This article introduces the paper ['ALUMINIUM DIE CASTING: LUBRICATION TECHNOLOGY AND TRENDS'] published by ['Chem-Trend L.P'].
1. Overview:
- Title: ALUMINIUM DIE CASTING: LUBRICATION TECHNOLOGY AND TRENDS
- Author: G.NATESH
- Publication Year: Not explicitly stated in the document, but likely around or after 1993 based on reference [2].
- Publishing Journal/Academic Society: Not explicitly stated, likely a conference or industry publication by Chem-Trend L.P.
- Keywords: aluminium die casting, lubrication technology, trends, die lubricant, Leidenfrost effect, cooling, productivity, solder, die adhesion.
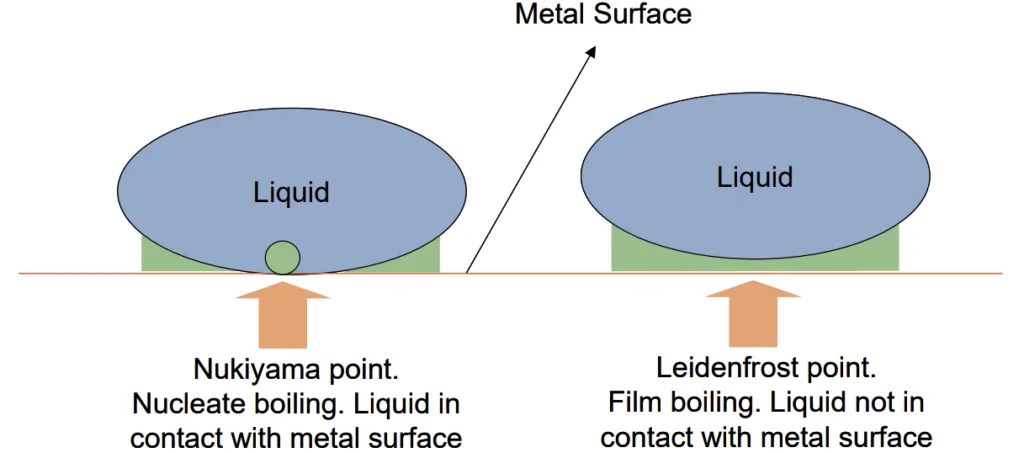
2. Abstracts or Introduction
Abstract: The drive for improved fuel efficiencies in the automobile industry has led to continuing growth in aluminium die casting as manufacturers strive to reduce the weight of automobiles by replacing steel with light metal components. Larger and more complex parts are being cast and this has set new challenges to die casters in their quest for improved quality and productivity. The paper examines the impact of these trends on die and plunger lubrication and discusses how lubrication technology has evolved to satisfy these requirements.
3. Research Background:
Background of the Research Topic:
High Pressure die-casting is a very popular process for manufacturing complex mechanical parts using light metals such as aluminium and magnesium alloys, especially for the automobile industry due to demands for rapid and reliable component production in assembly line and JIT manufacturing environments. The rapid growth of the Indian economy is also increasing the demand for die-cast products across various sectors including recreational vehicles, power tools, electrical machinery, electronic components, and house-ware.
Status of Existing Research:
The trend towards larger and more complex aluminium die cast parts, driven by the automotive industry's pursuit of weight reduction for improved fuel efficiency, presents challenges. Increased part complexity hinders uniform internal die cooling, leading to elevated die surface temperatures. Historically, die surface temperatures before spray ranged from 250°C to 350°C, but now can reach up to 400°C in hotter die portions while cooler areas may be as low as 220°C. This temperature variation results in localized hot spots and solder problems, increasing the reliance on die lubricants for die surface cooling. However, higher pre-spray temperatures exacerbate the Leidenfrost effect, making effective cooling and lubrication more difficult and necessitating increased lubricant spray quantities, which in turn increases cycle times and costs.
Necessity of the Research:
The rising cost of fuel and stringent environmental regulations are pushing the automotive industry to reduce vehicle weight by replacing steel with aluminium and magnesium castings. This shift, coupled with constant innovation in aluminium alloys and casting technology to produce larger and more complex parts like engine blocks and door frames, necessitates advancements in die lubrication technology to overcome challenges posed by increased die temperatures and complexity. Existing lubrication methods are challenged by the Leidenfrost effect at higher die temperatures, requiring innovative solutions to maintain productivity and part quality in aluminium die casting.
4. Research Purpose and Research Questions:
Research Purpose:
The paper aims to examine the impact of trends in aluminium die casting, specifically the production of larger and more complex parts, on die and plunger lubrication. It further aims to discuss the evolution of lubrication technology to meet these new demands and improve quality and productivity in die casting operations.
Key Research:
The key research focuses on understanding and mitigating the challenges posed by increased die surface temperatures and the Leidenfrost effect in high-pressure die casting. This involves:
- Investigating methods to increase the Leidenfrost temperature of die lubricants.
- Developing die lubricants capable of forming a film rapidly on die surfaces at elevated temperatures.
- Evaluating the cooling performance of different die lubricant formulations.
- Assessing the die adhesion properties of new lubricant materials at varying temperatures.
- Validating the performance of new die lubricants in industrial settings, focusing on solder reduction, productivity improvement, and cycle time reduction.
Research Hypotheses:
The research is based on the hypothesis that by increasing the Leidenfrost temperature of die lubricants or by developing lubricants that can rapidly form a film at high temperatures, it is possible to improve die casting productivity and reduce defects like solder, even with increasing die surface temperatures associated with larger and more complex parts. Specifically, the paper explores whether new lubricant formulations can outperform conventional lubricants in terms of cooling efficiency, film formation at high temperatures, and overall die casting performance under demanding conditions.
5. Research Methodology
Research Design:
The research employs an experimental design, involving laboratory experiments and field trials to evaluate the performance of new die lubricant formulations compared to conventional lubricants. The laboratory experiments focus on fundamental aspects like Leidenfrost temperature, cooling curves, and film formation at controlled temperatures. Field trials are conducted in industrial die casting settings to validate laboratory findings under real-world operating conditions.
Data Collection Method:
Data collection methods include:
- Temperature measurement: Using thermocouples to measure die surface temperatures and cooling curves under different lubricant applications (Figure 3). Thermal images were also taken to monitor temperature profiles and spray distribution.
- Film formation measurement: Weighing the amount of lubricant film formed on stainless steel plates at specific temperatures to assess film formation efficiency at high temperatures. Stainless steel was used to avoid oxidation issues associated with H13 tool steel.
- Hot Die Adhesion Index: Measuring the ratio of lubricant film weight formed at 350°C and 250°C to quantify the uniformity of film formation across different temperatures (Figure 4).
- Industrial performance evaluation: Observing and recording parameters like solder formation, in-cavity buildup, overspray, cycle times, polishing frequency, and cleaning time in actual die casting operations (Figure 5 & 6).
Analysis Method:
The analysis methods involve:
- Comparative analysis: Comparing the performance of new lubricant formulations (Product A, Product B) against conventional lubricants (Std Prod, DI Water, Soft Water, Filt. Hard Water) across various metrics like cooling curves (Figure 3), Hot Die Adhesion Index (Figure 4), and industrial performance parameters (Figure 6).
- Graphical analysis: Using graphs and figures to visualize and interpret experimental data, such as cooling curves (Figure 3), Hot Die Adhesion Index bar chart (Figure 4), and performance comparison charts (Figure 6).
- Qualitative assessment: Observing and documenting qualitative improvements in industrial settings, such as reduction in solder, in-cavity buildup, and polishing requirements (Figure 5).
Research Subjects and Scope:
The research focuses on die lubricants for aluminium high-pressure die casting. Laboratory experiments were conducted using water and various lubricant formulations on stainless steel plates. Industrial trials were performed at customer die casting facilities, including a North American die caster producing engine blocks and a small multi-cavity die caster. The scope of the research is limited to the evaluation of die lubricants and their impact on cooling, film formation, die adhesion, and reduction of casting defects like solder in aluminium die casting.
6. Main Research Results:
Key Research Results:
- Leidenfrost Temperature Increase: The research successfully developed materials that significantly increase the Leidenfrost point of water-based die lubricants. Studies with water showed that dissolved salts increase the Leidenfrost point, with hard water having a higher Leidenfrost point (~340°C) than soft water (~320°C) and DM water (~315°C). New materials developed in this research further increased the Leidenfrost point beyond conventional lubricants.
- Improved Cooling Efficiency: New lubricant materials demonstrated improved cooling efficiency, potentially reducing spray time by 20% to 30% compared to conventional lubricants. Figure 3 shows cooling curves indicating faster cooling with Product A and Product B compared to DI Water, Soft Water and Filt. Hard Water.
- Enhanced Film Formation at High Temperatures: The new materials exhibited superior film formation at high temperatures, as indicated by the Hot Die Adhesion Index (Figure 4). Product A and Product B showed significantly higher Hot Die Adhesion Index values compared to Std Prod, indicating more uniform film formation across different temperatures (350°C and 250°C). New materials were found to be 2 to 3 times more efficient than conventional die lubricants in film formation.
- Solder and Defect Reduction: Industrial trials demonstrated a dramatic reduction in solder and in-cavity buildup with the new Safety-Lube® product (Figure 5 & 6). In the engine block casting case, the new lubricant eliminated the need for polishing every shift and reduced cleaning time by 50%. In the small multi-cavity die casting example, the new lubricant reduced solder and in-cavity buildup, eliminating emergency polishing and increasing productivity from 65% to 84%.
Analysis of presented data:
- Figure 3 (Die Cooling Curve): This figure illustrates the cooling performance of different fluids. Product A (1:100) and Product B (1:100) show significantly faster cooling rates compared to DI Water, Soft Water, and Filt. Hard Water across a temperature range from 380°C to 140°C. This indicates the superior cooling capability of the new lubricant formulations.
- Figure 4 (Hot Die Adhesion Index): This bar chart compares the Hot Die Adhesion Index for Std Prod, Product A, and Product B. Product A and Product B exhibit substantially higher indices than Std Prod, demonstrating improved uniformity of film formation across hot (350°C) and cooler (250°C) die surface temperatures.
- Figure 5 (Old Product vs. New Product): This figure shows visual evidence of solder reduction. The "Old Product (After 8 hours)" image shows significant solder formation, while the "New Product (After 8 hours)" image shows a clean die surface with minimal solder, demonstrating the effectiveness of the new lubricant in preventing solder buildup.
- Figure 6 (Performance Comparison): This bar chart compares the performance of Std Product and Product A across four parameters: High temp adhesion, Overspray, In-cavity buildup, and Solder. Product A shows significant improvement in all parameters, particularly in reducing solder and in-cavity buildup, and improving high temperature adhesion.
Figure Name List:
![Figure 2: [No explicit title, but depicts Wall Heat Flux vs. Temperature curve showing Tsat, TNukiyama, TLeidenfrost and Wetting Zone, Transition Zone, Non-wetting Zone]](https://castman.co.kr/wp-content/uploads/image-1144-1024x600.webp)
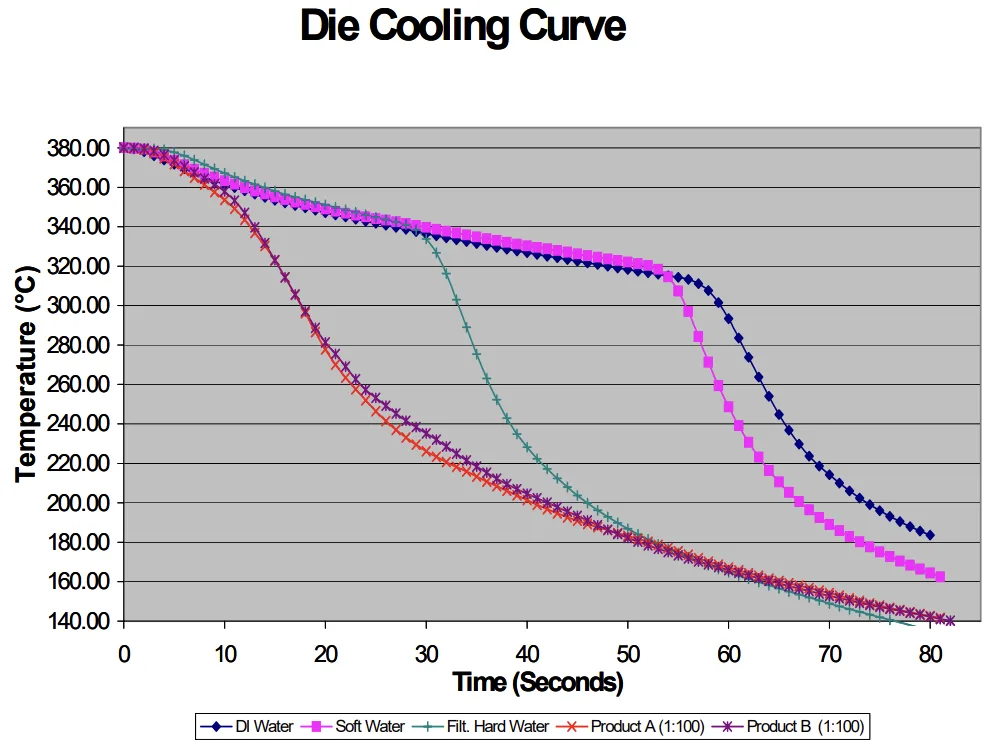
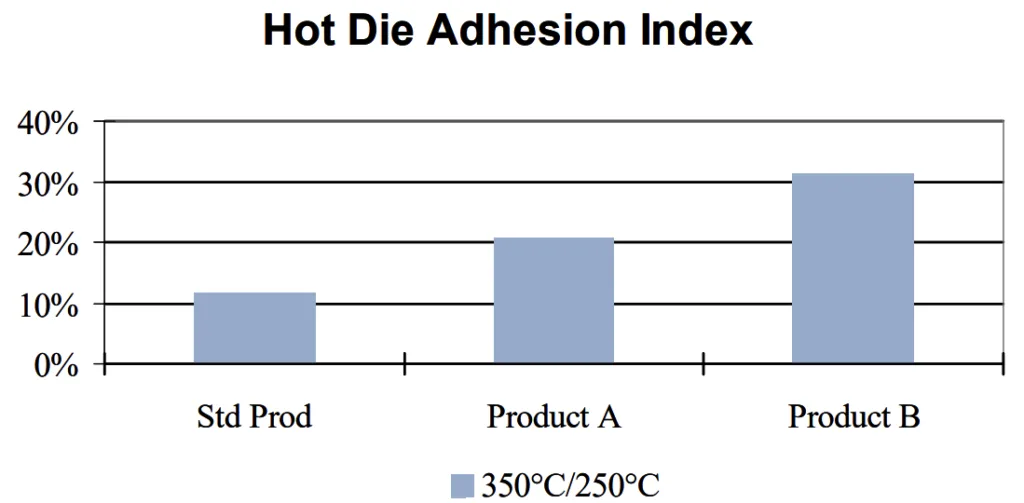
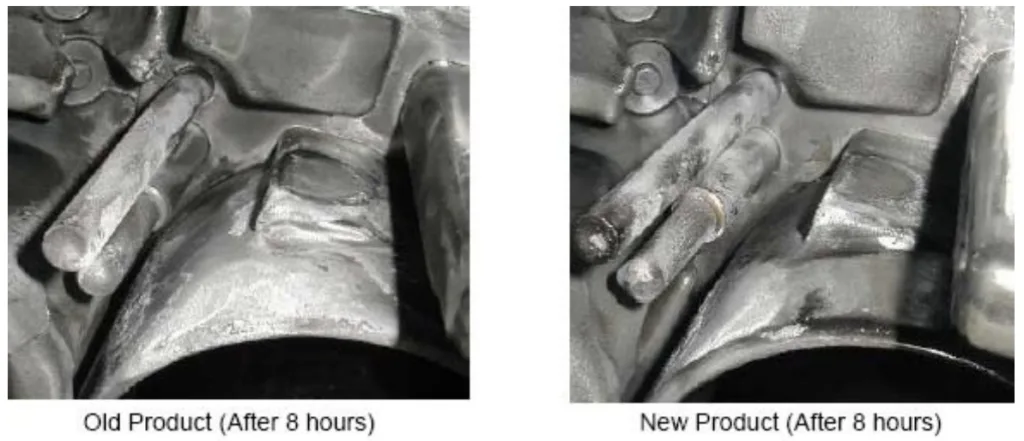
![Figure 6: [No explicit title, but depicts performance comparison between Std Product and Product A]](https://castman.co.kr/wp-content/uploads/image-1148-1024x839.webp)
- Figure 1: Nukiyama point. Nucleate boiling. Liquid in contact with metal surface / Leidenfrost point. Film boiling. Liquid not in contact with metal surface
- Figure 2: [No explicit title, but depicts Wall Heat Flux vs. Temperature curve showing Tsat, TNukiyama, TLeidenfrost and Wetting Zone, Transition Zone, Non-wetting Zone]
- Figure 3: Die Cooling Curve
- Figure 4: Hot Die Adhesion Index
- Figure 5: Old Product (After 8 hours) / New Product (After 8 hours)
- Figure 6: [No explicit title, but depicts performance comparison between Std Product and Product A]
7. Conclusion:
Summary of Key Findings:
The study successfully developed new die lubricant materials that significantly increase the Leidenfrost temperature and improve film formation at high die surface temperatures encountered in modern aluminium die casting. These new lubricants demonstrate enhanced cooling efficiency, leading to potential reductions in spray time and cycle times. Industrial trials confirmed that these lubricants effectively reduce solder formation, in-cavity buildup, and overspray, resulting in improved productivity and reduced die maintenance requirements, such as polishing and cleaning.
Academic Significance of the Study:
This study contributes to the fundamental understanding of die lubrication in high-pressure die casting, particularly in the context of increasing die temperatures and complex part geometries. It provides empirical evidence for the importance of Leidenfrost temperature and film formation characteristics of die lubricants in achieving efficient cooling and defect reduction. The research highlights the limitations of conventional die lubricants under increasingly demanding die casting conditions and demonstrates the potential of advanced lubricant formulations to overcome these limitations.
Practical Implications:
The development and validation of these new high-performance die lubricants have significant practical implications for the die casting industry. The use of these lubricants can lead to:
- Increased Productivity: Reduced cycle times due to improved cooling and minimized downtime for die polishing and cleaning.
- Improved Part Quality: Reduction in casting defects like solder and in-cavity buildup, leading to higher quality castings and reduced scrap rates.
- Cost Reduction: Lower lubricant consumption due to more efficient film formation, reduced die maintenance costs, and increased production output.
- Enhanced Operational Efficiency: Simplified die casting operations with less need for frequent interventions like polishing, leading to more consistent and reliable production.
Limitations of the Study and Areas for Future Research:
The paper does not explicitly state limitations or future research areas. However, potential limitations could include:
- Specific Alloy and Die Material Focus: The study may be primarily focused on aluminium die casting and specific die materials. Further research could explore the performance of these lubricants with different alloys (e.g., magnesium) and die materials.
- Long-term Durability: The paper focuses on short-term performance improvements. Long-term durability and performance of the new lubricants under continuous production conditions could be further investigated.
- Detailed Composition and Mechanism: While the paper highlights the performance benefits, further research could delve deeper into the detailed chemical composition of the new lubricants and the precise mechanisms by which they achieve increased Leidenfrost temperature and improved film formation.
- Optimization for Specific Applications: Further research could focus on tailoring lubricant formulations for specific die casting applications, considering factors like part geometry, alloy type, and production volume to optimize performance and cost-effectiveness.
8. References:
- "Simultaneous Measurements of droplet characteristics and surface thermal behaviour to study spray cooling with pulsed sprays" by Humberto M Loureiro, Miguel RA Panao, Antonio Luis L Moreira of Mechanical Engg Dept Instituto Superior Tecnico at Lisbon Portugal.
- "The effect of die lubricant spray on the thermal balance of dies" by Dr James L. Graff, Chem-Trend & Dr Lothar H. Kallien, presented at the NADCA conference in Cleveland, USA Oct 18-21, 1993
9. Copyright:
- This material is "G.NATESH"'s paper: Based on "ALUMINIUM DIE CASTING: LUBRICATION TECHNOLOGY AND TRENDS".
- Paper Source: [DOI URL] (Not available in the document)
This material was summarized based on the above paper, and unauthorized use for commercial purposes is prohibited.
Copyright © 2025 CASTMAN. All rights reserved.