This introductory paper is the research content of the paper "Estimation of Cooling Rates in Suction Casting and Copper-Mould Casting Processes" published by Archives of Metallurgy and Materials.
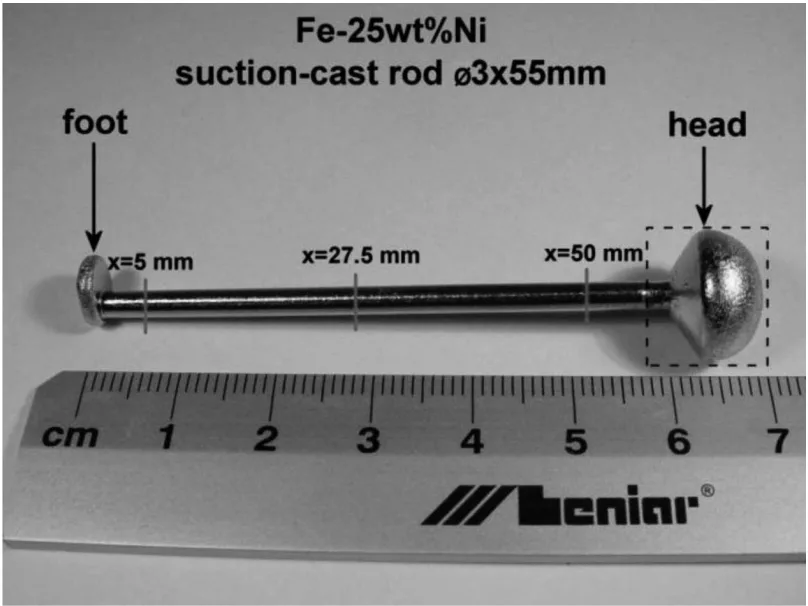
1. Overview:
- Title: Estimation of Cooling Rates in Suction Casting and Copper-Mould Casting Processes
- Author: T. Kozieł
- Publication Year: 2015
- Publishing Journal/Academic Society: Archives of Metallurgy and Materials
- Keywords: suction casting, copper mould casting, cooling rate, cellular solidification; eutectic solidification
2. Abstracts / Introduction
The cooling rates were determined for Fe-25wt%Ni and Al-33wt%Cu alloys in suction and copper-mould casting. Rods of ø2, ø3, and ø5 mm were produced. The rates were estimated based on cellular and lamellar spacings. It was found that temperature profiles in cylindrical eutectic alloys cannot be solely determined by microstructural examination. The concave solidification front in eutectics caused a decrease in lamellar spacing towards the rod center. Minimum axial cooling rates, based on cellular spacing in Fe-25wt%Ni, were approximately 200 K/s for ø2 and ø3 mm rods, and 30 K/s for ø5 mm suction cast rods. Copper-mould casting yielded slightly lower values.
3. Research Background:
Background of the Research Topic:
The critical cooling rate (Rc) needed to suppress crystallization during casting largely depends on alloy composition. Rapid solidification techniques, like suction casting and copper-mould casting, are crucial for producing bulk metallic glasses (BMGs) by achieving cooling rates above Rc.
Status of Existing Research:
- Early metallic glasses (e.g., Au-Si) required very high cooling rates (106 to 107 K/s) [1].
- BMGs were developed by improving glass-forming ability (GFA) at lower cooling rates. Pd-Cu-Ni-P system has a critical cooling rate below 1 K/s [2,3].
- Measuring Rc directly is difficult. Various parameters based on thermal analysis are used to infer relative GFA [9].
- Existing methods for estimating cooling rates from microstructural features have shown discrepancies between Fe-25Ni [14] and Al-33Cu [12] alloys.
Necessity of the Research:
Existing discrepancies in cooling rate estimations using microstructural features need to be addressed. The study investigates the applicability of microstructure-based cooling rate determination, particularly comparing suction and copper-mould casting, and highlights the limitations of using eutectic alloys for this purpose.
4. Research Purpose and Research Questions:
Research Purpose:
To estimate cooling rates during suction and copper-mould casting of Fe-25wt%Ni and Al-33wt%Cu alloys by examining their microstructures. To compare the cooling rates obtained from the two casting methods. To clarify if eutectic microstructures are suitable of estimation of cooling rate.
Key Research:
- What are the superficial and axial cooling rates in Fe-25wt%Ni and Al-33wt%Cu rods produced by suction and copper-mould casting?
- How do these cooling rates compare between the two casting methods?
- Can the cooling rate in cylindrical samples be determined by microstructural examination of eutectic sample alloys?
5. Research Methodology
Research Design:
Experimental study comparing two casting methods (suction casting and copper-mould casting) and two alloy systems (Fe-25wt%Ni and Al-33wt%Cu). Microstructural analysis was the primary method for inferring cooling rates.
Data Collection Method:
- Sample Preparation: Fe-25wt%Ni and Al-33wt%Cu alloy ingots were synthesized by arc melting. Rods of ø2, ø3, and ø5 mm with a length of 55 mm were produced using suction casting (Arc Melter AM, Edmund Bühler GmbH) and copper-mould casting (Melt Spinner HV, Edmund Bühler GmbH).
- Microstructural Analysis: Microsections were ground, polished, and etched. Light microscopy (Leica DM LM) and scanning electron microscopy (FEI Nova NanoSEM 450, for Al-33Cu) were used to observe and measure microstructural features (cellular spacing in Fe-25Ni, interlamellar spacing in Al-33Cu). Measurements were taken near the surface and in the center of the rods at three axial positions (x=5 mm, x=27.5 mm, x=50 mm), as shown in Figure 1.
Analysis Method:
- Cooling Rate Estimation in Fe-25Ni: Cooling rate (ε) was estimated using the relationship: ε = (B6 / λ)n, where λ is the dendrite arm spacing, B6 = 60 µm(K/s)n, and n = 0.32 [14, 15].
- Cooling Rate Estimation in Al-33Cu: Cooling rate (ε) was estimated using the relationships: v = K / λ2 (where v is the solidification front velocity, K = 27.5 · 10-12 cm3s-1, and λ is the interlamellar spacing) [12] and ε = (Δhf / cp) · (2v / R) (where Δhf is latent heat, cp is specific heat, and R is the cylinder radius) [12].
Research Subjects and Scope:
Fe-25wt%Ni and Al-33wt%Cu alloys cast into rods of 2, 3, and 5 mm diameters using suction and copper-mould casting.
6. Main Research Results:
Key Research Results:
- Fe-25Ni: Cellular morphology was observed, indicating radial heat flux. Superficial cooling rates were higher than 1000 K/s. Axial cooling rates were ~200 K/s for ø2 and ø3 mm suction-cast rods, and ~30 K/s for ø5 mm rods. Copper-mould casting showed slightly lower axial cooling rates.
- Al-33Cu: Lamellar eutectic morphology was observed. Unexpectedly, interlamellar spacing was smaller in the rod axis compared to the surface, indicating a higher axial cooling rate.
Analysis of presented data:
- Table 1: Provides cellular spacing measurements for suction-cast Fe-25Ni rods at different diameters and positions.
- Table 2: Provides cellular spacing measurements for copper-mould-cast Fe-25Ni rods.
- Figure 4: Shows the estimated superficial (a) and axial (b) cooling rates for Fe-25Ni, comparing suction and copper-mould casting.
- The interlamellar spacing of the Al-33Cu alloy did not correlate directly with expected cooling rate trends due to the concave shape of the solidification front in eutectic systems.
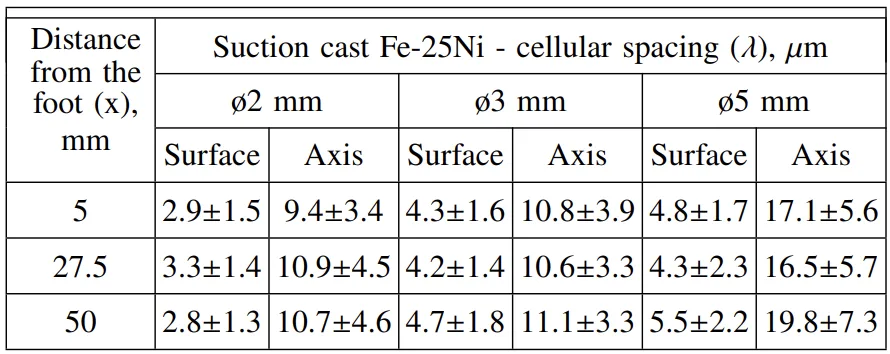
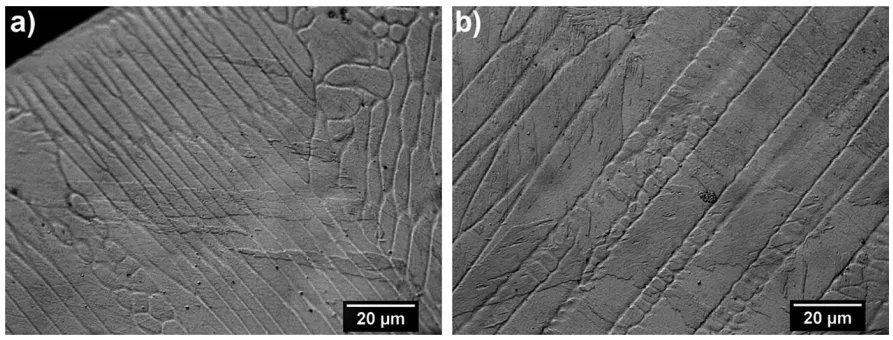
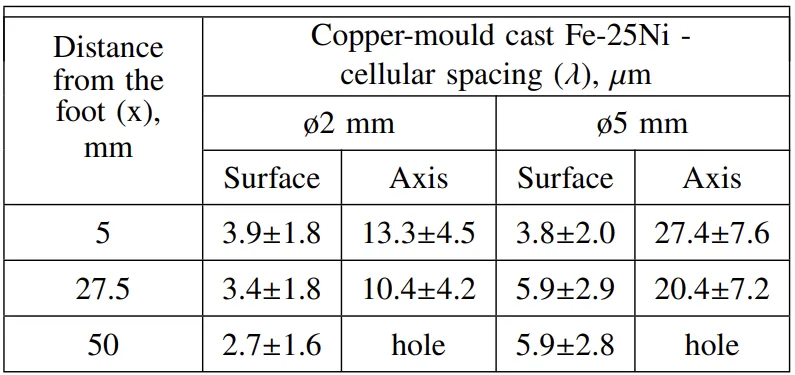
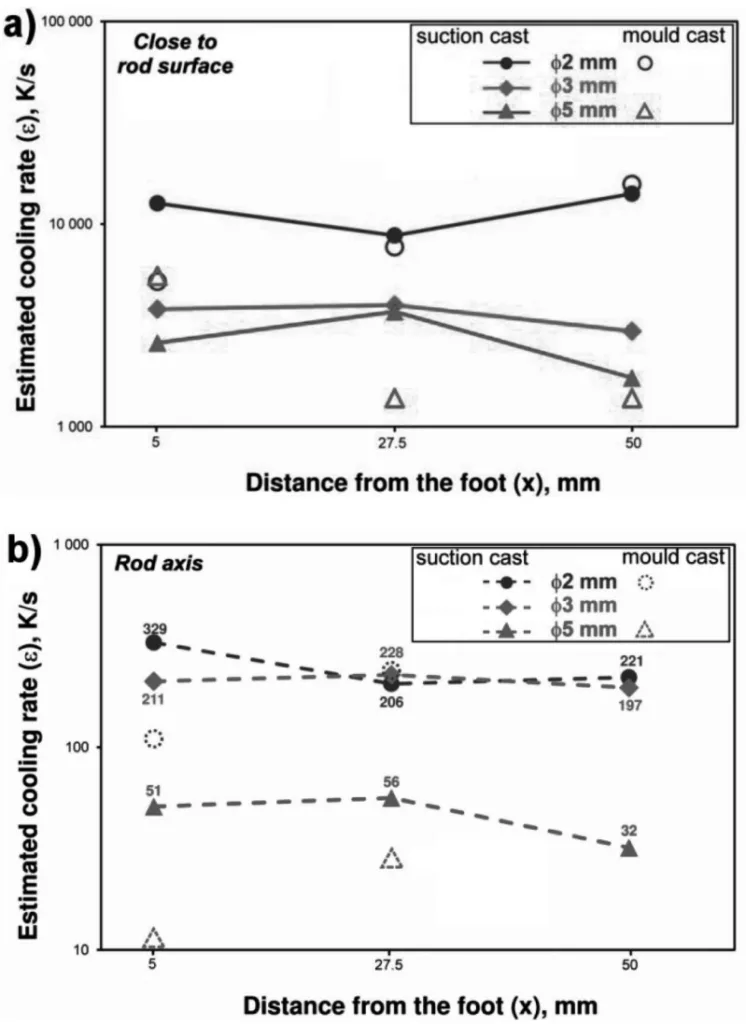
Figure Name List:
- Fig. 1. A suction-cast ø3×55 mm Fe-25Ni rod
- Fig. 2. Cross-sectional microstructure of the suction cast ø3 mm Fe-25Ni alloy at x=5 mm: a) near the rod surface, b) in the rod axis (light microscopy, 1000x)
- Fig. 3. Cross-sectional microstructure of the copper-mould cast ø3 mm Fe-25Ni alloy at x=5 mm: a) near the rod surface, b) in the rod axis (light microscopy, 1000x)
- Fig. 4. Estimated a) superficial and b) axial cooling rates based on observed cellular spacing in Fe-25Ni alloy
- Fig. 5. Microstructures of ø3 mm Al-33Cu rod suction-cast at x = 27.5 mm: a) close to the rod surface, b) in the rod axis (SEM, 30000x). Inset shows a schematic illustration of lamellar elimination caused by a concave perturbation of the eutectic front [17]
- Fig. 6. Estimated superficial and axial cooling rates in Al-33wt%Cu (ø3×55 mm) suction cast alloy
7. Conclusion:
Summary of Key Findings:
- Superficial cooling rates are significantly higher than axial cooling rates in Fe-25Ni, confirming dominant radial heat transfer.
- Suction casting generally resulted in slightly higher cooling rates than copper-mould casting in Fe-25Ni.
- Eutectic alloys (like Al-33Cu) are not suitable for estimating cooling rates or temperature profiles in cylindrical samples due to the influence of the concave solidification front on interlamellar spacing.
Academic Significance of the Study:
This study highlights the limitations of using eutectic microstructures to infer cooling rates in casting processes. It clarifies the discrepancies observed in previous research and provides a more accurate understanding of cooling rate variations in cylindrical samples.
Practical Implications:
- For BMG synthesis, understanding the minimum cooling rate across the sample is crucial. This study provides insights into achieving the required cooling rates.
- The findings emphasize the need for careful selection of alloy systems and analysis methods when estimating cooling rates based on microstructure.
Limitations of the Study and Areas for Future Research:
- The equations used for cooling rate estimation were derived from unidirectional solidification experiments, which differ from the actual casting processes.
- The study only considered two alloy systems. Further research could investigate other alloy compositions.
- The effect of interfacial resistance mould-metal was not quantitively.
8. References:
- [1] W. Klement, R.H. Willens, P. Duwez, Non-crystalline structure in solidified gold-silicon alloys, Nature 187, 869-870 (1960).
- [2] A. Nishiyama, A. Inoue, Stability and nucleation behavior of glass-forming Pd-Cu-Ni-P alloy with a critical cooling rate of 0.067 K/s, Intermetallics 10, 1141-1147 (2002).
- [3] H. Chakrabarti, C.B. Chaudhuri, B. Kanjilal, Glass transition temperature of Pd-Cu-Ni-P thin film metallic glass a 2D approach, J. Non-Cryst. Solids 359, 51-55 (2013).
- [4] J. Gondro, J. Zbroszczyk, W. Ciurzyńska, J. Olszewski, M. Nabiałek, K. Sobczyk, J. Świerczek, A. Łukiewska, Structure and Soft Magnetic Properties of Bulk Amporphous Fe0.61Co0.10Zr0.025W0.02Hf0.025Ti0.02B0.20)96Y4 Alloy, Arch. Metall. Mater. 55, 85-90 (2010).
- [5] M. Nabiałek, J. Zbroszczyk, W. Ciurzyńska, J. Olszewski, S. Lesz, P. Brągiel, J. Gondro, K. Sobczyk, A. Łukiewska, A. Świerczek, Microstructure, Some Magnetic and Mechanical Properties of Amorphous Fe60Co10Zr2.5Hf2.519W2Y2B21 Plates, Arch. Metall. Mater. 55, 195-203 (2010).
- [6] D.C. Hofmann, Bulk metallic glasses and their composites: a brief history of diverging fields J. Mater. 2013, 1-8 (2013).
- [7] Y. Li, W. Zhang, F.X. Qin, A. Makino, Mechanical properties and corrosion resistance of a new Zr56Ni20A115Nb4Cu5 bulk metallic glass with a diameter up to 25 mm, J. Alloys Compd. 615, S71-S74 (2014).
- [8] N. Hua, T. Zhang, Glass-forming ability, crystallization kinetics, mechanical property, and corrosion behavior of Zr-Al-Ni-Ag glassy alloys, J. Alloys Compd. 605, 339-345 (2014).
- [9] B.S. Dong, S.X. Zhou, D.R. Li, C.W. Lu, F. Guo, X.J. Ni, Z.C. Lu, A new criterion for predicting glass forming ability of bulk metallic glasses and some critical discussions, Prog. Nat. Sci. Materials International 21, 164-172 (2011).
- [10] W. Pilarczyk, Preparation and characterization of Zr-based bulk metallic glasses in form of plate, J. Alloys Compd. 615, S132-S135 (2014).
- [11] F.G. Coury, L.C.R. Aliaga, C.R.M. Afonso, C. Bolfarini, W.J. Botta, C.S. Kiminami, Comparative study between two die cast methods for processing Cu-Zr-Al bulk metallic glasses, J. Mater. Res. Tech 2, 125-129 (2013).
- [12] R.M. Srivastava, J. Eckert, W. Löser, B.K. Dhindaw, L. Schultz, Cooling rate evaluation for bulk amorphous alloys from eutectic microstructures in casting processes, Mater. Trans. 43, 1670-1675 (2002).
- [13] K.J. Laws, B. Gun, M. Ferry, Influence of casting parameters on the critical casting size of bulk metallic glass, Metall. Mater. Trans. A 40A, 2377-2387 (2009).
- [14] P. Pawlik, K. Pawlik, A. Przybył, Investigation of the cooling rate in the suction casting proces, Rev. Adv. Mater. Sci. 18, 81-84 (2008).
- [15] H. Jones, Rapid solidification of metals and alloys, Monograph No. 8, Institution of Metallurgists, London (1982).
- [16] L.J. Swartzendruber, V.P. Itkin, C.B. Alcock in H. Okamoto (ed.), Phase Diagrams of Binary Iron Alloys, Materials Information Soc., Materials Park, Ohio (1993).
- [17] A. Karma, M. Plapp, New insights into the morphological stability of eutectic and peritectic coupled growth, JOM 56, 28-32 (2004).
9. Copyright:
- This material is "T. Kozieł"'s paper: Based on "Estimation of Cooling Rates in Suction Casting and Copper-Mould Casting Processes".
- Paper Source: DOI: 10.1515/amm-2015-0204
This material was created to introduce the above paper, and unauthorized use for commercial purposes is prohibited.
Copyright © 2025 CASTMAN. All rights reserved.