This introductory paper is the research content of the paper "Medium temperature heat pipes – Applications, challenges and future direction" published by [Applied Thermal Engineering].
![Fig. 5. STRATFLY MR3 Hypersonic vehicle concept by Fusaro et al. [78].](https://castman.co.kr/wp-content/uploads/image-1638-png.webp)
1. Overview:
- Title: Medium temperature heat pipes – Applications, challenges and future direction
- Author: Thomas C. Werner, Yuying Yan, Tassos Karayiannis, Volker Pickert, Rafal Wrobel, Richard Law
- Publication Year: 2024
- Published Journal/Society: Applied Thermal Engineering
- Keywords: Heat pipe, Thermal management, Heat transfer, Medium temperature fluids, Two-phase heat transfer
2. Abstract
Heat pipes have been used for thermal management, especially in aerospace, electronics, automotive, and power generation. The operating temperature range requires specific fluid and casing materials. There is increasing demand for heat pipes operating in the 300-600°C ("medium" or "intermediate" temperature) range, but development is lacking due to a shortage of suitable fluids. This paper summarizes efforts in developing medium temperature heat pipes, highlighting promising fluids and wall materials. It explores (a) current applications, (b) medium temperature fluid investigations, (c) principles behind heat pipe performance prediction, and (d) suggests future research directions, including a standardized fluid assessment framework.
3. Research Background:
Background of the research topic:
Thermal management is crucial in modern engineering due to increasing power densities. Heat pipes offer superior heat transfer capabilities compared to conventional solid materials.
Status of previous research:
Heat pipes have been developed for various temperature ranges, from cryogenic to high temperature. However, the medium temperature range (300-600°C) faces challenges due to limited fluid options. Existing research often lacks continuity, with a focus on long-term compatibility tests and limited analytical approaches.
Need for research:
There's a growing demand for heat pipes in the medium temperature range, but development is hindered by the lack of suitable working fluids. Previous work is fragmented, and a comprehensive solution is missing.
4. Research purpose and research question:
Research purpose:
To summarize major efforts in developing medium temperature heat pipes and to highlight the most promising fluids and wall materials.
Core research:
(a) current applications that could benefit from medium temperature heat pipes, (b) existing research on medium temperature fluids, (c) principles behind heat pipe performance prediction, fluid analysis, fluid/metal compatibility, and fluid selection, and (d) potential future research directions, particularly focusing on novel heat pipe fluids.
5. Research methodology
This paper is a literature review. It summarizes and analyzes existing research on medium temperature heat pipes. The paper explores current applications, previous work on medium temperature fluids, principles of heat pipe performance, and future research directions. A fluid assessment framework is proposed. The research design is a review and analysis of published literature, including experimental studies, numerical modeling, and theoretical analyses. Data collection involved searching databases like Scopus.com [29] for relevant publications. The analysis includes qualitative assessment of research findings and quantitative comparison of fluid properties and performance.
6. Key research results:
Key research results and presented data analysis:
- Renewables Market: Concentrated solar power (CSP) plants often operate in the medium temperature range (Table 1, Fig. 3).
- Waste Heat Recovery: High-temperature waste heat (above 300°C) represents a significant portion of global heat recovery potential [68].
- Nuclear Market: Diverter target plates in nuclear fusion reactors operate within the 300-600°C range (Fig. 4).
- Other Markets: Hypersonic vehicle thermal management (Fig. 5) and engine wall cooling also present potential applications.
- Challenges with Existing Fluids:
- Mercury: Toxic, high density, and wick wetting issues [83, 97].
- Sulphur and Sulphur/Iodine: High viscosity, low thermal conductivity, and chemically aggressive [108].
- Organic Fluids: Thermal decomposition between 300°C and 400°C [82, 93, 102, 104, 106].
- Potassium and Caesium: Low vapor density at medium temperatures, handling difficulties, and extreme sensitivity to moisture [79].
- Sodium/Potassium (Na/K): "Geyser boiling" phenomenon at temperatures below 800°C [105, 109, 110].
- Categorical Analysis of Fluids:
- Organic Fluids: Generally limited to below 400°C due to thermal decomposition (Fig. 6, 7, 8, Table 4).
- Inorganic Fluids (Halides): Antimony Tribromide shows the best potential among tested halides, but still limited to low heat flux density applications above 320°C (Fig. 9, 10, 11, Table 5).
- Liquid Metals: Mercury and Caesium can theoretically operate within the medium temperature range, but face practical challenges (Fig. 12, 13, 14, Table 6, 7).
- Inorganic Mixtures: Sulphur/Iodine and Sodium/Potassium show promise but lack sufficient property data (Table 8).
- A fluid analysis process is proposed (Fig. 15).
![Fig. 1. Papers published directly relating to heat pipes. Produced using data from Scopus.com [29].](https://castman.co.kr/wp-content/uploads/image-1639-1024x642.webp)
![Fig. 3. Share of subjects linked to the exploration of medium temperature heat pipes taken from 70 papers on the topic spanning 1972 to 2022. Produced using data
from Scopus.com [29].](https://castman.co.kr/wp-content/uploads/image-1640-1024x796.webp)
![Table 1
Specifications for main large-scale concentrated solar power plants Produced using data from He et al. [67]. Third generation plants are exploring the use of silica sand,
calcinated flint clay and ceramic particles as well as a range of chlorinated or carbonated molten salts as heat absorbing mediums within the medium temperature
range.](https://castman.co.kr/wp-content/uploads/image-1641-1024x219.webp)
Specifications for main large-scale concentrated solar power plants Produced using data from He et al. [67]. Third generation plants are exploring the use of silica sand, calcinated flint clay and ceramic particles as well as a range of chlorinated or carbonated molten salts as heat absorbing mediums within the medium temperature range.
![Fig. 4. Diverter target plate structure. A re-creation of images from You et al. [74].](https://castman.co.kr/wp-content/uploads/image-1642-png.webp)
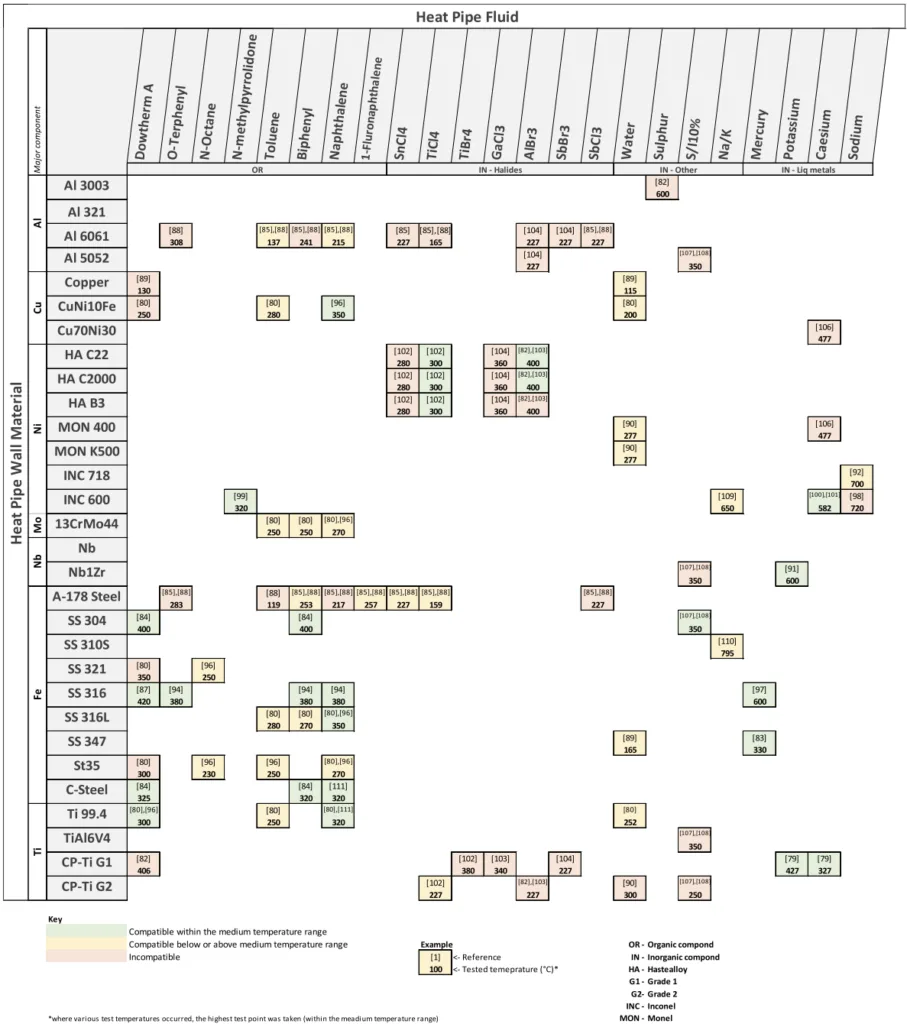
![Fig. 14. Maximum thermal transport capacity for main liquid metals explored for use in the medium temperature range. Modelled with heat pipe dimensions
presented in the study by Werner et al. [114] (see Table 3).](https://castman.co.kr/wp-content/uploads/image-1644-png.webp)
List of figure names:
- Fig. 1. Papers published directly relating to heat pipes. Produced using data from Scopus.com [29].
- Fig. 2. Share of top 13 countries contributing to heat pipe research data presented in Fig. 1 for years 1960-2022. Produced using data from Scopus.com [29].
- Fig. 3. Share of subjects linked to the exploration of medium temperature heat pipes taken from 70 papers on the topic spanning 1972 to 2022. Produced using data from Scopus.com [29].
- Fig. 4. Diverter target plate structure. A re-creation of images from You et al. [74].
- Fig. 5. STRATFLY MR3 Hypersonic vehicle concept by Fusaro et al. [78].
- Fig. 6. Liquid transport factor for main organic fluids explored for use in the medium temperature range.
- Fig. 7. Vapour pressure for main organic fluids explored for use in the medium temperature range.
- Fig. 8. Maximum thermal transport capacity for main organic fluids explored for use in the medium temperature range. Modelled with heat pipe dimensions presented in the study by Werner et al. [114] (see Table 3).
- Fig. 9. Liquid transport factor for main halide fluids explored for use in the medium temperature range.
- Fig. 10. Vapour pressure for main halides explored for use in the medium temperature range.
- Fig. 11. Maximum thermal transport capacity for main halide fluids explored for use in the medium temperature range. Modelled with heat pipe dimensions presented in the study by Werner et al. [114] (see Table 3).
- Fig. 12. Liquid transport factor for main liquid metal fluids explored for use in the medium temperature range.
- Fig. 13. Vapour pressure for main liquid metals explored for use in the medium temperature range.
- Fig. 14. Maximum thermal transport capacity for main liquid metal fluids explored for use in the medium temperature range. Modelled with heat pipe dimensions presented in the study by Werner et al. [114] (see Table 3).
- Fig. 15. Fluid analysis and selection process.
7. Conclusion:
Summary of key findings:
There is an increasing need for medium temperature heat pipes. Organic fluids are generally unsuitable above 400°C. Halides show limited performance. Liquid metals have the best theoretical performance but face practical challenges. Some mixtures show promise but lack data.
{Summary of research results. Academic significance of the research, practical implications of the research}
The paper concludes that more research is needed, particularly in developing and characterizing new fluids. A standardized fluid assessment framework is proposed to accelerate research. The development of central databases and heat pipe modeling tools is crucial.
8. References:
- [1] D. Reay, P. Kew, Heat Pipes Theory, Design and Applications, 2006.
- [2] M. Mochizuki, R. Sigh, T. Nguyen, Completely passive heat pipe based emergency core cooling system, in: 16th International Heat Pipe Conference (16th IHPC), 2012.
- [3] C. Hoa, B. Demolder, A. Alexandre, Roadmap for developing heat pipes for ALCATEL SPACE's satellites, Appl. Therm. Eng. 23(9 SPEC) (2003) 1099-1108. 10.1016/S1359-4311(03)00039-5.
- [4] G. Wang, D. Mishkinis, D. Nikanpour, Capillary heat loop technology: Space applications and recent Canadian activities, Appl. Therm. Eng. 28 (4) (2008) 284-303, https://doi.org/10.1016/j.applthermaleng.2006.02.027.
- [5] P.V. Panetta, et al., NASA/GSFC nano-satellite technology development, Science (1998) 115-122.
- [6] G. Canti, G.P. Celata, M. Cumo, M. Furrer, Thermal hydraulic characterization of a heat pipe with extracapillary circulation, Int. J. Therm. Sci. 41 (2) (2002) 115-123, https://doi.org/10.1016/S1290-0729(01)01289-3.
- [7] R. Wrobel, D. Reay, A feasibility study of heat pipes for thermal management of electrical machines, in: ECCE 2020 - IEEE Energy Conversion Congress and Exposition, Institute of Electrical and Electronics Engineers Inc., Oct. 2020, pp. 4230-4237, https://doi.org/10.1109/ECCE44975.2020.9236391.
- [8] Y. Changbao, Z. Hui, Z. Jingyang, Performance simulation analysis of composite thermal management system for hypersonic vehicle, IOP Conf. Ser. Mater. Sci. Eng. 751 (1) (2020) pp, https://doi.org/10.1088/1757-899X/751/1/012078.
- [9] L. Hongpeng, L. Weiqiang, Thermal-structural analysis of the platelet heat-pipe-cooled leading edge of hypersonic vehicle, Acta Astronaut. 127 (2016) 13–19, https://doi.org/10.1016/j.actaastro.2016.05.014.
- [10] R. Hay, W.G. Anderson, Water-titanium heat pipes for spacecraft fission power, in: 13th International Energy Conversion Engineering Conference, 2015, pp. 1-12.
- [11] G. C. Birur, Thermal control of small spacecraft using single and two-phase fluid loops, in: International Two-Phase Thermal Control Technology Workshop, no. 1, p. 2003, 2003. http://hdl.handle.net/2014/7668.
- [12] S. M. Cummings, R. W. Baldauff, M. A. Brown, Advanced Loop Heat Pipes For Spacecraft Central Thermal Bus Concept Technical Background of A-LHP Technology, 2002.
- [13] J. Baumann, S. Rawal, Viability of loop heat pipes for space solar power applications, in: 35th AIAA Thermophysics Conference. 2001. 10.2514/6.2001-3078.
- [14] A. Faghri, Heat pipes: review, opportunities and challenges, Front. Heat Pipes 5 (1) (2014) pp, https://doi.org/10.5098/fhp.5.1.
- [15] S. Jafari, T. Nikolaidis, Thermal management systems for civil aircraft engines: Review, challenges and exploring the future, Appl. Sci. (Switzerland) 8 (11) (2018) 1-16, https://doi.org/10.3390/app8112044.
- [16] M. Omidi, M. Farhadi, M. Jafari, A comprehensive review on double pipe heat exchangers, Appl. Therm. Eng. 110 (2017) 1075-1090, https://doi.org/10.1016/ j.applthermaleng.2016.09.027.
- [17] J. Jose, R. Baby, "Recent advances in loop heat pipes: A review", IOP Conf Ser, Mater Sci Eng 396 (1) (2018) pp, https://doi.org/10.1088/1757-899X/396/1/ 012060.
- [18] A. Faghri, Review and advances in heat pipe science and technology, J. Heat Transfer 134 (12) (2012) 1-18, https://doi.org/10.1115/1.4007407.
- [19] H.E. Ahmed, B.H. Salman, A.S. Kherbeet, M.I. Ahmed, Optimization of thermal design of heat sinks: a review, Int. J. Heat Mass Transf. 118 (2018) 129-153, https://doi.org/10.1016/j.ijheatmasstransfer.2017.10.099.
- [20] R. Wrobel, R.J. McGlen, Heat pipes in thermal management of electrical machines - a review, Therm. Sci. Eng. Prog. 26(April) (2021), 101053, https://doi.org/ 10.1016/j.tsep.2021.101053.
- [21] J.M. Ochterbeck, Heat pipes, NASA Contractor Rep. (1975) 1181-1230.
- [22] J. Jose, T. Kumar Hotta, A comprehensive review of heat pipe: its types, incorporation techniques, methods of analysis and applications, Thermal Science and Engineering Progress, vol. 42. Elsevier Ltd, Jul. 01, 2023. doi:10.1016/j. tsep.2023.101860.
- [23] M. Rogowski, R. Andrzejczyk, Recent advances of selected passive heat transfer intensification methods for phase change material-based latent heat energy storage units: a review, Int. Commun. Heat Mass Transfer 144 (May 2023), https://doi.org/10.1016/j.icheatmasstransfer.2023.106795.
- [24] K. Cheung, Thermal Performance and Operational Characteristics Of Loop Heat Pipe (NRL LHP), 1998.
- [25] Y. Wang, G.P. Peterson, Investigation of a novel flat heat pipe, J. Heat Transfer 127 (2) (2005) 165-170, https://doi.org/10.1115/1.1842789.
- [26] A. A. M. Delil, F. Mugele, Unrealised & novel thermal control issues for applications in future spacecraft, 2005.
- [27] H. Jouhara, J. Milko, J. Danielewicz, M.A. Sayegh, The performance of a novel flat heat pipe based thermal and PV/T (photovoltaic and thermal systems) solar collector that can be used as an energy-active building envelope material, Energy 108 (2016) 148-154, https://doi.org/10.1016/j.energy.2015.07.063.
- [28] R. S. Gaugler, Heat transfer device, 1944.
- [29] Scopus.com. by Elsevier.
- [30] A. Devarakonda, W.G. Anderson, Thermo-physical properties of intermediate temperature heat pipe fluids, AIP Conf. Proc. 746 (February) (2005) 179-186.
- [31] J. H. Rosenfeld, An Overview of Long Duration Sodium Heat Pipe Tests, no. March 2004, pp. 140-147, 2004, 10.1063/1.1649568.
- [32] W. G. Anderson, J. J. Bland, High temperature loop heat pipe, 1995.
- [33] A. Devarakonda, J. K. Olminsky, An evaluation of halides and other substances as potential heat pipe fluids, Collection of Technical Papers - 2nd International Energy Conversion Engineering Conference, vol. 1. pp. 471-477, 2004.
- [34] M. Groll, O. Brost, D. Heine, T. Spendel, Heat transfer, vapour liquid flow interations and material compatibility in two-phase thermosyphons, Energy Conservation in Industry: Combustion, Heat Recovery and Rakine Cycle Machines, 1982.
- [35] W. G. Anderson, W. Bienert, Loop heat pipe radiator trade study for the 300-550 K temperature range, 2005.
- [36] J.H. Rosenfeld, N.J. Gernert, Life test results for water heat pipes operating at 200 °C to 300 °C, AIP Conf. Proc. 969 (2008) 123-130, https://doi.org/10.1063/ 1.2844957.
- [37] E. W. Saaski, Two Phase working fluids for the temperature range 100°C to 350°C, 1977.
- [38] R.S. Reid, J.T. Sena, A.L. Martinez, Heat-pipe development for advanced energy transport concepts final report covering the period, Los Alamos National Lab no. September (2001).
- [39] J.H. Rosenfeld, N.J. Gernert, Advances in high temperature titanium-water heat pipe technology, AIP Conf. Proc. 880 (2007) 129-136, https://doi.org/10.1063/ 1.2437449.
- [40] R.S. Reid, M.A. Merrigan, J.T. Sena, Review of liquid metal heat pipe work at Los Alamos, AIP Conf. Proc. 999 (May) (1991) 999-1008, https://doi.org/10.1063/ 1.40058.
- [41] G.M. Grover, J.E. Kemme, E.S. Keddy, Advances in heat pipe technology, J. Chem. Inf. Model. 53 (9) (2013) 1689-1699, https://doi.org/10.1017/ CBO9781107415324.004.
- [42] E. W. Saaski, J. H. Hartl, High-performance heat pipes for heat recovery applications, 1980.
- [43] Y. Feng, Y. Ji, M. Wu, X. Yang, Y. Li, Z. Liu, Experimental investigation on diamond-sodium potassium alloy high- temperature oscillating heat pipe, J. Eng. Thermophys. (2022).
- [44] P. Wallin, Heat Pipe, Selection of Working Fluid, 2012, pp. 1-7.
- [45] J. H. Rosenfeld, Advances in High Temperature Ti-Water Heat Pipe Technology. pdf.
- [46] T. C. Werner, Challenges in operating heat pipes above 350°C, 2019. (Accessed Jul. 10, 2023).
- [47] T. C. Werner, Investigation of Novel Analytical Tools and Experimental Methods for the Development of Intermediate Temperature Heat Pipes.
- [48] P. Szymanski, D. Mikielewicz, Challenges in operating and testing loop heat pipes in 500-700 K temperature ranges, Arch. Thermodyn. 43(2) (2022) 61-73, 10.24425/ather.2022.141978.
- [49] H. Jouhara, N. Khordehgah, S. Almahmoud, B. Delpech, A. Chauhan, S.A. Tassou, Waste heat recovery technologies and applications, Therm. Sci. Eng. Prog. 6 (April) (2018) 268-289, https://doi.org/10.1016/j.tsep.2018.04.017.
- [50] J. Hammoud, S. Dudley, N. Apte, Use of heat pipe technology for multi media thermal management, SAE Techn. Papers 724 (2006), https://doi.org/10.4271/ 2006-01-0482.
- [51] J. Wen, Thermal resistance modeling of oscillating heat pipes filled with acetone by using artificial neural network, J. Therm. Anal. Calorim. 144 (5) (2021) 1873-1881, https://doi.org/10.1007/s10973-020-10536-x.
- [52] S.N. Li, Z.T. Liang, B.H. Yan, A medium temperature heat pipe cooled reactor, Ann. Nucl. Energy 172 (2022), https://doi.org/10.1016/j.anucene. 2022.109068.
- [53] P. A. Anil, Compound Parabolic Concentrator, 2018.
- [54] U.R. Singh, A. Kumar, Review on solar stirling engine: development and performance, Therm. Sci. Eng. Prog. 8 (July) (2018) 244-256, https://doi.org/ 10.1016/j.tsep. 2018.08.
- [55] G. Jing-hu, L. Yong, W. Jun, P. Lund, Performance optimization of larger-aperture parabolic trough concentrator solar power station using multi-stage heating technology, Energy 268 (2023), https://doi.org/10.1016/j.energy.2023.126640.
- [56] M. Tawalbeh, H.A. Khan, A. Al-Othman, F. Almomani, S. Ajith, A comprehensive review on the recent advances in materials for thermal energy storage applications, Int. J. Thermofluids 18 (2023), 100326, https://doi.org/10.1016/j. ijft.2023.100326.
- [57] R.P. Merchán, M.J. Santos, A. Medina, A. Calvo Hernández, High temperature central tower plants for concentrated solar power: 2021 overview, Renew. Sustain. Energy Rev. 155 (2022), 111828, https://doi.org/10.1016/j. rser.2021.111828.
- [58] R. Senthil, et al., A holistic review on the integration of heat pipes in solar thermal and photovoltaic systems, Sol. Energy 227 (June) (2021) 577-605, https://doi. org/10.1016/j.solener.2021.09.036.
- [59] M. Aramesh, B. Shabani, Experimental evaluation of a self storage integrated evacuated tube solar thermal collector, J. Energy Storage 62 (Jun. 2023), https:// doi.org/10.1016/j.est.: 106920.
- [60] P.V. Chilbule, L.P. Dhole, Heat pipe integrated solar thermal systems and applications: a review, Mater. Today Proc. 60 (2022) 1491-1496, https://doi. org/10.1016/j.matpr.2021.11.563.
- [61] R. Xu, J. Chen, X. Zhang, R. Wang, S. Xu, Heat leakage numerical investigation of a compound parabolic concentrator-pulsating heat pipe solar collector, J. Therm. Sci. 31 (5) (2022) 1318-1326, https://doi.org/10.1007/s11630-020-1293-3.
- [62] A. Kumar, Z. Said, E. Bellos, An up-to-date review on evacuated tube solar collectors, J. Therm. Anal. Calorim. vol. 145, no. 6. Springer Science and Business Media B.V., pp. 2873-2889, Sep. 01, 2021. 10.1007/s10973-020-09953-9.
- [63] Z. Wang, Y. Diao, Y. Zhao, C. Chen, T. Wang, L. Liang, Visualization experiment and numerical study of latent heat storage unit using micro-heat pipe arrays: melting process, Energy 246 (2022), https://doi.org/10.1016/j. energy.2022.123443.
- [64] S. Kraemer, TEXEL Explores US Market for 2-Cent Thermal Energy Storage in Metal Hydrides, 2020. .
- [65] P. White, Texel offers another candidate for a hydrogen based battery, 2021. (Accessed Jun. 24, 2023).
- [66] S. Simmonds, R. Corbishley, J. Hughes, G. Taylor, The Development of the MAHLE 25kWe Solar Heated Stirling Engine Topics: Thermodynamic & Mechanical Simulation, Engine Testing, p. 738100.
- [67] Y.L. He, Y. Qiu, K. Wang, F. Yuan, W.Q. Wang, Perspective of concentrating solar power, Energy 198 (2020), https://doi.org/10.1016/j.energy.2020.117373.
- [68] C. Forman, I.K. Muritala, R. Pardemann, B. Meyer, Estimating the global waste heat potential, Renew. Sustain. Energy Rev. 57 (2016) 1568-1579, https://doi. org/10.1016/j.rser.2015.12.192.
- [69] R.S. Vizitiu, A. Burlacu, C. Abid, M. Verdes, M.C. Balan, M. Branoaea, Experimental and numerical study of thermal performance of an innovative waste heat recovery system, Appl. Sci. (Switzerland) 11 (23) (2021), https://doi.org/ 10.3390/app112311542.
- [70] M. Sakthi Priya, D. Sakthivadivel, Experimental investigation on the thermal performance of a novel thermosyphon heat pipe with truncated cone for heat recovery systems, Energy Convers. Manag. 276 (2023), https://doi.org/10.1016/ j.enconman.2022.116522.
- [71] H. Jouhara, et al., Waste heat recovery solution based on a heat pipe heat exchanger for the aluminium die casting industry, Energy 266 (2023), https:// doi.org/10.1016/j.energy.2022.126459.
- [72] H. Jouhara, et al., Investigation on a full-scale heat pipe heat exchanger in the ceramics industry for waste heat recovery, Energy 223 (2021), 120037, https:// doi.org/10.1016/j.energy.2021.120037.
- [73] L. Yodrak, S. Rittidech, N. Poomsa-ad, Waste heat recovery by heat pipe air- preheater to energy thrift from the furnace in a hot forging process, Am. J. Appl. Sci. 7 (5) (2010) 675-681, https://doi.org/10.3844/ajassp.2010.675.681.
- [74] J.H. You, et al., European divertor target concepts for DEMO: design rationales and high heat flux performance, Nucl. Mater. Energy 16 (April) (2018) 1-11, https://doi.org/10.1016/j.nme. 2018.05.012.
- [75] B.H. Yan, C. Wang, L.G. Li, The technology of micro heat pipe cooled reactor: a review, Ann. Nucl. Energy 135 (2020), https://doi.org/10.1016/j. anucene.2019.106948.
- [76] B. Zohuri, S. Lam, C. Forsberg, Heat-pipe heat exchangers for salt-cooled fission and fusion reactors to avoid salt freezing and control tritium: a review, Nucl. Technol. 206(11). Bellwether Publishing, Ltd., pp. 1642-1658, Nov. 01, 2020. 10.1080/00295450.2019.1681222.
- [77] M. Coutinho et al., A review on the recent developments in thermal management systems for hybrid-electric aircraft, Appl. Therm. Eng. vol. 227. Elsevier Ltd, Jun. 05, 2023. 10.1016/j.applthermaleng.2023.120427.
- [78] R. Fusaro, D. Ferretto, N. Viola, R. Scigliano, V. De Simone, M. Marini, Liquid Metals Heat-Pipe solution for hypersonic air-intake leading edge: Conceptual design, numerical analysis and verification, Acta Astronaut. 197 (2022) 336-352, https://doi.org/10.1016/j.actaastro.2022.05.034.
- [79] P. M. Dussinger, W. G. Anderson, E. T. Sunada, Design and testing of titanium/ cesium and titanium/potassium heat pipes, in: Collection of Technical Papers - 3rd International Energy Conversion Engineering Conference, vol. 2, pp. 1088-1096, 2005.
- [80] M. Groll, Heat pipe research and development in western Europe, Heat Recovery Syst. CHP 9 (1) (1989) 19-66, https://doi.org/10.1016/0890-4332(89)90139-7.
- [81] W.G. Anderson, Evaluation of heat pipes in the temperature range of 450 to 700 K, AIP Conf. Proc. 746 (2005) 171-178, https://doi.org/10.1063/1.1867132.
- [82] W. G. Anderson, Intermediate temperature fluids for heat pipes and loop heat pipes, in: Collection of Technical Papers - 5th International Energy Conversion Engineering Conference, vol. 2, no. June, pp. 1147-1164, 2007.
- [83] J. E. Deverall, Mercury as a heat pipe fluid, 1970.
- [84] D. D. Kenney, K. T. Feldman, K. T. Jr. Feldman, Heat pipe life tests at temperatures up to 400 C, 1978.
- [85] E.W. Saaski, P.C. Owzarski, Two-phase working fluids for the temperature range 50° to 350°C, Heat Transfer Therm. Control Syst. (1978) 63-79, https://doi.org/ 10.2514/5.9781600865343.0063.0079.
- [86] I. E. Locci, A. Devarakonda, E. H. Copland, J. K. Olminsky, Analytical and experimental thermo-chemical compatibility study of potential heat pipe materials, in: Collection of Technical Papers - 3rd International Energy Conversion Engineering Conference, vol. 2, no. August, pp. 1285-1292, 2005, 10.2514/