This article introduces the paper "Clinching of Heated Aluminum Die Casting" presented at the "WGP 2021, LNPE, Springer Nature Switzerland AG 2022"
1. Overview:
- Title: Clinching of Heated Aluminum Die Casting
- Authors: S. Yarcu, S. Huebner, D. Yilkiran, K. Brunotte, B.-A. Behrens, T. Schuchardt, S. Mueller, and K. Dilger
- Publication Year: 2022
- Publishing Journal/Academic Society: WGP 2021, published in LNPE (Lecture Notes in Production Engineering), Springer Nature Switzerland AG
- Keywords: Joint clinching, Die cast, Heated clinching, Tempered clinching
![Fig. 1. Aluminum-intensive mixed construction using the Audi TT Coupé as an example [3].](https://castman.co.kr/wp-content/uploads/image-340-1024x307.webp)
2. Research Background:
In contemporary automotive manufacturing, the utilization of multi-material bodies (MMB) is increasingly prevalent. This approach addresses the complex demands of lightweight construction, cost optimization, and stringent performance criteria, particularly stiffness. However, the inherent disparities in electrochemical potentials, mechanical properties, and thermal expansion coefficients among dissimilar materials introduce significant challenges in joining technologies and corrosion mitigation. Conventional joining methodologies, such as resistance spot welding, commonly employed in body construction, are often inadequate for joining aluminum and steel due to their divergent thermal characteristics. Clinching emerges as a viable alternative for such applications.
Aluminum die cast alloys, however, exhibit limited clinching capability in their as-cast condition due to their inherent brittleness. Prior research has demonstrated that direct clinching of these alloys in their initial state frequently results in surface cracking at the joint. Existing studies have explored alternative joining methods for aluminum die casting, including self-pierce riveting and friction stir scribe. Jäckel et al. [5] investigated self-pierce riveting, mitigating cracking through optimized tool geometry but at the cost of reduced interlock. Neuser et al. [6] further explored self-pierce riveting with varied tool configurations, achieving crack reduction using a flat die without compromising joint strength. Hovanski et al. [7] examined friction stir scribe, highlighting the sensitivity of die cast joints to bending and premature failure due to material brittleness.
These limitations underscore the necessity for innovative approaches to enhance the clinchability of aluminum die casting alloys, particularly for robust and crack-free joint formation in MMB applications.
3. Research Purpose and Research Questions:
Research Purpose:
The primary objective of this research is to enhance the clinching performance of aluminum die casting alloys when joined with sheet metal. This is achieved through the integration of local annealing via controlled heating strategies, aiming for process-safe and reliable clinching. The study specifically investigates the influence of three distinct heating methodologies on the characteristics of clinched joints.
Key Research Questions:
This study seeks to address the following key research questions:
- How do different heating strategies – namely, heating plate, resistance heating, and inductive heating – impact the generation and quality of clinched joints in aluminum die casting alloys?
- What are the comparative effects of these heating strategies on critical process parameters such as process time, the geometrical attributes of the joining point, and the resultant bonding strength of the clinched joints?
- Among the investigated heating strategies, which method and associated process parameters demonstrate the most promising performance for achieving robust and efficient clinching of aluminum die casting components?
Research Hypotheses:
While not explicitly stated as formal hypotheses, the research is predicated on the understanding that incorporating a heating step prior to clinching will mitigate the brittleness of aluminum die casting alloys, thereby enabling the formation of crack-free joints with enhanced interlock and bonding strength compared to room temperature clinching. It is further anticipated that the different heating methods will exhibit varying degrees of effectiveness in achieving these improvements, influencing both joint quality and process efficiency.
4. Research Methodology
Research Design:
This research employed an experimental design to evaluate and compare the efficacy of three distinct heating methods in conjunction with the clinching process. The study focused on joining aluminum die casting alloy to aluminum sheet, systematically varying the heating strategy while maintaining consistent clinching parameters.
Data Collection Method:
The following data collection methods were utilized to comprehensively assess the clinched joints:
- Surface Analysis: Visual inspection and photographic documentation were conducted to evaluate the presence and extent of surface cracks around the clinched joints.
- Geometric Dimension Measurement: Metallographic micrographs of cross-sections of the clinched joints were analyzed to quantify key geometric parameters, including neck thickness (tn), interlock (f), and bottom thicknesses (tb1, tb2).
- Bonding Strength Tests: Head tensile tests and shear tests, conducted according to DIN EN ISO 14273 and DIN EN ISO 14272 [10] respectively, were performed to determine the mechanical strength of the clinched joints.
Analysis Method:
The collected data were analyzed using both qualitative and quantitative methods:
- Qualitative Analysis: Surface analysis data were qualitatively assessed to determine the presence or absence of cracks for each heating method and condition.
- Quantitative Analysis: Geometric measurements were statistically analyzed to determine the percentage change in characteristic dimensions relative to room temperature clinched joints. Bonding strength data were compared across different heating methods and conditions to evaluate their impact on joint performance.
Research Subjects and Scope:
The research focused on the following materials and experimental parameters:
- Materials:
- Punch Side Sheet: Aluminum sheet EN AW5182 with a thickness of 1.5 mm.
- Die Side Sheet: Aluminum die casting alloy AlSi10MnMg with a thickness of 3 mm, tested in the natural-hard condition F.
- Clinching Equipment: TOX CEJ 75.200 clinching press with a closed clinching die system.
- Heating Methods:
- Inductive Heating: Ring inductor connected to an Eldec MFG 18 generator (18 kW).
- Resistance Heating: Copper electrodes (CuBe2) connected to a 50 kW transformator.
- Heating Plate: Heating plate with four heating cartridges connected to a HOTSET RR508/1 temperature control unit (22 kW).
- Target Temperature: 250 °C for heated clinching experiments.
5. Main Research Results:
Key Research Results:
The experimental investigation yielded the following key results regarding the application of different heating methods to aluminum die casting clinching:
- Inductive Heating: Crack-free clinch points were consistently achieved using inductive heating with a heating time of 10 seconds at a generator power of 9 kW (50% power).
- Resistance Heating: Initial resistance heating trials resulted in crack formation due to rapid die heating (7 seconds). Modifying the process to incorporate a slower, controlled heating of the clinching die over 45 seconds to 400 °C significantly reduced crack formation.
- Heating Plate: Utilizing a heating plate resulted in clinch joints with minimal cracking when employing a prolonged holding time of 90 seconds. However, achieving completely crack-free joints with this method necessitated these extended holding times.
- Geometric Analysis: Compared to room temperature clinching, heated clinching demonstrably improved joint geometry. Inductive heating increased the interlock (f) by 15%, while the heating plate method yielded a 21% increase in interlock. The neck thickness (tn) remained relatively consistent across all heating methods. Partial bottom thickness measurements indicated a decrease on the punch side (tb1) and an increase on the die side (tb2) for heated clinching.
- Bonding Strength: Heating plate clinching exhibited the highest joint strength in head tensile tests. Inductive and resistance heating methods demonstrated comparable increases in joint strength relative to room temperature clinching, but were lower than the heating plate method.
Statistical/Qualitative Analysis Results:
- Surface Analysis (Fig. 8): Visual inspection confirmed the presence of cracks in room temperature clinched joints and joints produced with rapid resistance heating. Inductive heating and heating plate methods effectively reduced or eliminated cracking.
- Geometric Values (Table 1): Table 1 quantifies the percentage change in geometric parameters (tn, f, tb1, tb2) for each heating method compared to room temperature clinching, highlighting the increase in interlock with heated clinching.
- Head Tensile Strength (Fig. 9): Figure 9 graphically presents the head tensile strength for each heating method, demonstrating the superior performance of heating plate clinching and the comparable improvements achieved with inductive and resistance heating.
Data Interpretation:
The results indicate that heated clinching, regardless of the heating method, enhances the clinchability of aluminum die casting alloys. The increased interlock observed in heated clinched joints directly contributes to improved bonding strength. The heating plate method, while yielding the highest joint strength, suffers from prolonged process times. Inductive heating emerges as a promising compromise, offering a balance between process speed and joint quality, achieving crack-free joints with significantly reduced heating times compared to the heating plate. The slower, controlled resistance heating method also shows potential for crack reduction, but requires precise process control.
Figure Name List:
- Fig. 1. Aluminum-intensive mixed construction using the Audi TT Coupé as an example [3].
- Fig. 2. Clinching presses of the company TOX (left) and the used clinching tool system (right).
- Fig. 3. Geometric dimensions and relevant characteristic values of a clinching point [9]
- Fig. 4. Schematic magnetic flux line of an inductor and the position of tool system
- Fig. 5. Experimental setup for inductive heating.
- Fig. 6. a) CAD design of the resistance heating setup b) Experimental setup of the resistance heating tests.
- Fig. 7 a) Detailed view of the heating plate setup b) Overview of experimental setup.
- Fig. 8. Results of the surface analysis for the three investigated heating methods at room temperature and after heated clinching.
- Fig. 9. Head tensile strength of the clinching joints at room temperature and at heated clinching for different heating methods.
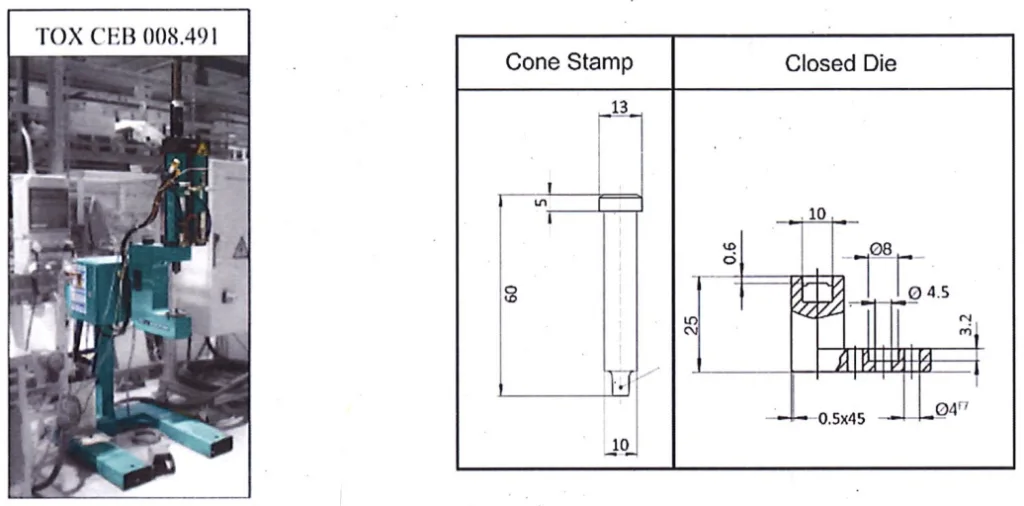
![Fig. 3. Geometric dimensions and relevant characteristic values of a clinching point [9]](https://castman.co.kr/wp-content/uploads/image-342-1024x330.webp)
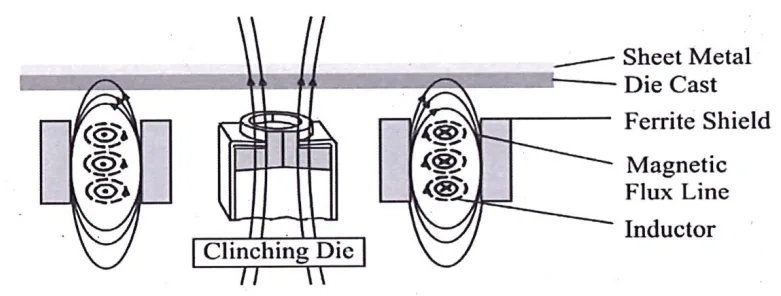
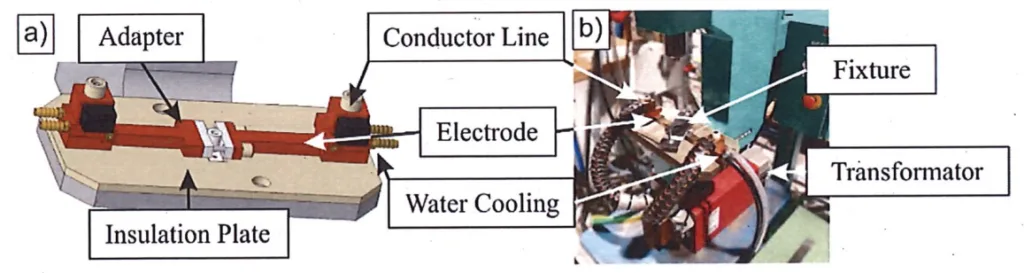
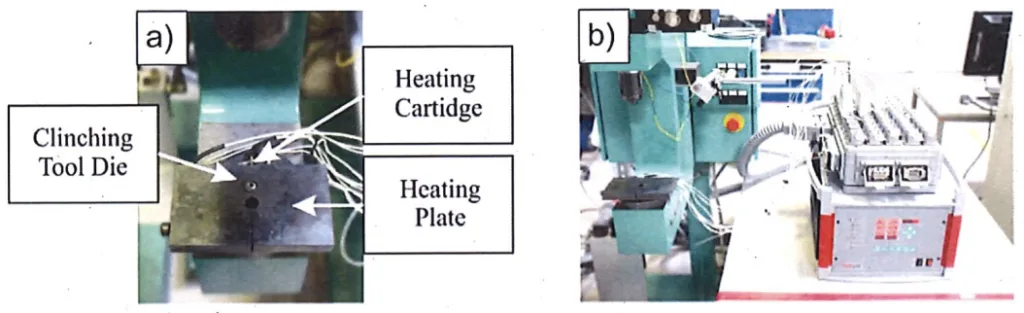
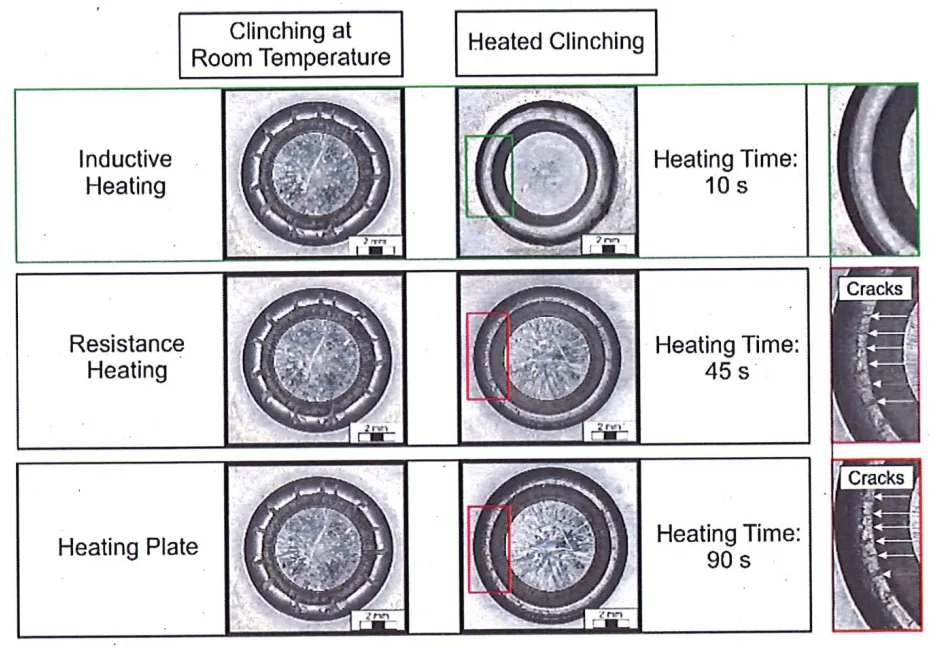
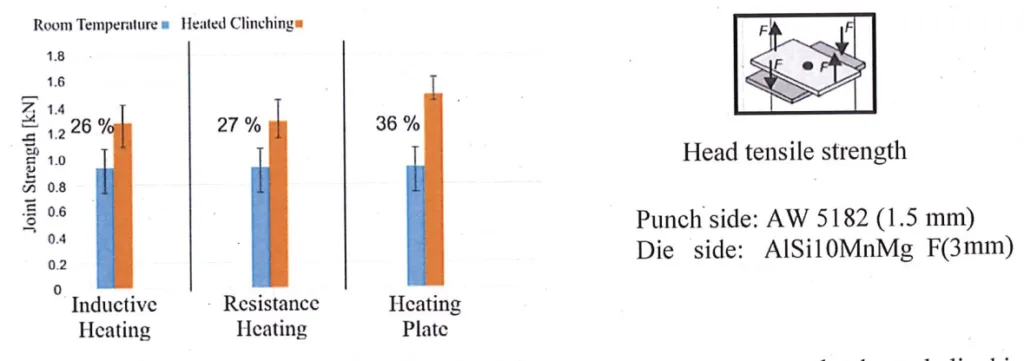
6. Conclusion and Discussion:
Summary of Main Results:
This research conclusively demonstrates that integrating a heating step into the clinching process effectively mitigates crack formation in brittle aluminum die casting alloys. All three investigated heating methods—inductive heating, resistance heating, and heating plate—successfully reduced cracking. Inductive heating stands out for its ability to achieve crack-free joints with short heating cycles, while heating plate clinching provides the highest joint strength but necessitates significantly longer process times. Resistance heating, with optimized slower heating parameters, also shows promise for crack reduction.
Academic Significance of the Research:
This study contributes significantly to the understanding of joining technologies for multi-material structures, particularly in the context of lightweight automotive design. It provides valuable insights into the application of heated clinching for joining challenging materials like aluminum die casting alloys. The comparative analysis of different heating methods offers a robust framework for selecting appropriate heating strategies based on desired joint quality and process efficiency.
Practical Implications:
The findings have significant practical implications for industrial applications, particularly in automotive manufacturing. Inductive heating presents a viable and efficient method for implementing heated clinching in series production due to its rapid heating capabilities and ability to produce crack-free joints. This research expands the applicability of clinching as a joining technology for aluminum die cast components, facilitating the increased use of lightweight multi-material designs.
Limitations of the Research:
The study is limited to specific materials (EN AW5182 and AlSi10MnMg) and clinching parameters. Further research is warranted to optimize heating parameters and clinching processes for a broader range of aluminum die casting alloys and sheet metals. The resistance heating method requires further refinement to enhance its robustness and process efficiency.
7. Future Follow-up Research:
Directions for Follow-up Research:
Future research should focus on the following areas to further advance the application of heated clinching for aluminum die casting:
- Optimization of Inductive Heating: Investigating the use of higher generator power in conjunction with optimized inductor designs to further reduce heating times for inductive heating, while ensuring thermal management of the clinching tools.
- Refinement of Resistance Heating: Further optimization of the resistance heating process to achieve better crack control and faster heating cycles, potentially through advanced feedback control systems and electrode designs.
- Structural Performance Evaluation: Conducting comprehensive structural tests, including fatigue and durability assessments, to further validate the crack reduction benefits and long-term performance of heated clinched joints.
Areas Requiring Further Exploration:
Further exploration should encompass:
- Material Parameter Optimization: Systematic investigation of optimal heating parameters and clinching parameters for a wider variety of aluminum die casting alloys and sheet metal combinations.
- Long-Term Joint Performance: Evaluating the long-term durability, corrosion resistance, and fatigue performance of heated clinched joints under various environmental and loading conditions.
- Cost-Benefit Analysis: Conducting a thorough cost-benefit analysis of different heating methods for industrial implementation, considering factors such as equipment costs, energy consumption, and process throughput.
8. References:
- [1] Hirsch, J.: Aluminium in innovative light-weight car design. Mater. Trans. 52(5), 818–824 (2011)
- [2] Taub, A.L., Krajewski, P.E., Luo, A.A., et al.: The evolution of technology for materials processing over the last 50 years: the automotive example. JOM 59(2), 48–57 (2007)
- [3] Mueller, S.: Flexibel einsetzbare Fügetechnologien zur Realisierung unterschiedlicher Karosseriekonzepte, Tagungsband des 7. Fügetechnischen Gemeinschaftskolloquiums Dresden (2017)
- [4] Behrens, B.-A., et al.: FEA-based optimisation of a clinching process with an open multiple-part die aimed at damage minimisation in CR240BH-AlSi10MnMg joints. Mater. Sci. Eng. Chem. 21, 04009 (2015)
- [5] Neuser, M., et al.: Joining suitability of cast aluminium for self-piercing riveting. IOP Conf. Ser. Mater. Sci. Eng. 1157, 012005 (2021)
- [6] Jäckel, M., et al.: Mechanical joining of materials with limited ductility: analysis of process-induced defects. In: Proceedings of the 20th International ESAFORM Conference on Material Forming, AIP Conference Proceedings, vol. 1896, pp. 110009-1–110009–6 (2017)
- [7] Hovanski, Y., Upadyay, P., Kleinbaum, S., Carlson, B., Boettcher, E., Ruokolainen, R.: Enabling dissimilar material joining using friction stir scribe technology. JOM 69(6), 1060–1064 (2017)
- [8] Varis, J.: Ensuring the integrity in clinching process. J. Mater. Process. Technol. 174, 277–285 (2006)
- [9] Xiaocong, H.: Clinching for sheet materials. Sci. Technol. Adv. Mater. 18, 381–405 (2017)
- [10] Varis, J.: The suitability of clinching as a joining method for high-strength structural steel. J. Mater. Process. Technol. 132, 242–249 (2003)
9. Copyright:
This material is "[S. Yarcu et al.]"'s paper: Based on "Clinching of Heated Aluminum Die Casting".
Paper Source: https://doi.org/10.1007/978-3-030-78424-9_10
This material was summarized based on the above paper, and unauthorized use for commercial purposes is prohibited.
Copyright © 2025 CASTMAN. All rights reserved.