How Simplified Simulations Can Unlock Major Efficiency Gains with Less Data and Faster Results
This technical brief is based on the academic paper "Simulative Study of Aluminium Die Casting Operations Using Models with Varying Degrees of Detail" by Johannes Dettelbacher and Wolfgang Schlüter, published in SNE - Simulation Notes Europe (2020). It is summarized and analyzed for HPDC professionals by the experts at CASTMAN.
![Figure 1: Scheme of an aluminium die casting plant with its process steps [3].](https://castman.co.kr/wp-content/uploads/Figure-1-Scheme-of-an-aluminium-die-casting-plant-with-its-process-steps-3.webp)
Keywords
- Primary Keyword: Die Casting Simulation Models
- Secondary Keywords: Aluminium Die Casting, Energy Consumption Simulation, Production Optimization, Model Predictive Control (MPC), Material Flow Simulation, Process Simulation, Hybrid Automata
Executive Summary
- The Challenge: Complex simulation models offer powerful optimization potential for die casting plants but are often impractical for companies with limited data acquisition and computational resources.
- The Method: Researchers developed and compared three simulation models of an aluminium die casting plant with varying levels of detail—"simplified," "detailed," and "highly-detailed"—to assess the trade-offs between complexity, speed, and accuracy.
- The Key Breakthrough: The "detailed" model achieved a remarkable balance, reducing simulation time by a factor of 33 compared to the "highly-detailed" model while predicting specific energy consumption with an error of only 0.4%.
- The Bottom Line: Die casting facilities do not always need the most complex, data-intensive simulations. A strategically simplified "detailed" model can provide rapid, highly accurate predictions for material and energy consumption, enabling faster and more agile operational decisions.
The Challenge: Why This Research Matters for HPDC Professionals
In the competitive world of aluminium die casting, optimizing production and energy efficiency is paramount. Simulation-supported methods are increasingly vital for identifying these optimization opportunities (Ref. [1]). However, there's a significant barrier to entry: highly accurate simulations traditionally demand a high level of detail. This translates to a massive modeling effort, a need for extensive operational data, and long, costly computing times.
For many companies, especially in the non-ferrous industry, the available data is often insufficient for such complex models. This creates a gap where the very tools that could provide the most significant benefits are inaccessible. This study directly addresses this challenge by asking a critical question: Can we create simplified models that are compatible with a low amount of data acquisition but still deliver plausible, actionable results?
The Approach: Unpacking the Methodology
To investigate this, the researchers based their study on a large, real-world aluminium die casting facility. The operational flow included continuous processes like melting and discrete steps like forklift transport (Figure 1).
They designed three distinct simulation models using Matlab, Simulink, and Stateflow, representing the system with hybrid automata that capture both continuous and discrete-event dynamics (Ref. [4]):
- Highly-detailed Model: A comprehensive model representing nearly all process steps, validated with data from two real facilities. This served as the accurate reference or "ground truth."
- Detailed Model: A simplified version where individual machines (e.g., melting furnaces, die casting machines) are still considered separate material storages, allowing for machine-specific analysis. It includes an individual energy model for each furnace and a forklift control logic based on fill levels (Figure 4).
- Simplified Model: The most abstract model, where entire machine groups (e.g., all melting shafts, all die casting machines) are aggregated into single large "storages." This drastically reduces complexity but loses individual machine detail (Figure 2).
These models were then compared across different scenarios to test their performance on calculation time, data requirements, and the accuracy of key outputs like molten mass and specific energy consumption.
The Breakthrough: Key Findings & Data
The results demonstrate a clear and compelling trade-off between model complexity and performance.
Finding 1: Massive Reduction in Time and Data: As shown in Table 1, moving from the highly-detailed model to the simplified versions yields enormous efficiency gains. The "detailed" model reduced calculation time from 132 minutes to just 4 minutes (a 33x speedup), while the "simplified" model ran in only 1 minute (a 132x speedup). Similarly, the number of required operating parameters dropped from 275 to 157 for the detailed model and to just 30 for the simplified model.
Finding 2: High Accuracy in the "Detailed" Model: When simulating a standard operating week, the "detailed" model proved remarkably accurate. As seen in Table 2, its prediction for molten mass was within 0.9% of the reference model, and its calculation of specific energy consumption was incredibly close, with a deviation of only 0.4%.
Finding 3: A Trade-off in the "Simplified" Model: While the simplified model accurately predicted material consumption, it showed a significant deviation of 12.5% in specific energy consumption (Table 2). The researchers explain this is because the model combines different furnace types into a single, homogenous storage tank, losing the nuance of their individual energy profiles.
Finding 4: Capturing Operational Trends: In a scenario where machine downtimes were varied, both the simplified and detailed models correctly illustrated the trend that reducing downtimes improves energy efficiency. As shown in Figure 7, the detailed model's behavior closely mirrored the highly-detailed model, proving its predictive power for "what-if" analyses.
Practical Implications for Your HPDC Operations
The conclusions from this paper offer direct, actionable insights for manufacturing leaders looking to leverage simulation without a massive upfront investment.
For Process Engineers: The "detailed" model provides a powerful "sweet spot." It is suitable for quick use to make reliable predictions about energy and material consumption. You can run multiple "what-if" scenarios (e.g., "What happens to our energy use if we reduce downtimes by 50%?") in minutes, not hours, providing agile decision support.
For Operations Managers: For companies with a "poor data basis," this research provides a clear path forward. Instead of abandoning simulation, you can start with a "detailed" model that requires 43% fewer parameters than a full-scale version but still delivers results with high confidence, particularly for energy and material flow planning.
For Future-Focused Plants: The study highlights that these simplified, fast-running models are the foundation for advanced "smart services." The ultimate goal is to integrate them into real-time operational controls, such as intelligent forklift truck routing or even model-predictive control (MPC) of the entire plant.
Paper Details
Simulative Study of Aluminium Die Casting Operations Using Models with Varying Degrees of Detail
1. Overview:
- Title: Simulative Study of Aluminium Die Casting Operations Using Models with Varying Degrees of Detail
- Author: Johannes Dettelbacher, Wolfgang Schlüter
- Year of publication: 2020
- Journal/academic society of publication: SNE - Simulation Notes Europe, ARGESIM Publisher Vienna
- Keywords: Aluminium die casting, simulation, energy efficiency, model simplification, hybrid automata
2. Abstract:
Aluminium die casting plants offer great potential for optimisation in terms of production and energy efficiency, which can be demonstrated by simulation. However, real companies often have a poor data basis for complex simulation. Based on a complex model, simplified simulation models are designed that are compatible with a low amount of data acquisition. These are described in this paper and tested on different scenarios. One scenario is the variation of downtimes of production machines. Considerable savings in computing time can be reached with still plausible results in terms of material and energy consumption.
3. Introduction:
Simulation-supported methods are increasingly used to demonstrate operational optimisation. While these models often aim for high accuracy, this requires a high level of detail, significant modeling effort, and detailed production data, which is often lacking in the non-ferrous industry. This study explores the creation of simplified models for an aluminium die casting plant to enable simulation even with a low data acquisition rate, focusing on predictions of material and energy consumption.
4. Summary of the study:
Background of the research topic:
The study is based on a large aluminium die casting facility where processes are both continuous (melting) and discrete (forklift transport). The melting and holding processes are particularly energy-intensive, accounting for about 50% of the plant's total energy consumption, making them a key focus for optimization.
Status of previous research:
Previous work involved developing a highly detailed simulation model that was validated by data from two real facilities. This complex model serves as the reference for evaluating the new, simplified models developed in this study.
Purpose of the study:
The primary goal is to design and test simplified simulation models that are compatible with a low amount of data acquisition. The study aims to quantify the savings in computing time and data requirements and to evaluate the accuracy of these simplified models compared to a highly detailed reference model, particularly for material and energy consumption under various operating scenarios.
Core study:
The core of the work involves creating three models with varying degrees of detail: a "simplified" model that aggregates machine groups, a "detailed" model that considers individual machines as storages, and a "highly-detailed" reference model. These models are then used to simulate a working week and a scenario with varying machine downtimes to compare their outputs (molten mass, cast mass, specific energy consumption) and performance (computation time, data needs).
5. Research Methodology
Research Design:
The study employs a comparative research design. A highly-detailed, validated simulation model acts as a benchmark. Two new models, "simplified" and "detailed," are created by abstracting processes from the benchmark model. All three models are then subjected to the same simulation scenarios, and their results are compared to quantify the impact of simplification.
Data Collection and Analysis Methods:
The models are constructed and simulated using Matlab, Simulink, and Stateflow. The processes are described using hybrid automata, which can model systems with both continuous dynamics (like melting) and discrete events (like feeding a furnace). The highly-detailed model was validated using operational data from two real facilities. The analysis compares key performance indicators: simulation duration, number of required parameters, molten mass, cast mass, and specific energy consumption.
Research Topics and Scope:
The scope is an aluminium die casting plant with four melting furnaces and 31 die casting machines. The research focuses on the material flow (from melting to casting) and the energy consumption of the melting furnaces. The study investigates the trade-offs between model detail, simulation speed, and predictive accuracy.
6. Key Results:
Key Results:
The study found that model simplification leads to a considerable reduction in simulation time and required data. The "simplified" model reduced calculation time by a factor of 132, and the "detailed" model by a factor of 33 (Table 1). In terms of accuracy for a real operating week, the "detailed" model performed very well, with only a 0.4% deviation in specific energy consumption. The "simplified" model, however, showed a significant deviation of 12.5% in energy consumption, attributed to its aggregation of different furnace types into a single storage unit (Table 2). When simulating varying downtimes, both simplified models correctly showed the trend of improved energy efficiency with reduced downtimes, with the detailed model's results being very close to the highly-detailed reference (Figure 7).
Figure Name List:
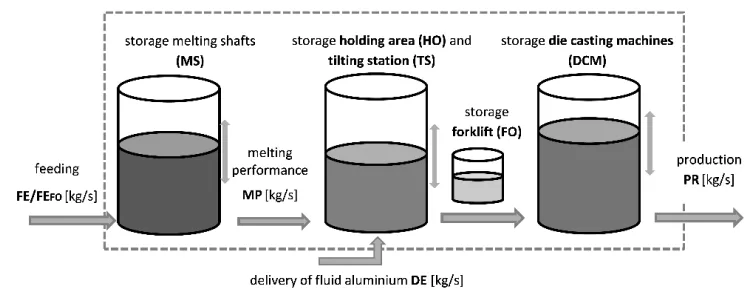
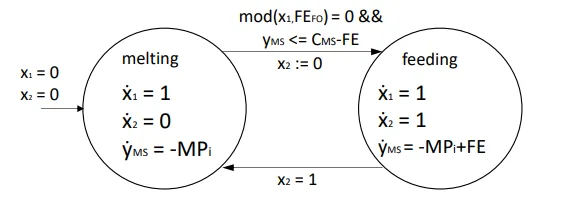
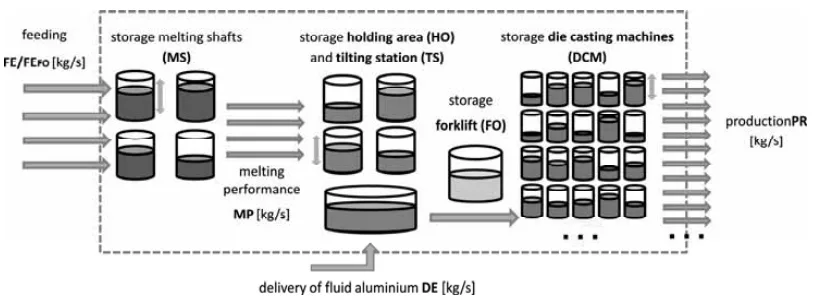
![Figure 6: Components of the highly detailed operational
simulation [5].](https://castman.co.kr/wp-content/uploads/image-2538.webp)
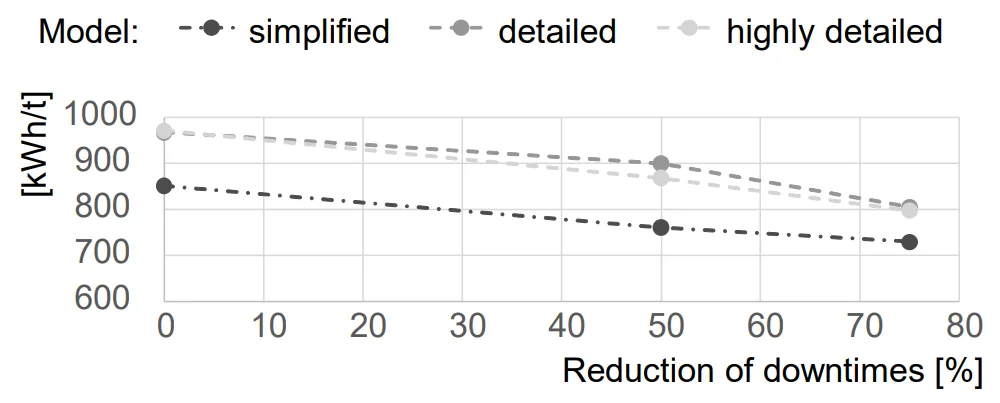
- Figure 1: Scheme of an aluminium die casting plant with its process steps [3].
- Figure 2: Scheme of the simplified model.
- Figure 3: Hybrid automat for the melting shafts in the simplified model...
- Figure 4: Scheme of the detailed model.
- Figure 5: Hybrid automat of a melting shaft in the detailed model...
- Figure 6: Components of the highly detailed operational simulation [5].
- Figure 7: Specific energy consumption in the models with a variation of downtimes at die casting machines.
7. Conclusion:
The study successfully created two simplified simulation models that enable a massive reduction in computing time and required operating data. The "detailed model" is particularly suitable for making quick and accurate predictions about energy and material consumption. While the "simplified model" shows significant deviations in energy calculations due to over-aggregation, it is still useful for material flow analysis. The final goal is to use these efficient models in smart services, such as intelligent forklift truck control and model-predictive control of the operation.
8. References:
- [1] März L, Krug W, Rose O, Weigert G. Simulation und Optimierung in Produktion und Logistik, Praxisorientierter Leitfaden mit Fallbeispielen. Berlin; Springer VDI; 2011.
- [2] Dettelbacher J. Simulative Untersuchung von Betriebserweiterungen in einem Aluminium-Schmelz- und Druckgussbetrieb anhand von Modellen mit unterschiedlichen Detaillierungsgrad. ASIM-Treffen STS/GMMS; 2019 February; Braunschweig. 53–58.
- [3] Jeckle D. Dokumentation der Software zur Simulation des Materialflusses und Untersuchung der Energieeffizienz eines Schmelz- und Druckgussbetriebes. Ansbach: Ansbach University of Applied Sciences; 2015.
- [4] Atterer R. Hybride Automaten. Munich: Technical University of Munich; 2001.
- [5] Buswell A, Schlüter W. E|Melt: Erweiterung einer unternehmensspezifischen Materialfluss- und Energiesimulation zur Abbildung variabler Betriebsstrukturen der Nichteisen-Schmelz- und Druckgussindustrie. In: Loose T, editor. Tagungsband Workshop 2018 ASIM/GI-Fachgruppen; 2018 March; Heilbronn. 33–38.
- [6] Buswell A, Schlüter W. E|Melt: A flexible material flow and energy simulation in the context of Industry 4.0. In: Deatcu C, Schramm T, Zobel K, editors. ASIM 2018 – 24. Symposium Simulationstechnik; 2018 October; Hamburg. 42–47.
Conclusion & Next Steps
This research provides a valuable roadmap for enhancing production and energy efficiency in HPDC operations. The findings offer a clear, data-driven path for facilities to adopt powerful simulation tools without being hindered by data or resource limitations. The "detailed" model, in particular, represents a pragmatic and powerful tool for process optimization.
At CASTMAN, we are dedicated to applying the latest industry research to solve our customers' most challenging die casting problems. If the issues discussed in this paper resonate with your operational goals, contact our engineering team to discuss how we can help you implement these advanced principles in your components.
Expert Q&A: Your Top Questions Answered
Q1: What did the study identify as the best approach for balancing simulation accuracy and speed?
A1: The study concluded that the "detailed model" offers the best balance. As stated in the Conclusion
, it "is particularly suitable for quick use to make predictions about energy and material consumption," achieving high accuracy with a massive reduction in computing time and data requirements compared to the highly-detailed model.
Q2: How does this research help a company that lacks detailed production data?
A2: The paper's Abstract
directly addresses this by designing models "that are compatible with a low amount of data acquisition." The "detailed model" requires 43% fewer operating parameters than the highly-detailed version (Table 1), making it a practical starting point for companies with a "poor data basis," as mentioned in the Introduction
.
Q3: Is this finding applicable to all types of casting operations?
A3: The research, as described in the Abstract
and throughout the paper, was specifically conducted on an "aluminium die casting plant." While the principles of model simplification could be applied elsewhere, the paper does not make claims about its applicability to other casting processes or materials.
Q4: What specific simulation technique did the researchers use to build these models?
A4: The researchers utilized "hybrid automata" to describe the processes, which account for both continuous and discrete event elements. As stated in the 2 Simulation Models
section, "The models are constructed and simulated with the software tools Matlab, Simulink, and Stateflow."
Q5: According to the paper, what is a key limitation of the simplified models and what is the next step?
A5: The Conclusion
states that the "simplified model shows significant deviations in the energy calculations, since a single storage does not sufficiently describe the different furnace types." The paper identifies the next step and "final goal" as the "use of the models in smart services, such as intelligent forklift truck control up to model-predictive control of the operation."
Q6: What is the direct, practical takeaway from this paper for a die casting facility?
A6: The core takeaway, based on the paper "Simulative Study of Aluminium Die Casting Operations Using Models with Varying Degrees of Detail," is that a facility can achieve rapid and reliable predictions for process optimization without a fully comprehensive, data-intensive model. The "detailed model" provides a highly effective tool for this, as strongly supported by the results in Table 2 and Figure 7.
Copyright
- This material is an analysis of the paper "Simulative Study of Aluminium Die Casting Operations Using Models with Varying Degrees of Detail" by Johannes Dettelbacher and Wolfgang Schlüter.
- Source of the paper: DOI: 10.11128/sne.30.tn.10538
- This material is for informational purposes only. Unauthorized commercial use is prohibited.
- Copyright © 2025 CASTMAN. All rights reserved.