This introductory paper is the research content of the paper "Optimizing Design of High Efficiency Induction Motor Considering Cost Effect" published by IEEE.

1. Overview:
- Title: Optimizing Design of High Efficiency Induction Motor Considering Cost Effect
- Author: P-W. Han, U-J. Seo, J-H. Choi, Y-D.Chun, D-H. Koo, J. Lee, W-G. Lee
- Publication Year: Not specified in the provided document.
- Published Journal/Society: IEEE (Based on references and context)
- Keywords: Induction Motor, Optimization, Genetic Algorithm, Efficiency, Material Cost, Multi-objective Design
2. Abstract
The characteristics of an induction motor vary with the number of parameters and the performance relationship between the parameters also is implicit. In case of the induction motor design, we generally should estimate many objective physical quantities in the optimization procedure. In this article, the multiobjective design optimization based on genetic algorithm is applied for the three phase induction motor. The efficiency, starting torque, and material cost are selected for the objectives. The validity of the design results is also clarified by comparison between calculated results and measured ones.
3. Research Background:
Background of the research topic:
Electric motors consume over half of all electricity, driving the need for energy conservation and increased motor efficiency [1].
Status of previous research:
Previous research includes methods like "boundary search along active constrains" [3] and Nonlinear analytical iterative field field-circuit model (AIM) [4]. Extensive research exists on multi-objective optimization using evolutionary algorithms.
Need for research:
While technologies like copper die-casting and low-loss electrical steel improve efficiency, they increase costs and require specialized manufacturing [2]. There's a need for optimization methods that balance efficiency gains with cost-effectiveness.
4. Research purpose and research question:
Research purpose:
To optimize the design of a three-phase induction motor for high efficiency while minimizing material cost.
Core research:
Applying a Multi-Objective Genetic Algorithm (NSGA-II) to optimize induction motor design, considering efficiency, starting torque, and material cost.
5. Research methodology
The research employs a multi-objective optimization approach using the NSGA-II genetic algorithm [5,6]. The design is based on the equivalent circuit method and the D²L sizing equation.
- Research Design: Multi-objective optimization using NSGA-II.
- Data Collection: Design parameters and performance characteristics are calculated using the D²L equation and equivalent circuit method. Experimental data is collected from a prototype.
- Analysis Method: NSGA-II algorithm for optimization, comparing simulation results with experimental data.
- Research Scope: Three-phase induction motor design.
- Design Variables: Output coefficient (Co), air gap flux density (Bg), teeth and yoke flux density ratio (Gt, Gc), current density (J) (Table I). The scope of Gt, Gc and J are described in Table II.
- Constraints: Starting torque/rated torque > 200%, power factor > 0.85.
- Objective Functions: Maximize efficiency, minimize material cost (excluding frame, shaft, and bearings).
6. Key research results:
Key research results and presented data analysis:
- The NSGA-II algorithm generated a set of non-dominated solutions, showing a trade-off between efficiency and material cost (Figure 2).
- Optimum III model was selected for the prototype due to its lower cost in the higher efficiency region.
- Optimum III achieved a 6.4% reduction in material cost at the target efficiency of 93.5% compared to the base model, primarily due to a smaller slot area and lower copper weight (Table III).
- The Stator Core Shape of Base model, Optimum I, II and III are described in Figure 1.
- The simulation result of GA is described in Figure 2.
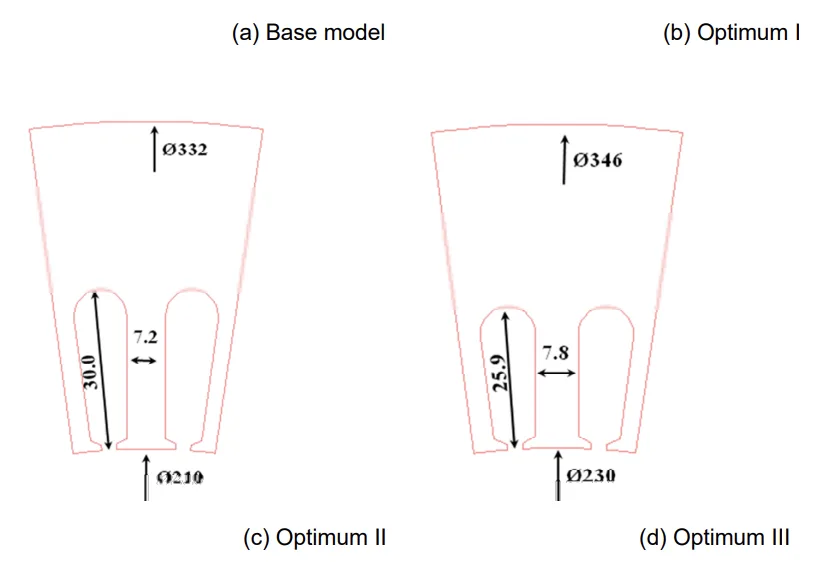
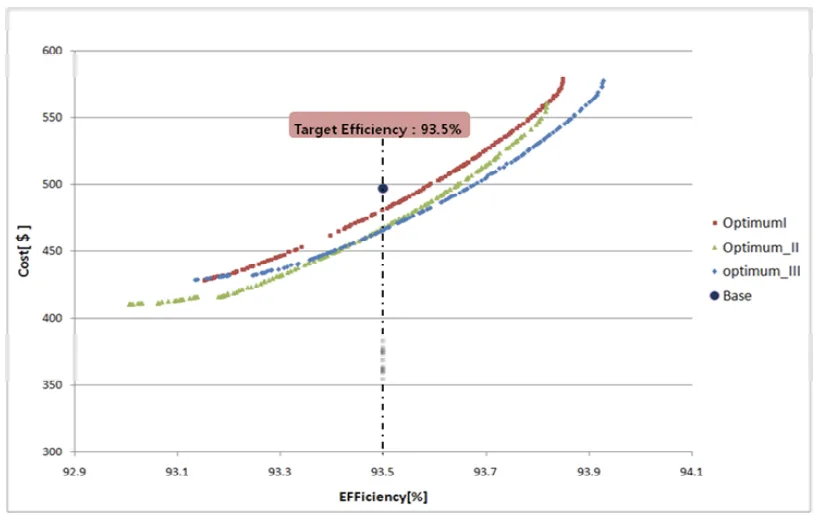
List of figure names:
- Figure 1. Stator Core Shape
- Figure 2. GA Simulation Results
- Figure 3. Core and Rotor Assembly for prototype
- Figure 4. Test and Simulation Results of Efficiency
7. Conclusion:
Summary of key findings:
The research successfully demonstrates the use of a Multi-Objective Genetic Algorithm (NSGA-II) to optimize the design of a three-phase induction motor. The optimized design (Optimum III) achieved the target efficiency (93.5% in simulation, 93.3% in testing) while reducing material cost by 6.4% compared to the base model. Test efficiency satisfies high efficiency level (93.0%) at 50%, 75%, 100% and 110% output power (Figure 4).
Academic significance of the research:
Provides a practical application of NSGA-II for multi-objective optimization in electrical machine design.
Practical implications of the research:
The design process can be used to develop more efficient and cost-effective induction motors, contributing to energy conservation efforts.
8. References:
- [1] M. Deivasahayam, “Energy Conservation through Efficiency Improvement in Squirrel Cage Induction Motors by Using Copper Die Cast”, International Conference of energy efficiency in motor driven systems (eemods'05), Vol. I, pp.92-101, September 2005, Heidelberg, Germany.
- [2] J. Haataja, J. Pyrhonen, “Improving three-phase induction motor efficiency in Europe”, Power Engineering Journal, Vol. 12, pp. 81-86, 1998
- [3] J. Appelbaum, E. F. Fuchs, and J. C. White, “Optimization of three-phase induction motor design", IEEE Trans. Energy Conversion, Vol. EC-2, PP. 407-422, Sept. 1987
- [4] G. Madescu, I. Bolea, and T. J. E. Miller, "An analytical iterative model (AIM) for induction motor design", in conf. Rec. IEEE-IAS Annu. Meeting, San Diego, CA, vol. I, pp. 556-583, 1996.
- [5] K. Deb, A. Pratap, S. Agarwal, and T. Meyarivan, “A Fast and Elitist Multiobjective Genetic Algorithm: NSGA-II” IEEE Trans. Evol. Comput., Vol. 6, pp. 182–197, April, 2002.
- [6] K. Deb, A. Anand, and D. Joshi, “A Computationally Efficient Evolutionary Algorithm for Real-Parameter Optimization,” Evol. Comput., Vol. 10, No. 4, pp. 371–395, Winter, 2002.
- [7] V. B. Honsinger, “Sizing equations for electrical machinery,” IEEE Trans. on Magnetics, vol. EC-2, no. 1, pp. 116-121, March, 1987.
- [8] IEEE Std. 112, “IEEE Standard Test Procedure for Polyphase Induction Motors and Generators," 2004.
- [9] IEC 60034-2-1, "Standard methods for determining losses and efficiency from tests(excluding machines for traction vehicles" 2007
9. Copyright:
- This material is a paper by "P-W. Han, U-J. Seo, J-H. Choi, Y-D.Chun, D-H. Koo, J. Lee, W-G. Lee": Based on "Optimizing Design of High Efficiency Induction Motor Considering Cost Effect".
- Source of paper: Not provided in the document.
This material was created to introduce the above paper, and unauthorized use for commercial purposes is prohibited. Copyright © 2025 CASTMAN. All rights reserved.