This article introduces the paper "Thermal Flow Analysis for Development of LED Fog Lamp for Vehicle".
1. Overview:
- Title: Thermal Flow Analysis for Development of LED Fog Lamp for Vehicle (English) / 차량 LED 안개등 개발을 위한 열유동 해석 (Korean)
- Author: 이석영 (Suk Young Lee)
- Publication Year: 2019
- Publishing Journal/Academic Society: 에너지공학 (Journal of Energy Engineering), Vol. 28, No. 4, pp.35-41(2019)
- Keywords: LED, 안개등, 열유동해석, 대류 (Korean) / Light emitting diode, fog lamp, thermal fluid analysis, convection (English)
2. Research Background:
- Social/Academic Context of the Research Topic:
- Halogen light sources, previously widely used in vehicle fog lamps, have disadvantages such as high power consumption and short lifespan.
- To overcome these drawbacks, automotive light source technology is gradually being replaced by LEDs (Light Emitting Diodes).
- LED light sources offer significantly longer lifespans compared to halogen lights and are effective in reducing fuel consumption and CO2 emissions.
- Furthermore, LEDs are composed of small chips, allowing for miniaturization and flexibility in light source arrangement when designing LED fog lamps for vehicles.
- Limitations of Existing Research:
- Vehicle LED fog lamps can experience shortened lifespans due to high heat generated by the LEDs during operation.
- Heat generated inside the fog lamp is primarily dissipated through the heatsink, but residual heat is released externally through convection.
- Existing research has mainly focused on heat dissipation methods using heatsinks, with limited studies on improving cooling efficiency through convection.
- If cooling efficiency through convection decreases, heat accumulation in major lamp components (lenses, reflectors, bezels, etc.) and high-temperature exposure of the LED light source can shorten the lifespan of the fog lamp.
- Necessity of the Research:
- To extend the lifespan and enhance the performance of LED fog lamps, it is essential to develop an efficient heat dissipation mechanism through convection.
- In particular, design technology that optimizes the airflow inside the fog lamp to maximize convective heat transfer performance is required.
- This study aims to improve the cooling efficiency of vehicle LED fog lamps by focusing on convection-based heat dissipation performance in addition to heatsinks.
- To achieve this, the core objective of the research is to design the optimal vent location to effectively discharge internal air and intake external air for LED fog lamps.
3. Research Purpose and Research Questions:
- Research Purpose:
- The primary purpose of this study is to improve the heat dissipation performance of vehicle LED fog lamps.
- Specifically, it aims to maximize cooling efficiency by utilizing convection phenomena in addition to heat dissipation through heatsinks.
- To this end, the goal is to control the airflow inside the LED fog lamp and design the optimal vent location to efficiently discharge heat to the outside.
- Ultimately, it aims to contribute to extending the lifespan and improving the reliability of LED fog lamps.
- Key Research Questions:
- What is the optimal vent installation location for efficient heat dissipation in vehicle LED fog lamps?
- How do airflow characteristics and velocity inside the fog lamp change with vent location variations?
- What is the impact of vent location variations on the temperature distribution and average temperature inside the fog lamp?
- Does vent design for improved convective heat transfer performance effectively contribute to the cooling efficiency of LED fog lamps?
- Research Hypotheses:
- The Case3 model (vents installed above and below the fog lamp) will effectively induce natural convection phenomena generated by temperature differences, increase airflow velocity, and exhibit superior cooling performance compared to the existing model (Case1) by efficiently dissipating heat.
- Specific vent locations will increase the turbulence intensity of the air inside the fog lamp, further activating convective heat transfer, which will contribute to reducing the internal temperature of the fog lamp.
- By comparing and verifying the numerical analysis results with experimental results, the validity of the proposed vent design can be demonstrated.
4. Research Methodology
- Research Design:
- This study adopted a research design that combines numerical analysis (Computational Fluid Dynamics, CFD) and experimental verification to improve the thermal management performance of vehicle LED fog lamps.
- First, CFD analysis of LED fog lamps was performed using ANSYS CFX v18.0 commercial software to predict cooling performance changes according to various vent locations.
- Subsequently, to verify the numerical analysis results, actual LED fog lamp prototypes were manufactured, and temperature measurement experiments were conducted to measure internal temperature changes and compare them with the numerical analysis results.
- Data Collection Method:
- Numerical Analysis (CFD Simulation):
- 3D thermal flow analysis was performed using ANSYS CFX v18.0 program.
- Analysis cases were configured by designing the existing prototype (Case1) and Case2, Case3 models with modified vent locations.
- For each case, the airflow velocity, temperature, turbulence intensity distribution, etc., inside the fog lamp were numerically calculated.
- Experimental Verification (Temperature Measurement):
- An air conditioning experimental apparatus was used to create experimental conditions (temperature 20℃, humidity RH40%, wind speed 0m/s).
- Resistance temperature sensors were installed at 3 points inside the fog lamp, and average temperatures were measured through 10 repetitions.
- Experimental measurements and numerical analysis results were compared to verify the validity of the analysis.
- Numerical Analysis (CFD Simulation):
- Analysis Method:
- Mesh Generation: Meshes for the analysis model were generated using the mesh generation program built into ANSYS. A mesh consisting of 2.51 million nodes and 5.57 million elements was used to ensure calculation accuracy.
- Boundary Conditions:
- Analysis conditions were set as Case1, Case2, and Case3, according to the vent inlet/outlet locations and number as shown in Fig. 7, including the existing prototype Case1.
- The heat generation rate of the LED was set to 1.5×10^4 W/m³.
- The airflow inside the fog lamp was assumed to be incompressible, turbulent, and viscous flow, and the k-ε model was used as the turbulence model.
- The working fluid was assumed to be air, and the external air temperature was set to 20℃, and the air velocity was set to 0m/s (vehicle stationary state).
- Data Analysis: From the numerical analysis results, the airflow velocity distribution (Fig. 10), airflow streamlines (Fig. 11), air temperature distribution (Fig. 12), and turbulence intensity distribution (Fig. 13) inside the fog lamp for each case were analyzed. Quantitative indicators such as average airflow velocity, average temperature, and average turbulence intensity (Table 3) were compared and analyzed to evaluate cooling performance changes according to vent location variations. Experimental measurements and numerical analysis results were compared to verify the accuracy of the analysis (Table 2).
- Research Subjects and Scope:
- The research subject of this study is vehicle LED fog lamps.
- The scope of the study is limited to the analysis of thermal flow phenomena inside LED fog lamps and the evaluation of cooling performance according to vent location variations.
- Studies on various vent shapes and size variations are excluded from the scope of this study.
- Furthermore, studies on cooling performance changes due to changes in external forced convection conditions of LED fog lamps are also not included in the scope of this study.
5. Main Research Results:
- Key Research Results:
- Airflow Velocity: The Case3 model (vents installed above and below) showed the highest average airflow velocity compared to the Case1 (existing prototype) and Case2 (vents installed on the side) models. In particular, the increase rate of airflow velocity in Case3 was relatively larger than in other cases.
- Internal Air Temperature: The Case3 model showed the lowest average internal air temperature, followed by Case2 and Case1 models in descending order. The average temperature of the Case3 model was the lowest.
- Turbulence Intensity: The Case3 model showed the highest average turbulence intensity, followed by Case2 and Case1 models in descending order. The turbulence intensity of the Case3 model was the highest.
- Experimental Verification: The error in average internal air temperature between experimental measurements and numerical analysis results was 1.7℃, verifying the validity of the numerical analysis.
- Statistical/Qualitative Analysis Results:
- Table 2. Experimental result: Positions 1 2 3 Average Temp.(°C) 63.2 33.7 37.9 44.9
- Experimental results showed that the temperature at Position 1 (near the LED) was the highest, and the temperatures at Position 2 and 3 (near the inner lens and housing) were relatively low. The average temperature of the 3 points was 44.9℃.
- Table 3. Calculated results: Items CASE1 CASE2 CASE3 Temperature (°C) 43.2 40.3 32.8 Velocity(mm/s) 2.11 2.32 3.16 Τ.Κ.Ε.(J/ton) 0.078 0.105 0.272
- Numerical analysis results showed that the Case3 model exhibited the lowest average temperature (32.8℃) and the highest average velocity (3.16 mm/s) and turbulence intensity (0.272 J/ton).
- Figure Name List:
- Fig. 1. Fog lights attached to the vehicle
- Fig. 2. Prototype of vehicle fog lamp
- Fig. 3. Exploded view of LED fog lamp for vehicle
- Fig. 4. 3D modeling for analysis
- Fig. 5. Fluid Region Extraction for Thermal Flow Analysis
- Fig. 6. Mesh generation
- Fig. 7. Set three parameters for the outside air entrance
- Fig. 8. Experimental equipment
- Fig. 9. Mounting position of temperature sensor for experiment
- Fig. 10. Distribution of calculated air velocity in LED fog lamp
- Fig. 11. Distribution of calculated air streamline in LED fog lamp
- Fig. 12. Distribution of calculated air temperature in LED fog lamp
- Fig. 13. Distribution of calculated air T.K.E. in LED fog lamp
- Table 2. Experimental result: Positions 1 2 3 Average Temp.(°C) 63.2 33.7 37.9 44.9
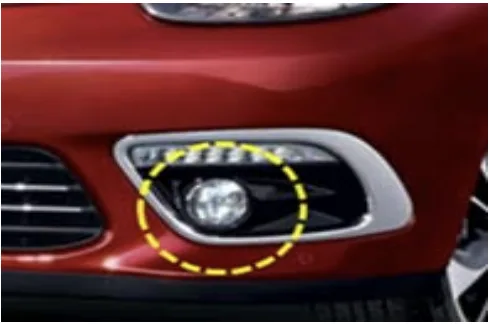
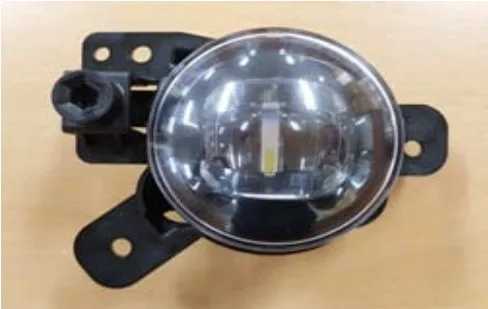
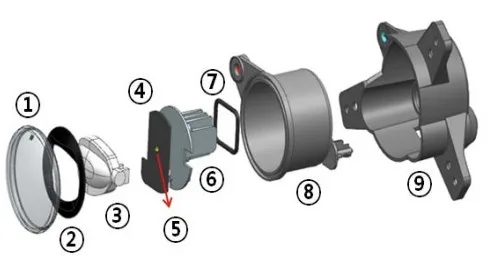
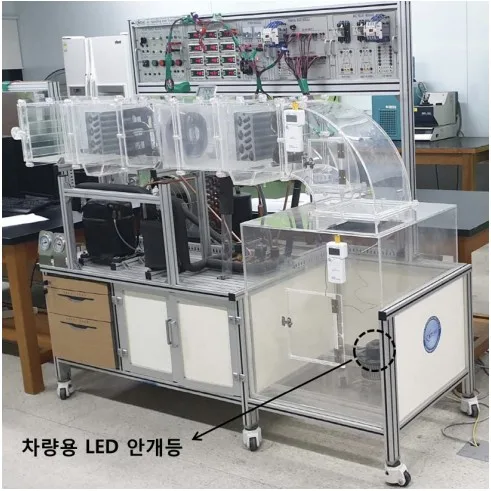
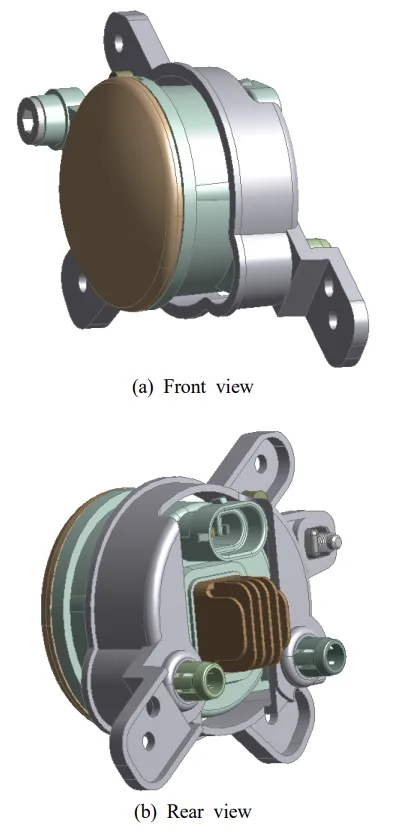
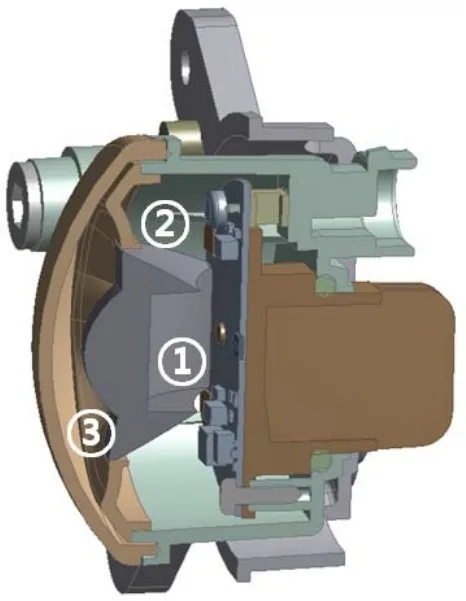
- Data Interpretation:
- The superior cooling performance of the Case3 model (vents installed above and below) can be interpreted as follows:
- Vents installed above and below the fog lamp effectively induce natural convection phenomena generated by temperature differences inside the fog lamp.
- A convective flow is formed where cool external air enters through the lower vent and hot internal air is discharged through the upper vent.
- This convective flow increases the airflow velocity inside the fog lamp and efficiently dissipates heat generated by the LED to the outside.
- On the other hand, Case1 and Case2 models are considered to have lower cooling performance compared to Case3 because the vent locations are unfavorable for convective flow formation.
- In particular, the high turbulence intensity of the Case3 model is analyzed to have further activated convective heat transfer, contributing to improved cooling performance.
- The superior cooling performance of the Case3 model (vents installed above and below) can be interpreted as follows:
6. Conclusion and Discussion:
- Summary of Main Results:
- In this study, thermal flow analysis was performed for vehicle LED fog lamps with varying vent locations to improve heat dissipation performance and to design the optimal vent location.
- Numerical analysis results confirmed that the Case3 model (vents installed above and below) exhibited the best cooling performance compared to the existing prototype (Case1).
- The Case3 model showed high airflow velocity, low internal temperature, and high turbulence intensity, which is considered to be due to the effective induction of natural convection by the upper and lower vents, efficiently dissipating heat.
- The validity of the numerical analysis was verified by comparing experimental measurements and numerical analysis results.
- Academic Significance of the Research:
- This study empirically demonstrated the importance of vent location design for improving the cooling performance of vehicle LED fog lamps through CFD analysis.
- In particular, it revealed that installing vents above and below the fog lamp can maximize cooling performance by effectively inducing natural convection.
- The results of this study are expected to contribute academically to the field of thermal management design for LED lighting systems.
- Practical Implications:
- The results of this study provide practical guidelines for vent location selection in the design of vehicle LED fog lamps.
- By implementing vents above and below the fog lamp, it is possible to improve the cooling performance of LED fog lamps, contributing to extending product lifespan and improving reliability.
- This is expected to contribute to the development and dissemination of high-performance LED fog lamps in the automotive industry.
- Limitations of the Research:
- This study's results are specific to a particular LED fog lamp model and vent shape, and there may be limitations in generalizing to various LED fog lamp designs and vent shapes.
- The analysis conditions assumed a vehicle stationary state (air velocity 0m/s), and changes in cooling performance under actual vehicle driving conditions were not considered.
- Only the k-ε model was used as the turbulence model, and changes in results due to the application of other turbulence models were not analyzed.
7. Future Follow-up Research:
- Directions for Follow-up Research:
- Research on LED fog lamp cooling performance according to variations in various vent shapes (size, shape, number, etc.)
- Research on LED fog lamp thermal management performance considering changes in vehicle driving speed and external wind conditions
- Application of various turbulence models (e.g., k-ω, SST k-ω, etc.) and comparative analysis of results
- Research on combined cooling systems of convective cooling methods with other cooling technologies such as heat pipes and liquid cooling
- Research on cooling performance changes according to changes in LED fog lamp material (application of materials with high thermal conductivity)
- Areas Requiring Further Exploration:
- Performance evaluation and durability testing of optimally designed LED fog lamps after actual vehicle mounting
- Research on changes in luminous efficiency and power consumption of LED fog lamps
- Research on changes in optical performance (light distribution characteristics, luminous intensity, etc.) of LED fog lamps
- Performance evaluation of LED fog lamps under various environmental conditions (high temperature, low temperature, humidity, etc.)
8. References:
- Kim, C. S. et al., 2008, Lifetime Estimation of an Automotive Halogen Lamp, Journal of Mechanical Science and Technology, Autumn Scientific Congress, pp. 1259-1264
- Shin, J. H., et al., 2011, A Study on design direction of automotive lamp through diver cases applied LED technology, Journal of Korean society of design science 24, pp. 47-57
- Kang, B. D., et al., 2009, Evaluation of fuel consumption between LED headlamp and halogen headlamp, KSAE09-A0294 pp. 1709-1714
- Jung, E. D., et al., Development of a heat dissipating LED headlamp with silicone lens to replace halogen bulbs in used cars, Applied Thermal engineering, volume 86, pp. 143-150
- Lee, J. W., et al., 2014, A Study to Compared on Maintenance and Electricity Energy Saving, to be Replaced by Halogen Lighting Fixtures and LED Lighting Fixture, in Workship Concert, Journal of Communications and Networks, pp. 63-64
- Sim, W. S., et al., 2016, Study on the development of lens-attached LED fog lamps for replacing halogen fog lamps, The Conference of Korean Society of Mechanical Engineers, pp. 280-282
- Chang, Y. K., et al., 2010, A Study of Thermal Factor of Automotive Lamps using CFD, The Conference of Korean Society of Automotive Engineers, pp. 877-883
- Jang, J. Y., et al., 2016, Thermal Analysis for the Development of the Railway Vehicle LED Headlamp Heat Sink, The Conference of Korean Society For Railway, pp. 944-947
9. Copyright:
- This material is 이석영 (Suk Young Lee)'s paper: Based on 차량 LED 안개등 개발을 위한 열유동 해석 (Thermal Flow Analysis for Development of LED Fog Lamp for Vehicle).
- Paper Source: https://doi.org/10.5855/ENERGY.2019.28.4.035
This material was summarized based on the above paper, and unauthorized use for commercial purposes is prohibited.
Copyright © 2025 CASTMAN. All rights reserved.