heat loads and fin configurations?
- Research Hypotheses:
The central research hypothesis is that strategic modifications to fin geometry and the inclusion of copper oxide nanoparticles can significantly enhance the thermal conductivity of PCM heatsink assemblies, thereby improving their effectiveness in managing heat from electronic components. It is also hypothesized that there are significant tradeoffs between thermal conductivity and latent heat storage when designing a finned PCM heatsink. The study further explores the hypothesis that optimized fin geometries, such as folded fins, can offer superior thermal performance compared to conventional fin designs under specific operational conditions.
4. Research Methodology
- Research Design:
This research employs a mixed-methods approach, combining experimental and computational studies to evaluate the thermal performance of PCM heatsink assemblies. The experimental phase involves fabricating and testing custom heatsink prototypes, while the computational phase utilizes numerical modeling to simulate and analyze heat transfer phenomena within these assemblies. - Data Collection Method:
Experimental data was collected using a custom-built apparatus comprising a PCM heatsink assembly, a flexible silicone heater to simulate a heat source, thermocouples for temperature measurement, a data acquisition system, and a power supply. Temperature data at various points within the heatsink, along with voltage and current readings, were recorded during experiments. Paraffin wax, both pure and mixed with copper oxide nanoparticles, was used as the PCM. Tests were conducted under varying conditions, including different fin geometries (commercial extruded and novel folded fins), heat loads, and nanoparticle concentrations. - Analysis Method:
The computational analysis was performed using ANSYS Fluent, a finite element analysis software. A 3D numerical model of the heatsink assembly was created, incorporating the enthalpy-porosity method to simulate PCM melting and solidification. The model was validated against experimental data. Grid independence studies were conducted to ensure the accuracy of numerical results. Simulations were then used to examine the effects of various parameters, including fin geometry (gap and thickness), applied power, and nanoparticle addition, on the thermal behavior of the PCM heatsink. Data reduction techniques, including 1-D thermal resistance analysis and uncertainty analysis based on Kline and McClintock method [11], were applied to both experimental and computational results. - Research Subjects and Scope:
The research subjects are PCM heatsink assemblies designed for cooling electronic components. The scope of the study includes:- Evaluation of two fin geometries: commercially available extruded fins and novel folded fins.
- Use of pure paraffin wax and paraffin wax mixed with 1.5% copper oxide nanoparticles as PCM.
- Experimental and numerical investigation of heatsink performance under varying heat loads (16W to 64W).
- Analysis of fin parameter variations, including fin thickness (0.8mm to 2.4mm) and fin gap (2.32mm to 5.52mm).
- Computational domain modeled as a quarter of the heatsink assembly due to symmetry, with dimensions based on fabricated prototypes (15.24cm × 7.62cm × 5.08cm aluminum housing).
- Material properties for aluminum housing (AL6061) and PCM (RT60 paraffin wax and CuO nanoparticles) sourced from ANSYS Fluent library, experimental measurements, and material data sheets [12].
5. Main Research Results:
- Key Research Results:
- Folded fin geometry demonstrated an 11% increase in the time required to fully melt the PCM compared to commercial extruded fins, but resulted in a 6.5% higher heat source interface temperature. This indicates a trade-off where folded fins offer extended operation time at the expense of slightly higher component temperature during operation.
- Thinner fins (0.8 mm wall thickness) increased the melt time by 17% compared to thicker fins (2.4 mm), suggesting that reduced fin thickness can enhance latent heat storage duration, albeit with a minor (4%) increase in interface temperature.
- Larger fin gaps (5.52 mm) resulted in the longest melt time (3093 s), but also the highest interface temperature, indicating that fin spacing affects both thermal storage capacity and heat dissipation efficiency.
- Addition of 1.5% copper oxide nanoparticles to paraffin wax decreased the heat source interface temperature by 5°C and improved the final operating temperature by 8.75% compared to pure paraffin wax configurations, highlighting the effectiveness of nanoparticles in enhancing thermal conductivity.
- Numerical simulations, validated by experimental data, closely matched experimental results, confirming the reliability of the computational model for predicting PCM heatsink performance.
- Statistical/Qualitative Analysis Results:
- Experimental data showed less than 6% difference between repeated tests, indicating good repeatability.
- Uncertainty analysis estimated a relative uncertainty in heat flux of ±0.8%.
- Grid independence study confirmed that a mesh with over 350,000 nodes provided results independent of mesh size.
- Quantitative comparisons were made for melt times and interface temperatures across different fin geometries, thicknesses, gaps, and nanoparticle additions, demonstrating statistically significant trends in thermal performance.
- Qualitative observations from temperature and liquid fraction contour plots provided visual insights into the PCM melting process and the influence of design parameters on heat distribution.
- Data Interpretation:
- The results indicate a significant trade-off between thermal conductivity and latent heat storage in PCM heatsink design. Folded fins, while extending melt time, lead to higher operating temperatures due to reduced fin volume and potentially lower effective thermal conductivity compared to extruded fins.
- Thinner fins and larger fin gaps, while increasing melt duration, also tend to elevate interface temperatures, suggesting a balance is needed to optimize both heat storage and dissipation.
- Copper oxide nanoparticles effectively enhance thermal conductivity, reducing operating temperatures and improving overall thermal management.
- The choice of optimal fin geometry and PCM composition depends on the specific application requirements, particularly the acceptable operating temperature range and desired duty cycle duration. For applications prioritizing longer operation times and capable of tolerating slightly higher temperatures, folded fins and thinner fin designs may be suitable. For applications requiring lower operating temperatures, nanoparticle-enhanced PCM and potentially extruded fins may be preferred.
- Figure Name List:
- Figure 1 Cross sectional drawing of heatsink geometry
- Figure 2 Schematic of the experimental setup
- Figure 3 A 3D schematic of the computational domain
- Figure 4 Comparison of experimental and simulation results at the heat source interface
- Figure 5 Temperature contours for simulation of commercial extruded fins at an input power of 32 W
- Figure 6 Liquid Fraction contours for simulation of commercial fins at an input power of 32 W
- Figure 7 Heat source interface temperature at 3 different input power values for extruded fins
- Figure 8 Heat source interface temperature at 3 different input power values for folded fins
- Figure 5. Grid Independence Study.
- Fig. 6. Comparison of heat source interface temperature between heatsink design with and without PCM.
- Fig. 7. Comparison of simulation and experimental results.
- Fig. 8. Contours of liquid fraction and temperature.
- Fig. 9. Effect of varying applied power on liquid fraction at a fin gap of 3.92 mm and a fin wall thickness of 1.6 mm.
- Fig. 10. Effect of varying applied power on interface temperature at a fin gap of 3.92 mm and a fin wall thickness of 1.6 mm.
- Fig. 11. Effect of varying fin thickness on liquid fraction at a fin gap of 3.92 mm and an applied power of 32 W.
- Fig. 12. Effects of varying fin thickness on interface temperature at a fin gap of 3.92 mm and an applied power of 32 W.
- Fig. 13. Effect of varying fin gap on liquid fraction at a fin wall thickness of 1.6 mm and an applied power of 32 W.
- Fig. 14. Effects of varying fin gap on interface temperature at a fin wall thickness of 1.6 mm and an applied power of 32 W.
- Figure 2 Schematic of the experiment assembly
- Figure 3 A 3D schematic of the computational domain
- Figure 4 Comparison of heat source interface temperature for experiment and simulation
- Figure 5 Comparison of experimental results for different fin geometries
- Figure 6 Experimental results for no fin and folded fin cases, with and without copper oxide nanoparticles
- Figure 7 Temperature contours for simulation of folded fins at an input power of 16 W
- Figure 8 Liquid Fraction contours for simulation of folded fins at an input power of 16 W
- Figure 9 Comparison of Folded Fin Heatsink Assembly with RT50, RT60, RT70HC
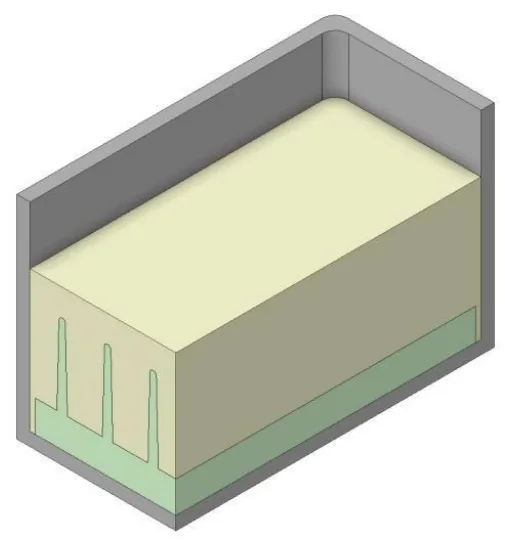
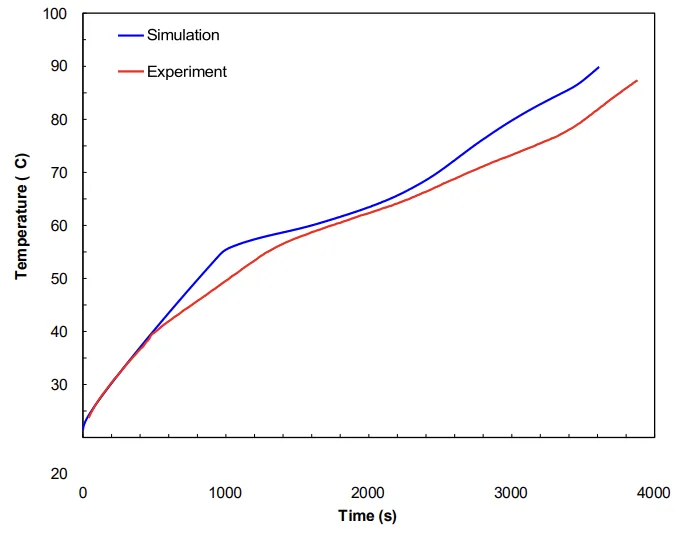
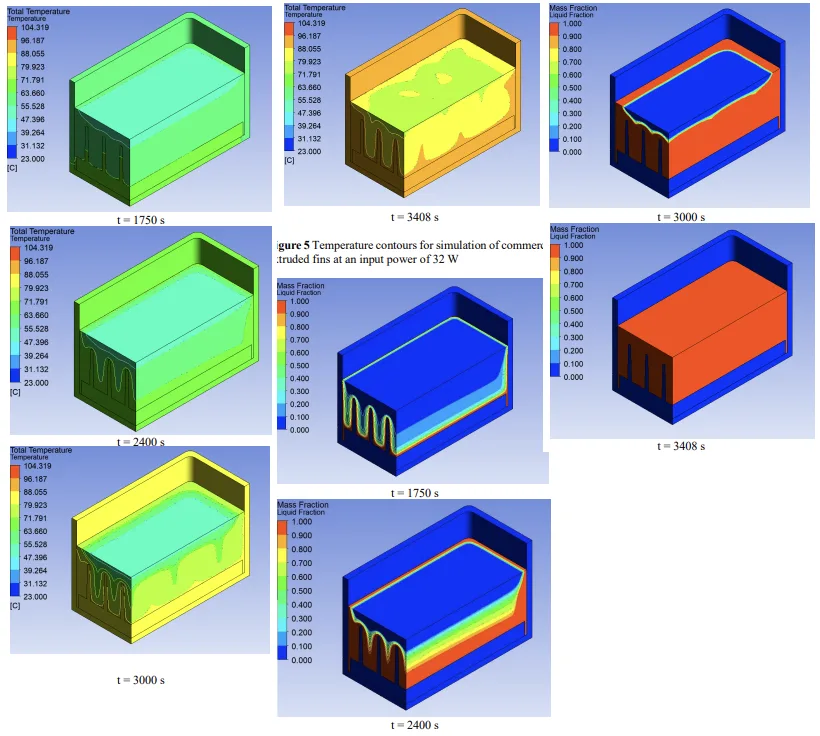
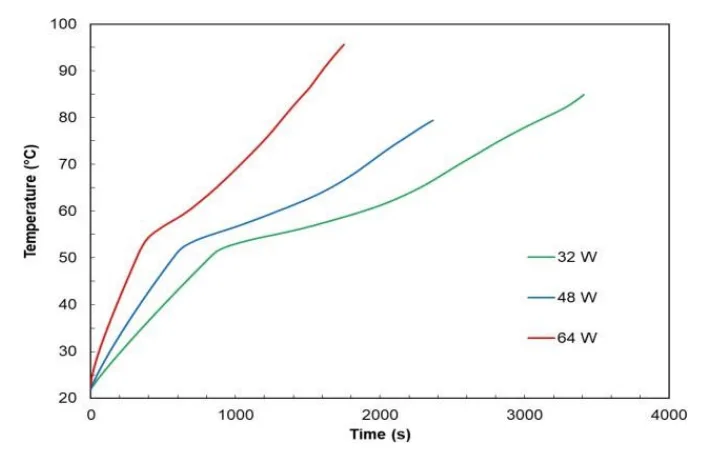
6. Conclusion and Discussion:
- Summary of Main Results:
This study experimentally and numerically investigated PCM heatsink assemblies with novel folded fins, comparing their performance to commercial extruded fins and a no-fin baseline. The folded fin design demonstrated a balance between extended melt times and manageable interface temperatures, particularly when combined with copper oxide nanoparticles. Parameter studies revealed that thinner fins and larger fin gaps can prolong melt times, while nanoparticle addition effectively reduces operating temperatures. The optimal configuration depends on the specific thermal requirements of the electronic device being cooled. - Academic Significance of the Research:
This research contributes to the academic understanding of PCM heatsink design by providing a detailed comparative analysis of different fin geometries and PCM enhancements. The validated computational model offers a valuable tool for future heatsink design and optimization studies. The findings highlight the complex interplay between fin geometry, PCM properties, and thermal performance, offering nuanced insights beyond simple thermal conductivity enhancement. - Practical Implications:
The practical implications of this study are significant for the design of passive cooling solutions for electronic devices, especially in scenarios with cyclical power demands. The results suggest that folded fin PCM heatsinks, particularly when enhanced with nanoparticles, can offer improved thermal management for high-power density electronics. The study provides guidance for engineers in selecting appropriate fin geometries, PCM materials, and nanoparticle additives to optimize heatsink performance based on specific application needs and thermal constraints. The findings are directly applicable to devices of similar size and power demands, aiming to increase the effectiveness of thermal cooling systems for devices with cyclical power demand. - Limitations of the Research:
The research is limited to the specific fin geometries (extruded and folded) and PCM materials (paraffin wax and copper oxide nanoparticles) tested. Further research is needed to explore a broader range of fin designs, PCM compositions, and operational conditions. The study primarily focused on a constant heat flux scenario; real-world electronic devices may exhibit more complex and transient heat generation profiles. The long-term performance and reliability of nanoparticle-enhanced PCM heatsinks, including potential nanoparticle settling or agglomeration, were not assessed in this study.
7. Future Follow-up Research:
- Directions for Follow-up Research:
Future research should focus on further optimization of the folded fin geometry, exploring variations in fin shape, spacing, and orientation to maximize thermal performance. Investigating the synergistic effects of combining optimized fin geometries with different types and concentrations of nanoparticles is another promising direction. Exploring alternative PCM materials with higher thermal conductivity and latent heat of fusion, and lower melting temperatures could also enhance heatsink performance. - Areas Requiring Further Exploration:
Areas requiring further exploration include:- Investigating the performance of optimized PCM heatsinks under transient and variable heat load conditions to better simulate real-world electronic device operation.
- Conducting long-term reliability studies to assess the thermal cycling stability and nanoparticle dispersion stability in enhanced PCM heatsinks.
- Exploring cost-effective manufacturing methods for folded fin heatsinks and nanoparticle-enhanced PCMs to facilitate practical implementation.
- Expanding the computational model to incorporate more complex heat transfer phenomena, such as natural convection within the PCM and radiative heat transfer from the heatsink surface.
- Investigating the potential for integrating active cooling elements, such as micro-fans or thermoelectric coolers, with optimized PCM heatsinks to create hybrid cooling solutions for extreme thermal management challenges.
8. References:
- [1] Yang, T., King, W., and Milijkovic, N., 2021, “Phase Change Material-based Thermal Energy Storage" Cell Reports Physical Science Vol. 2.
- [2] Chen Z., Xuelai Z., Jun J., and Yuyun L., 2022, “A review of the application of hydrated salt phase change materials in building temperature control,” Journal of Energy Storage, Volume 56, Part C.
- [3] Arshad A., Jabbal M., Faraji H., Talebizadehsardari P., Bashir M., and Yan Y., 2022, "Thermal performance of a phase change material-based heat sink in presence of nanoparticles and metal-foam to enhance cooling performance of electronics" Journal of Energy Storage, Vol. 48.
- [4] Colla L., Ercole D., Fedele L., Mancin S., Manca O., and Bobbo S., 2017, "Nano-Phase Change Materials for Electronics Cooling Application,” ASME. Journal of Heat Transfer, Vol. 135.
- [5] Fan, L., Zhu, Z., Zeng, Y., Xiao, Y., Liu, X., Wu, Y., Ding, Q., Yu, Z., and Cen, K., 2015, “Transient performance of a PCM-based heat sink with high aspect-ratio carbon nanofillers," Applied Thermal Engineering, Vol. 75 pp. 532-540.
- [6] Alimohammadi M., Aghli Y., Sadat E., Sardarabadi M., Passandideh-Fard M., 2017, “Experimental investigation of the effects of using nano/phase change materials (NPCM) as coolant of electronic chipsets, under free and forced convection.” Applied Thermal Engineering, Vol. 111 pp. 271–279.
- [7] Jaworski M., 2012, “Thermal Performance of Heat Spreader for Electronics Cooling with Incorporated Phase Change Material." Applied Thermal Engineering, Vol. 35 pp. 212-219.
- [8] Baby R., Balaji C., 2017, "Optimization of Phase Change Material (PCM) – Based Heat Sink for Electronics Cooling Application" M.S. Thesis, Department of Materials Science Engineering, University of California, Riverside.
- [9] Taremi N., 2013, “Experimental investigation on carbon nano tubes coated brass rectangular extended surfaces.” Applied Thermal Engineering, Vol. 50 pp. 1361-1368.
- [10] Incorpera, F. P., DeWitt, D. P., Bergman, T. L., and Lavine, A. S., 2006, Fundamentals of Heat and Mass Transfer, John Wiley & Sons; 6th edition, New York.
- [11] Kline, S., and McClintock J., 1953, “Describing Uncertainties in Single Sample Experiment." Mechanical Engineering, Vol. 75 pp. 3-9.
- [12] "Data sheet - Rubitherm.” [Online]. Available: https://www.rubitherm.eu/media/products/datasheets/Techdata_-RT60_EN_09102020.PDF. [Accessed: 12-Mar-2023].
- [13] Mohammad Ghalambaz, Jun Zhang,2020, “Conjugate solid-liquid phase change heat transfer in heatsink filled with phase change material-metal foam”, International Journal of Heat and Mass Transfer, Vol 146.
- [14] Mohammad Ghalambaz, S.A.M. Mehryan, Ahmad Hajjar, Ali Veismoradi, 2020, “Unsteady natural convection flow of a suspension comprising Nano-Encapsulated Phase Change Materials (NEPCMs) in a porous medium”, Advanced Powder Technology, Vol. 21, Issue 3.
- [15] Salma Gharbi, Souad Harmand, Sadok Ben Jabrallah, 2015, “Experimental Comparison Between Different Configurations of PCM Based Heat Sinks for Cooling Electronic Components", Applied Thermal Engineering, Vol. 87. pp. 454-462.
- [16] Zhen Qin, Chenzhen Ji, Zhenghua Low, Swapnil Dubey, Fook Hoong Choo, Fei Duan, 2017, "Effect of Fin Location on the Latent Heat Storage: A Numerical Study”, Energy Procedia, Vol. 143., pp. 320-326.
- [17] Debich B., Yaich A., Dammak K., El Hami A, Gafsi W., Walha L., Hadder M., 2020, “Design Optimization of PCM-Based Finned Heat Sinks for Mechatronic Components: A Numerical Investigation and Parametric Study.” Journal of Energy Storage, Vol. 32.
- [18] Bondareva, N.S., Sheremet, M.A., 2022, “Numerical study of PCMs arrangement effect on heat transfer performance in plate-finned heat sink for passive cooling system”, J Therm Anal Calorim, Vol. 147.
- [19] Choudhari V.G., Dhoble A.S., Panchal Satyam, 2020, “Numerical Analysis of Different Fin Structures in Phase Change Material Module for Battery Thermal Management System and its Optimization”, International Journal of Heat and Mass Transfer, Vol. 163.
- [20] V. Shatikian, G. Ziskind, R. Letan, 2005, “Numerical Investigation of a PCM-Based Heat Sink with Internal Fins”, International Journal of Heat and Mass Transfer, Vol. 48, Issue 17, pp. 3689-3706.
- [21] Kalbasi, Rasool, 2021, “Introducing a Novel Heat Sink Comprising PCM and air - Adapted to Electronic Device Thermal Management”, International Journal of Heat and Mass Transfer, Vol. 169.
- [22] Pingrui Huang, Gaosheng Wei, Liu Cui, Chao Xu, Xiaoze Du, 2021, “Numerical Investigation of a Dual-PCM Heat Sink Using Low Melting Point alloy and Paraffin”, Applied Thermal Engineering, Vol. 189.
- [23] Hadidi, B., Veysi, F. & Ghasemi, R., 2023, “Experimental investigation of the effects of using PCM, multi-PCMs, and forced convection on heat sinks for thermal management of electronic devices”, J Therm Anal Calorim, Vol. 148.
- [24] Babak Kamkari, Hossein Shokouhmand, 2014, “Experimental Investigation of Phase Change Material Melting in Rectangular Enclosures with Horizontal Partial Fins”, International Journal of Heat and Mass Transfer, Vol. 78, pp. 839-851.
- [25] R. Pakrouh, M.J. Hosseini, A.A. Ranjbar, R. Bahrampoury, 2015, “A Numerical Method for PCM-Based Pin Fin Heat Sinks Optimization”, Energy Conversion and Management, Vol. 103, pp. 542-552.
- [26] Hafiz Muhammad Ali, Muhammad Junaid Ashraf, Ambra Giovannelli, Muhammad Irfan, Talal Bin Irshad, Hafiz Muhammad Hamid, Faisal Hassan, Adeel Arshad, 2018, “Thermal Management of Electronics: An Experimental Analysis of Triangular, Rectangular and Circular Pin-Fin Heat Sinks for Various PCMs”, International Journal of Heat and Mass Transfer, Vol. 123, pp. 272-284.
- [27] Nadezhda S. Bondareva, Mikhail A. Sheremet, 2017, “3D Natural Convection Melting in a Cubical Cavity with a Heat Source”, International Journal of Thermal Sciences, Vol. 115, pp. 43-53.
- [28] Chenzhen Ji, Zhen Qin, Swapnil Dubey, Fook Hoong Choo, Fei Duan, 2018, “Simulation on PCM Melting Enhancement with Double-Fin Length Arrangements in a Rectangular Enclosure Induced by Natural Convection”, International Journal of Heat and Mass Transfer, Vol. 127, Part C, pp. 255-265.
- [29] Xie, J., Choo Kok Fah, Jianhua Xiang, Hsiao Mun Lee, 2019, “Characterization of Natural Convection in a PCM-Based Heat Sink with Novel Conductive Structures”, International Communications in Heat and Mass Transfer, Vol. 108.
- [30] “ANSYS FLUENT Documentation” [Online]. Available: https://www.afs.enea.it/project/neptunius/docs/fluent/index.htm. [Accessed: 12-Mar-2023].
- [31] Jones A., Darabi J., 2024, “Effect of Fin Geometry on the Thermal Performance of a Phase Change Material Heatsink”, Applied Thermal Engineering, Vol 236, Part E.
9. Copyright:
- This material is "Austin Jones"'s paper: Based on "An Experimental and Computational Study on the Thermal Performance of Phase Change Material Heatsink Assemblies".
- Paper Source: [DOI URL]
This material was summarized based on the above paper, and unauthorized use for commercial purposes is prohibited.
Copyright © 2025 CASTMAN. All rights reserved.