This article introduces the paper ["CO2 Laser Beam Welding of Magnesium-Based Alloys"] published by [Welding Research Supplement].
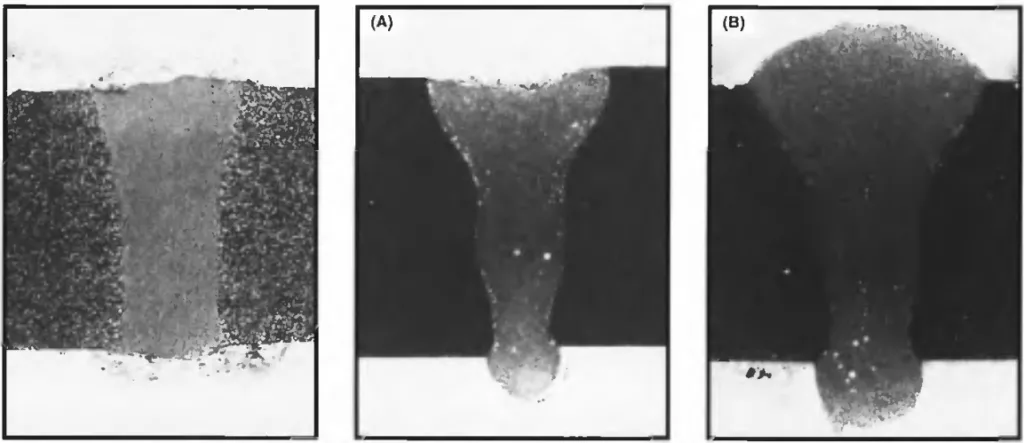
Fig. 2- Cross section of laser welded WE 54 T6, thickness 5 mm (11X); A - without welding wire, 2 kW, 2 m/min; B - with 2.3-mm welding wire, 2 kW, 1.25 m/min.
1. Overview:
- Title: CO2 Laser Beam Welding of Magnesium-Based Alloys
- Author: A. Weisheit, R. Galun and B. L. Mordike
- Publication Year: 1998
- Publishing Journal/Academic Society: Welding Research Supplement
- Keywords: Laser Beam Welding, Magnesium, Magnesium Alloys, Heat-Affected Zone, Fusion Zone, Die Cast Alloys, Age-Hardened Alloys
2. Abstracts or Introduction
This paper investigates the laser weldability of various cast and wrought magnesium alloys using a 2.5-kW CO₂ laser. Butt joints of 2.5-8 mm thick plates were produced with and without filler metal. The study demonstrates the feasibility of laser welding for both similar and dissimilar magnesium alloy joints, highlighting the characteristic small weld size and deep penetration depth achievable with laser beam welding. Crack-free welds with low porosity and good surface finish were obtained through optimized process parameters. The research further examines the influence of laser welding on the hardness of the fusion zone (FZ) and heat-affected zone (HAZ), revealing generally minimal changes or slight increases relative to the base metal, with the exception of cast alloy QE 22. Die cast alloys exhibited high porosity in the weld. The introduction emphasizes the increasing industrial interest in magnesium alloys, particularly in the automotive sector for weight reduction, and the importance of developing efficient welding techniques. Laser welding is presented as a superior alternative to Gas Tungsten Arc Welding (GTAW) due to its enhanced focusing capability, lower heat input, and potential for automated integration. The paper also notes the limited existing research on laser welding of magnesium alloys, citing prior studies on crack formation in WE 54 and successful welding of AZ 91. This study aims to provide a comprehensive overview of CO2 laser welding characteristics for a range of commercial magnesium alloys, considering different heat treatment conditions and focusing on macro- and microstructure analysis and hardness evaluation.
3. Research Background:
Background of the Research Topic:
Magnesium alloys are gaining significant traction as structural materials, especially in the automotive industry, driven by the need for weight reduction to improve fuel efficiency. This necessitates the development of effective joining technologies, with welding being a critical manufacturing process.
Status of Existing Research:
Current industrial welding practices for magnesium alloys primarily involve Gas Tungsten Arc Welding (GTAW), mainly for repair applications. Electron Beam Welding (EBW) is utilized in specific cases. However, GTAW presents disadvantages for age-hardened or extruded magnesium alloys due to its high energy input, leading to a broad heat-affected zone and requiring post-weld heat treatment. Research in laser welding of magnesium alloys is limited, with only a few prior studies. Baeslack, et al. (Ref. 3) reported crack formation during CO₂ laser welding of WE 54, attributed to liquation cracking. Chen, et al. (Refs. 4, 5) successfully welded cast AZ 91 plates using CO₂ laser, achieving pore and crack-free welds with high aspect ratios using Helium shielding gas.
Necessity of the Research:
The limited research and the drawbacks of conventional welding methods highlight the necessity for further investigation into laser welding of magnesium alloys. Specifically, there is a need to explore the weldability of a broader range of commercial magnesium alloys, including both cast and wrought alloys, and to evaluate the influence of different heat treatment conditions on the welding process and resulting weld properties.
4. Research Purpose and Research Questions:
Research Purpose:
The primary purpose of this research is to provide a comprehensive investigation into the similar and dissimilar alloy weldability of various commercial magnesium alloys utilizing a CO2 laser. A key objective is to assess the influence of different heat treatment conditions on the weldability of these alloys. The investigations are focused on macro- and microstructure analysis and hardness characteristics of the resulting welds.
Key Research:
This research focuses on:
- Evaluating the feasibility of CO2 laser welding for joining various cast and wrought magnesium alloys.
- Determining optimal laser welding parameters for achieving high-quality welds in magnesium alloys.
- Analyzing the macrostructure and microstructure of laser welds in magnesium alloys.
- Assessing the hardness distribution within the fusion zone (FZ) and heat-affected zone (HAZ) of laser-welded magnesium alloys.
- Investigating the impact of different heat treatment conditions on the laser weldability of magnesium alloys.
- Examining the weldability of dissimilar magnesium alloy combinations using CO2 laser welding.
Research Hypotheses:
While not explicitly stated as formal hypotheses, the research implicitly investigates the following:
- CO2 laser welding can produce high-quality welds in various magnesium alloys with appropriate parameter control.
- Laser welding will result in refined microstructures within the fusion zone due to rapid solidification.
- Heat treatment conditions will influence the weldability and resulting properties of laser-welded magnesium alloys.
- Dissimilar magnesium alloys can be successfully joined using CO2 laser welding, albeit with potential compositional gradients in the weld.
5. Research Methodology
Research Design:
The research employs an experimental design involving butt joint welding of similar and dissimilar combinations of six cast magnesium alloys (AZ 91, AM 60, ZC 63, ZE 41, QE 22, and WE 54) and four wrought magnesium alloys (AZ 31, AZ 61, ZW 3, and ZC 71). Welding was performed both with and without filler metal to assess its influence.
Data Collection Method:
The following methods were used for data collection:
- Macrostructural Analysis: Visual inspection and macroscopic examination of welds to assess weld quality, including undercut, surface finish, porosity, and crack formation.
- Microstructural Analysis: Light microscopy and scanning electron microscopy (SEM) were employed to characterize the microstructure of the fusion zone (FZ) and heat-affected zone (HAZ).
- Microhardness Measurements: Vickers microhardness testing (HV 0.05) was conducted across the weld cross-sections to evaluate hardness variations in the FZ and HAZ.
- Energy Dispersive X-ray Spectroscopy (EDS): EDS analysis was utilized for dissimilar joints to determine the distribution of alloying elements across the weld interface.
Analysis Method:
The collected data was analyzed using:
- Qualitative Assessment: Weld quality was evaluated based on visual inspection and macrostructural observations, categorized as good (+), average (o), or bad (-).
- Microstructural Interpretation: Micrographs were analyzed to characterize grain size, morphology, solidification structure, and phase distribution in the FZ and HAZ.
- Hardness Profile Analysis: Hardness profiles across the welds were plotted and analyzed to identify softening or hardening effects in the FZ and HAZ.
- Compositional Mapping: EDS data was used to map the distribution of alloying elements in dissimilar welds, revealing mixing characteristics.
Research Subjects and Scope:
The research subjects were plates of six cast magnesium alloys (AZ 91, AM 60, ZC 63, ZE 41, QE 22, WE 54) and four wrought magnesium alloys (AZ 31, AZ 61, ZW 3, ZC 71). Plate thicknesses ranged from 2.5 to 8 mm. The scope of the study was limited to CO2 laser welding using a Trumpf continuous wave CO₂ laser with a maximum output power of 2.5 kW and helium shielding gas.
6. Main Research Results:
Key Research Results:
- Weldability: Most magnesium alloys investigated exhibited good laser weldability in both similar and dissimilar joints. Crack-free welds with low porosity and good surface finish were achievable with optimized parameters.
- Weld Bead Characteristics: Laser welding resulted in small fusion zones and deep penetration depths, characteristic of laser beam processes.
- Shielding Gas: Helium was identified as the optimal shielding gas, providing the best surface quality, weld depth, and aspect ratio.
- Porosity: Sand cast and extruded alloys showed very low porosity. Alloys containing Zn and/or Al exhibited a few large pores. Pressure die-cast alloys (AZ 91, AM 60) showed extremely high porosity due to gas entrapment during die casting.
- Cracking: Except for QE 22 in the age-hardened (T6) condition, all investigated alloys produced crack-free welds. QE 22 (T6) exhibited cracking in the fusion zone parallel to the welding direction.
- Undercut: Full penetration welds without filler metal resulted in weld undercut, more pronounced in thicker plates and dependent on alloy composition (least in Zn-rich alloys, most in AZ alloys).
- Microstructure: A cellular solidification structure was generally observed in the fusion zone, except for WE 54 and AZ-type alloys. Grain refinement occurred in the fusion zone compared to the base metal. AZ 31 wrought alloy showed directed grain growth from the fusion boundary into the HAZ.
- HAZ Microstructure: No grain coarsening was observed in the HAZ of cast alloys. Liquation of grain boundaries adjacent to the fusion boundary was observed in cast alloys (except WE 54). Significant grain coarsening occurred in the HAZ of wrought alloy AZ 31.
- Hardness: In as-cast alloys, a hardness increase was observed in the weld. In wrought alloys, hardness remained unchanged in the weld. In age-hardened alloys (AZ 91, ZC 63, WE 54), hardness was maintained in the weld, but QE 22 (T6) showed a significant hardness decrease in the weld and HAZ.
Analysis of presented data:
- Table 2 and Table 3 summarize the condition, processing parameters, and weld quality of similar and dissimilar joints, respectively, providing a qualitative assessment of weld defects (undercut, surface, porosity, cracks).
- Figure 1 shows a cross-section of a laser-welded ZC 71 joint, illustrating typical weld geometry.
- Figure 2 compares cross-sections of laser-welded WE 54 T6 joints with and without filler wire, demonstrating the effect of filler wire on weld bead shape.
- Figure 3 displays the fusion boundary region of a QE 22 weld, highlighting the fine solidification subgrain structure.
- Figure 4 shows coarse grains in the fusion zone and HAZ of AZ 31F, illustrating directed grain growth.
- Figure 5 depicts liquation of grain boundaries at the fusion boundary in ZC 63 T6, along with a precipitation-free zone.
- Figure 6 presents the element distribution in a dissimilar weld of QE 22 and ZC 63, showing concentration gradients.
- Figure 7 shows the hardness profile across a weld in as-cast ZC 63, illustrating hardness variation across the weld.
- Figure 8 compares hardness profiles in welds of WE 54 T6 and QE 22 as-cast, highlighting different hardness responses.
- Figure 9 compares microstructures in a dissimilar joint of QE 22 and WE 54, showing differences in grain morphology and size.
Figure Name List:
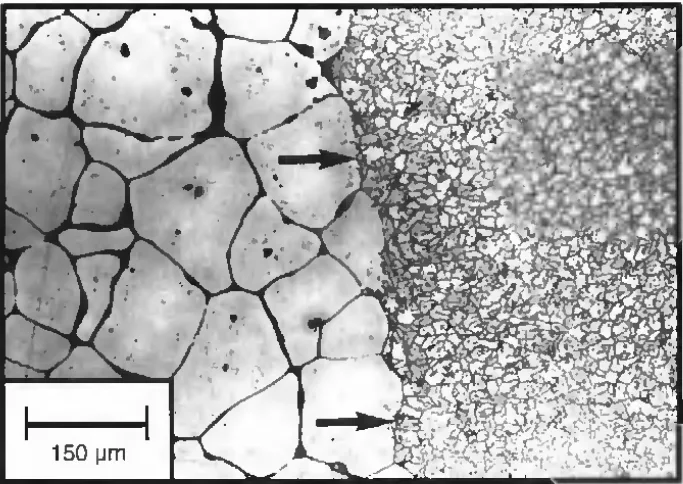
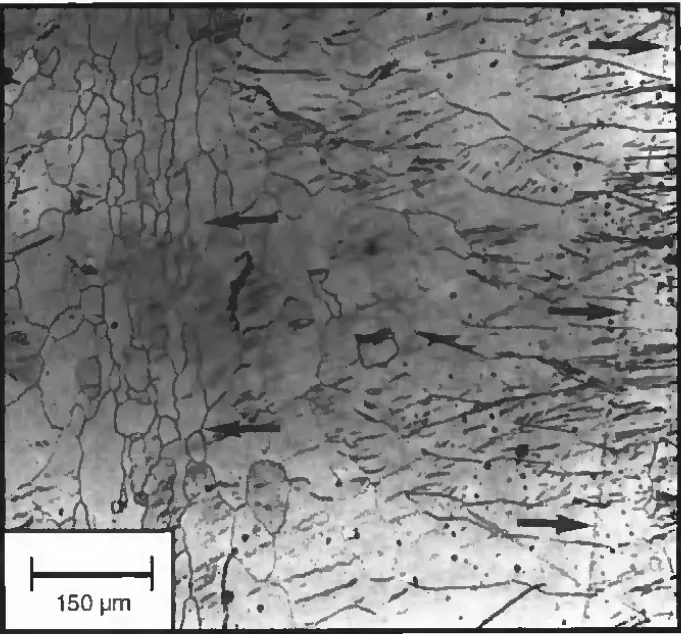
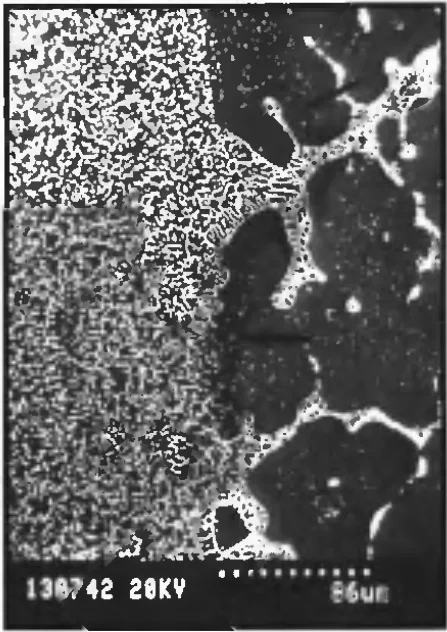
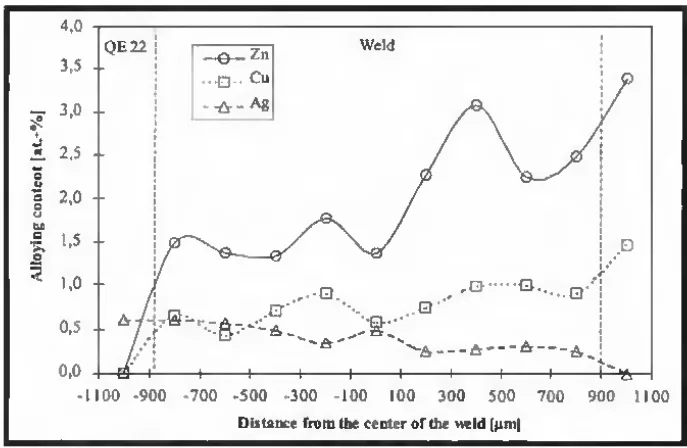
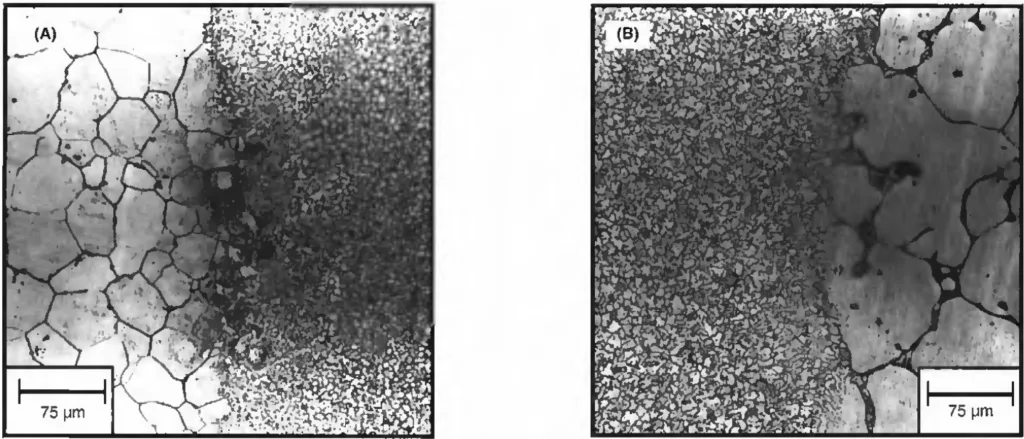
- Fig. 1- Cross section of laser welded ZC 71, thickness 3 mm, 1.5 kW, 3 m/min (17X).
- Fig. 2- Cross section of laser welded WE 54 T6, thickness 5 mm (11X); A - without welding wire, 2 kW, 2 m/min; B - with 2.3-mm welding wire, 2 kW, 1.25 m/min.
- Fig. 3 - Fusion boundary region of weld in QE 22, thickness 5 mm, laser power 2 kW, travel speed 1.75 m/min (100X). Note fine solidification subgrain structure in fusion zone, arrows indicate fusion boundary.
- Fig. 4- Coarse grains in fusion zone and HAZ of AZ 31F, thickness 2.5 mm, laser power 1.5 kW, travel speed 2.5 m/min (100X). Right arrows indicate fusion boundary, left arrows indicate perpendicular grain growth direction in the center of the fusion zone.
- Fig. 5- Liquation of grain boundaries at fusion boundary in ZC 63 T6, 5 mm, 2 kW, 1.75 m/min (350 X). Note also the precipitation-free zone at fusion boundary and grain boundary liquation (marked by arrows).
- Fig. 6 - Element distribution by EDS analysis in a dissimilar weld of QE 22 and ZC 63.
- Fig. 7- Hardness profile across weld in ZC 63 as-cast, 5 mm, 2 kW, 1.75 m/min.
- Fig. 8- Hardness profile in the weld of WE 54 T6 and QE 22 as-cast, 5 mm, 2 kW, 1.75 m/min.
- Fig. 9- Microstructure in the dissimilar joint of QE 22 and WE 54 (200X). The grains in fusion zone are finer and more globular shaped at the WE 54 side (A), whereas the grains at the QE 22 side are coarser and more cellular shaped (B).
7. Conclusion:
Summary of Key Findings:
This study demonstrates that CO2 laser welding is a viable technique for joining most magnesium alloys, offering the potential for high-quality welds with narrow fusion zones and heat-affected zones. Optimal process parameters, particularly shielding gas selection (helium) and focal point positioning, are crucial for achieving crack-free, low-porosity welds. While pressure die-cast alloys and age-hardened QE 22 presented challenges, the overall results indicate that laser welding of magnesium alloys is not fundamentally restricted by metallurgical issues.
Academic Significance of the Study:
This research contributes to the fundamental understanding of laser welding of magnesium alloys by providing a detailed investigation into the weldability characteristics of a wide range of commercial alloys. The study elucidates the influence of alloy composition, heat treatment, and process parameters on weld microstructure, hardness, and defect formation. The findings enhance the scientific knowledge base regarding the application of laser beam welding to lightweight magnesium alloys.
Practical Implications:
The findings of this study have significant practical implications for the manufacturing sector, particularly in the automotive industry. The research demonstrates the potential of CO2 laser welding as an efficient and effective joining method for magnesium components, facilitating the increased use of these lightweight alloys for structural applications. The identified optimal parameters and weld quality assessments provide valuable guidance for industrial implementation of laser welding for magnesium alloy fabrication.
Limitations of the Study and Areas for Future Research:
While this study provides valuable insights, it is acknowledged that research in this area is still in its early stages. Future research should focus on:
- Evaluating the static and dynamic mechanical properties of laser welds in magnesium alloys, including tensile strength, fatigue resistance, and impact toughness.
- Investigating the corrosion resistance of laser-welded magnesium joints to ensure long-term performance in service environments.
- Further exploring the submicroscopic structural changes in laser welds using techniques like transmission electron microscopy (TEM) to better understand the observed hardness variations.
- Developing laser beam welding techniques specifically tailored for challenging alloys like pressure die-cast magnesium and age-hardened QE 22 to mitigate porosity and cracking issues.
8. References:
- 1. Garber, F. 1993. Magnesium – Schwierigkeiten überwunden, neue Chancen im Blick. Metall 47 (6): 574-578.
- 2. Thomas, D. 1991. Increased magnesium usage: not just due to density. Automotive Engineering 99 (2): 47-49.
- 3. Baeslack, W. A., Savage, S. J., and Froes, F. H. 1986. Laser weld heat-affected zone liquation and cracking in a high-strength Mg-based alloy, Journal of Materials Science Letters (5): 935-939.
- 4. Chen, G., Roth, G., and Maisenhälder, F. 1993. Laserstrahlschneiden und -schweißen von Gußmagnesium, Laser und Optoelektronik 25 (1): 43-47.
- 5. Chen, G., and Volz, R. 1993. Leichtmetallbau in der Automobilindustrie – Ein Einsatzgebiet für die Lasertechnik, Automobiltechnische Zeitschrift, Sonderheft Fertigungstechnik, pp. 53-55.
- 6. Data base of Magnesium Elektron Ltd., 1994, Manchester, UK, CD-ROM.
9. Copyright:
- This material is "A. Weisheit, R. Galun and B. L. Mordike"'s paper: Based on "CO2 Laser Beam Welding of Magnesium-Based Alloys".
- Paper Source: WELDING RESEARCH SUPPLEMENT | 149-s
This material was created to introduce the above paper, and unauthorized use for commercial purposes is prohibited.
Copyright © 2025 CASTMAN. All rights reserved.