This article introduces the paper "The quality improvement of welded joints of die-cast Al alloys using oscillation and current modulation of the electron beam" presented at the 14th International Conference on Electron Beam Technologies (EBT 2022).
1. Overview:
- Title: The quality improvement of welded joints of die-cast Al alloys using oscillation and current modulation of the electron beam
- Author: D Drimal, L Kovac, R Sekerka and M Kasencak
- Publication Year: 2023
- Publishing Journal/Academic Society: Journal of Physics: Conference Series, IOP Publishing
- Keywords: die-cast aluminum alloys, weldability, electron beam welding, oscillation, current modulation, porosity, weld quality
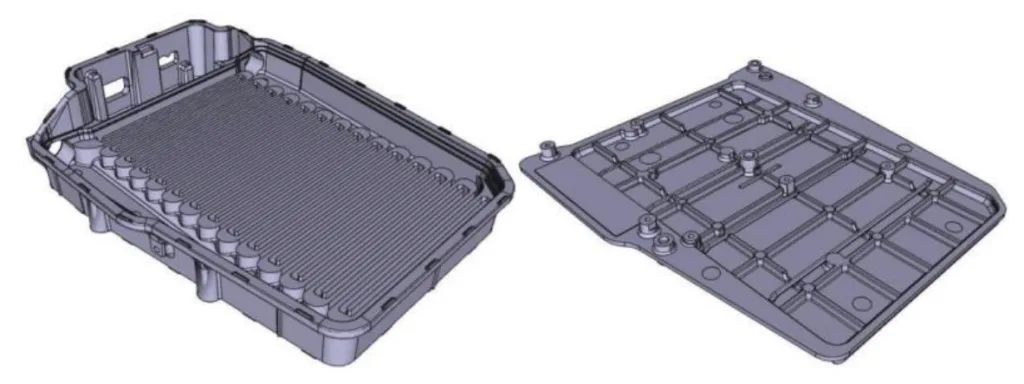
2. Research Background:
- Social/Academic Context of the Research Topic: Aluminum alloys are highly valued for their exceptional properties, leading to their widespread use across various industries including food, metallurgy, aerospace, and automotive. Aluminum alloying allows for tailored properties, but this versatility complicates welding processes. Key challenges in welding aluminum alloys stem from inherent material characteristics. These include the presence of a surface aluminum oxide layer hindering wettability, dissolved gases and inclusions, high thermal conductivity causing rapid heat dissipation, significant thermal expansion leading to distortions, hydrogen content contributing to porosity, and a wide solidification interval promoting segregation and hot cracking. Electron beam welding (EBW) of aluminum alloys is particularly susceptible to porosity and weld cracking. Porosity arises from gases and inclusions in the base metal and humidity in the aluminum oxide surface layer.
- Limitations of Existing Research: While robust electron beam welding technologies exist for joining die-cast aluminum alloys, a specific challenge arises with components like water circuits for electric vehicles. These applications exhibit sensitivity to material purity, making it difficult to establish consistently reliable welding processes using conventional methods.
- Necessity of the Research: Improving the weld quality of high-pressure die-cast aluminum alloys, specifically AlSi10Mg(Fe), is crucial. This research addresses the need for a more robust and less purity-sensitive welding process to overcome the limitations encountered when joining die-cast aluminum components, particularly for critical applications.
3. Research Purpose and Research Questions:
- Research Purpose: The primary aim of this research is to enhance the quality of welded joints in die-cast aluminum alloy AlSi10Mg(Fe) using electron beam welding (EBW). This is achieved through the application of dynamic deflection of the electron beam and pulse modulation of its power. A further objective is to reduce the susceptibility of the welding process to material impurities.
- Key Research Questions:
- What are the potential origins of pore formation within the weld metal of die-cast aluminum alloys?
- How can a welding procedure be developed to effectively minimize or eliminate porosity in the weld metal to the greatest possible extent?
- How do variations in electron beam oscillation frequencies, amplitudes, and patterns influence the resultant weld quality?
- Research Hypotheses: While not explicitly stated as hypotheses, the research explores the premise that employing dynamic deflection and pulse modulation of the electron beam during EBW can effectively improve weld quality and reduce porosity in die-cast aluminum alloy joints.
4. Research Methodology
- Research Design: The study employed a comparative experimental research design. Welding tests were conducted to evaluate the impact of different welding parameters and contamination conditions on weld quality.
- Data Collection Method: The quality of the welds was assessed using a combination of analytical techniques:
- Metallographic analysis: Microscopic examination of weld cross-sections to evaluate weld geometry and identify defects.
- Computed Tomography (CT) analysis: Non-destructive inspection to detect internal cavities and porosity within the weldments.
- Energy-Dispersive X-ray spectroscopy (EDX) analysis: Chemical analysis to identify elemental composition and potential contaminants in the weld and surrounding areas.
- Analysis Method: The collected data from metallographic, CT, and EDX analyses were comparatively analyzed to determine the effects of varying welding parameters, such as oscillation frequencies, amplitudes, and patterns, as well as the presence of intentional contaminants, on the resulting weld quality.
- Research Subjects and Scope: The primary material investigated was the high-pressure die-cast aluminum alloy AlSi10Mg(Fe)/EN AC 43400, commonly used in automotive components. For comparative purposes, wrought aluminum alloy AlMg3/EN AW 5754 was also utilized in some experiments. The research focused on welding components relevant to a water circuit for electric vehicles. To simulate real-world contamination scenarios, potential contaminants identified from the casting and post-casting processes, including mold release agent, injection chamber piston lubricant, cutting fluid, and detergent, were intentionally introduced into the weld joints.
5. Main Research Results:
- Key Research Results:
- Potential sources of contamination in die-cast components were identified as mold release agent, injection chamber piston lubricant, cutting fluid, and detergent from cleaning processes.
- Intentional contamination, particularly with piston lubricant and mold agent, demonstrably reduced weld quality, leading to increased porosity and surface imperfections. Figure 5 illustrates the appearance of contaminated welds.
- The application of dynamic deflection and pulse modulation of the electron beam during EBW proved effective in enhancing weld quality and reducing porosity.
- Various electron beam oscillation patterns, including saw, circle, "flower", and coaxial circles, were tested, along with different frequencies (333 Hz, 555 Hz, 1111 Hz) and amplitudes (0.5 mm, 1.0 mm).
- The "flower" oscillation pattern and coaxial oscillation showed promising results in minimizing spiking and porosity formation.
- Combining electron beam oscillation with beam current intensity modulation significantly improved the stability of the welding process.
- Statistical/Qualitative Analysis Results:
- Qualitative assessment of weld macrostructures revealed differences between sound welds and inferior welds with defects (Figure 3).
- CT analysis (Figure 4) confirmed the presence of cavities in thicker sections of castings.
- Measurements of weld width (Figure 6) and weld depth (Figure 7) were conducted for various electron beam deflection parameters, showing the influence of oscillation on weld geometry.
- Table 2 presents the nominal chemical composition of the experimental alloys (EN AC 43400 and EN AW 5754).
- Table 3 details the measured chemical composition in different areas of the weldment, including the surface, weld bead, and cut sections, for both sound and inferior welds.
- Data Interpretation: The results indicate that electron beam oscillation and current modulation are effective strategies for mitigating the negative impacts of impurities and improving the weldability of die-cast aluminum alloys. These techniques likely enhance melt pool dynamics, promote degassing, and contribute to a more stable welding process.
- Figure Name List:
- Figure 1. 3D model of the heating unit.
- Figure 2. Electron beam welding machine PZ ELZA UNI.
- Figure 3. Weld macrostructures: a) Sound weld 1; b) Inferior weld 3.
- Figure 4. Visualization of CT analysis.
- Figure 5. The appearance of the contaminated welds.
- Figure 6. Change of the weld width depending on electron beam deflection parameters.
- Figure 7. Change of the weld depth depending on electron beam deflection parameters.
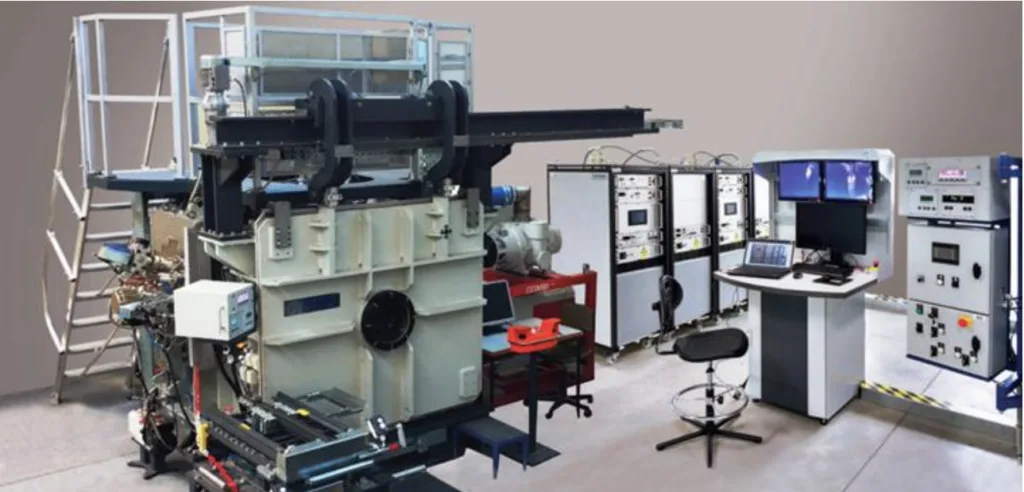
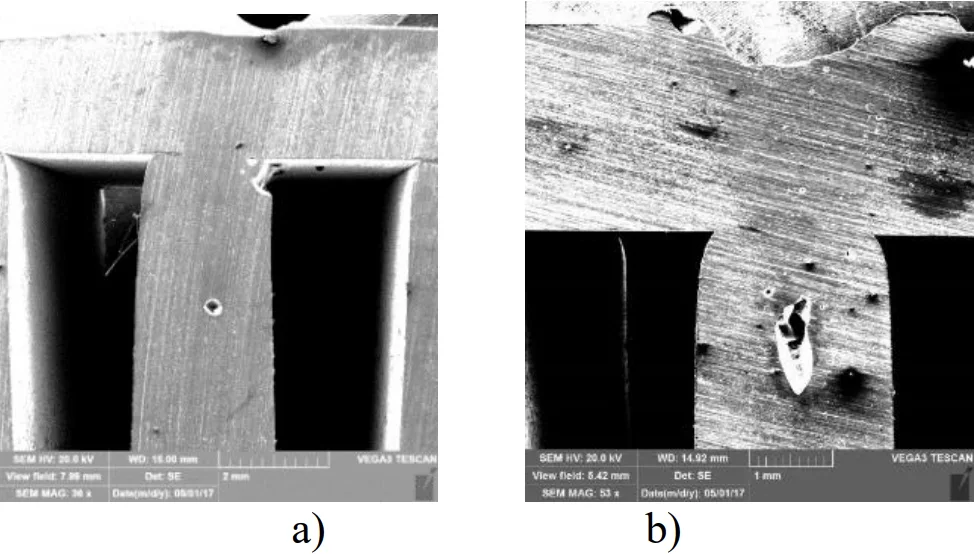
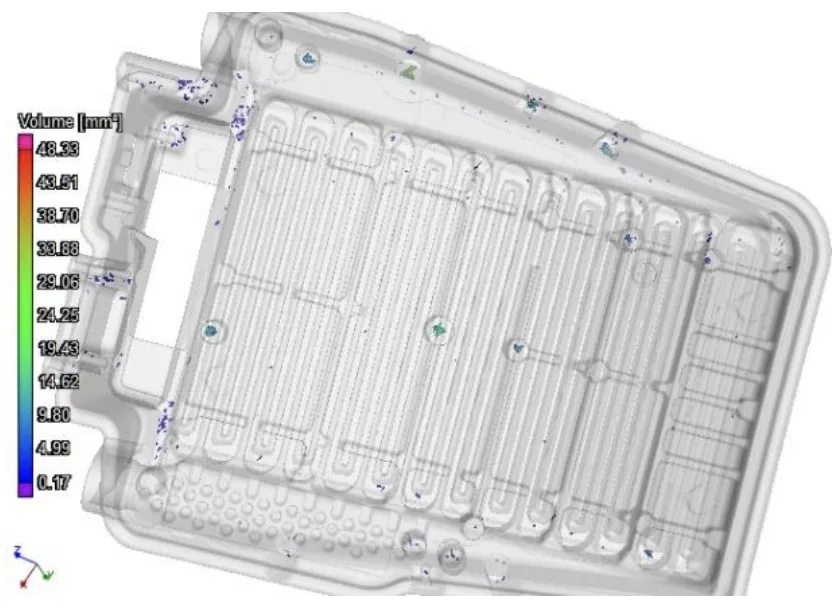
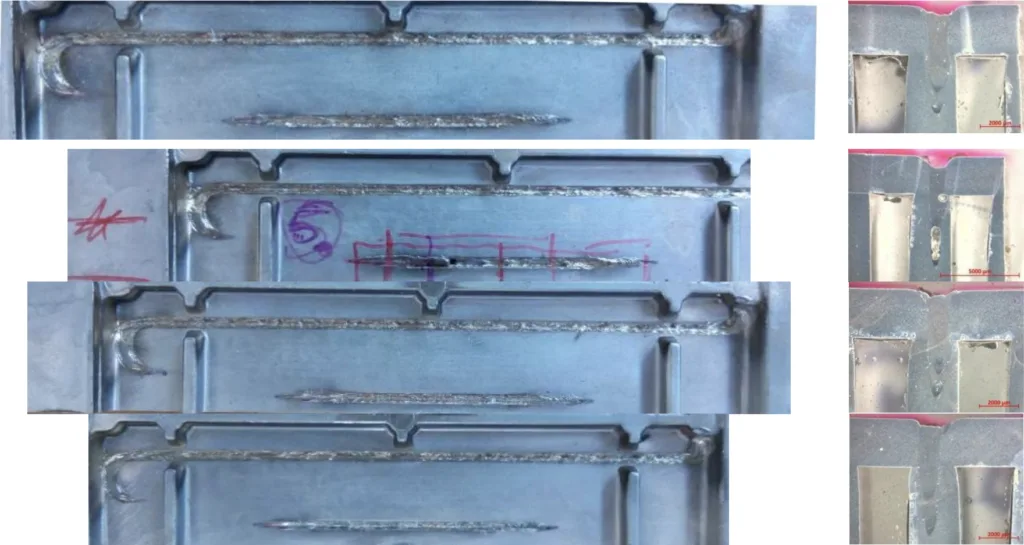
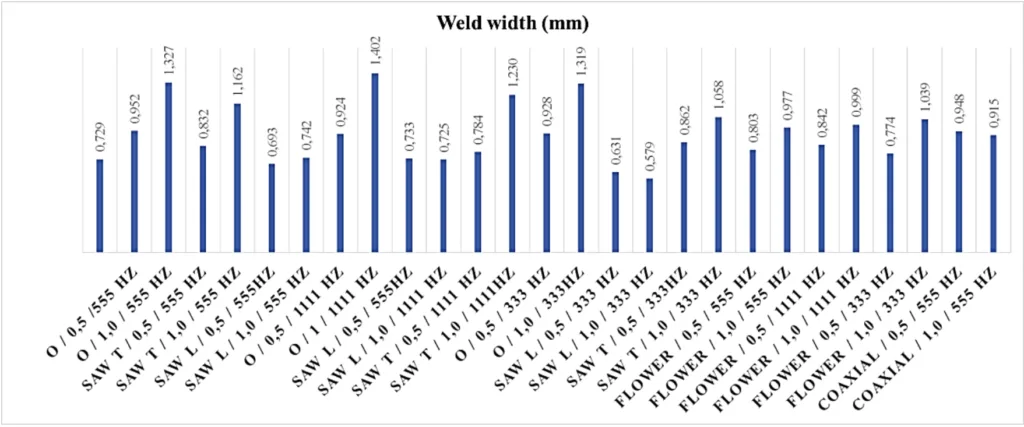
6. Conclusion and Discussion:
- Summary of Main Results: This research investigated the improvement of electron beam welding for high-pressure die-cast AlSi10Mg(Fe) alloys. Material contamination from the casting process was identified as a significant factor affecting weldability. The study demonstrated that employing electron beam oscillation and current modulation techniques effectively enhances process stability and weld quality, leading to a reduction in porosity and spiking defects.
- Academic Significance of the Research: This study contributes to the understanding of electron beam welding of die-cast aluminum alloys by demonstrating the effectiveness of dynamic electron beam control. The findings highlight the role of oscillation and current modulation in overcoming weldability challenges associated with these materials, offering valuable insights into melt pool behavior and the influence of impurities in EBW processes.
- Practical Implications: The research successfully developed and verified an improved electron beam welding technology utilizing electron beam oscillation and current modulation. This technology is specifically tailored for joining die-cast aluminum alloys, particularly for critical components like water circuits in electric vehicles. The implementation of this technology can lead to more robust and reliable welding processes, reduced defect rates, and enhanced quality and reliability of die-cast aluminum components in industrial applications.
- Limitations of the Research: While the research successfully addressed the specific challenges of welding AlSi10Mg(Fe) alloy for water circuit applications, further investigation may be needed to generalize these findings to a broader range of die-cast aluminum alloys and diverse welding applications.
7. Future Follow-up Research:
- Directions for Follow-up Research: Future research should focus on further optimizing the modulation of electron beam power to achieve even greater process stability and weld quality.
- Areas Requiring Further Exploration: Continued investigation into the optimization of electron beam power modulation is recommended to further enhance the stability of the welding process and minimize defects.
8. References:
[1] Schultz H 2000 Electron beam welding (Cambridge, Englandn: Abington Publishing)
[2] Mathers G 2002 The welding of aluminium and its alloys, (Cambridge, England: Woodhead Publishing, Ltd.)
[3] Kearns W H 1982 Welding handbook (American Welding Society vol 4, 7 ed) (Miami, Florida)
[4] Hrivňák I 1992 Theory of weldability of metals and alloys (Amsterdam: Elsevier)
[5] Kolenič F and Kováč L 2006 Electron and laser beam welding of die-cast aluminium alloy components of heat exchanger for automotive industry IIW DOC XII-1881-06 Commission XII Intermediate meeting (April 2006)
9. Copyright:
This material is D Drimal, L Kovac, R Sekerka and M Kasencak's paper: Based on The quality improvement of welded joints of die-cast Al alloys using oscillation and current modulation of the electron beam.
Paper Source: doi:10.1088/1742-6596/2443/1/012010
This material was summarized based on the above paper, and unauthorized use for commercial purposes is prohibited.
Copyright © 2025 CASTMAN. All rights reserved.