This introduction paper is based on the paper "System for Computer Aided Cavity Layout Design for Diecasting Dies" published by "Proceedings of NAMRI/SME".
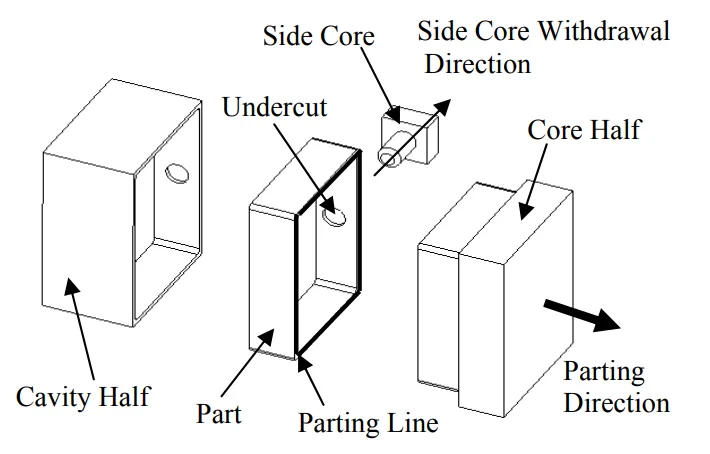
1. Overview:
- Title: System for Computer Aided Cavity Layout Design for Diecasting Dies
- Author: V. Kumar, J. Madan
- Year of publication: 2011
- Journal/academic society of publication: Proceedings of NAMRI/SME, Vol. 39
- Keywords: Diecasting, Die Design, Multi Cavity Dies, Layout Patterns, Layout Design
2. Abstract:
Diecasting is one of the forming methods which is used for producing large number of components with good surface finish by injecting cast alloys in a metal mould under high pressure. Design of a diecasting die requires human expertise and is normally performed by trial and error method, which leads to monetary and time loss. Automation at initial die design stage will result in higher productivity besides reducing production lead time. Decision about number of cavities, layout pattern and placement of cavities in diecasting is critical for die design and manufacturing. This paper presents research work related to system for computer aided cavity layout design for diecasting dies. Proposed system consists of three modules namely determination of number of cavities, selection of layout pattern and placement of cavities in the die-base. It enables die designers to generate cavity layout design automatically from CAD (Computer Aided Design) file of the part with little information provided manually. Optimal number of cavities is determined by considering economic, technical, geometrical and time limitations followed by selection of layout pattern. Thereafter, cavities are placed in the die-base. The developed system depends upon database of diecasting machines and materials along with a knowledgebase of die design. This system has been tried on a number of diecasting parts and results have been found to be on the lines of those obtained from industry. Proposed system is more comprehensive than those available presently and is a step forward in the direction of design-manufacturing integration for diecasting.
3. Introduction:
Die casting is a versatile process for producing metal parts by forcing molten metal under high pressure into reusable steel molds, called dies. These dies can produce complex shapes with high accuracy and repeatability. The quality of diecast parts is essentially determined by the die, which consists of two mould halves: the stationary cavity half (or cover die) and the movable core half (or ejector die).
Diecasting die design is a complex, time-consuming process requiring significant technical know-how and experience. Key tasks include determining the number of cavities and their layout, gating system design, die-base design, parting design, setting shrinkage, core & cavity creation, ejection design, cooling design, side core design, and standard component design. These tasks can be divided into initial (conceptual) die design and detail die design. At the conceptual stage, selecting the mould configuration, determining the number of cavities, and its layout are major tasks influencing subsequent design stages. While single cavity dies are for large components, multi-cavity dies are more economical for producing multiple components per cycle, reducing cost and increasing productivity. For designing a cavity layout, the designer must first determine the number of cavities, considering factors like time, cost, manufacturing, and geometric limitations. These decisions are crucial for downstream activities in die design and manufacturing.
4. Summary of the study:
Background of the research topic:
Diecasting die design is a critical process that traditionally relies on human expertise and trial-and-error methods, leading to increased costs and production time. Automation, particularly at the initial die design stage, is essential for improving productivity and reducing lead times. Key decisions at this stage, such as determining the number of cavities, their layout pattern, and placement within the die-base, significantly impact the overall die design and manufacturing efficiency. There is a need for an automated system to assist designers in these critical tasks.
Status of previous research:
Most prior research in die design for diecasting focused on parting line and parting surface determination, with less attention on optimizing the number of cavities and their layout. Existing systems for cavity layout design, including those for injection molding (which shares similarities with diecasting), often had limitations:
- Some systems required the number of cavities as a user input [Hu and Masood 2002].
- Others used only standard cavity layouts stored in a database [Low and Lee 2003].
- Determination of the number of cavities was often based on single factors like the selected machine [Ravi et al. 1994, Fuh et al. 2002], empirical relations without considering geometric constraints [Chan et al. 2003, Wu et al. 2007], or cost factors alone [Dewhurst and Blum 1989].
- Comprehensive consideration of multiple factors (machine selected, production cost, delivery date, part geometrical constraints) for selecting the number of cavities was lacking.
- Layout pattern selection was often manual or limited to symmetric types.
- Clearances for gating systems and side-pulls were not adequately addressed in earlier systems.
- Many systems required significant user interaction and lacked a high degree of automation.
Purpose of the study:
The present work aims to bridge the identified research gaps by developing a comprehensive system for computer-aided design of cavity layout for a diecasting die. The objectives include:
- To develop a system consisting of three modules that utilizes a knowledge base of diecasting die design, along with databases for diecasting machines and cast alloys.
- To determine the optimal and feasible number of cavities by comprehensively considering technical, economical, time, and geometrical limitations.
- To automatically determine the layout pattern of the die (circular, series, symmetric) based on the number of cavities and die design knowledge.
- To arrange and place individual cavities in a suitable die base, accounting for necessary clearances for the gating system and side pulls.
- To provide a more automated solution, reducing manual input and expert dependency.
Core study:
The core of this study is the development of a knowledge-based system for computer-aided cavity layout design for multi-cavity diecasting dies. This system automates the determination of the number of cavities, the selection of an appropriate layout pattern, and the placement of these cavities within the die-base. It achieves this by integrating geometrical information extracted from a CAD file of the part with user-provided data, and by utilizing databases of diecasting machines and materials, alongside a dedicated knowledge base for die design. The system is structured into three main modules:
- Determination of number of cavities: Considers economic viability, technical permissibility (machine constraints), geometrical feasibility (part features), and time limitations (delivery date).
- Selection of layout pattern: Chooses from circular, series, or symmetric patterns based on the determined number of cavities and established die design principles.
- Placement of cavities in the die-base: Orients and positions cavities, incorporating necessary clearances for feed systems and side-pull mechanisms.
5. Research Methodology
Research Design:
The proposed system for computer-aided cavity layout design is designed with a modular approach, consisting of three main functional modules:
- Determination of Number of Cavities: This module calculates the number of cavities based on four criteria:
- Delivery Date [Ndel]: Calculated based on cycle time for die casting and trimming processes, using relationships from Menges et al. [2001] and Boothroyd et al. [1994].
- Part Manufacturing Cost [Ncost]: Optimum number of cavities determined using formulas from Dewhurst and Blum [1989] and Madan et al. [2006].
- Machine Parameters [Nmac]: The minimum of cavities determined by clamping force (Ncf), maximum flow rate (Nfr), and machine size (Nms), based on Herman [1996], Boothroyd et al. [1994], and Fuh et al. [2002].
- Part Geometric Features [Ngeo]: Maximum cavities based on industry rules related to undercuts and side-pulls.
The final number of cavities selected must be economically acceptable, technically permissible, geometrically feasible, and meet time constraints.
- Selection of Cavity Layout Pattern: Once the number of cavities is determined, this module selects a suitable layout pattern (circular, series, or symmetric) using diecasting die design knowledge. For example, single cavities are centered; for multi-cavity moulds, geometrically balanced patterns are preferred. Circular patterns are often chosen for odd numbers of cavities, while series or symmetric patterns are used for even numbers, with symmetric patterns preferred for powers of two.
- Orientation and Placement of Cavities: This module orients and positions the cavities in the die base. It considers factors like the number and position of undercuts and the gate position. Clearances for the feed system (biscuit, runner, overflow wells) and side-pulls mechanism are incorporated based on a database developed from industry practices and literature [Boothyard et al. 1994].
The system was implemented using MATLAB 7, with part geometry extracted from CAD files modeled in SolidWorks 2010.
Data Collection and Analysis Methods:
The system utilizes several data sources and analysis methods:
- CAD File Input: Geometrical information of the part (projected area, volume, envelope size, wall thickness, longest part depth) is extracted from its CAD file.
- User Input: Interactive input is required for details such as lot size, delivery date, undercut features (number and location), and material selection.
- Databases:
- Material Database: Contains properties of cast alloys (e.g., Table 1. Representative Cast Alloy Material Database [15]).
- Machine Database: Contains specifications of diecasting machines (e.g., Table 2. Representative Machine Database [15]).
- Clearance Database: Stores minimum required clearances between cavities, die base edge and cavity, for feed system, and side-pull mechanism.
- Knowledge Base: A die design knowledge base is used for decision-making, such as rules for determining Ngeo, selecting layout patterns, orienting cavities, and applying clearances.
- Analytical Calculations: Formulas and procedures from existing literature and industry practice are used to calculate Ndel, Ncost, Ncf, Nfr, and Nms.
- Information Flow: The system processes information as depicted in flow diagrams (Figure 2 and Figure 5), integrating data from various sources to arrive at the final cavity layout design.
Research Topics and Scope:
The research focuses on the computer-aided design of cavity layouts for multi-cavity diecasting dies. Key research topics addressed include:
- Automated determination of the optimal and feasible number of cavities by considering a comprehensive set of factors: economic (cost), technical (machine capacity), geometrical (part features like undercuts), and time (delivery requirements).
- Automated selection of cavity layout patterns (circular, series, symmetric) based on the number of cavities and die design knowledge.
- Automated orientation and placement of cavities within the die-base, including the provision of necessary clearances for feed systems and side-pull mechanisms.
The scope of the system is to provide an automated tool for the initial stages of die design, specifically for cavity layout. It aims to reduce reliance on manual expertise and trial-and-error, thereby improving efficiency. The system currently assumes that the parting direction is known.
6. Key Results:
Key Results:
The research resulted in a developed system for computer-aided cavity layout design for diecasting dies.
- The system is capable of automatically calculating the number of cavities by considering delivery date, production cost, machine constraints, and part geometric limitations.
- It selects an appropriate layout pattern (circular, series, or symmetric) based on the determined number of cavities and die design knowledge.
- The system positions the cavities in the die and displays the layout graphically, determining the die base size along with possible alternatives, selecting the one with the minimum size.
- The system was successfully tested on a number of diecasting parts, including those with undercut features.
- For an example part with an undercut feature (Figure 6), the system determined four cavities, selected a symmetric layout pattern, and calculated a die base size of 465 mm x 585 mm (Figure 8).
- For an example part without an undercut feature (Figure 7), the system determined five cavities, selected a circular layout pattern, and calculated a die base size of 760 mm x 760 mm (Figure 9).
- The proposed system is reported to be user-friendly and utilizes databases for machines and materials, along with a die design knowledgebase.
- The system is more comprehensive than previously available systems and represents a step towards design-manufacturing integration for diecasting.
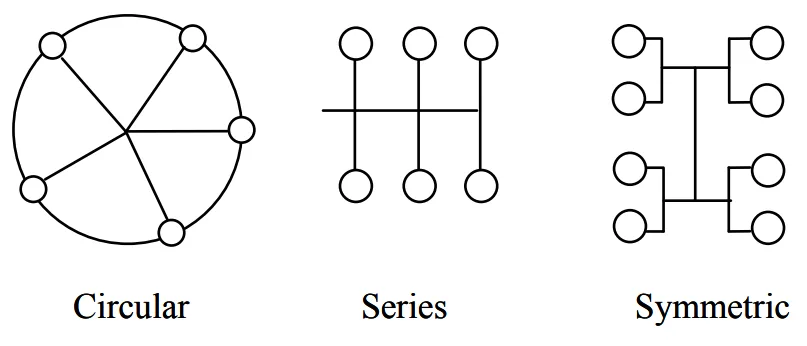
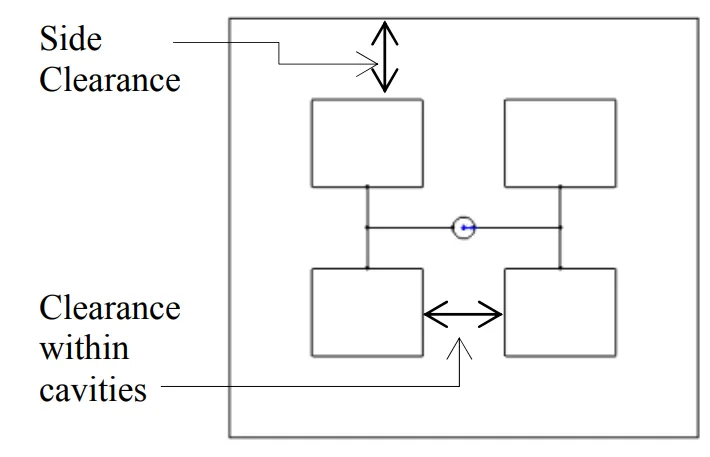
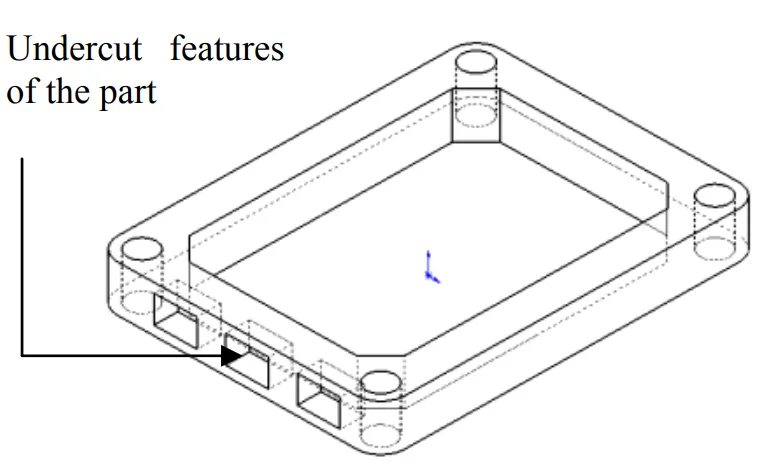
Figure Name List:
- Figure 1. Diecasting Process Terminology.
- Figure 2. Information Flow Diagram for Determination of Number of Cavities for Multi-cavity Die.
- Figure 3. Cavity layout patterns.
- Figure 4. Arrangement of clearances in die-base
- Figure 5. Information Flow Diagram for Automatic Cavity Layout Design of Multi-cavity Die.
- Figure 6. Example Part 1 with Undercut Feature.
- Figure 7. Example Part 2 without Undercut Feature.
- Figure 8. Cavity Layout Design for Example Part 1.
- Figure 9. Cavity Layout Design for Example Part 2.
7. Conclusion:
The paper presents a system for computer-aided cavity layout design for diecasting that has been developed. This system is a significant step towards design-manufacturing integration for the diecasting process. The selection of cavity layout at the die design stage is identified as a major problem faced by diecasting industries. The developed system is considered very useful for diecasting industries as it would help in reducing lot of human expertise and effort for selection of cavity layout.
The proposed system is capable of calculating the number of cavities by considering delivery date, production cost, machine constraints, and part geometric limitations. It uses standardized layout patterns for better geometrical balance. Finally, orientation and placement of cavities are determined keeping in view the clearances and geometric aspects such as number and location of undercuts. The system displays a graphical arrangement of cavities as output. It is user-friendly and makes use of machine, material databases, and a die design knowledgebase. It assumes the parting direction is already known to the user.
Future work could include the identification of undercut features and their location in an automated manner, use of non-standard cavity layout patterns, placement of feeding system analysis, and integration with other aspects of die design.
8. References:
- Blum C (1989) Early cost estimation of die cast components. MS Thesis, University of Rhode, Island.
- Boothroyd G, Dewhurst P, Knight W (1994) Product design for manufacture and assembly. Marcel Dekker, New York.
- Chan WM, Yan L, Xiang W, Cheok BT (2003) A 3D CAD knowledge-based assisted injection mould design system. International Journal of Advance Manufacturing Technology 22, 387–395.
- Dewhurst P, Blum C (1989) Supporting analysis for the economic assessment of diecasting in product design. Annual CIRP 38, 161–164.
- Fuh JYH, Wu SH, Lee KS (2002) Development of a semi-automated die casting die design System. Proceedings of the Institution of Mechanical Engineers, Part B: Journal of Engineering Manufacture 216 (12), 1575-1588.
- Fuh JYH, Zhang YF, Nee AYC, Fu MW (2004) Computer-aided injection mold design and manufacture, Marcel Dekker Inc., New York.
- Herman EA (1996) Designing die casting die. North American Die Casting Association (NADCA).
- Herman EA (1996) Gating system design. North American Die Casting Association (NADCA).
- Hu W, Masood S (2002) An intelligent cavity layout design system for injection moulds. International Journal of CAD/CAM, 2(1), 69-75.
- Low MLH, Lee KS (2003) A parametric-controlled cavity layout design system for a plastic injection mould. International Journal of Advance Manufacturing Technology 21, 807–819.
- Low MLH, Lee KS (2003) Application of standardization for initial design of plastic injection moulds. International Journal of Production Research, 41, 2301–2324.
- Madan J, Rao PVM, Kundra TK (2006) System for early cost estimation of die-cast parts. International Journal of Production Research, 45(20), 4823-4847.
- Menges G, Michaeli W, Mohren P (2001) How to Make Injection Molds. 3rd edition, Hanser Gardner Publications, Cincinnati.
- NADCA, North American Die Casting Association, (http://www.diecasting.org/faq) accessed on 2010-10-10.
- Ravi B, Pande SS, Reddy AP (1994) Computer aided design of die casting dies. IIF Transactions, 94(19), 239-245.
- Reinbacker WR (1980) A computer approach to mold quotations, PACTEC V, 5th Pacific Tech. Conference, Los Angeles.
- Woon YK, Lee KS (2004) Development of a die design system for die casting. International Journal of Advance Manufacturing Technology 23, 399-411.
- Wu SH, Fuh JYH, Lee KS (2007) Semi-automated parametric design of gating systems for diecasting die. Computers and Industrial Engineering, 53 (2), 222-232.
- Ye XG, Lee KS, Fuh JYH, Zhang YF, Nee AYC (2000) Automatic initial design of injection mould. International Journal Material Production Technology, 15, 503-517.
9. Copyright:
- This material is a paper by "V. Kumar, J. Madan". Based on "System for Computer Aided Cavity Layout Design for Diecasting Dies".
- Source of the paper: DOI not provided in the paper. (Published in: Proceedings of NAMRI/SME, Vol. 39, 2011)
This material is summarized based on the above paper, and unauthorized use for commercial purposes is prohibited.
Copyright © 2025 CASTMAN. All rights reserved.