This introduction paper is based on the paper "SURFACE MODIFICATIONS OF MARAGING STEELS USED IN THE MANUFACTURE OF MOULDS AND DIES" published by "Materiali in tehnologije / Materials and technology".
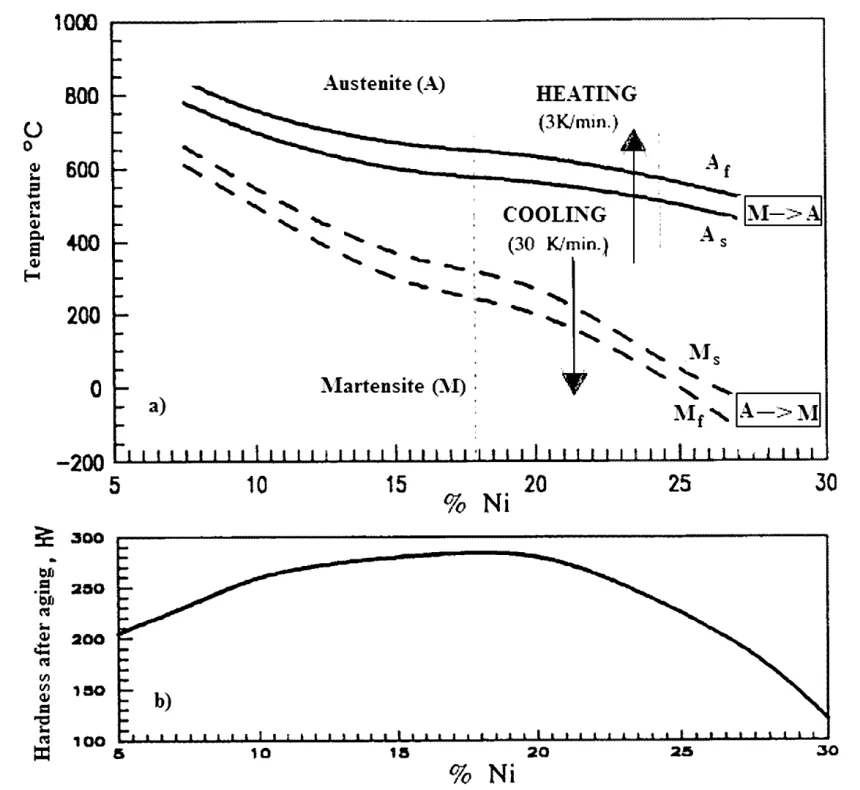
1. Overview:
- Title: SURFACE MODIFICATIONS OF MARAGING STEELS USED IN THE MANUFACTURE OF MOULDS AND DIES
- Author: Franjo Cajner¹, Darko Landek¹, Vojteh Leskovšek²
- Year of publication: 2010
- Journal/academic society of publication: Materiali in tehnologije / Materials and technology
- Keywords: MARAGING steels, thermo-chemical treatment, PVD coating, wear resistance
2. Abstract:
Low-carbon, high-alloy, precipitation hardening MARAGING steels have been developed in the early sixties of the last century as a high strength structural materials for application in aeronautical and missile engineering. Due to their excellent properties, such as: high hardenability, good toughness, and high resistance to thermal fatigue, and due to simple heat treatment (without protective atmosphere) with very small distortions, MARAGING steels are successfully used for the fabrication of moulds and dies. The main drawback of these steels is their relatively low wear resistance, particularly if the die is subjected to extensive wear during service. The paper presents an overview of existing MARAGING steels used in mould manufacturing and gives their general properties. Also, the results of the applied modification and coating processes are presented with a special focus on the increase in wear resistance.
3. Introduction:
Low-carbon, high alloy MARAGING steels, belonging to the Fe-Ni-Co alloying system with Mo, Ti, and Al as alloying elements, were developed in the early sixties for high-strength structural applications in aeronautical and aerospace engineering. Modifications with Cr created Fe-Ni-Cr or Fe-Ni-Co-Cr systems suitable for highly corrosive environments. Later, MARAGING steels found use in tool manufacturing due to superior properties:
- High toughness and fracture toughness combined with very high strength.
- High resistance to thermal fatigue.
- Simple heat treatment (solution annealing and precipitation hardening/aging) without protective atmosphere, as there is no risk of decarburization or surface oxidation.
- Excellent hardenability, achieved by slow cooling from solution annealing, significantly reducing distortion and cracking risks.
- Good weldability.
- Good electro-erosion machinability.
- Good chip machinability and/or cold deformability after quenching, allowing tool manufacturing to final dimensions before aging.
- Minimal dimensional changes during heat treatment (approx. 0.1% shortening in solution annealing and cooling, practically no deformation in aging).
The primary disadvantage of MARAGING steels compared to high alloy tool steels is their relatively low hardness (HRC = 50–57 at most), leading to insufficient wear resistance. This makes them unsuitable for cutting tools but suitable for moulds and dies. The relatively high price is comparable to tool steels produced by powder metal forming. This paper reviews MARAGING steels and presents research on improving their wear resistance through surface modifications.
4. Summary of the study:
Background of the research topic:
MARAGING steels possess excellent properties for manufacturing moulds and dies, including high toughness, simple heat treatment with minimal distortion, and good weldability. However, their primary limitation is a relatively low wear resistance, particularly when dies are subjected to extensive wear during service. This necessitates surface modifications to enhance their performance and lifespan in such applications.
Status of previous research:
Previous literature (references 3-5) commonly recommends nitriding and/or nitrocarburising to improve the wear resistance of MARAGING steels. Further investigations (references 6-10) have explored the application of other thermo-chemical treatments such as carburizing and boriding, as well as physical vapour deposition (PVD) coating processes. This paper synthesizes findings from existing literature and presents results from the authors' research on enhancing the wear resistance of MARAGING steels.
Purpose of the study:
The study aims to provide a comprehensive overview of MARAGING steels used in mould and die manufacturing, detailing their general properties. A primary focus is on presenting the results of various applied surface modification and coating processes specifically designed to increase the wear resistance of these steels, addressing their main drawback.
Core study:
The core of the study involves an experimental investigation into the effects of different surface treatments on MARAGING steel 14 10 5 (chemical composition detailed in Table 2). The treatments examined include carburizing, boriding, nitriding (in Tenifer salt bath and plasma), and a duplex treatment consisting of plasma nitriding followed by a PVD TiN coating. The efficacy of these treatments was evaluated through microstructural analysis, hardness distribution profiles, and comprehensive tribological tests assessing abrasive, erosive, and adhesive wear resistance.
5. Research Methodology
Research Design:
The study employed a twofold approach:
- A review of existing literature to establish the general properties, heat treatment characteristics (as illustrated in Figure 1 and Figure 2), and classification of MARAGING tool steels (Table 1).
- An experimental investigation focused on various surface modification techniques applied to MARAGING steel 14 10 5 to enhance its wear resistance.
Data Collection and Analysis Methods:
- Material: MARAGING steel 14 10 5, with its chemical composition provided in Table 2.
- Surface Treatments: Test samples underwent a series of heat treatment and surface modification processes, with parameters listed in Table 3. These included:
- Aging (500 °C/4h)
- Nitrocarburizing by the TENIFER procedure (580 °C/4h)
- Ion-nitriding (500 °C/72h and 500 °C/20h)
- Duplex treatment: Ion-nitriding (500 °C/20h) + PVD coating (TiN at 450 °C/70 min)
- Carburizing in Degussa KG 6 granulate (900 °C/4h) + aging (500 °C/4h)
- Boriding in EKABOR 2 (Degussa) powder (900 °C/4h) + aging (500 °C/4h)
- Evaluation Techniques:
- Microstructure Examination: To observe the characteristics of the treated surfaces.
- Hardness Distribution: Measured on the cross-section of test samples to determine hardness profiles from the surface inwards (results presented in Figure 3, Figure 5, Figure 7, Figure 8).
- Tribological Tests:
- Abrasive wear: Dry sand/rubber wheel tests (Ottawa 50/70 quartz sand) at a compressive force of 45 N (Figure 4).
- Erosive wear: Tests using sand grains colliding with the test sample surface at an angle of incidence of 90° (Figure 6).
- Adhesive wear: Tests using a friction ring made of hardened steel at a compressive force of 100 N, with determination of friction coefficient values (Figure 9).
Research Topics and Scope:
The research covered the following key areas:
- An overview of the properties of MARAGING tool steels, including different grades suitable for various working temperatures and corrosive environments.
- Detailed investigation of surface modification techniques to improve the wear resistance of MARAGING steel 14 10 5, specifically:
- Carburization and its effects on surface hardness and wear.
- Boriding and its impact on surface properties and wear.
- Nitriding processes (plasma nitriding and salt bath nitrocarburizing) and their influence on wear and core properties.
- Duplex treatment involving plasma nitriding followed by PVD TiN coating.
- A brief discussion on the repair of worn tools made from MARAGING steels, highlighting laser remelting.
6. Key Results:
Key Results:
- Carburization: Carburizing MARAGING steel 14 10 5 at 900 °C/4h followed by aging at 500 °C/4h resulted in a carburized layer of approx. 0.8 mm. While this improved abrasive wear resistance (Figure 4), it led to a hard martensite layer (approx. HV 700, Figure 3), accompanied by distortions and more difficult chip machining, thereby negating the "distortionless" heat treatment advantage of MARAGING steels.
- Boriding: Boriding at 900 °C/4h followed by aging at 500 °C/4h produced a boride layer of approx. 50 µm with high hardness (above HV0.5 1000) (Figure 5). This layer exhibited high resistance to erosive wear and improved abrasive wear (Figure 4, Figure 6). However, issues such as a soft zone below the boride layer, transverse cracks in the boride layer, and risk of dimensional intolerance make this process problematic, as it also compromises the "distortionless" heat treatment property.
- Nitriding and Nitrocarburizing:
- Nitrocarburizing in a TENIFER salt bath (580 °C/4h) and ion-nitriding at higher temperatures or longer durations (e.g., 500 °C/72h) can lead to overaging of the core, resulting in a decrease in core hardness and the hardness of the nitrided layer (Figure 7). This can negatively impact wear resistance (Figure 6).
- Plasma nitriding at temperatures around 500 °C (within the aging temperature range) can successfully increase wear resistance (Figure 4, Figure 6) while retaining other advantages of MARAGING steels. Formation of a single-phase Fe4N nitride layer is recommended for a good combination of hardness and ductility.
- Duplex Treatment (Plasma Nitriding + PVD TiN): Ion-nitriding (500 °C/20h) followed by a PVD TiN coating (1.8 µm thick, Figure 8) on MARAGING steel 14 10 5 showed significant improvements. This combination provided high resistance to abrasive, erosive, and adhesive wear, along with an extremely low friction coefficient (Figure 4, Figure 9).
- Repair of Worn Tools: Low carbon MARAGING steels are weldable. Laser remelting (e.g., using a diode laser) is a successful procedure for repairing worn tool surfaces and thermal fatigue cracks, as demonstrated for X 2 NiCoMoTi 12 8 8 steel.
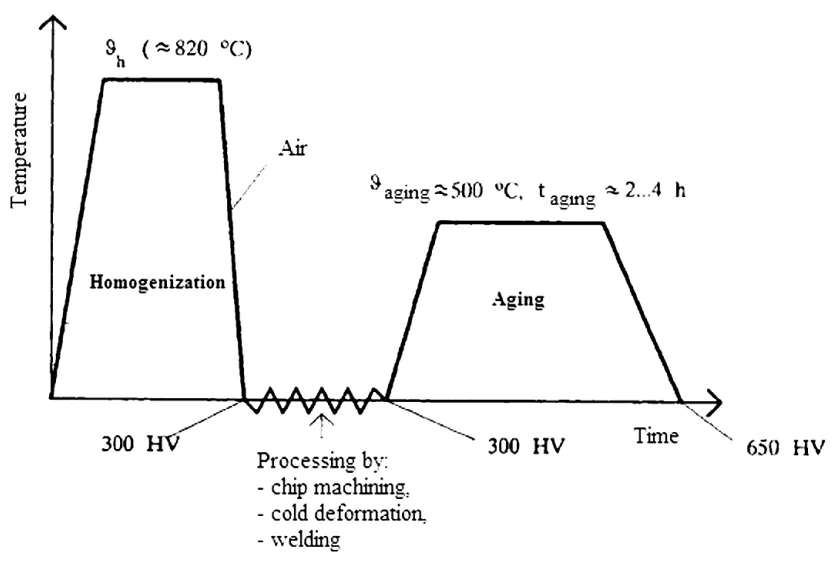
Figure Name List:
- Figure 1: a) Real phase diagram Fe-Ni ¹¹, b) Quenching hardness of Fe-Ni alloys in dependence of the percentage of nickel (with the addition of Co, Mo, Ti, and Al) ¹²
- Figure 2: A flow diagram of the heat treatment process of MARAGING steels ²
- Figure 3: Hardness distribution in the edge layer of carburized test samples made of MARAGING steel 14-10-5
- Figure 4: The abrasive wear mass loss of test samples made of MARAGING steels 14-10-5 with and without surface modifications compared with the wear of samples made of high alloy tool steel X155CrVMol2 1 ⁹﹐¹⁰
- Figure 5: The microstructure and hardness distribution in the edge layer of borided test samples made of MARAGING steel 14-10-5 ¹⁰
- Figure 6: Mass loss in erosive wear tests carried out on test samples made of MARAGING steel 14-10-5 with and without surface modifications ¹⁰
- Figure 7: Microstructure and hardness distribution in the edge layer of test samples of MARAGING steel 14-10-5, nitrided in plasma and nitrocarburized in the TENIFER salt bath ¹⁰
- Figure 8: Microstructure and hardness distribution in the edge layer of test samples made of MARAGING steel 14-10-5, nitrided in plasma and coated by a PVD TiN coating ¹⁰
- Figure 9: Friction coefficient determined in the adhesive wear testing of test samples made of MARAGING steel 14-10-5 with and without modifications of the surface ¹⁰
7. Conclusion:
MARAGING tool steels are well-suited for manufacturing moulds (for polymer processing), dies (for die-casting), drop-hammer dies, punches, matrices, and other non-cutting tools due to their good mechanical/technological properties and near-distortionless heat treatment. Besides the basic 18% Ni grades, special groups resistant to temperatures up to 600 °C and for corrosive applications exist.
The study confirms that the relatively poor wear resistance of MARAGING steels can be improved by thermo-chemical heat treatments:
- Carburizing: Improves abrasion resistance but is not recommended due to risks of dimensional/shape changes and difficult prior-to-aging machining, losing a key advantage.
- Boriding: Significantly improves abrasive and erosive wear, but issues like transverse cracks, dimensional changes, and loss of "distortionless" heat treatment make it currently unsuitable for tool manufacture.
- Nitrocarburizing (gases/salt baths): Produces good quality layers, but high process temperatures (550–600 °C) cause a significant decrease in core hardness of standard MARAGING steels.
- Plasma nitriding: This is the most suitable heat treatment. Nitriding temperature can be at or below the optimal aging temperature, allowing aging during nitriding. It improves abrasive, erosive, and adhesive wear more effectively than solution annealing/aging alone (though less than carburizing/boriding). Plasma nitriding also offers improved thermal fatigue resistance, corrosion stability, and resistance to adhesion of processed molten mixtures. It is recommended for moulds used in polymer and metal processing.
- Duplex Treatment (Plasma Nitriding + TiN): Significant improvements in erosion and adhesion resistance of MARAGING steel 14 10 5 were achieved by plasma nitriding followed by TiN coating. This combination is favorable for moulds requiring increased wear resistance.
Laser beams are expected to find future applications in surface modification, coating, and repair of MARAGING steel tool surfaces, especially with compact and portable diode lasers.
8. References:
- [1] Novosel M., Cajner F., Krumes D.: Tool Materials, Faculty of Mechanical Engineering in Slavonski Brod, Slavonski Brod, Croatia, 1996 (book published on croatian)
- [2] Cajner F., Krumes D.: MARAGING steels – new tool materials, Proceedings of symposium Modern technologies of heat treatment of steels, Zagreb, Croatia, 11. 6. 1998, 69-80
- [3] ASM Handbook, Part 4, ASM International, Metals Park, Ohio, 1994
- [4] Heberling J. M.: MARAGING steel: A dependable alloy, Heat Treating, (1993), Sept., 22-24
- [5] Decker, R. F.: MARAGING steels: Getting better with age, AMP Metal Progress (1988) 6, 45-50
- [6] Novosel M:, Cajner F.: Applicability of thermochemical treatment for MARAGING steels and use for manufacturing of the moulds for polymer processing, Proceedings of the 13th days of Polymer and Rubber Society, Zagreb, Croatia, 1995, 3-12
- [7] Cajner F., Leskovšek V.: Influence of thermochemical treatment of MARAGING steel on wear resistance, Proceeding of international conference MATRIB’99, Trogir, Croatia, 1999, 15-22
- [8] Kladarić, I., Cajner F., Krumes D.: Optimization of Parameters for Ageing of MARAGING Steel, Proceedings of the 8th Seminar of the International Federation for Heat Treatment and Surface Engi- neering, Dubrovnik-Cavtat, Croatia, 12-14. September 2001, 111-117
- [9] Cajner F.; Landek D. Kladarić I.: Improvement of wear resistance of MARAGING steel by applying thermochemical processes, Proceedings of the 1st International Conference on Material & Tribology 2002., Dublin, Ireland, 2002
- [10] Cajner F., Landek, D. Šolić S., Cajner H.: Effects of thermochemical treatments on properties of MARAGING steels, Surface Engi- neering, 22 (2006) 6, 468-471
- [11] Johs F. W., Pumphrey W. I.: Free energy and metastabile in the iron-nickel and iron-manganese systems, Journal Iron and Steel Institute, 163 (1949), 121-128
- [12] Goldštejn M. J., Gračev S. V., Veksler Y. G.: Specijalnie stali, Metalurgija, Moskva, 1985
- [13] Shetty, K., Kumar, S., Raghothama, R.: Effect of ion nitriding on the microstructure and properties of Maraging steel (250 Grade), Surface & Coatings Technology 203 (2009), 1530–1536
- [14] Yan, M.F., Wu, J. Y., Liu, R., L.: Plasticity and ab initio characteri- zations on Fe4N produced on the surface of nanocrystallized 18Ni-maraging steel plasma nitrided at lower temperature, Applied Surface Science 255 (2009), 8902-8906
- [15] Grum, J., Slabe, J. M.: Effect of laser-remelting of surface cracks on microstructure and residual stresses in 12Ni maraging steel, Applied Surface Science 252 (2006), 4486-4492
9. Copyright:
- This material is a paper by "Franjo Cajner, Darko Landek, Vojteh Leskovšek". Based on "SURFACE MODIFICATIONS OF MARAGING STEELS USED IN THE MANUFACTURE OF MOULDS AND DIES".
- Source of the paper: DOI not provided in the paper. Published in Materiali in tehnologije / Materials and technology, 44 (2010) 2, 85-91.
This material is summarized based on the above paper, and unauthorized use for commercial purposes is prohibited.
Copyright © 2025 CASTMAN. All rights reserved.