This article introduces the paper "Influence of Different Rapid Injection Velocity on Forming Quality of Magnesium Alloy Vacuum Die Casting".
1. Overview:
- Title: Influence of Different Rapid Injection Velocity on Forming Quality of Magnesium Alloy Vacuum Die Casting
- Authors: Chen Sitao¹, Song Dongfu², Qi Wenjun², Zhou Feng¹
- Year of Publication: 2024
- Journal/Conference: Special Casting & Nonferrous Alloys
- Keywords: Magnesium Alloy, Processing Parameter, Vacuum Die Casting
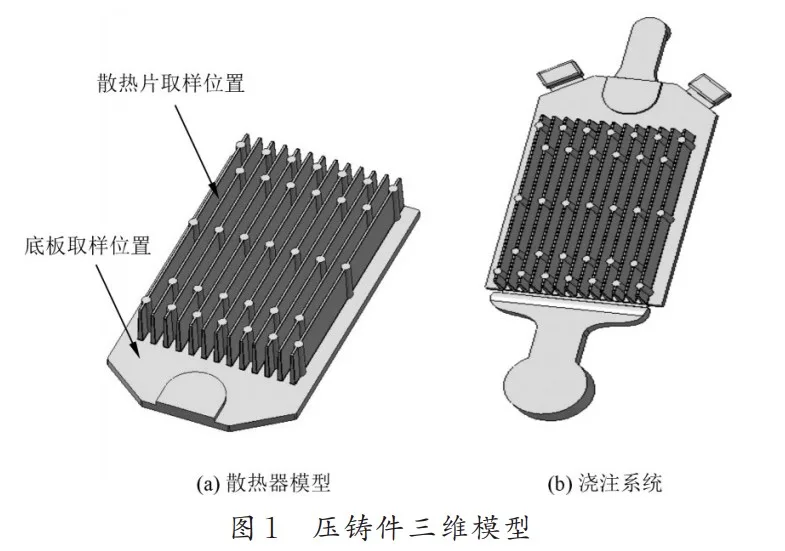
2. Research Background:
This research investigates the impact of rapid injection speed on the quality of magnesium alloy vacuum die castings using AZ91D magnesium alloy. Magnesium alloys are widely used in aerospace, 3C industries, and more due to their high specific strength, stiffness, impact resistance, electromagnetic shielding, thermal conductivity, and recyclability. Existing vacuum die-casting processes suffer from drawbacks such as low cavity evacuation efficiency, unreliable vacuum valve closure, slow valve response, and high cost. This study addresses these issues by designing a vacuum pumping system with both full-process and semi-process exhaust channels. Rapid injection speed significantly influences the microstructure and mechanical properties of vacuum die castings; therefore, this research analyzes this impact across different speeds.
3. Research Objectives and Questions:
- Research Objective: To investigate the effects of different rapid injection speeds on the mechanical properties and microstructure of vacuum die-cast parts made from AZ91D magnesium alloy using a self-designed vacuum pumping system.
- Key Research Question: How do different rapid injection velocities affect the forming quality of magnesium alloy vacuum die castings?
- Research Hypothesis: Rapid injection speed impacts the forming quality of magnesium alloy vacuum die castings, and an optimal rapid injection speed exists.
4. Research Methodology:
- Research Design: An experimental design employing three different rapid injection speeds (3 m/s, 4 m/s, and 5 m/s) for AZ91D magnesium alloy vacuum die casting experiments. Mechanical properties and microstructure were analyzed for each condition.
- Data Collection Methods: AZ91D magnesium alloy LED heat sinks were manufactured using a self-designed vacuum pumping system with three different rapid injection speeds.
- Analysis Methods: Tensile strength and elongation were measured. Microstructures were observed and analyzed using metallography.
- Research Subjects and Scope: AZ91D magnesium alloy LED heat sinks, rapid injection speeds (3 m/s, 4 m/s, 5 m/s), vacuum die-casting process.
5. Main Research Results:
- Key Findings: Die castings produced by the self-designed vacuum pumping system exhibited better mechanical properties than ordinary die castings. At 3 m/s, the surface easily formed cold shuts and flow marks, and the microstructure showed numerous shrinkage porosity and holes. At 5 m/s, flash easily occurred, and the microstructure contained many shrinkage holes. At 4 m/s, the castings had a complete shape with only a few shrinkage cavities; the tensile strength and elongation of the heat sink reached 226 MPa and 5.4%, respectively.
- Statistical/Qualitative Analysis Results: Table 3 shows that the highest tensile strength (226 MPa) and elongation (5.4%) were achieved at 4 m/s. Figure 4 shows surface defects (cold shuts and flow marks) at 3 m/s. Figures 5 and 6 present microstructures at different speeds; 3 m/s and 5 m/s showed many shrinkage cavities and pores, while 4 m/s showed fewer.
- Data Interpretation: 4 m/s yielded optimal results, suggesting it's suitable for metal flow and solidification. 3 m/s was too slow (causing surface defects), and 5 m/s was too fast (causing flash).
- Figure List and Description: (Descriptions of Figures 1-6 and Tables 1-3 as detailed in the Chinese summary).
6. Conclusion and Discussion:
This study demonstrates that a rapid injection speed of 4 m/s yields optimal mechanical properties (tensile strength of 226 MPa and elongation of 5.4%) in AZ91D magnesium alloy vacuum die casting using the self-designed vacuum pumping system. Slower (3 m/s) and faster (5 m/s) speeds resulted in surface defects and flashing, respectively. This offers significant insights for optimizing vacuum die-casting processes. However, a limitation is the relatively small sample size.
7. Future Research:
Future research could involve further experiments with a wider range of rapid injection speeds and different magnesium alloys to broaden the optimal parameter range. Studies on various part geometries and process optimization using numerical simulation are also warranted.
8. References Summary:
Please refer to the original paper (pages 127 and 129) for the complete list of references.
Copyright and Source Material:
This summary is based on the paper "Influence of Different Rapid Injection Velocity on Forming Quality of Magnesium Alloy Vacuum Die Casting" by Chen Sitao et al.
Source: DOI: 10.15980/j.tzzz.2024.01.025
This summary is based on the above-mentioned paper and is not permitted for commercial use without authorization.
Copyright © 2025 CASTMAN. All rights reserved.