This article introduces the paper "Heat treatment impact on the structure of die-cast magnesium alloys" published in the Journal of Achievements in Materials and Manufacturing Engineering in 2007.
1. Overview:
- Title: Heat treatment impact on the structure of die-cast magnesium alloys
- Authors:
- L.A. Dobrzańskia
- T. Tańskia
- L. Čížekb
- a Division of Materials Processing Technology, Management and Computer Techniques in Materials Science, Institute of Engineering Materials and Biomaterials, Silesian University of Technology, ul. Konarskiego 18a, 44-100 Gliwice, Poland
- b Faculty of Metallurgy and Materials Engineering, Technical University of Ostrava, Tř.17 Listopadu 15, 708 33 Ostrava, Czech Republic
- Published Year: 2007
- Published Journal/Conference: Journal of Achievements in Materials and Manufacturing Engineering, Volume 20, Issues 1-2, January-February 2007
- Keywords:
- Heat treatment
- Metallography
- Magnesium alloys
- Structure
2. Research Background:
- Research Topic's Social/Academic Context:
- The paper highlights the increasing importance of material selection based on various factors including mechanical properties, design considerations, environmental impact, urbanization demands, recyclability, cost-effectiveness, availability, and weight.
- "The strive to decrease the weight of products becomes an important challenge for designers and process engineers."
- Magnesium alloys are presented as promising materials due to their low density and high strength, making them suitable for applications requiring weight reduction, particularly in the automotive industry.
- "A desire to create as light vehicle constructions as possible and connected with it low fuel consumption have made it possible to make use of magnesium alloys as a constructional material in automotive industry."
- Magnesium alloys are already "successfully used for a long time in different industry branches" due to "a combination of low density and high strength".
- Their low inertia is beneficial in "fast moving elements, in locations where rapid velocity changes occur and in products in which lowering a final mass of a product is required."
- The automotive industry shows significant and ongoing interest in magnesium alloys.
- Limitations of Existing Research:
- While not explicitly stating limitations of prior research, the study implicitly addresses the need for a deeper understanding of how chemical composition and heat treatment processes affect the microstructure and properties of die-cast magnesium alloys. This suggests a gap in detailed knowledge regarding the specific alloy MCMgAl6Zn1 and the optimization of its properties through heat treatment.
- Necessity of Research:
- The research is necessary to "aim at defining the influence of a chemical composition and precipitation processes on the structure and casting magnesium alloy properties in its as-cast state and after heat treatment with a different content of alloy components."
- Specifically, the study focuses on the MCMgAl6Zn1 magnesium cast alloy, investigating the impact of heat treatment on its microstructure. This is crucial for optimizing the use of this alloy in applications where specific mechanical properties are required.
3. Research Purpose and Research Questions:
- Research Purpose:
- The primary purpose is to investigate and present the "investigation results of the casting magnesium alloy in its as-cast state and after heat treatment."
- The study aims to define "the influence of a chemical composition and precipitation processes on the structure and casting magnesium alloy properties in its as-cast state and after heat treatment with a different content of alloy components."
- Core Research Questions:
- How does heat treatment affect the microstructure of die-cast MCMgAl6Zn1 magnesium alloy?
- What are the changes in the phases and their distribution within the microstructure of MCMgAl6Zn1 alloy after different heat treatment processes?
- How do solution treatment and aging processes influence the precipitation of intermetallic phases in MCMgAl6Zn1 alloy?
- Research Hypothesis:
- While not explicitly stated as a formal hypothesis, the research operates under the implicit hypothesis that heat treatment will significantly alter the microstructure of the MCMgAl6Zn1 magnesium alloy, leading to changes in the distribution and morphology of intermetallic phases compared to the as-cast state. This microstructural modification is expected to influence the overall properties of the alloy.
4. Research Methodology:
- Research Design:
- The study employs an experimental research design focused on comparative analysis of the microstructure of MCMgAl6Zn1 magnesium alloy in the as-cast condition and after undergoing various heat treatment processes.
- Data Collection Method:
- Material Preparation: MCMgAl6Zn1 magnesium alloy was cast in an induction crucible furnace using a protective salt bath "Flux 12" and ceramic filters at a melting temperature of "750±10°C". "Emgesalem Flux 12" was used for refining. Casting was performed in dies with betonite binder.
- Heat Treatment: Cast alloys were subjected to heat treatment in an "electrical vacuum furnace Classic 0816 Vak" in a protective argon atmosphere. Four different heat treatment conditions were applied (Table 3 in the original paper):
- Condition 0: As-cast
- Condition 1: Solution treatment at 430°C for 10 minutes, air cooling.
- Condition 2: Solution treatment at 430°C for 10 minutes, water cooling.
- Condition 3: Solution treatment at 430°C for 10 minutes, furnace cooling.
- Condition 4: Solution treatment at 430°C for 10 minutes, water cooling, followed by aging treatment at 190°C for 15 minutes, air cooling.
- Microscopy:
- Light Microscopy: Observations were made using a "light microscope LEICA MEF4A at magnification 500x".
- Scanning Electron Microscopy (SEM): "Electron scanning microscope Opton DSM-940" was used for higher magnification imaging.
- Microanalysis:
- Energy Dispersive Spectroscopy (EDS): "Opton DSM-940 scanning microscope with the Oxford EDS LINK ISIS dispersive radiation spectrometer at the accelerating voltage of 15 kV" was used for qualitative and quantitative microanalysis and surface distribution analysis of elements.
- X-ray Microanalyzer: "JEOL JCXA 733 x-ray microanalizer" was also utilized for microanalysis.
- Metallographic Preparation: Specimens were mounted in thermohardening resins and etched with "a 5% molybdenic acid" for "5-10 s" to reveal grain boundaries and microstructure.
- Analysis Methods:
- Metallographic Examination: Microstructures were analyzed using light and scanning electron microscopy to identify phases, grain boundaries, and precipitates in as-cast and heat-treated samples.
- Chemical Composition Analysis: EDS and X-ray microanalysis were used to determine the chemical composition of the alloy and to analyze the distribution of elements within the microstructure, particularly in different phases and precipitates.
- Qualitative and Quantitative Microanalysis: These techniques were employed to identify the types of phases present and to quantify the elemental composition of these phases.
- Research Subject and Scope:
- The research focuses on the MCMgAl6Zn1 magnesium cast alloy.
- The scope of the study includes investigating the microstructure in the as-cast state and after four different heat treatment conditions, encompassing solution treatment with varying cooling methods and a subsequent aging treatment.
5. Major Research Findings:
- Core Research Findings:
- As-Cast State: The microstructure of MCMgAl6Zn1 alloy in the as-cast state is characterized by:
- "a microstructure of the solid solution α constituting the alloy matrix".
- "the β - Mg17Al12 discontinuous intermetallic phase in the forms of plates located mostly at grain boundaries."
- "the phase AlMnFe with irregular shape, occurred often in the shape of blocks or needles".
- "the Laves phase Mg2Si".
- "in the vicinity of the β intermetallic phase precipitations the presence of the needle eutectics (α+β) has been revealed".
- Solution Treatment (Conditions 1, 2, 3):
- After solutioning, "trace quantities of the β (Mg17Al12) phase and single precipitations of a Mg2Si phase in the structure of the alloy" were observed.
- "There have not been noticed any locations of eutectic occurrences in the structure" after solution treatment with water cooling (Condition 2).
- After cooling bell annealing (furnace cooling, Condition 3), "the structure of the solid solution α with many precipitations of the secondary phase β has been revealed (locations resembling eutectics)."
- "The precipitations of the β (Mg17Al12) phase, located at grain boundaries and the Mg2Si phase located mostly at the phase β boundary have also been observed."
- The structure after furnace cooling (Condition 3) is "similar to the structure of the as-cast alloy".
- Aging Treatment (Condition 4):
- The applied aging process "has caused the release of the β phase at grain boundaries as well as in the form of pseudo eutectic locations."
- "There have been revealed, in the structure of the material, the parallel twinned crystals".
- As-Cast State: The microstructure of MCMgAl6Zn1 alloy in the as-cast state is characterized by:
- Statistical/Qualitative Analysis Results:
- EDS Analysis: "The results of the EDS chemical composition analysis confirm the presence of magnesium, aluminum, manganese, and zinc, constituting the structure of a solid solution". It also confirmed the presence of "manganese, and zinc, also Fe and Si".
- Microstructural Observations (Figure 1):
- Figure 1a (As-cast): Shows the β-Mg17Al12 phase at grain boundaries and needle-like eutectics.
- Figure 1b (Heat Treatment 2 - Solution & Water Quench): Demonstrates a reduction in the β phase and absence of eutectic structures.
- Figure 1c (Heat Treatment 3 - Solution & Furnace Cool): Shows reappearance of β phase precipitates, resembling eutectic locations.
- Figure 1d (Heat Treatment 4 - Solution, Water Quench & Aging): Reveals β phase precipitation at grain boundaries and pseudo-eutectic locations, along with parallel twinned crystals.
- Chemical Composition (Table 2): The chemical composition of the investigated alloy is provided in Table 2, confirming the presence of main elements:
- Al: 5.624 %
- Zn: 0.46 %
- Mn: 0.16 %
- Si: 0.034 %
- Fe: 0.07 %
- Pb: 0.034 %
- Ce: 0.01 %
- Mg: 93.6 %
- Rest: 0.008 %
- Data Interpretation:
- Heat treatment significantly alters the microstructure of the MCMgAl6Zn1 magnesium alloy by modifying the distribution and morphology of the β-Mg17Al12 intermetallic phase.
- Solution treatment effectively reduces the presence of the β phase, especially with rapid cooling (water quenching).
- Furnace cooling after solution treatment leads to the re-precipitation of the β phase, resembling the as-cast structure.
- Aging treatment after solutioning promotes further precipitation of the β phase at grain boundaries and in pseudo-eutectic regions, and induces the formation of parallel twinned crystals.
- The presence of Al, Mn, Fe, and Si contributes to the formation of various intermetallic phases, influencing the overall microstructure and potentially the properties of the alloy.
- "The chemical analysis of the surface element decomposition and the quantitative micro analysis made on the transverse microsections have also confirmed the evident concentrations of magnesium, silicon, aluminium, manganese and iron what suggests the occurrence of precipitations containing Mg and Si with angular contours, as well as phases with high Mn and Al concentrations that are irregular with a non plain surface, often occurring in the forms of blocks or needles."
- "A prevailing participation of magnesium and aluminium and a slight concentration of Zn has been ascertained in the alloy matrix as well as in the location of eutectics and big precipitations that arouse at phase boundaries identified as Mg17Al12."
- Figure Name List:
- Fig 1. Microstructure alloy MCMgAl6Zn1:
- a) without heat treatment - 0
- b) after heat treatment - 2
- c) after heat treatment - 3
- d) after heat treatment - 4
- Fig 1. Microstructure alloy MCMgAl6Zn1:
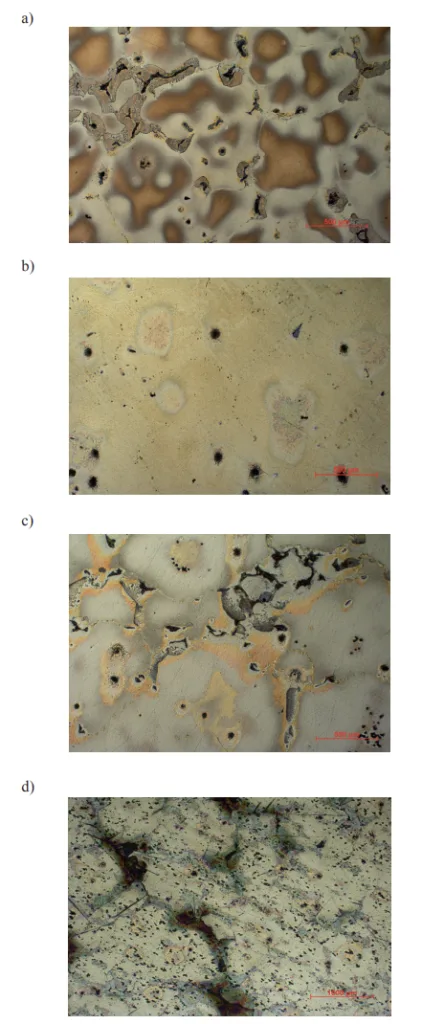
6. Conclusion and Discussion:
- Summary of Key Results:
- The study successfully demonstrated the impact of heat treatment on the microstructure of die-cast MCMgAl6Zn1 magnesium alloy.
- As-cast microstructure is characterized by α solid solution, β-Mg17Al12 phase at grain boundaries, AlMnFe, and Mg2Si phases.
- Solution treatment reduces the β-Mg17Al12 phase, with water quenching being more effective.
- Furnace cooling after solution treatment leads to β-Mg17Al12 re-precipitation.
- Aging treatment after solutioning further precipitates β-Mg17Al12 and induces twinned crystal formation.
- Research's Academic Significance:
- The research contributes to the fundamental understanding of the phase transformations and microstructural evolution in MCMgAl6Zn1 magnesium alloy during different heat treatment processes.
- It provides valuable insights into the influence of solution treatment and aging on the precipitation behavior of intermetallic phases, particularly β-Mg17Al12, in this specific magnesium alloy.
- This knowledge is crucial for materials scientists and engineers working with magnesium alloys, aiding in the design of optimized heat treatment cycles to achieve desired microstructures and properties.
- Practical Implications:
- The findings have practical implications for the die casting industry, particularly in the processing of MCMgAl6Zn1 magnesium alloy for automotive and other lightweight applications.
- Understanding the effects of different cooling rates and aging parameters allows for tailoring heat treatment processes to optimize the microstructure and potentially enhance mechanical properties such as strength, ductility, and corrosion resistance.
- The research supports the use of heat treatment as a viable method to modify and control the microstructure of die-cast magnesium alloys to meet specific performance requirements.
- "According to the alloys characteristic, the applied cooling rate and alloy additions seems to be a good compromise for mechanical properties and microstructures, nevertheless further tests should be carried out in order to examine different cooling rates and parameters of solution treatment process and aging process."
- Research Limitations:
- The study is limited to the specific MCMgAl6Zn1 magnesium alloy and the investigated heat treatment parameters.
- "further tests should be carried out in order to examine different cooling rates and parameters of solution treatment process and aging process." This suggests that the research is not exhaustive in exploring the entire range of heat treatment possibilities for this alloy.
- The paper primarily focuses on microstructural characterization. Mechanical property evaluation is suggested for future work to fully correlate microstructure with performance.
7. Future Follow-up Research:
- Future Research Directions:
- Further research should focus on "further tests… to examine different cooling rates and parameters of solution treatment process and aging process."
- Investigating the impact of varying solution treatment temperatures and times on microstructure evolution.
- Exploring a wider range of aging temperatures and durations to optimize precipitation hardening effects.
- Studying the influence of heat treatment parameters on the mechanical properties (tensile strength, yield strength, elongation, hardness, fatigue resistance) and corrosion behavior of MCMgAl6Zn1 alloy.
- Areas for Additional Exploration:
- Detailed quantitative analysis of phase fractions and grain size under different heat treatment conditions.
- Transmission electron microscopy (TEM) analysis to further characterize the morphology and crystallography of precipitates.
- Modeling and simulation of phase transformations during heat treatment to predict microstructure evolution and optimize processing parameters.
- Investigating the effect of heat treatment on other magnesium alloys and die casting processes.
8. References:
- [1] K.U. Kainer, Sb. Int. Congress Magnesium Alloys and their Application, Mnichov, 2000, 534-608.
- [2] J.F.Grandfield, J.A.Taylor, Tensile cohereny in semi-solid AZ91, Held during the TMS Annual Meting in Seattle, Washington, USA, 2002.
- [3] H. Baker: ASM Specialty Handbook. Magnesium and Magnesium Alloys, ed. Avedesian, ASM International, The Materials Information Society, USA 1999, 3-84.
- [4] A.K. Dahle, D.N. StJohn, "The Origin of Banded Defects in High Pressure Die Cast Magnesium Alloys", World of Die Casting, Cleveland T99-062.
- [5] J.M. Tartaglia, J.C. Grebetz, “Observations of Intermetallic Particle and Inclusion Distributions in Magnesium Alloys", The Minerals, Metals&Materials Society, 2000.
- [6] B.L. Mordike, T. Ebert: Magnesium. Properties-applications-potential, Materials Science and Enrineering nr A302, Journal of Materials Processing Technology, 117 (2001) 37-45.
- [7] L. Čížek, M. Greger, L. Pawlica, L.A. Dobrzański, T. Tański: Study of selected properties of magnesium alloy AZ91 after heat treatment and forming, Journal of Materials Processing Technology, 157-158 (2004) 466-471.
- [8] A. Maltaisa, D. Dubé, M. Fiseta, G. Larochea, S. Turgeon: Improvements in the metallography of as-cast AZ91 alloy, Materials Characterization, 52 (2004) 103-119.
- [9] L.A. Dobrzański, T. Tański, L. Čížek, Influence of modification with chemical elements on structure of magnesium casting alloys, 13th Scientific International Conferences "Achievements in Mechanical and Materials Engineering AMME', 2005", Gliwice - Wisła 2005, 199-202.
- [10] L.A. Dobrzański, T. Tański, L. Čížek, Influence of Al addition on structure of magnesium casting alloys, Journal of Achievements in Mechanical and Materials Engineering, 17 (2006) 221-224.
- [11] R.M. Wang, A. Eliezer, E. Gutman, Microstructures and dislocations in the stressed AZ91D magnesium alloys, Materials Science and Engineering, A344 (2002) 279-287.
- [12] K. Ishikawaa, H. Watanabea, T. Mukaib, High strain rate deformation behavior of an AZ91 magnesium alloy at elevated temperatures, Materials Letters, 59 (2005) 1511-1515.
- [13] K. Iwanaga, H. Tashiro, H. Okamoto, K. Shimizu: Improvement of formability from room temperature to warm temperature in AZ31 magnesium alloy, Journal of Materials Processing Technology, 155-156 (2004) 1313-1316.
- [14] H. Friedrich, S. Schumann, Research for a "new age of magnesium" in the automotive industry, Journal of Materials Processing Technology, 117 (2001) 276-281.
- [15] A. Fajkiel, P. Dudek: Foundry engineering - Science and Practice, Publishers Institute of Foundry engineering, Cracow, 2004, 18-21.
9. Copyright:
- This material is based on the paper: Heat treatment impact on the structure of die-cast magnesium alloys. Dobrzański, T. Tański, L. Čížek
This material is a summary based on the above paper, and unauthorized use for commercial purposes is prohibited.
Copyright © 2025 CASTMAN. All rights reserved.