This introduction paper is based on the paper "[WATER-SOLUBLE CORES – VERIFYING DEVELOPMENT TRENDS]" published by "[Materiali in tehnologije / Materials and technology]".
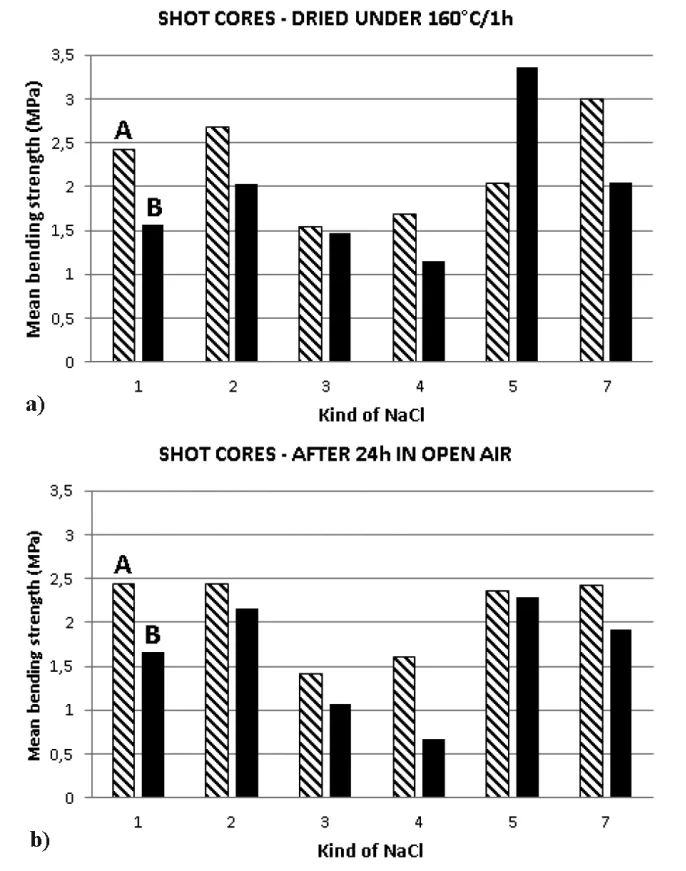
1. Overview:
- Title: WATER-SOLUBLE CORES – VERIFYING DEVELOPMENT TRENDS
- Author: Eliška Adámková, Petr Jelínek, Jaroslav Beňo, František Mikšovský
- Year of publication: 2015
- Journal/academic society of publication: Materiali in tehnologije / Materials and technology
- Keywords: salt cores, inorganic salts, die casting, warm box, non-ferrous metals
2. Abstract:
Application of pure inorganic salt-based cores has been known since the end of the 20th century, especially in the field of gravity and low-pressure die casting. The contemporary trend in technology leads to the use of the cores in the field of non-ferrous-alloy high-pressure die casting. The main methods of the core production include high-pressure squeezing and shooting (warm core box). During research processes it was shown that pure-salt application is not very suitable for high-pressure casting. That is why a composite salt-based matrix of defined properties was started to be used. The aim of the paper is to verify the influences of the chemical composition, shape and morphology of the grains of various NaCl compounds on the mechanical properties (the bending strength) of water-soluble salt cores used for Al-alloy high-pressure die casting and to evaluate their properties resulting from the squeezing and shooting methods.
3. Introduction:
The increasing demand for complex castings, particularly in the automotive industry, necessitates solutions for removing cores from hard-to-reach areas. Water-soluble inorganic salt cores offer a viable solution, enabling core removal via dissolution in water, which facilitates an environmentally friendly closed-loop production system through reverse crystallization. While traditionally used in gravity and low-pressure die casting of non-ferrous alloys, there is potential for their application in Al-alloy high-pressure die casting. Current development focuses on two manufacturing techniques: high-pressure squeezing utilizing recrystallization, and shooting using inorganic binders like alkaline silicates. Due to the high cost of chemically pure salts, investigating more cost-effective common salts as the basic matrix is crucial.
4. Summary of the study:
Background of the research topic:
The production of increasingly complex castings presents challenges for core removal. Water-soluble salt cores provide a technological solution, particularly for areas inaccessible to mechanical cleaning, and allow for environmentally friendly closed-circuit production.
Status of previous research:
The use of water-soluble salt cores is established in gravity and low-pressure die casting [2]. Research is exploring their application in high-pressure die casting of Al-alloys [3, 4]. Two primary manufacturing methods are under development: high-pressure squeezing [5, 6] and shooting with inorganic binders [5, 6]. The need for cost-effective alternatives to chemically pure salts drives the investigation into common salts.
Purpose of the study:
The study aims to verify the applicability of various commercially available NaCl salts (common salts) in the Czech market as potential replacements for expensive chemically pure salt in core production. It investigates the influence of salt origin (rock, Alpine, sea), chemical composition, grain shape, and surface morphology on the mechanical properties (bending strength) of salt cores manufactured using both high-pressure squeezing and shooting methods.
Core study:
The research involved selecting six different types of NaCl salts (technical/common and chemically pure) based on declared chemical compositions, grain shapes, and morphologies (Table 1). Salt cores were produced using two methods: shooting (warm core box with Na-silicate binder) and high-pressure squeezing. The mechanical properties (bending strength) of the cores were evaluated under different conditions (after 24h in air, after drying). Apparent porosity was calculated, and actual porosity was measured using mercury porosimetry. Grain shape, surface morphology, and the presence of additives were analyzed using SEM and EDX techniques (Figures 4-7). The hygroscopicity of cores made by both methods was also investigated (Figure 8).
5. Research Methodology
Research Design:
The research employed an experimental design comparing the properties of water-soluble salt cores made from different types of commercially available NaCl salts using two distinct manufacturing techniques: shooting and high-pressure squeezing. Key properties like bending strength, porosity, and hygroscopicity were measured and compared. Microstructural analysis (SEM/EDX) was used to correlate salt characteristics with core properties.
Data Collection and Analysis Methods:
- Salt Selection: Six types of NaCl salts were chosen based on manufacturer-declared chemical compositions (Table 1), representing different origins (rock, Alpine, sea) and purity levels (including chemically pure).
- Core Production (Shooting): A mixture of 100 mass parts NaCl and 5 mass parts Na-sodium silicate (M = 1.85) was used. Cores were produced with a hardening time of 50 s, core-box temperature of 190 °C, shooting speed of 7.5 s, and air pressure of 7.5-8 bar. Both original granulometry and a sieved fraction (0.063-1.0 mm) were tested.
- Core Production (Squeezing): A sieved fraction (0.063-1.0 mm) with NaCl humidity of 0.65–1.04 % was used. Cores were produced with a squeezing force of 200 kN, squeezing tension of 104 MPa, and a load rate of 9 kN/s.
- Mechanical Testing: Bending strength was measured after 24 h in open air and after drying (160 °C for 1 h for shot cores, 105 °C for 1 h for squeezed cores).
- Porosity Measurement: Apparent porosity was calculated from bulk density (Equation 1). Actual porosity, pore size, and distribution were measured using mercury porosimetry (Table 3).
- Microanalysis: SEM was used to observe grain shape and surface morphology. EDX microanalysis determined the elemental composition of the salts and identified additives (Table 2, Figures 4-7).
- Hygroscopicity Test: Weight change of cores stored under controlled climate conditions (35-58 % RH, 20.7-24.9 °C) was measured over 23 days (Figure 8).
Research Topics and Scope:
The study focused on evaluating the suitability of various common NaCl salts as a replacement for chemically pure NaCl in water-soluble core production for potential use in high-pressure die casting of Al-alloys. The scope included:
- Comparison of six NaCl salt types (rock, Alpine, sea, chemically pure).
- Evaluation of two core manufacturing methods: shooting and high-pressure squeezing.
- Assessment of core properties: bending strength, apparent and actual porosity, hygroscopicity.
- Analysis of salt characteristics: chemical composition, grain shape, surface morphology, and the effect of additives using SEM/EDX.
- Impact of dust fraction removal and drying on core properties.
6. Key Results:
Key Results:
- Cores manufactured using the squeezing method consistently achieved 2-3 times higher bending strengths compared to shot cores (Figures 1, 2, 3).
- Squeezed cores exhibited significantly lower actual porosity (6-12%) compared to shot cores (19-24%) (Table 3), resulting in lower hygroscopicity (Figure 8).
- Shot cores showed high hygroscopicity correlating with their higher porosity, suggesting a need for surface protection (coatings, lubricants) for practical application (Section 7).
- For shot cores, removing the dust fraction (< 0.063 mm) generally led to a decrease in bending strength (except for sea salt) and an increase in apparent porosity (Figures 1, 2). Drying significantly increased the strength of shot sea salt cores (Figure 1a).
- Drying significantly increased the bending strength of squeezed cores (Figure 3a).
- Crushed rock salts (samples 1, 2) generally yielded good strength results for both production methods. The presence of fine dust in rock salt contributed positively to strength (Section 8).
- Alpine salts (samples 3, 4), characterized by regular cubic grains resulting from recrystallization, showed lower strengths. This was attributed to anti-sticking additives (CaCO3, MgCO3), confirmed by EDX (Figure 5), hindering grain binding during both shooting (with silicate) and squeezing (recrystallization) (Sections 4, 7).
- Chemically pure NaCl (sample 7), with a regular dipyramidal grain shape, demonstrated high strength in both squeezed and shot cores. This shape, resembling SiO2 sand, allows for a high coordination number and appears advantageous for both core production methods (Sections 3.2, 4, 7, Figure 7).
- Anti-sticking additives (CaCO3, MgCO3, SiO2, K4[Fe(CN6)]·3H2O) present in some commercial salts (especially Alpine) adversely affected core strength properties for both production techniques (Section 7, 8).
- The investigation concluded that chemically pure salt can be adequately replaced by significantly cheaper (up to 50 times) crushed rock salt for producing water-soluble cores (Section 8).
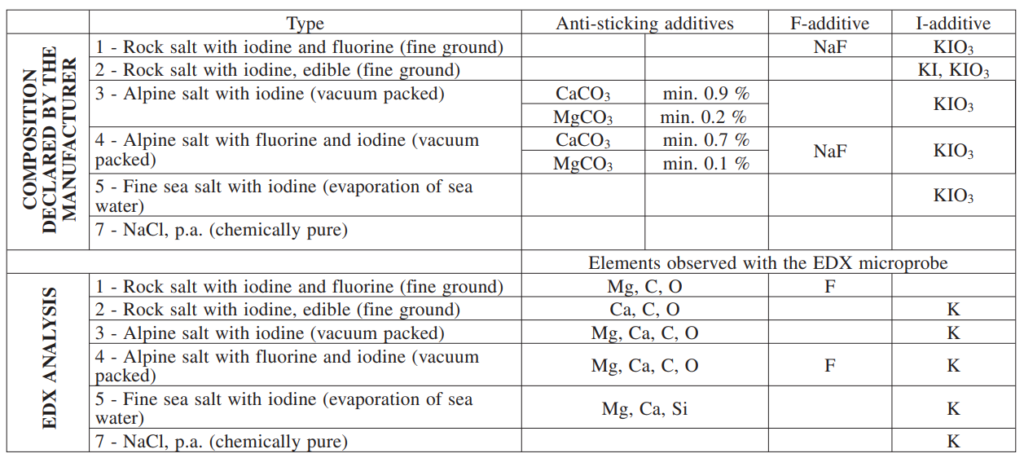
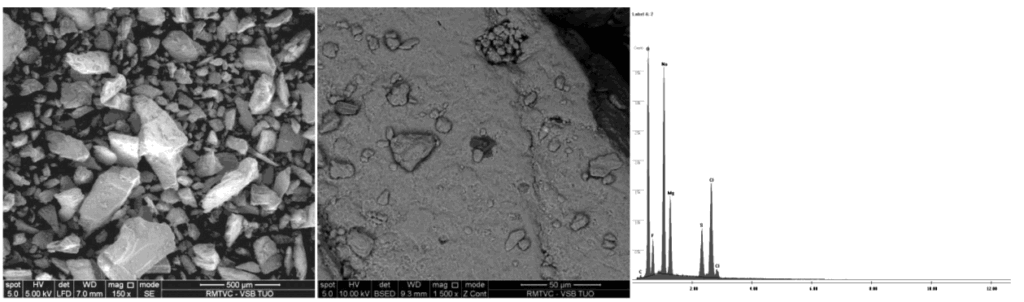
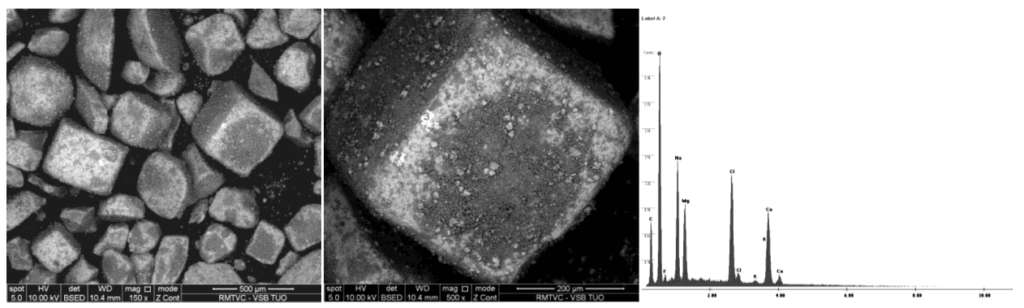
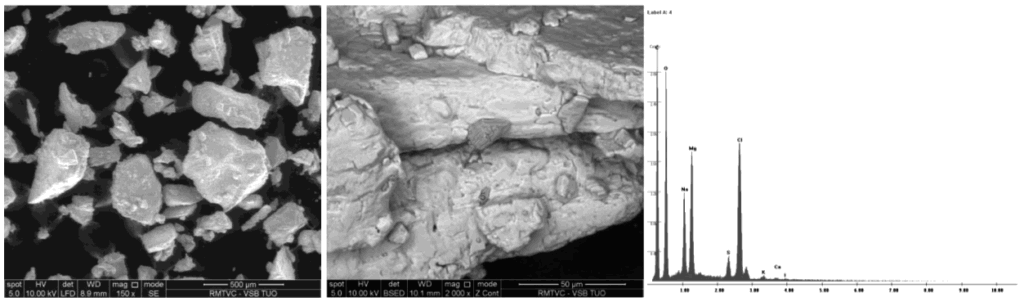
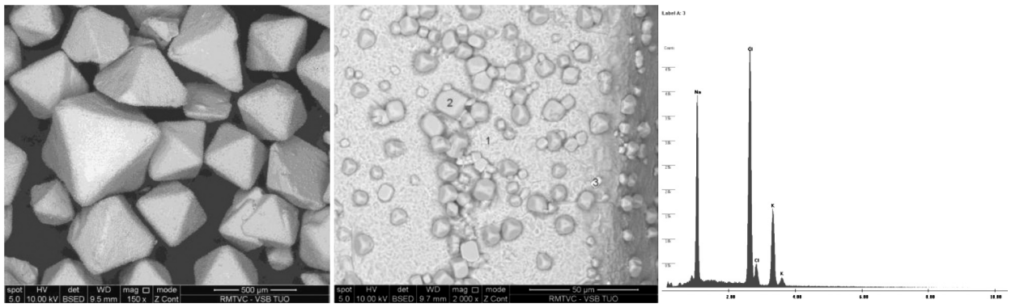
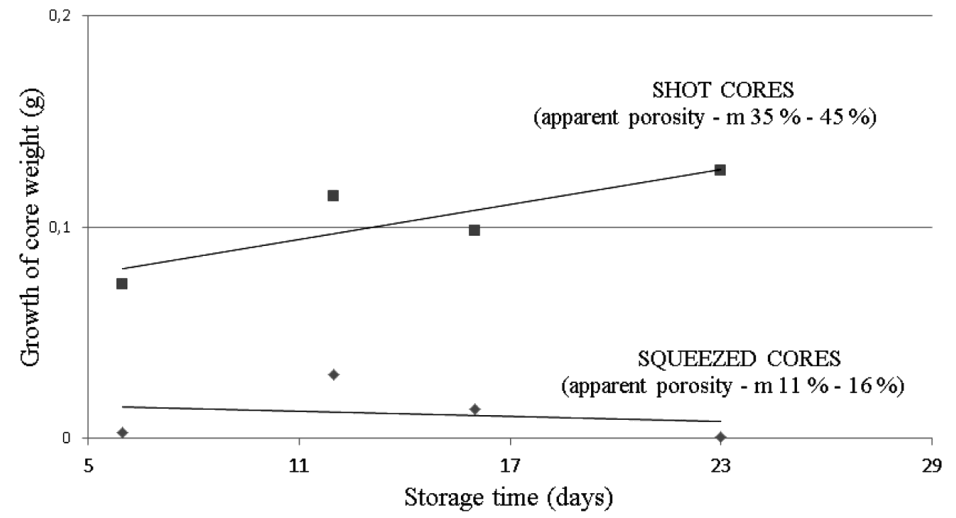
Figure Name List:
- Figure 1: Comparison of the mean bending strengths of 6 types of shot salt: a) after drying and b) after 24 h in the open air (the mean value for 6 cores; A – original granularity, B – fraction of 0.063–1.0 mm)
- Figure 2: Comparison of: a) the mean bending strengths and b) apparent porosities of 6 types of shot salts after 24 h in the open air (the mean value for 6 cores; A – original granularity, B – fraction of 0.063–1.0 mm)
- Figure 3: Comparison of: a) the mean bending strengths and b) apparent porosities of 6 types of squeezed salts (the mean value for 6 cores; A – cores additionally dried at 105 °C 1 h, B – 24 h in the open air)
- Figure 4: Shattered surface of crushed-rock salts (samples Nos. 1, 2) and EDX analysis of its chemical composition
- Figure 5: Regular cubic grains of Alpine salts (samples Nos. 3, 4) and EDX analysis confirming the presence of anticaking agents on the salt grain surface (MgCO3, CaCO3)
- Figure 6: Oval form of sea-salt grains (sample No. 5) and EDX analysis of its chemical composition
- Figure 7: Regular dipyramidal form of NaCl, p. a. – standard (sample No. 7) and EDX analysis of its chemical composition
- Figure 8: Different hygroscopicity trends for squeezed and shot cores
7. Conclusion:
The research investigated replacing expensive chemically pure salt with common salt for producing foundry cores potentially applicable in gravity, low-pressure, and high-pressure die casting of non-ferrous alloys.
- The best strength results were achieved using crushed rock salts for both squeezing and shooting methods. Fine-dust fractions present in these salts contributed positively to core strength.
- Salts with recrystallized, regular cubic grains (Alpine salts) were less suitable due to lower strengths, negatively impacted by anti-sintering additives (SiO2, MgCO3, CaCO3, K4[Fe(CN6)]·3H2O) which hinder binding mechanisms.
- The dipyramidal shape of chemically pure salt proved advantageous for strength.
- Comparing production methods, squeezed cores exhibited higher mechanical properties (bending strength) and minimum hygroscopicity due to lower actual porosity.
- The study demonstrated that chemically pure salt can be effectively replaced by common rock salt, offering a significant cost reduction (up to 50 times cheaper).
8. References:
- [1] H. Michels et al., Suitability of lost cores in rheocasting process, Trans. Nonferrous Met. Soc. China, 20 (2010), s948–s953
- [2] P. Stingl, G. Schiller, Leichte und rückstandfreie Entkernung, Giesserei Erfahrungsaustausch, 6 (2009), 4–8
- [3] P. Jelínek et al., Salt cores in high-pressure die-casting technology, In: 5. Holečkova's conference, 1 edition, Czech Foundry Society, Brno 2013, 63–67 (in Czech)
- [4] E. Adámková et al., Technology of Water Soluble Cores for Foundry Applications, Proceedings of XX. International Student's Day of Metallurgy, Cracow, Poland, 2013, 8 p. (CD-ROM)
- [5] P. Jelínek et. al., Development of technology of salt cores manufacture, Slévárenství, LXI (2013) 1–2, 28–31 (in Czech)
- [6] P. Jelínek et. al., Influencing the strength characteristics of salt cores soluble in water, Slévárenství, LX (2012) 3–4, 85–89 (in Czech)
9. Copyright:
- This material is a paper by "Eliška Adámková, Petr Jelínek, Jaroslav Beňo, František Mikšovský". Based on "[WATER-SOLUBLE CORES – VERIFYING DEVELOPMENT TRENDS]".
- Source of the paper: [DOI URL not available in the provided document]
This material is summarized based on the above paper, and unauthorized use for commercial purposes is prohibited.
Copyright © 2025 CASTMAN. All rights reserved.