M. Schütze1, J. Ganzenmüller2, M. Becker3, C. Mangos1, G. Piazza2, L. Kallien1, E. Beeh2
1Aalen University; 2German Aerospace Center (DLR), Stuttgart; 3Oskar Frech GmbH + Co. KG, Schorndorf
The industrial shift towards e-mobility is an opportunity for the economic production of high pressure
die castings (HPDC) components, such as motor housings, gearboxes and covers. Those parts are mainly
manufactured in large serial numbers from aluminum alloys. Although the use of high strength
magnesium alloys for structural castings has the potential of further weight reduction in lightweight
constructions [1].
To manufacture high quality castings with low amounts of internal defects the casting processes have
been upgraded over the past years. One of these improvements is the Vacural® die casting process from
Oskar Frech GmbH which provides the best possible casting quality for aluminum alloys [2]. The process
differs from vacuum-assisted die casting. The vacuum is applied continuously from the beginning of the
dosing process until the mold is completely filled. In the process the molten material is sucked directly
from the furnace via a pipe into the casting chamber. The closed system reduces oxidation of the melt
while dosing. Until the mold is filled, a vacuum of around 70 mbar is achieved, which reduces air
inclusions in the die casting parts.
The Vacural® die casting process provides the same benefits for magnesium. In the project InDrutec-E,
funded by the BMWK, three different alloys - AZ91, AS31 and AE 44-2 - were casted and afterwards
tested. For this study all alloys were casted in 4 mm plates via vacuum-assisted and compared to the
Vacural® die casting. Afterwards flat samples were tested for static and fatigue strength.
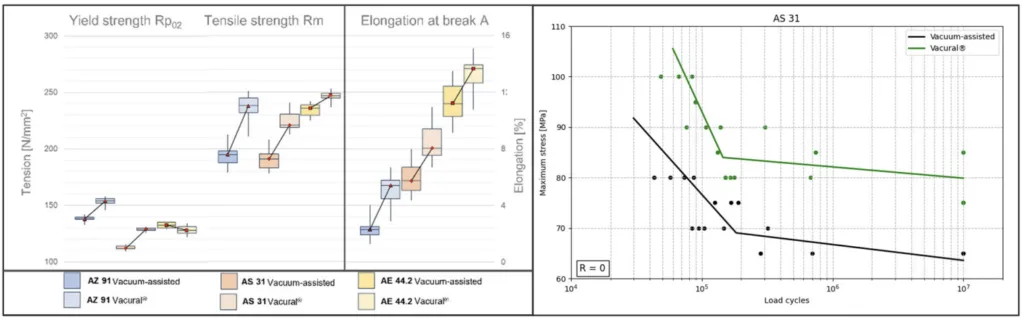
The results in Figure 1 (left) shows the increase of static properties like tensile and yield strength as a
result of Vacural® die casting. For all three alloys a significant increase in strength and ductility was
investigated. For the AZ 91 and AE 44-2 no mentionable increase of the fatigue strength due to the
advanced casting process were visible. On the other hand, a significant elevation of the fatigue strength
for AS 31 was observed. The fatigue behavior comparison for the two casting processes of AS 31 is
shown in the right plot of Figure 1.
The investigation shows, that the Vacural® die casting process has a high influence on the mechanical
properties of magnesium alloys. For further investigation the alloy AS 31 in combination with the
Vacural® process was used to show the light weight potential of a gearbox cover for electrical
powertrain applications [3].
References
- [1] Magnesium: Eigenschaften, Anwendungen, Potenziale; Kainer, K.U., Ed., 1st ed.; WILEY-VCH Verlag GmbH:
- Weinheim, 2000, ISBN 3527299793.
- [2] https://www.frechusa.com/vacural-technology
- [3] Beeh, E. (2023, 15. Februar). Leichtbau- und Ressourcenschonungspotentiale bei Druckgussteilen
- [Konferenzbeitrag]. Fachtagung für neue Fahrzeug- und Werkstoffkonzepte, Stuttgart, Germany