This article introduces the paper "Compute-Aided Design of Low Pressure Die-Casting Process of A356 Aluminum Wheels".
1. Overview:
- Title: Compute-Aided Design of Low Pressure Die-Casting Process of A356 Aluminum Wheels
- Authors: Pei-Hsing Huang, Wei-Jen Wu, Chung-Han Shieh
- Publication Year: April 2017
- Journal/Conference: Applied Mechanics and Materials
- Keywords:
- low pressure die-casting
- A356 aluminum
- Anycasting
- shrinkage defect
- mold flow analyses
2. Research Background:
- Social/Academic Context of the Research Topic:
- The automotive industry is vigorously developing lightweight, high-strength, and impact-resistant vehicle designs.
- Low pressure die-casting is widely used for wheel production.
- Defects during die-casting can lead to wheel frame deformation and creep damage, affecting traffic safety.
- Ensuring high-quality die-casting wheel frame products is crucial.
- Limitations of Existing Research:
- Existing research implicitly acknowledges the challenge of defects in low pressure die-casting of aluminum wheels due to complex shapes and high-speed filling.
- Previous studies have used numerical simulation to predict defects and optimize parameters, but further improvement is needed to effectively eliminate defects.
- Necessity of Research:
- To understand the evolution of mold flow, temperature field, and solidification in low pressure die-casting of A356 aluminum wheels.
- To reduce defects occurring in wheel products through optimized casting parameters and designs of flow channels and overflows.
- To predict defect positions and distributions to eliminate shrinkage voids and porosity defects.
3. Research Objectives and Research Questions:
- Research Objective:
- To design and simulate the low pressure die-casting process of A356 aluminum wheels using Anycasting software.
- To predict the formation of defects and improve defect reduction strategies by optimizing process parameters and overflow tank configuration.
- Core Research Question:
- How can compute-aided design and simulation of the low pressure die-casting process, particularly through the use of Anycasting software and overflow tank optimization, effectively reduce shrinkage and porosity defects in A356 aluminum wheels?
- Research Hypothesis:
- Setting up an overflow tank can effectively prevent the formation of shrinkage void and porosity of die-castings and significantly promote the quality and productivity of die-casting wheel products.
4. Research Methodology:
- Research Design:
- Simulation-based study using numerical simulation technique.
- Data Collection Method:
- Simulation data generated by Anycasting software package.
- Analysis Method:
- Anycasting numerical simulation analysis, employing the finite difference method (FDM).
- Retained melt modulus (RMM) analysis to predict defect positions and distribution.
- Simulation of mold flow, temperature field, and solidification processes.
- Analysis of process parameters and configuration design of overflow tank.
- Research Subject and Scope:
- Low pressure die-casting process of A356 aluminum wheels.
- Simulation analysis focused on lift wheel, wheel, and overflow tank with different overflow tank configurations.
- Material: SKD61 die steel for mold and A356 aluminum for wheel casting.
5. Key Research Findings:
- Core Research Findings:
- Setting up an overflow tank effectively prevents the formation of shrinkage void and porosity in A356 aluminum die-castings.
- The use of an overflow tank significantly promotes the quality and productivity of die-casting wheel products.
- Numerical simulation using Anycasting software can effectively predict the formation and distribution of defects in low pressure die-casting.
- Statistical/Qualitative Analysis Results:
- Retained melt modulus (RMM) analysis was used to predict defect probability distribution.
- Simulation results showed that defects were mainly distributed in the bottom of the rim and the wheel center in the initial approach without an overflow tank.
- With the addition of an overflow tank, the independent residual melt, which contributes to defects, could be effectively discharged.
- Data Interpretation:
- The initial approach with a taper opening lift tube (70° taper angle, 706.5mm² water entry sectional area) resulted in defects concentrated at the bottom rim and wheel center due to independent residual melt.
- Adding an overflow tank facilitated the discharge of independent residual melt, redirecting shrinkage and porosity to the overflow tank and away from the wheel body.
- Figure Name List:
- Fig. 1: (a) 3D Model of assembly of wheel and lift tube (b) results after mesh generation of physical model.
- Fig. 2: Diagram of Low Pressure Die-casting Mold Filling.
- Fig. 3: (a) external view & (b) cutaway view of defects probability distribution through retained melt modulus analysis of the initial approach of taper opening lift tube.
- Fig. 4: Solidification Order Diagram of (a) Initial Approach (b) Improvement Approach by Adding of Overflow Tank.
- Fig. 5: (a) External View, (b) Front View & (c) Rear View of Defects Probability Distribution via Retained Melt Modulus analysis of the Improvement Approach by Adding of Overflow Tank.

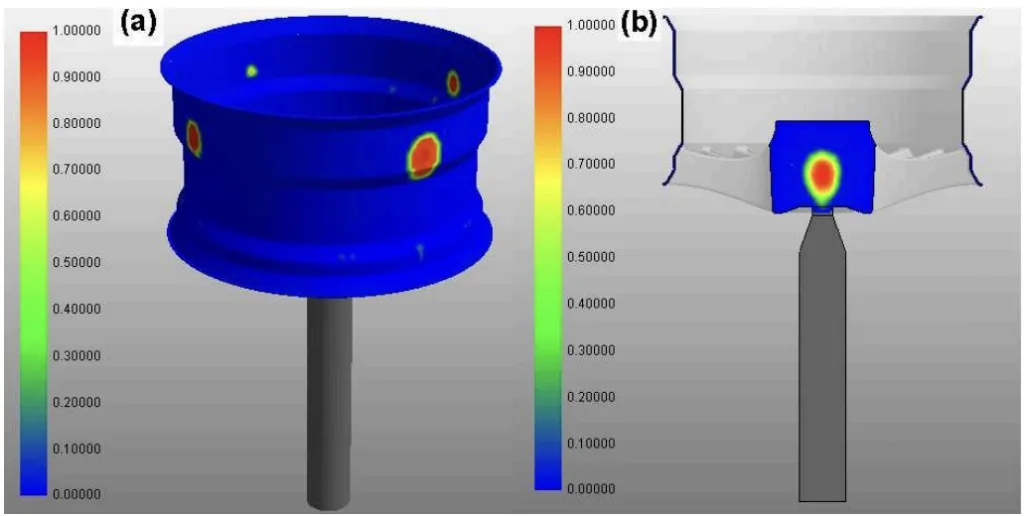


6. Conclusion and Discussion:
- Summary of Main Results:
- The study demonstrated that adding an overflow tank in the low pressure die-casting process of A356 aluminum wheels effectively reduces shrinkage and porosity defects.
- Numerical simulation using Anycasting software and RMM analysis accurately predicted defect formation and distribution.
- The overflow tank design allowed for the venting of gas and the migration of shrinkage and porosity to the overflow tank, eliminating defects in the wheel rim and center.
- Academic Significance:
- The research validates the use of compute-aided design and numerical simulation, specifically Anycasting software and RMM analysis, for optimizing low pressure die-casting processes.
- It provides a detailed understanding of defect formation mechanisms related to independent residual melt and the effectiveness of overflow tanks in mitigating these defects.
- The study contributes to the body of knowledge on die-casting process optimization for lightweight automotive components.
- Practical Implications:
- The findings offer practical guidance for die-casting engineers to improve the quality and productivity of aluminum wheel manufacturing.
- Implementing overflow tank designs, informed by simulation analysis, can lead to a significant reduction in defects, scrap rates, and manufacturing costs.
- The study highlights the importance of considering mold flow, temperature field, and solidification during the design phase of die-casting processes.
- Limitations of Research:
- The paper does not explicitly discuss the limitations of the research.
7. Future Follow-up Research:
- Future Research Directions:
- Further research could explore the optimization of overflow tank designs in terms of size, shape, and placement for various wheel geometries and casting parameters.
- Investigating the influence of different process parameters (e.g., casting temperature, pressure profiles, cooling rates) in conjunction with overflow tank designs could be beneficial.
- Experimental validation of the simulation results through physical die-casting trials would further strengthen the findings.
- Areas for Further Exploration:
- Exploring the application of this methodology to other aluminum alloys and die-casting processes.
- Investigating the use of advanced simulation techniques and material models for even more accurate defect prediction.
- Studying the impact of overflow tank design on the mechanical properties and fatigue life of the die-cast aluminum wheels.
8. References:
[1] P. H. Huang, S. C. Hung, C. J. Lin, Optimal pouring system design for investment casting of cladding thin-plate heater using metallic mold flow analyses, Appl. Mech. Mater. 627 (2014) 46-49 doi:10.4028/www.scientific.net/AMM.627.46
[2] P. H. Huang, B. T. Wang, Y. T. Chen, An effective method for separating casting components from the runner system using vibration-induced fatigue damage, Int. J. Adv. Manuf. Technol. 74(9) (2014) 1275-1282 doi:10.1007/s00170-014-6077-z
[3] J. L. Chen, Automotive aluminum wheels low pressure casting process overview, Theor. Urban Construct. 13 (2014).
[4] Z. J. Wang, Y. Zhao, H. W. Song, X. D. Xu, R. J. You, Numerical Simulation of Low Pressure Casting Large Size Aluminum Alloy Wheel and its Process Optimization, Comput. Appl. Technol. 34(3) (2014) doi:1001-2249(2014)0.-0256-04
[5] P. H. Huang, M. J. Guo, A study on the investment casting of 17-4PH stainless steel helical impeller of centrifugal pump, Mater. Res. Innov. 19(sup9) (2015) 77-81. doi:10.1179/1432891715Z.0000000001924
[6] P. H. Huang, C. J. Lin, Computer-aided modeling and experimental verification of optimal gating system design for investment casting of precision rotor, Int. J. Adv. Manuf. Technol. 79(5) (2015) 997-1006.
[7] J. K. Kuo, P. H. Huang, M. J. Guo, Removal of CrMo alloy steel components from investment casting gating system using vibration-excited fatigue failure, Int. J. Adv. Manuf. Technol. In press (2016) doi:10.1007/s00170-016-9079-1
[8] G. F. Mi, X. Y. Liu, K. F. Wang, J. T. Niu, Numerical simulation of low pressure die-casting aluminum wheel, China Foundry, 48(1) (2009) 48-52.
[9] X. F. Huang, Z. Y. Tian, K. Zhu, X. J. Cao, R. Xie, Study and Application of Die-Casting Aluminum Alloy and Die-Casting Technology, Cast. Forg. Weld. 37(17) (2008) doi:1001-3814(2008)17-0137-05
[10] Y. J. Zhang, Study of Performance of Automobile Wheel of A356 AL-alloy by Low Pressure Casting, Foundry Technol. 35(2) (2014).
9. Copyright:
Copyright: This summary is based on the paper: Compute-Aided Design of Low Pressure Die-Casting Process of A356 Aluminum Wheels.
doi:10.4028/www.scientific.net/AMM.864.173
Unauthorized commercial use is prohibited.
Copyright © 2025 CASTMAN. All rights reserved.