This article introduces the paper 'Diesel engine for aircraft propulsion system' published by 'Combustion Engines'.
1. Overview:
- Title: Diesel engine for aircraft propulsion system
- Author: Michał GĘCA, Zbigniew CZYŻ, Mariusz SUŁEK
- Publication Year: 2017
- Publishing Journal/Academic Society: Combustion Engines
- Keywords: diesel engine, aircraft propulsion system, power-to-weight ratio, specific fuel consumption
![Fig. 1. Austro Engine AE 300 diesel aircraft piston engine [7]](https://castman.co.kr/wp-content/uploads/Fig.-1.-Austro-Engine-AE-300-diesel-aircraft-piston-engine-7-png.webp)
2. Abstracts
Stricter requirements for power in engines and difficulties in fueling gasoline engines at the airport make aircraft engine manufacturers design new engines capable of combusting fuel derived from JET-A1. New materials used in compression-ignition engines enable weight reduction, whereas the technologies of a Common Rail system, supercharging and 2-stroke working cycle enable us to increase the power generated by an engine of a given displacement. The paper discusses the parameters of about 40 types of aircraft compression ignition engines. The parameters of these engines are compared to the spark-ignition Rotax 912 and the turboprop. The paper also shows trends in developing aircraft compression-ignition engines.
3. Research Background:
Background of the Research Topic:
The selection of an engine for light aircraft is multifaceted, hinging on factors such as power output, engine weight, the power-to-weight ratio, specific fuel consumption, and power density. While the power-to-weight ratio is a crucial consideration, studies indicate that specific fuel consumption exerts a more significant influence on overall aircraft design. Consequently, engines characterized by low specific fuel consumption, while still meeting power demands, are frequently favored [1].
Contemporary trends in aircraft piston engine development are increasingly influenced by advancements in automotive engineering. The adoption of technologies like computer-controlled Common Rail high-pressure injection systems and variable pressure turbochargers, initially refined for automotive applications, is becoming more prevalent in aircraft engines. Furthermore, growing ecological concerns and the imperative to mitigate climate change are driving the development of aircraft piston engines that leverage these automotive innovations. The integration of diesel engines, designed to operate on unified fuel [5], is particularly noteworthy due to their potential for reduced toxic exhaust emissions, stemming from a fuel composition devoid of harmful substances like lead, benzene, and solvents. Diesel engines also promise enhanced reliability and reduced maintenance costs by eliminating issues associated with carburetor icing, ignition system failures, and vapor lock [2].
Status of Existing Research:
Historically, aviation favored lightweight, water-cooled, in-line spark ignition engines, achieving peak performance during the Second World War. However, current reciprocating engines in sectors like sports, emergency, agricultural, and recreational aviation often reflect pre-war design and manufacturing philosophies, particularly when contrasted with the sophisticated advancements in automotive engine technology. These engines commonly employ carburetors of a relatively primitive design. Despite this, the General Aviation sector, particularly the ultralight aircraft market, remains substantial. The autogyro, in particular, has seen a resurgence due to less stringent regulatory oversight on construction and certification [18]. This research endeavors to address the current landscape by focusing on the parameters of compression ignition engines and comparing them against established aircraft engine technologies like spark-ignition engines.
Necessity of the Research:
The impetus for this research stems from the increasingly stringent power demands in aviation and the logistical challenges associated with fueling gasoline engines at airports. This necessitates the development of novel engine designs capable of utilizing fuels derived from JET-A1. The advent of new materials in compression-ignition engines, coupled with technologies such as Common Rail systems, supercharging, and 2-stroke working cycles, facilitates weight reduction and power augmentation for engines of a given displacement. This paper aims to define and analyze the characteristics of compression-ignition engines specifically tailored for lightweight aircraft applications.
4. Research Purpose and Research Questions:
Research Purpose:
This paper aims to comprehensively analyze and discuss the operational parameters of approximately 40 distinct types of aircraft compression ignition engines. A key objective is to benchmark these parameters against those of the widely used spark-ignition Rotax 912 engine and turboprop engines, providing a comparative performance perspective. Furthermore, the paper seeks to elucidate prevailing trends in the ongoing development of aircraft compression-ignition engine technology.
Key Research:
The core research questions addressed in this paper are centered on:
- Detailed examination of the operational parameters of various aircraft compression ignition engines.
- Comparative analysis of these parameters with those of the spark-ignition Rotax 912 engine and turboprop engine technologies.
- Identification and analysis of current developmental trends shaping the evolution of aircraft compression-ignition engines.
Research Hypotheses:
While not explicitly formulated as formal hypotheses, the research operates under the implicit premise that compression-ignition engines represent a viable and increasingly attractive alternative for aircraft propulsion. This viability is predicated on their inherent fuel efficiency advantages and the continuous advancements in compression-ignition engine technologies, making them potentially competitive with, or even superior to, traditional spark-ignition and turboprop systems in specific aviation applications.
5. Research Methodology
Research Design:
The research employed a comparative analysis design, underpinned by the creation of a comprehensive database. This database encompasses approximately 40 different diesel piston engines specifically utilized in light aircraft and gyroplanes. The study systematically compares and contrasts the operational parameters of these engines to discern trends and performance characteristics.
Data Collection Method:
Data collection was primarily achieved through an extensive literature review. The research team compiled existing data and specifications for a wide range of aircraft compression ignition engines from publicly available sources, technical publications, and manufacturer specifications. This method allowed for the aggregation of a substantial dataset necessary for comparative analysis. (Methodology is inferred from the content of the paper, though not explicitly stated.)
Analysis Method:
The collected data underwent a parameter-based comparative analysis. Key engine parameters, such as power output, engine weight, brake specific fuel consumption (BSFC), and cylinder arrangement, were systematically compared across the dataset of compression-ignition engines, as well as against benchmark engines like the Rotax 912 and turboprop designs. The analysis included descriptive statistics to determine average values and identify performance trends within the studied engine types.
Research Subjects and Scope:
The research focused on a defined scope of approximately 40 types of aircraft compression ignition engines. The comparative analysis specifically included the Rotax 912 spark-ignition engine and turboprop engines as benchmarks. The study's scope was limited to engines intended for use in light aircraft and gyroplanes, reflecting a specific segment of the aviation market where diesel engine technology is gaining traction.
6. Main Research Results:
Key Research Results:
The research yielded a comprehensive overview of aircraft compression-ignition engine designs, encompassing manufacturers such as Austro Engine, Safran, WAM Engines, CKT Aero Engines, Continental Motors, Superior Air Parts, Weslake, DeltaHawk Engines, Zoche Aero-Diesel, and DAIR. A key output was the establishment of a database detailing approximately 40 diesel piston engines used in light aircraft. The study systematically compared engine characteristics across several critical parameters:
- Operating Cycle: Analysis of 2-stroke versus 4-stroke engine performance and prevalence.
- Cylinder Arrangement: Examination of different configurations including boxer, in-line, V-type, radial, and opposed-piston arrangements.
- Number and Displacement of Cylinders: Statistical analysis of cylinder count and engine displacement.
- Engine Power and Weight: Comparative assessment of power output and engine weight metrics.
- Fuel Consumption: Evaluation of brake specific fuel consumption (BSFC) values.
- Chamber Dimensions: Analysis of stroke-to-bore (S/D) ratios.
- Compression Ratio: Comparison of compression ratios across different engine types.
Analysis of presented data:
The analysis of the collected data revealed several key trends and performance characteristics of aircraft compression-ignition engines:
- Weight and Fuel Efficiency Trade-off: Diesel engines, while generally heavier than gasoline counterparts, exhibit superior fuel efficiency.
- 2-Stroke Cycle Advantages and Disadvantages: 2-stroke engines offer a better power-to-weight ratio but tend to be less fuel-efficient compared to 4-stroke engines.
- Dominant Cylinder Arrangements: Boxer and opposed-piston cylinder arrangements are prevalent in aircraft diesel engine designs.
- Compact Designs: In-line and V90° engine configurations offer more compact installation options.
- Average Engine Parameters: The average displacement per cylinder for the analyzed diesel aircraft engines is 812 cm³. The average power-to-weight ratio is approximately 0.97 kW/kg, and the average BSFC is 237 g/kWh.
- Performance Benchmarks: The Zoche ZO03A and Rotax 912 engines were identified as exhibiting particularly favorable BSFC and power-to-weight ratios within their respective engine classes.
- S/D and Compression Ratios: The stroke-to-bore ratio for compression-ignition engines typically ranges from 0.9 to 1.1, and the compression ratio averages around 18.
Figure Name List:
![Fig. 2. Safran SR 460 diesel aircraft piston engine [16]](https://castman.co.kr/wp-content/uploads/image-689-png.webp)
![Fig. 3. WAM-165BB diesel aircraft piston engine [19]](https://castman.co.kr/wp-content/uploads/image-690-png.webp)
![Fig. 4. CKT-240 TD diesel aircraft piston engine [8]](https://castman.co.kr/wp-content/uploads/image-691-png.webp)
![Fig. 5. CD-135/155 diesel aircraft piston engine [9]](https://castman.co.kr/wp-content/uploads/155-diesel-aircraft-piston-engine-9--png.webp)
![Fig. 6. Gemini 100 diesel aircraft opposite piston engine (right) and its cylinder liner (left) [6]](https://castman.co.kr/wp-content/uploads/image-692-png.webp)
![Fig. 7. DAIR 100 diesel aircraft piston engine [10]](https://castman.co.kr/wp-content/uploads/image-693-png.webp)
![Fig. 8. Weslake A80 diesel aircraft opposite piston engine [17]](https://castman.co.kr/wp-content/uploads/image-694-png.webp)
![Fig. 9. Delta Hawk diesel aircraft piston engine [11]](https://castman.co.kr/wp-content/uploads/image-695-png.webp)
![Fig. 10. Zoche aero-diesel ZO series diesel aircraft piston engines [20]](https://castman.co.kr/wp-content/uploads/image-696-png.webp)
![Fig. 11. Aircraft turboshaft TP- 100 engine (right) [15] and Rotax 912- ULS spark ignition engine (left) [13]](https://castman.co.kr/wp-content/uploads/image-697-png.webp)
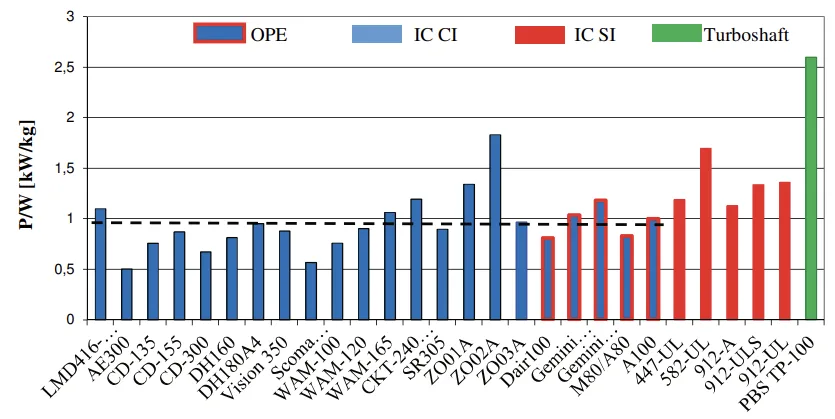
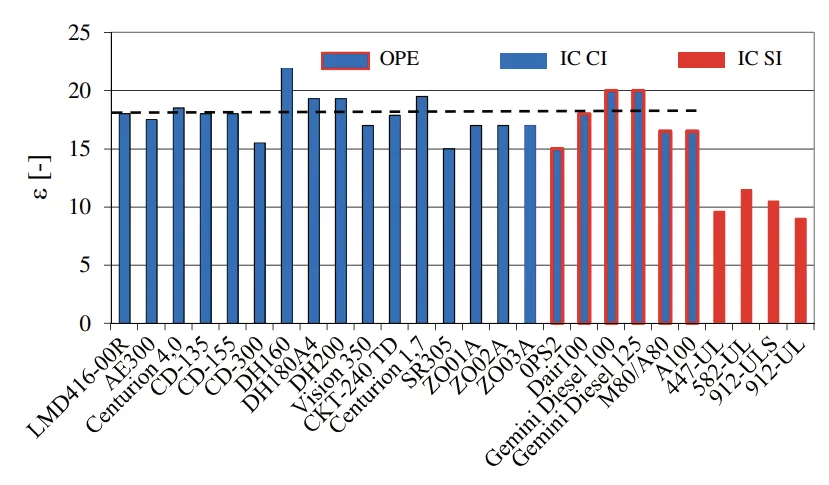
- Fig. 1. Austro Engine AE 300 diesel aircraft piston engine [7]
- Fig. 2. Safran SR 460 diesel aircraft piston engine [16]
- Fig. 3. WAM-165BB diesel aircraft piston engine [19]
- Fig. 4. CKT-240 TD diesel aircraft piston engine [8]
- Fig. 5. CD-135/155 diesel aircraft piston engine [9]
- Fig. 6. Gemini 100 diesel aircraft opposite piston engine (right) and its cylinder liner (left) [6]
- Fig. 7. DAIR 100 diesel aircraft piston engine [10]
- Fig. 8. Weslake A80 diesel aircraft opposite piston engine [17]
- Fig. 9. Delta Hawk diesel aircraft piston engine [11]
- Fig. 10. Zoche aero-diesel ZO series diesel aircraft piston engines [20]
- Fig. 11. Aircraft turboshaft TP- 100 engine (right) [15] and Rotax 912-ULS spark ignition engine (left) [13]
- Fig. 12. Cylinder arrangement in diesel aircraft engines.
- Fig. 13. Power/unit displacement ratio for aircraft piston engines
- Fig. 14. Power-to-weight ratio for aircraft engines
- Fig. 15. Power vs. BSFC for the aircraft engines studied here
- Fig. 16. Weight vs. BSFC for the aircraft engines studied here
- Fig. 17. Stroke vs. bore as S/D ratio for the aircraft piston engines studied here
- Fig. 18. Compression ratio for the models of the aircraft piston engines studied here
7. Conclusion:
Summary of Key Findings:
The research concludes that the developmental trajectory of aircraft compression-ignition engines is bifurcated, encompassing both the adaptation of existing car engine designs and the creation of entirely new engine architectures, particularly 2-stroke opposed-piston engines. The majority of contemporary aircraft compression-ignition engines are characterized as 4-stroke, 4-piston, liquid-cooled, and supercharged. While diesel engines typically exhibit a lower power-to-weight ratio compared to spark-ignition and turboprop engines, they offer significant advantages in fuel consumption. Notably, the Zoche ZO03A and Rotax 912 engines stand out for their superior performance in terms of BSFC and power-to-weight ratio, respectively. Furthermore, diesel engines possess the operational benefit of being able to run without a reduction gear, simplifying the powertrain and reducing overall mass.
Academic Significance of the Study:
This study provides a valuable academic contribution by offering a structured and comprehensive overview of the current state of aircraft compression-ignition engine technology. It establishes a comparative framework for evaluating different engine designs and identifies key performance parameters relevant to aircraft applications. The research enhances the understanding of the potential and limitations of diesel engines in aviation and serves as a foundational resource for further academic inquiry in this domain.
Practical Implications:
The findings of this research hold significant practical implications for aircraft engine designers and manufacturers. The comparative analysis of engine parameters offers valuable insights for optimizing future engine designs, particularly in the context of fuel efficiency and power density. The study underscores the advantages of diesel engines in terms of fuel economy and the broader availability of diesel and JET A-1 fuel, which can inform strategic decisions regarding engine selection for specific aircraft applications. Ultimately, this research supports the ongoing development of more fuel-efficient and environmentally conscious aircraft propulsion systems.
Limitations of the Study and Areas for Future Research:
The study's primary limitation lies in its reliance on existing engine data and literature, which may inherently reflect certain biases or data gaps. Future research endeavors could benefit from more granular performance data, including detailed emissions testing and comprehensive lifecycle cost analyses for aircraft diesel engines. Further investigation into the перспективный 2-stroke opposed-piston engine technology for aircraft propulsion is also warranted, given its potential for enhanced power-to-weight ratios and fuel efficiency.
8. References:
- [1] DONOVAN, R. The design of an uninhabited air vehicle for remote sensing in the cryosphere. University of Kansas 2007.
- [2] FAROKHI, S. Aircraft propulsion. ISBN: 978-1-118-80677-7, 2004.
- [3] FLINT, M., PIRAULT, J.P. Opposed piston engines: evolution, use, and future applications. SAE International. PA ISBN 978-0-7680-1800-4, Warrendale 2009.
- [4] REGNER, G., JOHNSON, D., KOSZEWNIK, J., DION, E. et al. Modernizing the opposed piston, two stroke engine for clean, efficient transportation. SAE Technical Paper. 2013, 2013-26-0114.
- [5] Revised IPCC Guidelines for National Greenhouse Gas Inventories, 1996.
- [6] www.achatespower.com
- [7] www.austroengine.at
- [8] www.cktaeroengines.com/
- [9] www.continentalmotors.aero
- [10] www.dair.co.uk
- [11] www.deltahawkengines.com
- [12] www.dlapilota.pl/wiadomosci/dlapilota/aktualizacja-ceny-paliw-lotniczych-na-polskich-lotniskach
- [13] www.faston.pl
- [14] www.generalaviationnews.com/2015/01/01/measuring-growth-in-lsa/
- [15] www.pbsvb.com
- [16] www.smaengines.com
- [17] www.weslake.eu
- [18] www.wiatrakowce.org
- [19] www.wilksch.net
- [20] www.zoche.de
9. Copyright:
- This material is "Michał GĘCA, Zbigniew CZYŻ, Mariusz SUŁEK"'s paper: Based on "Diesel engine for aircraft propulsion system".
- Paper Source: 10.19206/CE-2017-202
This material was summarized based on the above paper, and unauthorized use for commercial purposes is prohibited.
Copyright © 2025 CASTMAN. All rights reserved.