This article introduces the paper ['Design, Development and Analysis Wheel Rim by using Composite Material'] published by ['International Journal For Research in Applied Science & Engineering Technology (IJRASET)'].
1. Overview:
- Title: Design, Development and Analysis Wheel Rim by using Composite Material
- Author: Sayyed Fayaz Sayyed Musheer¹, Dr V.V. Mane²
- Publication Year: August 2022
- Publishing Journal/Academic Society: International Journal For Research in Applied Science & Engineering Technology (IJRASET)
- Keywords: (Not specified in the paper)
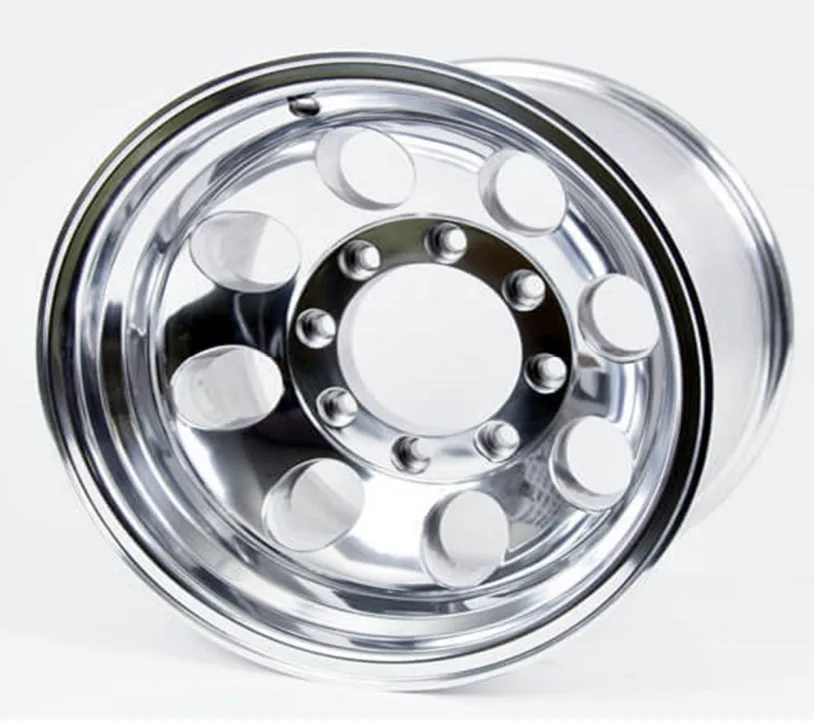
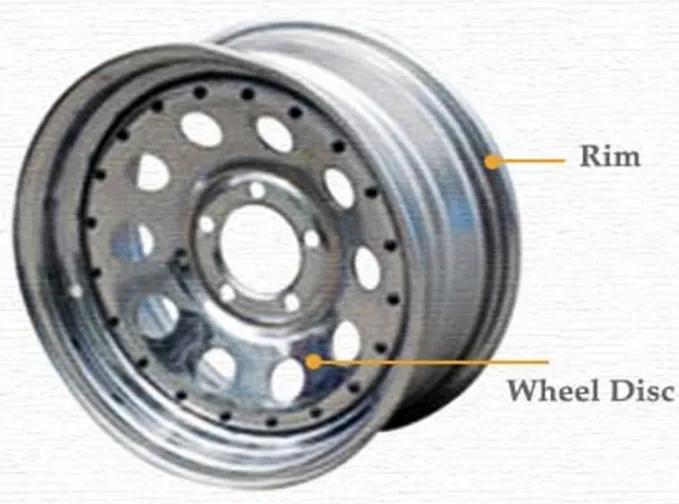
2. Abstracts or Introduction
The paper commences with an overview of the historical evolution of wheels, tracing back to rudimentary wooden forms and highlighting their fundamental role as one of the six basic machines. It elucidates the operational principles of wheels in diverse orientations—horizontal and vertical—for applications ranging from load transportation to material shaping and directional control in vehicles. Furthermore, it mentions the function of a wheel in energy transmission, exemplified by the flywheel. The introduction sets the stage for discussing modern wheel rim design and material considerations.
3. Research Background:
Background of the Research Topic:
The backdrop to this research is rooted in the ongoing development of wheel technology, progressing from early wooden wheels to more sophisticated designs incorporating various materials. The paper highlights the evolution of alloy wheels, noting the emergence of Wire Spoke Wheels, Steel Disc Wheels, and Light Alloy Wheels. Light Alloy Wheels, utilizing materials like aluminum and magnesium, gained prominence due to their advantageous properties. The paper points out the increasing adoption of Light Alloy Wheels, becoming standard in European vehicles by the 1960s and for replacement tires in the United States in the 1970s.
Status of Existing Research:
Existing research, as implicitly indicated in the paper, encompasses the exploration of diverse materials for wheel rim construction, including Aluminium Alloy, Magnesium Alloy, Titanium Alloy, and Composite Material Wheel. Each material presents a unique set of characteristics influencing wheel performance. Aluminium alloys are recognized for their "phenomenal daintiness, warm conductivity, and rust encounter," alongside favorable "physical characteristics of throwing, low warmth, machine handling and reutilizing." Magnesium alloys are noted for being lighter than aluminum, albeit with utilization primarily in racing applications. Titanium alloys offer superior "erosion resistance and quality" but are challenged by "machine handling, designing and more cost." Composite materials are presented as an alternative for weight reduction, though facing challenges in "consistency against warm and for best quality."
Necessity of the Research:
The research is implicitly necessitated by the continuous demand for enhanced vehicle performance, fuel efficiency, and safety. The exploration of advanced materials like light alloys and composites for wheel rims addresses the critical need to reduce unsprung weight, thereby improving "handling acceleration and breaking." Furthermore, the paper underscores the economic imperative to optimize the wheel design process, advocating for Finite Element Analysis (FEA) to "reduce the time spent during the development and testing phase of a new wheel" and to minimize "costly alteration to tooling and equipment in real production."
4. Research Purpose and Research Questions:
Research Purpose:
The primary research purpose is to analyze and compare the structural performance of wheel rims constructed from different materials, specifically Aluminium Alloy, Magnesium Alloy, Titanium Alloy, and Forged Steel Alloy, under static loading conditions. This analysis aims to evaluate the suitability of these materials for wheel rim applications based on key mechanical characteristics.
Key Research:
The key research focuses on employing Finite Element Analysis (FEA) to simulate and assess the structural behavior of wheel rims made from the aforementioned materials. The analysis investigates "Total Deformation", "Maximum Shear Stress", and "Equivalent Stress" as critical performance indicators. The study also considers different wheel rim designs, including "simple rim design", "centrifugal rim", and "pentagonal rim", although the material comparison appears to be the central focus.
Research Hypotheses:
(Not specified in the paper)
5. Research Methodology
Research Design:
The research employs a simulation-based approach utilizing Finite Element Analysis (FEA). The study involves designing a wheel rim model in CATIA V5 and subsequently importing it into ANSYS 15.0 for static structural analysis. Different material assignments (Aluminium Alloy, Magnesium Alloy, Titanium Alloy, Forged Steel Alloy) are applied to the wheel rim model to facilitate comparative performance evaluation.
Data Collection Method:
Data is collected through FEA simulations conducted in ANSYS 15.0. The software is used to compute and generate numerical results for "Total Deformation", "Maximum Shear Stress", and "Equivalent Stress" for each material under defined loading and boundary conditions.
Analysis Method:
The analysis method is based on static structural analysis within the ANSYS workbench. The "imported file geometry undergoes meshing after which boundary conditions are applied to the physical domain." The fine mesh is utilized for enhanced accuracy. The analysis focuses on comparing the simulation results across the four different materials to discern their relative structural performance in wheel rim applications.
Research Subjects and Scope:
The research subjects are passenger car wheel rims virtually modeled and analyzed. The scope encompasses the structural analysis of wheel rims made from Aluminium Alloy, Magnesium Alloy, Titanium Alloy, and Forged Steel Alloy. The analysis is limited to static loading conditions, simulating a stationary vehicle with a load of 5200N applied to the wheel rim. The "rim from 60 series 195/60 R 14" is used as the basis for the wheel rim model.
6. Main Research Results:
Key Research Results:
The key research results are derived from the FEA simulations and are presented in the form of numerical values and visual representations of stress and deformation distributions. For "Basic Design" wheel rims, the maximum "Total Deformation" observed was 3.6018 mm for Aluminium Alloy and the minimum was 2.3256 mm for Titanium Alloy. The maximum "Equivalent Stress" was 18.207 MPa for Aluminium Alloy and the minimum was 18.077 MPa for Magnesium Alloy. For "Simple Model" wheel rims, the maximum "Total Deformation" was 3.1153 mm for Aluminium Alloy and the minimum was 2.0109 mm for Titanium Alloy. The maximum "Equivalent Stress" was 16.679 MPa for Magnesium Alloy and 16.647 MPa for Titanium Alloy.
Analysis of presented data:
The presented data indicates that Titanium Alloy exhibits the least deformation under static loading conditions in both "Basic Design" and "Simple Model" wheel rims. Magnesium Alloy generally shows higher deformation compared to Titanium Alloy and Forged Steel Alloy. Aluminium Alloy demonstrates deformation values between Magnesium Alloy and the stiffer materials. In terms of stress, the Equivalent Stress values are relatively close across all materials, suggesting that stress distribution is less material-dependent within the analyzed designs. The "Graphical Representation of Static Analysis" (Chart of Properties Row 12) illustrates the relationship between "Alternating Stress" and "Cycles", providing fatigue-related data, although the direct comparison of materials based on this chart is not explicitly elaborated in the paper's result analysis. The "Result and Comparision" section states, "When comparing between alloy materials aluminium alloy has better deformation factors and better strain coefficients But when alloy materials is compared to composite material, composite material has better deformation and stress factors," although composite material analysis is not explicitly presented in the numerical results.
Figure Name List:
- Figure not named (Diagram of Wheel Rim Dimensions) (Page 2)
- Figure not named (Rim and Wheel Disc of Steel Wheel) (Page 4)
- Figure not named (Aluminium Wheel) (Page 4)
- A] Total Deflection (Aluminium Alloy Basic Design) (Page 12)
- B] Maximum shear stress (Aluminium Alloy Basic Design) (Page 12)
- C] Equivalent Stress (Aluminium Alloy Basic Design) (Page 12)
- A] Total Deflection (Magnesium Alloy Basic Design) (Page 12)
- B] Maximum shear stress (Magnesium Alloy Basic Design) (Page 12)
- C] Equivalent Stress (Magnesium Alloy Basic Design) (Page 12)
- A] Total Deflection (Titanium Alloy Basic Design) (Page 13)
- B] Maximum shear stress (Titanium Alloy Basic Design) (Page 13)
- C] Equivalent Stress (Titanium Alloy Basic Design) (Page 13)
- A] Total Deflection (Forged Steel Alloy Basic Design) (Page 14)
- B] Maximum shear stress (Forged Steel Alloy Basic Design) (Page 14)
- C] Equivalent Stress (Forged Steel Alloy Basic Design) (Page 14)
- A] Total Deflection (Aluminium Alloy Simple Model) (Page 14)
- B] Maximum shear stress (Aluminium Alloy Simple Model) (Page 14)
- A] Total Deflection (Magnesium Alloy Simple Model) (Page 15)
- B] Maximum shear stress (Magnesium Alloy Simple Model) (Page 15)
- C] Equivalent Stress (Magnesium Alloy Simple Model) (Page 15)
- A] Total Deflection (Titanium Alloy Simple Model) (Page 16)
- B] Maximum shear stress (Titanium Alloy Simple Model) (Page 16)
- C] Equivalent Stress (Titanium Alloy Simple Model) (Page 17)
- A] Total Deflection (Forged Steel Alloy Simple Model) (Page 17)
- B] Maximum shear stress (Forged Steel Alloy Simple Model) (Page 17)
- C] Equivalent Stress (Forged Steel Alloy Simple Model) (Page 17)
- Modeling of Wheel Rim with J Contour (Page 9)
- Front View of Wheel Rim (Page 9)
- Modeling Of Spoke Design (Page 10)
- Meshing of Wheel Rim (Page 10)
- Chart of Properties Row 12: Alternating Stress R-Ratio (Page 17)
- Figure not named (Table of Alternating Stress vs Cycles) (Page 18)
- Figure not named (Practical Failure Cases Images) (Page 18)
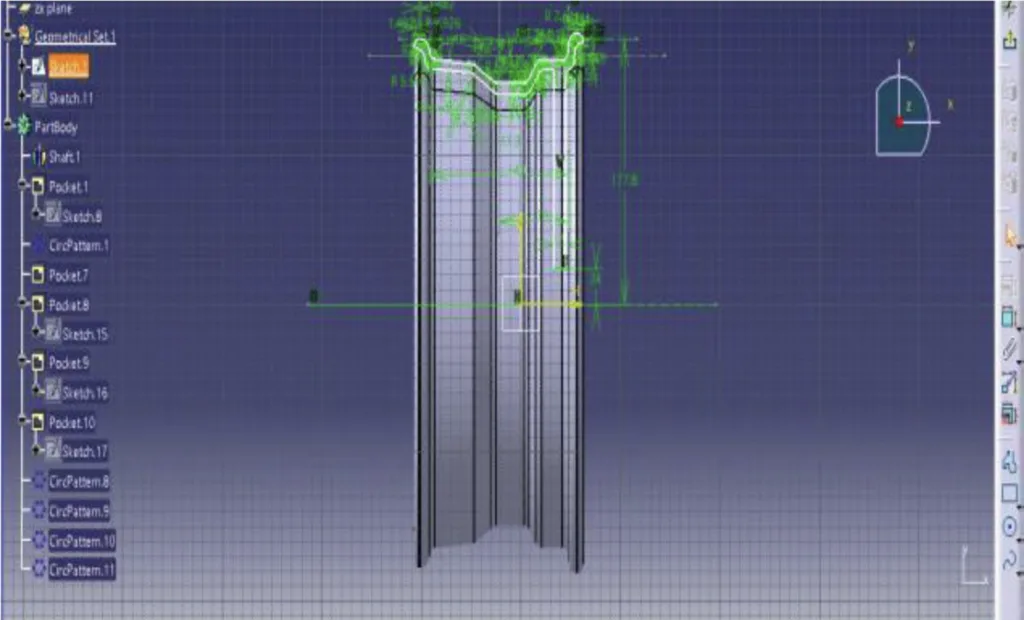
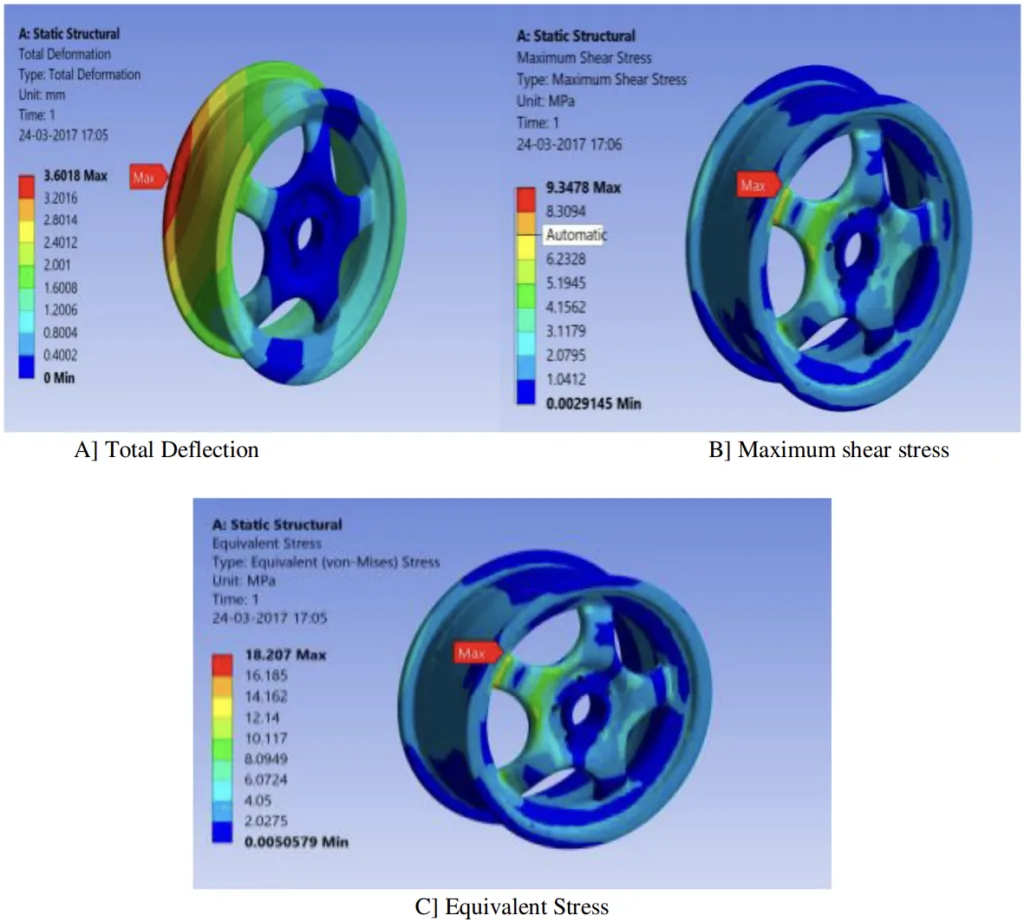
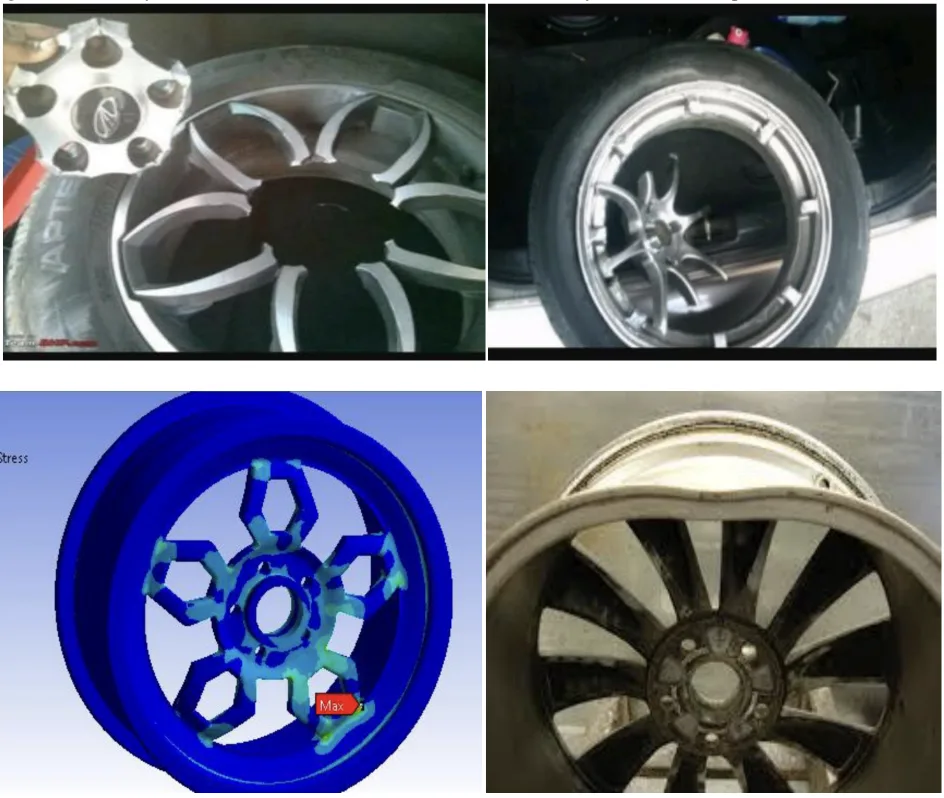
7. Conclusion:
Summary of Key Findings:
The study concludes that all four analyzed wheel rim designs (simple rim, centrifugal rim, pentagonal rim, and basic rim - although centrifugal and pentagonal rims results are not explicitly detailed in the result section) are structurally safe and within standard limits. Among the materials, "steel alloy is the best material followed by aluminium and magnesium occupies last position as it has more deformation for the same loading condition." The analysis suggests that Magnesium Alloy, while lightweight, exhibits higher deformation, potentially limiting its use to specialized applications like racing. Aluminium Alloy demonstrates a longer fatigue life than steel alloy. The inside bead seat is identified as the area of greatest deflection and potential air pressure loss. "Actually failure of alloy wheel occurs mostly at the areas where there is max stress values occur (predicted by analysis software)."
Academic Significance of the Study:
This study contributes to the academic understanding of material performance in wheel rim design by providing a comparative FEA-based analysis of different alloys. It offers insights into the structural behavior of wheel rims under static loading, which is fundamental for design optimization and material selection in automotive engineering. The research highlights the trade-offs between material properties like stiffness, weight, and deformation in the context of wheel rim applications.
Practical Implications:
The practical implications of this study are relevant for material selection in wheel rim manufacturing. The findings suggest that Forged Steel Alloy and Titanium Alloy offer superior stiffness and lower deformation, making them suitable for applications demanding high structural integrity. Aluminium Alloy provides a balance of performance and weight, with a better fatigue life than steel, making it a viable option for general vehicle applications. Magnesium Alloy, due to its higher deformation, may be best suited for niche applications where weight is a paramount concern, such as racing vehicles, despite potential limitations in durability and fatigue life for prolonged use.
Limitations of the Study and Areas for Future Research:
(Not specified in the paper)
8. References:
- [1] V.Karthi et, al., "Design and analysis of alloy wheel rim" International Journal of Innovative Research in Science, Engineering and Technology An ISO 3297: 2007 Certified Organization Volume 3, Special Issue 2, April 2014.
- [2] Daniel Antony C et,al., "Design and Analysis of Two Wheeler Alloy Wheel Rim Using Composite Materials". International Journal of Innovative Research in Science, Engineering and Technology (An ISO 3297: 2007 Certified Organization) Vol. 5, Issue 5, May 2016.
- [3] G.Ashokkumar et, al., "Design and analysis of wheel rim by using CATIA & ANSYS". International Research Journal of Engineering and Technology (IRJET) Volume: 03 Issue: 12 Dec-2016 e-ISSN: 2395-0056 p-ISSN: 2395-0072
- [4] Gudise Venkateswarlu et, al., "Design and analysis of alloy wheel with different alloys". International journal of advance research in science and engineering volume no 06 issue no 10, Octomber 2017.
- [5] J Stearns et, al., "performed analysis to understand the pressure and radial loads influence on stress and displacement response of rotating bodies in automobiles". International Journal of Scientific and Research Publications, Volume 8, Issue 11, November 2018 486 ISSN 2250-3153.
- [6] Ravi Lidoriya, SanjayChaudhary and Anil Kumar Mohopatra, "Design and Analysis of Aluminium Alloy Wheel using PEEK Material", International Journal of Mechanical Engineering and Research. ISSN No. 2249-0019, Volume 3, Number 5 (2013), pp. 503-516.
- [7] M. Saran Theja, M. Vamsi Krishna, "Structural and Fatigue Analysis of Two Wheeler Lighter Weight Alloy Wheel", IOSR Journal of Mechanical and Civil Engineering (IOSR-JMCE). e-ISSN: 2278-1684,p-ISSN: 2320-334X, Volume 8, Issue 2 (Jul. - Aug. 2013), PP 35-45.
- [8] V.Karthi, N. Ramanan and J. Justin Maria Hillary, "DESIGN AND ANALYSIS OF ALLOY WHEEL RIM", International Journal of Innovative Research in Science, Engineering and Technology. ISSN (Online): 2319-8753 ISSN (Print): 2347 - 6710 Volume 3, Special Issue 2, April 2014.
9. Copyright:
- This material is "Sayyed Fayaz Sayyed Musheer¹ and Dr V.V. Mane²"'s paper: Based on "Design, Development and Analysis Wheel Rim by using Composite Material".
- Paper Source: https://doi.org/10.22214/ijraset.2022.45886
This material was summarized based on the above paper, and unauthorized use for commercial purposes is prohibited.
Copyright © 2025 CASTMAN. All rights reserved.