This article introduces the paper "RESEARCH ON THE DESIGN FOR PROTECTING THE ARDUINO-MEGA MICROCONTROLLER USED AT AQUATIC EXPLORATION" presented at the ACTA TECHNICA NAPOCENSIS
1. Overview:
- Title: RESEARCH ON THE DESIGN FOR PROTECTING THE ARDUINO-MEGA MICROCONTROLLER USED AT AQUATIC EXPLORATION
- Author: Mircea Ionuţ GELER, Dan LEORDEAN
- Publication Year: February, 2024
- Publishing Journal/Academic Society: ACTA TECHNICA NAPOCENSIS, Series: Applied Mathematics, Mechanics, and Engineering, Vol. 67, Issue Special I
- Keywords: CAD, FEA, Arduino Mega, Deep-Sea, exploration, waterproof, shockproof, protective case.
![Fig. 2. MAS hardware configuration. [5]](https://castman.co.kr/wp-content/uploads/image-375-png.webp)
2. Research Background:
- Social/Academic Context of the Research Topic: Ocean exploration is increasingly important, with approximately 80% of the ocean floor and 90% of marine species remaining undiscovered. Scientists are actively seeking enhanced methods for safer and more accessible ocean exploration. The Arduino Mega microcontroller is being increasingly adopted in these endeavors due to its affordability, versatility, and capacity for large-scale applications in projects like Autonomous Underwater Vehicles (AUVs), Remotely Operated Vehicles (ROVs), and miniature autonomous submersibles.
- Limitations of Existing Research: Existing methods for protecting microcontrollers in aquatic environments present several limitations. Metallic housings, while offering some protection, may not adequately fix the microcontroller, leading to potential damage from dynamic shock. Solutions relying on the device's outer surface for waterproofing offer insufficient protection against water ingress if the primary waterproofing fails. Cylindrical chambers, while providing watertight storage, also fail to protect against dynamic shock damage from external factors. These existing protective methods exhibit flaws such as inadequate microcontroller fixation, susceptibility to shock damage, and lack of backup water protection, potentially leading to short circuits and system failure.
- Necessity of the Research: To facilitate reliable underwater projects using Arduino Mega microcontrollers, there is a critical need for improved protective casings. A robust, waterproof, and shockproof casing is essential to prevent microcontroller damage from physical shocks, water, and dust, ensuring uninterrupted operation and reducing research expenses associated with exploratory technologies. Furthermore, a user-friendly design that allows access to microcontroller features without opening the case is desirable.
3. Research Purpose and Research Questions:
- Research Purpose: The primary research purpose is to design and analyze a new protective case for the Arduino Mega microcontroller specifically for extreme deep-sea exploration. This design aims to overcome the limitations of existing protective methods by providing waterproof, shockproof, and user-friendly features.
- Key Research Questions:
- Can a protective case be designed using die casting that effectively protects the Arduino Mega microcontroller from water ingress and physical shocks at significant depths?
- What is the maximum admissible depth the designed protective case can withstand under hydrostatic pressure, considering different die casting materials?
- How effectively does the integrated heat sink design dissipate heat generated by the Arduino Mega microcontroller within the enclosed protective case?
- Research Hypotheses:
- A die-cast protective case, incorporating specific design features such as rounded corners, reinforcement ribs, and rubber seals, will provide effective waterproofing and shock protection for the Arduino Mega microcontroller.
- A protective case manufactured from Casted Ductile Iron will withstand greater hydrostatic pressure and thus a greater maximum admissible depth compared to a case made from Aluminum A380.
- An integrated heat sink, designed with consideration for die casting manufacturing rules and thermal conductivity of the case material, will effectively manage heat dissipation from the Arduino Mega microcontroller, preventing overheating.
4. Research Methodology
- Research Design: The research employs a design and simulation-based methodology. It involves the CAD design of a protective case for the Arduino Mega microcontroller, followed by Finite Element Analysis (FEA) to evaluate its structural integrity and thermal performance. The design process explicitly considers die casting manufacturing rules to ensure mass production feasibility.
- Data Collection Method: Data is generated through sequential static simulations at various depths to assess the case's structural response to hydrostatic pressure and thermal simulations to evaluate the heat sink's efficiency. Material properties for Aluminum A380 and Casted Ductile Iron, sourced from material databases, are used as input parameters for the simulations.
- Analysis Method: Static simulations using FEA are conducted to determine the maximum stress and deformation of the protective case under increasing hydrostatic pressure, thereby predicting the maximum admissible depth. Thermal simulations using FEA are performed to analyze heat transfer from the microprocessor to the heat sink and the surrounding environment, assessing the heat sink's effectiveness in maintaining the microprocessor temperature within acceptable limits.
- Research Subjects and Scope: The research focuses on the design of a protective case specifically for the Arduino Mega microcontroller. The scope is limited to the structural and thermal analysis of the designed case using FEA simulations. Two materials, Aluminum A380 and Casted Ductile Iron, are considered for comparative analysis of structural and thermal performance. The design incorporates features for waterproofing, shockproofing, microprocessor cooling via a heat sink, and external connectivity (DC power, USB, and pins).
5. Main Research Results:
- Key Research Results:
- Maximum Admissible Depth (Static Simulation): FEA static simulations revealed that a protective case made from Aluminum A380 has a maximum admissible depth of 36m (Figure 9a), based on the Yield Strength of Aluminum A380 (159MPa). Identical simulations for a case made from Casted Ductile Iron (Yield Strength - 276MPa) showed a maximum admissible depth of 63m (Figure 9b). This indicates that the Casted Ductile Iron case can withstand approximately 75% greater depths compared to the Aluminum A380 case.
- Thermal Simulation Results: Thermal simulations demonstrated that the Aluminum A380 case exhibits superior heat dissipation compared to the Die Cast Iron case. The maximum temperature reached on the Aluminum heat sink fins was 43.33°C, while for the Die Cast Iron heat sink, it was 39.15°C (Figure 11a). Further analysis of a cross-sectioned heat sink fin (Figure 11b) indicated uneven heat distribution across the fin surface. Aluminum A380 was found to dissipate heat 10.7% more efficiently than Die Cast Iron.
- Statistical/Qualitative Analysis Results: The research primarily employs quantitative FEA simulation results. Qualitative observations from the design process include the incorporation of die casting rules (constant wall thickness of 4mm, 2° draft angles, rounded corners - Figure 4) and design features for waterproofing (rubber seals - Figure 7), shockproofing (rubber gaskets in fixing mechanism - Figure 5), and user accessibility (external connectors - Figure 8).
- Data Interpretation: The static simulation results indicate that while both materials provide protection, Casted Ductile Iron offers significantly greater depth resistance due to its higher yield strength. However, the thermal simulation results suggest that Aluminum A380 is more effective in dissipating heat. This presents a trade-off between depth capability and thermal management when selecting the case material. The uneven heat distribution on the heat sink fins suggests potential for design optimization by reducing fin length to minimize material usage and cost without significantly compromising thermal performance.
- Figure Name List:
- Fig. 1. Hardware of the haptic driven system within the joystick. [4]
- Fig. 2. MAS hardware configuration. [5]
- Fig. 3. Nautilus II hardware configuration. [6]
- Fig. 4. Rounded corners and reinforcement ribs on the lower part (left) and the upper part (right).
- Fig. 5. Arduino Mega fixing method: a) lower pin and upper pin holding the board in place, b) cross section, c) arduino mega in a fixed position.
- Fig. 6. Heat sink: a) upper part's contact area pressing against the microprocessor, b) shape of the fins.
- Fig. 7. Waterproofing method: a) rubber seal positioned in the lower part's groove, b) position of the screws, c) rubber seals of the main connector (bottom right) and secondary connectors (bottom left).
- Fig. 8. Connectivity method.
- Fig. 9. Simulation results: a) Aluminum A380, b) casted ductile Iron
- Fig. 10. Maximum deformation
- Fig. 11. Thermal simulation results: a) maximum temperature, b) cross section of the result.
![Fig. 1. Hardware of the haptic driven system within the joystick. [4]](https://castman.co.kr/wp-content/uploads/image-374-png.webp)
![Fig. 2. MAS hardware configuration. [5]](https://castman.co.kr/wp-content/uploads/image-375-png.webp)
![Fig. 3. Nautilus II hardware configuration. [6]](https://castman.co.kr/wp-content/uploads/image-376-png.webp)
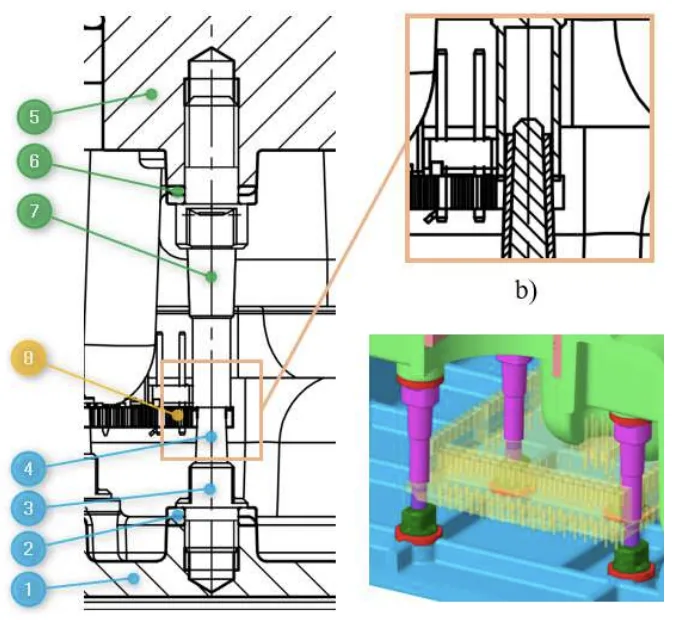
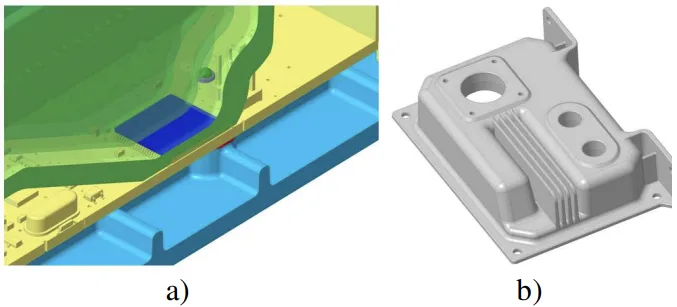
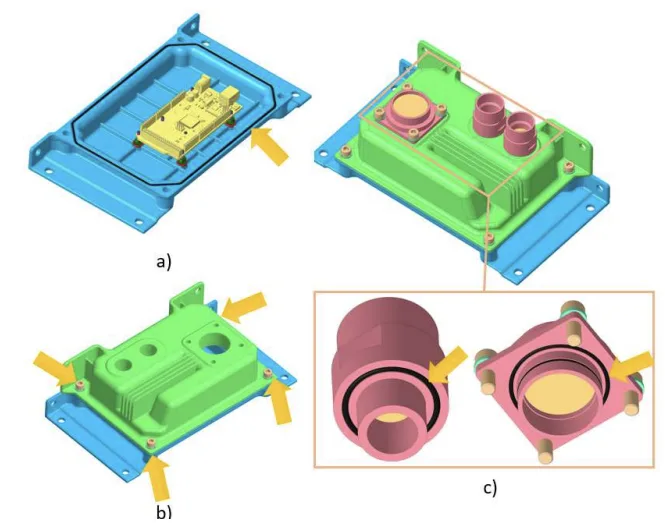
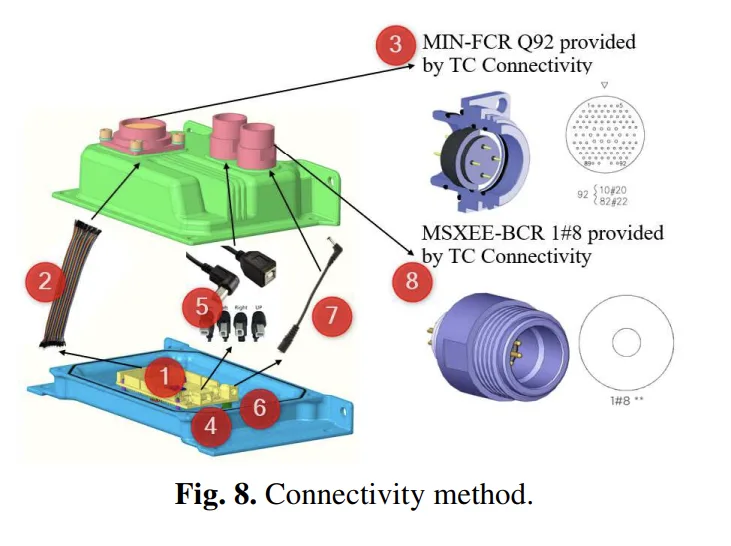
6. Conclusion and Discussion:
- Summary of Main Results: This research successfully designed a new protective case for the Arduino Mega microcontroller suitable for deep-sea aquatic exploration, addressing limitations of previously used methods. FEA simulations demonstrated the structural integrity and thermal performance of the design. A case made from Casted Ductile Iron can withstand greater depths (63m) compared to Aluminum A380 (36m), while Aluminum A380 exhibits superior heat dissipation (10.7% more efficient).
- Academic Significance of the Research: This research contributes to the field of underwater robotics and microcontroller applications in extreme environments. It provides a detailed design methodology for creating robust protective casings using die casting, incorporating considerations for waterproofing, shockproofing, and thermal management. The comparative analysis of Aluminum A380 and Casted Ductile Iron offers valuable insights for material selection based on specific application requirements (depth vs. heat dissipation).
- Practical Implications: The designed protective case has practical utility for researchers, enthusiasts, and hobbyists working on underwater projects using Arduino Mega. The detailed design and analysis provide a foundation for constructing reliable and cost-effective protective enclosures. The inclusion of external connectors enhances user-friendliness by allowing access to microcontroller functionalities without disassembling the case. The findings regarding material performance offer guidance for selecting the optimal material based on the intended depth of operation and thermal considerations.
- Limitations of the Research: The research is primarily based on FEA simulations. Experimental validation of the designed case's performance in real-world underwater conditions is not included. The thermal simulation assumes a specific convection coefficient and microprocessor heat output, which may vary in actual applications. Further research could benefit from experimental testing and sensitivity analysis of simulation parameters.
7. Future Follow-up Research:
- Directions for Follow-up Research: Future research should focus on experimental validation of the designed protective case through pressure testing and thermal performance evaluation in underwater environments. Optimizing the heat sink design by reducing fin length based on the observed uneven heat distribution could be explored to minimize material usage and production costs.
- Areas Requiring Further Exploration: Further exploration could investigate:
- Optimizing the width and configuration of reinforcement ribs to further enhance structural integrity and increase maximum admissible depth.
- Investigating the impact of varying round values on stress concentration and structural performance.
- Exploring the use of alternative die casting materials with improved strength-to-weight ratios and thermal conductivity.
- Considering more intricate case designs and alternative manufacturing methods (beyond die casting) to achieve even greater depth capabilities.
- Conducting more detailed thermal analysis considering varying convection coefficients and microprocessor power consumption profiles.
8. References:
- [1] National Geographic Society, ‘Ocean', https://education.nationalgeographic.org/resource/ocean
- [2] A. Cadena, “A Modular Hardware-Software Architecture of an Autonomous Underwater Vehicle for Deep Sea Exploration.", Proceedings of the World Congress on Engineering, Vol I, pp. 178-183, 2017
- [3] S. K. Deb, J. H. Rokky, T. C. Mallick and J. Shetara, "Design and construction of an underwater robot," 2017 4th International Conference on Advances in Electrical Engineering (ICAEE), 2017
- [4] K. Duy Le, H. D. Nguyen, D. Ranthumugala and A. Forrest, "Haptic driving system for surge motion control of underwater remotely operated vehicles," Proceedings of 2014 International Conference on Modelling, Identification & Control, 2014
- [5] T. Soriano, N.V. Hien, K.M. Tuan, T.V. Anh, An object-unified approach to develop controllers for autonomous underwater vehicles, Mechatronics, Volume 35, ISSN 0957-4158, 2016
- [6] Kraig Kreiner et al. “Nautilus II Technical Report", 2015 www.marinetech.org/files/marine/files/ROV%20Competition/2015%20files/TECHNICAL%20REPORTS/Palos_Verdes_Institute_Technology_TechReport.pdf, acc. 2023
- [7] MESInc, “Alloy Data: Aluminum Die Casting Alloys”, www.mesinc.net/wp-content/uploads/2020/02/Die-Casting-Aluminum-Selection-Guide.pdf, acc. 2023
- [8] Matweb, “Ductile Iron grade 60-40-18", www.matweb.com/search/datasheet_print.aspx?matguid=be37a34ca60a484394a1d28f5a02de67, acc. 2023
- [9] Philip Kosky, Robert Balmer, William Keat, George Wise, Chapter 12 Mechanical Engineering, Editor(s): Philip Kosky, Robert Balmer, William Keat, George Wise, Exploring Engineering (Third Edition), Academic Press, Pages 259-281, ISBN 9780124158917, 2013
9. Copyright:
- This material is "Mircea Ionuţ GELER, Dan LEORDEAN"'s paper: Based on "RESEARCH ON THE DESIGN FOR PROTECTING THE ARDUINO-MEGA MICROCONTROLLER USED AT AQUATIC EXPLORATION".
- Paper Source: https://doi.org/ (DOI URL was not provided in the paper, please insert DOI URL if available)
This material was summarized based on the above paper, and unauthorized use for commercial purposes is prohibited.
Copyright © 2025 CASTMAN. All rights reserved.