This article introduces the paper "Computer Aided Design Library of Gating System for a Die Casting" presented at the "International Journal of Applied Studies (IJAS)"
1. Overview:
- Title: Computer Aided Design Library of Gating System for a Die Casting
- Authors: Chandan Deep Singh, Sukhjinder Singh, Varun Panwar, Sheetal Bansal
- Publication Year: January 2014
- Publishing Journal/Academic Society: International Journal of Applied Studies (IJAS), Volume: 1, Issue: 1
- Keywords: Die-Casting, Gating System, CAD/CAM, Design
![Figure 1 Gating system nomenclature [Casting Plant & Technology]](https://castman.co.kr/wp-content/uploads/image-350-png.webp)
2. Research Background:
- Social/Academic Context of the Research Topic: Die casting is a 'near net shape' manufacturing process widely utilized for producing high-quality components across various engineering sectors. Its advantages include high production rates, cost-effectiveness, enhanced quality, and process automation. Designing die casting tooling, particularly the gating system, is a critical and intricate step in die manufacturing. Activities such as cavity design, cavity layout, and gating system design are fundamental to the overall die casting die design process.
- Limitations of Existing Research: Designing a gating system for die casting is influenced by numerous parameters related to part design, die casting machines, and die casting alloys. Traditionally, this process relies heavily on manual input and iterative design adjustments, demanding significant expertise in die casting. While CAD/CAM tools are prevalent in modern die casting die design and manufacturing, the necessity for expert intervention throughout the gating system design phase makes it a time-consuming and potentially expensive bottleneck. Existing CAD systems for die casting often lack automated gating system design capabilities, or are limited to simple geometries and require substantial user input. Prior research, as reviewed in the paper, indicates gaps in feature libraries for gates, runners, and overflow designs within existing CAD systems.
- Necessity of the Research: The paper highlights the need for automating gating system design to reduce lead times, improve design quality, ensure design consistency, and minimize human effort. The iterative nature of manual gating system design is described as "very prolonged and pricey" [Lee et al., 2004]. Therefore, developing a system for automated gating system generation is crucial to bridge the gap between die casting design and manufacturing, enhancing efficiency and reducing reliance on expert-driven manual processes.
3. Research Purpose and Research Questions:
- Research Purpose: The primary research purpose is to develop a CAD library for gating systems in die casting dies. This library aims to automate the design process by incorporating die casting process knowledge, machine parameters, and alloy properties to determine gating system parameters and generate CAD models of gating components.
- Key Research Questions:
- How can a feature library be developed to represent different types of gates, runners, and overflow wells for die casting?
- Can a CAD system be designed to automatically generate gating system designs based on input CAD files of die casting parts and die casting process knowledge?
- How effective is a feature-based parametric approach in generating CAD models of gating system components?
- Research Hypotheses: While not explicitly stated as hypotheses, the research operates under the premise that:
- A CAD library of gating system features can significantly automate and improve the efficiency of gating system design.
- Parametric design principles, combined with a feature library, can effectively generate CAD models of gating system components.
- An automated system can reduce design lead time, improve quality, and bring consistency to gating system design compared to manual methods.
4. Research Methodology
- Research Design: The research adopts a development and implementation approach, focusing on creating a CAD library and a system for automated gating system design. It involves conceptualizing and designing a feature library for gating system components (runners, gates, overflow wells).
- Data Collection Method: The paper does not explicitly detail data collection in the traditional sense of empirical data. However, the "die casting process, machine and alloy knowledge" are used as input to determine gating system parameters. The system's effectiveness is evaluated by testing it on "a number of industrial parts."
- Analysis Method: The research focuses on the development and testing of the proposed system. The "results found are quite encouraging," suggesting a qualitative assessment of the system's performance based on its application to industrial parts. The paper mentions the system "would go a long way in bridging the gap between designing and manufacturing of die-casting," indicating a practical validation of the system's utility.
- Research Subjects and Scope: The research scope is focused on the design of gating systems for die casting dies. The system is designed to take a CAD file of a die casting part as input and generate a CAD model of the gating system. The types of gating system components considered include runners, gates, and overflows. The system's applicability is tested on "a number of industrial parts," suggesting a practical, industry-relevant scope.
5. Main Research Results:
- Key Research Results: The primary outcome of this research is the proposal and development of a feature library for gating system components. This library, coupled with parametric design principles, enables the automated generation of CAD models for runners, gates, and overflows. The system is designed to utilize CAD input of the die casting part and incorporate knowledge of die casting processes, machines, and alloys to determine gating system parameters.
- Statistical/Qualitative Analysis Results: The paper states that the system has been "tested on a number of industrial parts and results found are quite encouraging." This suggests a qualitative evaluation where the system's performance was deemed satisfactory based on its practical application. No specific statistical or quantitative analysis is presented in the paper.
- Data Interpretation: The encouraging results imply that the proposed feature library and automated system are effective in generating gating system designs. The system's ability to generate CAD models of gating components based on part geometry and process knowledge suggests a significant step towards automating die casting die design.
- Figure Name List:
- Figure 1: Gating system nomenclature [Casting Plant & Technology]
- Figure 2: Overflow Well
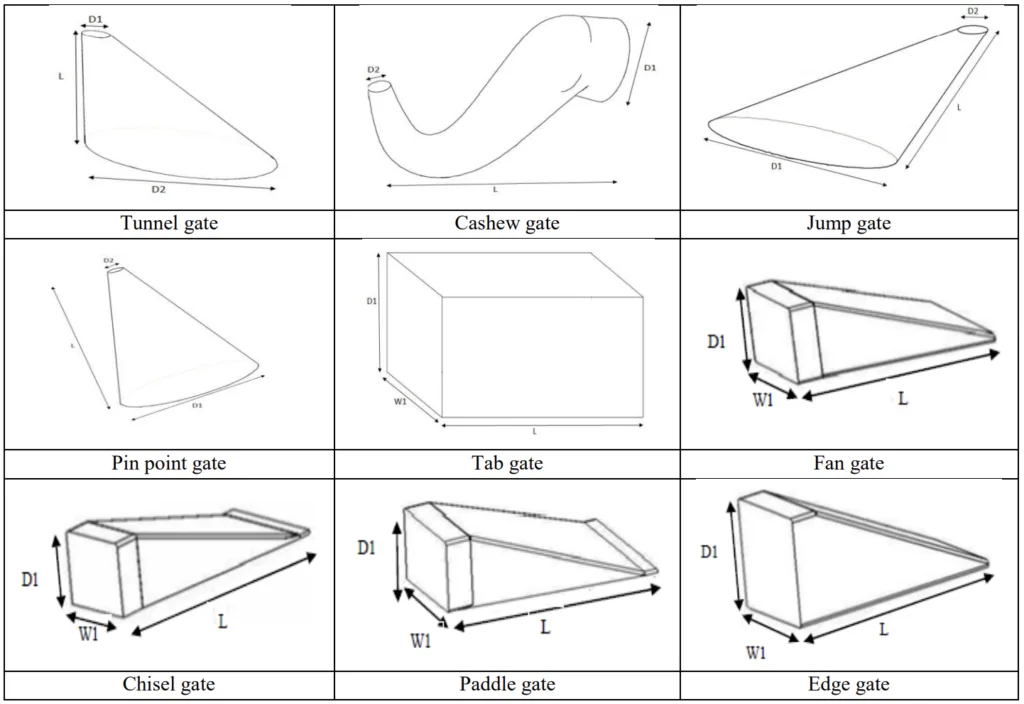
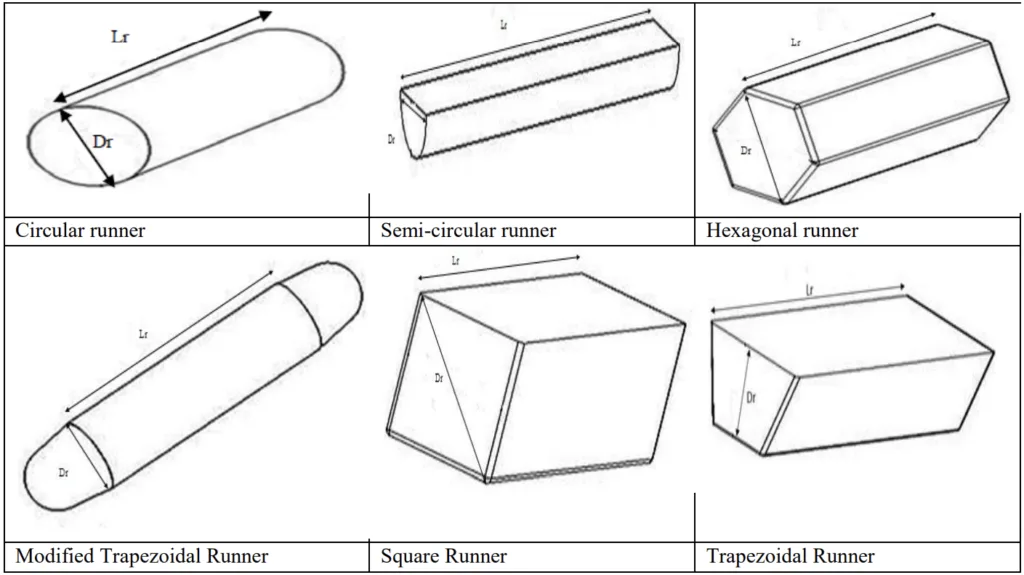
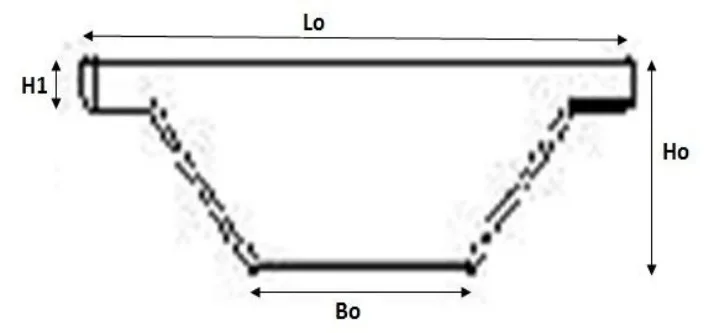
6. Conclusion and Discussion:
- Summary of Main Results: The research successfully proposed and developed a CAD library for gating system design in die casting. This library, combined with parametric design, automates the generation of CAD models for gating system components like runners, gates, and overflows. The system leverages die casting process knowledge and CAD input of the part. Testing on industrial parts yielded encouraging results, indicating the system's potential.
- Academic Significance of the Research: This research contributes to the field of die casting by addressing the critical challenge of automating gating system design. The proposed feature library and parametric CAD system represent an advancement in CAD/CAM applications for die casting, potentially reducing the reliance on manual, expert-driven design processes. It provides a framework for integrating die casting knowledge into a CAD environment for automated design generation.
- Practical Implications: The practical implications of this research are significant for the die casting industry. The automated gating system design tool promises to:
- Reduce design lead time: Automating the design process can significantly shorten the time required to develop gating systems.
- Improve quality: Consistent and knowledge-based automated design can lead to improved gating system designs and, consequently, casting quality.
- Bring consistency in design: The feature library ensures a standardized approach to gating system design.
- Reduce Human Effort involved: Automation minimizes the need for manual design iterations and expert intervention, freeing up valuable engineering resources.
- Limitations of the Research: The paper acknowledges that the system is currently limited to "simple shapes." Further development is needed to incorporate "parts with complex geometrical features" and to enhance the "feature library for gating system." The system's capability for "gating design for multiple cavity die" is also identified as a future area for inclusion.
7. Future Follow-up Research:
- Directions for Follow-up Research: The authors explicitly suggest several directions for future research:
- Incorporating complex geometries: Expanding the system's capability to handle die casting parts with complex geometrical features.
- Enhancing the feature library: Further enriching the feature library with more diverse and advanced gating system components and design rules.
- Multi-cavity die design: Extending the system to support the design of gating systems for multi-cavity die casting dies.
- Areas Requiring Further Exploration: Beyond the explicitly stated future directions, further exploration could include:
- Quantitative performance evaluation: Conducting more rigorous quantitative testing and benchmarking of the system's performance against manual design methods, measuring metrics like design time, casting quality, and defect rates.
- Integration with CAE software: Exploring tighter integration with CAE software (like MAGMASOFT) for simulation and optimization of the automatically generated gating systems.
- User interface and usability studies: Developing a user-friendly interface and conducting usability studies to ensure the system is practical and accessible for die casting engineers.
8. References:
- [1] Choi, J.C., Kwon, T.H., Park, J.H., Kim, J.H., and Kim, C.H., “A study on development of a die design system for die casting”, Int. J Adv.Manuf.Technol 20:pp. 1-8, 2002.
- [2] Hu B.H., Tong K.K., Niu X.P., Pinwill I. "Design and optimazation of runner and gating system for die casting of thin walled magnesium telecommunication parts through numerical Simulation" Journal Of Material Processing Technology 105, pp. 128-133, 2000
- [3] Kim. C., and kwon H.T., “A runner gate design system for die casting dies". 2000
- [4] Lee, K.S., and Lin, J.C., “Design of runner and gating system parameters for a multi-cavity injection mold using FEM and neural network”, Int. J Adv.Manuf.Technol 27:pp. 1089-1096, 2006.
- [5] Lee, K.S., Fuh, J.Y.H., and Wu, S.H.,, “Development of semi-automated die casting die design system”, Proc. Instn. Mech. Engrs Vol. 216, Part B: J Engineering Manufacture, pp.1557-1588, 2002.
- [6] Lee K.S., Wu, S.H., Fuh, and J.Y.H., “Semi-automated parametric design of gating systems for die casting die", Computers and Industrial Engineering53, 2: pp. 222-232, 2007
- [7] Lee, K.S., and Woon, Y.K., “Development of a die design for die casting”, Int. J Adv.Manuf.Technol 23:pp. 399-411,(2004
- [8] Lee K.S., Wu, S.H., Fuh, and J.Y.H., (2002), “Feature based parametric design of gating system for die casting die", Journal of Advanced Manufacturing technology, 19:pp. 821-829, 2002.
- [9] Lin, J.C., “Selection of the optimal gate location for a die casting die with a freeform surface", Int. J Adv.Manuf.Technol 19:pp. 278-284, 2002.
- [10] Lin., and Tai., “A runner optimization study of a Die Casting Die", Journal of Materials Processing Technology 84, pp. 1–12, 1998.
- [11] Reddy, A.P., Pande S.S., and Ravi B.,, “Computer aided design of die casting dies", IIF transactions(94-19),pp. 239-245, 1994.
- [12] Singh, C.D., Madan,J., and Singh, A., “Computer aided design of gating system for die casting die.". Int. J. Computer Applications in Technology, Vol. 46, No. 2, 201, pp: 113-127, 2013.
- [13] Singh,C.D., "Feature library of gating system for a die casting die”, International Journal on Emerging Technology, pp: 93-100, 2012.
- [14] Singh, C.D., "Automated determination of gating system parameters for a die casting die", International Journal on Emerging Technology, 3(2): pp. 84-89, 2012.
- [15] Singh,C.D., and Singh, R., "Study of design of gating system for a die casting die-A review”, International Conference on Advancement and Futuristic Trends In Mechanical Engineering. pp: 53-63, October, 5-7, 2012.
- [16] Singh.C.D., "Computer aided design of gating system for a die casting die", thesis, 2011
- [17] Sulaiman, S., and Keen T.C., "Flow analysis along the runner and gating system of a casting process”, Journal of material processing technology 63: pp. 690-695, 1997.
- [18] Weishan Z., Shoumei X., Baicheng L., “A Study on a CAD/CAE system of die casting", Journal Of Material Processing Technology 63, pp. 707-711, 1997.
- [19] Wong Yoon Khai, “Development of windows based computer die design system for die casting dies”. ,2003.
- [20] Yue S., Wang G., Yin F., Wang Y., Yang J. "Application of an integrated CAD/CAE/CAM System for die casting dies", Journal Of Material Processing Technology 139, pp. 465-468, 2003.
- [21] Zahi, M., Lam, Y.C., and Au, C.K., “Runner sizing in multiple cavity injection mold by non-dominated sorting genetic algorithm", Engineering with Computers 25:pp. 237-245,2009.
- [22] Bill Anderson, “Die Casting Engineering: a hydraulic, thermal and mechanical process”, Marcel Dekker, 2005.
- [23] Geoffrey Boothroyd, Peter Dewhurst, Winston Knight, "Product Design for Manufacture and Assembly” CRC Press, 2004.
- [24] Frank E.Goodwin, “Handbook of Metallurgical Process Design",CRC Press, 2004.
- [25] Jay Shoemaker, “Moldflow Design Guide", Hanser Publishers, Munich, 2006.
- [26] John P. Beaumont, “Runner and Gating Design Handbook", Hanser Publishers, Munich, 2007.
- [27] Pye, R.G.W., “Injection Mould Design", Affiliated East-West press Pvt Ltd, New Delhi, 2000.
- [28] Richard A. Flinn, “Fundamentals of Metal Casting”, Addison-Wesley Publishing Company, Inc., 1962.
- [29] "Automatic Computerised optimization in die casting”, Casting Plant & Technology 4/2008.
- [30] http://www.brockmetal.co.uk/papers/14_runner_design_guide_lines_issue_5.php
- [31] http://www.chinyen-engineering.com/english/product-hot-standard.html
- [32] http://www.die casting.org/faq/
- [33] http://www.themetalcasting.com/casting-parting-line.html
- [34] http://en.wikipedia.org/wiki/Computer-aided_design
- [35] http://en.wikipedia.org/wiki/Computer-aided_manufacturing
- [36] http://en.wikipedia.org/wiki/Die_casting
- [37] http://www.custompartnet.com/wu/die casting
- [38] http://dc435.4shared.com/doc/4ZuYyzVq /preview_html_27bd02ea.jpg
- [39] http://www.brockmetal.co.uk/papers/ 14_runner_design_guide_lines_issue_5.php
- [40] http://www.lkadvantage.com/
9. Copyright:
- This material is Chandan Deep Singh, Sukhjinder Singh, Varun Panwar, Sheetal Bansal's paper: Based on "Computer Aided Design Library of Gating System for a Die Casting".
- Paper Source: https://www.researchgate.net/publication/280324770
This material was summarized based on the above paper, and unauthorized use for commercial purposes is prohibited.
Copyright © 2025 CASTMAN. All rights reserved.