Hardik Lakhlani, Jyotirmoy Barman, Karan Rajput, and Angshuman Goswami
VE Commercial Vehicles Ltd
ABSTRACT
Future emissions regulations like BSIV and above in India, Diesel engine manufacturers are forced to find complex ways to reduce exhaust gas pollutant emissions, in particular NOx and particulate matter (PM). Exhaust gas recirculation (EGR) into the engine intake is an established technology to reduce NOx emissions. The distribution of EGR in each cylinder plays vital role in combustion process and hence it will affect exhaust emissions. The influence of EGR mixture design and its effect on distribution across the cylinder has significant impact on the NOx-PM trade-off which is studied on light duty direct injection diesel engine. A simulation and experimental study of EGR mixer design is conducted to explain this effect and the distribution of EGR across the cylinder at different EGR flow rate. Experiments have been conducted on an engine test bench with and without air-EGR mixer and demonstrated that variations in cylinder-to-cylinder EGR distribution results in a deteriorated NOx-PM trade-off (increased NOx emission level at a given PM emission level, or increased PM emission level at a given NOx emission level) as compared to the well mixed with EGR mixture configuration with equal EGR rate for all the cylinders. The aim of this study is to show that EGR mixture effect & cylinder-to-cylinder variations in EGR can lead to higher NOx and PM emissions as compared to a configuration where the EGR is equally distributed amongst all cylinders. The influence of the NOx-PM trade-off has been experimentally studied in details.
INTRODUCTION
Light-duty trucks play the main role in FMCG logistics and intercity transportation. In India higher subsidy in diesel fuel forced commercial vehicle manufacturers to develop trucks with diesel engines, which are superior for fuel economy and low-end torque due to higher thermal efficiency. Meanwhile, regulations on the harmful diesel exhaust emissions coming out from engines have been increasingly stringent. Meeting BSIV emission norms has become quite complex by introduction of cost effective EGR system in high rating engine. Study of EGR application is very important topic nowadays.
Turbo-charging, high-pressure fuel injection, exhaust gas recirculation (EGR) and exhaust after-treatments have been successfully used in combination to comply with emission legislations of various stages. Among Technical routes to implement emission control, the EGR system is an external device used to control NOx emissions, which has been regarded as an in-engine purification measure for reorganizing the intake and adjusting the in-cylinder combustion process [8, 9].
Engine having EGR emission system where homogeneously exhaust gas mixes with fresh intake charge is very important from the emission & engine fuel consumption point of view. Proper exhaust gas mixing and distribution across cylinder to cylinder will lead to robust engine exhaust gas emission control. The study was conducted on LDT engine's ESC cycle (Figure 15) which had low load, part load & full load with different operating speeds. EGR is one of the most cost effective techniques which are currently available for reducing NOx emissions in internal combustion engines however in the case of diesel engines; they result in worsening of specific fuel consumption and particulate emissions [3, 4, 5].
In particular, EGR aggravates the trade-off between NOx and particulate emissions, especially at high loads. The EGR system reduces NOx emissions by introducing concentration of the exhaust gas into the combustion chamber to increase the heat capacity of mixture hence lower the temperature of burning gases reduce the NOx emission. As EGR would result in the combustion lag and reduced the temperature [10], there is also a possibility that HC, CO, and PM emission would increase. [11].
It is very important in inline multi-cylinder engine that EGR distribution across all cylinders should be uniform. Improper charge (i.e. Fresh air + EGR) distribution leads to uneven charge combustion and unpredictable exhaust emission. Therefore, to achieve the best power performance of engine and the lowest emissions, it is required to figure out a proper EGR rate in each cylinder, by using EGR mixture techniques with EGR system [12].
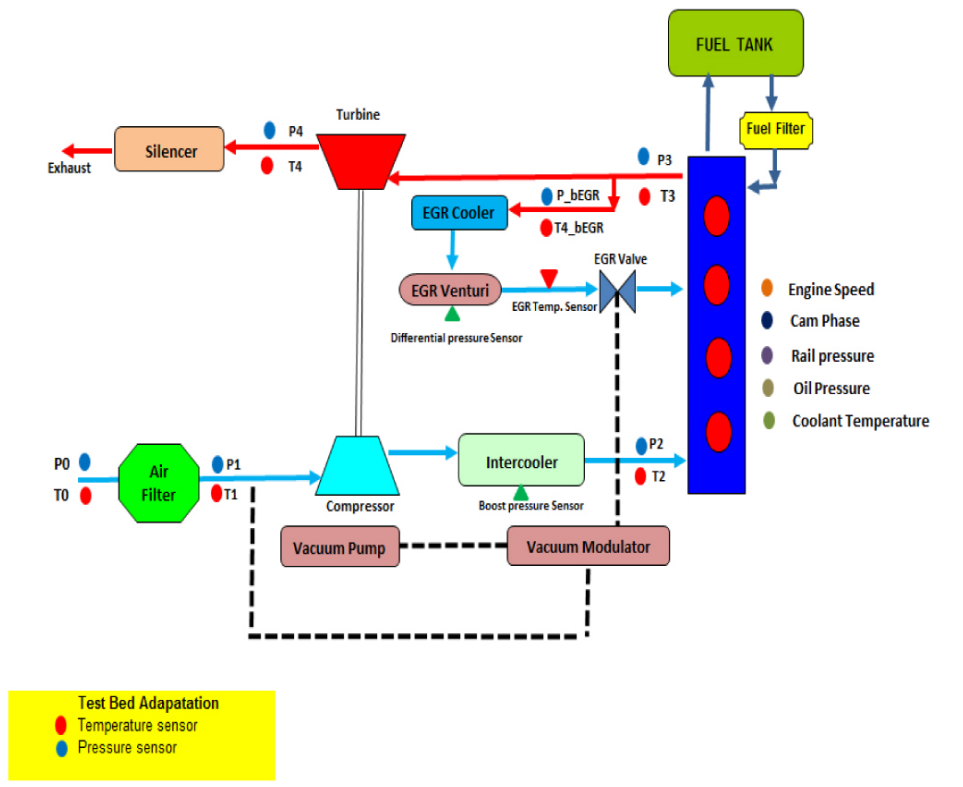
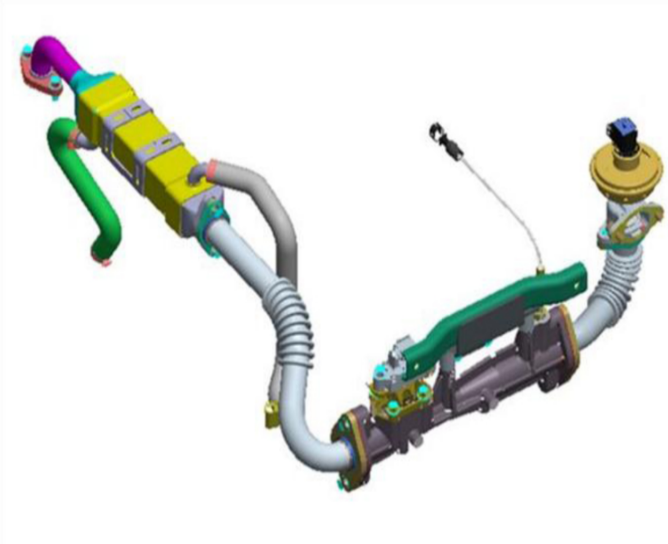
CONCLUSION
Experiments were carried out to analyze the effect of different multiple injection strategies with EGR system on reduction of emissions, torque and BSFC improvement of 3.7 liters diesel engine. Major findings from this study are summarized as follows:
Related Topics:
REFERENCES
- Heywood, J. B., Internal Combustion Engine, McGrawHill Publishing Company, New York, 1988.
- Lapuerta M, Hernandez JJ, Gimenez F. Evaluation of exhaust gas recirculation as a technique for reducing Diesel engine NOX emissions. Proc Instn Mech Engrs Part D, J
Autom Engng 2000;214:85-93. - Ladommatos N, Abdelhalim SM, Zhao H, Hu Z. The effects of carbon dioxide in exhaust gas recirculation on Diesel engine emission. Proc Instn Mech Engng part D J
Autom Engng 1998; 212:25-42. - Beatric C et al. Influence of high EGR rate on emissions of a DI Diesel engine. ASME ICE Div 1998;ICE 22:193-201.
- Baert, R., Beckman, D., and Verbeek, R., “New EGR Technology Retains HD Diesel Economy with 21st Century Emissions,” SAE Technical Paper 960848, 1996, doi:
10.4271/960848. - Dekker, H. and Sturm, W., “Simulation and Control of a HD Diesel Engine Equipped with New EGR Technology,”
SAE Technical Paper 960871, 1996, doi:10.4271/960871. - Zelenka, P., Aufinger, H., Reczek, W., and Cartellieri, W.,
“Cooled EGR - A Key Technology for Future Efficient HD Diesels,” SAE Technical Paper 980190, 1998, doi:
10.4271/980190. - Ghaffarpour, M. and Baranescu, R., “NOx Reduction Using Injection Rate Shaping and Intercooling in Diesel Engines,” SAE Technical Paper 960845, 1996, doi:
10.4271/960845. - Kohketsu, S., Mori, K., Sakai, K., and Hakozaki, T.,
“EGR Technologies for a Turbocharged and Intercooled Heavy-Duty Diesel Engine,” SAE Technical Paper 970340,
1997, doi:10.4271/970340. - Changming G., Shufangetc Y. et al., “Emission characteristics of automobile turbocharged diesel engine with EGR,” Transactions of The Chinese Society for Agricultural
Machinery, vol. 36, no. 4, pp. 144-146, 2005. - Wasiu S. O., Sulaiman S. A., and Aziz A. R. A., “An experimental study of different effects of EGR rates on the performance and exhaust emissions of the stratified charge piston direct injection compressed natural gas engine,”
Journal of Applied Sciences, vol. 11, no. 9, pp. 1479-1490,
2011.
Downloaded from SAE International by Univ of California Berkeley, Friday, July 27, 2018 - Baert, R., Beckman, D., and Veen, A., “Efficient EGR Technology for Future HD Diesel Engine Emission Targets,”
SAE Technical Paper 1999-01-0837, 1999, doi:10.4271/1999-01-0837. - Udayakumar, R., Sundaram, S., and Sriram, R.,
“Reduction of NOx Emissions by Water Injection in to the Inlet Manifold of a DI Diesel Engine,” SAE Technical Paper 2003-01-0264, 2003, doi:10.4271/2003-01-0264. - Stumpp, G. and Banzhaf, W., “An Exhaust Gas
Recirculation System for Diesel Engines,” SAE Technical Paper 780222, 1978, doi:10.4271/780222. - Dürnholz, M., Eifler, G., and Endres, H., “Exhaust-Gas Recirculation - A Measure to Reduce Exhaust Emissions of DI Diesel Engines,” SAE Technical Paper 920725, 1992, doi:
10.4271/920725. - Tullis, S. and Greeves, G., “Improving NOx Versus BSFC with EUI 200 Using EGR and Pilot Injection for
Heavy-Duty Diesel Engines,” SAE Technical Paper 960843,
1996, doi:10.4271/960843. - Bazari, Z. and French, B., “Performance and Emissions Trade-Offs for a HSDI Diesel Engine - An Optimization Study,” SAE Technical Paper 930592, 1993, doi:
10.4271/930592. - Ladommatos, N., Balian, R., Horrocks, R., and Cooper, L., “The Effect of Exhaust Gas Recirculation on Soot Formation in a High-Speed Direct-injection Diesel Engine,”
SAE Technical Paper 960841, 1996, doi:10.4271/960841. - Egnell, R., “The Influence of EGR on Heat Release Rate and NO Formation in a DI Diesel Engine,” SAE Technical Paper 2000-01-1807, 2000, doi:10.4271/2000-01-1807.