This article introduces the paper "An Automated System for Design for Manufacturability Analysis for Die-Casting" presented at the Proceedings of the ASME 2018 International Manufacturing Science and Engineering Conference
1. Overview:
- Title: An Automated System for Design for Manufacturability Analysis for Die-Casting
- Author: Sunil Kumar, Jatinder Madan
- Publication Year: June 2018
- Publishing Journal/Academic Society: Proceedings of the ASME 2018 International Manufacturing Science and Engineering Conference
- Keywords: Design for manufacturability, die-casting, knowledgebase, feature extraction, model updation.
![FIGURE 1: SCHEMATIC OF A DIE CASTING DIE [1]](https://castman.co.kr/wp-content/uploads/FIGURE-1-SCHEMATIC-OF-A-DIE-CASTING-DIE-1-1024x466.webp)
2. Research Background:
- Social/Academic Context of the Research Topic: Design for Manufacturing (DFM) is crucial for incorporating manufacturability considerations early in the design stage. This is especially important when design and manufacturing are performed by different, potentially remote teams. The development of automated DFM tools is therefore increasingly significant.
- Limitations of Existing Research: Traditional approaches to ensure manufacturability rely on iterative consultations with manufacturing experts. This process is time-consuming, increases design lead times, raises production costs, and delays time to market, negatively impacting organizational profits. Existing DFM systems for die-casting have not fully addressed the need for automated analysis and application of manufacturability advice. Specifically, there's a gap in systems that offer comprehensive knowledgebases, efficient feature extraction from CAD models, and automated model updates based on DFM analysis.
- Necessity of the Research: To overcome the limitations of traditional DFM and existing systems, there is a need for an automated DFM system for die-casting. Such a system can generate manufacturability advice and automatically modify part designs, thereby reducing design iterations, lead time, and production costs.
3. Research Purpose and Research Questions:
- Research Purpose: The primary purpose of this research is to present an automated system for design for manufacturability analysis specifically for die-cast parts.
- Key Research Questions: The paper aims to address how to:
- Develop a knowledgebase of DFM guidelines for die-casting.
- Implement die casting feature extraction from part CAD models.
- Create an automated system for DFM analysis and model updation of die-cast part CAD models.
- Research Hypotheses: While not explicitly stated as hypotheses, the research operates under the premise that an automated DFM system can effectively analyze die-cast part designs, provide manufacturability advice, and automatically update CAD models to improve manufacturability and reduce material usage.
4. Research Methodology
- Research Design: The research involves the development of an automated DFM system. This includes creating a knowledgebase of DFM guidelines, developing a feature extraction methodology, and integrating these components into a system capable of analyzing CAD models and suggesting design modifications.
- Data Collection Method: The system's capabilities are demonstrated and validated by applying it to die-cast part CAD models. The results are then validated through consultation with industrial experts.
- Analysis Method: The system analyzes CAD models by extracting feature parameters and comparing them against the DFM knowledgebase. The effectiveness of the system is evaluated by assessing the manufacturability advice generated, the automated model updates, and the resulting changes in part weight.
- Research Subjects and Scope: The system is designed to work with CAD models of die-cast parts that are created using feature-based modeling and include features such as boss, rib, hole, and draft.
5. Main Research Results:
- Key Research Results: The paper successfully presented an automated system for DFM analysis for die-casting. The system encompasses:
- A knowledgebase of DFM guidelines.
- Die casting feature extraction from part CAD models.
- An automated system for DFM analysis and model updation.
The system's capabilities were demonstrated on die-cast part CAD models, and the results were validated with industrial experts.
- Statistical/Qualitative Analysis Results:
- Application of the system on example parts showed significant material saving. For "part model-1," material saving was approximately 35%. For "part model-2," material saving was approximately 37%. These savings were achieved through automated redesign based on DFM advice, primarily by reducing wall thickness and optimizing features.
- Expert validation confirmed the practical relevance and effectiveness of the system's advice and model updates.
- Data Interpretation: The automated DFM system effectively identifies manufacturability issues in die-cast part designs and provides actionable advice, which can be automatically implemented to update the CAD model. This leads to improved manufacturability and reduced material consumption.
- Figure Name List:
- FIGURE 1: SCHEMATIC OF A DIE CASTING DIE [1]
- FIGURE 2: DIE-CASTING FEATURE TERMINOLOGY
- FIGURE 3: FEATURE EXTRACTION
- FIGURE 4: FEATURE PARAMETERS
- FIGURE 5: THE PROPOSED DFM SYSTEM
- FIGURE 6: FEATURE BASED PART MODELS
- FIGURE 7: EXISTING AND REDESIGNED FEATURE BASED PART MODEL-1
- FIGURE 8: EXISTING AND REDESIGNED FEATURE BASED PART MODEL-2
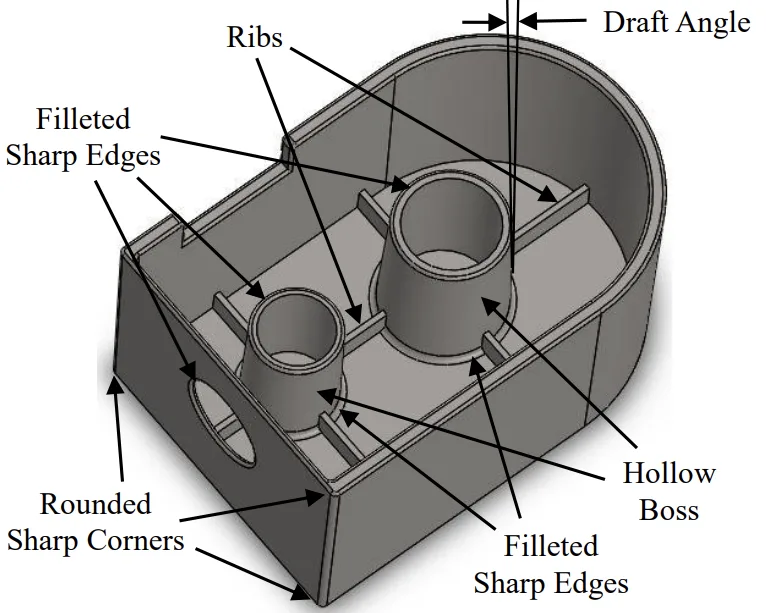
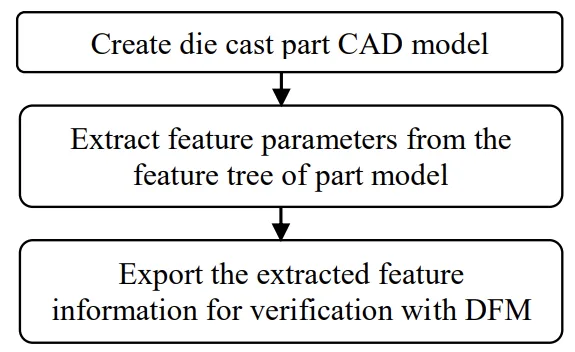
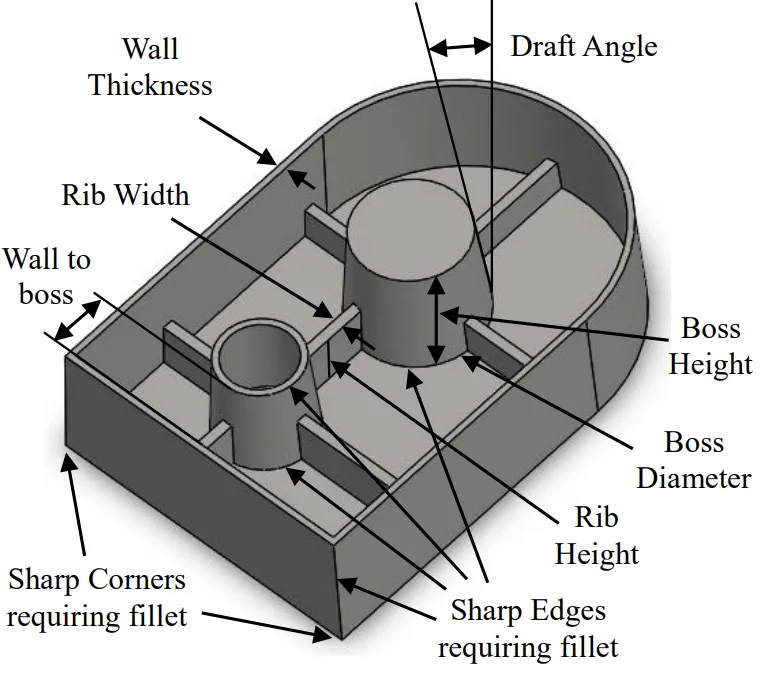
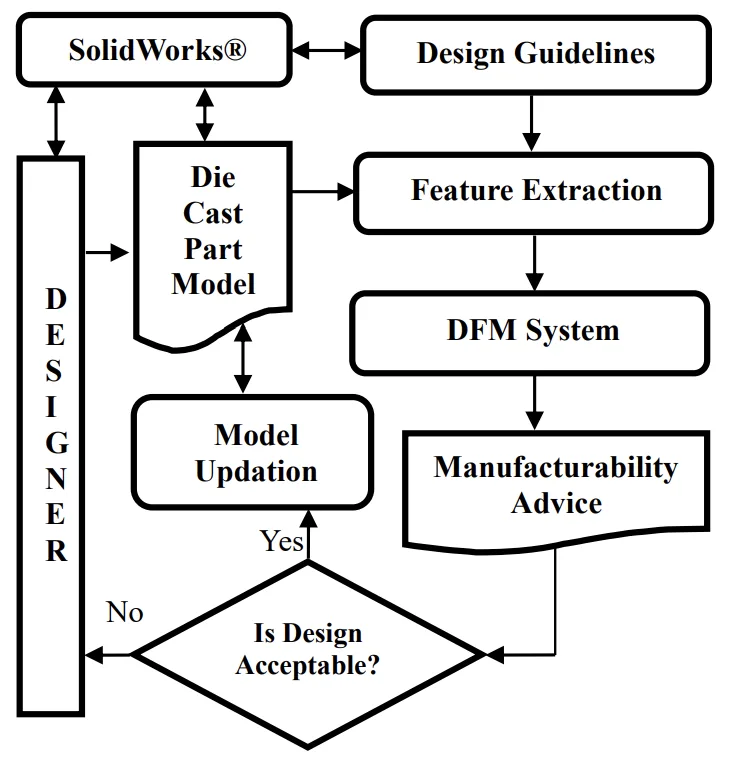
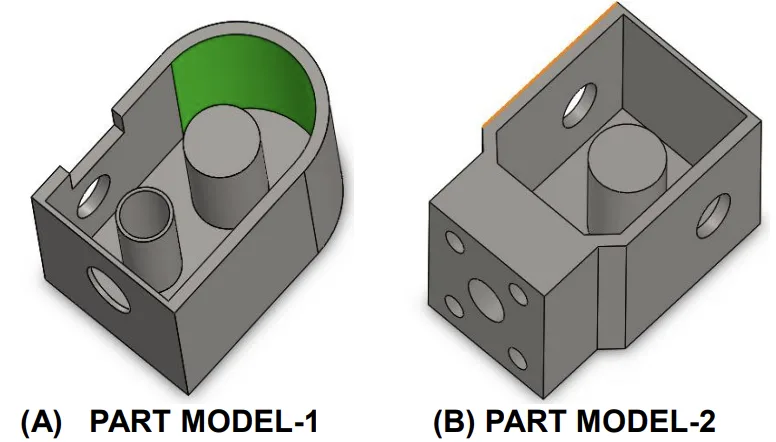
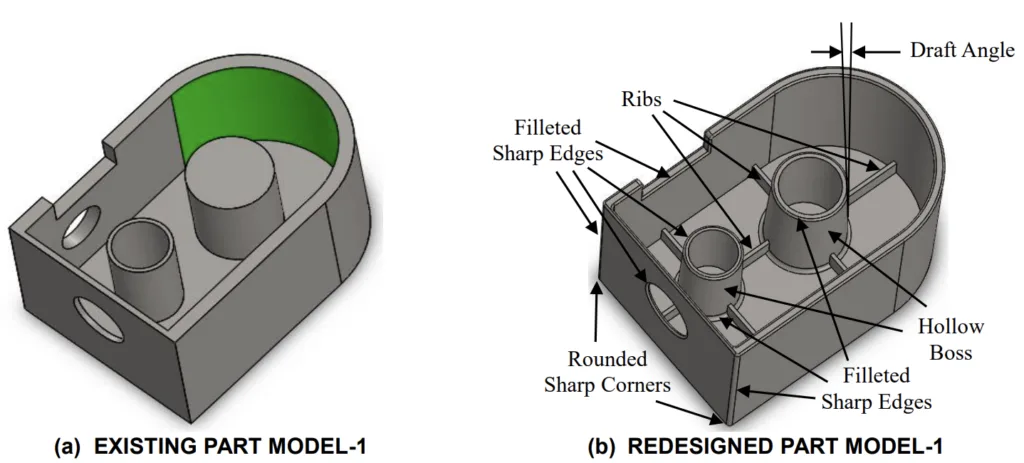
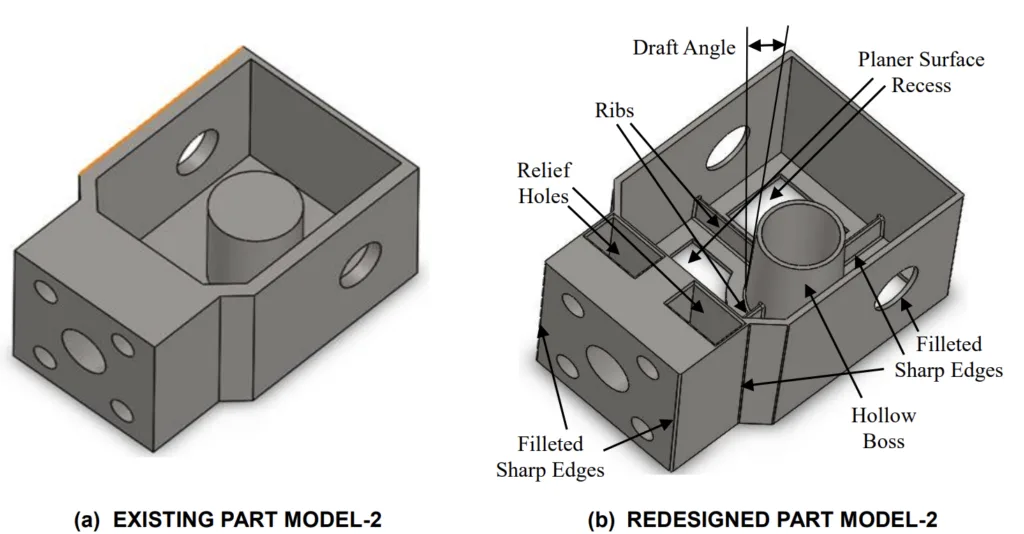
6. Conclusion and Discussion:
- Summary of Main Results: This research successfully developed and demonstrated an automated system for DFM analysis of die-cast parts. The system automates the process of manufacturability assessment and CAD model modification, leading to designs with improved manufacturability and reduced material weight.
- Academic Significance of the Research: The research contributes to the field of automated DFM, specifically addressing the needs of die-casting. It provides a methodology for automating DFM analysis and model updates, which was previously lacking in existing systems, particularly for die-casting.
- Practical Implications: The developed system offers significant practical benefits for the die-casting industry. By automating DFM analysis and model updates, it can substantially reduce design lead times, lower production costs, and optimize material usage. This can lead to faster product development cycles and more cost-effective and sustainable manufacturing processes.
- Limitations of the Research: The current system has certain limitations:
- It is designed for feature-based CAD models and may not be directly applicable to models created using other modeling methods.
- The system's feature recognition and DFM advice are currently limited to specific features like boss, rib, hole, and draft.
- The system, in its current form, does not explicitly account for functional requirements of the part during the automated redesign process. Designer intervention is still needed to accept or reject suggestions based on functional needs.
7. Future Follow-up Research:
- Directions for Follow-up Research: Future research should focus on:
- Expanding the system's capabilities to handle a wider range of die-casting features and more complex part geometries.
- Integrating functional requirements into the automated DFM analysis and redesign process to ensure that design modifications maintain part functionality.
- Enhancing the automation level of the system to further reduce the need for manual intervention.
- Exploring the application of the system to other die-casting alloys and process variations.
- Areas Requiring Further Exploration: Further exploration is needed in developing more comprehensive DFM knowledgebases that incorporate a broader range of industry best practices and design guidelines for die-casting. Improving the robustness and efficiency of feature extraction methods for complex die-cast parts is also an area for future work.
8. References:
- [1]. Madan J., Rao P.V.M., Kundra T.K., 2007, “Computer aided manufacturability analysis of die cast parts", Computer Aided Design and Applications, 4 (1-4), pp. 147-158.
- [2]. Bralla, J. G., 1999, “Design for manufacturability handbook", McGraw-Hill Inc., New York. (2nd Ed.).
- [3]. Hui K.C., 1997, “Geometric aspects of the mouldability of parts", Computer Aided Design, 29 (3), pp. 197-208.
- [4]. O'Driscoll M., 2001, “Design for manufacture”, Journal of Materials Processing Technology, 122, pp. 318-321.
- [5]. Gupta S.K., Regli W.C., Das D., Nau D.S., 1997, "Automated manufacturability analysis: A survey, Res. Eng. Des., 9 (3), pp.168–190.
- [6]. Chen Y., Miller R.A., Sevenler K., 1995, “Knowledge based manufacturability assessment: an object oriented approach", Journal of Intelligent Manufacturing, 6, pp.321-337.
- [7]. Datar J.S., Ravi B., Pande S.S., 1992, "feature based modeler for the design of die cast components", IIF Transactions, 94-18, pp. 247-252.
- [8]. Ramana K.V., Rao P.V.M., 2005, “Automated manufacturability evaluation system for sheet metal components in mass production”, International Journal of Production Research, 43 (18), pp. 3889–3913.
- [9]. Ramana K.V., Singh M., Gupta A., Dey R., Kapoor A., Rao P.V.M., 2006, “A manufacturability advisor for spun and roll formed sheet metal components", International Journal of Advances in Manufacturing Technology, 28, pp. 249-254.
- [10]. Venkatachalam A. R., Mellichamp J. M., Miller D. M., 1993, "A knowledge based approach to design for manufacturability", Journal of Intelligent Manufacturing, 4, pp. 355-366.
- [11]. Chen Y.M., Wen C.C., Ho C.T., 2003, “extraction of geometric characteristics for manufacturability assessment", Robotics and Computer Integrated Manufacturing, 19, pp. 371-385.
- [12]. Jacob D.V., Ramana K.V., Rao P.V.M., 2004, “Automated manufacturability assessment of rotational parts by grinding”, International Journal of Production Research, 42 (3), pp. 505-519.
- [13]. Das D., Gupta S. K., Nau D., 1996, “Generating redesign suggestions to reduce setup cost: a step towards automated redesign”, Computer Aided Design, 28 (10), pp. 763-782.
- [14]. Kumar S., Gupta A.K., Chandna P., 2012, "Optimization of process parameters of pressure die casting using Taguchi methodology", World Academy of Science, Engineering and Technology, 6, pp. 590-594.
- [15]. Bidkar R. A., McAdams D. A., 2010, "Methods for automated manufacturability analysis of injection-molded and die-cast parts", Research in Engineering Design, 21 (1), pp. 1-24.
- [16]. Shukor S.A., Axinte D.A., 2009, “Manufacturability analysis system: issues and future trends", International Journal of Production Research, 47 (5), pp. 1369-1390.
- [17]. Srikumaran S., Sivaloganathan S., 2005, “Proving manufacturability at the design stage using commercial modeling software", Computer Aided Design and Applications, 2, pp. 507-516.
- [18]. Madan J., Rao P.V.M., Kundra T.K., 2006, "System for early cost estimation of die-cast parts”, International Journal of Production Research, 45 (20), pp. 1-25.
- [19]. Poli C., 2001, “Design for manufacturing: A structured approach", Elsevier Science and Technology Books publishers.
- [20]. Chougule R. G., Ravi B., 2005, "Casting cost estimation in an integrated product and process design environment", International Journal of Computer Integrated Manufacturing, 19 (7), pp. 2-5.
- [21]. Chan D.S.K., 2003, "Expert system for product manufacturability and cost evaluation", Materials and Manufacturing Process, 18 (2), pp. 313-322.
- [22]. Hayes C.C., 1996, “Plan-based manufacturability analysis and generation of shape changing redesign suggestions", Journal of Intelligent Manufacturing, 7 (2), pp. 121-132.
- [23]. Korosec M., Balic J., Корас J., 2015, “Neural network based manufacturability evaluation of free form machining", International Journal of Machine Tools & Manufacturing, 45 (1), pp. 13-20.
- [24]. North American Die Casting Association, 2015, NADCA product specification standards for die casting, retrieved from https://www.diecasting.org/wcm/Technology/Standards/Die_Casting/wcm/Technology/Die_Casting_Standards.aspx?hkey=73d48de9-87ff-4e3.e-ace2-657a2cf33d99 (Assessed at 11am on 7-2-2018).
- [25]. Dhaliwal S., Gupta S. K., Huang J., Kumar M., 2002, "A step towards automated design of multi-piece sacrificial molds", ASME International Design Engineering Technical Conferences and Computers and Information in Engineering Conference, 3, pp. 337-347.
9. Copyright:
- This material is Sunil Kumar and Jatinder Madan's paper: Based on An Automated System for Design for Manufacturability Analysis for Die-Casting.
- Paper Source: DOI: 10.1115/MSEC2018-6510
This material was summarized based on the above paper, and unauthorized use for commercial purposes is prohibited.
Copyright © 2025 CASTMAN. All rights reserved.