This introductory paper is the research content of the paper ["Expanding Lightweight Design Potential by Hybrid Joining of Aluminum Sheets with Aluminum Casting Through Compound Sand Casting and Induction Heating"] published by ['Wiley-VCH GmbH'].
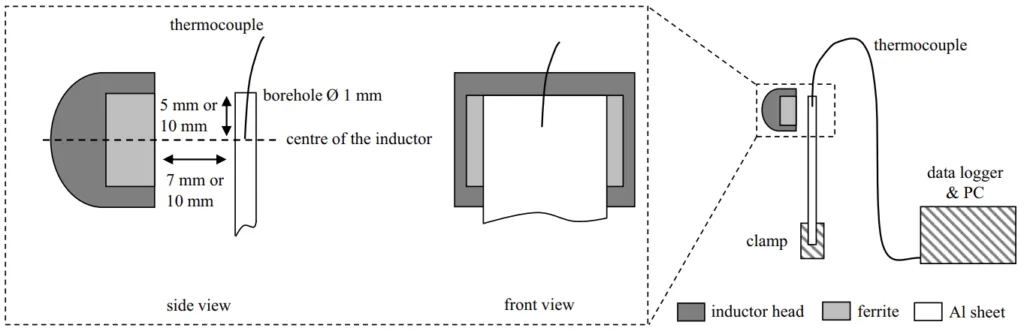
1. Overview:
- Title: Expanding Lightweight Design Potential by Hybrid Joining of Aluminum Sheets with Aluminum Casting Through Compound Sand Casting and Induction Heating
- Author: Christopher Locke, Raffael Pichler, Martin Guggemos, Wolfram Volk, and Daniel Günther
- Publication Year: 2024
- Publishing Journal/Academic Society: Advanced Engineering Materials
- Keywords: aluminum, car body, compound casting, induction, joining, lightweight
2. Abstracts / Introduction
Combining light metals like aluminum offers high weight-saving potential for automotive structures. Compound casting is promising, but creating metallic continuity between insert (sheet) and casting is difficult. This study uses induction heating to improve the metallic bond in aluminum-aluminum compound casting. Compression shear tests and microscopy characterize the bond. The research shows that sound metallic bonding is achieved with induction and no insert coating. Key factors include insert preheating and temperature. Heat treatment further increases bond strength.
3. Research Background:
Background of the Research Topic:
The European automotive industry is under pressure to reduce emissions, driving a need for lightweight materials and designs. Compound casting, joining sheet metal and cast metal, can meet complex structural component requirements. Specifically, aluminum-aluminum (Al-Al) compounds offer low density and contribute to a circular economy.
Status of Existing Research:
Existing research on Al-Al compound casting has focused on:
* Using metallic coatings (e.g., Zn, Ni, Cu) to remove the oxide layer and improve wetting.[16-22]
* Sufficient mold design and casting systems to remove the oxide film.[24]
* Inductive insert preheating of a zinc-coated steel sheet.[25]
* Production of thin-walled steel-Al structures.[26]
Necessity of the Research:
Prior studies demonstrate that is difficult point of Al-Al compound casting.
- Studies that different Al-Al compound casting processes can achieve a metalluc bond.[16-24]
- Only by inductive insert preheating of a zinc-coated steel sheet created a metallic bond.[25]
- Enhancing the compound sand casting process by inductive sheet preheating to form a hybrid process.[26]
This hybrid joining process has not yet been applied to Al alloys. The novelty of this study is to investigate the applicability of inductive sheet preheating to the Al-Al system.
4. Research Purpose and Research Questions:
Research Purpose:
To investigate the applicability of inductive sheet preheating to the Al-Al system in compound sand casting to improve metallic continuity. The aim is to expand further the lightweight design potential of Al-Al structures in sand casting.
Key Research:
- Investigate the heating behavior and influence of inductive preheating on the mechanical properties of EN AW-5754 (AlMg3) and EN AW-6082 (AlSi1MgMn) sheet inserts.
- Investigate the influence of casting temperature, induction power, coatings, casting wall thickness, and insert alloys on the metallic bond strength.
- Investigate the influence T6 heat treatment on the EN AW-6082/EN AC-42100
- Characterize the metallic bond strength using compression shear tests and microstructural analysis.
5. Research Methodology
Research Design:
Experimental study using a hybrid joining process combining compound sand casting and induction heating. An overlap joint sample was used to ensure a pure metallic bond.
Data Collection Method:
- Temperature measurement during inductive preheating using thermocouples (Figure 1).
- Tensile testing of preheated sheet metal specimens (Figure 2).
- Compression shear tests of compound casting samples (Figures 3, 4).
- Microstructural analysis using metallography (Figures 4,11).
- Optical emission spectrometer (Table 1)
Analysis Method:
- Quantitative analysis of temperature-time curves.
- Quantitative analysis of tensile properties (yield strength, tensile strength, elongation at break).
- Quantitative analysis of compression shear strength (comp = Fmax/A).
- Qualitative and quantitative analysis of microstructure (optical microscopy, element mapping).
Research Subjects and Scope:
- Insert materials: EN AW-5754 (AlMg3) and EN AW-6082 (AlSi1MgMn) sheets.
- Casting alloy: EN AC-42100 (AlSi7Mg03).
- Compound zone sizes: 20 x 30 mm² and 10 x 30 mm².
- Inductor-to-sheet distances: 7 mm and 10 mm.
- Induction power levels: 50%, 70%, 80%, and 90%.
- Casting temperatures: 720 ± 5 °C and 760 ± 5 °C.
- Casting wall thicknesses: 10 mm, 6 mm, and 4 mm.
- Coatings: Zn, Ni, and no coating.
- T6 heat treatment (for EN AW-6082/EN AC-42100 compounds).
6. Main Research Results:
Key Research Results:
- Inductive preheating significantly influences the insert temperature, with inductor-to-sheet distance having the greatest effect, followed by induction power, compound zone size, and chemical composition of the insert alloy (Figures 5 and 6).
- Inductive preheating has a minor effect on the tensile properties of EN AW-5754, but significantly reduces the strength of EN AW-6082 due to precipitate coarsening (Figures 7 and 8).
- Zn coatings showed poor performance due to blistering and low wettability (Figure 9).
- Ni coatings improved wettability, but the best results were achieved with uncoated inserts and inductive preheating (Figure 10).
- A higher casting temperature and induction heating generally improved metallic bond strength (Figure 10).
- Reducing casting wall thickness to 4 mm maintained strength levels comparable to 10 mm, demonstrating lightweight potential.
- T6 heat treatment significantly increased the strength of EN AW-6082/EN AC-42100 compounds (Figure 14).
Analysis of presented data:
- The influence of the compound zone, inductor-to-sheet distance, and induction power. (Figures 5 and 6).
- Inductive preheating hardly influences the tensile strength properties of the EN AW-5754. (Figure 7).
- Induction preheating strongly influences the tensile strength of the EN AW-6082 insert negatively. (Figure 8).
- Qualitative comparison of the influence of induction preheating on the Al sheet metal and coating. (Figure 9).
- Coating type and induction heating infulence of The metallic bond strength (Figure 10).
- The parameter study with EN AW-5754/EN AC-42100 Microstructure analysis. (Figure 11).
- Mapping of a Mg-P-rich phase (Figure 12).
- increasing dissolution with increasing temperature input between casting and uncoated insert. (Figure 13).
- The metallic bond strength and microstructure of EN AW-6082/EN AC-42100 depends on the configuration. (Figure 14, 15)
- SEM-EDX images of EN AW-6082/EN AC-42100 (Figure 16).
- Measured melt temperature in the crucible before casting: 760 ± 5 °C. (Figure 17).
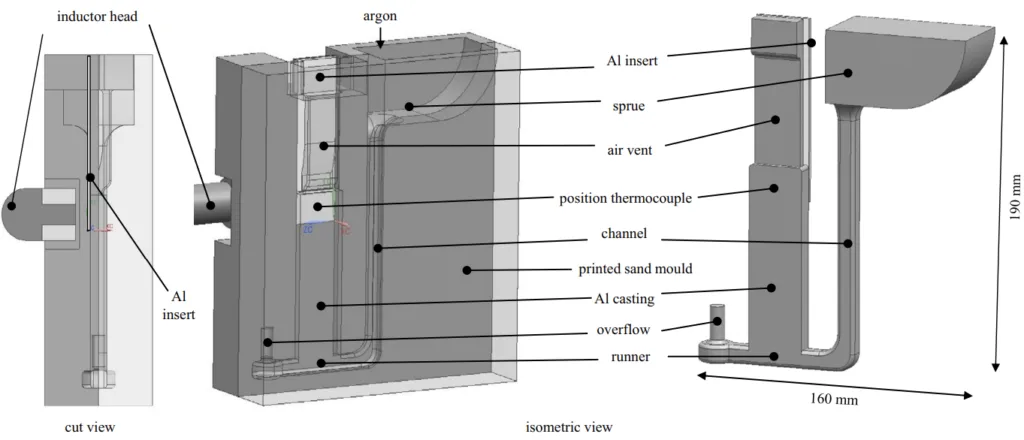
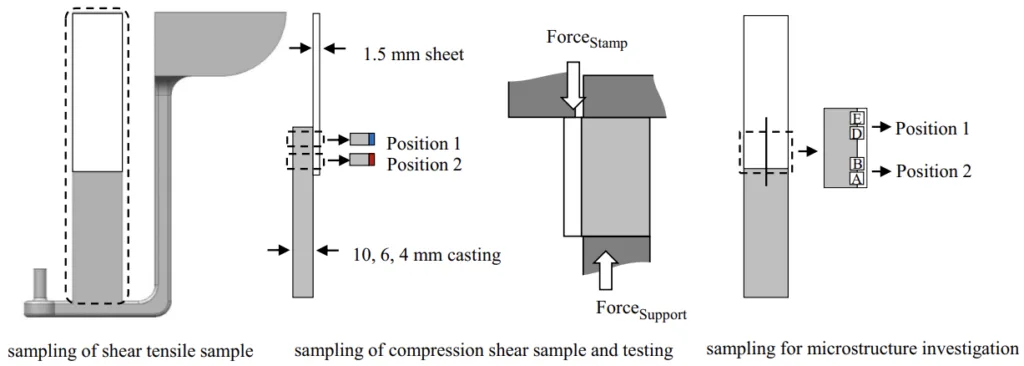
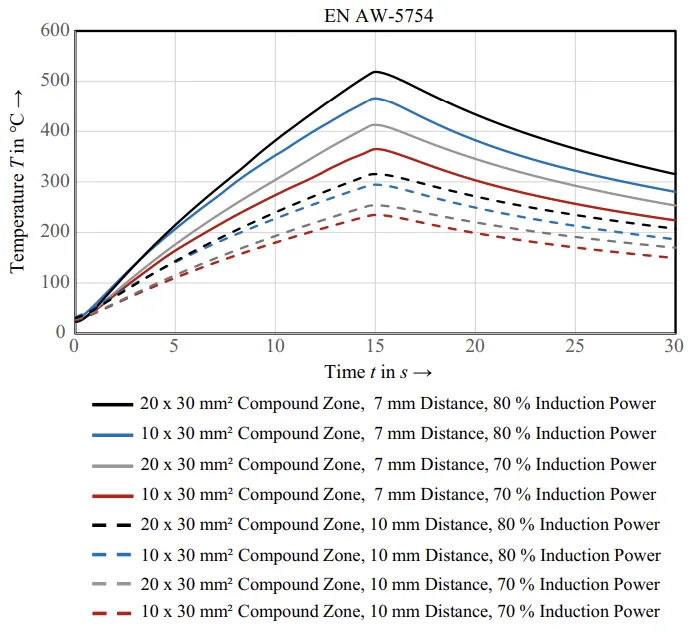
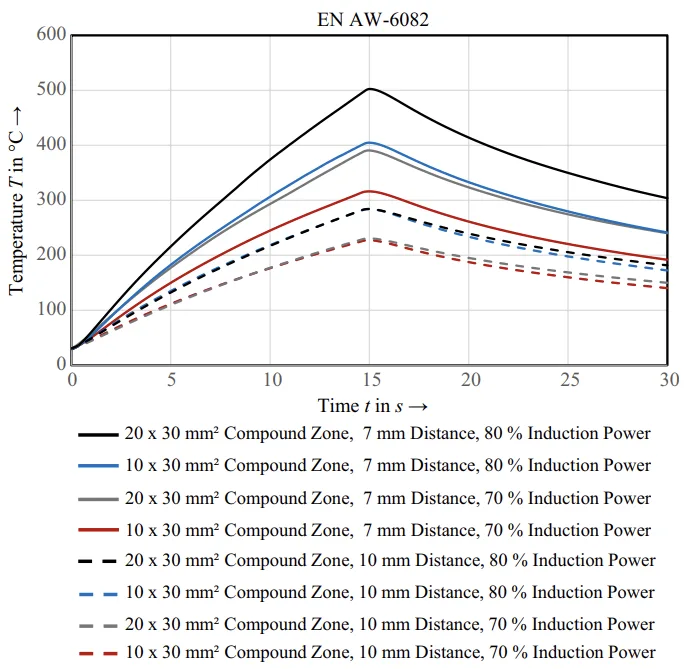
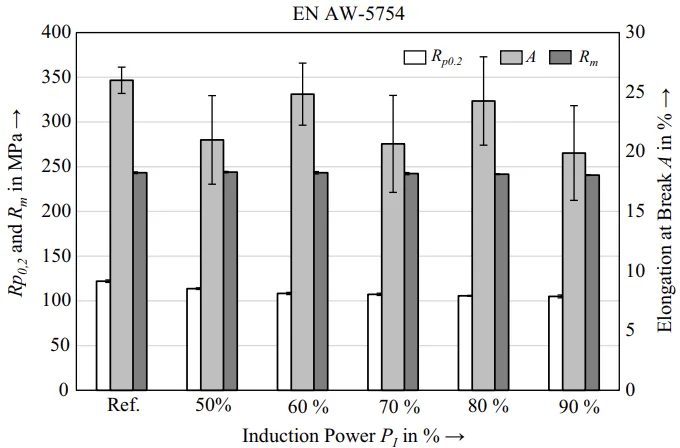
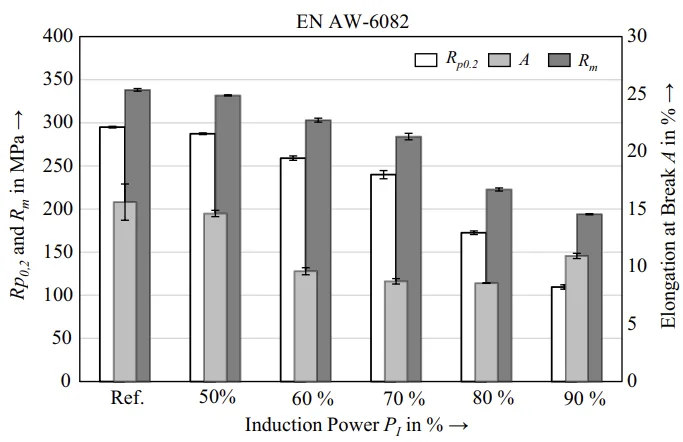
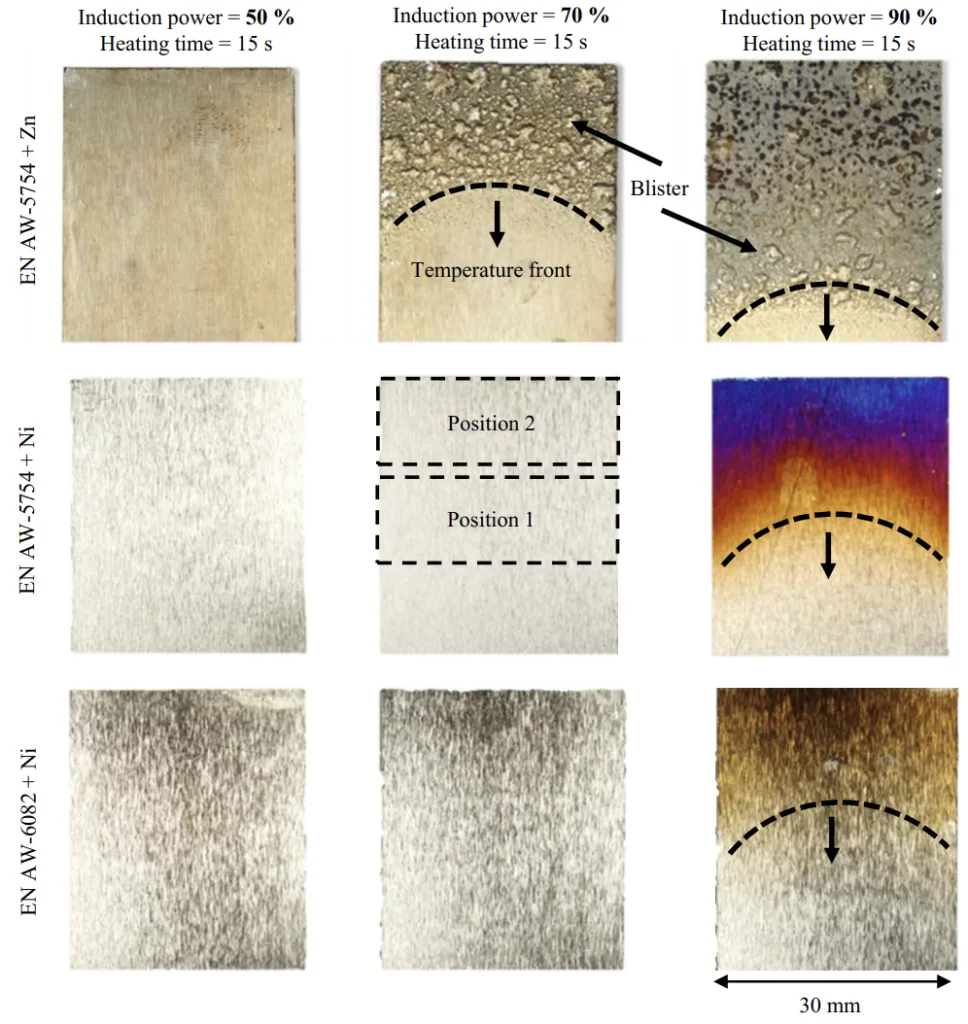
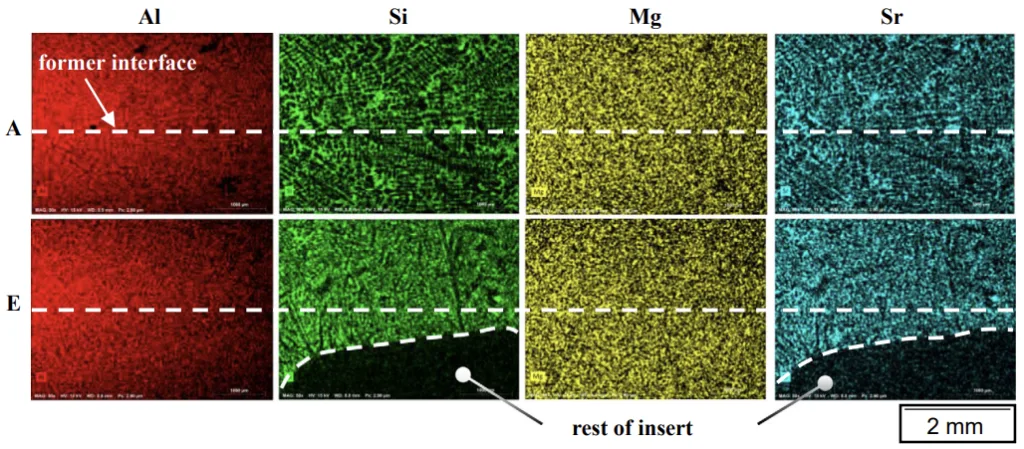
Figure Name List:
- Figure 1. Setup to measure the heating behavior of inductive preheated Al sheets.
- Figure 2. Setup to preheat Al sheets for tensile testing.
- Figure 3. Setup for hybrid joining through compound sand casting and induction heating.
- Figure 4. Sampling and experimental overview for Al-Al compound characterization.
- Figure 5. Temperature curves of EN AW-5754 with changes in the parameters of compound zone size, inductor to sheet distance, and induction power.
- Figure 6. Temperature curves of EN AW-6082 with changes in the parameters of compound zone size, inductor to sheet distance, and induction power.
- Figure 7. EN AW-5754 tensile properties are influenced by induction heating.
- Figure 8. EN AW-6082 tensile properties are influenced by induction heating.
- Figure 9. Qualitative comparison of the influence of induction preheating on the Al sheet metal and coating.
- Figure 10. The metallic bond strength EN AW-5754/EN AC-42100 depends on the configuration.
- Figure 11. Microstructure analysis of the parameter study with EN AW-5754/EN AC-42100 in the former area of the compound zone between both alloys. Images taken with 500x magnification.
- Figure 12. Element mapping of a Mg–P-rich phase in the configuration of Ni1 of the EN AW-5754/EN AC-42100 compound.
- Figure 13. EN AW-5754/EN AC-42100 compound. a) Microscopic overview images show a dislocation of the Ni coating. b) Increasing dissolution with increasing temperature input between casting and uncoated insert.
- Figure 14. The metallic bond strength of EN AW-6082/EN AC-42100 depends on the configuration.
- Figure 15. Microstructure analysis of the parameter study with EN AW-6082/EN AC-42100 in the former area of the compound zone between both alloys. Images taken with 500x magnification.
- Figure 16. SEM-EDX images of EN AW-6082/EN AC-42100 (x4T6) in areas A and E of the microscopic sample after T6 heat treatment.
- Figure 17. Melt temperature in the compound zone and cooling curves with different cast wall thicknesses. Measured melt temperature in the crucible before casting: 760 ± 5 °C.
7. Conclusion:
Summary of Key Findings:
- Compound sand casting with induction heating is a viable method for producing Al-Al hybrid structures.
- Insert coating is unnecessary if sufficient inductive preheating is applied.
- The insert temperature in the compound zone is the critical factor for achieving a sound metallic bond.
- EN AW-5754/EN AC-42100 compounds achieved strengths of 50-60 MPa (uncoated, 760 °C, 70% induction).
- EN AW-6082/EN AC-42100 compounds achieved strengths of 60-70 MPa (uncoated, 760 °C, 70% induction, T6 heat treatment).
- The hybrid joining process demonstrates high process stability.
Academic Significance of the Study:
- Challenges existing research that emphasizes the necessity of insert coatings for Al-Al compound casting.
- Demonstrates the effectiveness of induction heating as a means of enhancing metallic bonding in compound casting.
- Provides a deeper understanding of the process parameters influencing Al-Al compound casting.
Practical Implications:
- Offers a potential method for producing lightweight Al-Al structures for automotive applications.
- Could reduce production costs by eliminating the need for insert coatings and associated processes.
- Demonstrates the feasibility of using thinner casting walls, further enhancing lightweight potential.
Limitations of the Study and Areas for Future Research:
- Only flat sheet inserts were investigated; other geometries (tubes, profiles) should be studied.
- Further investigation of different load types and sample geometries is needed.
- The contribution of force-fit and form-locking to overall compound strength should be explored.
- Adaptation of inductor head geometry for complex insert shapes is required.
- Transferring the process to low-pressure sand casting could improve performance.
- Process simulation would provide further insights.
8. References:
- [1] European Commission, CO2 Emission Performance Standards for Cars and Vans, https://doi.org/https://climate.ec.europa.eu/eu-action/ transport/road-transport-reducing-co2-emissions-vehicles/co2-emission- performance-standards-cars-and-vans_en (accessed: January 2024).
- [2] J. Meckling, J. Nahm, Energy Policy 2019, 126, 470.
- [3] N. S. X. Yu, Z. Y. Sandhu, M. Zheng, Appl. Energy 2020, 271, 115169.
- [4] D. L. McCollum, C. Wilson, M. Bevione, S. Carrara, O. Y. Edelenbosch, J. Emmerling, C. Guivarch, P. Karkatsoulis,
- I. Keppo, V. Krey, Z. Lin, E. Ó Broin, L. Paroussos, H. Pettifor, K. Ramea, K. Riahi, F. Sano, B. S. Rodriguez, D. P. van Vuuren, Nat. Energy 2018, 3, 664.
- [5] F. Czerwinski, Materials 2021, 14, 6631.
- [6] Wen Zhang, Jun Xu, Mater. Des. 2022, 221, 110994.
- [7] D. Lehmus, Metals 2022, 12 1959.
- [8] T. A. Baser, E. Umay, V. Akinci, Eurasia Proc. Sci. Technol. Eng. Math. 2022, 21, 79.
- [9] G. Kopp, E. Beeh, Mater. Sci. Forum 2010, 638, 437.
- [10] S. Kleemann, D. Inkermann, B. Bader, E. Türck, T. Vietor, in 21st Int. Conf. Engineering Design (ICED17) 2017, p. 290, https://doi.org/10. 24355/dbbs.084-201708301114.
- [11] D. Lehmhus, A. von Hehl, J. Hausmann, K. Kayvantash, R. Alderliesten, J. Hohe, Adv. Eng. Mater. 2019, 21, 1900056.
- [12] A. Lange, Doctoral Dissertation 1998.
- [13] A. Bührig-Polaczek, W. Michaeli, G. Spur, Handbuch Urformen, Carl Hanser Verlag, München 2014, p. 98.
- [14] K. J. M. Papis, B. Hallstedt, J. F. Löffler, P. J. Uggowitzer, Acta Mater. 2008, 56, 3036.
- [15] O. Dezellus, N. Eustathopoulos, J. Mater. Sci. 2010, 45, 4256.
- [16] K. J. M. Papis, J. F. Loeffler, P. J. Uggowitzer, Sci. China Ser. E-Technol. Sci. 2009, 52, 46.
- [17] M. Rübner, M. Günzl, C. Körner, R. F. Singer, Mater. Sci. Eng.: A 2011, 528, 7024.
- [18] M. Schwankl, C. Koerner, D. Himmler, J. Mater. Process. Technol. 2014, 214, 1094.
- [19] J. Wedler, M. Schwankl, C. Körner, J. Mater. Process. Technol. 2016, 238, 160.
- [20] Q. Wang, T. Liu, Q. Wang, Y. Sui, W. Ding, Mater. Des.2015, 68, 8.
- [21] Q. Wang, T. Liu, Y. Sui, Q. Wang, J. Mater. Sci. Technol. 2016, 32, 298.
- [22] J. Feng, B. Ye, L. Zuo, Q. Wang, H. Jiang, W. Ding, Trans. A 2017, 48, 4632.
- [23] A. O. Bakke, L. Arnberg, Y. Li, IOP Conf. Ser.: Mater. Sci. Eng., 2019, 529, 012024.
- [24] S. Ji, Y. Zhang, G. Scamans, Z. Fan, J. Mater. Process. Technol. 2017, 243, 197.
- [25] C. Locke, M. Guggemos, M. Gruber, L. Maier, L. Mayr, T. Weiß, W. Volk, D. Günther, Metals 2023, 13, 354.
- [26] M. Guggemos, C. Locke, C. Hartmann, L. Maier, Wolfram Volk, Daniel Günther, J. Mater. Process. Technol. 2024, 324, 118261.
- [27] M. Timpel, N. Wanderka, R. Schlesiger, T. Yamamoto, N. Lazarev, D. Isheim, G. Schmitz, S. Matsumura, J. Banhart, Acta Mater. 2012, 60, 3920.
- [28] Springer Handbook of Condensed Matter and Materials Data, Springer, Deutschland 2006, p. 192.
- [29] W. Hesse, Aluminium-Schlüssel: Deutsch/Englisch, Beuth Verlag GmbH, Österreich 2016, p. 543.
- [30] M. Schwankl, Dissertation 2017, p. 58, https://open.fau.de/handle/ openfau/8624.
- [31] Elements of Metallurgy and Engineering Alloys, ASM International, USA 2008, p. 522.
- [32] H. Gut, Prozeßstrukturen der chemischen Vernickelung. Zugl.: Stuttgart, Univ., Diss., Springer, Berlin, Heidelberg 1993, p. 25.
- [33] C. Kammer, Aluminium Taschenbuch 1. Grundlagen und Werkstoffe (16. Auflage), Beuth Verlag GmbH 2012, p. 255.
- [34] F. Ostermann, Anwendungstechnologie Aluminium. 3., neu bearbeitete Auflage, VDI-Buch, Springer Vieweg, Berlin 2014, p. 795, ISBN 978-3- 662-43807-7.
9. Copyright:
- This material is "Christopher Locke, Raffael Pichler, Martin Guggemos, Wolfram Volk, and Daniel Günther"'s paper: Based on "Expanding Lightweight Design Potential by Hybrid Joining of Aluminum Sheets with Aluminum Casting Through Compound Sand Casting and Induction Heating".
- Paper Source: https://doi.org/10.1002/adem.202400549
This material was created to introduce the above paper, and unauthorized use for commercial purposes is prohibited.
Copyright © 2025 CASTMAN. All rights reserved.