This article introduces the paper "AUTOMATIC DETERMINATION OF PARTING LINE AND NUMBER OF CAVITIES IN DIE CASTING DIE" presented at the 10th IRAJ International Conference
1. Overview:
- Title: AUTOMATIC DETERMINATION OF PARTING LINE AND NUMBER OF CAVITIES IN DIE CASTING DIE
- Authors: SUNIL KUMAR, RANJIT SINGH, VIJAY KUMAR, VINOD KUMAR
- Publication Year: 2013
- Publishing Journal/Academic Society: Proceedings of 10th IRAJ International Conference
- Keywords: Die-casting, Parting line, Parting direction, GUI, Multi Cavity Dies, STL file
![Fig 2: Dominations in Parting Line [3]](https://castman.co.kr/wp-content/uploads/Fig-2-Dominations-in-Parting-Line-3.webp)
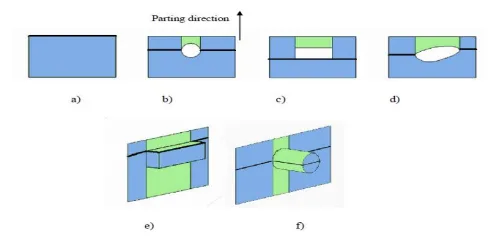
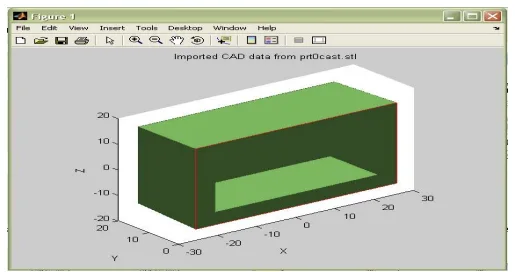
2. Research Background:
- Social/Academic Context of the Research Topic: Die-casting is a widely used process for manufacturing engineered metal parts with complex shapes, high accuracy, and repeatability. Designing die casting dies is a critical and time-consuming step in the process. The design process, especially determining parameters like parting direction, parting line, parting surface, and the number of cavities, heavily relies on expert knowledge and is often iterative and manual. This manual approach creates a gap in design manufacturing integration within the die-casting process.
- Limitations of Existing Research: Existing die design processes often lack automation, relying on expert intuition and manual selection for critical parameters like parting line and number of cavities. This manual approach is time-consuming and can be a bottleneck in the die-casting process. While CAD models are used, the generation of manufacturing data and the determination of die parameters are not fully integrated or automated.
- Necessity of the Research: To improve the efficiency and reduce the time involved in die design for casting, there is a need for automated systems that can determine key die design parameters. Specifically, automating the determination of the parting line and the number of cavities in a die casting die can significantly enhance the design process and reduce reliance on manual, expert-driven methods. Such automation would contribute to better design manufacturing integration in die casting.
3. Research Purpose and Research Questions:
- Research Purpose: The primary purpose of this research is to develop an automatic system to determine the parting line and direction, along with the parting surface, and to calculate the number of cavities in a die casting die. The system aims to take machine and product data as input and automatically output the number of cavities and parting line information.
- Key Research Questions:
- Can an automatic system be developed to determine the parting line and parting direction for die casting dies using CAD models as input?
- Can MATLAB be used to implement such a system for parting line and parting surface determination?
- Can an automatic system be developed to calculate the optimal number of cavities in a die casting die based on various design criteria and input parameters?
- How can a GUI be implemented in MATLAB to facilitate the use of this automated system for die casting die design?
- Research Hypotheses:
- It is possible to automate the determination of the parting line and direction by analyzing the 3D CAD model of the part.
- MATLAB can be effectively used to develop algorithms and a GUI for automating parting line determination and cavity number calculation.
- An automated system can provide a more consistent and efficient method for determining the number of cavities compared to manual calculations.
4. Research Methodology
- Research Design: The research employs a system development approach, focusing on creating an automated system using MATLAB. This involves algorithm development for parting line determination and cavity number calculation, and the creation of a GUI for user interaction.
- Data Collection Method: The input data for the system consists of 3D CAD models of parts in STL file format, and die casting machine and product data. The CAD models are designed in SolidWorks. The system uses standard formulae and design criteria related to production, part, machine, and material databases for cavity number calculation.
- Analysis Method:
- Parting Line Determination: The system uses MATLAB to process the STL file of the 3D CAD model. The algorithm identifies the parting line by analyzing the geometry of the part. The direction in which the projected area of the part is maximum is selected as the parting direction. Parting line determination starts with common edges between core and cavity molded facets. Parting line regions are selected based on undercut position and shape.
- Number of Cavities Determination: The system calculates the number of cavities based on several criteria: delivery date, cost, machine parameters, clamping force, and maximum flow rate. Formulas (1) to (5) from the paper are used for these calculations. The minimum value among the number of cavities calculated based on clamping force, flow rate, and machine size is considered as the machine-parameter-based number of cavities [Nmac].
- Research Subjects and Scope: The system is tested using sample 3D CAD part models designed in SolidWorks and saved as STL files. The scope includes automating parting line determination and number of cavity calculation for die casting dies, implemented in a MATLAB environment with a GUI.
5. Main Research Results:
- Key Research Results:
- Automatic Parting Line Determination: The developed MATLAB system successfully automates the determination of the parting line for 3D CAD models. Figure 8 and Figure 10 show the result windows from MATLAB, demonstrating the automatically generated parting lines for sample parts. The system identifies the outer parting line covering the maximum projected area. For complex parts like sample part 2 (P2), the system correctly identifies the parting line at the core side of the casting.
- Automatic Number of Cavities Determination: A GUI-based system in MATLAB was developed to calculate the number of cavities. The system considers various criteria and constraints. Figures 11, 12, 13, and 14 show the GUI windows for different cases, demonstrating the system's ability to calculate the number of cavities based on input parameters.
- Case Studies: The system was tested with different cases, varying part models and machine parameters. Table 1 summarizes the results for multi-cavity dies for four cases. For example, for part number 1 with machine number 1 (Case 1), the optimum number of cavities is determined to be 2. For part number 2 with machine number 3 (Case 4), the optimum number of cavities is 6.
- Statistical/Qualitative Analysis Results: The paper primarily presents a system development and case study approach, and does not include statistical analysis. The results are evaluated qualitatively based on the successful implementation and demonstration of the automated systems for parting line and cavity number determination.
- Data Interpretation: The results indicate that the developed MATLAB-based system is effective in automating both parting line determination and number of cavity calculation for die casting dies. The GUI provides a user-friendly interface for inputting parameters and obtaining results. The case studies demonstrate the applicability of the system for different part geometries and machine configurations.
- Figure Name List:
- Fig 2: Dominations in Parting Line [3]
- Fig 3: Automatic cavity layout design [4]
- Fig 4: Parting line regions (in blue colour) for vertical surfaces
- Fig 5: Parting line (bold black line) for different vertical surface
- Fig 6: Sample part 1 (P1)
- Fig 7: Typical window of solid works containing sample part
- Fig 8: Automatic parting line determined by proposed methodology
- Fig 9: Sample Part 2 (P2)
- Fig 10: Parting line determined for a free form part model
- Fig 11: GUI window case 1
- Fig 12: GUI window case 2
- Fig 13: GUI window case 3
- Fig 14: GUI window case 4
6. Conclusion and Discussion:
- Summary of Main Results: The research successfully developed and implemented an automated system for determining the parting line and calculating the number of cavities in die casting dies. The system, built in MATLAB with a GUI, takes 3D CAD models (STL files) and machine/product data as input. It automatically determines the parting line and calculates the optimal number of cavities based on various design and manufacturing constraints.
- Academic Significance of the Research: This research contributes to the field of die casting die design by providing a methodology and a working system for automating critical and time-consuming design tasks. It demonstrates the application of computational methods and software tools like MATLAB for enhancing die design processes. The work addresses the gap in design manufacturing integration in die casting by reducing reliance on manual expert intervention.
- Practical Implications: The developed system has significant practical implications for the die casting industry. By automating parting line determination and cavity number calculation, it can:
- Reduce design time and cost.
- Improve design consistency and accuracy.
- Enable faster turnaround times for die design and manufacturing.
- Assist die designers in making informed decisions regarding cavity layout and die configuration.
- Limitations of the Research: The paper does not explicitly discuss limitations in detail. However, potential limitations could include:
- The system's performance with extremely complex part geometries or non-standard die casting processes might need further investigation.
- The accuracy and reliability of the system are dependent on the quality and format of the input CAD models and data.
- The paper does not provide extensive validation of the system in real-world industrial settings.
7. Future Follow-up Research:
- Directions for Follow-up Research: Future research could focus on:
- Expanding the system's capabilities to handle more complex part geometries and die casting scenarios.
- Integrating the system with commercial CAD/CAM software for seamless workflow.
- Validating the system's performance and benefits through extensive industrial case studies and user feedback.
- Incorporating optimization algorithms to further refine the parting line and cavity layout for improved die performance and casting quality.
- Exploring the application of AI and machine learning techniques to enhance the automation and decision-making capabilities of the system.
- Areas Requiring Further Exploration: Further exploration is needed in areas such as:
- The robustness of the parting line determination algorithm for a wider range of part features and complexities.
- The sensitivity of the cavity number calculation to variations in input parameters and cost models.
- The user-friendliness and efficiency of the GUI for practical industrial applications.
8. References:
- [1] R. Khardekar and S. McMains, "Efficient computation of a near-optimal primary parting line", Joint Conference on Geometric and Physical Modeling, 2009, pp. 319-324.
- [2] Z. Zhiqiang, "Automated Parting Methodology for Injection mold", University of Singapore, 2009, pp. 59-69.
- [3] J. Madan, P.V.M. Rao and T.K. Kundra, "Die-casting feature recognition for automated parting direction and parting line determination", Journal of Computing and Information Science in Engineering, 7 (3), 2007, pp. 236-248.
- [4] Y. Xin and Y. Yanto, "Research on method choosing parting line in die NC machining", IEEE Vol. 5, 2011, pp. 2628-2631.
- [5] R. Singh, J. Madan and A. Singh, "Optimal selection of parting line for die-casting", International Journal of Applied Research, Vol.5, No. 17, 2010, pp. 2899-2906.
- [6] V. Kumar, J. Madan and P. Gupta (2010), " Development of a system for automated cavity layout design of die-casting die", Computer Aided Design & Applications, 7(a), 2013, pp. 2083-2107.
- [7] P. Chakraborty and N.V. Reddy, "Automatic determination of parting directions, parting lines and parting surfaces for two-piece permanent molds", Journal of Materials Processing Technology, 209, 2009, pp. 2464-2476.
- [8] V. Kumar, J. Madan and P. Gupta, "System for Computer Aided Cavity Layout Design of Die-Casting Die", International Journal of Production Research, Vol. 50, Issue 18, 2012, pp. 5181-5194.
- [9] W. Hu and S. Masood, "Development of an Intelligent Cavity Layout Design System for Injection Molding Dies", IJE Transactions A: Basics, Vol. 15, No. 4, 2002, pp. 339-348.
- [10] P. Dewhurst and C. Blum, "Supporting Analyses for Economic Assesment of Die-Casting in Product Design", Annals of the CIRP Vol. 38, Issue 1, 1989, pp. 161-164.
9. Copyright:
*This material is SUNIL KUMAR, RANJIT SINGH, VIJAY KUMAR, VINOD KUMAR's paper: Based on AUTOMATIC DETERMINATION OF PARTING LINE AND NUMBER OF CAVITIES IN DIE CASTING DIE.
*Paper Source: https://www.researchgate.net/publication/344146489_AUTOMATIC_DETERMINATION_OF_PARTING_LINE_AND_NUMBER_OF_CAVITIES_IN_DIE_CASTING_DIE (DOI URL not explicitly available in the document, ResearchGate link provided as source)
This material was summarized based on the above paper, and unauthorized use for commercial purposes is prohibited.
Copyright © 2025 CASTMAN. All rights reserved.