This article introduces the paper['Casting of product of Al-25%Si with thin fins'] published by ['La Metallurgia Italiana'].
1. Overview:
- Title: Casting of product of Al-25%Si with thin fins
- Author: Toshio Haga, Hiroshi Fuse
- Publication Year: 2016
- Publishing Journal/Academic Society: La Metallurgia Italiana - n. 6
- Keywords: AI-25%SI - THIN FIN - FLUIDITY - THERMAL CONDUCTIVITY - T DENSITY
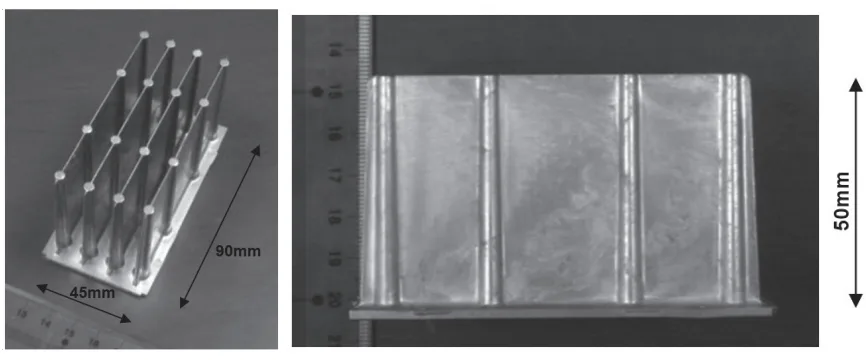
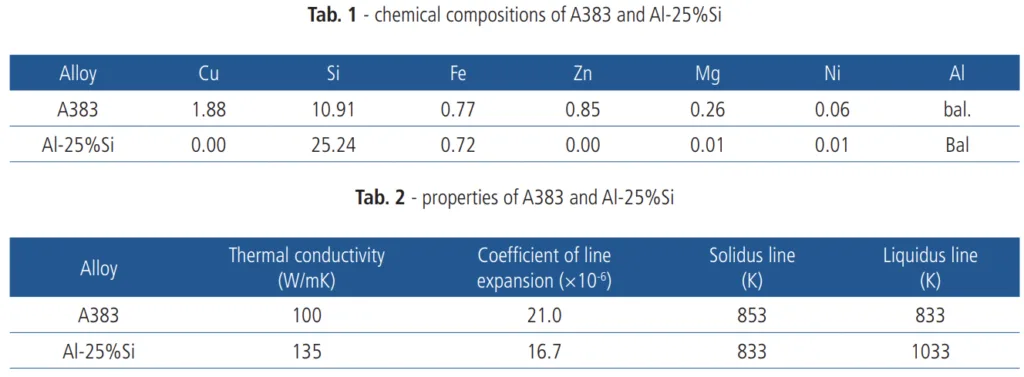
2. Abstracts or Introduction
Recently, the demand for die-casting products with thin fins for heat sinks has increased. A383 aluminum alloy is commonly used for die-casting due to its excellent flowability. However, producing A383 components thinner than 1 mm using conventional die-casting machines is challenging and expensive, often necessitating high-speed die-casting machines. This study explores the potential of utilizing an aluminum alloy with superior flowability compared to A383 in conventional die-casting to manufacture thin-finned products. The research focuses on leveraging the significant latent heat of Silicon (Si) in hyper-eutectic Al-Si alloys to achieve improved flowability through a gradual temperature drop during casting. Considering the liquidus line temperature increase with higher Si content, the study sets 25mass%Si as the upper limit. The lower solidification temperature of this alloy is advantageous for extending die life. Super cooling and low solid fraction semisolid casting (simple rheocasting) techniques were employed. This paper investigates the flow ability of Al-25mass%Si and presents the production of a heat sink model with thin fins.
3. Research Background:
Background of the Research Topic:
The increasing demand for die-cast products featuring thin fins, particularly for heat sink applications, drives the need for efficient manufacturing methods. Conventional die-casting of thin-walled components, specifically those under 1mm thickness using A383 alloy, presents significant manufacturing difficulties and cost implications.
Status of Existing Research:
A383 aluminum alloy is established as a popular choice in die-casting due to its favorable flow characteristics. High-speed die-casting machines offer a solution for casting thinner fins but incur substantial capital expenditure. Existing research explores super cooling and semisolid casting (rheocasting) as alternative approaches to enhance flowability and castability in die-casting processes [1-4].
Necessity of the Research:
The limitations of conventional die-casting for thin-finned products, coupled with the high cost of high-speed die-casting, necessitate the exploration of alternative alloy systems and casting strategies. Utilizing an alloy with enhanced flowability compared to A383 in conjunction with conventional die-casting equipment offers a cost-effective solution for manufacturing thin-finned components. The latent heat of Si in hyper-eutectic Al-Si alloys presents a potential avenue for improving flowability, warranting investigation into Al-25%Si alloy for this application.
4. Research Purpose and Research Questions:
Research Purpose:
The primary purpose of this research is to evaluate the feasibility of using Al-25%Si alloy in conventional die-casting to produce components with thin fins. The study aims to characterize the casting properties of Al-25%Si, particularly its flowability and thermal conductivity, in comparison to the benchmark A383 alloy.
Key Research:
- To investigate the flowability of Al-25%Si alloy in thin die cavities under die-casting conditions.
- To compare the flowability of Al-25%Si with that of A383 alloy in both liquid and semisolid states.
- To assess the thermal conductivity and density of Al-25%Si alloy relative to A383 alloy.
- To demonstrate the casting of a heat sink model with thin fins using Al-25%Si alloy in a conventional die-casting setup.
Research Hypotheses:
- Al-25%Si alloy exhibits superior flowability compared to A383 alloy, particularly in thin die cavities, due to the utilization of the latent heat of Si and super cooling effects.
- Semisolid Al-25%Si demonstrates enhanced flowability compared to liquid A383 under conditions relevant to thin-wall die-casting.
- Al-25%Si alloy possesses higher thermal conductivity and lower density than A383 alloy.
- Super cooling phenomenon can be effectively induced in hyper-eutectic Al-25%Si alloy during die-casting.
5. Research Methodology
Research Design:
The research employs an experimental design to investigate the casting characteristics of Al-25%Si alloy. The study involves comparative experiments using both Al-25%Si and A383 alloys under identical die-casting conditions.
Data Collection Method:
- Cooling Curve Measurement: Cooling curves of Al-25%Si were recorded by pouring molten metal at 830 °C into the sleeve of the die-cast machine to determine the crystallization temperature of primary Si and assess super cooling.
- Fluidity Test: A spiral die (Fig. 1) was used to evaluate the fluidity of both alloys. The length of the spiral flow was measured to quantify fluidity.
- Die-casting of Heat Sink Model: A model of a heat sink with thin fins (Fig. 4) was die-cast using Al-25%Si to demonstrate the alloy's capability to fill intricate shapes.
- Microstructure Analysis: The microstructure of the die-cast Al-25%Si was examined (Fig. 5) to characterize the phase distribution and morphology.
Analysis Method:
- Fluidity Comparison: The fluidity length of Al-25%Si and A383 was compared across varying casting temperatures (650 °C, 700 °C, 740 °C), die cavity gaps (0.5 mm, 1 mm, 2 mm), and plunger speeds (0.5 m/s, 0.8 m/s).
- Cooling Curve Analysis: The cooling curve was analyzed to determine the crystallization temperature and the degree of super cooling achieved.
- Microstructural Observation: Microscopic examination was used to identify and characterize the phases present in the Al-25%Si die-casting.
Research Subjects and Scope:
The research focuses on Al-25mass%Si alloy and compares its die-casting performance to the widely used A383 aluminum alloy. The scope of the study is limited to conventional cold chamber die-casting using a small die-cast machine with a 500 KN die clamping force and a 45 mm sleeve diameter. The fluidity tests were conducted using a spiral die with cavity gaps of 0.5 mm, 1 mm, and 2 mm. The heat sink model had thin fins with a tip thickness of 0.5 mm and a height of 50 mm.
6. Main Research Results:
Key Research Results:
- Fluidity: Semisolid Al-25%Si at 650 °C exhibited superior fluidity compared to liquid A383 at 740 °C, particularly when the die cavity gap was less than 1 mm (Fig. 3). This advantage diminished at a 2 mm gap.
- Cooling Curve: The cooling curve analysis (Fig. 2) indicated that crystallization of primary Si in Al-25%Si started at approximately 700 °C, with super cooling occurring by approximately 60 °C from the liquidus temperature of 760 °C.
- Heat Sink Casting: Successful casting of a heat sink model with 0.5 mm thin fins using Al-25%Si was achieved (Fig. 4), demonstrating the alloy's suitability for intricate geometries.
- Microstructure: The microstructure of die-cast Al-25%Si (Fig. 5) consisted of globular primary Si, Al, and eutectic phases. The primary Si particles were small, minimizing flow obstruction in thin gaps.
Analysis of presented data:
- Fluidity Data (Fig. 3): The graphical data clearly illustrates the enhanced fluidity of Al-25%Si over A383, especially at lower casting temperatures and narrower die gaps. The trend suggests that the semisolid state of Al-25%Si at lower temperatures contributes to improved flow in restricted spaces.
- Cooling Curve Data (Fig. 2): The cooling curve confirms the super cooling phenomenon in Al-25%Si, which is crucial for achieving the desired semisolid state for rheocasting. The crystallization temperature around 700 °C is a key parameter for process control.
- Heat Sink Model (Fig. 4): The successful casting of the complex heat sink geometry validates the practical applicability of Al-25%Si for thin-finned components using simple rheocasting.
- Microstructure Image (Fig. 5): The microstructure image supports the mechanism of improved flowability by showing fine, globular primary Si particles that do not impede metal flow in thin sections.
Figure Name List:
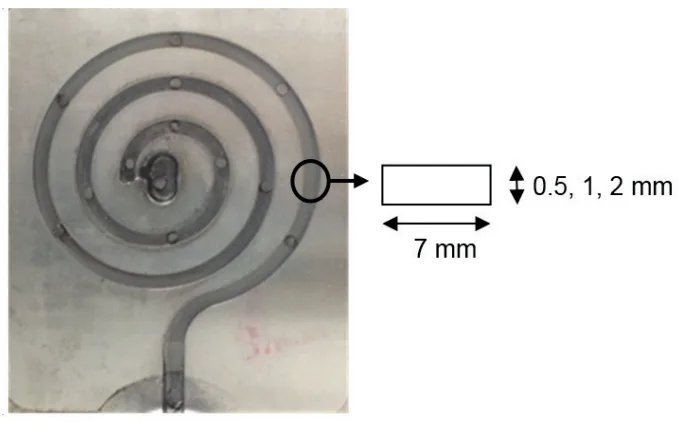
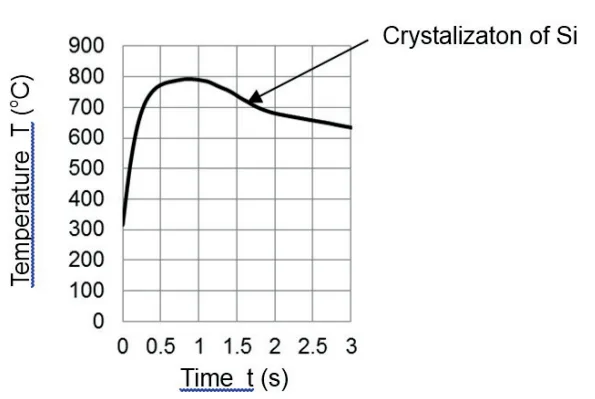
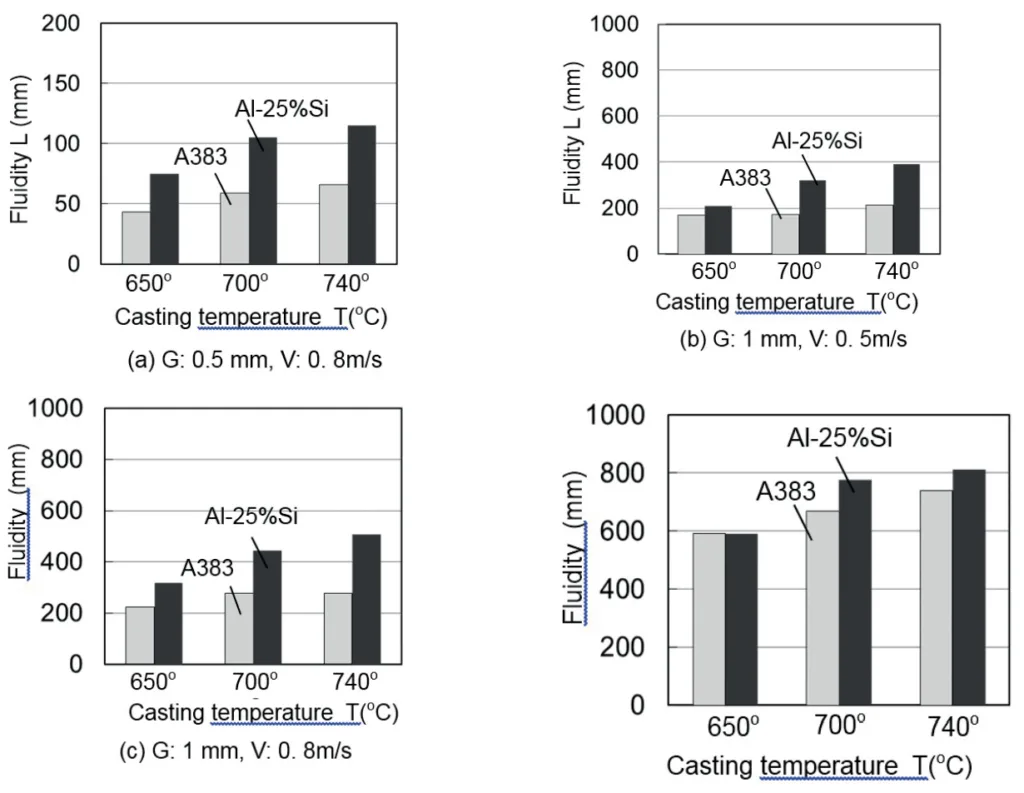
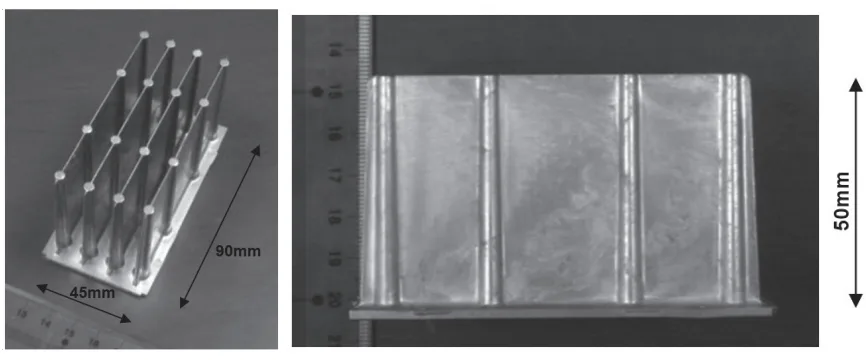
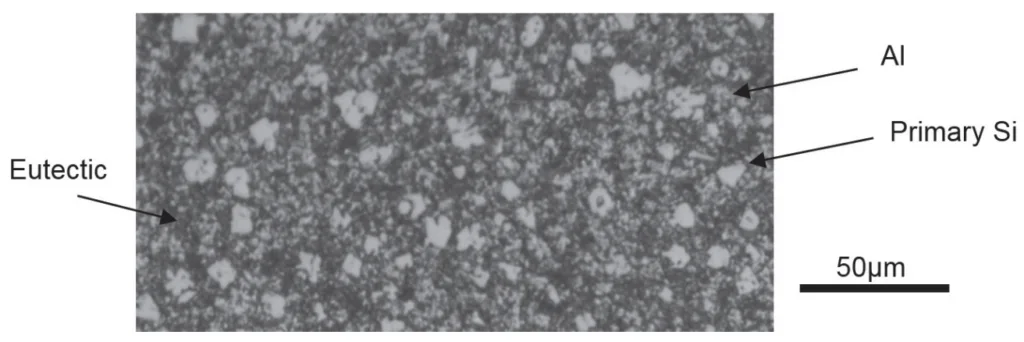
- Fig.1 - photograph of a spiral die used for investigation of fluidity
- Fig.2 - cooling curves of Al-25%Si in the sleeve of the die-cast machine
- Fig.3 - caption Result of the fluidity test of A383 and Al-25%Si using a spiral die by a die-cast machine
- Fig.4 - Model of the heat sink cast from Al-25%Si. The height of the fin was 50 mm. The thickness of the tip of the fine was 0.5 mm, and the draft angle of the fin was 0.5 degree.
- Fig.5 - Microstructure of die-cast Al-25%Si
7. Conclusion:
Summary of Key Findings:
This study demonstrated that Al-25%Si alloy exhibits superior flowability compared to A383 in die-casting, particularly in thin cavity sections (less than 1mm). Semisolid casting of Al-25%Si at lower temperatures (650-700°C) through simple rheocasting enhances fluidity. The alloy's higher thermal conductivity and lower density compared to A383 were also confirmed. Successful casting of a thin-finned heat sink model validated the practical application of Al-25%Si for complex geometries using conventional die-casting equipment. Super cooling in Al-25%Si facilitates the simple rheocasting process.
Academic Significance of the Study:
This research contributes to the understanding of the die-casting behavior of hyper-eutectic Al-Si alloys, specifically Al-25%Si. It highlights the potential of utilizing the latent heat of Si and super cooling to enhance flowability in conventional die-casting processes. The study provides valuable data on the comparative fluidity and thermal properties of Al-25%Si and A383 alloys, expanding the material selection options for die-casting applications.
Practical Implications:
The findings suggest that Al-25%Si alloy offers a viable alternative to A383 for die-casting thin-finned components, such as heat sinks, using conventional die-casting machines. The enhanced flowability of Al-25%Si in the semisolid state, achieved through simple rheocasting, can reduce manufacturing costs by eliminating the need for high-speed die-casting equipment. The improved thermal conductivity of Al-25%Si can also enhance the performance of heat sink applications. Furthermore, the lower casting temperatures associated with semisolid processing can potentially extend die life.
Limitations of the Study and Areas for Future Research:
This study primarily focused on fluidity and basic casting characteristics. Further research is recommended to investigate the mechanical properties, corrosion resistance, and long-term reliability of Al-25%Si die-cast components. A more detailed optimization of the rheocasting process parameters for Al-25%Si, including gate design and injection parameters, is warranted. Additionally, exploring the performance of Al-25%Si in other complex die-casting geometries and applications would be beneficial. The economic feasibility and scalability of using Al-25%Si in industrial die-casting production should also be evaluated.
8. References:
- [1] P.Eisen, K. Young, Diecasting system for semi-liquidus and semisolid metal casting, Proceedings of the Sixth International Conference on Semisolid Processing of Alloys and Composites, (2000) 41-46.
- [2] T.Haga, P.Kapranos, Simple rheocasting processs, J. Mater. Process. Technol. (2002), 594-598.
- [3] T.Haga, P.Kapranos, Billetless simple thixoforming process, J. Mater. Process. Technol. (2002), 581-586.
- [4] A.Kraly, Development and industrial production of thix-alloy as a system solution, Proceedings of the Sixth International Conference on Semisolid Processing of Alloys and Composites, (2000) 495-500.
9. Copyright:
- This material is "Toshio Haga, Hiroshi Fuse"'s paper: Based on "Casting of product of Al-25%Si with thin fins".
- Paper Source: https://doi.org/ (DOI URL was not provided in the text, please add if available)
This material was summarized based on the above paper, and unauthorized use for commercial purposes is prohibited.
Copyright © 2025 CASTMAN. All rights reserved.