This article introduces the paper 'A Water-Soluble Core for Manufacturing Hollow Injection-Molded Products' published by 'MDPI'.
1. Overview:
- Title: A Water-Soluble Core for Manufacturing Hollow Injection-Molded Products
- Author: Chung-Chih Lin and Chao-Long Yang
- Publication Year: 2022
- Publishing Journal/Academic Society: Polymers
- Keywords: injection molding; water-soluble core; insert molding; Taguchi method
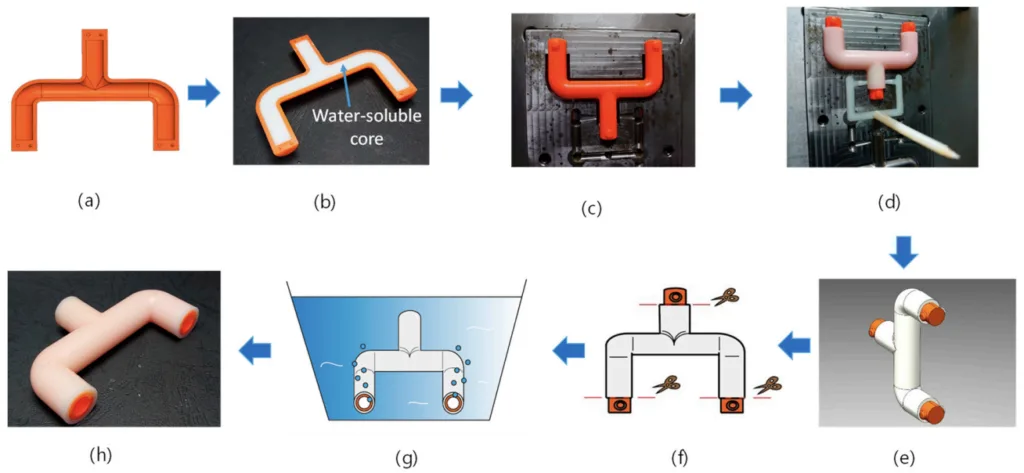
2. Abstracts or Introduction
Abstract: To manufacture a complicated hollow product without any assembly process, for example, the plastic intake manifold, is difficult by the traditional injection molding method. The fusible-core technique, which uses a low-melting-point alloy as a sacrificial core, was developed to solve this problem; however, the limited selection of resin type and the huge capital investment have caused this technique to spread slowly. In this work, a novel method is established that can produce similar products without the limitation of resin type, as well as a lower-energy-consumption process. The concept of the enveloped core defined by a water-soluble core assembled with a shell is proposed herein; it provides both rigidity and toughness to resist the pressure during the injection molding process. The shape of the enveloped core equals the internal contour of the designated product. An insert molding process was introduced to cover the enveloped core with a skin layer. Cut out the end of the enveloped core and immerse it into a water bath. When the water-soluble core inside the shell is dissolved, the product with a special internal contour is accomplished. A tee-joint is presented to demonstrate how the proposed method can be utilized. The optimal ingredient of the core and processing parameters are determined by the Taguchi method. The result shows that the proposed product is molded successfully when the compressive strength of the core is larger than 2 MPa. In addition, the eccentricity measurement of internal contour of the optimal sample exhibits a 56% improvement, and the required time for the core removal is less than 154 s.
3. Research Background:
Background of the Research Topic:
Manufacturing complicated hollow products, such as plastic intake manifolds, using traditional injection molding methods presents significant challenges. Conventional methods often require dividing the product into subcomponents, followed by assembly processes like mechanical fastening or adhesive bonding. These assembly steps increase manufacturing costs, accumulate dimensional errors [5,6], and create weak points in the final product, potentially leading to failures under high pressure or heavy loading. Furthermore, bonding processes may involve chemical solvents that "contaminate the environment".
Status of Existing Research:
Existing techniques to manufacture hollow products include "removable or collapse core skill", such as sand cores for metal casting [7] and polymer cores like polyoxymethylene (POM) or polystyrene (PS) foam for resin transfer molding (RTM). Salt cores are also utilized due to their "good solubility in water" [7-11]. However, "the pressure induced by the RTM process is much lower than that in the plastic injection process", making brittle salt cores susceptible to cracking and core shift during injection molding. The "fusible-core technique" using low-melting-point alloys as sacrificial cores [12] improves upon these methods but suffers from "limited selection of resin type and the huge capital investment". Another method using "water-soluble polyvinyl alcohol (PVOH) patterns" [13] exists, but it differs from fusible-core techniques in its support mechanism within the mold cavity.
Necessity of the Research:
Despite existing methods for hollow product manufacturing, there is a need for improvement, particularly in injection molding, to produce "special hollow product[s]". Current methods like fusible core techniques have limitations in resin compatibility and cost, while salt cores are challenging to use directly in injection molding due to their brittleness. Therefore, a novel method is needed to overcome these limitations and enable efficient and versatile manufacturing of complex hollow parts via injection molding.
4. Research Purpose and Research Questions:
Research Purpose:
This research aims to establish a novel method for manufacturing complicated hollow products using injection molding, addressing the limitations of existing techniques. The proposed method focuses on an "enveloped core defined by a water-soluble core assembled with a shell", aiming to produce products "without the limitation of resin type, as well as a lower-energy-consumption process". The method intends to provide a core with "both rigidity and toughness to resist the pressure during the injection molding process".
Key Research:
The key research focuses include:
- Developing and characterizing a water-soluble core material composed of NaCl (salt) and trehalose sugar (binder).
- Designing and implementing an "enveloped core" system using a water-soluble core and a plastic shell.
- Optimizing the "ingredient of the core and processing parameters" using the Taguchi method to achieve adequate core strength.
- Demonstrating the feasibility of the proposed method by manufacturing a tee-joint product with a complex internal contour.
- Evaluating the "influence of the binder content, applied pressure, processing temperature, and processing time on the core strength and the dimension accuracy of the molded product, as well as the core removal rate".
Research Hypotheses:
The research hypothesizes that:
- An enveloped core, consisting of a water-soluble core and a plastic shell, can withstand the pressure of injection molding, unlike a bare water-soluble core.
- Optimizing the composition (salt and binder ratio) and processing parameters (pressure, temperature, time) of the water-soluble core using the Taguchi method will lead to cores with sufficient compressive strength for injection molding.
- The proposed enveloped core method will enable the manufacturing of hollow products with complex internal geometries, such as tee-joints, with improved dimensional accuracy and efficient core removal.
5. Research Methodology
Research Design:
The research employs an experimental design based on the Taguchi method to optimize the water-soluble core formulation and processing parameters. The study involves fabricating water-soluble cores with varying compositions and under different processing conditions, followed by mechanical testing and evaluation of the resulting molded products. A tee-joint product was chosen as a demonstrator for the proposed method.
Data Collection Method:
Data was collected through the following methods:
- Compression Test: Compressive strength of the water-soluble cores was measured using a "HongTa testing machine (HT-2402, Taichung, Taiwan)" according to ASTM D695-15 and C473-15 standards. Specimens were cylindrical with dimensions of "35 mm × 35 mm in diameter and height".
- Dimensional Measurement: The geometrical accuracy of the molded tee-joint products was evaluated using a "coordinate measuring machine (Brown & Sharpe Co., Ltd., Inspector classic, North Kingston, RI, USA)". Eccentricity of the internal contour was calculated to quantify dimensional accuracy.
- Core Removal Rate Measurement: The core removal rate was determined by measuring the conductivity change of a water bath as the salt core dissolved, using a "conductivity meter (DFRobot SEN0244)", "TDS (total dissolved solids) probe", and a "data acquisition board (DFRduino UNO R3)".
Analysis Method:
The collected data was analyzed using:
- Taguchi Method: An "L9(34) orthogonal array" was used to design experiments and determine the optimal parameters for core preparation. "S/N ratio" and "ANOVA" were employed to analyze the results and identify significant factors.
- Eccentricity Calculation: Eccentricity was calculated using equations (2) and (3) to quantify the deviation of the internal contour from a perfect circle.
- Core Removal Rate Calculation: Core removal rate was calculated using equation (4), based on conductivity measurements.
Research Subjects and Scope:
The research focused on:
- Materials: Water-soluble core material composed of "NaCl (salt)" and "trehalose sugar (binder)", and "acrylonitrile butadiene styrene (ABS, POLYLAC PA-757, from CHIMEI Corp., Taipei, Taiwan)" for the shell and skin layer.
- Product: A tee-joint with a specific internal contour as shown in "Figure 3".
- Process Parameters: Binder content, applied pressure, processing time, and processing temperature for core preparation, and molding parameters for shell and skin layer injection molding as listed in "Table 2".
6. Main Research Results:
Key Research Results:
- Optimal Core Parameters: The Taguchi method identified the optimal parameters for water-soluble core preparation as "A3B3C2D3", corresponding to specific levels of binder content, applied pressure, processing time, and processing temperature.
- Compressive Strength: The optimal core achieved a compressive strength of "3.2 MPa", a "17.2% improvement compared to the maximum strength of Exp. No. 5 listed in Table 3". The proposed product can be "molded successfully when the compressive strength of the core is larger than 2 MPa".
- Dimensional Accuracy Improvement: The eccentricity measurement of the internal contour of the optimal sample showed a "56% improvement" compared to samples made with non-optimal parameters. The eccentricity was reduced from "26.3% to 11.5%".
- Core Removal Time: The required time for core removal for the optimal core was "less than 154 s".
Analysis of presented data:
- Figure 7 presents "Compressive-stress-and-strain curves for salt core with respect to setting parameters", showing the compressive strength of cores prepared with different parameter combinations.
- Figure 9 shows "The eccentricity measurement of internal contour of samples", comparing the eccentricity of the optimal sample with a destroyed sample across five locations. The optimal sample exhibits lower eccentricity values in most locations.
- Figure 10 illustrates "(a) Core removal rate of the lowest strength group and (b) core removal rate of the highest strength group", showing the dissolution rate of cores with different compressive strengths. Higher strength cores take longer to dissolve.
Figure Name List:
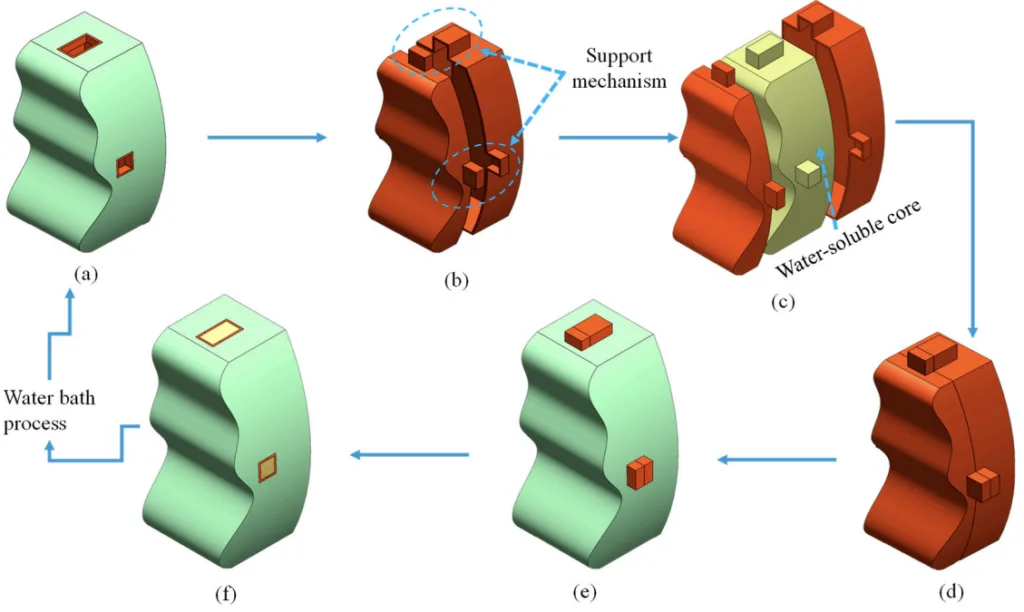
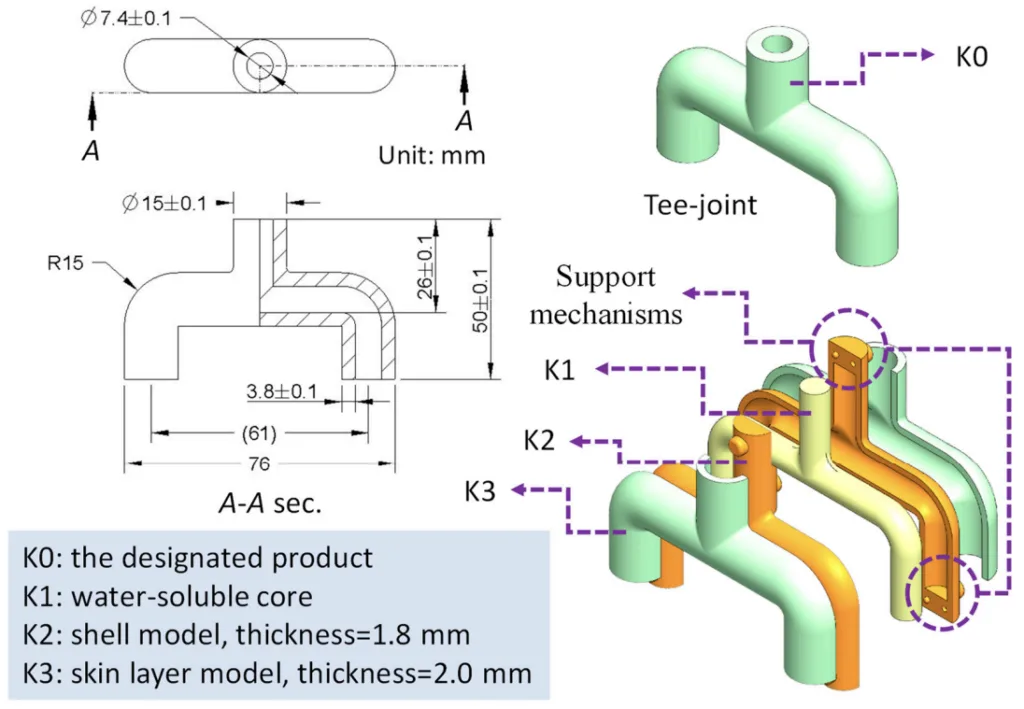
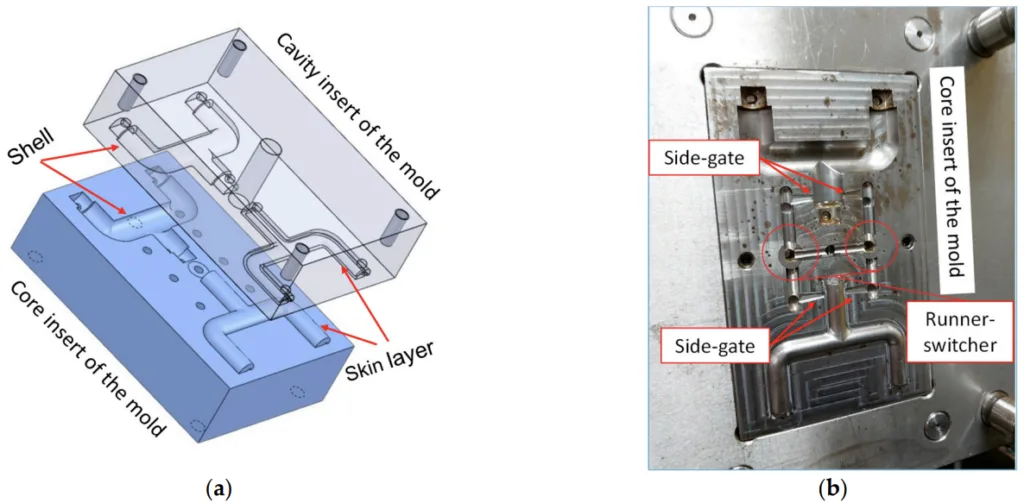
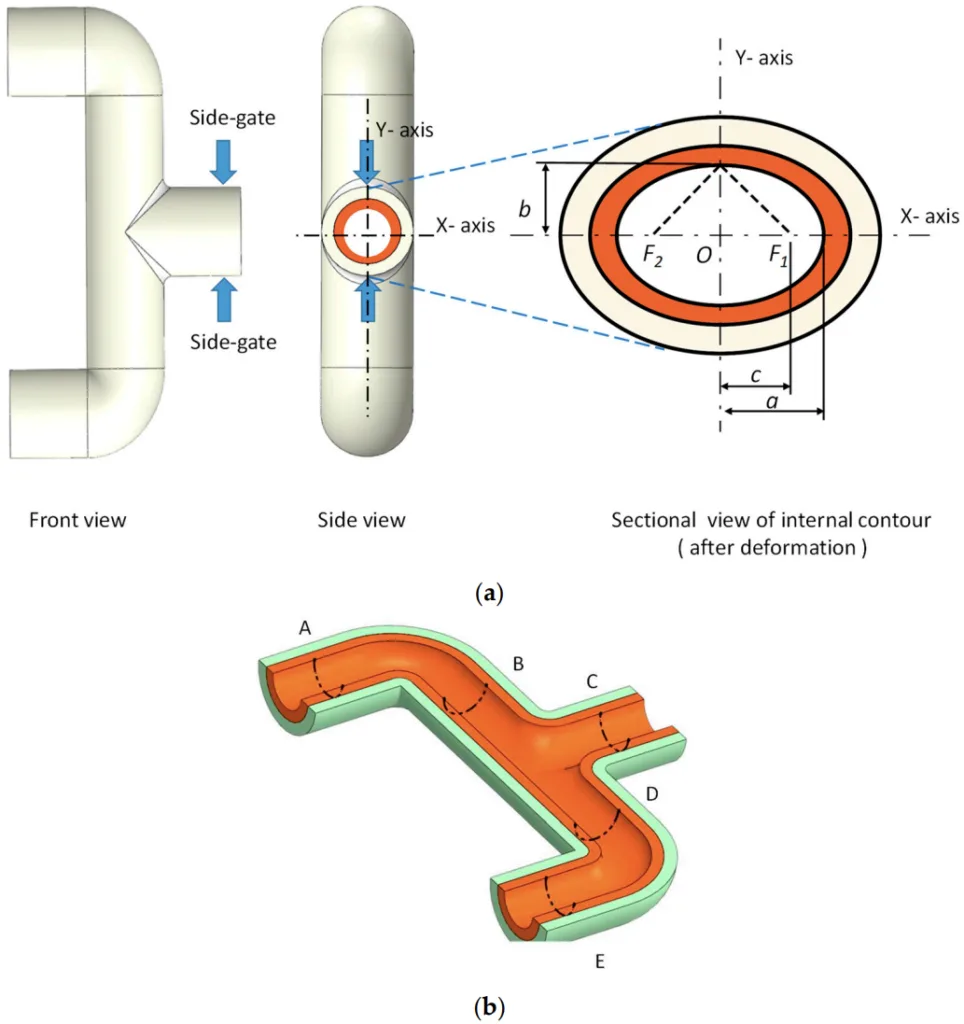
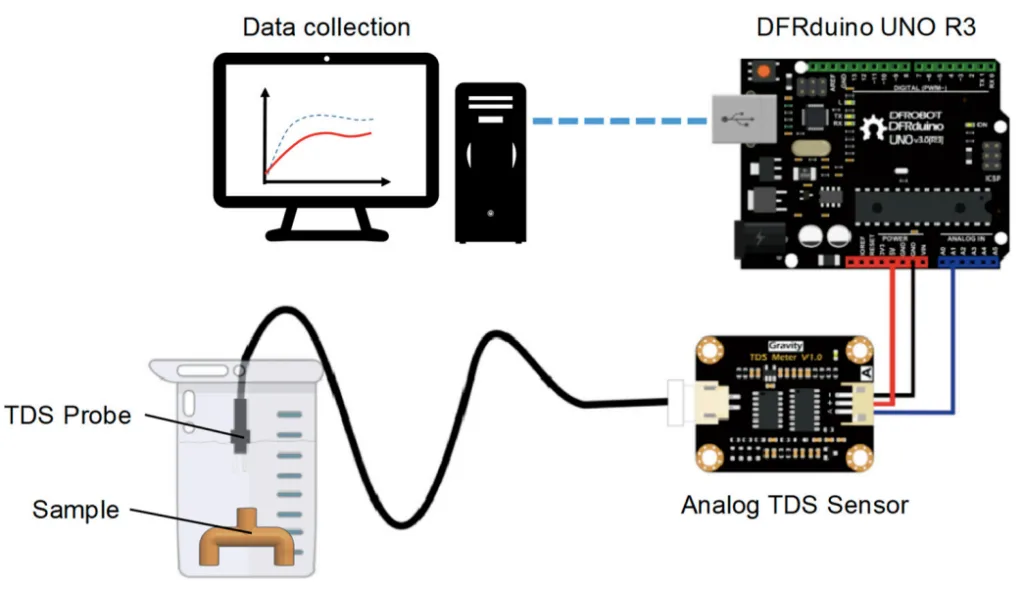
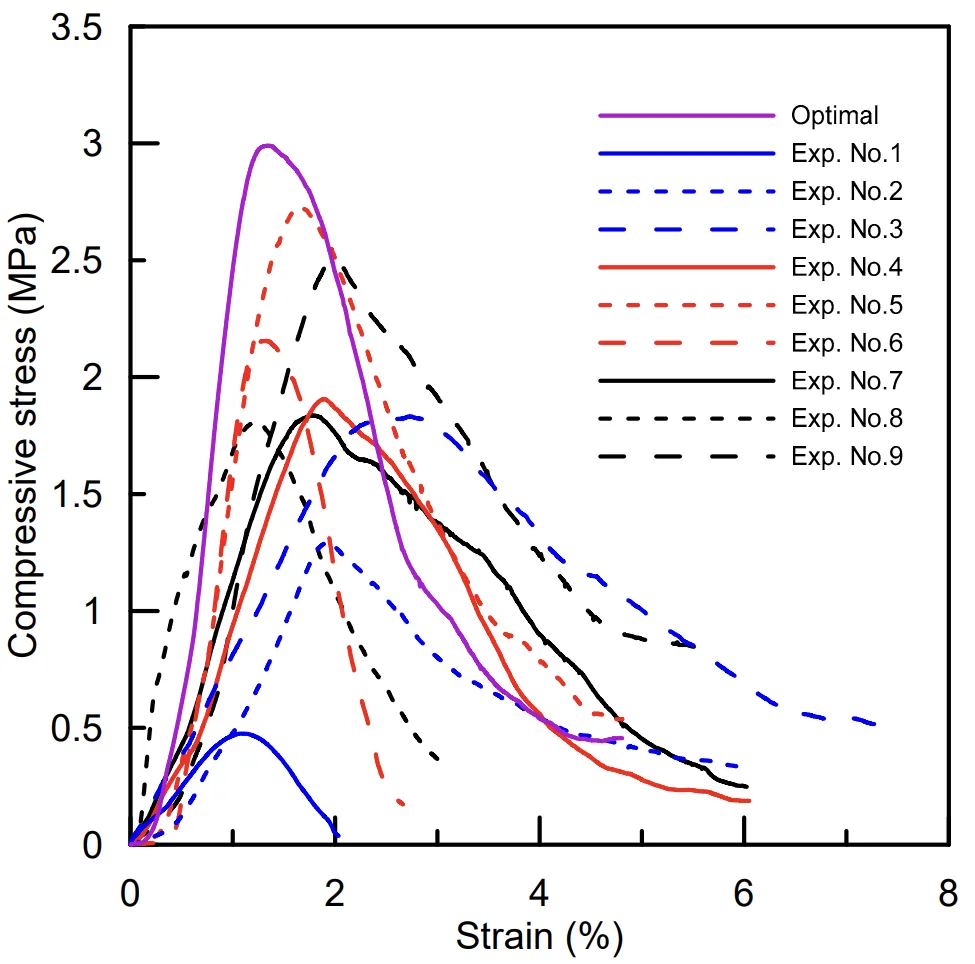
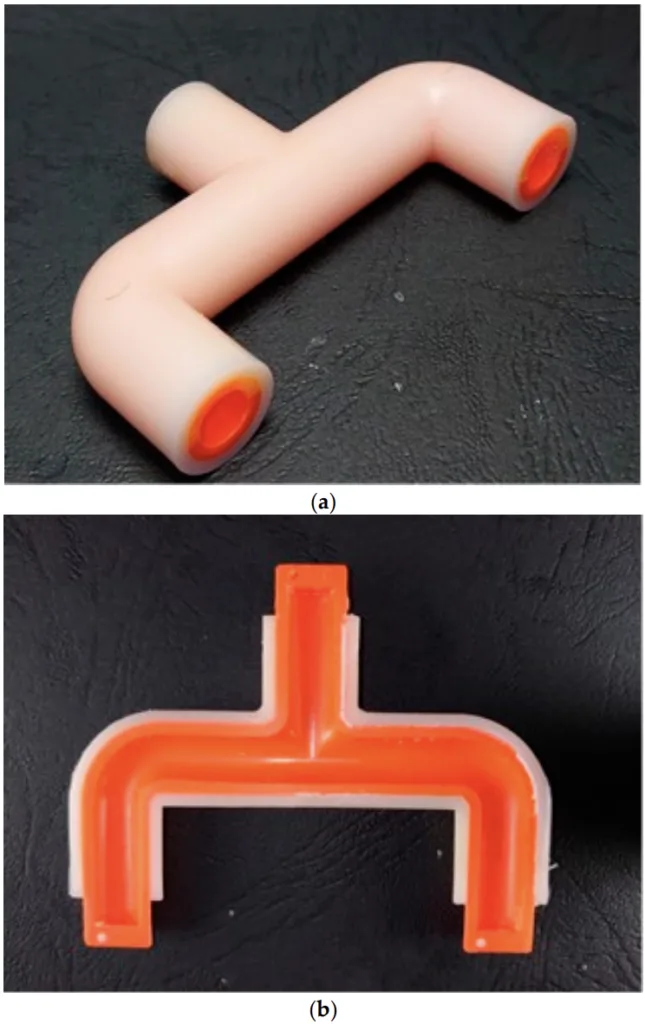
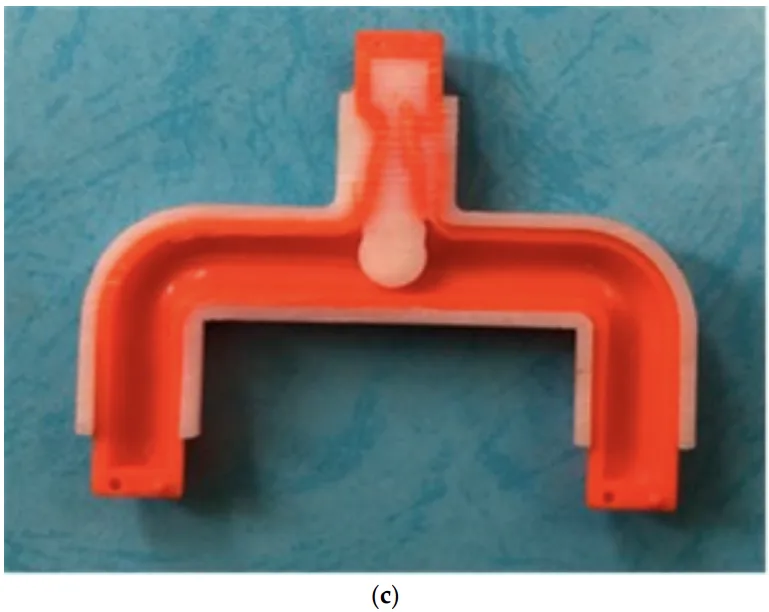
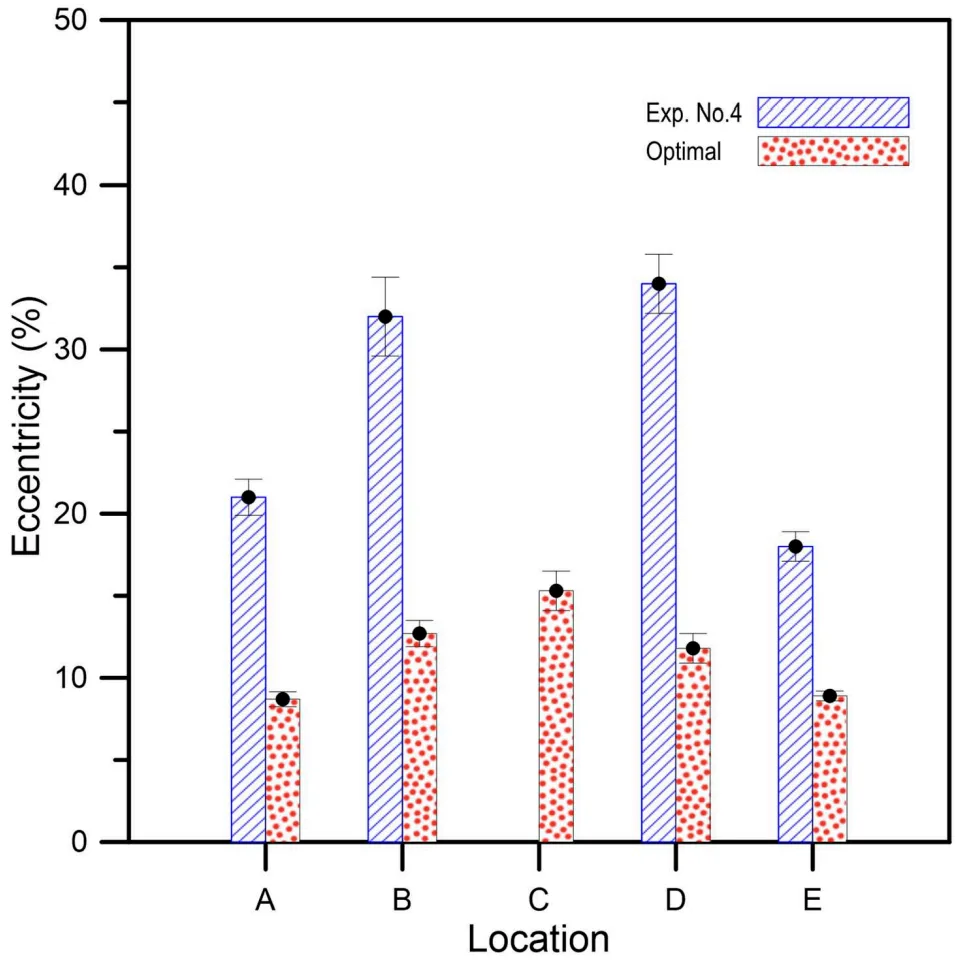
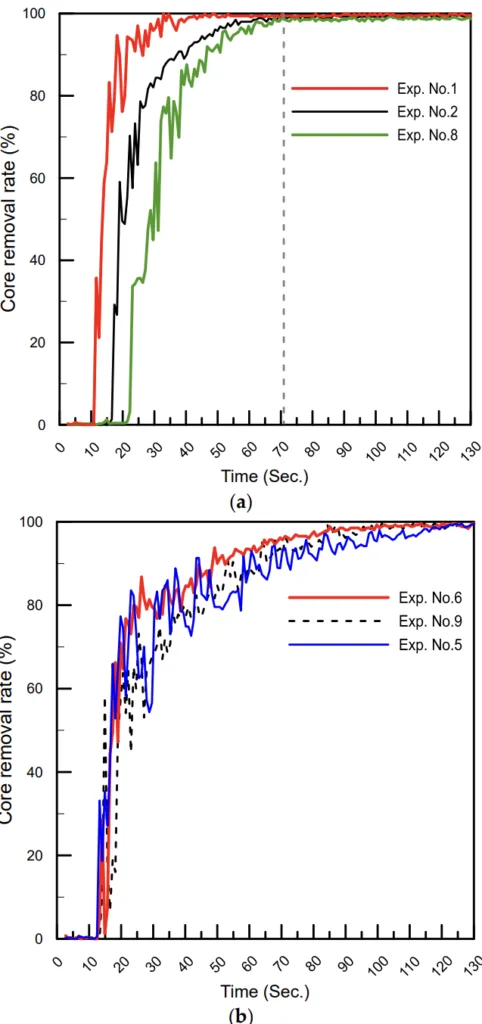
- Figure 1. Preparation procedures to produce a hollow product by using water-soluble core and (a) shell (b): the water-soluble core with a shell is prepared; (c) the enveloped core is prepared by two core shells and located in the mold cavity, (d) the skin layer is molded, (e) the product ejected from the mold, (f) the ends are cut out of the enveloped core, (g) the product is immersed into a water bath and core dissolution, and (h) the final product is obtained.
- Figure 2. Schematic illustration of design flow: (a) the designated product, (b) two halves of the shell model generated from the internal contour of the product, (c) the sketch of the core assembled into the shells, (d) the enveloped core, (e) the skin model covers the core entirely, and (f) cut out the support mechanism.
- Figure 3. Schematic drawing of the designated tee-joint (K0), the core (K1), the shell model (K2), and skin layer model (K3).
- Figure 4. (a) Sketch of the core and cavity inserts, and (b) the half side of the test mold.
- Figure 5. (a) Eccentricity measurement of the molded product and (b) five locations defined for each sample measurement.
- Figure 6. The schematic illustration of the core removal rate measurement.
- Figure 7. Compressive-stress-and-strain curves for salt core with respect to setting parameters.
- Figure 8. Cont.
- Figure 9. The eccentricity measurement of internal contour of samples.
- Figure 10. (a) Core removal rate of the lowest strength group and (b) core removal rate of the highest strength group.
7. Conclusion:
Summary of Key Findings:
The research successfully demonstrated a novel method for manufacturing hollow injection-molded products using an enveloped water-soluble core. The key findings are: (1) The enveloped core concept, combining a water-soluble core and a shell, enables injection molding of complex hollow parts. (2) Optimization using the Taguchi method identified optimal parameters for core preparation, resulting in enhanced compressive strength. (3) The proposed method significantly improved dimensional accuracy, reducing eccentricity by 56%. (4) The core removal process is efficient, with a dissolution time of less than 154 seconds for the optimal core.
Academic Significance of the Study:
This study contributes to the field of injection molding by introducing and validating the enveloped water-soluble core concept. It expands the applicability of water-soluble cores from low-pressure to high-pressure molding processes. The research provides valuable insights into the material composition and processing parameters for water-soluble cores, optimized for injection molding applications. The use of the Taguchi method for core optimization and the detailed evaluation of dimensional accuracy and core removal rate add to the academic rigor and practical relevance of the study.
Practical Implications:
The proposed method offers a practical alternative to existing techniques for manufacturing complex hollow plastic parts. It overcomes limitations associated with fusible cores, such as resin type restrictions and high capital investment. The use of readily available and inexpensive materials (salt and sugar) for the core, combined with lower energy consumption and ease of implementation, makes this method industrially attractive. It can be applied to manufacture products with special internal contours, such as intake manifolds, in a cost-effective and environmentally conscious manner. The efficient core removal process further enhances its practical utility.
Limitations of the Study and Areas for Future Research:
The paper does not explicitly state limitations or future research areas within the conclusion section. However, based on the research, potential limitations and future research directions could include:
- Further investigation into the range of applicable polymers for the shell and skin layer. While ABS was used in this study, exploring compatibility with other engineering plastics would broaden the method's applicability.
- Exploring the scalability of the process for mass production. The current study demonstrates feasibility on a lab scale; further research is needed to optimize the process for high-volume manufacturing.
- Investigating the reusability and recycling of the shell material and the potential for salt and sugar recovery from the waste solution to further enhance environmental sustainability.
- Exploring more complex product geometries beyond the tee-joint to fully demonstrate the versatility of the enveloped core method.
- Further optimization of the core removal process to reduce dissolution time and water consumption.
8. References:
- [1] Dorp, E.R.; Blume, C.; Haedecke, T.; Pata, V.; Reith, D.; Bruch, O.; Möginger, B.; Hausnerova, B. Process-dependent structural and deformation properties of extrusion blow molding parts. Polym. Test. 2019, 77, 105903.
- [2] Rodríguez-Castellanos, W.; Martínez-Bustos, F.; Rodrigue, D.; Trujillo-Barragán, M. Extrusion blow molding of a starch-gelatin polymer matrix reinforced with cellulose. Eur. Polym. J. 2015, 73, 335–343.
- [3] Mikhail Katsevman, M.; Pavlov, A.; Kruglov, P. Production of thermoplastic compound materials for processing by injection molding, blow molding and extrusion. Reinf. Plast. 2018, 62, 318–321.
- [4] Stevenson, J.F. Innovation in Polymer Processing: Molding; Carl Hanser Verlag: Munich, Germany, 1996.
- [5] Yaagoubi, M.E.; Haas, S.; Schwegler, D. The magnetic orientation of hard ferrites rubber bonded permanent magnets using the injection moulding. Sens. Actuators A Phys. 2021, 230, 112571.
- [6] Klein, R. Laser Welding of Plastics: Materials, Processes and Industrial Applications; John Wiley & Sons: Hoboken, NJ, USA, 2012.
- [7] Ettemeyer, F.; Schweinefuß, M.; Lechner, P.; Stahl, J.; Greß, T.; Kaindl, J.; Durach, L.; Volk, W.; Günther, D. Characterisation of the decoring behaviour of inorganically bound cast-in sand cores for light metal casting. J. Mater. Process. Technol. 2021, 296, 117201.
- [8] Kohlstädt, S.; Vynnycky, M.; Goeke, S. On the CFD Modelling of Slamming of the Metal Melt in High-Pressure Die Casting Involving Lost Cores. Metals 2021, 11, 78.
- [9] Jelínek, P.; Adámková, E. Lost cores for high-pressure die casting. Arch. Foundry Eng. 2014, 14, 101–104.
- [10] Kaerger, J.; Atz, L. Water soluble mandrels for lost core applications in manufacturing of hollow composite structures. In Proceedings of the SAMPE Europe Conference Nantes, Nantes, France, 17-19 September 2019.
- [11] Xiao, Z.; Harper, L.T.; Kennedy, A.R.; Warrior, N.A. A water-soluble core material for manufacturing hollow composite sections. Compos. Struct. 2017, 182, 380–390.
- [12] Osswald, T.A.; Turng, L.-S.; Gramann, P. Injection Molding Handbook; Carl Hanser Verlag: Munich, Germany, 2008.
- [13] McNulty, J.D.; Kharbas, H.; Thompson, C.; Ashton, R.S.; Turng, L.S. A method to create internal geometries within injection molded parts using water soluble Polyvinyl alcohol (PVOH) inserts. In Proceedings of the ANTEC Conference Orlando, Orlando, FL, USA, 23-25 March 2015.
- [14] Salzmann, M.; Blößl, Y.; Todorovic, A.; Schledjewski, R. Usage of Near-Infrared Spectroscopy for Inline Monitoring the Degree of Curing in RTM Processes. Polymers 2021, 13, 3145.
- [15] Bhudolia, S.K.; Perrotey, P.; Gohel, G.; Joshi, S.C.; Gerard, P.; Leong, K.F. Optimizing Bladder Resin Transfer Molding Process to Manufacture Complex, Thin-Ply Thermoplastic Tubular Composite Structures: An Experimental Case Study. Polymers 2021, 13, 4093.
- [16] Bargaoui, H.; Azzouz, F.; Thibault, D.; Cailletaud, G. Thermomechanical behavior of resin bonded foundry sand cores during casting. J. Mater. Process. Technol. 2017, 246, 30-41.
- [17] Sussich, F.; Urbani, R.; Princivalle, F.; Cesàro, A. Polymorphic amorphous and crystalline forms of trehalose. J. Am. Chem. Soc. 1998, 120, 7893-7899.
- [18] Kan, Z.; Yan, X.; Ma, J. Conformation dynamics and polarization effect of α, α-Trehalose in a vacuum and in aqueous and salt solutions. J. Phys. Chem. A 2015, 119, 1573–1589.
- [19] Yanykin, D.V.; Khorobrykh, A.A.; Semenov, A.Y.; Mamedov, M.D. Effect of Trehalose on the Functional Properties of Photosystem II. In Allakhverdiev, Photosynthesis: Molecular Approaches to Solar Energy Conversion, Proceedings of the Advances in Photosynthesis and Respiration; Shen, J.R., Satoh, K., Eds.; Springer: Cham, Switzerland, 2021; Volume 47.
9. Copyright:
- This material is "Chung-Chih Lin and Chao-Long Yang"'s paper: Based on "A Water-Soluble Core for Manufacturing Hollow Injection-Molded Products".
- Paper Source: https://doi.org/10.3390/polym14112185
This material was summarized based on the above paper, and unauthorized use for commercial purposes is prohibited.
Copyright © 2025 CASTMAN. All rights reserved.