This introductory paper is the research content of the paper ["ECO-DESIGN OF HEAT SINKS BASED ON CAD/CAE TECHNIQUES"] published by [Proceedings in Manufacturing Systems].
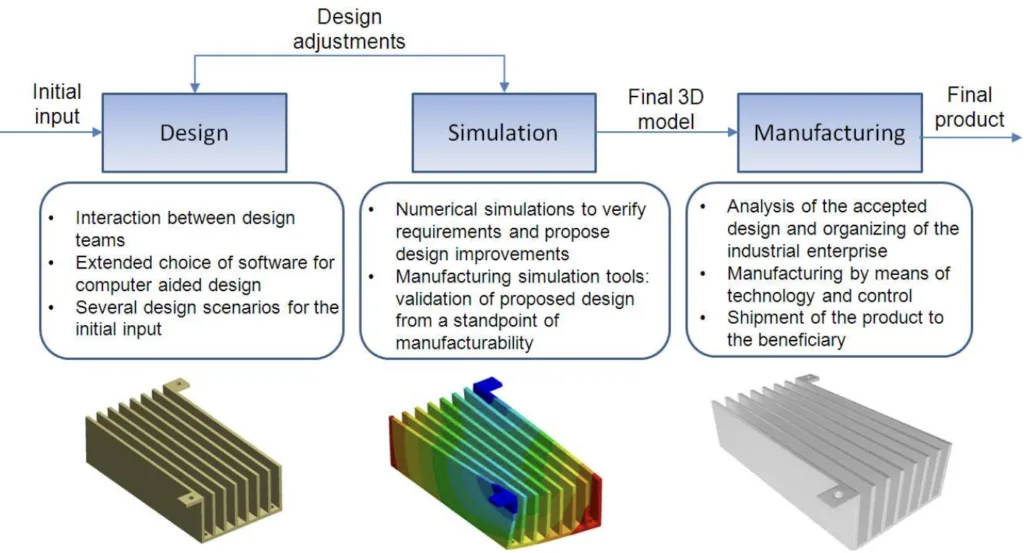
1. Overview:
- Title: ECO-DESIGN OF HEAT SINKS BASED ON CAD/CAE TECHNIQUES
- Author: Tudor-George ALEXANDRU, Cristina PUPĂZĂ
- Publication Year: 2017
- Publishing Journal/Academic Society: Proceedings in Manufacturing Systems
- Keywords: heat sinks, design tools, eco-design, variable speed drives
2. Abstracts / Introduction
In the era of Industry 4.0, the performance of manufacturing systems is intrinsically linked to the efficacy of embedded electronics. These components are crucial for information conditioning between machines, enabling desired input/output actions. To maintain competitiveness, manufacturers are refining product design through iterative decision loops, focusing on lifecycle performance. However, rapid technological advancements lead to product obsolescence and a surge in electronic waste. To mitigate this, eco-design principles and sustainable technologies are gaining prominence, guiding manufacturers towards products that meet both environmental and customer demands. Interdisciplinary approaches are essential to balance environmental costs and material needs across a product's lifecycle, minimizing landfill and maximizing product value. Knowledge transfer through guidelines and software tools is vital. Power electronics in manufacturing necessitate robust thermal designs, and heat sinks are pivotal for cooling. This paper explores the lifecycle of heat sinks, examining traditional CAD/CAE design tools and their adaptation to eco-design criteria. A case study of a variable speed drive passive cooler exemplifies these concepts.
3. Research Background:
Background of the Research Topic:
Modern industrial applications are characterized by high automation levels, with complex systems generating physical outputs through signal processing. Numerically controlled axes, comprising mechanical and electrical components such as servo drives, gearboxes, PLCs, and variable speed drives, are fundamental. The advent of Industry 4.0 has led to increased connectivity and the rise of cyber-physical systems, where hardware and software equally govern performance. This necessitates the integration of intelligent machines and embedded electronics. Ecological awareness is driving demand for environmentally sound manufacturing systems and sustainable electronics, especially given the growing concern over electronic waste, which is hazardous and complex to treat, with recycling rates remaining low. Miniaturization of industrial electronics has intensified thermal design challenges, making sustainable thermal design a critical area.
Status of Existing Research:
Prior research has explored sustainability in heat sink design. One approach focuses on "least energy" designs for natural and forced convection heat sinks, aiming to optimize heat transfer with minimal material usage, as studied in reference [7]. Another study, reference [8], uses a sustainability index to balance thermal performance and material investment in cooling designs for environmentally optimal configurations.
Necessity of the Research:
The increasing volume of electronic waste and the environmental impact of manufacturing necessitate a shift towards sustainable design practices in industrial engineering. Traditional thermal design approaches for heat sinks need to evolve to incorporate eco-design principles, considering not only thermal performance but also environmental costs throughout the product lifecycle. There is a need for methodologies and tools that facilitate the design of heat sinks that are both thermally efficient and environmentally sustainable.
4. Research Purpose and Research Questions:
Research Purpose:
The primary purpose of this research is to present a sustainable design approach for heat sinks used in industrial electronics cooling, leveraging CAD/CAE techniques and integrating eco-design principles. The paper aims to discuss the lifecycle stages of heat sinks and demonstrate how traditional CAD/CAE tools can be extended to meet eco-design criteria.
Key Research:
This paper focuses on developing and illustrating a CAD/CAE approach for designing heat sinks that are environmentally conscious. A key aspect is the integration of Life Cycle Assessment (LCA) considerations into the design process. The research uses a case study to exemplify the proposed approach, specifically focusing on the design of a passive cooler for a variable speed drive, ensuring it meets performance and sustainability requirements.
5. Research Methodology
Research Design:
The research employs a CAD/CAE-driven design methodology, augmented with eco-design considerations. This approach extends the traditional heat sink design process by incorporating environmental impact assessments at each stage. The design process is iterative, involving design, simulation, and manufacturing stages with feedback loops for design adjustments as shown in Fig. 1.
Fig. 1. Stages of Heat Sinks design, simulation and manufacturing.
Data Collection Method:
This research does not involve direct empirical data collection in the conventional sense. Instead, it utilizes:
- Analytical Solutions: Employing established heat transfer equations and guidelines to determine initial design parameters for heat sinks.
- 3D CAD Modeling: Creating virtual prototypes of heat sink designs using CAD software (AutoCAD, ProEngineer).
- CAE Simulations: Utilizing Computer Aided Engineering (CAE) software (ANSYS Workbench, MSC Patran) to simulate thermal and structural performance of the designs.
- Environmental Impact Data: Utilizing existing data and methodologies like Life Cycle Assessment (LCA) principles to estimate environmental impacts, including CO2 emissions, associated with different design choices and manufacturing processes.
Analysis Method:
The analysis involves a multi-faceted approach:
- Thermal Analysis: Using analytical solutions and CAE simulations to evaluate heat transfer performance, determine optimal fin spacing, fin thickness, and overall thermal resistance.
- Structural Analysis: CAE simulations to assess the structural integrity of the heat sink design under operational loads, ensuring it can withstand mechanical stresses.
- Environmental Impact Assessment: Applying LCA principles to benchmark design scenarios based on environmental costs. This includes evaluating raw material requirements, manufacturing energy consumption, and end-of-life considerations to estimate CO2 emissions.
- Comparative Analysis: Comparing different design scenarios based on thermal performance, structural integrity, manufacturability, and environmental impact to identify the most sustainable design.
Research Subjects and Scope:
The subject of this research is heat sinks designed for cooling electronic components in industrial applications. The scope is specifically focused on the eco-design of a passive heat sink for a variable speed drive. The design process and methodology are presented as applicable to general heat sink design but are exemplified through this specific case study. The material considered for the heat sink is Aluminum A360.0-F.
6. Main Research Results:
Key Research Results:
The research successfully developed and demonstrated a CAD/CAE approach for eco-designing heat sinks. Key results include:
- Analytical and Numerical Design Concordance: Analytical solutions were used to derive initial heat sink parameters, which were then validated through CAE thermal simulations, showing a good agreement with a margin of error of 1.84%.
- Eco-Design Integration: The traditional CAD/CAE design process was extended to incorporate environmental considerations, allowing for the assessment of environmental impacts alongside performance metrics.
- Case Study Validation: The case study of a heat sink for a variable speed drive illustrated the effectiveness of the proposed approach. The design process considered both thermal performance and environmental impact, leading to a sustainable heat sink design.
- Environmental Benchmark: Different design scenarios were evaluated for their environmental impact, enabling the selection of a design that balances performance and environmental sustainability, as shown in Fig. 8.
Fig. 8. Environmental benchmark of multiple design scenarios.
Analysis of presented data:
- Fig. 1 illustrates the iterative stages of heat sink design, simulation, and manufacturing, emphasizing the integration of design adjustments based on simulation and manufacturability feedback.
- Fig. 2 outlines the CO2 emissions associated with each stage of a heat sink's lifecycle: manufacturing, use, and end-of-life, highlighting manufacturing as the major contributor.
- Fig. 3 presents the ECO-Design principles, focusing on design parameters like number of fins, fin spacing, fin thickness, and material choice, aiming for manufacturing with lower environmental impact and enhanced end-of-life strategies.
- Fig. 4 contrasts the traditional design approach with the extended Eco-Design approach, showing the integration of environmental benchmarks into the design validation loop.
- Fig. 5 shows the relationship between optimum fin thickness and heat transfer rate for a 20W forced-convection cooled heat sink, demonstrating the optimization process for fin dimensions.
- Fig. 6 is a 3D CAD model of the heat sink created using PTC ProEngineer, illustrating the virtual prototype developed in the design stage.
- Fig. 7 shows the CAE model pre-processing in MSC Patran, indicating the setup for simulation and analysis.
- Fig. 9 compares the baseline and final heat sink designs, highlighting design modifications made based on analysis and optimization.
- Fig. 10 displays the steady-state temperature distribution at the bottom of the heat sink from CAE simulation, showing thermal performance.
- Fig. 11 presents the equivalent Von-Mises stress distribution in the heat sink from structural analysis, confirming structural integrity.
- Fig. 12 illustrates multiple design scenarios with varying profile lengths, used for environmental benchmarking and design selection.
- Fig. 13 shows the Sandvik CoroGuide tool used for determining tool and process parameters for machining operations, relevant to manufacturing cost and emission estimation.
Figure Name List:
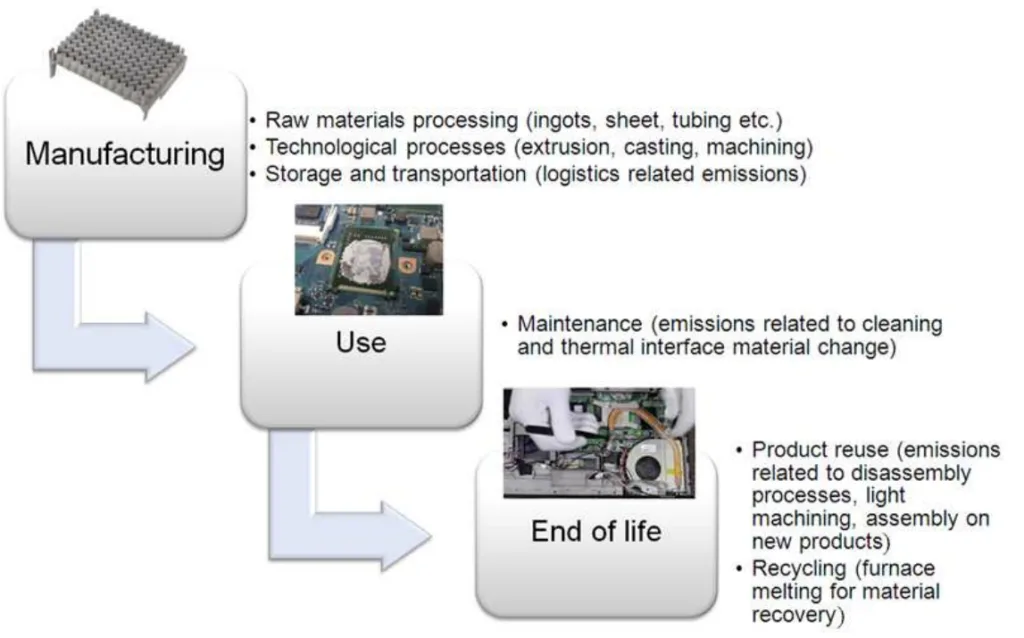
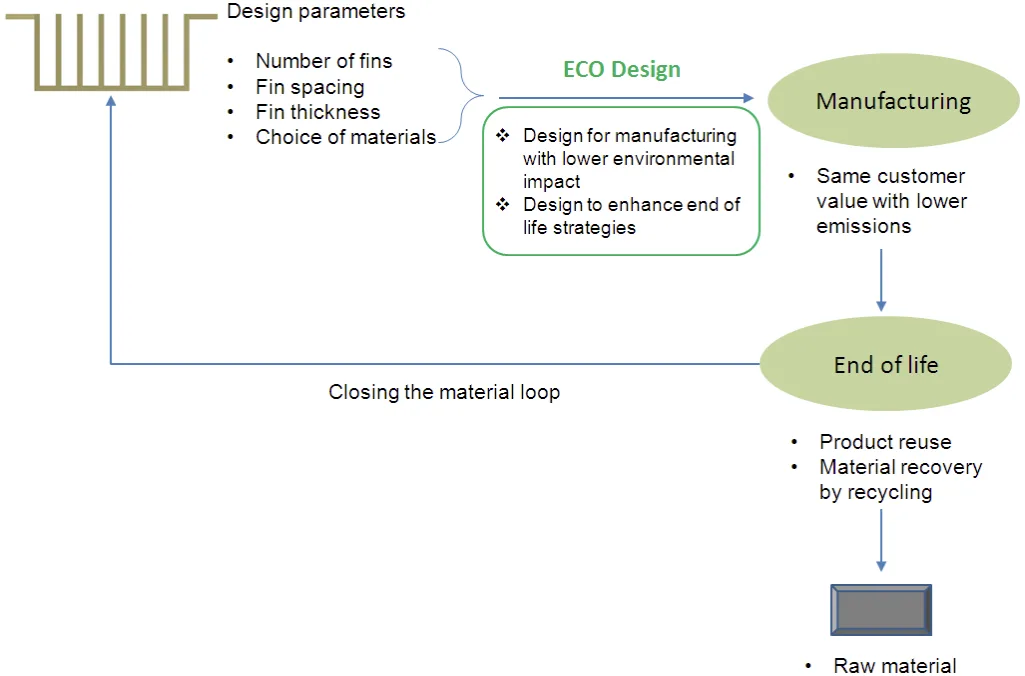
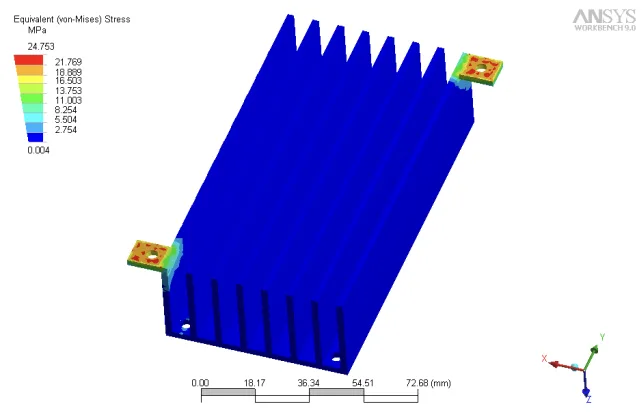
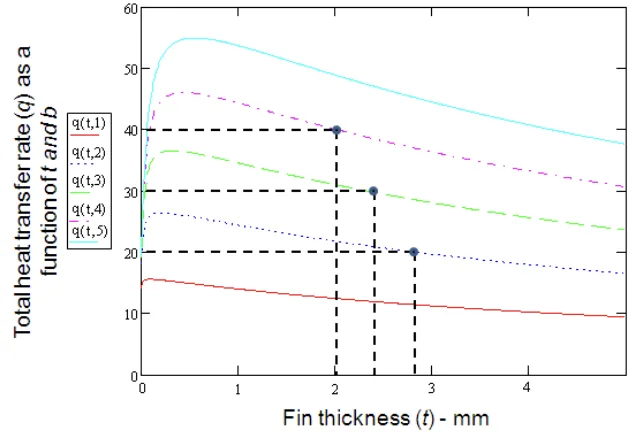
- Fig. 1. Stages of Heat Sinks design, simulation and manufacturing.
- Fig. 2. CO2 Emissions related to the life cycle of a heat sink.
- Fig. 3. ECO-Design principles.
- Fig. 4. The extension of traditional to Eco Design.
- Fig. 5. Optimum fin thickness vs heat transfer rate for a 20W forced-convection cooled heat sink design.
- Fig. 6. 3D CAD model using PTC ProEngineer.
- Fig. 7. CAE Model Pre-processing using MSC Patran.
- Fig. 8. Environmental benchmark of multiple design scenarios.
- Fig. 9. Heat sink: a - baseline design; b -final design.
- Fig. 10. Steady-state temperature at the bottom of the heat-sink.
- Fig. 11. Equivalent Von-Misses stress of the heat sink.
- Fig. 12. Multiple design scenarios for varying the total profile length.
- Fig. 13. Sandvik CoroGuide tool and process parameter calculator.
7. Conclusion:
Summary of Key Findings:
This study introduces an innovative CAD/CAE approach for heat sink design in industrial engineering, integrating Eco-Design principles. It extends traditional design methodologies by incorporating a decision loop to assess environmental scenarios based on their costs. The research emphasizes the novelty of combining manufacturing criteria with emission estimation. A case study on a variable speed drive heat sink demonstrates the efficiency of this new CAD/CAE approach, successfully meeting design requirements while promoting sustainability. The approach involves analytical solutions, 3D CAD modeling, CAE simulations for thermal and structural analysis, and environmental benchmarking using LCA principles.
Academic Significance of the Study:
The academic significance lies in the development of an integrated CAD/CAE framework for sustainable product design, specifically for heat sinks. It contributes to the field by providing a structured methodology that combines thermal engineering with environmental impact assessment. The research highlights the importance of considering the entire product lifecycle and incorporating environmental factors early in the design phase.
Practical Implications:
Practically, this research offers a valuable methodology for engineers and manufacturers to design more environmentally friendly heat sinks. By using the proposed CAD/CAE approach, companies can reduce the environmental footprint of their electronic products, decrease electronic waste, and meet growing ecological demands without compromising product performance. The case study provides a concrete example of how to implement this approach in industrial applications.
Limitations of the Study and Areas for Future Research:
The study acknowledges that future work can focus on incorporating multicriteria optimization techniques to further minimize manufacturing costs and environmental impacts. Exploring different materials, manufacturing processes, and more sophisticated LCA tools could also enhance the approach. Further research could also investigate the application of this methodology to other electronic components and thermal management solutions to broaden its impact.
8. References:
- [1] A. Popescu, G. Enciu, Data acquisition regarding the landmarks achieved inside a manufacturing flexible cell. Proceedings in Manufacturing Systems, Vol.6, No.3, 2011, pp. 29-26.
- [2] D. Ioan, CYBER-PHYSICAL-SYSTEMS (CPS) – Factor determinant în economia bazată pe inovare și cunoştinţe, Revista Română de Informatică şi Automatică, Vol.23, No.4, 2013, pp. 43-54.
- [3] F. Shrouf, J. Ordieres, Miraghotta G., Smart factories in Industry 4.0: A review of the concept and of energy management approached in production based on the Internet of Things paradigm, Industrial Engineering and Engineering Management (IEEM), Ed. Ghauth Jasmon, Malaysia, December 2014, IEEE, Selangor, pp. 697-701.
- [4] E. Westkämpfer, Next Generation Manufacturing Manufacturing 2030, available at: http://www.manufuture2011.eu/presentations/Ps1-Implementa-tion%20of%20ManuFuture%20Strategic%20Research%20Agenda/Engelbert%20Westk%C3%A4mper/Engelbert%20Westkamper.pdf, accessed: 2017-01-20.
- [5] K. Lundgren, The global impact of e-waste: Addressing the challenge, available at: http://www.ilo.org/sector/Resources/publications/WCMS_196105/lang--en/index.htm, accessed: 2017-01-22.
- [6] J. Ladou, S. Lovegrove, Export of electronics equipment waste., International journal of occupational and environmental health, Vol.14, No.1, 2008, pp. 1-10.
- [7] A.B. Cohen, R. Bahadur, Iyengar M. Least-energy optimization of air-cooled heat sinks for sustainability-theory, geometry and material selection., Energy, Vol.31, No.5, 2006, pp. 579-619.
- [8] N. Afgan, M.G. Caravalho, S. Prstic, A.B. Cohen, A. Sustainability assessment of aluminum heat sink design., Heat transfer engineering, Vol.24, No.4, 2003, pp. 39-48.
- [9] Gh. Amza, V.O. Rîndaşu, Tehnologia Materialelor, Volumul I (Technology of Materials, 1st volume), Editura Tehnică, Bucharest, 1997, pp. 10-30.
- [10] G. Rebitzer, T. Ekvallb, R. Frischknechtc, D. Hunkelerd, G. Norrise, T. Rydbergf, W.P. Schmidtg, S. Suhh, B.P. Weidemai, D.W. Penningtonf, Life cycle assessment: Part 1: Framework, goal and scope definition, inventory analysis, and applications, Environment International, Vol.30, No.5, 2004, pp. 701-720.
- [11] M. Holtzer, A. Bobrowski, B. Grabowska, Life cycle assessment as a method of limitation of a negative environment impact of castings, Archives of Foundry Engineering, Vol.11, No.3, 2011, pp. 25-30.
- [12] J. Pralea, E. Soltuz, ECO DESIGN PROCESS, Annals of the University of Oradea Fascicle of textiles, Leatherwork, Vol.15, No.1, 2014, pp. 167-170.
- [13] F. Vallet, D. Millet, S.G. Mahul, B. Tyl, Gwenola B., Using eco-design tools: An overview of experts' practices, Design Studies, Vol.34, No.3, 2013, pp. 345-377.
- [14] L. Ho Sung, Thermal design: heat sinks, thermoelectrics, heat pipes, compact heat exchangers, and solar cells, John Wiley & Sons, New Jersey, 2010, pp. 67-75.
- [15] G. Constantin, Modelarea 3D cu AutoCAD, Aplicaţii (3D Modeling using AutoCAD, Applications), Editura Politehnica Press, Bucharest, 2015, pp. 5-12.
- [16] V. Marek, Basic Research of Thermal Transfer Simulations, Proceedings in Manufacturing Systems, Volume 11, Iss. 3, 2016, pp. 119-124.
- [17] JF Schifo, Theoretical/Best Practice Energy Use in Metalcasting Operations, available at: www.afsinc.org/files/best%20practice%20energy-schifo-radia-may%202004.pdf, accessed: 2017-01-26.
- [18] S. Grimes, Donaldson J., G.C Gomez:, Report on the Environmental Benefits of Recycling, available at: http://www.bir.org/assets/Documents/publications/brochures/BIR_CO2_report.pdf, accessed: 2017-01-26.
- [19] ***, Anexă tehnică la instrucțiunile pentru modelul SEAP Factorii de emisie, available at: http://www.qaghaqapeteridashnagir.eu/IMG/pdf/technical_annex_ro.pdf, accessed: 2017-02-03
9. Copyright:
- This material is "Tudor-George ALEXANDRU, Cristina PUPĂZĂ"'s paper: Based on "ECO-DESIGN OF HEAT SINKS BASED ON CAD/CAE TECHNIQUES".
- Paper Source: [DOI URL] (Please replace with the actual DOI URL if available from the paper, otherwise remove)
This material was created to introduce the above paper, and unauthorized use for commercial purposes is prohibited.
Copyright © 2025 CASTMAN. All rights reserved.