This article introduces the paper ["Efficiency and agility of a liquid CO2 cooling system for molten metal systems"] published by Elsevier.
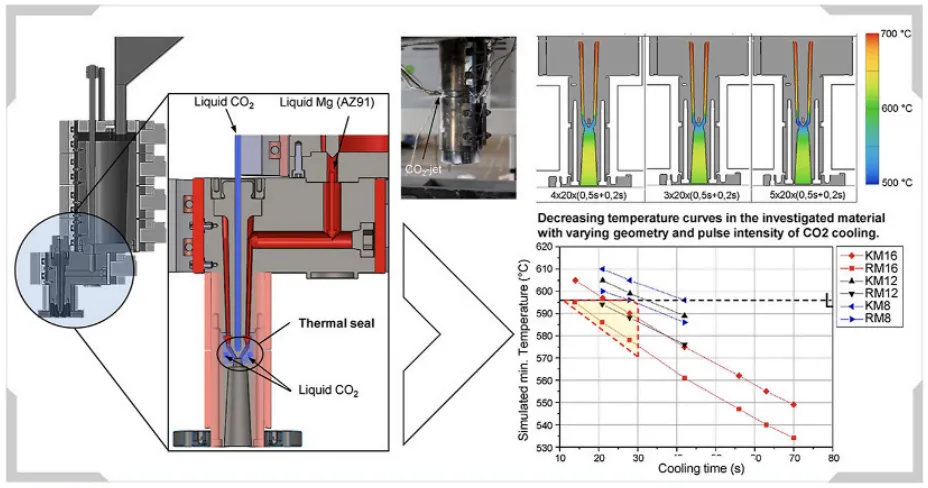
1. Overview:
- Title: Efficiency and agility of a liquid CO2 cooling system for molten metal systems
- Author: J. Glueck, A. Schilling, N. Schwenke, A. Fros, M. Fehlbier
- Publication Year: September 2021
- Publishing Journal/Academic Society: Case Studies in Thermal Engineering
- Keywords: CO2 cooling, Magnesium, Hot runner, Thermal seal, Simulation, Cooling rates
2. Abstracts or Introduction
In this study investigations on the efficiency and agility of a liquid CO2 cooling system are performed in a test rig. The system uses expansion bores fed with liquid CO2 by capillary tubes, to form a thermal seal in a magnesium hot runner channel. Via temperature measurements the performance of different sets of cooling parameters is tested and cooling rates are identified depended on a varying nozzle geometry. To validate the measurements, the tests are modelled in a thermal simulation study. The applicability of the liquid CO2 cooling was demonstrated for engineering purposes. Adequate process times could be achieved while using a 16 mm diameter as annular gap, which results in cooling rates up to 4.8 °C/s. The tests were validated by a simulation model. The simulations illustrate the inner processes of the test rig and the comparison of temperature curves of the cooling process show a good correlation.
3. Research Background:
Background of the Research Topic:
The use of lightweight designs using metallic lightweight materials such as magnesium is being constantly promoted. Magnesium alloys offer great potential to replace aluminum and steel in cost-effective processes, particularly in automotive structural components where cold-chamber die casting is a key technology. However, conventional die casting processes generate large quantities of internal cycle material, leading to energy-intensive remelting. Minimizing the casting run system is crucial for reducing recycling material and CO2 emissions. Hot runner technology, already established in plastic injection molding, offers a way to guide melt from the casting chamber to the gate in a liquid state, potentially reducing internal cycle material in magnesium die casting.
Status of Existing Research:
Conventional cooling technologies in die casting, using water or oil as heat transfer media, achieve CTEs of up to 2500 W/m²K. Pulsating heat transfer medium variants offer slightly higher CTEs but remain sluggish for thermal closure systems. Newer technologies using two-phase heat transfer via evaporation, such as near-contour spray cooling with water evaporation, show promise. Nanofluids with hybrid nanoparticles like Cu and Al2O3 can further increase thermal conductivity. CO2 is recognized as a coolant for rapid cooling, utilizing the Joule-Thomson effect for intensive cooling. However, its application in liquid molten magnesium alloys for thermal seals in hot runner systems is a novel area.
Necessity of the Research:
The reactivity of liquid magnesium makes water-based coolants unsuitable. While CO2 cooling and the Joule-Thomson effect are known, their application to form thermal seals in magnesium hot runner systems is unexplored. There is a need to investigate the efficiency and agility of liquid CO2 cooling in this context, particularly regarding its effectiveness and industrial applicability in reducing internal cycle material and improving the die casting process for magnesium alloys. This research aims to address this gap by testing and validating a liquid CO2 cooling system for magnesium hot runner applications.
4. Research Purpose and Research Questions:
Research Purpose:
The study aims to evaluate the efficiency and agility of a liquid CO2 cooling system for forming a thermal seal in a magnesium hot runner system for die casting. The research focuses on testing the system's performance with varying cooling parameters and nozzle geometries and validating its applicability for engineering purposes in industrial foundry applications.
Key Research:
- Investigation of the efficiency and agility of a liquid CO2 cooling system using expansion bores and capillary tubes to create a thermal seal in a magnesium hot runner.
- Testing the performance of different cooling parameter sets and identifying cooling rates based on varying nozzle geometries.
- Validation of experimental measurements through thermal simulation studies.
- Demonstration of the applicability of liquid CO2 cooling for engineering purposes in die casting.
- Evaluation of process times achievable with a 16 mm annular gap and resulting cooling rates.
- Comparison of simulation and experimental temperature curves to assess correlation.
Research Hypotheses:
- Liquid CO2 cooling can effectively create a thermal seal in a magnesium hot runner system.
- Varying cooling parameters and nozzle geometries will significantly impact cooling rates and the efficiency of thermal seal formation.
- Simulation models can accurately predict and validate the thermal behavior of the CO2 cooling system in the test rig.
- The liquid CO2 cooling system can achieve adequate process times for industrial applications in die casting.
5. Research Methodology
Research Design:
The research employs an experimental approach using a test rig designed to simulate a magnesium hot runner system. The test rig is gravity-driven and based on real geometries of hot runner components. Temperature measurements are taken to assess the performance of the CO2 cooling system under different conditions. A simulation model is developed to validate the experimental results and analyze the inner processes of the test rig.
Data Collection Method:
Temperature measurements are continuously recorded using a data logger and NiCr-Ni thermocouples placed at characteristic points within the nozzle's annular gap and pin tip. Variations in cooling parameters, including the number of pulses, pulse duration, and pulse pause, are tested for different nozzle geometries (8 mm, 12 mm, and 16 mm inner cone diameters). The melt temperature is controlled at 640 °C, and AZ91D magnesium alloy is used.
Analysis Method:
The collected temperature data is analyzed to determine cooling rates and minimum temperatures achieved under different cooling parameters and nozzle geometries. The experimental data is compared with the results from the thermal simulation model to validate the model's accuracy and assess the correlation between simulated and measured temperature curves. The study also examines the relationship between cooling parameters, nozzle geometry, cooling rates, and the formation of a thermal seal.
Research Subjects and Scope:
The research focuses on a test rig simulating a magnesium hot runner system using AZ91D magnesium alloy. The scope includes investigating the impact of varying CO2 cooling parameters and nozzle geometries on thermal seal formation and cooling efficiency. The study is limited to experimental tests and simulations conducted on this specific test rig setup and material.
6. Main Research Results:
Key Research Results:
- Applicability of liquid CO2 cooling for thermal seals in magnesium hot runners was demonstrated.
- Adequate process times were achieved using a 16 mm diameter annular gap, with cooling rates up to 4.8 °C/s.
- Tests were validated by simulation models, showing good correlation between temperature curves.
- Minimum temperatures showed an almost linear correlation with nozzle diameters.
- Nozzle with 16 mm diameter showed higher thermal agility compared to smaller diameters.
- Cooling rates decreased exponentially with increasing cooling duration for all diameters.
- Simulation results correlated well with experimental data, validating the model and approach.
Analysis of presented data:
- Cooling Rates: Figure 10 shows an exponentially decreasing trend of cooling rate with increasing cooling duration for all nozzle diameters (8 mm, 12 mm, 16 mm). The 16 mm nozzle achieved the highest cooling rates.
- Minimum Temperatures: Figure 9 illustrates that minimum temperatures correlate almost linearly with nozzle diameters. The 16 mm nozzle showed a linear decreasing trend in minimum temperature with increased cooling duration.
- Temperature Distribution: Figure 8 shows the locally limited cooling effect of CO2, with thermal cooling capacity decreasing exponentially with distance from the cooling holes.
- Simulation Validation: Figure 11 demonstrates a conformity between averaged experimental temperature curves and simulated curves, particularly for measuring positions 1 and 2. Offsets were observed in positions 3 and 4, attributed to slight deviations in heat transfer coefficients. Figure 13 shows simulated minimum temperatures in the melt channel and annular gap, indicating a temperature gradient and confirming test observations.
Figure Name List:
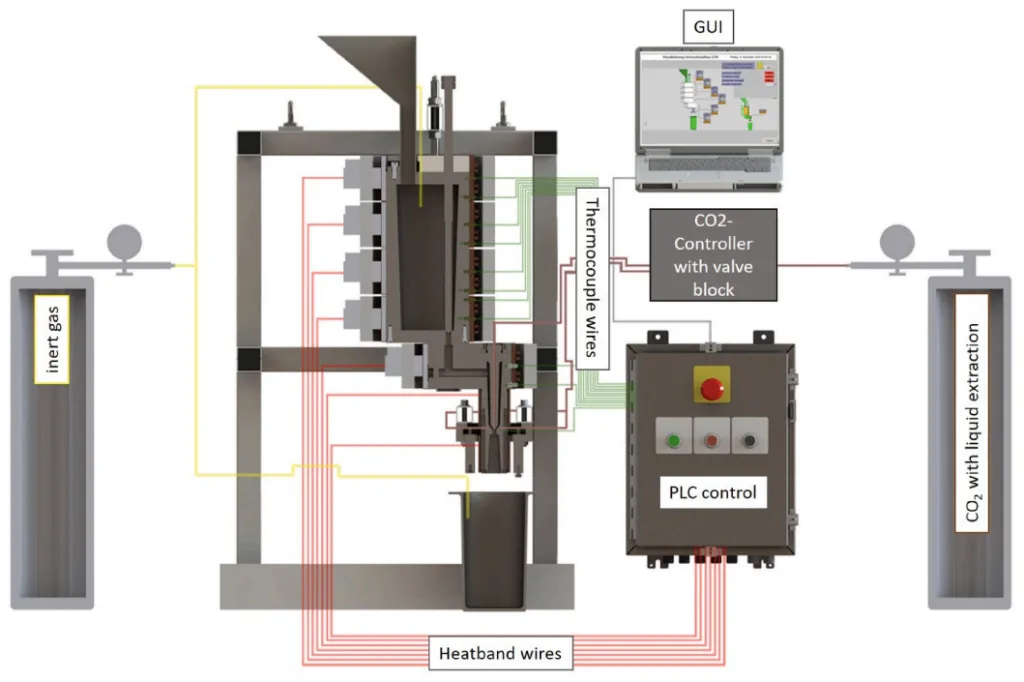
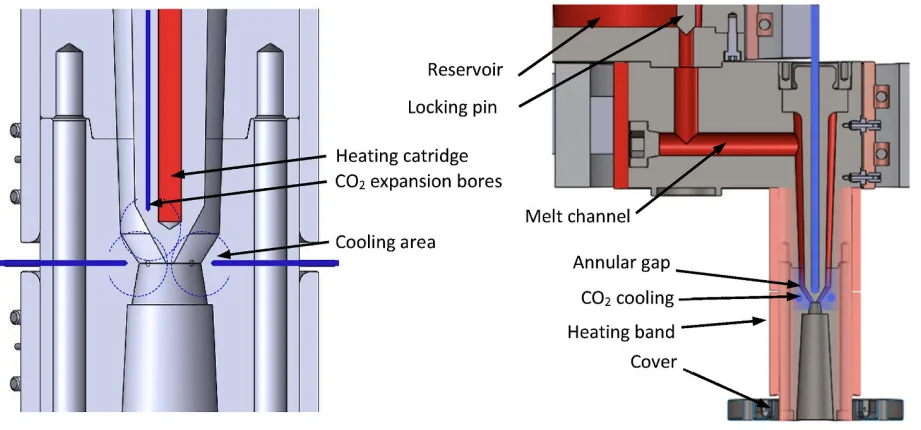
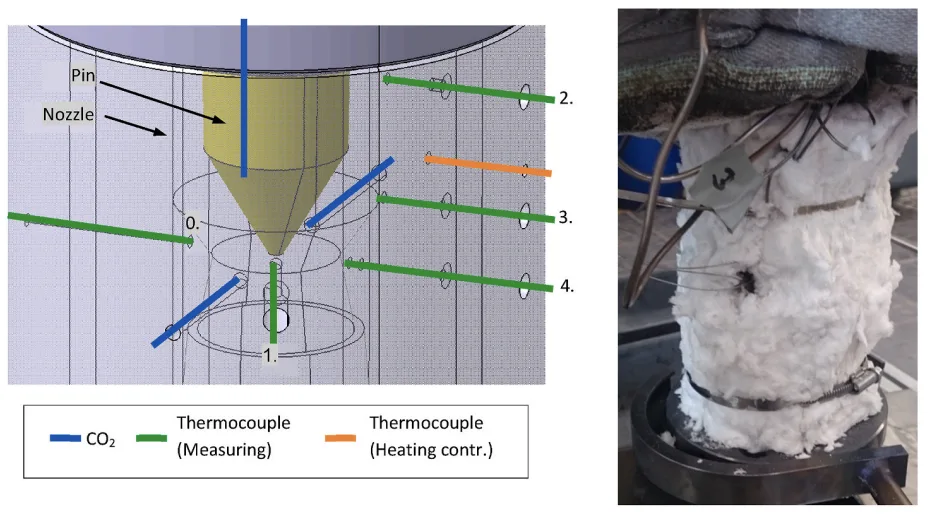
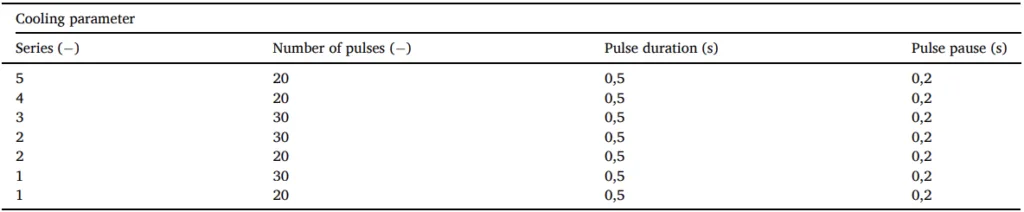
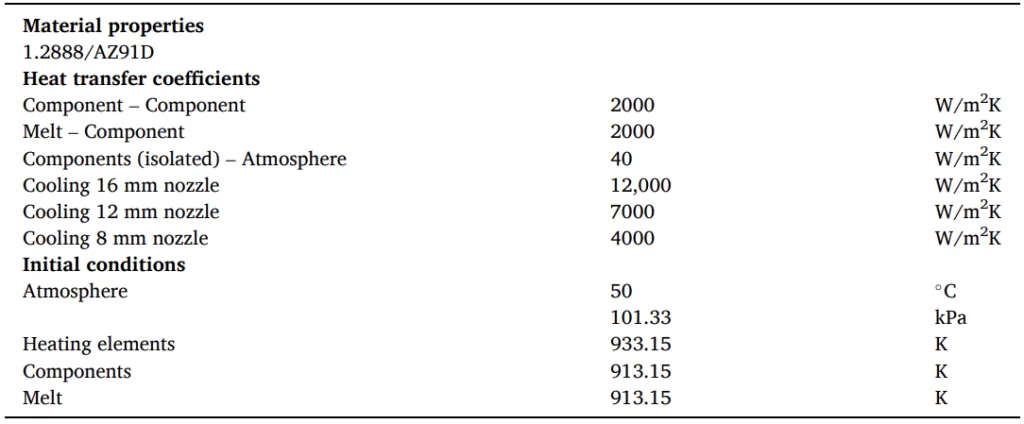
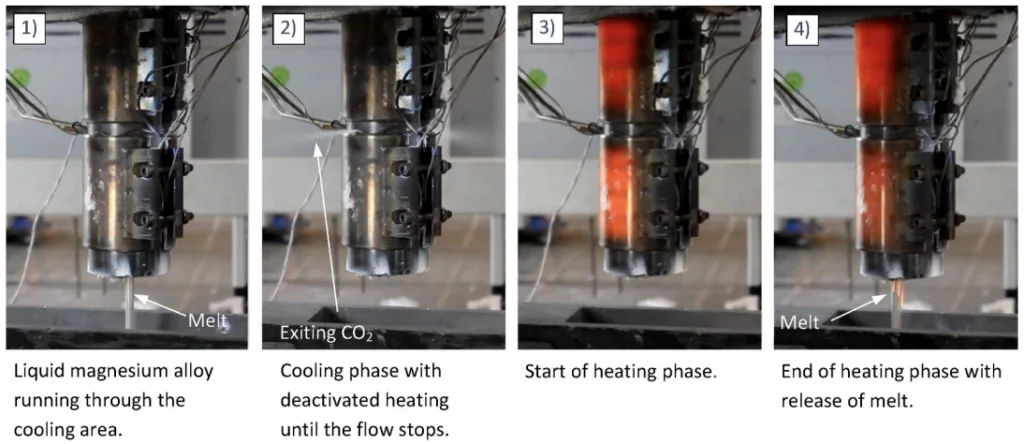
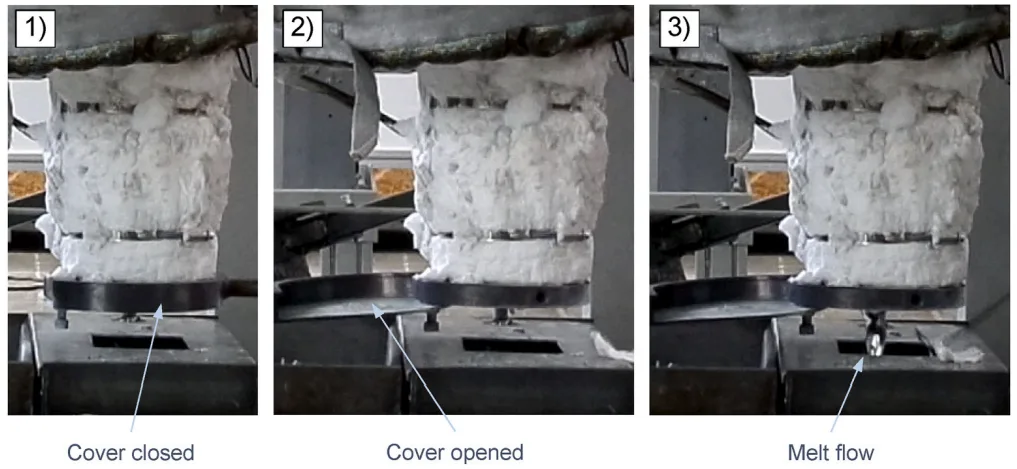
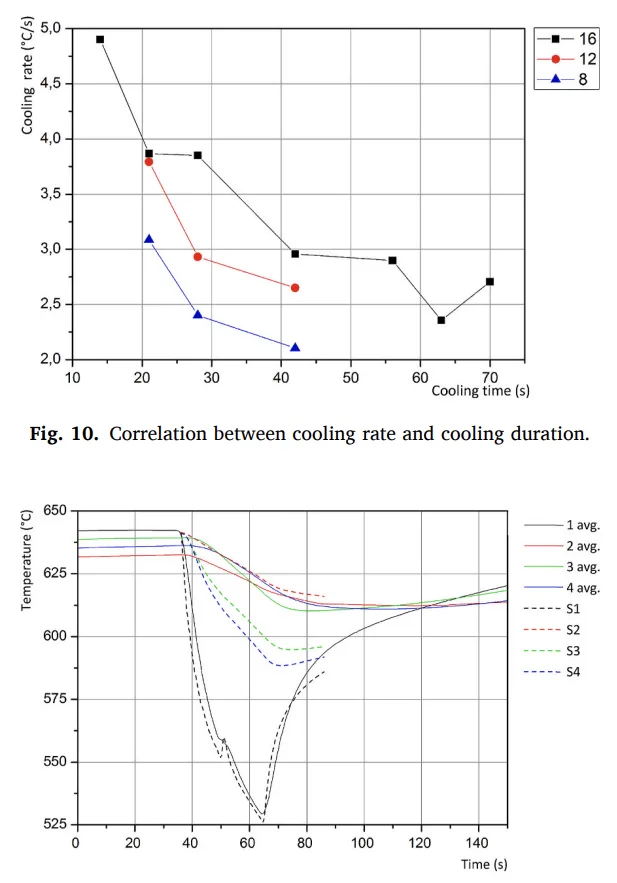
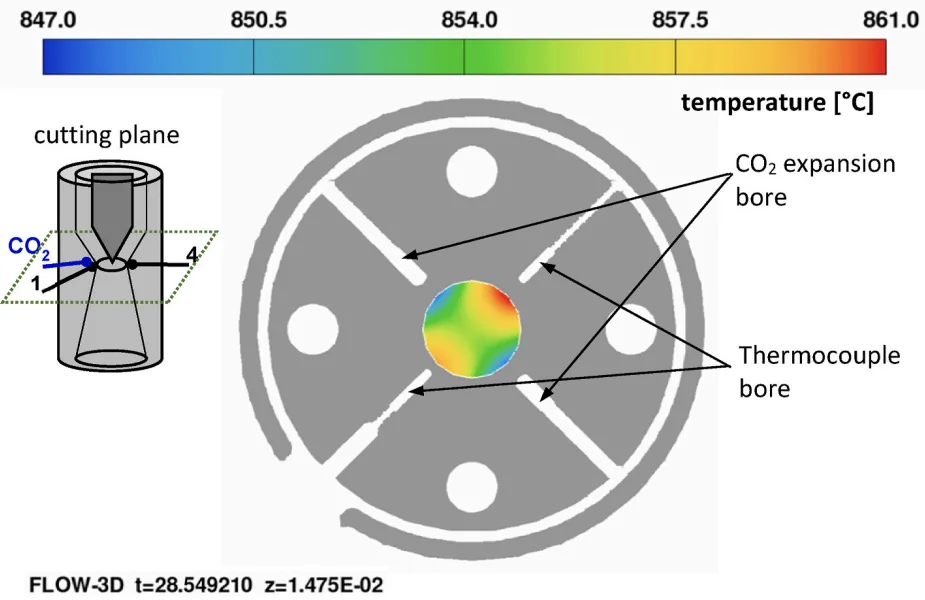
- Fig. 1. Sectional view of the test rig structure with supply and control devices.
- Fig. 2. Sectional view of the structure of the annular gap in the nozzle with heating cartridge in the pin and representation of the CO2 cooling positions (left) and of the internal structure of the melt channel as connection between reservoir and nozzle area (right).
- Fig. 3. CAD representation of the measuring range around the pin tip with color-coded thermocouples for the heating control (orange), for measuring (green) and the feeds of the CO2 cooling (blue). The pin in the center of the hot runner is shown in yellow. The annular gap around the pin is conical (left). Representation of the nozzle in the installed state in the test rig with ceramic insulation wool and cover (right). (For interpretation of the references to color in this figure legend, the reader is referred to the Web version of this article.)
- Fig. 4. Structure of the nozzle in the simulation model with positions of the simulated thermocouples.
- Fig. 5. Initial procedure of the cooling test.
- Fig. 6. Sequence representation of the test according to a defined parameter at characteristic points in time.
- Fig. 7. Characteristic curve of the nozzle temperature [measuring point 0, parameter 5x20x (0.5s + 0.2s)].
- Fig. 8. Interpolation of the temperature curves at measuring points 1, 2 and 3 over time and distance from CO2 cooling [parameter 2x30x (0.5s + 0.2s)].
- Fig. 9. Minimum temperatures in the cooling phase and average heating times.
- Fig. 10. Correlation between cooling rate and cooling duration.
- Fig. 11. Averaged temperature curves for the measuring positions 1 to 4 and the simulated temperature curves for the parameter 2x20x (0.5s + 0.2s) with a nozzle diameter of 16 mm.
- Fig. 12. Sectional view of the nozzle with color scaled temperatures in the melt. (For interpretation of the references to color in this figure legend, the reader is referred to the Web version of this article.)
- Fig. 13. Simulation of minimum temperatures in the center of the melt channel and the center of the annular gap for all nozzle diameters.
7. Conclusion:
Summary of Key Findings:
This study successfully demonstrated the efficiency and agility of a liquid CO2 cooling system for creating thermal seals in magnesium hot runner systems. The 16 mm diameter nozzle exhibited the best performance, achieving cooling rates up to 4.8 °C/s and adequate process times. Simulation models validated the experimental results, showing good correlation and confirming the suitability of the 16 mm diameter nozzle for hot runner applications requiring local thermal closure. The research also highlighted the impact of nozzle geometry and cooling parameters on cooling efficiency and thermal seal formation.
Academic Significance of the Study:
This research contributes to the fundamental understanding of liquid CO2 cooling in die casting, specifically for magnesium alloys and hot runner systems. It provides valuable experimental data and validated simulation models for analyzing and optimizing CO2 cooling processes. The study advances the knowledge of thermal management in die casting and offers insights into the relationship between cooling parameters, nozzle geometry, and cooling performance.
Practical Implications:
The findings have significant practical implications for the die casting industry, particularly for magnesium component manufacturing. The demonstrated applicability of liquid CO2 cooling offers a promising technology for reducing internal cycle material and improving process efficiency in cold-chamber die casting. The use of a 16 mm diameter nozzle with optimized CO2 cooling parameters can lead to faster cycle times and reduced material waste. This technology can be implemented in industrial settings to enhance the production of high-quality magnesium die castings.
Limitations of the Study and Areas for Future Research:
The study is limited to a specific test rig setup and AZ91D magnesium alloy. Further research is needed to investigate the performance of the CO2 cooling system with other magnesium alloys and in more complex industrial die casting molds. The long-term operational stability and robustness of the CO2 cooling system in industrial environments should also be evaluated. Future research could explore further optimization of cooling parameters, nozzle designs, and control strategies to maximize cooling efficiency and minimize CO2 consumption. Investigating the effects of pulsating CO2 cooling and different capillary tube configurations could also be beneficial.
8. References:
- [1] C. Herrmann, H. Pries, G. Hartmann, Energie- und ressourceneffiziente Produktion von Aluminiumdruckguss, Springer Vieweg, Heidelberg, 2013, ISBN 978-3-642-39852-0.
- [2] V. Goryany, P.J. Mauk, O. Myronova, Magnesium als Leichtbauwerkstoff - Eigenschaften, Anwendungen, Entwicklungspotential, Giesserei-Rundschau 53 (2006) 9-10.
- [3] A. Lohmüller, M. Scharrer, C. Rauber, et al., Neue Entwicklungen beim Thixospritzgießen von Magnesium, Neue Materialien Fürth GmbH, Fürth, 2007.
- [4] D.V. Rosato, M.G. Rosato. Injection Molding Handbook 3, Springer Science & Business Media, 2012.
- [5] R. Spina, Injection moulding of automotive components: comparison between hot runner systems for a case study, J. Mater. Process. Technol. 155-156 (2004) 1497-1504, https://doi.org/10.1016/j.jmatprotec.2004.04.359.
- [6] A. Demirer, Y. Soydan, A.O. Kapti, An experimental investigation of the effects of hot runner system on injection moulding process in comparison with conventional runner system, Materials and Design 28 (5) (2007) 1467-1476, https://doi.org/10.1016/j.matdes.2006.03.015.
- [7] J. Glück, A. Schilling, M. Fehlbier, J. Röse, A. Gebauer-Teichmann. Düse für Metall-Druckgussanwendungen, DE102015224410B4, 2020, DPMA German Patent.
- [8] J. Glück; A. Schilling; M. Fehlbier; J. Röse; A. Gebauer-Teichmann. Rückschlagventil. 2019, 1-11. DE102015224411B4.
- [9] J. Glück; A. Schilling; M. Fehlbier; J. Röse; A. Gebauer-Teichmann; Gusseinrichtung; DPMA German Patent. 2017, 1-19. DE102015224414A1.
- [10] L. Reiche, Entwicklung einer geregelten und energieeffizienten Werkzeugtemperierung im Dauerformguss unter Einsatz einer Sprühkühlung mit Wärmerückgewinnung, Dissertation, Universität Kassel, Kassel, 2019, https://doi.org/10.17170/kobra-202007281500.
- [11] W. Kotzab, Methoden der Impulstemperierung, in: In: Kunststoffe, Hanser Verlag, München, 2006, 8/2006.
- [12] W. Steinko, C. Bader, Optimierung von Spritzgießprozessen, Hanser, München, 2008, ISBN 978-3-446-40977-4.
- [13] N. Abbas, S. Nadeem, A. Saleem, Computational analysis of water based Cu - Al2O3/H2O flow over a vertical wedge, Adv. Mech. Eng. 12 (11) (2020) 1-10, https://doi.org/10.1177/1687814020968322.
- [14] S. Nadeem, N. Abbas, A.U. Khan, Characteristics of three dimensional stagnation point flow of Hybrid nanofluid past a circular cylinder, Results in physics 8 (2018) 829-835, https://doi.org/10.1016/j.rinp.2018.01.024.
- [15] X.C. Liu, Y.F. Sun, H. Fujii, Clarification of microstructure evolution of aluminum during friction stir welding using liquid CO2 rapid cooling, Mater. Des. 129 (2017) 151-163, https://doi.org/10.1016/j.matdes.2017.05.013.
- [16] Nan Xu, Rintaro Ueji, Yoshiaki Morisada, Hidetoshi Fujii, Modification of mechanical properties of friction stir welded Cu joint by additional liquid CO2 cooling, Mater. Des. 6 (2014) 20-25, https://doi.org/10.1016/j.matdes.2013.10.076 (1980-2015).
- [17] N. Hanenkamp, S. Amon, D. Gross, Hybrid supply system for conventional and CO2/MQL-based cryogenic cooling, Procedia CIRP 77 (2018) 219-222, https://doi.org/10.1016/j.procir.2018.08.293.
- [18] Huihong Liu, Kohsaku Ushioda, Hidetoshi Fujii, Elucidation of microstructural evolution of beta-type titanium alloy joint during friction stir welding using liquid CO2 cooling, Mater. Char. 145 (2018) 490-500, https://doi.org/10.1016/j.matchar.2018.09.005.
- [19] Zaman Ziabakhsh-Ganji, Henk Kooi, Sensitivity of Joule-Thomson cooling to impure CO2 injection in depleted gas reservoirs, Appl. Energy 113 (2014) 434-451, https://doi.org/10.1016/j.apenergy.2013.07.059. ISSN 0306-2619.
- [20] C.M. Oldenburg, Joule-Thomson cooling due to CO2 injection into natural gas reservoirs, Energy Convers. Manag. 48 (6) (2007) 1808-1815, https://doi.org/10.1016/j.enconman.2007.01.010. ISSN 0196-8904.
- [21] G. Walker, Joule-thomson cooling systems, in: Cryocoolers. The International Cryogenics Monograph Series, Springer, Boston, MA, 1983, https://doi.org/10.1007/978-1-4899-5286-8_6.
- [22] K.-P. Tucan, R. Gschwandtner, P. Hofer, G. Schindelbacher, P. Schumacher, Vergleich der Wirkung von lokalen Temperiermaßnahmen in Druckgießformen, Giesserei-Rundschau 59 (2012) 211-216, 7/8.
9. Copyright:
- This material is "J. Glueck et al."'s paper: Based on "Efficiency and agility of a liquid CO2 cooling system for molten metal systems".
- Paper Source: https://doi.org/10.1016/j.csite.2021.101485
This material was created to introduce the above paper, and unauthorized use for commercial purposes is prohibited.
Copyright © 2025 CASTMAN. All rights reserved.