This article introduces the paper "Evaluation of the Microstructure and Properties of As-Cast Magnesium Alloys with 9% Al and 9% Zn Additions" presented in Materials, MDPI.
1. Overview:
Title: Evaluation of the Microstructure and Properties of As-Cast Magnesium Alloys with 9% Al and 9% Zn Additions
Authors: Lechosław Tuz, Vít Novák, and František Tatíček
Publication Year: 2025
Publishing Journal: Materials, MDPI
Keywords: magnesium alloys; mechanical properties; microstructure; weldability; forming; elevated temperature; thermal conductivity
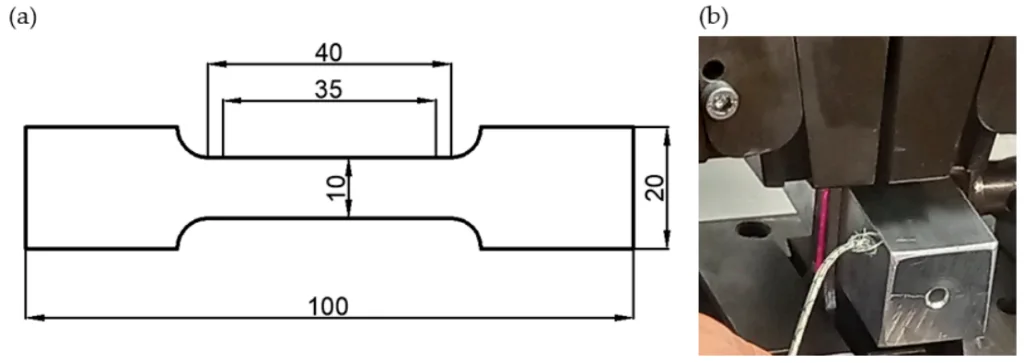
2. Research Background:
The ongoing demand for reduced energy consumption necessitates lighter vehicle designs, driving the re-evaluation of magnesium alloys as primary construction materials, particularly with the rise of electric vehicles. Magnesium alloys offer favorable mechanical properties, natural degradation, and are increasingly considered for both massive and thin-walled components, even in elevated temperature applications within the automotive and aviation sectors. However, a significant challenge in utilizing magnesium alloys, especially in massive castings produced via methods like sand casting or high-pressure die casting, is inherent porosity. This porosity negatively impacts mechanical and plastic properties and restricts the effectiveness of heat treatments. Furthermore, the presence of low-melting point structural components and phases within these alloys poses additional complexities. Therefore, understanding and mitigating these limitations is crucial for expanding the application of magnesium alloys.
3. Research Purpose and Research Questions:
This research aims to evaluate the microstructure and material properties of as-cast magnesium alloys with specific alloying additions relevant to industrial applications. The study focuses on comparing the effects of aluminum and zinc as primary alloying elements on the resulting alloy characteristics.
Key Research Questions:
- How do 9% Aluminum (Al) and 9% Zinc (Zn) additions, respectively, influence the microstructure of as-cast magnesium alloys?
- What are the effects of these alloying additions on the mechanical properties (tensile strength, hardness, plasticity) of as-cast magnesium alloys at both ambient and elevated temperatures?
- How does the thermal conductivity of these magnesium alloys vary with temperature and alloying composition?
Research Hypotheses:
The study posits that high concentrations of aluminum or zinc in magnesium alloys will promote the formation of low-melting point phases, potentially increasing susceptibility to hot cracking during processing. Furthermore, the research investigates the temperature-dependent property changes in these alloys to understand their behavior under service conditions and during thermal processes like welding.
4. Research Methodology
Research Design: This study employed a comparative experimental design, examining two distinct magnesium alloys cast in sand molds: Mg-Al-Zn (approximately 9% Al, 0.5% Zn, balance Mg) and Mg-Zn-Al (approximately 9% Zn, 1% Al, balance Mg). Both alloys were tested in the as-cast state without subsequent heat treatment.
Data Collection Method: A comprehensive suite of characterization techniques was utilized:
- Microscopy: Light Microscopy (LM) and Scanning Electron Microscopy (SEM) were used to observe the microstructure of etched samples. Energy Dispersive Spectroscopy (SEM-EDS) was employed for phase identification and elemental mapping.
- Thermal Conductivity Measurement: The thermal conductivity coefficient was measured at temperatures ranging from 25 °C to 200 °C, adhering to ASTM E1461 standards.
- Tensile Testing: Static tensile tests were conducted at ambient temperature and elevated temperatures (120 °C, 150 °C, 180 °C, and 240 °C). Samples were heated using contact heating with inductive elements. Elongation was measured using a laser extensometer.
- Hardness Testing: Vickers hardness measurements (HV10) were performed to assess the hardness of both alloys.
- Fractography: Fracture surfaces of tensile tested samples were examined using SEM to analyze fracture mechanisms.
Analysis Method: The collected data was analyzed using qualitative and quantitative methods. Microstructural features and phase compositions were identified through microscopy and EDS. Statistical analysis was applied to mechanical and thermal property data. Fractographic analysis provided insights into the fracture behavior of the alloys.
Research Subjects and Scope: The study focused on two specific magnesium alloy compositions, Mg-Al-Zn and Mg-Zn-Al, prepared by gravity casting into sand molds. The scope was limited to the as-cast condition and the evaluation of microstructure, thermal conductivity, and tensile properties up to 240 °C.
5. Main Research Results:
Key Research Results:
- Microstructure: Both alloys exhibited a dendritic microstructure typical of cast materials. Interdendritic regions contained low-melting eutectic phases, intermetallic compounds, and Laves phases. The Mg-Al-Zn alloy showed local porosity in interdendritic areas (Figures 2 and 3). In the Mg-Al-Zn alloy, the γ-Mg17Al12 phase was prevalent in grain boundaries, while both γ-Mg17Al12 and β-MgZn2 phases were likely present in the Mg-Zn-Al alloy (Figures 4 and 5).
- Thermal Conductivity: The thermal conductivity coefficient remained relatively constant with increasing temperature up to 200 °C for both alloys. The Mg-Zn-Al alloy demonstrated a significantly higher thermal conductivity (approximately 77 W/mK) compared to the Mg-Al-Zn alloy (approximately 49 W/mK) (Figure 8, Table 4).
- Tensile Properties: Tensile strength (Rm) increased with temperature initially for both alloys, reaching peak values at elevated temperatures. For the Mg-Zn-Al alloy, the maximum tensile strength of 121 MPa was observed at 150 °C, while the Mg-Al-Zn alloy reached a maximum of 122 MPa at 180 °C (Figure 9, Table 5). Elongation remained low for both alloys in the as-cast state.
- Hardness: The Mg-Al-Zn alloy exhibited a significantly higher Vickers hardness (83 HV10) compared to the Mg-Zn-Al alloy (46 HV10) (Table 6).
Statistical/Qualitative Analysis Results: EDS analysis confirmed the presence of alloying elements in interdendritic regions and identified the primary phases. Tensile test data showed a temperature-dependent trend in strength and elongation. Thermal conductivity measurements provided quantitative values for heat transfer characteristics. Fractographic analysis indicated brittle intergranular fracture in both alloys (Figures 10 and 11).
Data Interpretation: The results indicate that alloying elements, particularly Al and Zn, segregate to interdendritic regions during solidification, forming low-melting point phases. Zinc addition significantly enhances thermal conductivity, likely due to the formation of Laves phases. Elevated temperatures initially improve tensile strength, potentially due to increased atomic mobility, but can reduce plasticity. The presence of porosity in the Mg-Al-Zn alloy and the formation of brittle zinc-rich phases in the Mg-Zn-Al alloy influence their mechanical behavior and potential weldability.
Figure Name List:
- Figure 1. Sample for the tensile test (a) and the heating equipment (b), LabTest Model 5.100SP1, used for the tests.
- Figure 2. Macrostructure of the alloy in the cross-section: (a) Mg-Al-Zn, (b) Mg-Zn-Al.
- Figure 3. Microstructure near porosity in the Mg-Al-Zn alloy.
- Figure 4. Microstructure of the Mg-Al-Zn alloy. (a-d) light microscopy, (e,f) SEM images.
- Figure 5. Microstructure of the Mg-Zn-Al alloy. (a-d) light microscopy, (e,f) SEM images.
- Figure 6. Map of the element distribution in the Mg-Al-Zn alloy.
- Figure 7. Map of the element distribution in the Mg-Zn-Al alloy.
- Figure 8. Change in the thermal conductivity coefficient in the temperature function.
- Figure 9. Change in mechanical properties in the function temperature of the (a) Mg-Al-Zn and (b) Mg-Zn-Al alloys.
- Figure 10. Fracture morphology of samples 92 (a,b) and 96 (c,d).
- Figure 11. Fracture morphology of samples L2 (a,b) and L6 (c,d).
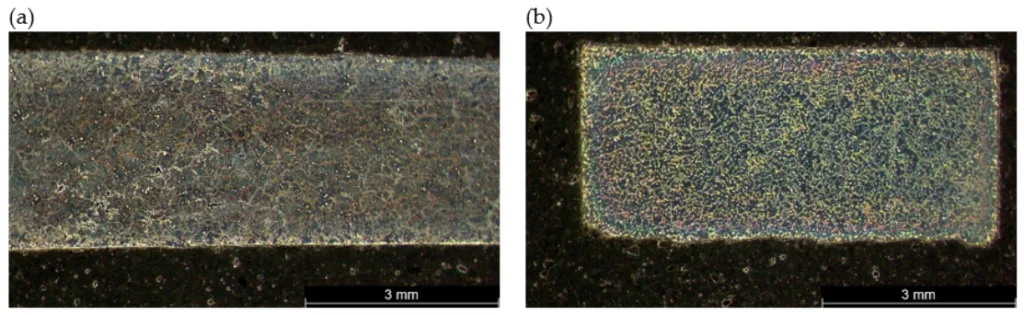
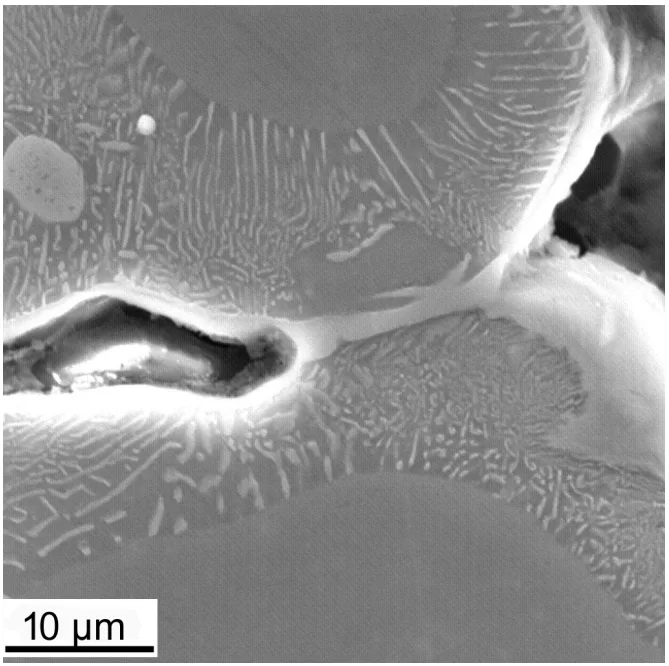
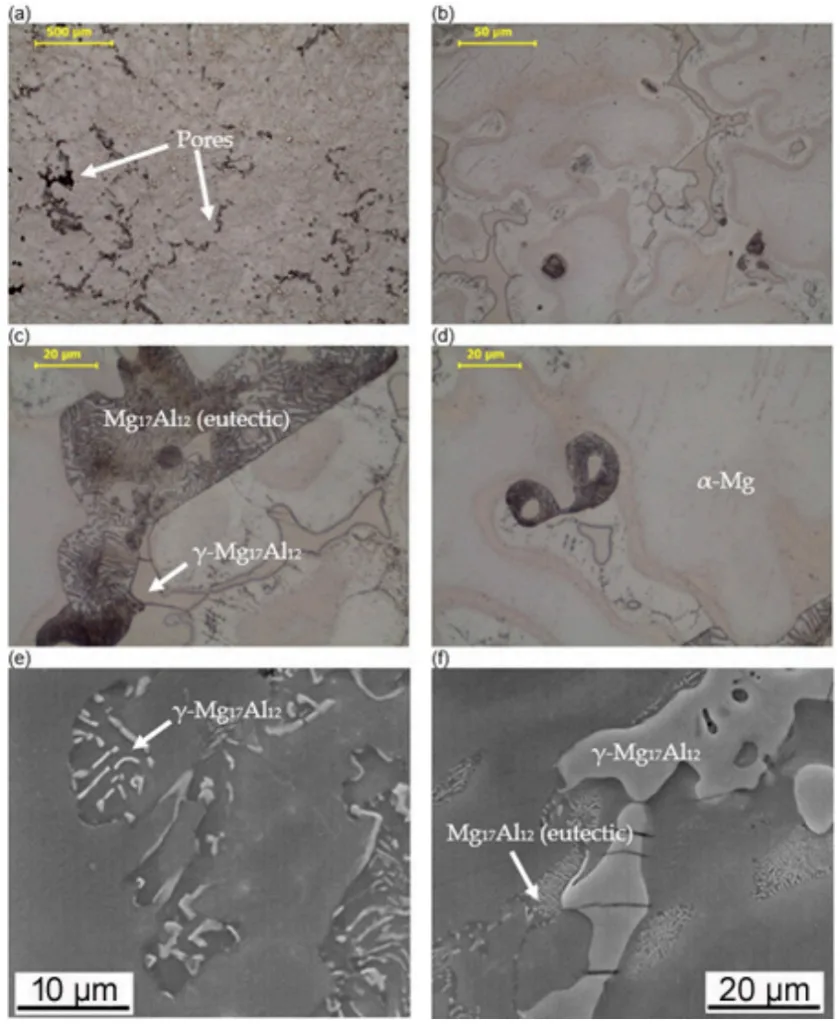
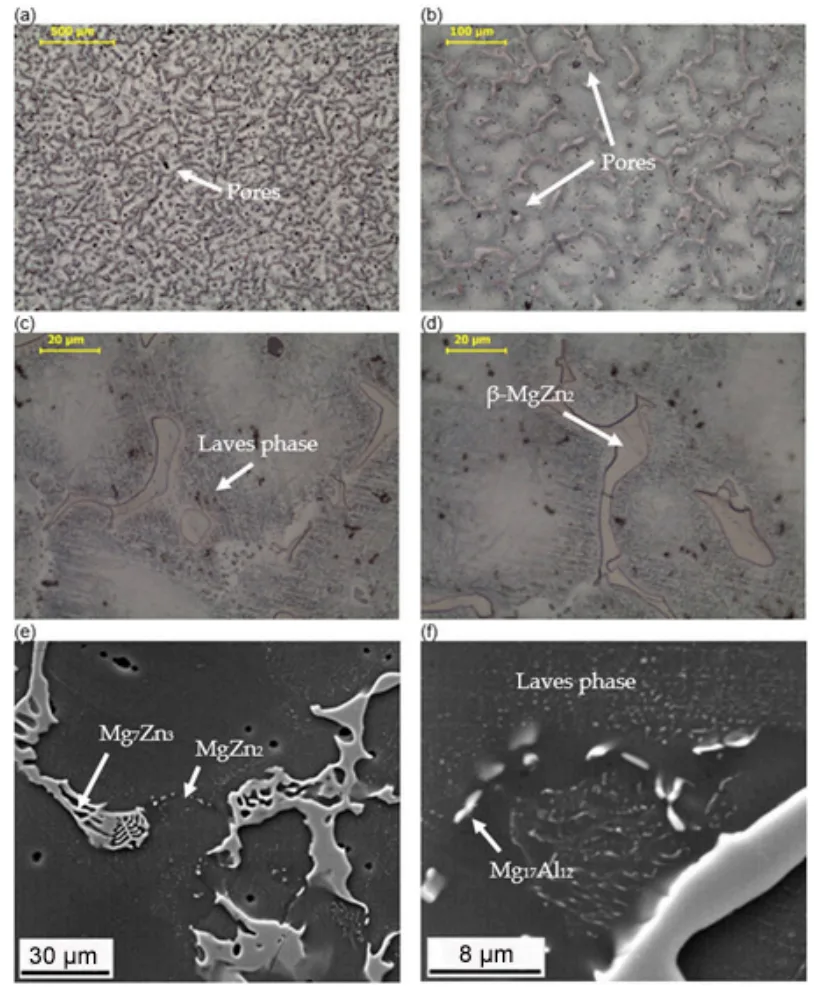
6. Conclusion and Discussion:
Summary of Main Results: This study demonstrates that both as-cast Mg-Al-Zn and Mg-Zn-Al alloys exhibit dendritic microstructures with alloying elements concentrated in interdendritic regions. The Mg-Zn-Al alloy, with 9% zinc, shows superior thermal conductivity but lower hardness compared to the Mg-Al-Zn alloy (9% aluminum). Both alloys exhibit peak tensile strengths at elevated temperatures, but are susceptible to hot cracking due to the presence of low-melting point phases.
Academic Significance of the Research: This research provides valuable insights into the comparative effects of aluminum and zinc alloying additions on the microstructure and properties of as-cast magnesium alloys. It contributes to a deeper understanding of phase formation, thermal behavior, and mechanical response in these industrially relevant alloy systems.
Practical Implications: The findings have practical implications for material selection and processing in die casting and welding of magnesium alloys. The higher thermal conductivity of the Mg-Zn-Al alloy may be advantageous in applications requiring efficient heat dissipation. However, the susceptibility to hot cracking in both alloys highlights the need for careful control of casting and welding parameters, including preheating, to ensure component integrity, particularly in large castings for automotive and aviation industries. Preheating in the range of peak tensile strength (150-180°C) is suggested to mitigate cracking during welding.
Limitations of the Research: The study is limited to two specific alloy compositions in the as-cast state. Weldability tests were not conducted, and further research is needed to optimize welding parameters and explore the effects of heat treatment on these alloys.
7. Future Follow-up Research:
Directions for Follow-up Research: Future research should focus on:
- Detailed analysis of precipitation behavior within the magnesium matrix and phase transformations under heat treatment and artificial aging conditions.
- Comprehensive weldability testing of both alloys to determine optimal welding parameters and strategies to prevent hot cracking.
Areas Requiring Further Exploration:
- Investigating the optimization of preheating temperatures and cooling rates during casting and welding to minimize hot cracking susceptibility.
- Further exploration of the influence of minor alloying elements and impurity levels on the microstructure, properties, and weldability of these magnesium alloys.
8. References:
- [1] Zeng, X.; Yi, S. Deformation Mechanisms of Magnesium Alloys with Rare-Earth and Zinc Additions under Plane Strain Compression. Materials 2024, 17, 33. CrossRef
- [2] Cheng, M.; Jia, X.; Zhang, Z. Prediction of Mechanical Properties of Rare-Earth Magnesium Alloys Based on Convolutional Neural Networks. Materials 2024, 17, 4956. CrossRef PubMed
- [3] Sharma, S.K.; Gajević, S.; Sharma, L.K.; Pradhan, R.; Miladinović, S.; Ašonja, A.; Stojanović, B. Magnesium-Titanium Alloys: A Promising Solution for Biodegradable Biomedical Implants. Materials 2024, 17, 5157. CrossRef PubMed
- [4] Zhao, D.; Lü, S.; Guo, W.; Li, S.; Li, J.; Guo, G.; Guo, W.; Wu, S. Effects of Mg17Al12 phase on microstructure evolution and ductility in the AZ91 magnesium alloy during the continuous rheo-squeeze casting-extrusion process. J. Mater. Sci. Technol. 2024, 191, 63–79. CrossRef
- [5] Mashoufi, K.; Garmroodi, P.; Mirzakhani, A.; Assempour, A. Cyclic contraction-expansion extrusion (CCEE): An innovate severe plastic deformation method for tailoring the microstructure and mechanical properties of magnesium AZ91 alloy. J. Mater. Res. Technol. 2023, 26, 8541–8554. CrossRef
- [6] Chai, F.; Ma, Z.; Han, X.; Hu, X.; Chang, Z.; Zhou, J. Effect of strain rates on mechanical behavior, microstructure evolution and failure mechanism of extruded-annealed AZ91 magnesium alloy under room-temperature tension. J. Mater. Res. Technol. 2023, 27, 4644–4656. CrossRef
- [7] Wang, R.; Yan, F.; Sun, J.; Xing, W.; Li, S. Microstructural Evolution and Mechanical Properties of Extruded AZ80 Magnesium Alloy during Room Temperature Multidirectional Forging Based on Twin Deformation Mode. Materials 2024, 17, 5055. CrossRef
- [8] Venkatesh, R.; Hossain, I.; Mohanavel, V.; Soudagar, M.E.M.; Alharbi, S.A.; Al Obaid, S. Analysis and optimization of machining parameters of AZ91 alloy nanocomposite with the Influences of nano ZrO2 through vacuum diecast process. Heliyon 2024, 10, e34931. CrossRef
- [9] Sadiq, T.O.; Sudin, I.; Alsakkaf, A.; Idris, J.; Fadil, N.A. Effect of homogenization heat treatment on the microstructure of AZ91 magnesium alloy at different temperatures and ageing times. J. Eng. Res. 2023, 11, 212–218. CrossRef
- [10] Ganguly, S.; Chaubey, A.; Sahoo, R.; Kushwaha, A.; Basu, A.; Majhi, J.; Gupta, M. Influence of ultrasonic shot peening on the microstructure and impression creep performance of squeeze-cast AZ91 alloy reinforced with graphene nanoplatelets. J. Alloys Compd. 2023, 938, 168640. CrossRef
- [11] Kandemir, S.; Bohlen, J.; Dieringa, H. Influence of recycled carbon fiber addition on the microstructure and creep response of extruded AZ91 magnesium alloy. J. Magnes. Alloys 2023, 11, 2518–2529. CrossRef
- [12] Motavallian, P.; Rabiee, S.M.; Aval, H.J. Effect of solution treatment of AZ91 alloy on microstructure, mechanical properties and corrosion behavior of friction stir back extruded AZ91/bioactive glass composite. J. Mater. Res. Technol. 2023, 25, 6992–7007. CrossRef
- [13] Cui, P.-X.; Hu, M.-L.; Ji, Z.-S.; Wang, Y.; Guo, Y.; Xu, H.-Y. Effect of La/Nd ratio on microstructure and tensile properties of AZ91-RE alloys. Trans. Nonferrous Met. Soc. China 2024, 34, 1456–1469. CrossRef
- [14] Luo, H.; Li, J.; Wang, Y.; Ye, J.; Zhang, Z.; Guan, B.; Chen, X.; Zheng, K.; Pan, F. Influence of Ti particle sizes on microstructure and mechanical behaviors of AZ91-Ti composites under different loading paths. Mater. Sci. Eng. A 2023, 886, 145723. CrossRef
- [15] Mehdipour, M.; Aval, H.J. Effect of friction stir back extrusion rotational speed on microstructure, mechanical properties, and corrosion behaviour of AZ91-Ca alloy. J. Mater. Res. Technol. 2023, 25, 4441–4456. CrossRef
- [16] Motavallian, P.; Rabiee, S.M.; Aval, H.J. Investigation of microstructure and corrosion behavior of AZ91/64SiO2-31CaO-5P2O5 composite wire fabricated by friction stir back extrusion. Surf. Coat. Technol. 2023, 464, 129451. CrossRef
- [17] Patil, H.; Marodkar, A.; Ghosh, A.; Borkar, H. Effect of Ca addition on the microstructure and creep behaviour of AZ91 Mg alloy. Mater. Today Proc. 2023, in press. CrossRef
- [18] Jin, G.; Xiao, M.; Liu, F.; Liu, W.; Chen, Y. Microstructure and mechanical properties of hybrid hexagonal BN nanotube and nanoplatelet reinforced AZ91 Mg matrix composites. J. Mater. Res. Technol. 2024, 32, 1509–1520. CrossRef
- [19] Xiao, P.; Gao, Y.; Sheng, Y.; Yang, C.; Liu, Z.; Yi, Y.; Wu, W.; Zhao, Q.; Gupta, M. Improving wear and corrosion resistances of Mg2Si/AZ91 composites via tailoring microstructure and intrinsic properties of Mg2Si induced by Sb modification. J. Magnes. Alloys 2023, in press. CrossRef
- [20] Milan, S.; Branislav, H.; Martina, J.; Jana, P. Microstructure evolution and corrosion mechanism of AZ91 magnesium alloy in chloride environments for commercial purposes prepared by Ohno continuous casting. Transp. Res. Procedia 2023, 74, 530–537. CrossRef
- [21] Shabestari, S.G.; Ghaniabadi, E. Effect of Ca and rotation speed on microstructure and solidification parameters of AZ91 magnesium alloy produced by semi-solid casting through rotating container process. Trans. Nonferrous Met. Soc. China 2023, 33, 396–408. CrossRef
- [22] Yang, H.; Cui, J.; Zhou, Y.; Tan, J.; Chen, X.; Huang, G.; Zheng, K.; Jin, Y.; Jiang, B.; Pan, F. Microstructures and the improved mechanical properties of AZ91 alloy by incorporating Ti-6Al-4V particles. J. Mater. Res. Technol. 2023, 26, 7340–7353. CrossRef
- [23] Fan, W.; Bai, Y.; Li, T.; Hao, H.; Zhang, X. Effect of hard-plate rolling and annealing treatment on the microstructure and mechanical properties of NbB2 particle-reinforced AZ91 composite. J. Magnes. Alloys 2024, in press. CrossRef
- [24] Zheng, Z.-L.; Deng, K.-K.; Nie, K.-B.; Wang, C.-J.; Xu, C.; Shi, Q.-X. Microstructure and mechanical properties of freeze-casted in-situ ABOW@Al2O3/AZ91 composites. Ceram. Int. 2024, 50, 42015–42025. CrossRef
- [25] Du, Z.-Q.; Deng, K.-K.; Nie, K.-B.; Wang, C.-J.; Xu, C.; Shi, Q.-X. Preparation, microstructure, and mechanical properties of SiCp/AZ91 magnesium matrix laminar material. Mater. Sci. Eng. A 2024, 891, 145977. CrossRef
- [26] Trojanová, Z.; Gärtnerová, V.; Jäger, A.; Námešný, A.; Chalupová, M.; Palček, P.; Lukáč, P. Mechanical and fracture properties of an AZ91 Magnesium alloy reinforced by Si and SiC particles. Compos. Sci. Technol. 2009, 69, 2256–2264. CrossRef
- [27] Yin, C.; Shen, J.; Hu, S.; Zhang, Z. Microstructure and mechanical properties of AZ91 magnesium alloy fabricated by multi-layer and multi-pass CMT based WAAM technique. Results Eng. 2023, 18, 101065. CrossRef
- [28] Srinivasan, S.; Bharath, R.R.; Atrens, A.; Srinivasan, P.B. Microstructure and mechanical properties of welds of AZ31B magnesium alloy produced by different gas tungsten arc welding variants. Def. Technol. 2024, in press. CrossRef
- [29] Braszczyńska-Malik, K.; Mróz, M. Gas-tungsten arc welding of AZ91 magnesium alloy. J. Alloys Compd. 2011, 509, 9951–9958. CrossRef
- [30] Sunil, B.R.; Reddy, G.P.K.; Mounika, A.; Sree, P.N.; Pinneswari, P.R.; Ambica, I.; Babu, R.A.; Amarnadh, P. Joining of AZ31 and AZ91 Mg alloys by friction stir welding. J. Magnes. Alloys 2015, 3, 330–334. CrossRef
- [31] Kumar, S.; Vigneshwar, M.; Selvamani, S.; Prakash, A.; Hariprasath, P. The Comparative Analysis on Friction Stir Welded and Gas Tungsten Arc Welded AZ91 Grade Magnesium Alloy Butt Joints. Mater. Today Proc. 2017, 4, 6688–6696. CrossRef
- [32] Tuz, L.; Kołodziejczak, P.; Kolasa, A. Structure of butt joint of as-cast magnesium alloys. Weld. Int. 2015, 30, 43–47. CrossRef
- [33] Asgari, A.; Delavar, H.; Sedighi, M. Microstructure and surface integrity of machined AZ91 magnesium alloy. J. Mater. Res. Technol. 2023, 22, 735–746. CrossRef
- [34] Swetha Chowdary, V.; Ravikumar, D.; Anand Kumar, S.; Kondaiah, V.V.; Ratna Sunil, B. Influence of heat treatment on the machinability and corrosion behavior of AZ91 Mg alloy. J. Magnes. Alloys 2018, 6, 52–58. CrossRef
- [35] Marakini, V.; Srinivasa Pai, P.; D’Mello, G. Effect of liquid nitrogen assisted milling on AZ91 magnesium alloy. Results Eng. 2024, 22, 102207. CrossRef
- [36] Marodkar, A.S.; Patil, H.; Chavhan, J.; Borkar, H. Effect of gravity die casting, squeeze casting and extrusion on microstructure, mechanical properties and corrosion behaviour of AZ91 magnesium alloy. Mater. Today Proc. 2023, in press. CrossRef
- [37] Lü, Y.; Wang, Q.; Ding, W.; Zeng, X.; Zhu, Y. Fracture behavior of AZ91 magnesium alloy. Mater. Lett. 2000, 44, 265–268. CrossRef
- [38] Sovík, J.; Kajánek, D.; Pastorek, F.; Štrbák, M.; Florková, Z.; Jambor, M.; Hadzima, B. The Effect of Mechanical Pretreatment on the Electrochemical Characteristics of PEO Coatings Prepared on Magnesium Alloy AZ80. Materials 2023, 16, 5650. CrossRef PubMed
- [39] ASTM E1461-13; Standard Test Method for Thermal Diffusivity by the Flash Method. ASTM International: West Conshohocken, PA, USA, 2022.
- [40] Alrasheedi, N.H.; Ataya, S.; Seleman, M.M.E.-S.; Ahmed, M.M.Z. Tensile Deformation and Fracture of Unreinforced AZ91 and Reinforced AZ91-C at Temperatures up to 300 °C. Materials 2023, 16, 4785. CrossRef PubMed
- [41] Lin, Z.; Sheng, D.; Fang, Y.; Xiong, K.; Song, Y. Experimental and Numerical Investigation of the Tensile and Failure Response of Multiple-Hole-Fiber-Reinforced Magnesium Alloy Laminates under Various Temperature Environments. Materials 2023, 16, 5573. CrossRef
9. Copyright:
*This material is Lechosław Tuz, Vít Novák, and František Tatíček's paper: Based on Evaluation of the Microstructure and Properties of As-Cast Magnesium Alloys with 9% Al and 9% Zn Additions.
*Paper Source: https://doi.org/10.3390/ma18010010
This material was summarized based on the above paper, and unauthorized use for commercial purposes is prohibited.
Copyright © 2025 CASTMAN. All rights reserved.