This introductory paper is the research content of the paper ["Process Analysis and Defect Improvement of Integrated Die Casting Parts for a Certain Automobile Rear Cabin"] published by [SPECIAL CASTING & NONFERROUS ALLOYS].
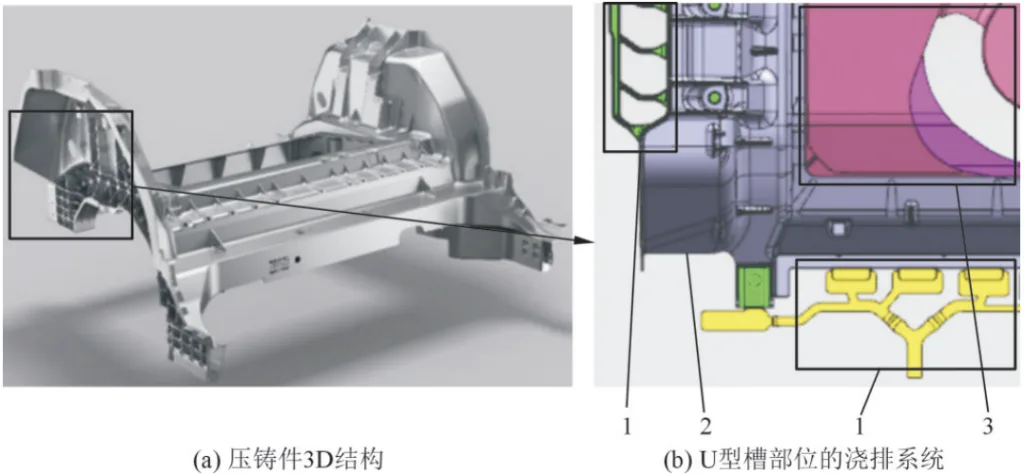
1. Overview:
- Title: Process Analysis and Defect Improvement of Integrated Die Casting Parts for a Certain Automobile Rear Cabin
- Author: LU Canxiong, LUO Wei, LI Jiqiang, JIA Zhixin, LIU Lijun, WU Shirong, YANG Bin, SUN Lili, GUO Tao
- Publication Year: Jan. 2025
- Publishing Journal/Academic Society: SPECIAL CASTING & NONFERROUS ALLOYS
- Keywords: Automotive Rear Cabin, Die Casting, Defect Analysis, Intergrated Technology
2. Abstracts or Introduction
Abstract: Using Flow-3D simulation software to fill the initial solution of the product, it is found that there is a quality risk in the U-shaped groove area of the rear cabin castings. Mechanical performance experiments show that the mechanical properties at the U-shaped groove position are unqualified. Further X-ray inspection was conducted to confirm the presence of porosity defects in the U-shaped groove area of the casting. In order to improve the quality in the area of the casting, the overflow system was optimized. The X-ray inspection results based on products by optimized system reveal that the internal structure of the area is dense without obvious porosity defects. Mechanical experiments show that the optimization scheme effectively improve the mechanical properties of the U-shaped groove, and the average elongation is increased by 30%.
3. Research Background:
Background of the Research Topic:
Automotive lightweighting is an effective measure to cope with the rapid growth of car ownership, which has been widely valued by car companies. The automobile rear cabin is an important structural part of the chassis system, which provides installation positions for the suspension system and in-vehicle cabin components, and plays a good role in bearing support. Its quality directly affects the stability, comfort, durability, NVH and collision resistance of the whole vehicle. Due to the large volume, uneven wall thickness and complex structure of automobile rear cabin die castings, porosity defects are easily generated in the die casting process, especially at the end of filling, which affects the quality of die castings. Improving the quality of die castings is the key to ensuring the safety of the whole vehicle.
Status of Existing Research:
NIU Z et al. used CAE technology to analyze the defects of die castings and found that the mold structure is the key to determining the quality of die castings. SCHILLING A et al. studied die casting defects by modifying the mold structure and combining numerical simulation technology, and found that optimizing the mold venting system design is helpful to reduce casting defects. SHU Huping found that optimizing the overflow groove structure can effectively discharge the air in the molten metal and prevent porosity defects.
Necessity of the Research:
This research focuses on the die casting process of an automobile rear cabin die casting part of a certain brand. By analyzing its die casting process and defect reasons, optimizing the process to reduce the generation of defects in die casting production, and exploring the process optimization and defect control methods of large integrated die castings, it aims to provide reference for its application.
4. Research Purpose and Research Questions:
Research Purpose:
The purpose of this study is to analyze the defects in the U-shaped groove area of a certain brand automobile rear cabin die casting and improve its mechanical properties by optimizing the overflow system.
Key Research:
- Analyze the filling process of the initial scheme using Flow-3D simulation software to identify potential quality risks in the U-shaped groove area.
- Conduct mechanical performance tests and X-ray inspection to confirm the presence of porosity defects in the U-shaped groove area.
- Optimize the overflow system through CAE analysis to improve the quality of the U-shaped groove area.
- Verify the effectiveness of the optimized scheme through X-ray inspection and mechanical performance testing of samples produced by the optimized system.
5. Research Methodology
Research Design:
The research design involves numerical simulation using Flow-3D software, experimental validation through mechanical performance testing and X-ray inspection, and CAE analysis for optimization of the overflow system.
Data Collection Method:
- Simulation Data: Flow-3D software was used to simulate the filling process and identify air entrapment risks.
- Experimental Data: Mechanical performance data was collected through tensile tests. X-ray inspection was used to detect porosity defects.
Analysis Method:
- Flow-3D Simulation Analysis: Analysis of the filling process to identify areas prone to defects.
- Mechanical Performance Analysis: Tensile testing to evaluate the elongation rate in the U-shaped groove area.
- X-ray Inspection Analysis: Non-destructive testing to identify and confirm porosity defects.
- CAE Analysis: Used for optimizing the overflow system design.
Research Subjects and Scope:
The research subject is an integrated die casting part for a certain automobile rear cabin made of JDA1B aluminum alloy. The scope of the study is focused on analyzing and improving the quality of the U-shaped groove area of this specific die casting part.
6. Main Research Results:
Key Research Results:
- Initial Scheme Defect Identification: Flow-3D simulation revealed air entrapment risk in the U-shaped groove area. Mechanical testing and X-ray inspection confirmed porosity defects and unqualified mechanical properties in this area.
- Overflow System Optimization: CAE analysis was used to optimize the overflow system by disconnecting the overflow groove connected to the U-shaped groove from the one connected to the right side overflow cavity, and providing an independent venting path for the U-shaped groove cavity.
- Optimized Scheme Validation: X-ray inspection of samples produced with the optimized system showed a dense internal structure without obvious porosity defects in the U-shaped groove area. Mechanical testing demonstrated a 30% increase in average elongation in the U-shaped groove area compared to the initial scheme.
Analysis of presented data:
- Fig.1: Shows the 3D structure of the die casting part and the gating system of the U-shaped groove area.
- Fig.2: Illustrates the casting filling process from Flow-3D simulation, showing air entrapment in the U-shaped groove area in the initial design.
- Fig.3: Displays the sample cutting position for mechanical testing.
- Fig.4: Shows the dimensions of the tensile test specimens.
- Fig.5: Presents the elongation rate test results of the initial scheme, indicating that the elongation rate in the U-shaped groove area did not meet the requirement of ≥5%.
- Fig.6: Shows the X-ray inspection results of the initial scheme samples, confirming porosity defects in the U-shaped groove area.
- Fig.7: Illustrates the overflow system before optimization.
- Fig.8: Illustrates the optimized overflow system.
- Fig.9: Shows the die-casting flow field in the U-shaped groove area after optimizing the overflow system, demonstrating reduced air entrapment.
- Fig.10: Shows the X-ray inspection results of optimized samples, indicating no obvious porosity defects.
- Fig.11: Presents the elongation rate test results of optimized samples, showing improved elongation rate compared to the initial scheme.
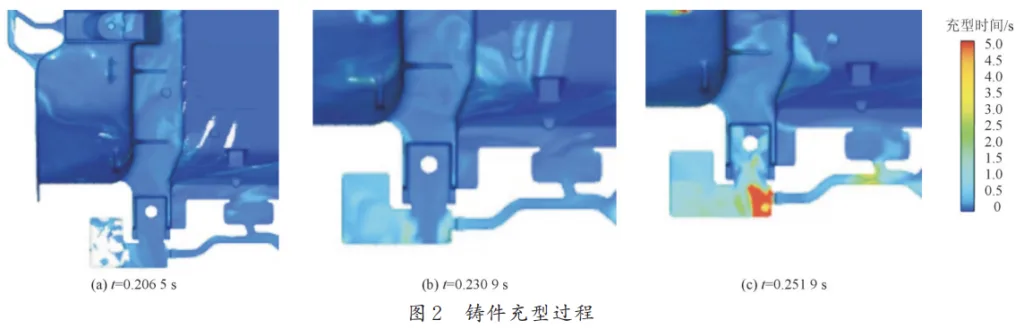
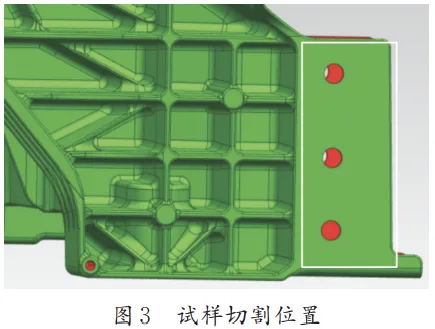
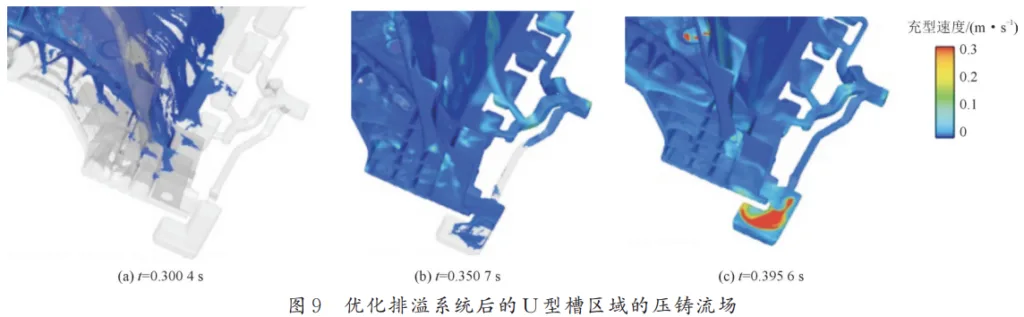
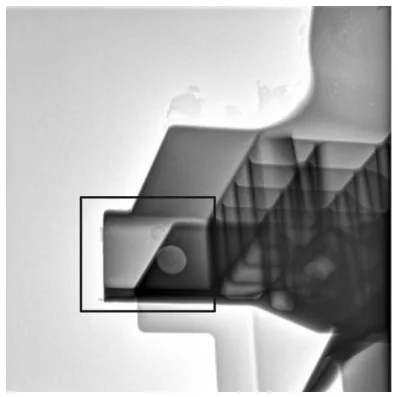
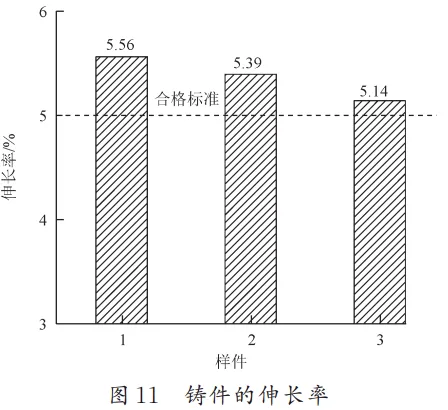
Figure Name List:
- Fig.1 Die casting and local structure of automobile rear cabin
- Fig.2 Casting filling process
- Fig.3 Sample cutting position
- Fig.4 Dimension diagram of tensile specimens
- Fig.5 Elongation of tested specimens
- Fig.6 X-ray detection of the specimens
- Fig.7 Overflow system before optimization
- Fig.8 Optimized overflow system
- Fig.9 Die-casting flow field in the U-shaped groove area after optimizing overflow system
- Fig.10 X-ray results of optimized sample
- Fig.11 Elongation of specimens
7. Conclusion:
Summary of Key Findings:
This study investigated defects in the U-shaped groove area of an automobile rear cabin die casting. Through Flow-3D simulation, mechanical testing, and X-ray inspection, porosity defects were identified as the cause of insufficient mechanical properties. Optimization of the overflow system, by separating the venting for the U-shaped groove and reducing melt flow interference, significantly improved the casting quality. The optimized design demonstrated a 30% increase in elongation rate in the U-shaped groove area.
Academic Significance of the Study:
This research provides a detailed case study on applying numerical simulation and experimental validation to analyze and improve die casting defects in complex, large-scale integrated parts. It highlights the importance of optimized overflow system design in achieving high-quality die castings, contributing to the body of knowledge in die casting process optimization.
Practical Implications:
The findings offer practical guidance for die casting manufacturers in optimizing gating and venting systems for large, complex parts like automobile rear cabins. The optimized overflow system design presented in this study can be directly applied to similar die casting applications to reduce porosity defects and enhance mechanical performance, leading to improved product quality and reduced scrap rates.
Limitations of the Study and Areas for Future Research:
This study focused on a specific automobile rear cabin die casting part and a particular defect location. Future research could explore the generalizability of these findings to other die casting parts with different geometries and alloys. Further investigation into the effects of other process parameters, such as injection speed profiles and cooling strategies, on defect formation and mechanical properties would also be valuable.
8. References:
- [1] LI Long, XIA Chengdong, SONG Youbao, et al. Application status and prospect of aluminum alloy in new energy vehicle industry [J]. Light Alloy Processing Technology, 2017, 45(9): 18-25.
- [2] MA Jin. Research on key technologies of lightweighting of new energy vehicles [J]. Industrial Innovation Research, 2022(2): 45-47.
- [3] FAN Zhenzhong, YUAN Wanquan, WANG Duanzhi, et al. Research status and future development trend of die-casting aluminum alloy [J]. Foundry, 2020, 69(2): 159-166.
- [4] JEONG SI, JIN CK, SEO HY, et al. Mold structure design and casting simulation of the high-pressure die casting for aluminum automotive clutch housing manufacturing [J]. The International Journal of Advanced Manufacturing Technology, 2016, 84: 1 561-1 572.
- [5] NIU Z, LIUG, LIT, et al. Effect of high pressure die casting on the castability, defects and mechanical properties of aluminium alloys in extra-large thin-wall castings [J]. Journal of Materials Processing Technology, 2022, 303: 117-525.
- [6] SCHILLING A, SCHMIDT D, GLÜCK J, et al. About the impact on gravity cast salt cores in high pressure die casting and rheo-casting [J]. Simulation Modelling Practice and Theory, 2022, 119: 102-585.
- [7] SHU Huping. Effect of cooling rate on porosity formation in aluminum alloy castings [A]. Proceedings of the 12th National Foundry Annual Meeting and 2011 China Foundry Activity Week [C]. Suzhou, 2011.
9. Copyright:
- This material is "[LU Canxiong, LUO Wei, LI Jiqiang, JIA Zhixin, LIU Lijun, WU Shirong, YANG Bin, SUN Lili, GUO Tao]"'s paper: Based on "[Process Analysis and Defect Improvement of Integrated Die Casting Parts for a Certain Automobile Rear Cabin]".
- Paper Source: DOI: 10.15980/j.tzzz.T20230539
This material was created to introduce the above paper, and unauthorized use for commercial purposes is prohibited.
Copyright © 2025 CASTMAN. All rights reserved.