AI-Powered Design: Eliminating Heatsink Fracture Before It Happens
This technical brief is based on the academic paper "Prevention of the Fracture Problem Occurring in Automotive Alternator Heatsink Blocks Using Artificial Intelligence" by Dinçer Kökden, Adem Egi, Emre Bulut, Emre İsa Albak, İbrahim Korkmaz, and Ferruh Öztürk, published in Applied Sciences (2024). It is summarized and analyzed for HPDC professionals by the experts at CASTMAN.
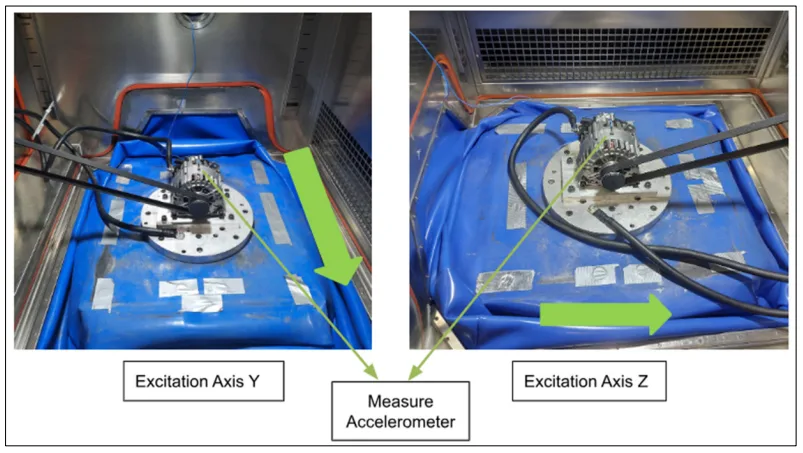
Keywords
- Primary Keyword: AI for Automotive Heatsink Fracture Prevention
- Secondary Keywords: vibration fatigue, artificial neural network (ANN), resonance frequency prediction, alternator heatsink, fatigue crack, regression analysis, design optimization
Executive Summary
- The Challenge: Automotive alternator heatsinks, often complex parts with thin structures, are prone to fracture during high-cycle vibration fatigue testing when the test frequency matches the part's natural resonance frequency. This leads to costly and time-consuming redesign cycles.
- The Method: Researchers developed an efficient Artificial Neural Network (ANN) model to predict the resonance frequency of a heatsink based on key geometric and loading parameters. The model was trained and validated using data from physical vibration tests and finite element simulations.
- The Key Breakthrough: The AI model achieved high accuracy in predicting the heatsink's natural frequency, enabling engineers to optimize the design and shift the resonance above the critical 700 Hz threshold, effectively preventing the vibration-induced fractures seen in initial tests.
- The Bottom Line: This study proves that integrating AI into the early design stages can significantly reduce the time and cost associated with physical prototyping and testing, preventing component failure by predicting and designing around harmful resonance.
The Challenge: Why This Research Matters for HPDC Professionals
In the automotive world, reliability is non-negotiable. Components like alternator heatsinks must endure a lifetime of vibration without failing. As described in the paper, these parts are subjected to high-cycle vibration loads that can lead to fatigue cracks and catastrophic failure (Ref. [5]). A common cause of failure during validation testing is resonance, where the frequency of the vibration test excites the part's own natural frequency, amplifying stress and causing it to break, as shown in Figure 4.
For manufacturers, this is a recurring nightmare. A fracture during a late-stage durability test means going back to the drawing board. This involves intensive simulation studies, creating new tooling, and re-running expensive, time-consuming tests. The paper highlights that these redesigns lead to "significant time losses and high costs." This research tackles this problem head-on by asking: Can we predict and design out this failure before we ever build a physical part?
The Approach: Unpacking the Methodology
To solve this challenge, the researchers adopted a data-driven, AI-powered approach, detailed in the flowchart in Figure 1.
- Problem Identification: They began by conducting a vibration fatigue test on an existing alternator, which resulted in a fracture at the heatsink bolt area. A sine sweep test identified a local resonance mode at 496.17 Hz as the culprit (Figure 3, Table 1).
- Simulation & Validation: Using ANSYS simulation software, they replicated the failure mode, confirming that the high stress at the heatsink bolt hole was caused by excitation at its local natural frequency (Figure 6).
- Data Generation: To train an AI model, they systematically created 60 new heatsink designs by varying three key parameters: the B+ cross-section thickness (Td1), the bolt hole thickness (Td2), and the B+ cable weight (Td3). They then ran modal analysis simulations on each design to determine its new natural frequency (Table 2).
- AI Model Development: An Artificial Neural Network (ANN) was developed in MATLAB. This network was trained to find the relationship between the three design inputs (Td1, Td2, Td3) and the resulting natural frequency output. The model's high accuracy was confirmed with R-values consistently above 0.997 (Table 3).
- Optimization: Finally, they used the trained ANN as a fast, accurate surrogate model to run multiple optimization algorithms (including GA, AOA, AVOA, and EO) to find the ideal design parameters that would maximize the natural frequency, pushing it safely out of the test range.
The Breakthrough: Key Findings & Data
The study yielded several powerful results that demonstrate the viability of using AI for predictive design in component engineering.
- Accurate Failure Replication: The initial simulation successfully identified the local resonance mode at 460.21 Hz, closely matching the 496.17 Hz frequency that caused the physical fracture in the lab test. This validated the simulation model as a reliable foundation for further study (Figure 5).
- High-Fidelity AI Prediction: The ANN model proved to be exceptionally accurate. When comparing the AI's predictions to the computationally-intensive finite element analysis (FEA) results, the relative error was extremely low, with the largest error being only -1.64% for the PSO algorithm's optimal design (Table 5).
- Successful Design Optimization: The optimization algorithms, guided by the AI model, successfully identified new design parameters. For example, the AVOA, EO, and GA algorithms all converged on an optimal design (Td1=3.275 mm, Td2=4 mm, Td3=40 g) that was predicted to have a natural frequency of 728.902 Hz.
- Drastic Reduction in Calculation Time: The core advantage of the AI model is speed. Compared to running a full FEA simulation for every design iteration, the trained ANN and MATLAB Simulink models provided near-instantaneous predictions, dramatically reducing the time required for design and optimization.
Practical Implications for HPDC Products
While the paper focuses on an alternator heatsink, the principles are directly applicable to any complex, thin-walled structural component produced via HPDC that is subject to vibration.
- For Process Engineers: This research underscores the critical link between minor geometric features and real-world performance. The data in Table 2 clearly shows how changes in thickness (a key factor in die casting) directly impact a part's vibration characteristics. This knowledge empowers engineers to have more informed design-for-manufacturability (DFM) discussions with customers, highlighting how process capabilities can influence end-use reliability.
- For Quality Control: A robust, optimized design is inherently easier to produce with consistent quality. By using predictive models to eliminate resonance-related failure modes, manufacturers can reduce the likelihood of downstream quality issues that arise from a design being too close to its operational limits.
- For Die Design: This is the most significant takeaway. The study provides a clear methodology for front-loading performance optimization into the design phase. For HPDC companies offering design services, this approach is a powerful value-add. Instead of only optimizing for castability (flow, fill, solidification), you can now incorporate performance metrics like vibration resistance. The optimization of "Bolt hole thickness" and "cross section thickness" demonstrates that features directly controlled by die design have a profound impact on the part's final durability.
Paper Details
Prevention of the Fracture Problem Occurring in Automotive Alternator Heatsink Blocks Using Artificial Intelligence
1. Overview:
- Title: Prevention of the Fracture Problem Occurring in Automotive Alternator Heatsink Blocks Using Artificial Intelligence
- Author: Dinçer Kökden, Adem Egi, Emre Bulut, Emre İsa Albak, İbrahim Korkmaz and Ferruh Öztürk
- Year of publication: 2024
- Journal/academic society of publication: Applied Sciences (MDPI)
- Keywords: vibration; neural network; heatsink; fracture; fatigue; automotive; crack; regression; optimization
2. Abstract:
In this study, prevention of fracture in vibration fatigue testing of automotive alternator heatsink blocks was investigated using an artificial neural network. Automotive components such as alternator heatsink blocks are subjected to high cyclic vibration fatigue loads throughout their lifespan, which can lead to the formation and propagation of fatigue cracks and ultimately component failure. The basic parameters affecting the resonant frequency of the heatsink blocks, including geometry and loading conditions, are determined. Data-driven decision making provides advanced predictive insights to analyze data for prediction and decisions using artificial intelligence approaches. An efficient artificial neural network model was defined to predict the resonance frequency in the vibration fatigue test. While the artificial neural network was trained to establish a functional relationship between the parameters and the resonance frequency, regression analysis was used to develop a predictive model to detect the resonance frequency of the heatsinks. The proposed approach aims to provide a comprehensive framework for preventing fracture problems in vibration fatigue tests of automotive alternator heatsinks and ultimately contribute to the reliable design and performance of these critical components. While the artificial neural network approach achieved high classification accuracy in predicting the new natural frequency, the regression model was also able to make accurate predictions. The results of this study showed that the time spent on design and simulation can be significantly reduced in preventing breakage problems that may occur before dynamic tests such as vibration tests of alternator components.
3. Introduction:
The performance and reliability of alternators in vehicles depend on effective thermal management. Alternators generate significant heat, and heatsinks are designed to dissipate it efficiently, often using thin structures with a large surface area. However, these thin structures can be susceptible to fracture from dynamic loads if their natural frequency coincides with the excitation frequency from the vehicle or engine. This study investigates the prevention of such fractures in alternator heatsinks by using an artificial neural network to predict and optimize the component's resonance frequency behavior. The goal is to develop a methodology that shortens calculation times and introduces a new, more efficient approach to the design process, moving away from experience-based suggestions.
4. Summary of the study:
Background of the research topic:
Automotive components are constantly subjected to vibration, which can lead to fatigue cracks and failure. This is a major concern in engineering, accounting for up to 90% of all structural failures. Specifically, alternator heatsinks, designed with thin fins for cooling, can break if their natural resonance frequency is excited during operation.
Status of previous research:
Researchers have previously used computational techniques like artificial neural networks (ANNs) and regression analysis to predict fatigue life. ANNs are effective at modeling complex, nonlinear relationships. However, the application of these AI models specifically to predict and optimize the local resonance frequency of alternator heatsinks to prevent fracture is a novel approach.
Purpose of the study:
The study aimed to develop a comprehensive framework to prevent fracture problems in automotive alternator heatsinks during vibration fatigue tests. The primary goals were:
1. To identify the key design parameters affecting the heatsink's resonance frequency.
2. To build an accurate predictive model using an ANN.
3. To use this model to optimize the heatsink design, shifting its natural frequency to a safe range.
4. To demonstrate that this AI-driven approach can significantly reduce design time and costs compared to traditional trial-and-error methods.
Core study:
The core of the study involved a six-step process:
1. Acquiring real-world test data from a vibration test that caused a heatsink to fracture.
2. Verifying the test results with a finite element simulation to understand the failure mode.
3. Creating a Design of Experiments (DOE) with 60 different heatsink geometries and running simulations to generate a dataset.
4. Building and training an ANN to predict resonance frequency based on the design parameters.
5. Using the trained ANN with various optimization algorithms to find the best design that maximized the natural frequency.
6. Validating the results of the optimization.
5. Research Methodology
Research Design:
The study followed a structured approach combining physical experimentation, computer-aided engineering (CAE), and artificial intelligence. It started with a physical test to establish a baseline failure. This was followed by simulation to diagnose the root cause (resonance). A parametric study was then conducted via simulation to generate data, which was used to train and validate a predictive AI model. Finally, this AI model was used within an optimization loop to find an improved design.
Data Collection and Analysis Methods:
- Physical Test: A 40 kN electrodynamic shaker was used for a vibration fatigue test (100–500 Hz at 10 g) and a sine sweep characterization test (100–1000 Hz at 5 g).
- Simulation: Modal and stress analyses were performed using ANSYS 2019 R2.
- Experimental Design: A Latin hypercube method was used to generate 60 experimental design points.
- AI Modeling: An artificial neural network (surrogate model) was created and trained in MATLAB (version R2024a) using the Levenberg-Marquardt algorithm. The model's performance was evaluated using k-fold cross-validation and R-values.
- Optimization: Six different optimization algorithms were compared: AOA, Aquila, AVOA, EO, GA, and PSO.
Research Topics and Scope:
The research focused on an automotive alternator heatsink block. The scope was limited to preventing fracture caused by resonance during Z-axis vibration. The key variables investigated were the B+ cross-section thickness, the bolt hole thickness, and the weight of the attached B+ cable. The objective was to maximize the heatsink's natural frequency to move it above 700 Hz.
6. Key Results:
Key Results:
- The initial heatsink failed due to a local resonance mode at 496.17 Hz, which was confirmed by simulation.
- An ANN surrogate model was created with very high accuracy (R-values > 0.997), capable of predicting the natural frequency based on three design inputs.
- A MATLAB Simulink prediction model was also created, allowing for instant frequency estimation for new designs (Figure 10).
- Optimization using the AI model found a new design with a predicted natural frequency of 728.902 Hz, well above the target.
- The AOA, AVOA, EO, and GA optimization algorithms were identified as the most suitable for this problem in terms of both speed and accuracy (Table 4).
- The error between the AI model's prediction and a final FEA validation was less than 1.64%, confirming the model's high fidelity (Table 5).
Figure Name List:
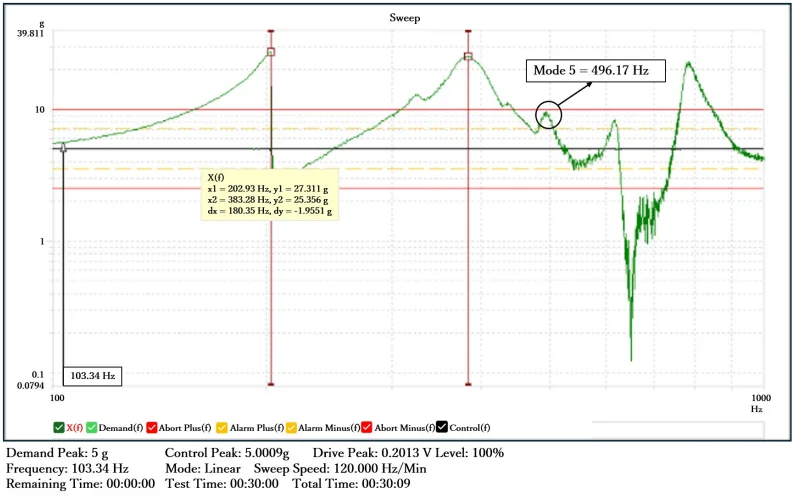
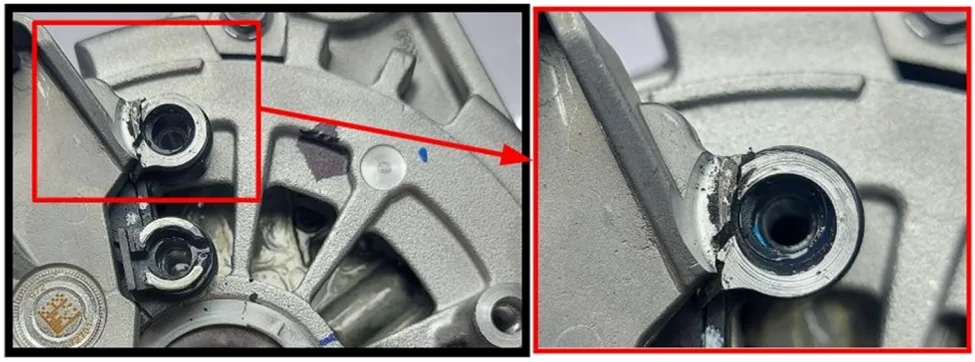
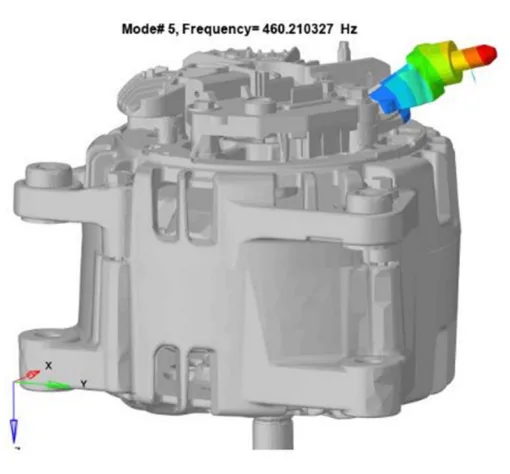
- Figure 1. Flowchart of proposed study.
- Figure 2. Alternator resonance frequency characterization test setup.
- Figure 3. Resonance frequency characterization test results of alternator at Z-axis.
- Figure 4. Heatsink fracture after durability test.
- Figure 5. Alternator heatsink B+ zone local resonance modal shape.
- Figure 6. Alternator heatsink analysis with ANSYS 2019 R2.
- Figure 7. Heatsink modal analysis with ANSYS 2019 R2.
- Figure 8. NN architecture.
- Figure 9. MATLAB R-values.
- Figure 10. MATLAB Simulink prediction model.
- Figure 11. Convergence curves of each optimization algorithm.
- Figure 12. Best convergence curve of each optimization.
7. Conclusion:
The study successfully demonstrated the effectiveness of using artificial neural networks to predict and prevent vibration-induced fractures in automotive alternator heatsinks. The AI model accurately predicted the component's natural frequency, allowing for an optimized design that resolved the resonance problem. The authors conclude that this approach can significantly reduce the time and cost associated with design and simulation by preventing failures before physical testing. The integration of ANN and optimization provides a powerful framework for designing reliable critical components.
8. References:
- [List of 36 references as provided in the paper.]
Expert Q&A: Your Top Questions Answered
Q1: What was the single most critical factor identified in this study for improving the heatsink's vibration resistance?
A1: The study didn't identify a single factor but rather an optimal combination of three: the B+ region cross-sectional thickness, the bolt hole thickness, and the B+ cable weight. The goal was to optimize these three parameters together to maximize the natural frequency and shift it out of the dangerous range, as detailed in the "Optimization of Alternator Heatsink" section.
Q2: How does this research compare to traditional methods for addressing resonance problems?
A2: The paper's conclusion states that traditional methods involve redesign and simulation studies after a failure occurs, which leads to "significant time losses and high costs." This AI-driven research introduces a predictive approach that acts as a "time-saving and cost-reduction method" by resolving potential resonance problems during the initial design phase.
Q3: Is this finding applicable to all types of alloys, or a specific one?
A3: The paper does not specify the material or alloy used for the alternator heatsink. Therefore, the direct applicability of the specific numerical results to other alloys would require further investigation. However, the methodology itself—using AI to predict resonance based on geometry—is a principle that could be applied to components made from various materials.
Q4: What specific measurement or simulation technique did the researchers use to arrive at this conclusion?
A4: The researchers used a combination of techniques. For physical testing, they used an electrodynamic shaker. For simulation, they used "ANSYS 2019 R2" for modal analysis. To create the predictive model, they developed an "artificial neural network" using the "Levenberg-Marquardt" training function within "MATLAB Simulink," as described in the "Surrogate Modeling" and "Other Design and Simulation Studies" sections.
Q5: According to the paper, what is the main limitation or area for future research?
A5: The authors do not explicitly state limitations in the "Conclusions" section. Instead, they focus on the success and contributions of their approach. The paper presents a successful case study, implying that future work could involve applying this validated methodology to other components or more complex vibration scenarios.
Q6: What is the direct, practical takeaway from this paper for a die casting facility?
A6: The core takeaway is that by leveraging AI and simulation, it's possible to predict how design choices will affect a part's real-world performance, specifically its resistance to vibration fatigue. As stated in the conclusion, developing AI models to predict the natural frequency "can be used as an important time-saving and cost-reduction method in addressing recurrent resonance-related breakage and cracking problems." For a die casting facility, this means you can offer customers a higher level of design assurance, preventing costly failures long before a die is ever cut.
Conclusion & Next Steps
This research provides a valuable roadmap for enhancing component reliability in demanding automotive applications. By moving from a reactive "test-fail-redesign" cycle to a proactive "predict-optimize-build" model, manufacturers can save significant time and money. The findings offer a clear, data-driven path toward improving quality, reducing defects, and optimizing production for parts subjected to harsh vibrational environments.
At CASTMAN, we are dedicated to applying the latest industry research to solve our customers' most challenging die casting problems. If the issues discussed in this paper resonate with your operational goals, contact our engineering team to discuss how we can help you implement these advanced principles in your components.
Copyright
- This material is a paper by "Dinçer Kökden, Adem Egi, Emre Bulut, Emre İsa Albak, İbrahim Korkmaz and Ferruh Öztürk". Based on "Prevention of the Fracture Problem Occurring in Automotive Alternator Heatsink Blocks Using Artificial Intelligence".
- Source of the paper: https://doi.org/10.3390/app142411758
This material is for informational purposes only. Unauthorized commercial use is prohibited.
Copyright © 2025 CASTMAN. All rights reserved.