This introduction paper is based on the paper "Thermal management technology of high-power light-emitting diodes for automotive headlights" published by "IEICE Electronics Express".
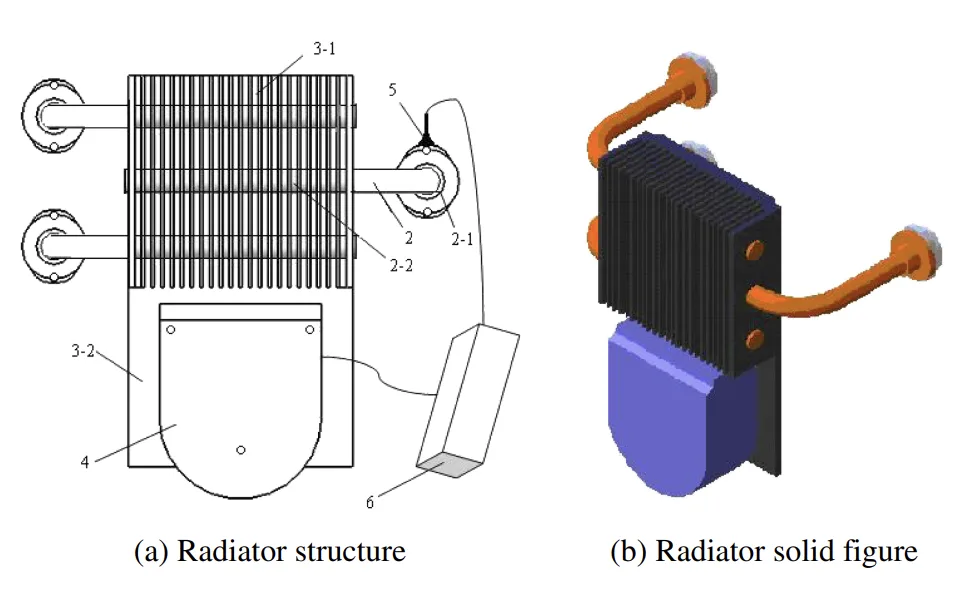
1. Overview:
- Title: Thermal management technology of high-power light-emitting diodes for automotive headlights
- Author: Hui-Ming Qu, Xiao-Hui Yang, Qi Zheng, Xin-Tao Wang, and Qian Chen
- Year of publication: 2014
- Journal/academic society of publication: IEICE Electronics Express
- Keywords: LED automotive headlight, thermal management, cooling structure, thermal simulation, temperature feedback
2. Abstract:
The heat dissipation problem of high-power LEDs (Light-Emitting Diodes) limits their applications in automobile headlights. The heat demand for cooling LED headlights is analyzed based on heat transfer theory. This study proposes an initiative heat dissipation technology of temperature feedback control combined heat pipe and heat sink. The corresponding hardware and software control processes are designed. The temperature feedback control is realized with an MCU (Micro Control Unit) that judges and controls the synthetic jet device working process. A 3D model for the heat pipe radiator is constructed using CATIA. The model is optimized with the fluid thermodynamic simulation software FLOEFD. Finally, a sample lamp is prepared and tested with an infrared thermometer. The temperature distribution on each LED light source and radiator fin is quantitatively measured and analyzed. These results confirm that the designs of the thermal management system and the proposed technique solve the heat dissipation problem of high-power LED automotive headlights under the ambient temperature 50°C indeed.
3. Introduction:
Light-Emitting Diodes (LEDs) are increasingly used in automotive lighting due to their small size, long life, low energy consumption, vibration resistance, fast start-up time, and environmental friendliness. High-power, high-brightness white LEDs are becoming candidates for automobile headlights, positioning them as "fourth-generation" lighting. However, the low electro-optical conversion efficiency of LEDs results in a significant portion of input power transforming into heat, leading to increased junction temperatures. High junction temperatures can cause reliability issues such as low quantum efficiency, wavelength shifts, short lifetime, and catastrophic failure. Therefore, proper thermal management is critical for the adoption of LEDs in high-efficiency lighting systems, especially for automotive headlights which operate in demanding environments close to the engine compartment, requiring high sealing, shock resistance, stability at high ambient temperatures, and within limited space. Effective thermal design is crucial to ensure the normal operation and improve the performance of LED automotive headlights.
4. Summary of the study:
Background of the research topic:
High-power LEDs, while promising for automotive headlights, generate substantial heat. This heat, if not managed effectively, increases the LED junction temperature, leading to performance degradation and reduced lifespan. Automotive headlights operate in harsh conditions, including high ambient temperatures and limited space, making thermal management particularly challenging.
Status of previous research:
Various thermal management methods for LEDs have been studied, including passive solutions like fin-heat sinks [17] and heat pipes [18], and active cooling systems [15, 16]. Other advanced methods include micro-channel heat sinks [12, 13], micro-jet array cooling [21, 22], electrohydrodynamic approaches [23], thermoelectric cooling [24], phase change methods using MEMS technology [25], and piezoelectric fans [26]. However, these strategies can involve complex design, reliability issues, high costs, or insufficient cooling capability, hindering their commercialization, especially for the demanding requirements of automotive LED headlights.
Purpose of the study:
The study aims to design an effective cooling structure combined with temperature feedback control heat dissipation to meet the cooling requirements of high-power LED automotive headlights. The goal is to solve the heat dissipation problem that limits the application and popularization of high-power LED headlights.
Core study:
This study proposes an initiative heat dissipation technology that combines a heat pipe and heat sink with temperature feedback control. The system includes:
- A thermal design based on heat transfer theory for LED headlights, using three integrated packages of white LEDs and three corresponding heat pipes.
- A temperature feedback active cooling device where a synthetic jet is installed with the heat pipe condenser section and aluminum pipe sink.
- An MCU (Micro Control Unit) to monitor the temperature via a sensor and control the synthetic jet device.
- 3D modeling of the heat pipe radiator structure using CATIA.
- Optimization of the model using fluid thermodynamic simulation software FLOEFD.
- Experimental validation of a sample lamp equipped with the designed thermal management system using an infrared thermometer.
5. Research Methodology
Research Design:
The research involved several stages:
- Theoretical analysis of heat transfer in LED headlights and development of a thermal resistance model for the cooling system.
- Design of a cooling system incorporating passive elements (heat pipes, heat sink fins) and an active element (synthetic jet device).
- Integration of a temperature feedback control system using a temperature sensor (DS18B20) and an MCU to manage the operation of the synthetic jet.
- Construction of a 3D model of the LED headlight radiator using CATIA.
- Thermal and fluid dynamic simulation of the designed radiator using FLOEFD software to predict performance under specific operating conditions.
- Fabrication of a sample LED headlight based on the design.
- Experimental testing of the sample lamp to verify the simulation results and assess the effectiveness of the thermal management system.
Data Collection and Analysis Methods:
- Simulation: The FLOEFD software was used to simulate the temperature distribution on the radiator and the airflow patterns. Key outputs included temperature contours and maximum temperatures at various points.
- Experimental Testing: An infrared thermometer was used to measure the temperature distribution on the LED light sources and radiator fins of the sample lamp in an obturation room at a controlled ambient temperature. Real-time temperature data was recorded and analyzed, particularly the effect of the synthetic jet operation.
Research Topics and Scope:
The research focused on the thermal management of high-power LEDs specifically for automotive headlight applications. The scope included:
- The design and analysis of a hybrid cooling system combining heat pipes, heat sinks, and an MCU-controlled synthetic jet.
- Modeling and simulation of the radiator structure under conditions relevant to automotive use (ambient temperature 50°C, driving speed 45 km/h for simulation).
- Experimental validation of the cooling performance, particularly the effectiveness of the temperature feedback control and synthetic jet, under stationary conditions at an ambient temperature of 50°C.
6. Key Results:
Key Results:
- A thermal resistance model for the cooling system was established (Fig. 1, Equations 1-10).
- A 3D model of the LED headlight radiator, incorporating heat pipes, heat sink fins, a synthetic jet device, a temperature sensor, and an MCU control unit, was designed using CATIA (Fig. 2).
- FLOEFD simulation results (Fig. 3) for an ambient temperature of 50°C and a driving speed of 45 km/h showed:
- Maximum radiator temperature of 92.9°C.
- LED junction temperature of 124.6°C (calculated with a fixed temperature difference of 31.7°C between bracket and PN junction), meeting the design requirement of <125°C.
- Experimental tests on a sample lamp (Fig. 4) at an ambient temperature of 50°C (stationary condition) demonstrated:
- The light source temperature stabilized after 10 minutes of synthetic jet operation (Fig. 5).
- The synthetic jet, when active, lowered the sample lamp temperature by 18°C (Fig. 6).
- The temperature feedback control system effectively managed the LED temperature, ensuring it did not exceed design requirements.
- The proposed thermal management system and technique successfully address the heat dissipation problem of high-power LED automotive headlights.
Figure Name List:
- Fig. 1. Thermal resistance network diagram of the cooling system
- Fig. 2. LED headlight radiator structure
- Fig. 3. FLOEFD simulation results of the radiator
- Fig. 4. Image of the sample lamp test
- Fig. 5. The highest temperature of test positions versus the run time of synthetic jet
- Fig. 6. Heat dissipation effect with the synthetic jet
7. Conclusion:
The study analyzes the cooling requirements of LED headlights under different conditions. A passive heat pipe cooling technology, relying on the reverse flow of driving, and an active cooling technology using temperature feedback control are proposed. The radiator structure and sample lamp were designed with CATIA. FLOEFD simulation and experimental results demonstrate that the junction temperature of the LEDs remains in an appropriate range when the ambient temperature is 50°C, even under motionless conditions. The highest temperature can be controlled within the required range. The proposed technology provides a viable approach for solving the heat dissipation problem, which currently limits the application and popularization of high-power LED headlights.
8. References:
- [1] C.-C. Hsieh, Y.-H. Li and C.-C. Hung: Appl. Opt. 52 (2013) 5221. DOI:10.1364/AO.52.005221
- [2] M. Arik, C. Becker, S. Weaver and J. Petroski: Proc. SPIE 5187 (2004) 64. DOI:10.1117/12.512731
- [3] R. V. Steele: Laser Focus World 41 (2005) 91.
- [4] A. Cvetkovic, O. Dross, J. Chaves, P. Benitez, J. C. Miñano and R. Mohedano: Opt. Express 14 (2006) 13014. DOI:10.1364/OE.14.013014
- [5] J.-J. Chen, K.-L. Huang and P.-C. Lin: Opt. Eng. 49 (2010) 073002. DOI:10.1117/1.3461984
- [6] W. Pohlmann, T. Vieregge and M. Rode: Proc. SPIE 6797 (2007) 67970D. DOI:10.1117/12.760978
- [7] M. Ha and S. Graham: Microelectron. Reliab. 52 (2012) 836. DOI:10.1016/j.microrel.2012.02.005
- [8] M. Arik, A. Setlur, S. Weaver, D. Haitko and J. Petroski: J. Electron. Packag. 129 (2007) 328. DOI:10.1115/1.2753958
- [9] N. Narendran and Y. Gu: IEEE/OSA J. Disp. Technol. 1 (2005) 167. DOI:10.1109/JDT.2005.852510
- [10] Q. Chen, X. Luo, S. Zhou and S. Liu: Rev. Sci. Instrum. 82 (2011) 084904. DOI:10.1063/1.3624699
- [11] A. Jayawardena, Y.-w. Liu and N. Narendran: Solid-State Electron. 86 (2013) 11. DOI:10.1016/j.sse.2013.04.001
- [12] D. B. Tuckerman and R. F. W. Pease: IEEE Electron Device Lett. 2 (1981) 126. DOI:10.1109/EDL.1981.25367
- [13] T. Kishimoto and S. Sasaki: Electron. Lett. 23 (1987) 456. DOI:10.1049/el:19870328
- [14] A. S. Panahi: Proc. SPIE 8368 (2012) 83680T. DOI:10.1117/12.977566
- [15] A. Christensen and S. Graham: Appl. Therm. Eng. 29 (2009) 364. DOI:10.1016/j.applthermaleng.2008.03.019
- [16] O. Kückmann: Proc. SPIE 6134 (2006) 613404. DOI:10.1117/12.646321
- [17] X. B. Luo, W. Xiong, T. Cheng and S. Liu: IET Optoelectron. 3 (2009) 225. DOI:10.1049/iet-opt.2008.0068
- [18] L. Kim, J. H. Choi, S. H. Jang and M. W. Shin: Thermochim. Acta 455 (2007) 21. DOI:10.1016/j.tca.2006.11.031
- [19] Z. M. Wang, K. Bao, L. P. Xu, C. X. Luo, B. Zhang, H. Ji, Q. Ouyang and Y. Chen: Microelectron. Eng. 84 (2007) 1223. DOI:10.1016/j.mee.2007.01.188
- [20] Y. Lai, N. Cordero, F. Barthel, F. Tebbe, J. Kuhn, R. Apfelbeck and D. Würtenberger: Appl. Therm. Eng. 29 (2009) 1239. DOI:10.1016/j.applthermaleng.2008.06.023
- [21] X. B. Luo and S. Liu: IEEE Trans. Adv. Packag. 30 (2007) 475. DOI:10.1109/TADVP.2007.898522
- [22] S. Liu, J. H. Yang, Z. Y. Gan and X. B. Luo: Int. J. Therm. Sci. 47 (2008) 1086. DOI:10.1016/j.ijthermalsci.2007.09.005
- [23] S. W. Chau, C. H. Lin, C. H. Yeh and C. Yang: 33rd Annual Conference of the IEEE Industrial Electronics Society (2007) 2934. DOI:10.1109/IECON.2007.4460209
- [24] J. Li, B. Ma, R. Wang and L. Han: Microelectron. Reliab. 51 (2011) 2210. DOI:10.1016/j.microrel.2011.05.006
- [25] H. Ye, M. Mihailovic, C. K. Y. Wong, H. W. van Zeijl, A. W. J. Gielen, G. Q. Zhang and P. M. Sarro: Appl. Therm. Eng. 52 (2013) 353. DOI:10.1016/j.applthermaleng.2012.12.015
- [26] T. Acikalin, S. V. Garimella, J. Petroski and A. Raman: 9th Intersociety Conference on Thermal and Thermomechanical Phenomena in Electronic Systems (2004) 663. DOI:10.1109/ITHERM.2004.1319239
- [27] X.-Y. Lu, T.-C. Hua, M.-J. Liu and Y.-X. Cheng: Thermochim. Acta 493 (2009) 25. DOI:10.1016/j.tca.2009.03.016
- [28] X.-Y. Lu, T.-C. Hua and Y.-X. Cheng: Microelectron. J. 42 (2011) 1257. DOI:10.1016/j.mejo.2011.08.009
- [29] F. Chen, K. Wang, Z. Qin, D. Wu, X. Luo and S. Liu: Opt. Express 18 (2010) 20926. DOI:10.1364/OE.18.020926
- [30] S. Jang and M. W. Shin: IEEE Trans. Device Mater. Rel. 8 (2008) 561. DOI:10.1109/TDMR.2008.2002355
- [31] H.-Y. Ryu, K.-H. Ha, J.-H. Chae, O.-H. Nam and Y.-J. Park: Appl. Phys. Lett. 87 (2005) 093506. DOI:10.1063/1.2037201
- [32] Y.-J. Lee, C.-J. Lee and C.-H. Chen: Jpn. J. Appl. Phys. 50 (2011) 04DG18. DOI:10.1143/JJAP.50.04DG18
- [33] M. Le Berre, G. Pandraud, P. Morfouli and M. Lallemand: J. Micromech. Microeng. 16 (2006) 1047. DOI:10.1088/0960-1317/16/5/023
- [34] G. J. Michna, E. A. Browne, Y. Peles and M. K. Jensen: J. Heat Transfer 131 (2009) 111402. DOI:10.1115/1.3154750
9. Copyright:
- This material is a paper by "Hui-Ming Qu, Xiao-Hui Yang, Qi Zheng, Xin-Tao Wang, and Qian Chen". Based on "Thermal management technology of high-power light-emitting diodes for automotive headlights".
- Source of the paper: 10.1587/elex.11.20140965
This material is summarized based on the above paper, and unauthorized use for commercial purposes is prohibited.
Copyright © 2025 CASTMAN. All rights reserved.