The content of this introduction paper is based on the article 'DESIGN FOR MANUFACTURABILITY OF A HIGH-PERFORMANCE INDUCTION MOTOR ROTOR' published by 'Massachusetts Institute of Technology'.
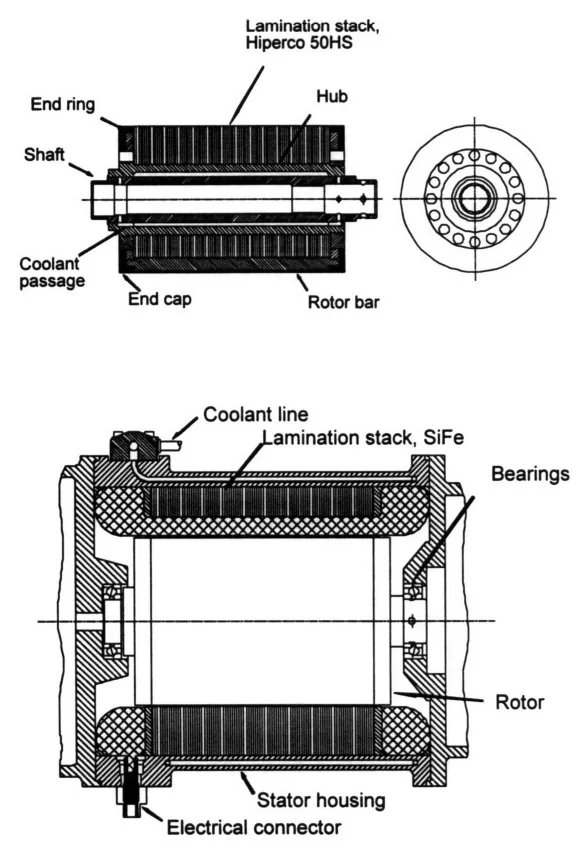
1. Overview:
- Title: DESIGN FOR MANUFACTURABILITY OF A HIGH-PERFORMANCE INDUCTION MOTOR ROTOR
- Author: Christopher P. Brown
- Year of publication: 1996
- Journal/academic society of publication: Submitted to the Department of Mechanical Engineering, Massachusetts Institute of Technology, in partial fulfillment of the requirements for the degree of Master of Science.
- Keywords: Induction Motor, Rotor, Design for Manufacturability, Diffusion Bonding, High-Performance, Manufacturing Process, Investment Casting, Squirrel Cage, Aermet 100, Chromium Copper.
2. Abstract:
A study is conducted on the state-of-the-art manufacturing practices of conventional industrial and research-and-development (R&D) firms manufacturing electric induction motors. It is found that current industrial processes cannot produce high-performance motors, and that current R&D processes are too costly. A new manufacturing process for fabricating the rotors of squirrel cage induction motors is developed. The new process addresses the issues raised by the study by delivering high performance at a reduced cost.
The induction rotor manufacturing process presented involves using net shape processes to manufacture the parts which are manually assembled and subsequently joined. A squirrel cage of extruded chromium copper bars and end rings is used. Investment casting is used to fabricate a core of high-strength Aermet. It is shown that it is necessary to open the slots of the magnetic core of the motor in order to make effective use of investment casting and to ease assembly. The effect on motor performance of changing materials and opening slots is analyzed. The squirrel cage, impellers and shaft can be manually assembled to the core. The assembly is then joined using a diffusion bonding process. The feasibility of a Cr-Cu/Aermet diffusion bond is experimentally verified.
A systematic method of designing and optimizing a manufacturing process is presented. It is based on the experience of designing the process for the rotor.
3. Summary of the Study:
Background of the Research Topic:
High-speed, high-power-density electric machines offer significant performance benefits in various applications, including turbomachinery, machining, HVAC systems, and electric vehicles. These machines reduce size and weight while increasing efficiency. Recent advances in power electronics have enabled better motor control and adjustable-speed drives, further enhancing the need for optimized motor designs.
Status of Previous Research:
Conventional industrial manufacturing practices for induction motor rotors are limited in terms of strength, electrical performance, and dimensional accuracy. Materials like silicon iron and aluminum are commonly used, but they limit the speed and power density achievable. Research and development efforts (e.g., at SatCon Technology Corporation) have explored higher-performance materials like Aermet 100 and Glidcop, but these are currently formed using costly machining processes.
Purpose of the Study:
The purpose of this study is to develop a cost-effective manufacturing process for high-performance induction motor rotors, addressing the limitations of current industrial and R&D practices. The study aims to optimize the process in terms of part quality (materials properties and geometry) and cost.
Core Study:
The core of the study is to develop a new manufacturing process.
The study focuses on the rotor assembly of a high-power-density induction motor. It investigates alternative materials and manufacturing processes to improve performance and reduce cost compared to conventional methods and existing prototype designs. A key aspect is the exploration of net-shape manufacturing techniques and diffusion bonding for assembly.
4. Research Methodology
Research Design:
The research employs a combination of analytical modeling, experimental verification, and cost analysis. It follows a systematic approach to manufacturing process design, including functional decomposition, materials and process selection, and cost estimation.
Data Collection and Analysis Methods:
- Analytical Modeling: A Matlab code (developed by SatCon) is used to model the electromagnetic performance of the induction motor and evaluate the impact of design changes (e.g., opening the rotor slots). Finite Element Analysis (FEA) using ANSYS is used to analyze mechanical and thermal stresses.
- Experimental Verification: Diffusion bonding experiments are conducted to verify the feasibility of joining chromium-copper and Aermet 100.
- Cost Analysis: Vendor quotations and machining time calculations are used to estimate the cost of the proposed manufacturing process and compare it to existing methods.
Research Topics and Scope:
The research focuses on the manufacturing process for the rotor assembly, specifically addressing:
- Magnetic Core: Material selection (Aermet 100), net-shape fabrication (investment casting), and the impact of open slots on performance.
- Squirrel Cage: Material selection (chromium-copper), fabrication (extrusion), and assembly (diffusion bonding).
- Shaft and Impellers: Material selection (410 stainless steel) and fabrication (casting for impellers, bar stock for shaft).
- Rotor Assembly: Diffusion bonding process parameters and feasibility.
- Cost Estimation: Comparison of the proposed process with conventional and prototype manufacturing methods.
5. Key Results:
Key Results:
- A new manufacturing process for high-performance induction motor rotors is developed, utilizing investment casting for the Aermet 100 core, extrusion for the chromium-copper squirrel cage, and diffusion bonding for assembly.
- Opening the slots in the magnetic core is necessary for effective investment casting and has a minimal negative impact on motor performance.
- Diffusion bonding is a feasible method for joining the chromium-copper squirrel cage to the Aermet 100 core, providing sufficient strength and electrical conductivity.
- The proposed process offers a significant cost reduction compared to existing prototype manufacturing methods (from approximately $10,000 to $275 per rotor).
- A systematic method for manufacturing process design is presented.
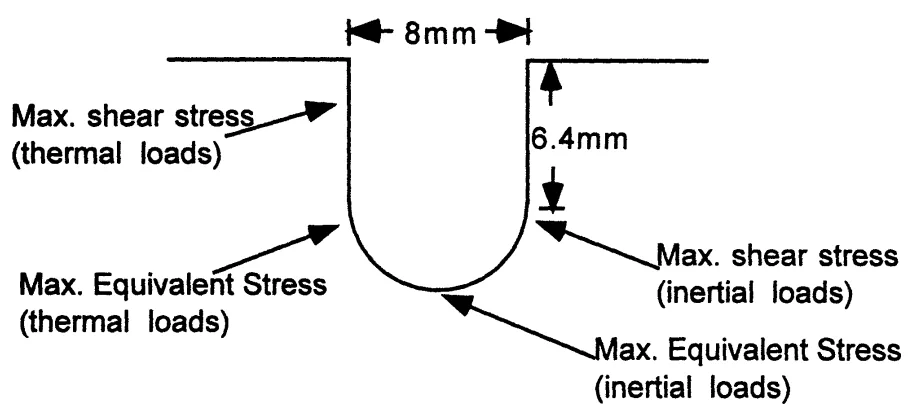
shown
![Figure 3.17. Schematic of the diffusion bonding process [20]](https://castman.co.kr/wp-content/uploads/image-1739-png.webp)
Figure Name List:
- Figure 1.1 - The SatCon traction motor built for the Chrysler Corporation
- Figure 1.2 - Schematic of a typical induction motor assembly
- Figure 1.3 - The magnetic field of a number of current-turns around a ferromagnetic material
- Figure 1.4 - Conceptual picture of the stator illustrating the three phases a, b, and c
- Figure 1.5 - Illustration of how the three phases create a radially oriented rotating magnetic field
- Figure 1.6 - Induction rotor schematic showing the electromagnetic interaction of one slot
- Figure 2.1 - Conventional rotor production sequence
- Figure 2.2 - Typical fully assembled rotor
- Figure 2.3 - Progressive die sequence
- Figure 2.4 - Impeller for an air-cooled motor
- Figure 2.5 - Barsky pump for a water-cooled motor
- Figure 3.1 - Final new production sequence for the high-performance induction rotor
- Figure 3.2 - Exploded view of the rotor assembly
- Figure 3.3 - Starter/Generator motor magnetic core
- Figure 3.4 - Traction motor magnetic core with integrally machined shaft
- Figure 3.5 - Cross section of the original core contrasted with that of an open slot core
- Figure 3.6 - Typical wall dimensions of a closed slot core (starter/generator geometry)
- Figure 3.7 - An illustration of the concept of leakage flux in an electric machine
- Figure 3.8 - Slot model geometry
- Figure 3.9 - Flux concentration due to open slots
- Figure 3.10 - Tooth flux density vs. Slot width for open slots
- Figure 3.11 - Efficiency vs. Slot width for open slots
- Figure 3.12 - Power factor vs. Slot width for open slots
- Figure 3.13 - Integral shaft/core using representative dimensions from the starter/generator
- Figure 3.14 - Canned rotor assembly
- Figure 3.15 - Partial assembly showing bars and end rings assembled to the core
- Figure 3.16 - Slot shape used in the FEA with maximum stress locations shown
- Figure 3.17 - Schematic of the diffusion bonding process
- Figure 3.18 - Diffusion bonding using a fusible interlayer in the Cr-Cu/Aermet system
6. Conclusion:
Summary of Key Results:
The study successfully develops a new, cost-effective manufacturing process for high-performance induction motor rotors. The key innovations include the use of investment casting for the Aermet 100 core, extrusion for the chromium-copper squirrel cage, and diffusion bonding for assembly. Opening the rotor slots is crucial for the casting process and has a manageable impact on performance. The new process significantly reduces manufacturing costs compared to previous methods.
Limitations of the Study
- The diffusion bonding process parameters are not fully optimized.
- The heat treatment of Aermet 100 is optimized for fracture toughness, not magnetic properties.
7. Future Follow-up Research:
Directions for Follow-up Research:
- Optimize the diffusion bonding process parameters (temperature, pressure, time, interlayer thickness) to achieve the strongest and most reliable bond.
- Investigate alternative interlayer materials for diffusion bonding.
Areas for Further Exploration:
- Investigate and optimize the heat treatment of Aermet 100 to improve its magnetic permeability and saturation induction.
- Explore the application of the developed manufacturing process to other types of electric machines.
- Conduct a more detailed analysis of the long-term reliability and performance of the diffusion-bonded rotor assembly.
8. References:
- [1] Pasquarella, G., & Reichert, K. (1990). Development of Solid Rotors for a High-Speed Induction Machine with Magnetic Bearings. Technical Report. Zurich: Swiss Federal Institute of Technology.
- [2] SatCon Technology Corporation. (1995). Annual Report. Cambridge, Mass: SatCon Technology Corporation.
- [3] Baldor Motors and Drives. (1994). Stock Product Catalog 501. Fort Smith, AR: Baldor Electric Co.
- [4] O'Handley, R.C. (1996). Unpublished Lecture Notes: Magnetic Materials. Massachusetts Institute of Technology, Cambridge.
- [5] Slemon, G.R., and Straughen, A. (1980). Electric Machines. Reading, Mass: Addison-Wesley.
- [6] Kirtley, J.L. (1995). Unpublished Lecture Notes: Mathematically Assisted Design of Electric Machines. Massachusetts Institute of Technology, Cambridge.
- [7] Kirtley, J.L. (1994). MatLab script: Polyphase Motor Design Program MOTOR. Massachusetts Institute of Technology, Cambridge.
- [8] Metals Handbook (1990). Metals Park, OH: American Society for Metals.
- [9] Arnon Data Sheet (1995). [Arnold Engineering Company]: Marengo, IL. Arnold Engineering Company.
- [10] Stock Product Catalog 501 (1994). [Baldor Motors and Drives]: Fort Smith, AR. Baldor Electric Co.
- [11] ASM Handbook, Vol. 14: Forming and Forging (1995). Materials Park, OH: ASM International.
- [12] Tempel Steel Services Division (1993). [Tempel Motor Laminations]: Niles, IL Tempel Steel Company.
- [13] ASM Handbook, Vol. 2: Non-ferrous Materials: Properties and Materials Selection Guide. (1995). Materials Park, OH: ASM International.
- [14] Avallone, E. A. (ed.) (1987). Mark's Standard Handbook for Mechanical Engineers, 9th ed. New York: McGraw-Hill.
- [15] Machinery's Handbook. (1994). New York: Industrial Press.
- [16] Alloy Data Sheet: Hiperco 50 HS (1995). [Carpenter Steel Division]: Reading, PA. Carpenter Technology Corporation.
- [17] Alloy Data Sheet: Aermet 100 (1995). [Carpenter Steel Division]: Reading, PA Carpenter Technology Corporation.
- [18] Kalpakjian, Serope. (1995). Manufacturing Engineering and Technology. Reading, MA: Addison-Wesley.
- [19] Glidcop: Copper Dispersion Strengthened with Aluminum Oxide (1994). [SCM Metal Products]: Research Triangle Park, NC. SCM Metal Products.
- [20] Cronin, J.J. (1976). Selecting High Conductivity Copper Alloys for Elevated Temperature Use. Metals Engineering Ouarterlv. Aug. pp 1-14.
- [21] Roark, R.J. (1989). Roark's Formulas for Stress and Strain. (6th ed.). New York: McGraw-Hill.
- [22] Alloy Data Sheet: Hiperco 50 HS (1995). [Carpenter Steel Division]: Reading, PA, Carpenter Technology Corporation.
- [23] Pasquarella, G., & Reichert, K. (1990). Development of Solid Rotors for a High-Speed Induction Machine with Magnetic Bearings. Technical Report. Zurich: Swiss Federal Institute of Technology.
- [24] Kirtley, J.L. (1994). MatLab script: Polyphase Motor Design Program MOTOR. Massachusetts Institute of Technology, Cambridge.
- [25] Sawhney, A.K. (1992). A Course in Electrical Machine Design. Delhi: Dhanpat Rai and Sons.
- [26] Kirtley, J.L. (1995). Unpublished Lecture Notes: Mathematically Assisted Design of Electric Machines. Massachusetts Institute of Technology, Cambridge.
- [27] Kalpakjian, Serope. (1995). Manufacturing Engineering and Technology. Reading, MA: Addison-Wesley.
- [28] Novotny, P. & Maguire, M. Navy Fighter Demands Evolve into Tough Castings. Foundry Management and Technology, Dec. pp.33- 36.
- [29] O'Handley, R.C. (1996). Unpublished Lecture Notes: Magnetic Materials. Massachusetts Institute of Technology, Cambridge.
- [30] Keystone Powder Metal Parts & Self-Lube Bearings (1994). [Keystone Carbon Company]: St. Marys, PA. Keystone Carbon Company.
- [31] Brazing Handbook, 4th ed. (1991). Miami: American Welding Society.
- [32] ASM Handbook, Vol. 2: Non-ferrous Materials: Properties and Materials Selection Guide. (1995). Materials Park, OH: ASM International.
- [33] Chakrabarti, D.J., & Laughlin, D.E. (1984). The Cr-Cu (Chromium-Copper) System. Bulletin of Alloy Phase Diagrams, Vol. 5, No. 1 pp. 59-67.
- [34] Glidcop: Copper Dispersion Strengthened with Aluminum Oxide (1994). [SCM Metal Products]: Research Triangle Park, NC. SCM Metal Products.
- [35] Lessman, G.G. & Bryant, W.A. (1972). Complex Rotor Fabrication by Hot Isostatic Pressure Welding. Research Supplement, Welding Journal, 51 (12). p. 606-s.
- [36] The Torrington Company Service Catalog (1988). [Torrington Company]: Torrington, CT. Ingersoll-Rand.
- [37] Schwartz, M. (1967). Modem Metal Joining Techniques. New York: Wiley-Interscience. pp. 370-470.
- [38] Swanson Analysis Company. (1995). ANSYS Ver. 5.2. Milford, OH: Swanson Analysis Company.
- [39] Welding Handbook, 8th ed. (1987). Miami: American Welding Society.
- [40] Ishida, Yoichi (ed.). (1987). Fundamentals of Diffusion Bonding. Amsterdam: Elsevier. pp. 71-88.
- [41] Alloy Data Sheet: Aermet 100 (1995). [Carpenter Steel Division]: Reading, PA. Carpenter Technology Corporation.
- [42] Kazakov, N.F.(ed.). (1985). Diffusion Bonding of Materials. Oxford: Pergamon Press, pp. 10-70, 162-166, 201-210.
- [43] Machining Data Handbook 3d ed. (1980). Cincinnati: Machinability Data Center.
- [44] Lessman, G.G. & Bryant, W.A. (1972). Complex Rotor Fabrication by Hot Isostatic Pressure Welding. Research Supplement, Welding Journal. 51 (12). 606-s.
- [45] Bralla, J.G. (ed.). (1986). Handbook of Product Design for Manufacturing-A Practical Guide for Low-Cost Production. New York: McGraw-Hi'l.
- [46] Boothroyd, G., P. Dewhurst, & W. Knight. (1994). Product Design for Manufacture and Assembly. New York: Marcel Dekker.
- [47] Kalpakjian, Serope. (1995). Manufacturing Engineering and Technology. Reading, MA: Addison-Wesley.
- [48] Tempel Motor Laminations (1993). [Tempel Steel Services Division]: Niles, IL. Tempel Steel Company.
- [49] Slemon, G.R., and Straughen, A. (1980). Electric Machines. Reading, Mass: Addison-Wesley.
- [50] Novotny, P. & Maguire, M. Navy Fighter Demands Evolve into Tough Castings. Foundry Management and Technology, Dec. pp.33-36.
9. Copyright:
- This material is a paper by "Christopher P. Brown". Based on "DESIGN FOR MANUFACTURABILITY OF A HIGH-PERFORMANCE INDUCTION MOTOR ROTOR".
- Source of the paper: [No DOI URL was provided in the document.]
This material is summarized based on the above paper, and unauthorized use for commercial purposes is prohibited.
Copyright © 2025 CASTMAN. All rights reserved.