This article introduces the paper "Development of the Rheo-Diecasting Process for Mg-Alloys" by Z. Fan, S. Ji, and G. Liu, published in Materials Science Forum Vols. 488-489 (2005), pages 405-412.
1. Overview:
- Title: Development of the Rheo-Diecasting Process for Mg-Alloys
- Author: Z. Fan, S. Ji, G. Liu
- Publication Year: 2005
- Publishing Journal/Academic Society: Materials Science Forum Vols. 488-489
- Keywords: Semisolid, Rheo-diecasting, Microstructure, Mechanical properties.
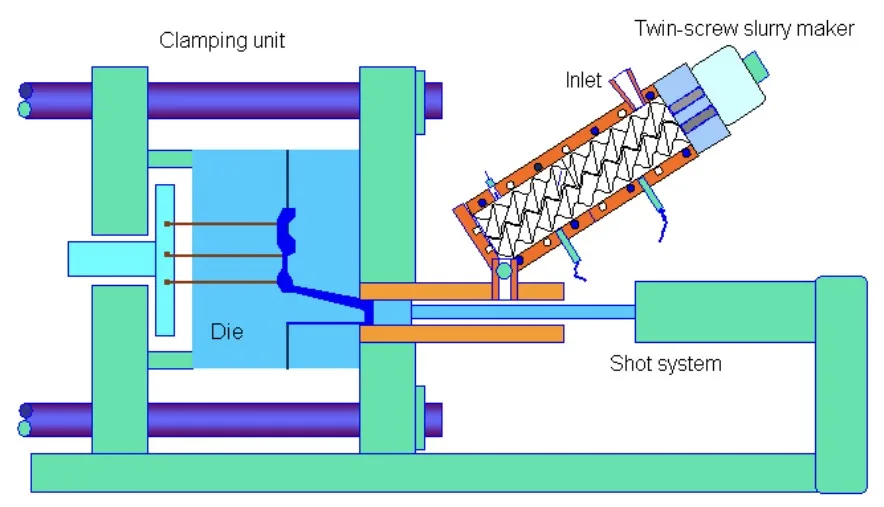
2. Research Background:
- Social/Academic Context of the Research Topic:
- Increasing environmental concerns and tightening government regulations on CO2 emission are driving the automotive industry to focus on vehicle weight reduction and improved fuel economy.
- Magnesium alloys, being the lightest structural materials, are highly suitable for automotive applications to achieve these goals.
- Magnesium usage in the automobile industry has seen substantial growth in recent years, and this trend is expected to continue, extending to other sectors like aerospace, electronics, and healthcare.
- Currently, high pressure diecasting (HPDC) is the dominant processing method for magnesium alloy components, primarily limited to alloys like AZ91 and AM60.
- Limitations of Existing Research:
- Further growth in magnesium applications is hindered by the limitations of existing processing technologies, particularly HPDC, in producing high quality, low-cost components and enabling the use of new alloys with higher operating temperatures.
- Conventional HPDC processes may not be optimal for achieving the desired microstructure and mechanical properties for advanced magnesium alloy applications.
- Necessity of the Research:
- There is a need for the development of new processing technologies for magnesium alloys that can overcome the limitations of HPDC.
- Specifically, a new semisolid processing technique is required to produce high-quality, cost-effective magnesium components with enhanced performance characteristics.
- The development of such a technology would facilitate the wider adoption of magnesium alloys in various industries, particularly in demanding applications requiring high safety and structural integrity.
3. Research Purpose and Research Questions:
- Research Purpose:
- To develop a new semisolid processing technique called rheo-diecasting (RDC) for Mg-alloys.
- To optimize the rheo-diecasting process using AZ91D Mg-alloy.
- To evaluate the microstructure and mechanical properties of rheo-diecast AZ91D Mg-alloy and compare them with those produced by other processing methods.
- Key Research Questions:
- What are the ideal characteristics of a semisolid slurry for semisolid metal (SSM) processing to achieve laminar mould filling and fine, uniform microstructure?
- What are the conditions necessary to enhance effective nucleation and promote spherical growth during solidification in semisolid processing?
- How does the rheo-diecasting (RDC) process, utilizing a twin-screw slurry maker, affect the microstructure of AZ91D Mg-alloy compared to conventional HPDC and other semisolid processing techniques?
- What are the mechanical properties of rheo-diecast AZ91D Mg-alloy, and how do they compare to those achieved by other processing methods?
- Research Hypotheses:
- By controlling nucleation and growth processes through uniform temperature and chemistry, high shear rate, and high intensity of turbulence during solidification, an ideal semisolid slurry can be produced.
- The rheo-diecasting (RDC) process, based on the twin-screw slurry maker, will produce AZ91D Mg-alloy components with close-to-zero porosity, fine and uniform microstructure.
- Rheo-diecast AZ91D Mg-alloy components will exhibit improved mechanical properties, particularly ductility, compared to components produced by conventional HPDC and other semisolid processing techniques.
4. Research Methodology
- Research Design:
- The research employed an experimental investigation approach combined with theoretical analysis of solidification under forced convection.
- The study involved the development and implementation of the rheo-diecasting (RDC) process.
- Microstructure characterization and mechanical property evaluation were conducted on rheo-diecast AZ91D Mg-alloy samples.
- Comparative analysis was performed against samples produced by other processing technologies reported in literature.
- Data Collection Method:
- Material: AZ91D (Mg-8.8Al-0.67Zn-0.22Mn-0.03Si, in wt.%) Mg-alloy supplied by MEL (Manchester, UK).
- Rheo-diecasting Process: A new rheo-diecasting (RDC) process was developed, combining a twin-screw slurry maker with a conventional HPDC machine.
- AZ91D alloy ingot was melted at 675°C under N2+0.5vol.% SF6 gas mixture and fed into the slurry maker at 630°C.
- Slurry maker temperature range corresponded to a solid fraction range of 0-0.5.
- A 280ton cold chamber die casting machine was used for casting.
- Microstructure Examination: Optical microscopy and Scanning Electron Microscopy (SEM) were used to characterize the microstructure of rheo-diecast samples. EDX analysis was also employed for detailed microstructural examination.
- Mechanical Property Testing: Tensile tests were conducted on standard tensile test samples cast using a specially manufactured die to evaluate the mechanical properties of rheo-diecast AZ91D alloy.
- Analysis Method:
- Microstructural Analysis: Qualitative and quantitative analysis of micrographs to assess porosity, grain size, morphology of primary particles and eutectic phases, and uniformity of microstructure.
- Mechanical Property Analysis: Determination of Yield strength, Tensile Strength, and Elongation from tensile test data.
- Comparative Analysis: Comparison of microstructure and mechanical properties of rheo-diecast AZ91D with those reported in literature for AZ91D alloy processed by HPDC, thixocasting, thixomoulding, and New rheocasting (NRC).
- Research Subjects and Scope:
- The research focused on the development and optimization of the rheo-diecasting (RDC) process for Mg-alloys, specifically using AZ91D alloy.
- The scope included investigating the effect of RDC process parameters on the microstructure and mechanical properties of AZ91D alloy.
- Component production trials were conducted to assess the reliability and consistency of the RDC process.
5. Main Research Results:
- Key Research Results:
- The rheo-diecasting (RDC) process successfully produced AZ91D Mg-alloy samples with significantly improved microstructure and mechanical properties compared to conventional HPDC and other semisolid processing techniques.
- Rheo-diecast samples exhibited close-to-zero porosity (well below 0.5 vol.%).
- The microstructure was fine and uniform throughout the sample, with no observed segregation.
- Primary particles were fine (around 50µm), spherical, and uniformly distributed.
- Oxide particles were fine (a few microns), spherical, well-dispersed, and uniformly distributed.
- Mechanical properties were significantly enhanced, particularly ductility, which was approximately twice that of HPDC processed samples.
- Statistical/Qualitative Analysis Results:
- Porosity: Porosity in rheo-diecast samples was consistently well below 0.5 vol.%, with pores rarely observed and occasionally small in size (at micron level). Micro-porosity due to solidification shrinkage was significantly reduced or eliminated.
- Microstructure:
- Primary particles were uniformly distributed throughout the entire sample.
- No chemical segregation was observed throughout the casting.
- The remaining liquid in the SSM slurry solidified under high cooling rate, resulting in extremely fine α-phase (<10µm).
- The Mg17Al12 β-phase formed through eutectic solidification exhibited an irregular morphology and was located at grain boundaries, with no evidence of coupled eutectic growth, suggesting divorced eutectic solidification.
- Mechanical Properties: Table 1 presents a comparison of mechanical properties: Table 1. Mechanical properties of AZ91D alloy produced by different processing technologies. Process Yield strength (MPa) Tensile Strength (MPa) Elongation (%) Reference HPDC 146 212 3.3 [10] Thixocasting 134 223 3.6 [11] Thixomoulding -- 150-241 3-5 [12] New rheocasting (NRC) -- 230 5.5 [13] Rheo-diecasting (RDC) 145 248 8.9 This work
- Rheo-diecasting (RDC) demonstrates a significantly higher Elongation (8.9%) compared to HPDC (3.3%), Thixocasting (3.6%), and Thixomoulding (3-5%). Tensile Strength is also improved compared to HPDC and Thixocasting.
- Data Interpretation:
- The improved microstructure achieved by the RDC process, characterized by fine and uniform grains, reduced porosity, and well-dispersed oxide particles, is directly responsible for the enhanced mechanical properties, particularly the significant increase in ductility.
- The twin-screw slurry maker effectively promotes nucleation and spherical growth through high shear rate and turbulence, leading to the desirable semisolid slurry characteristics and subsequent microstructure refinement in the rheo-diecast components.
- The laminar mould filling in RDC minimizes gas entrapment, contributing to the low porosity levels.
- Figure Name List:
- Figure 1. Schematic illustration of the rheo-diecasting (RDC) process.
- Figure 2. Photograph and micrographs showing the laminar flow front during mould filling.
- Figure 3. Microstructure of the rheo-diecast AZ91D alloy through the entire cross-section of the φ6 tensile test bar.
- Figure 4. Microstructures of rheo-diecast AZ91D alloy produced at different processing temperatures. (a) 585°C; (b) 589°C; (c) 593°C; (d) 600°C.
- Figure 5. SEM micrographs of rheo-diecast AZ91D alloy showing the morphology of primary particles formed through the secondary solidification of the remaining liquid and the detailed morphology of the Mg17Al12 β-phase formed through eutectic solidification.
- Figure 6. Optical micrographs showing the microstructure of rheo-diecast LM24 components at different locations.
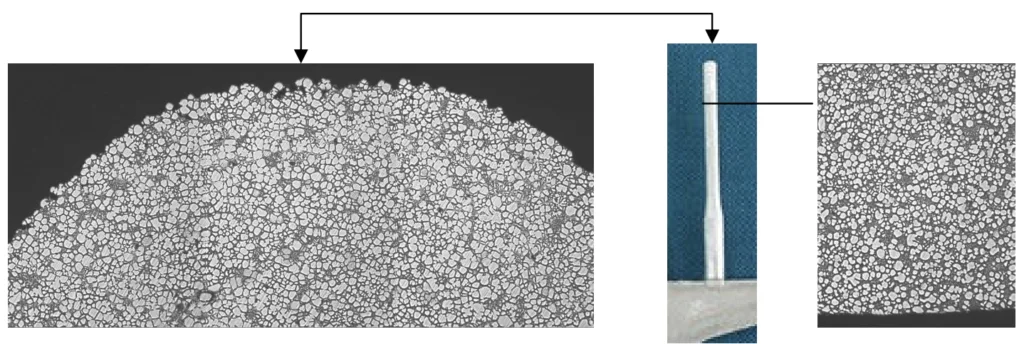

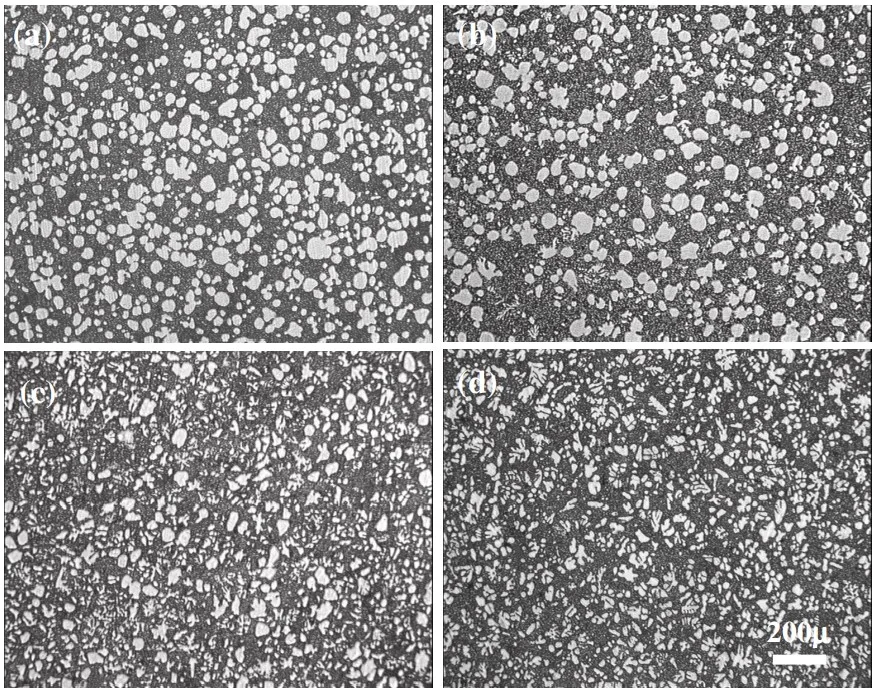


6. Conclusion and Discussion:
- Summary of Main Results:
- The research successfully developed a new semisolid metal processing technology, rheo-diecasting (RDC), for producing high integrity Mg-alloy components.
- The RDC process is based on the understanding of semisolid slurry rheology and the conditions for achieving ideal semisolid slurries, including uniform temperature and chemistry, high shear rate, and high intensity of turbulence during solidification.
- Experimental results using AZ91D Mg-alloy demonstrated that RDC produces samples with close-to-zero porosity, fine and uniform microstructure, and significantly improved mechanical properties, especially ductility.
- Component production trials further confirmed the reliability and consistency of the RDC process.
- Academic Significance of the Research:
- The study provides valuable insights into the development of ideal semisolid slurries for SSM processing by identifying the critical conditions for enhanced nucleation and spherical growth.
- It demonstrates the effectiveness of the twin-screw slurry maker in achieving these conditions and enabling the successful implementation of the rheo-diecasting (RDC) process.
- The research contributes to the fundamental understanding of semisolid solidification and its application in advanced metal processing.
- Practical Implications:
- The rheo-diecasting (RDC) process offers a viable and advantageous alternative to conventional HPDC and other semisolid processing techniques for producing high-performance Mg-alloy components.
- RDC is particularly suitable for the production of high-safety, airtight, and highly stressed components, especially in the automotive industry, where weight reduction and structural integrity are critical.
- The process offers potential benefits such as lower scrap rate, higher material yield, and lower overall component production cost due to increased productivity and reduced defects.
- The ease of implementing RDC by attaching a slurry maker to a cold chamber HPDC machine makes it practically attractive for industrial adoption.
- Limitations of the Research:
- The study primarily focused on AZ91D Mg-alloy. Further research is needed to evaluate the applicability and optimize the RDC process for other Mg-alloys and different component geometries and complexities.
- While component production trials were conducted, further industrial-scale validation and cost-effectiveness analysis are required to fully assess the practical viability of the RDC process in mass production environments.
7. Future Follow-up Research:
- Directions for Follow-up Research:
- Further optimization of the rheo-diecasting (RDC) process parameters to enhance microstructure and mechanical properties further.
- Investigation of the RDC process for a wider range of Mg-alloys, including high-performance alloys and alloys with improved high-temperature properties.
- Exploration of the application of RDC to produce larger and more complex Mg-alloy components for various industrial sectors.
- Detailed investigation of the heat treatment response of rheo-diecast Mg-alloy components and optimization of heat treatment procedures to maximize mechanical performance without compromising surface quality and dimensional control.
- Areas Requiring Further Exploration:
- Long-term performance and reliability evaluation of rheo-diecast Mg-alloy components under various service conditions.
- Comprehensive cost-effectiveness analysis of the RDC process compared to conventional HPDC and other competing manufacturing technologies, considering factors such as production volume, material costs, and energy consumption.
- Development of advanced control systems and automation for the RDC process to ensure consistent and high-quality component production in industrial settings.
8. References:
[1] H. Fridrich, and S. Schumann: in Proc. 2nd Israeli Inter. Conf. Mg Science and Technology, Dead Sea, Israel, (2000), 9.
[2] H. Fridrich and S. Schumann: in Proc. IMA 2001 Magnesium Conf., Brussels, Belgium, (2001), 8.
[3] S. Ji, Z. Fan, G. Liu, X. Fang and S.H. Song, in in “Proc. 7th Inter. Conf. Semisolid Metal Processing", Tsukuba, Japan, Sept. 25-27, 2002, eds. Y Tsutsui et al, pp683-688
[4] J.Y. Chen and Z. Fan: Mater. Sci. Tech., 18 (2002), 237, 243, 250, 258.
[5] P.D. Lee, Private communication, Department of Materials, Imperial College, London, 2003.
[6] A Das and Z Fan, Mat. Sci. Tech., 19 (2003) 573-580.
[7] A. Das, S. Ji and Z. Fan, Acta Materialia, 50 (2002), 4571-4585.
[8] S. Ji and Z. Fan, Met. Mater. Trans. 33A (2002), 3511-3520.
[9] S. Ji, Z. Fan and M. J. Bevis: Mater. Sci. Eng., A299 (2001), 210-217
[10]C. Pitsaris, T.Abbott, C.H.J. Davies and G. Savage, in Magnesium: Proc. 6th Inter. Conf. Magnesium Alloy and Their Application, ed. By K.U. Kainer, (Weinheim, Wiley-VCH, Verlay GmbH & Co. KGaA, 2003), 694.
[11]J. Aguilar, T. Grimming and A. Bührig-Polaczek, in Magnesium: Proc. 6th Inter. Conf. Magnesium Alloy and Their Application, ed. By K.U. Kainer, (Weinheim, Wiley-VCH, Verlay GmbH & Co. KGaA, 2003), 767.
[12]F. Czerwinski, et al., Acta Materialia, 49 (2001), 1225-1235
[13]H. Kaufmann and P.J. Uggowitzer, in Magnesium Alloy and Their Application, ed. By K.U. Kainer, (Weinheim, Wiley-VCH, Verlay GmbH & Co. KGaA, 2000), 533.
9. Copyright:
*This material is Z. Fan, S. Ji, G. Liu's paper: Based on Development of the Rheo-Diecasting Process for Mg-Alloys.
*Paper Source: http://dx.doi.org/10.4028/www.scientific.net/MSF.488-489.405
This material was summarized based on the above paper, and unauthorized use for commercial purposes is prohibited.
Copyright © 2025 CASTMAN. All rights reserved.