This introduction paper is based on the paper "The tool steel producer's contribution to successful die casting of structural components" published by "AIM / La Metallurgia Italiana".
![FIG. 1 Cast aluminium structural components (red) in the auto body of the AUDI A 8 [4]. Componenti strutturali di alluminio pressocolati (in rosso) nella carrozzeria della AUDI A 8 [4].](https://castman.co.kr/wp-content/uploads/image-1915-png.webp)
Componenti strutturali di alluminio pressocolati (in rosso) nella carrozzeria della AUDI A 8 [4].
1. Overview:
- Title: The tool steel producer's contribution to successful die casting of structural components
- Author: I. Schruff (Kind & Co., Edelstahlwerk, KG, Wiehl, Germany)
- Year of publication: 2012
- Journal/academic society of publication: La Metallurgia Italiana - n. 9/2012 (Paper presented at the European Conference HTDC High Tech Die Casting, Vicenza 9-11 febbraio 2012- Como, 21-23 September 2011, organized by AIM)
- Keywords: Structural components, automotive industry, hot-work tool steel, special hot-work tool steel grades, mechanical properties, heat checking resistance, thermal conductivity, heat treatment
2. Abstract:
Die cast structural components for the automotive industry gain more and more importance as they highly contribute to a weight reduction of cars and thus to a reduced fuel consumption as well as CO2-emission. So today very often die cast aluminium A-, B- or C-pillar, shock towers, or door components replace traditional steel parts. These structural components are often characterised by large dimensions and complicated design. Die casting dies for structural components have to fulfil highest requirements with respect to toughness, high-temperature strength, and thermal fatigue resistance. Often the traditionally used hot-work tool steels like 1.2343 (AISI H 11), 1.2344 (Η 13), or 1.2367 cannot fulfil these requirements. Kind & Co. has developed three special hot-work tool steels with significantly improved properties: TQ 1, HP 1, and HTR. The report will not only give a survey on the properties of these steels but also on practical experience gained with these grades. A proper heat treatment is essential for the performance of the dies. Kind & Co has recently set up one of the largest and most modern vacuum hardening furnaces in the world which focuses on these large die casting dies. The report will also show up the contribution of a modern heat treatment facility to an economic die casting process of high-class structural components.
3. Introduction:
The international automotive industry is driven by political decisions to drastically restrict CO2 emissions from passenger cars, with the European Union setting aggressive targets (e.g., 130 g CO2/km mandatory reduction target). Weight reduction is a key strategy to meet these goals, directly influencing fuel consumption and CO2 emissions. Consequently, automotive manufacturers increasingly utilize die-cast aluminium structural components, replacing traditional steel parts. Audi pioneered this approach, notably in the AUDI A8 (FIG. 1), and such components are now common in applications like door frames (FIG. 2) and hatchback support frames (FIG. 3). These components are often characterized by large dimensions and complex designs, posing significant challenges for the die casting process and the dies themselves. Dies must handle long melt flow paths, potentially requiring higher melt temperatures, leading to localized high thermal loads and thermal inhomogeneities. Complex geometries with features like ribs can create stress concentrations, increasing the risk of gross cracking. Therefore, die design, tool steel selection, die manufacturing, and heat treatment must be carefully considered, necessitating early cooperation among all involved parties.
4. Summary of the study:
Background of the research topic:
The increasing demand for lightweight automotive construction to reduce fuel consumption and CO2 emissions has led to the widespread adoption of large, complex die-cast aluminium structural components.
Status of previous research:
The dies required for producing these large structural components face extreme conditions, including high thermal loads, significant thermal stresses due to temperature inhomogeneities, and high mechanical stresses from complex geometries. Traditional hot-work tool steels, such as 1.2343 (H11), 1.2344 (H13), and 1.2367, often reach their performance limits regarding toughness, high-temperature strength, and thermal fatigue (heat checking) resistance under these demanding conditions. These steels must be produced via Electro-Slag-Remelting (ESR) for adequate quality.
Purpose of the study:
This study aims to present three special hot-work tool steels (TQ 1, HP 1, HTR) developed by Kind & Co. specifically to address the challenges of die casting large structural components. It details their improved properties compared to standard grades and discusses practical experiences. Furthermore, it highlights the critical role of advanced heat treatment processes and facilities in achieving optimal die performance, particularly for large die inserts.
Core study:
The core of the study involves the introduction and characterization of three special ESR hot-work tool steels: TQ 1, HP 1, and HTR (chemical compositions in TAB. 1). TQ 1 was designed to combine high toughness and high high-temperature strength. HP 1 serves as an economical alternative to TQ 1 with slightly modified composition. HTR is alloyed differently (reduced Cr, added W) for extreme high-temperature strength and thermal conductivity. The study compares key mechanical properties of these special steels against standard grades 1.2343, 1.2344, and 1.2367:
- Tempering resistance (FIG. 4)
- High-temperature strength (0.2% Yield Strength) (FIG. 5)
- Toughness (ISO-V-Notch impact energy) (FIG. 6)
- Heat checking resistance (laboratory simulation) (FIG. 7)
- Thermal conductivity (TAB. 3)
The study also emphasizes the necessity of appropriate heat treatment (recommended parameters in TAB. 2), discussing hardening, tempering, and the critical importance of achieving sufficient quenching rates to ensure a fully martensitic transformation and maximize toughness, referencing NADCA, Ford, and GM specifications. It introduces a new, large-scale vacuum hardening furnace (Ipsen Turbo Treater ST6672, FIG. 8) capable of handling very large die inserts (examples in FIG. 9, FIG. 10) and achieving high quenching rates (FIG. 11). The effectiveness of the heat treatment is demonstrated via microstructure analysis (FIG. 12). The importance of adequate forging technology (three-dimensional forging) for large blocks is also mentioned.
5. Research Methodology
Research Design:
The research involved the development of novel hot-work tool steel compositions (TQ 1, HP 1, HTR) tailored for demanding die casting applications. A comparative analysis methodology was employed, evaluating the properties of these new grades against established standard steels (1.2343, 1.2344, 1.2367). The study integrates material science principles with practical manufacturing considerations, including steel production (ESR, specialized melting for TQ 1/HP 1), forging techniques (three-dimensional forging), and state-of-the-art heat treatment technology.
Data Collection and Analysis Methods:
Material properties were quantified using standardized testing procedures:
- Chemical composition analysis (results in TAB. 1).
- Hardness measurements (HRC) after tempering at various temperatures to generate tempering curves (FIG. 4).
- Elevated temperature tensile testing to determine 0.2% Yield Strength (Rp0.2) as a measure of high-temperature strength (FIG. 5).
- Impact toughness testing using ISO-V-Notch samples in transverse orientation from forged bars (approx. 320 mm dia.) hardened to 45 HRC (FIG. 6).
- Laboratory simulation of thermal fatigue (heat checking) involving 4,000 cycles of heating to 600 °C followed by water quenching, with subsequent crack evaluation (FIG. 7).
- Measurement of thermal conductivity (λ) at various temperatures (100°C, 400°C, 600°C) on hardened and tempered samples (45 HRC) (TAB. 3).
- Microstructural characterization using optical microscopy on both soft annealed and vacuum heat-treated samples (FIG. 12). Grain size was assessed using Snyder-Graff Number.
- Performance validation of a new vacuum furnace by comparing its quenching pressure and cooling rate capabilities against industry standards (NADCA #207-2008, Ford AMTD-DC2010, GM DC-9999-1) (FIG. 11).
Research Topics and Scope:
The research focused specifically on hot-work tool steels intended for large dies used in the high-pressure die casting of automotive structural components. The scope encompassed:
- Development and characterization of special steel grades (TQ 1, HP 1, HTR).
- Comparative evaluation of critical performance properties: tempering resistance, high-temperature strength, toughness, heat checking resistance, and thermal conductivity.
- Investigation of the influence of steel production methods (ESR, cleanliness) and forging techniques (three-dimensional forging) on material properties.
- Emphasis on the critical role and requirements of vacuum heat treatment, including austenitization, quenching rates, tempering, and the capabilities needed for processing large-dimension die inserts (up to >5 tons).
6. Key Results:
Key Results:
- Standard hot-work tool steels (1.2343, 1.2344, 1.2367) often exhibit limitations in toughness, high-temperature strength, or thermal fatigue resistance when used for large, complex structural component dies.
- Kind & Co. developed three special ESR hot-work tool steels with optimized properties:
- TQ 1: Offers an outstanding combination of high toughness (exceeding 1.2343 by approx. 25%, FIG. 6) and high tempering resistance/high-temperature strength, comparable to 1.2367 (FIG. 4, FIG. 5). Exhibits improved heat checking resistance over standard grades (FIG. 7). Requires super-clean melting process.
- HP 1: Provides similar high toughness and heat checking resistance benefits as TQ 1 (FIG. 6, FIG. 7) but with slightly lower tempering resistance and high-temperature strength, serving as a more economical alternative. Also requires super-clean melting process.
- HTR: Features a different alloy concept (W-alloyed, lower Cr) resulting in the highest high-temperature strength, tempering resistance, and thermal conductivity among the discussed grades (FIG. 4, FIG. 5, TAB. 3). Offers the best heat checking resistance (FIG. 7) but has lower toughness compared to TQ 1 and HP 1 (FIG. 6). Recommended for specific inserts exposed to extreme thermal loads, typically hardened to max. 43 HRC.
- Electro-Slag-Remelting (ESR) is mandatory for the required homogeneity, cleanliness, and toughness. TQ 1 and HP 1 utilize special metallurgical processes for ultra-low detrimental trace elements.
- Three-dimensional forging is recommended for large die blocks to ensure homogeneous plastic deformation and enhance mechanical properties, especially toughness.
- Proper vacuum heat treatment is crucial. Achieving high cooling rates during quenching (exceeding NADCA, Ford, GM minimums, e.g., >28-30 °C/min) is essential to suppress detrimental carbide precipitation and obtain a fine martensitic microstructure for optimal toughness (FIG. 12).
- Large, powerful vacuum hardening furnaces (e.g., Ipsen Turbo Treater ST6672, FIG. 8) with high quenching pressure (e.g., 15 bar N2) and capacity (e.g., 5,500 kg load, large chamber) are necessary to successfully harden large die inserts (FIG. 9, FIG. 10) and achieve the required cooling rates throughout the component (FIG. 11).
- For large dies, reducing the target hardness (e.g., to 40-42 HRC instead of 44-46 HRC) can be beneficial for die life by increasing toughness.
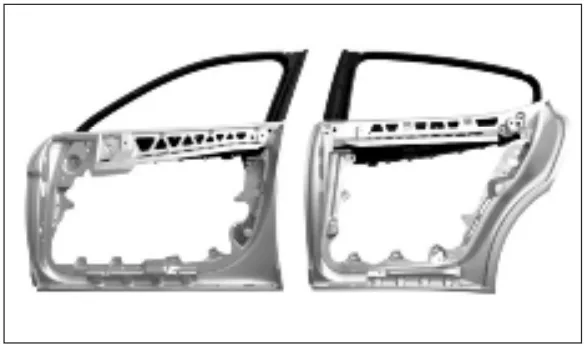
Telai di portiere e finestrini di un’automobile sportiva tedesca (Photo: Georg Fischer AG).
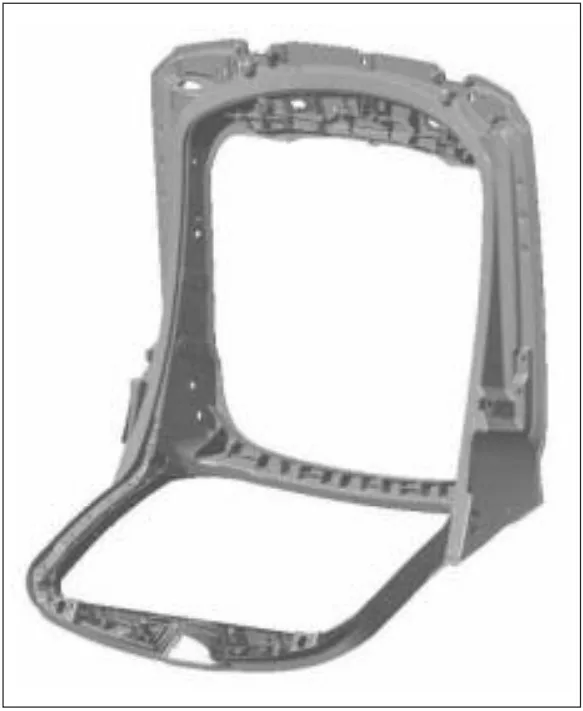
Telaio di supporto di un portellone posteriore pressocolato.
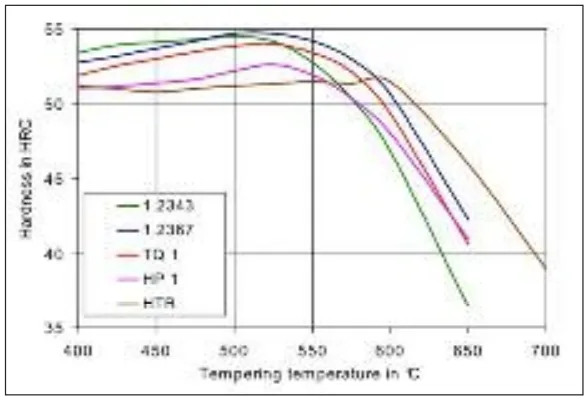
Diagramma di rinvenimento di acciai standard e acciai speciali da utensili per lavorazione a caldo per stampi da pressocolata.
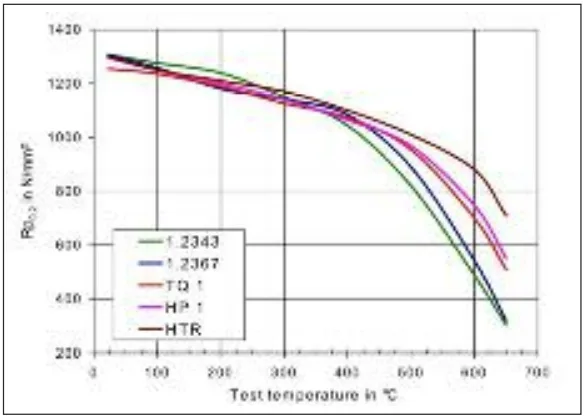
Resistenza meccanica alle temperature elevate di acciai standard e acciai speciali da utensili per lavorazione a caldo per stampi di pressocolata.
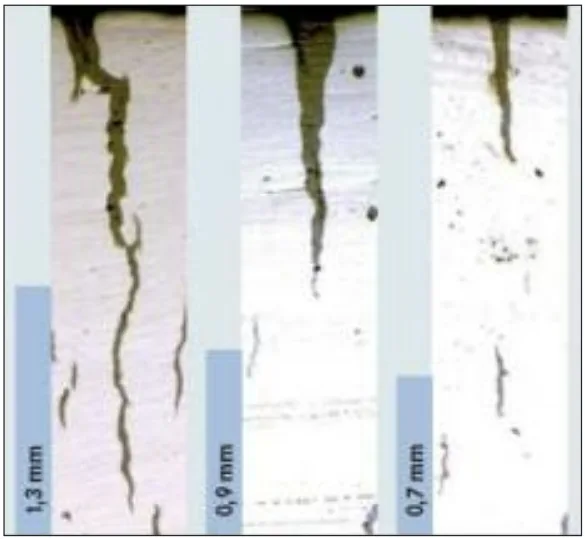
Aspetto delle cricche superficiali da fatica termica dopo 4.000 cicli a 600 °C / acqua - a): acciaio 1.2343; b): steel HP 1; c): acciaio HTR.
Figure Name List:
- FIG. 1 Cast aluminium structural components (red) in the auto body of the AUDI A 8 [4].
- FIG. 2 Door and window frames for a German sports car (Photo: Georg Fischer AG).
- FIG. 3 Die cast hatchback support frame (Photo: BMW AG).
- FIG. 4 Tempering curves of standard and special hot-work tool steels for die casting dies.
- FIG. 5 High-temperature strength of standard and special hot-work tool steels for die casting dies.
- FIG. 6 Toughness of hot-work tool steels for die casting dies (ISO-V-Notch samples, transverse, centre of forged bars, approx. 320 mm dia., 45 HRC).
- FIG. 7 Appearance of heat-checking cracks after 4.000 cycles 600 °C / water - a): steel 1.2343; b): steel HP 1; c): steel HTR.
- FIG. 8 New vacuum hardening furnace Ipsen Turbo Treater ST6672 at Kind & Co.
- FIG. 9 Die insert for a passenger car door, 3.820 kg.
- FIG. 10 Die insert for a hatchback support frame, 1.350 mm x 1.720 mm x 440 mm, 5.440 kg.
- FIG. 11 Properties of the furnace compared to requirements.
- FIG. 12 Microstructure of a die casting die insert made of USN ESR (1.2343 ESR), 3820 kg. a: soft annealed microstructure; b: microstructure after vacuum heat treatment in the new hardening furnace.
- TAB. 1 Chemical compositions of hot-work tool steels for die casting dies.
- TAB. 2 Recommended hardening parameters for hot-work tool steels for die casting dies.
- TAB. 3 Thermal conductivity λ in W / (m * K) of hot-work tool steels.
7. Conclusion:
The use of die-cast aluminium structural components is a significant contributor to automotive weight reduction, reduced fuel consumption, and lower CO2 emissions. However, these components often necessitate large, complex die inserts that operate near the limits of availability and producibility. The specific shapes frequently lead to inhomogeneous temperature distributions and high thermal stresses, challenging the applicability of standard hot-work tool steels like 1.2343 and 1.2344. Specially developed ESR hot-work tool steels such as TQ 1, HP 1, and HTR offer optimized properties, including improved high-temperature strength, tempering resistance, toughness, and heat-checking resistance. HTR, with its drastically improved high-temperature properties and thermal conductivity but lower toughness, is best suited for partial inserts under extreme thermal load, typically used below 43 HRC. The successful application of these steels, especially in large dimensions, hinges critically on advanced heat treatment. The new vacuum hardening furnace (IPSEN Super Turbo ST6672) provides the necessary capacity and high quenching capability to harden very large die inserts (over 5 tons), suppressing undesirable carbide precipitations and achieving a fine martensitic microstructure. This ensures excellent toughness values even in massive dies. The combination of modern, tailored hot-work tool steels and state-of-the-art heat treatment facilities provides the optimal foundation for the successful and economic die casting of complex, high-class structural components.
8. References:
- [1] Decision No 1753/2000/EC of the European Parliament and of the Council of 22 June 2000 establishing a scheme to monitor the average specific emissions of CO2 from new passenger cars. www.europa.eu
- [2] Communication from the Commission to the Council of the European Parliament - A community strategy to reduce CO2 emissions from passenger cars and improve fuel economy. www.europa.eu
- [3] Communication from the Commission to the Council and the European Parliament - 6 Results of the review of the Community Strategy to reduce CO2 emissions from passenger cars and light commercial vehicles. www.europa.eu
- [4] G. BRANNER and P. WANKE: The Role of High Pressure Die Casting in the AUDI Lightweight Strategy, Proc. International Forum on Structural Components by HPDC, Vicenza, September 2011, AIM
- [5] NADCA DIE MATERIALS COMMITTEE: Special Quality Die Steel & Heat Treatment Acceptance Criteria for Die Casting Dies. NADCA #207-2008, North American Die Casting Association (2008)
- [6] FORD MOTOR COMPANY: Die Insert Material and Heat Treatment Performance Requirements, General Applications. Specification No. AMTD-DC2010, Rev. L (1999)
- [7] GM POWERTRAIN GROUP: Standard Specification. Die Insert Material and Heat Treating Specification. Specification No. DC-9999-1, Rev. 18 (2005)
- [8] H. BERNS, E. HABERLING, and F. WENDL: Influence of the Annealed Microstructure on the Toughness of Hot-work Tool Steels. Thyssen Edelst. Techn. Ber., Special Issue 1990, pp. 45 – 52
- [9] H. BERNS: Die Bedeutung der t10/7-Zeit für die Wärmebehandlung hochlegierter Stähle. HTM J. Heat Treatm. Mat. 65 (2010) 4, pp. 182 – 188
9. Copyright:
- This material is a paper by "I. Schruff". Based on "The tool steel producer's contribution to successful die casting of structural components".
- Source of the paper: La Metallurgia Italiana - n. 9/2012, pp. 37-43
This material is summarized based on the above paper, and unauthorized use for commercial purposes is prohibited.
Copyright © 2025 CASTMAN. All rights reserved.