This introductory paper is the research content of the paper "Identify Microstructure and Mechanical Behavior of Aluminum Hybrid Nano Composite Prepared by Casting Technique" published by Jordan Journal of Mechanical and Industrial Engineering.
![Figure 1. Various matrix and strengthening materials are utilized for MMC production[25].](https://castman.co.kr/wp-content/uploads/image-1561-1024x830.webp)
1. Overview:
- Title: Identify Microstructure and Mechanical Behavior of Aluminum Hybrid Nano Composite Prepared by Casting Technique
- Author: Khaldun Aldawoudi, Ayad Mohammed Nattah, Nabaa Sattar Radhi, Zainab S. Al-Khafaji, Manar Khaleel Ibrahim
- Publication Year: 2025
- Published Journal/Society: Jordan Journal of Mechanical and Industrial Engineering
- Keywords: Aluminum Matrix Composites (AMCs), Fe2O3, SiO2 hybrid particles, stir casting method, reinforcement, and Brinell hardness.
2. Abstract
The development of Aluminum-based composite metallic matrices (AMMCs) has become one of the main requirements for engineering applications due to their low weight, high strength, and superior mechanical characteristics. In this work, the effect of adding 1.25 wt% SiO2, 1.25 wt% Fe2O3, or a mixture of 1.25 wt% SiO2 and 1.25 wt% Fe2O3 hybrid particles on the hardness and compressive strength of an aluminum matrix composite fabricated by stir casting will be studied. A scanning electron microscope was utilized to investigate the microstructure of the specimens. Measurements of hardness and compressive strength characteristics revealed an improvement with increasing reinforcement weight percentage. Results for specimens of reinforced aluminum with 1.25 SiO2, 1.25 Fe2O3, or a mixture of 1.25 SiO2 and 1.25 Fe2O3 wt% particles indicated that the increment percentage of Brinell hardness was, respectively, 25.5%, 6.8%, and 19.3%. Finally, with an increasing percentage of iron or silicon oxide, the yield point and young modulus significantly decreased, even reaching the minimum magnitude at the composite containing 1.25% Fe2O3 and 1.25% SiO2.
3. Research Background:
Background of the research topic:
A "composite" is a material system that consists of a distinct component (the reinforcement) dispersed in a continuous phase (the matrix) [1]-[9]. The literature has extensively examined metal matrix composites, particularly aluminum matrix composites (AMCs). [15], [16].
Status of previous research:
The literature has extensively examined metal matrix composites, particularly aluminum matrix composites (AMCs). Silicon carbide, alumina oxide, tungsten carbide, and titanium carbide are widely recognized as the most frequently utilized materials for reinforcing aluminum composites[21].
Need for research:
Previous research explored single-particle reinforcement. This study needs synergistic effects of hybrid nano-sized reinforcements.
4. Research purpose and research question:
Research purpose:
This research aims to fabricate, identify, and characterize the mechanical behavior and hardness of (AMC) reinforced with nano Hematite, nano silicon oxide, hybrid nano Hematite, and nano silicon oxide.
Core research:
Exploring the synergistic effects of hybrid nano-sized reinforcements, specifically SiO2 and Fe2O3 particles, within an aluminum matrix composite (AMC).
5. Research methodology
The research employed a stir casting technique, specifically a two-step stir-casting procedure, to fabricate aluminum matrix composites.
- Specimen Preparation: High-purity aluminum wires were used as the matrix material. Reinforcing materials (SiO2, Fe2O3, or a mixture) were added at 1.25 wt% each (Table 2). The aluminum was melted in a furnace, and the temperature was controlled using a thermocouple. A mechanical stirrer was used to mix the molten aluminum and the preheated reinforcement particles.
- Preheating of Reinforcement: Reinforcement particles were preheated to 300°C for 2 hours to improve wettability and remove moisture.
- Two-Step Stirring: A two-step stirring process. The first stir at the semi-solid state(620°C). The second stir above the liquidus temperature of 750°C.
- Casting: The molten composite was poured into a preheated steel mold for solidification.
- Heat Treatment: Cast samples were heat-treated at 350°C for 5 hours for homogenization and to relieve thermal stresses.
- Microstructural Analysis: Scanning Electron Microscopy (SEM) was used to examine the microstructure (Figure 2). X-ray Diffraction (XRD) was used to identify the phases present (Figure 3).
- Mechanical Testing:
- Brinell Hardness Test: Performed according to ASTM E10-15a, using a 5mm ball indenter and 31.25 Kg force (Figure 4).
- Compression Test: Conducted on cylindrical samples (12 mm diameter, 24 mm height) according to ASTM standard (L=2D) (Figure 5).
-Wear Test: using the wear tester equipment model MT-4003, version 10.0, which operates on the pin-on-disk idea. (Figure 7).
6. Key research results:
Key research results and presented data analysis:
- Microstructure: SEM images (Figure 2) show the distribution of nanoparticles within the aluminum matrix. XRD analysis (Figure 3) confirmed the presence of Al, SiO2, and Fe2O3 phases.
- Brinell Hardness: The addition of nanoparticles increased hardness. The Brinell hardness shows the increment percentage at (25.5%), (6.8%) and (19.3%) for aluminum reinforced with (1.25 SiO2, 1.25 Fe2O3 and 1.25 SiO2- 1.25 Fe2O3)wt. % of particle specimens respectively (Figure 4).
- Compressive Strength: The Al+ 1.25% Fe2O3 specimen showed a maximum increase of 165% compared with the pure aluminum. (Figure 5).
- Young's Modulus: Decreasing Young modulus value with increasing reinforcement percentage was (47 Gpa) for Al+(1.25 SiO2+1.25 Fe2O3) (Figure 6).
- Wear Rate: The wear rate is reduced by (46.4) % in aluminum reinforced by 1.25% Fe2O3. (Figure 7)
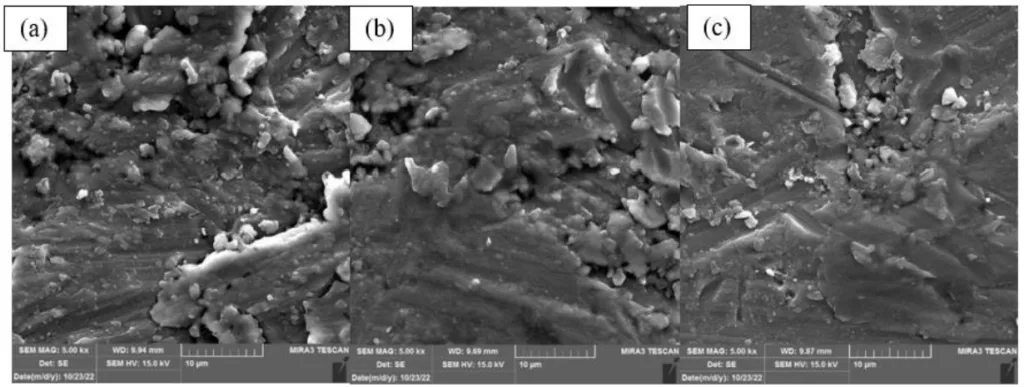
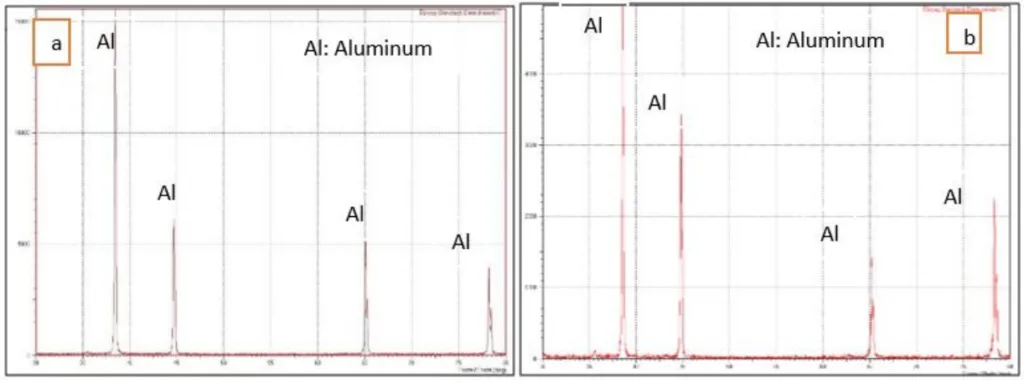
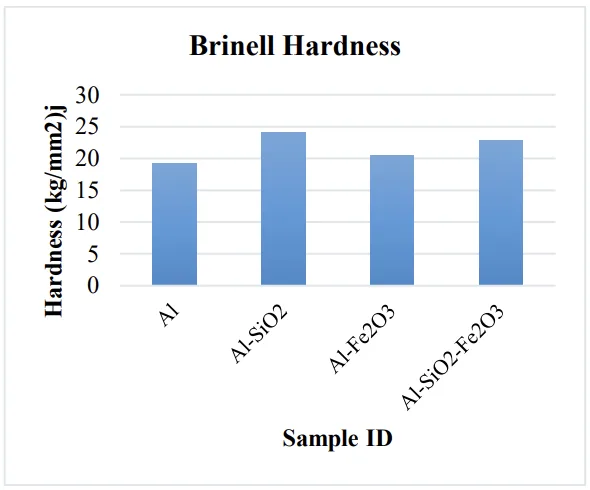
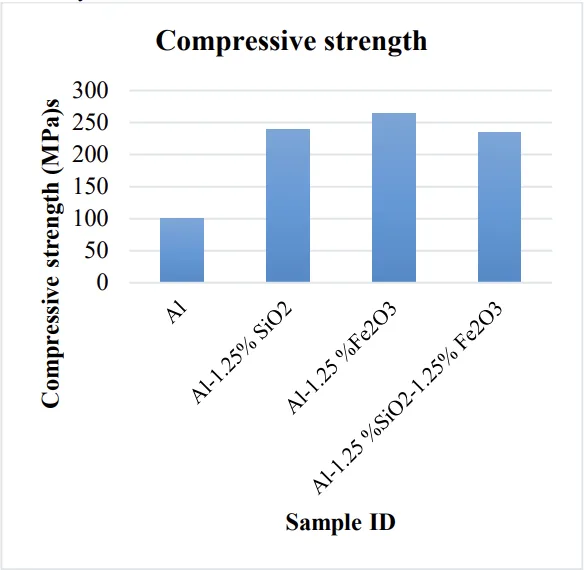
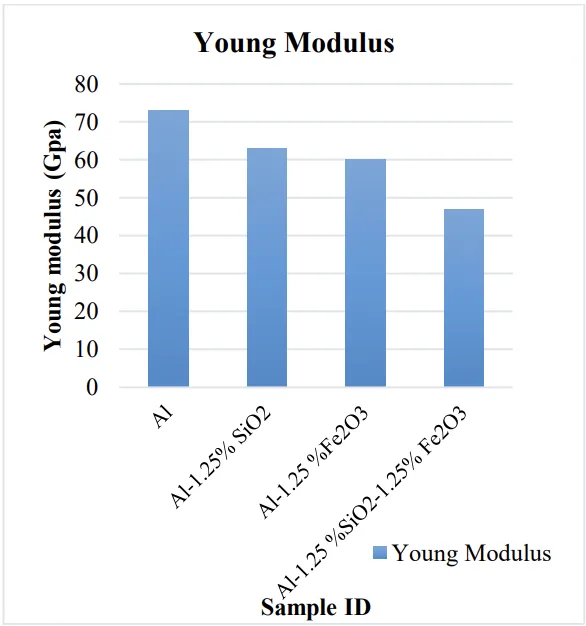
List of figure names:
- Figure 1. Various matrix and strengthening materials are utilized for MMC production[25].
- Figure 2. SEM a) 1.25 wt%Fe2O3, b) 1.25 wt%SiO2, c)1.25 wt%Fe2O3+1.25 wt%SiO2.
- Figure 3. XRD pattern of a: Al-(1.25 wt.%) Fe2O3 b: Al-(1.25 wt.%) SiO2.
- Figure 4. The Brinell hardness magnitudefordifferent Al alloys.
- Figure 5: Compressive strength magnitude of different Al alloys.
- Figure 6: Shows the Young modulus vs Al percentage.
- Figure 7: At steady state, the wear rate for Al specimens at (time=20 min.).
7. Conclusion:
Summary of key findings:
- SEM and XRD results show the nanoparticles impeded in the aluminum matrix and shifting the peaks of the XRD pattern.
- The finding illustrated that at 10 N, the highest wear rate is in the Al sample, and the wear rate is reduced by (46.4) % in aluminum reinforced by 1.25% Fe2O3.
- The percentage increment of Brinell hardness is (25.5%), (6.8%) and (19.3%) for aluminum reinforced with 1.25 SiO2, 1.25 Fe2O3, and (1.25 SiO2, 1.25 Fe2O3) wt.% particles specimens, respectively.
- The maximum improvement for the Al+1.25 Fe2O3 specimen was recorded at 26.5% in compressive strength.
- The young modulus values decrease with an increasing reinforcement percentage.
Possible areas for future expansion research:
Further optimization of stir-casting parameters is recommended to enhance particle wettability and minimize agglomeration. Exploring different weight percentages and hybrid reinforcement combinations. Fatigue testing and long-term environmental exposure studies.
8. References:
- [1] D. K. Rajak, D. D. Pagar, R. Kumar, and C. I. Pruncu, "Recent progress of reinforcement materials: a comprehensive overview of composite materials," Journal of Materials Research and Technology, vol. 8, no. 6, pp. 6354- 6374, 2019.
- [2] M. Balasubramanian, Composite materials and processing, vol. 711. CRC press Boca Raton, 2014.
- [3] A. H. Haleem, N. S. Radhi, N. T. Jaber, and Z. Al-Khafaji, "Preparation and Exploration of Nano-Multi-Layers on 3161 Stainless Steel for Surgical Tools," Jordan Journal of Mechanical and Industrial Engineering (JJMIE), vol. 18, no. 2, 2024.
- [4] M. R. Jasim, Y. Alaiwi, and Z. Al-khafaji, "Investigation Of The Effect Of Adding Nitrogen On The Torque Generated By A Four-Cylinder Engine," Jordan Journal of Mechanical and Industrial Engineering, pp. 1–30, 2024.
- [5] Ł. J. Orman, "Enhanced Boiling Heat Transfer on Surfaces Covered with Microstructural Mesh Coatings.," Jordan Journal of Mechanical and Industrial Engineering, vol. 13, no. 3, pp. 155-160, 2019.
- [6] A. Ismail, R. Zenasni, K. S. M. Amine, and S. Ahmed, "Effect of tempering temperature on the mechanical properties and microstructure of low alloy steel DIN 41Cr4," Jordan Journal of Mechanical and Industrial Engineering, vol. 13, no. 1, pp. 9–14, 2019.
- [7] R. M. K. Ali and S. L. Ghashim, "Thermal performance analysis of heat transfer in pipe by using metal foam.," Jordan Journal of Mechanical & Industrial Engineering, vol. 17, no. 2, pp. 205-218, 2023.
- [8] A. R. I. Kheder, N. M. Jubeh, and E. M. Tahah, "Fatigue Properties under Constant Stress/Variable Stress Amplitude and Coaxing Effect of Acicular Ductile Iron and 42 CrMo4 Steel.," Jordan Journal of Mechanical and Industrial Engineering, vol. 5, no. 4, pp. 301-306, 2011.
- [9] S. Dwivedi and S. Sharma, "Optimization of Resistance Spot Welding Process Parameters on Shear Tensile Strength of SAE 1010 steel sheets Joint using Box-Behnken Design.," Jordan Journal of Mechanical and Industrial Engineering, vol. 10, no. 2, pp. 115–122, 2016.
- [10] V. V Vasiliev and E. V Morozov, Advanced mechanics of composite materials and structures. Elsevier, 2018.
- [11] H. Altenbach, J. Altenbach, W. Kissing, and H. Altenbach, Mechanics of composite structural elements. Springer, 2004.
- [12] A. Mortensen and J. Llorca, "Metal matrix composites," Annual review of materials research, vol. 40, no. 1, pp. 243- 270, 2010.
- [13] K. K. Chawla, Ceramic matrix composites. Springer Science & Business Media, 2013.
- [14] R. N. Hwayyin and A. S. Ameed, "The Time Dependent Poisson's Ratio of Nonlinear Thermoviscoelastic Behavior of Glass/Polyester Composite.," Jordan Journal of Mechanical and Industrial Engineering, vol. 16, no. 4, pp. 515-528, 2022.
- [15] S. T. Mavhungu, E. T. Akinlabi, M. A. Onitiri, and F. M. Varachia, "Aluminum matrix composites for industrial use: advances and trends," Procedia Manufacturing, vol. 7, pp. 178-182, 2017.
- [16] M. H. Rahman and H. M. M. Al Rashed, "Characterization of silicon carbide reinforced aluminum matrix composites," Procedia Engineering, vol. 90, pp. 103-109, 2014.
- [17] M. B. N. Shaikh, S. Arif, T. Aziz, A. Waseem, M. A. Ν. Shaikh, and M. Ali, "Microstructural, mechanical and tribological behaviour of powder metallurgy processed SiC and RHA reinforced Al-based composites," Surfaces and Interfaces, vol. 15, pp. 166–179, 2019.
- [18] D. Manfredi et al., "Additive manufacturing of Al alloys and aluminium matrix composites (AMCs)," Light metal alloys applications, vol. 11, pp. 3-34, 2014.
- [19] Y. Wang and T. Monetta, "Systematic study of preparation technology, microstructure characteristics and mechanical behaviors for SiC particle-reinforced metal matrix composites," Journal of Materials Research and Technology, vol. 25, no. 1, pp. 7470-7497, 2023.
- [20] A. M. Nattah, K. E. F. Aldawoudi, and E. M. S. Salih, "Effects of Nano particles of (Al2O3, Fe2O3) as Reinforcement on Mechanical Properties of Aluminum," Journal of University of Babylon for Engineering Sciences, pp. 59-71, 2023.
- [21] M. B. N. Shaikh, S. Arif, and M. A. Siddiqui, "Fabrication and characterization of aluminium hybrid composites reinforced with fly ash and silicon carbide through powder metallurgy," Materials Research Express, vol. 5, no. 4, p. 46506, 2018.
- [22] M. S. Fuhaid, R. V Murali, M. A. Maleque, P. K. Krishnan, and M. A. Rahaman, "Synthesis and Characterization of Aluminium Composite with Graphene Oxide Reinforcement," in IOP Conference Series: Materials Science and Engineering, IOP Publishing, 2021, p. 12005.
- [23] Α. Μ. Α. Abdo, "Utilizing Reclaimed Asphalt Pavement (RAP) Materials in New Pavements A Review," International Journal of Thermal and Environmental Engineering, vol. 12, no. 1, pp. 10-16, 2015, doi: 10.5383/ijtee.12.01.008.
- [24] K. S. Randhawa, "A state-of-the-art review on advanced ceramic materials: fabrication, characteristics, applications, and wettability," Pigment & Resin Technology, 2023.
- [25] L. Singh, B. Singh, and K. K. Saxena, "Manufacturing techniques for metal matrix composites (MMC): an overview," Advances in Materials and Processing Technologies, vol. 6, no. 2, pp. 441-457, 2020.
- [26] S. J. Huang, A. Abbas, and B. Ballóková, "Effect of CNT on microstructure, dry sliding wear and compressive mechanical properties of AZ61 magnesium alloy," Journal of Materials Research and Technology, vol. 8, no. 5, pp. 4273-4286, 2019.
- [27] A. Ramanathan, P. K. Krishnan, and R. Muraliraja, "А review on the production of metal matrix composites through stir casting-Furnace design, properties, challenges, and research opportunities," Journal of Manufacturing processes, vol. 42, pp. 213-245, 2019.
- [28] E. Bayraktar and D. Katundi, "Development of a new aluminium matrix composite reinforced with iron oxide (Fe3O4)," Journal of achievements in materials and manufacturing engineering, vol. 38, no. 1, pp. 7-14, 2010.
- [29] B. B. Verma, J. D. and Atkinson, and M. Kumar, "Study of fatigue behaviour of 7475 aluminium alloy," Bulletin of Materials Science, vol. 24, pp. 231-236, 2001.
- [30] M. Jimenez-Martinez and M. Alfaro-Ponce, "Effects of synthetic data applied to artificial neural networks for fatigue life prediction in nodular cast iron," Journal of the Brazilian Society of Mechanical Sciences and Engineering, vol. 43, no. 1, p. 10, 2021.
- [31] J. F. Barbosa, J. A. F. O. Correia, R. C. S. F. Júnior, and A. M. P. De Jesus, "Fatigue life prediction of metallic materials considering mean stress effects by means of an artificial neural network," International Journal of fatigue, vol. 135, p. 105527, 2020.
- [32] S. Malakar, A. kumar Malaker, M. N. Islam, H. Karmaker, and A. Siddique, "Mechanical characterization of Aluminum Matrix Composite Reinforcement with Fly Ash, Al2O3 and Fe2O3".
- [33] S. M. Jiaad, K. D. Salman, and A. A. Hussein, "Evaluation the microstructure, physical, magnetic and electrical properties of Al/Fe3O4+ Ni hybrid nanocomposite," in Journal of Physics: Conference Series, IOP Publishing, 2021, p. 12094.
- [34] N. S. Radhi, A. M. Nattah, and Z. S. Al-Khafaji, "Identify the effect of Fe2O3 nanoparticles on mechanical and microstructural characteristics of aluminum matrix composite produced by powder metallurgy technique,” Open Engineering, vol. 14, no. 1, p. 20220519, 2024.
- [35] N. S. Radhi, A. H. Jasim, Z. S. Al-khafaji, and M. Falah, "Investigation of Hematite Nanoparticles According to Mechanical Characteristics of Aluminium Matrix Composite," Nanosistemi, Nanomateriali, Nanotehnologii, vol. 21, no. 4, pp. 769-778, 2023.
- [36] A. J. Salman, "Experimental Analysis of In-situ Composite Al-Si Eutectic Alloy"." MSc thesis, university of Babylon, 2009.
- [37] ASTM-E9, "Compression Testing of Metallic Materials at Room Temperature," ASTM International, West Conshohocken, pp. 517-543, 2015.
- [38] W. Conshohocken, "ASTM G99-17, standard test method for wear testing with a pin-on-disk apparatus, ASTM International," Wear, vol. 1, pp. 1–5, 2017.
- [39] N. M. Dawood, N. S. Radhi, and Z. S. Al-Khafaji, "Investigation corrosion and wear behavior of Nickel-Nano silicon carbide on stainless steel 316L," in Materials Science Forum, Trans Tech Publ, 2020, pp. 33-43.
- [40] X. Ren, W. Zhang, Y. Zhang, P. Zhang, and J. Liu, "Effects of Fe2O3 content on microstructure and mechanical properties of CaO-Al2O3-SiO2 system," Transactions of Nonferrous Metals Society of China, vol. 25, no. 1, pp. 137- 145, 2015.
- [41] D. S. Ng et al., "Influence of SiO2, TiO2 and Fe2O3 nanoparticles on the properties of fly ash blended cement mortars," Construction and Building Materials, vol. 258, p. 119627, 2020.
- [42] K. Ma et al., "Mechanical behavior and strengthening mechanisms in ultrafine grain precipitation-strengthened aluminum alloy," Acta Materialia, vol. 62, pp. 141-155, 2014.
- [43] F. Bosio, P. Fino, D. Manfredi, and M. Lombardi, "Strengthening strategies for an Al alloy processed by in-situ alloying during laser powder bed fusion," Materials & Design, vol. 212, p. 110247, 2021.
- [44] M. Nuthalapati, "Development of Nano-Tio2/Y203 Dispersed Zirconium Alloys By Mechanical Alloying Followed By Conventional and Spark Plasma Sintering." 2016.
- [45] A. Rozhkovskaya, "Synthesis of high quality zeolite from alum sludge for water treatment applications." Queensland University of Technology, 2021.
- [46] M. S. L. Amirkhanyan, "Thermodynamic properties of intermetallics." Technische Universität Bergakademie Freiberg Saxony, Germany, 2017.
9. Copyright:
- This material is a paper by "Khaldun Aldawoudi, Ayad Mohammed Nattah, Nabaa Sattar Radhi, Zainab S. Al-Khafaji, Manar Khaleel Ibrahim": Based on "Identify Microstructure and Mechanical Behavior of Aluminum Hybrid Nano Composite Prepared by Casting Technique".
- Source of paper: https://doi.org/10.59038/jjmie/190112
This material was created to introduce the above paper, and unauthorized use for commercial purposes is prohibited. Copyright © 2025 CASTMAN. All rights reserved.