This article introduces the paper ['Development of a die design system for die casting'] presented at the ['Int J Adv Manuf Technol']
1. Overview:
- Title: Development of a die design system for die casting
- Author: Y. K. Woon, K. S. Lee
- Publication Year: 2004
- Publishing Journal/Academic Society: Int J Adv Manuf Technol (International Journal of Advanced Manufacturing Technology)
- Keywords: Die casting, Die design system, Feature-based, Constraint-based, Parametric design, B-rep model
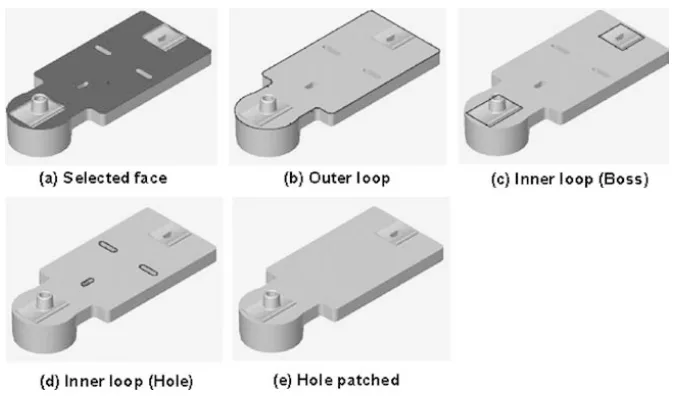
2. Research Background:
Background of the Research Topic:
The die casting process is a prominent manufacturing method for producing dimensionally accurate and sharply defined metal components. Designing die casting dies is a multi-stage process that is inherently time-intensive. The complexity of achieving an acceptable initial die design often necessitates iterative modifications, further prolonging the design cycle.
Status of Existing Research:
Prior research efforts have explored automated or semi-automated design solutions for individual die elements, particularly focusing on gating systems. Examples include prototype gating system designs utilizing P-Q² techniques and feature-based parametric design, and commercial applications like DiEdiFice, which specializes in gating and runner system design for pressure die casting. However, DiEdiFice does not extend to ejector and cover cavity insert creation. Existing complete die design systems, such as those based on AutoCAD, are limited in application to simple shapes and single impression dies without undercuts. Integrated CAD/CAE systems have been explored for die geometry and process parameter optimization using simulation analysis. Specialized software packages like IMOLD exist for semi-automated injection mold design, but are not directly applicable to die casting due to the increased complexity of die casting gating systems.
Necessity of the Research:
The die casting industry would significantly benefit from application software that integrates the various die design stages and facilitates design editing. The increasing adoption of 3D CAD in die design underscores the need for systems that enhance visualization and streamline design revisions. Therefore, the development of a computer-aided die design system to reduce die design time is crucial.
3. Research Purpose and Research Questions:
Research Purpose:
The practical objectives of this research are twofold:
(1) To develop a system that integrates the different stages of the die design process.
(2) To facilitate the editing of die casting designs during and after the design process.
Key Research:
This research focuses on creating a user-friendly, computer-aided die design system for die casting dies. The system aims to enable both experienced and novice designers to efficiently design dies from a product part model.
Research Hypotheses:
The research hypothesizes that a die design system incorporating feature-based and constraint-based modeling, parametric design, and geometric/topological information extraction from B-rep models can automate and improve the efficiency, quality, and cost-effectiveness of the die casting die design process.
4. Research Methodology
Research Design:
The research adopts an approach that combines:
(1) Feature-based and constraint-based modelling.
(2) Parametric design.
(3) Geometric and topological information extraction technique from a Boundary Representation (B-rep) model.
Data Collection Method:
The paper does not explicitly detail specific data collection methods in the traditional sense of empirical data gathering. However, the development and validation of the prototype system implicitly involve data related to system performance, user interaction, and design outcomes, although these are not presented as formal datasets within the paper. The case study of a push-button housing serves as a form of demonstrative data, showcasing the system's capabilities.
Analysis Method:
The paper focuses on the development and functional demonstration of the die design system. The analysis is primarily qualitative, assessing the system's ability to integrate design stages, facilitate design editing, and automate die design tasks. The case study provides a practical example of the system's application and workflow. Quantitative performance metrics, such as time savings or design quality improvements, are not explicitly measured or analyzed in this paper.
Research Subjects and Scope:
The research focuses on the development of a prototype die design system applicable to general die casting die design. The system's scope encompasses the design of dies with cavity inserts, core slides, die bases, gating systems, ejector systems, and standard components. The system is implemented using Visual C++ on the SolidWorks 2001 platform. The case study demonstrates the system's application to a push-button housing die design.
5. Main Research Results:
Key Research Results:
- A prototype computer-aided die design system for die casting, comprising seven distinct modules, was developed.
- The system integrates various stages of the die design process, from cast design to ejector system design, within a single environment.
- The system incorporates feature-based and constraint-based modeling, parametric design, and B-rep model information extraction.
- The system includes user-defined die casting feature libraries for components like slides, gating elements, and ejector pins.
- Algorithms for tasks such as "hole patching" for parting surface creation were implemented using geometric and topological information.
- The system architecture is modular, allowing for project management, cavity insert building, die base design, gating system construction, ejector system construction, core slide design, and standard component integration.
- A case study demonstrated the system's capability to design a 2-cavity die for a push-button housing, including cavity inserts, core slides, gating and runner system, die base, and ejector system.
Data Interpretation:
The developed prototype system demonstrates the feasibility of integrating various die casting die design stages into a cohesive CAD environment. The feature-based and constraint-based approach, combined with parametric design, enables efficient and flexible die design and modification. The modular architecture and user-defined feature libraries enhance the system's usability and adaptability to different die design requirements. The case study illustrates the system's practical application in designing a complex die casting die.
Figure Name List:
- Fig. 1 Flowchart of the die design system for die casting
- Fig. 2 Example of a topological constraint—top face of leader pin align with top face of top plate
- Fig. 3a-e Graphical illustration: "hole patching" algorithm
- Fig. 4 System architecture and menu options
- Fig. 5 Project manager module and the new project interface
- Fig. 6a,b Cavity insert builder module. a Bolster builder interface. b Bolster breaker interface
- Fig. 7a,b Gating system designer module. a Gates interface. b Overflows interface
- Fig. 8a,b Die base designer module. a Load N configure interface. b Thickness interface
- Fig. 9 a Slide core designer module: head design interface. b Standard component interface
- Fig. 10 Push-button housing
- Fig. 11a-c Cavity insert builder: a Parting face generator interface. b Cover cavity insert. c Ejector cavity insert
- Fig. 12 a Undercut feature. b Core slide head
- Fig. 13a,b Core slide designer: a Body design interface. b Cavity inserts with core slides mechanism
- Fig. 14 2-cavity layout with 500 mm distance between cavity inserts
- Fig. 15 a Gating system-biscuit; gate; runner; overflow. b Enlarged view of cavity insert
- Fig. 16 DME Die base D series
- Fig. 17 a Typical ejector pin. b Reinforced ejector pin
- Fig. 18 a Ejector system constructor interface. b Cavity insert with the 10 ejector pins of two different types
- Fig. 19 Die design for die casting of the push button casing using the proposed system
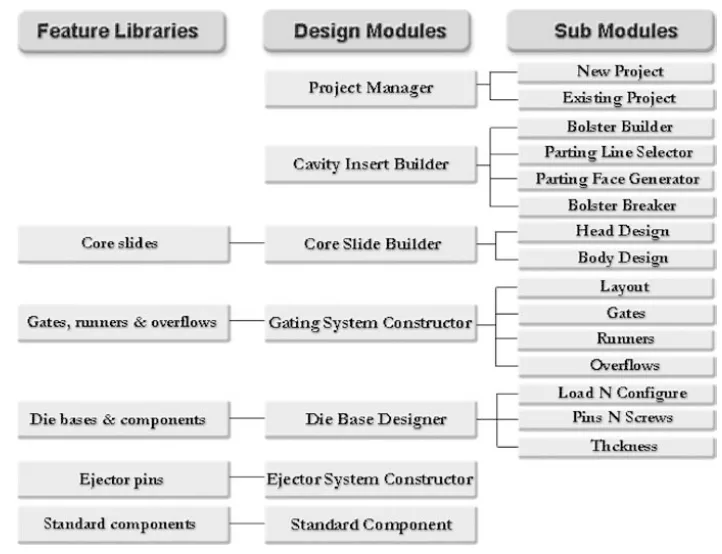

6. Conclusion:
Summary of Main Results:
This research successfully developed a prototype computer-aided die design system for die casting. The system integrates feature-based and constraint-based modeling, parametric design, and B-rep model information to automate and streamline the die design process. It encompasses modules for all critical stages of die design, from initial project setup to ejector system design, and includes customizable feature libraries. A case study demonstrated the system's practical application in designing a complex die casting die.
Academic Significance of the Research:
This research contributes to the field of computer-aided die design by presenting a comprehensive system that integrates multiple design stages and leverages advanced CAD techniques. The application of feature-based and constraint-based modeling, along with geometric and topological information extraction, provides a robust framework for automating complex die design tasks. The modular architecture and customizable feature libraries offer a flexible and adaptable platform for die casting die design.
Practical Implications:
The developed die design system has significant practical implications for the die casting industry. By integrating design stages and facilitating design modifications, the system has the potential to substantially reduce die design lead times, improve design quality, and lower design costs. The user-friendly interface and modular design make the system accessible to both experienced and novice die designers, enhancing productivity and efficiency in die design workflows.
Limitations of the Research
The feature libraries included in the prototype system are not exhaustive, requiring further expansion to cover a broader range of die casting components and design scenarios. Furthermore, the current system does not incorporate a cooling system design module, which is a critical aspect of die casting die design. The system's performance was demonstrated through a single case study, and further validation with diverse and complex die designs is needed to fully assess its robustness and general applicability. Quantitative metrics for design time reduction and quality improvement were not formally evaluated.
7. Future Follow-up Research:
- Directions for Follow-up Research
Future research directions include:- Expanding the feature libraries to encompass a wider range of die casting components and design variations.
- Developing and integrating a cooling system design module into the system.
- Enhancing the system with computational capabilities for cavity filling time analysis, venting analysis, and gating system optimization.
- Conducting comprehensive performance evaluations using diverse and complex die designs to quantify design time reduction, quality improvements, and system robustness.
- Areas Requiring Further Exploration
Further exploration is needed in areas such as:- Integration of CAE analysis tools for process simulation and design optimization within the system.
- Development of more advanced algorithms for automated parting line and parting surface generation, particularly for complex geometries.
- Incorporation of knowledge-based engineering principles and design rules to further automate and optimize the die design process.
- Development of user interface enhancements and customization options to improve user experience and system adaptability.
8. References:
- [1] Wu SH, Lee KS, Fuh JY (2002) Feature-based parametric design of a gating system for a die-casting die. Int J Adv Manuf Technol 19:821-829
- [2] http://www.diedifice.com
- [3] Choi JC, Kwon TH, Park JH, Kim JH, Kim CH (2002) A study on development of a die design system for die-casting. Int J Adv Manuf Technol 20:1-8
- [4] Zhang WS, Xiong SM, Liu BC (1997) Study on a CAD/CAE system of die casting. J Mater Process Tech 63:707-711
- [5] Lee KS, Fuh JYH, Zhang YF, Nee AYC, Li Z (1997) IMOLD: An intelligent plastic injection mold design and assembly system. In: Proceedings of the 4th international conference on die and mold technology, 4-16 June 1997, Kuala Lumpur, Malaysia, pp 30-37
- [6] Shimizu S, Numao M (1997) Constraint-based design for 3D shapes. Artif Intell 91:51-69
- [7] Roller D (1991) An approach to computer-aided parametric design. Comput Aided Des 23(5):385-391
- [8] Anderl R (1994) Parametrics for product modelling. J. Hoschek and Teubner, Stuttgart
- [9] Herman EA (1996) Gating die casting dies. North American Die Casting Association
- [10] Chen YM, Wei CL (1997) Computer-aided feature-based design for net shape manufacturing. Comput Integr Manuf Syst 10(2):147-164
- [11] Hoffmann CM, Joan-Arinyo R (1998) On user-defined features. Comput Aided Des 30(5):321-332
9. Copyright:
- This material is "Y. K. Woon K. S. Lee"'s paper: Based on "Development of a die design system for die casting".
- Paper Source: DOI 10.1007/s00170-003-1754-3
This material was summarized based on the above paper, and unauthorized use for commercial purposes is prohibited.
Copyright © 2025 CASTMAN. All rights reserved.