This introduction paper is based on the paper "Optimisation of Casting parameters of Squeeze cast LM-24 Al-Si Alloy" published by "International Journal of Engineering Research & Technology (IJERT)".
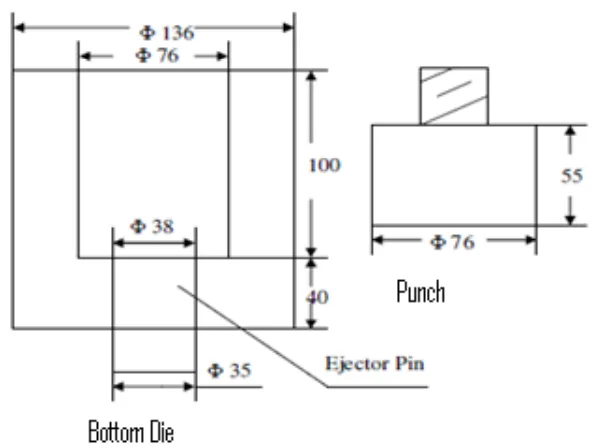
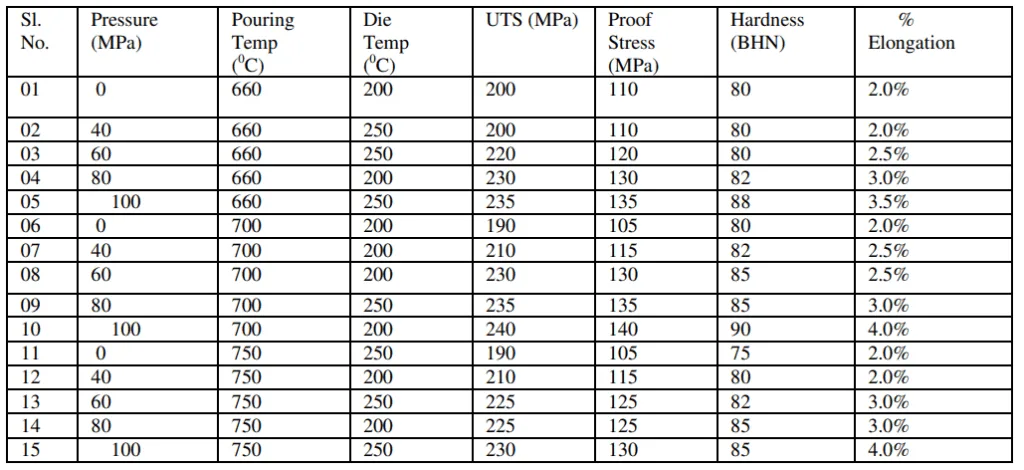
1. Overview:
- Title: Optimisation of Casting parameters of Squeeze cast LM-24 Al-Si Alloy
- Author: Dr. Susanta Gangopadhyay
- Year of publication: 2014
- Journal/academic society of publication: International Journal of Engineering Research & Technology (IJERT)
- Keywords: Squeeze casting; Process parameters; Aluminium alloy.
2. Abstract:
The conventional die casting employs metal flow with high gate velocity resulting in nonlaminar fluid flow affecting the quality of the cast product. A potential defect, commonly found in conventionally die cast components is porosity attributed to solidification shrinkage and gas entrapment. The high integrity die casting processes like Squeeze casting, and semi-solid casting( like Thixocasting and Rheocasting [1]) have been developed. Squeeze casting, however, is a simpler process than semisolid and will be more economical. The Squeeze casting process utilizes relatively slow feeding velocity of the melt into the die and application of high pressure during solidification. Investigation reveals that slower injection speed causes less turbulence and less retention of air and the applied pressure during solidification eliminates shrinkage and gas porosity, decreases thermal resistance and accelerates solidification effecting improvement in microstructure and mechanical properties of the cast material. The suitability of the process for light weight non-ferrous metal alloys has made increasing demand for this emerging process for automobile and aerospace industry.
A study of the Direct squeeze casting process was conducted on aluminiun-silicon alloy LM-24 with 9% Si. LM- 24 is essentially a widely used pressure die casting aluminium alloy with excellent casting characteristics suitable for thin walled casting .The experimental design and the parameters has been organized with variation of pressure, pouring temperature and die temperature.
The result shows increase of density of squeeze cast material indicating near elimination of porosity, improvement of surface finish, improvement in microstructure and increase in hardness and tensile strength. The feed rate is controlled to a lower value to avoid turbulence. For LM-24 aluminium alloy a pouring temperature of 700°C, die temperature of 200°C and a pressure of 100 MPa is found to be the optimum combination for better mechanical properties.
3. Introduction:
The art of metal forming by casting dates back to 4000 years BC, with pressure die casting emerging in the early 1820s. Initial methods were mechanical, later evolving to pneumatic and hydraulic systems, significantly progressing with the development of the cold chamber process in the 1920s. The idea of Squeeze casting, applying pressure to solidifying metal, was originated as early as 1878 by Chernov. The first scientific squeeze casting experiment was carried out in Germany in 1931 by G. Welter on Al-Si alloy, who was later joined by V. M. Plyatskii in 1937. The bulk of work in the West has focused on Aluminium alloys, copper alloys, and magnesium alloys.
The Squeeze casting process utilizes a relatively slow feeding velocity of the melt into the die and the application of high pressure during solidification. There are two main variants:
- Direct Squeeze casting: Pressure is applied on the entire surface of the liquid metal. In this method, a pre-measured quantity of molten metal is poured directly into an open die. The upper die is then lowered, forcing the molten metal under pressure into the cavity. After the metal has solidified, the upper die is lifted and the cast product is ejected. Figure 1 depicts the stages of direct squeeze casting: (a) Molten Metal Pouring, (b) Pressurising, (c) Lifting of top die, (d) Ejection.
- Indirect Squeeze casting: Pressurisation is done through a plunger.
4. Summary of the study:
Background of the research topic:
Conventional die casting processes, characterized by high gate velocities and nonlaminar fluid flow, often lead to defects such as porosity from solidification shrinkage and gas entrapment. To overcome these limitations, high integrity die casting processes like Squeeze casting and semi-solid casting (e.g., Thixocasting and Rheocasting [1]) have been developed. Squeeze casting is presented as a simpler and more economical alternative, particularly suitable for producing high-quality, lightweight non-ferrous alloy components for the automobile and aerospace industries.
Status of previous research:
The concept of squeeze casting has been known since 1878, with systematic scientific investigations commencing in the 1930s. Previous research has largely concentrated on aluminium, copper, and magnesium alloys. It has been established that the process, involving slow melt feeding and high-pressure application during solidification, can reduce turbulence, air entrapment, and porosity, thereby enhancing the microstructure and mechanical properties of cast components.
Purpose of the study:
The primary purpose of this study was to investigate and optimize the parameters of the Direct squeeze casting process for aluminium-silicon alloy LM-24 (containing 9% Si). The research aimed to determine the optimal combination of applied pressure, pouring temperature, and die temperature to achieve improved mechanical properties in the cast LM-24 alloy.
Core study:
The core of the study involved an experimental investigation into the Direct squeeze casting of LM-24 aluminium alloy. The experimental design focused on systematically varying key process parameters: applied pressure (0, 40, 60, 80, 100 MPa), pouring temperature (660°C, 700°C, 750°C), and die temperature (200°C, 250°C). The influence of these variations on the resulting surface finish, mechanical properties (including Ultimate Tensile Strength, Proof Stress, Percentage Elongation, and Hardness), and microstructure of the cast alloy was thoroughly evaluated to identify the optimum processing conditions.
5. Research Methodology
Research Design:
The study utilized a direct squeeze casting process. The material investigated was Aluminium-Silicon alloy LM-24 (BS1490:1988), containing 9% Si, with its detailed composition provided in Table-1. Melting of the alloy was performed in a crucible furnace with electrical resistance heating (maximum temperature 1200°C), under an inert atmosphere created by injecting industrial argon gas to prevent oxidation. A comprehensive direct squeeze casting machine, depicted schematically in Figure-2, with a capacity of 50 T (eject cylinder capacity 25 T), was employed. This machine included facilities for die heating, pressurization during solidification, and ejection of the cast product. The die and punch, shown in Figure-3, were fabricated from hardened steel EN24 and coated with Molybdenum sulphide (MoS2). Die preheating to temperatures of 200°C or 250°C was accomplished using a portable electric heater with a digital temperature controller.
Data Collection and Analysis Methods:
A pre-measured quantity of molten LM-24 alloy was poured into the lower die cavity. Prior to pouring, the melt surface was treated with a mixture of boric acid and sulphur to prevent spontaneous oxidation, and the melt was skimmed to remove oxides and impurities.
- Temperature Measurement: 'K' type chromel alumel thermocouples, inserted in the mould wall and mould cavity, were connected to a data logger for measuring mould and molten metal temperatures.
- Mechanical Properties: Tensile properties (Ultimate tensile strength, Proof stress, Percentage Elongation) were determined using a Hounsfield Tensometer on test specimens with a 6.5 mm diameter. Hardness was measured using a Brinell hardness test machine. Surface finish was quantified in terms of RMS value.
- Metallographic Properties: Samples cast under different parameters were mechanically polished, with the final polish achieved using 0.5-micron alumina powder suspended in distilled water and diamond paste. After etching, the microstructure was observed and photographed using an electron microscope.
Research Topics and Scope:
The research focused on the optimisation of casting parameters for the direct squeeze casting of LM-24 Al-Si alloy. The scope of the study encompassed:
- Investigation of the effects of varying squeeze pressure (ranging from 0 MPa for gravity casting to 100 MPa).
- Assessment of different pouring temperatures (660°C, 700°C, 750°C).
- Evaluation of die preheating temperatures (200°C, 250°C).
- Analysis of the impact of these parameter variations on the surface finish, mechanical properties (tensile strength, proof stress, elongation, hardness), and microstructure of the cast LM-24 alloy.
- Determination of the optimum combination of these process parameters to achieve enhanced mechanical properties.
6. Key Results:
Key Results:
The study found that increasing the applied pressure in squeeze casting leads to a better surface finish for the LM-24 alloy products, with the highest quality observed at 100 MPa, as detailed in Table-2 regarding RMS values.
Mechanical properties, including UTS, Proof Stress, Hardness, and % Elongation, were significantly improved in squeeze cast specimens compared to gravity cast ones (0 MPa pressure). The optimum combination of parameters for LM-24 aluminium alloy was identified as a pouring temperature of 700°C, a die temperature of 200°C, and an applied pressure of 100 MPa. Under these conditions, the alloy exhibited a UTS of 240 MPa, a Proof Stress of 140 MPa, a Hardness of 90 BHN, and a % Elongation of 4.0% (Table-3). The percentage improvement in these properties at 100 MPa pressure across different pouring temperatures is graphically represented in Figure-4.
Microstructural analysis revealed that the application of pressure during solidification affects phase relationships by increasing the freezing temperature (as per the Clausius-Clapeyron equation ΔTf/ΔP = Tf (Vl−Vs) / ΔHf) [2]. This, along with the reduction/elimination of the air gap between the molten metal and die wall, increases heat-transfer coefficients, leading to a greater cooling rate and consequently a finer grain size [5]. Figure-5 provides a visual comparison, showing noticeable grain refinement in the squeeze cast LM-24 alloy (produced at 100 MPa pressure and a pouring temperature of 700°C) compared to the gravity die cast sample.
Figure Name List:
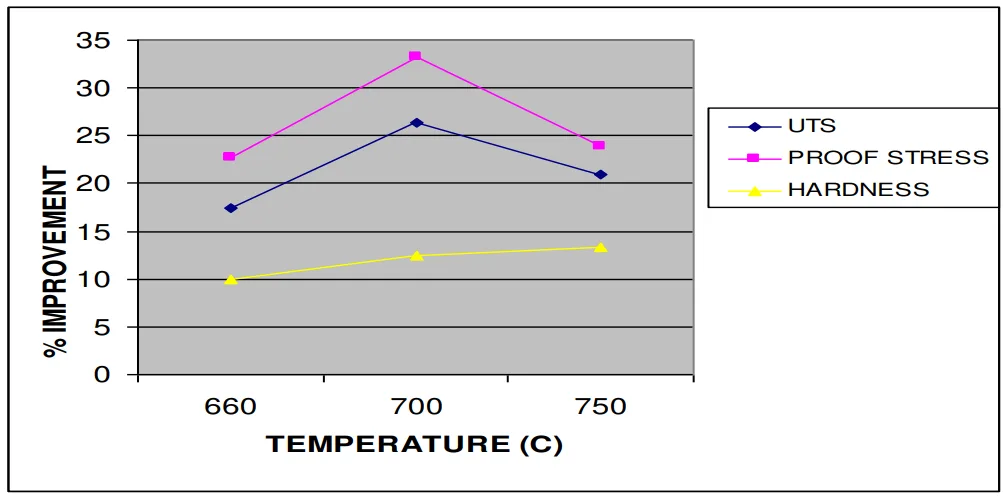
- Figure 1: depicts the stages of direct squeeze casting.
- Figure-2: shows a schematic diagram of Squeeze casting m/c.
- Figure-3: (Shows die and punch, made from hardened steel EN24, with dimensions)
- Figure-4: % improvement of UTS, Proof stress and Hardness at 100 MPa pressure (from '0' pressure) against pouring temperature.
- Figure-5: gives a comparison of the microstructure of gravity die cast and squeeze casting at100 MPa pressure and pouring temp of 700° C.
7. Conclusion:
The squeeze-casting process has proven to be an ideal method for producing near net-shape, high-quality engineering components, particularly for the automobile and aerospace industries, using both conventionally-cast and wrought-alloy compositions [3]. The direct squeeze casting method results in better pressurization compared to the indirect squeeze casting process.
Key findings and advantages highlighted include:
- Slower injection speed causes less turbulence and less retention of air.
- The combination of high pressure and a metal mould in squeeze casting leads to a high heat transfer coefficient [9], which in turn leads to refinement of microstructure and thereby improvement in mechanical properties.
- Density of squeeze cast material increases, indicating near elimination of porosity.
- Achievement of near net shape and improvement of surface finish.
- Squeeze casting can be carried out without feeding systems like runners, gates, and shrinkage compensating units like risers, resulting in high yield with almost no scrap for recycling.
- Fluidity or castability is not very important because the filling of the dies is achieved by pressurisation.
The thermal limitation of the die material means the squeeze casting process should be kept limited to lower melting point alloys like aluminium and magnesium. Pouring temperature affects fluidity; while higher temperatures increase fluidity and improve metal-mould contact, the solidification time will also increase [4].
Compared to other high integrity die casting processes like Thixocasting and Rheocasting, squeeze casting is a simpler process and is more economical. For LM-24 aluminium alloy, a pouring temperature of 700°C, a die temperature of 200°C, and a pressure of 100 MPa provided the optimal results.
8. References:
- [1] Tim Basner, Delphi Automotive Systems, Rheocasting of Semi-Solid A357 Aluminium, Society of Automotive Engineers, 2000-01-0059 (2000).
- [2] M.R. Ghomashchi, A. Vikhrov, Squeeze Casting: An Overview, Journal of Material Processing Technology 101, P. 1-9 (2000).
- [3] T.M. Yue, Squeeze Casting of High Strength Aluminium Wrought alloy AA7010, Journal of Material Processing Technology 66 P. 179-185 (1997).
- [4] L.J. Yang, The effect of Casting Temperature on the properties of Squeeze Cast Aluminium and zinc alloys, Journal of Materials Processing Technology 140 P. 391-396(2003)
- [5] D.Y. Maeng, J.H. Lee, C.W. Won, S.S. Cho, B.S. Chun, The Effects of Processing Parameters on the Microstructure and Mechanical properties of modified B390 alloy in Direct Squeeze casting, Journal of Materials Processing Technology 105 P. 196-203 (2000).
- [6] S. W. Kim, D.Y. Kimb, W.G. Kimb, K.D. Woo, The Study on characteristics of heat treatment of the Direct Squeeze cast 7075 wrought Aluminium alloy, Journal of Material Science and Engineering A304-306 P. 721-726 (2001).
- [7] David.Schwam, John F. Wallace, Qingming Chang, Yulong. Zhu, Optimisation of the Squeeze Casting Process for Aluminium alloy parts,
- [8] Stefanos M. Skolianos, Grigoris Kiourtsidis, Thomas Xatzifotiou, Effect of Applied pressure on the Microstructure and Mechanical properties of Squeeze-cast Aluminium AA6061 alloy.Journal of Material Science and Engineering- A231 P. 17-24 (1997).
- [9] Y.Nishida and H. Matsubara, Effect of Pressure on Heat Transfer at the Metal- Mould Casting Interface, The British Foundryman, P274-278 (1972).
9. Copyright:
- This material is a paper by "Dr. Susanta Gangopadhyay". Based on "Optimisation of Casting parameters of Squeeze cast LM-24 Al-Si Alloy".
- Source of the paper: https://www.ijert.org/optimisation-of-casting-parameters-of-squeeze-cast-lm-24-al-si-alloy
This material is summarized based on the above paper, and unauthorized use for commercial purposes is prohibited.
Copyright © 2025 CASTMAN. All rights reserved.
Key Questions & Answers for Researchers:
Q1. What are the main advantages of squeeze casting over conventional die casting mentioned in the paper?
A1. Squeeze casting utilizes slower injection speed, causing less turbulence and air retention. Applied pressure during solidification eliminates shrinkage and gas porosity, decreases thermal resistance, and accelerates solidification, leading to improved microstructure and mechanical properties.
Q2. What specific alloy was studied, and why was it chosen?
A2. The study focused on aluminium-silicon alloy LM-24 with 9% Si. LM-24 is a widely used pressure die casting aluminium alloy known for its excellent casting characteristics, making it suitable for thin-walled castings.
Q3. What were the optimal squeeze casting parameters found for LM-24 aluminium alloy in this study?
A3. For LM-24 aluminium alloy, the optimum combination for better mechanical properties was found to be a pouring temperature of 700°C, a die temperature of 200°C, and an applied pressure of 100 MPa.
Q4. How does applied pressure in squeeze casting affect the microstructure of LM-24 alloy?
A4. Applied pressure reduces or eliminates the air gap between the molten metal and the die wall. This increases heat-transfer coefficients and the cooling rate, thereby achieving a finer grain size, as shown in Figure-5.
Q5. What improvements in mechanical properties were observed with the optimized squeeze casting parameters for LM-24?
A5. The optimized parameters led to an increase in density (near elimination of porosity), improved surface finish, refined microstructure, and increased hardness and tensile strength. Specifically, at 700°C pouring temperature, 200°C die temperature, and 100 MPa pressure, UTS was 240 MPa, proof stress 140 MPa, hardness 90 BHN, and elongation 4.0% (Table-3).
Q6. What is a key constraint in the direct squeeze casting process that requires careful control?
A6. A key constraint is metal filling. A highly accurate metering system for the molten metal is required. Additionally, the metal pouring and punch lowering must be synchronized, as a higher die filling rate may lead to turbulent flow, and any time delay between metal pouring and pressurization may lead to premature solidification.